The Essential Handbook for Construction Equipment Repair and Maintenance
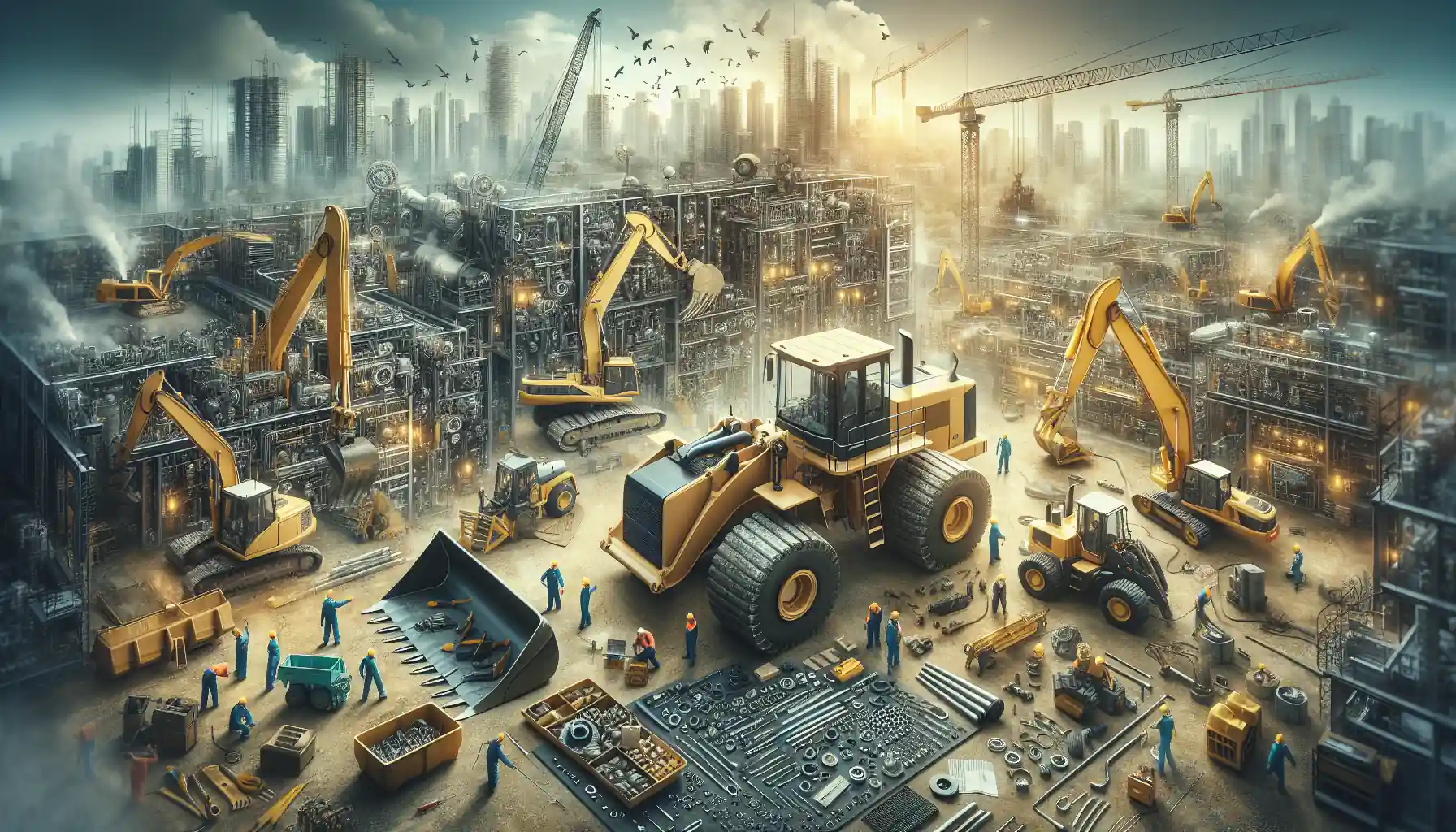
As we delve into the essential handbook for construction equipment repair, we'll explore procurement strategies and other tactics for effective management, focusing on optimizing repair and maintenance expenses. Deciding when to repair or replace, implementing effective maintenance programs, and the benefits of regular upkeep.
This guide also highlights the role of advanced technologies in enhancing maintenance and repair processes, aiming for operational excellence in construction equipment management.
Evaluate When to Repair or Replace Equipment
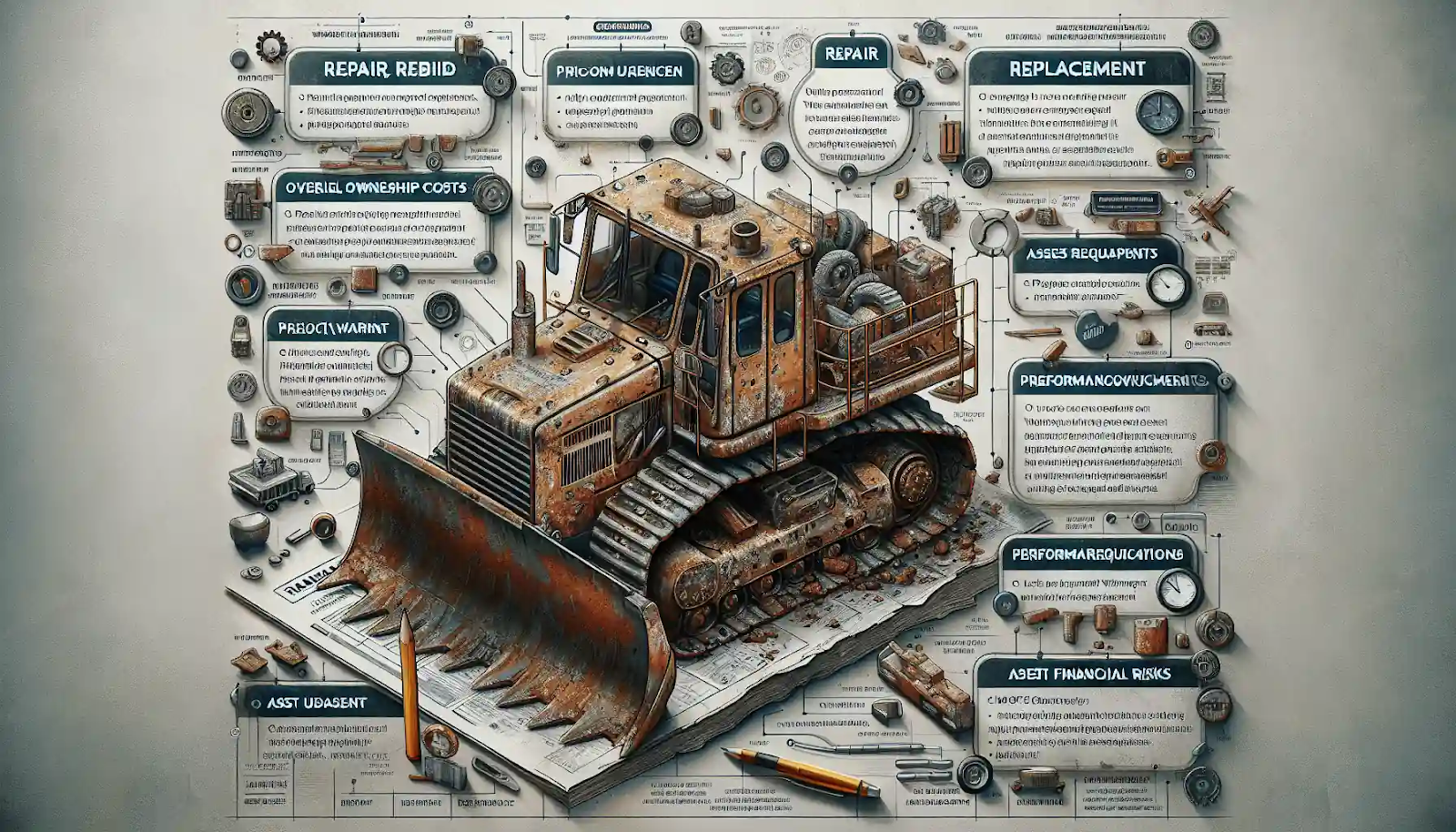
When faced with the decision to repair or replace construction equipment, several critical factors must be considered to ensure cost-effectiveness and operational efficiency. This includes weighing the pros and cons of repair vs replace decisions and incorporating procurement strategies to significantly impact your project's success and your company's bottom line.
Key Considerations for Repair or Replacement
- Age and Usage: Assess the equipment's age and how intensively it has been used. Older equipment or those that have been heavily used may require more frequent repairs.
- Repair Costs vs. Technological Advances compares the cost of repairs against the benefits of newer technology. Modern equipment may offer improved efficiency and safety features, making equipment replacement a strategic decision.
- Project Needs and Safety Compliance evaluate whether the existing equipment meets the current and future project requirements and complies with safety standards, considering the service life of the machinery.
- Total Cost of Ownership (TCO): Consider not only the purchase price but also operational, downtime, and maintenance costs. This comprehensive view helps in making an informed decision.
- Asset Utilization calculate the machine's cost per hour by dividing the Total Cost of Ownership by total run time. This metric, reflecting operating costs, helps in assessing whether keeping the equipment is cost-effective.
- Performance Metrics: Key performance indicators such as overall equipment effectiveness, failure rate, mean time to repair, and return on investment should guide the decision-making process.
- Legal and Financial Risks: Operating unsafe equipment can pose significant legal and financial risks to your business.
- Real-time Data having accurate, real-time cmms data on equipment performance, maintenance, and costs is crucial for making informed decisions.
Guidelines for Decision-Making
- Repair when minor components need replacement, if the machine is under warranty, or if it's still being paid off, parts procurement becomes a critical consideration, emphasizing the importance of a well-managed parts inventory.
- Rebuild if the cost of repairs exceeds half the cost of replacing the machine, or if the machine is still in relatively good condition but requires significant updates, it's time to consider economical repair options.
- Replace when the machine is excessively worn out, repairs are becoming too frequent and severe, or if expanding operations necessitate newer technology, it signals when to replace the equipment.
Factors to Weigh
Consider warranty coverage considering outstanding payments, the improvement in performance after repairs or rebuild, the need for power or performance upgrades, resale or scrap value, tax implications, competitive advantage in bidding, and optimization of operation costs are crucial.
A thorough repair vs replace cost analysis can help in determining the salvage value of construction equipment, guiding whether to repair, rebuild, or replace.
Making the right choice between repairing, machine rebuilding, or replacing construction equipment is pivotal for maintaining operational efficiency and managing costs effectively.
By carefully evaluating these factors and implementing strategic procurement strategies, including repair and replace decisions, you can ensure that your decisions are both cost-effective and align with your company's financial and operational goals.
Implement Effective Maintenance Strategies
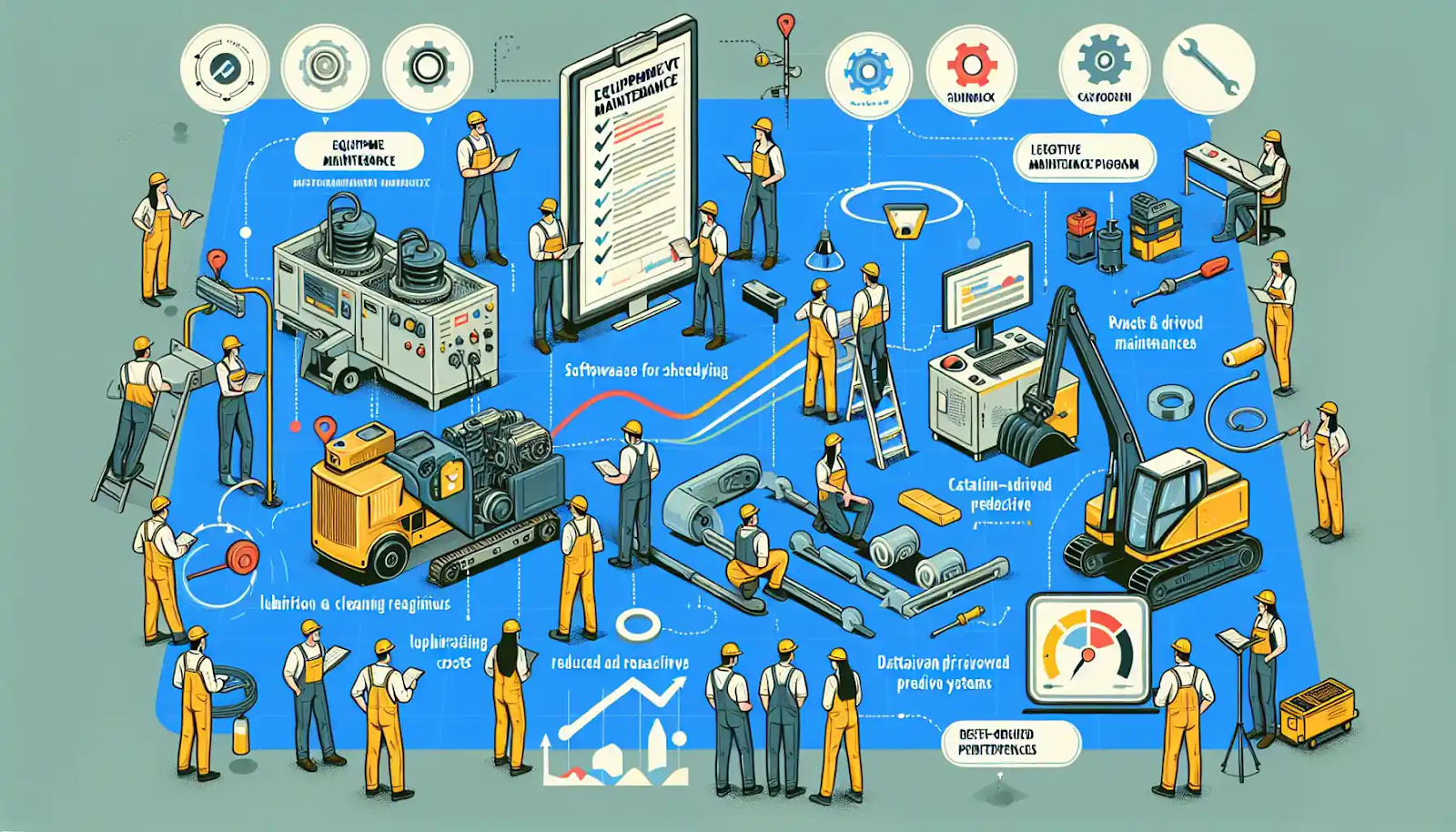
Comprehensive Equipment Maintenance Checklist
- Create a detailed checklist for each machine, covering all components and systems.
- Consult the original equipment manufacturer's (OEM) manuals for maintenance intervals and procedures.
- Include routine tasks, such as inspections and part replacements, in the program.
Training and Documentation
- Train employees on proper equipment operation for safer, more cost-effective operations.
- Designate a responsible person to administer the maintenance program and schedule service milestones.
- Document all service work and preventive maintenance to predict potential issues and maintain the machine's value.
Maintenance Program and Software
- Establish a construction equipment maintenance program that covers routine and preventive maintenance.
- Utilize construction equipment maintenance software to manage tasks and schedules efficiently.
Preventive Maintenance and Repairs
- Implement both proactive and reactive maintenance as part of your preventive plan.
- Schedule regular inspections and part replacements to prevent excessive wear and sudden failures.
Lubrication and Cleaning
- Adopt proper lubrication programs to extend equipment life and save on maintenance cost to replace.
- Regularly clean equipment to prevent overheating and wear, ensuring optimal functioning.
Utilizing Data for Maintenance
- Leverage data-driven insights and predictive maintenance systems to identify potential failures before they occur, reducing downtime.
- Monitor equipment utilization and performance through digital solutions for efficient resource use.
Remember, a well-maintained fleet not only saves on repair costs but also enhances safety and productivity on the job site, embodying the principle of maintenance vs repair.
The Impact of Regular Repair and Maintenance
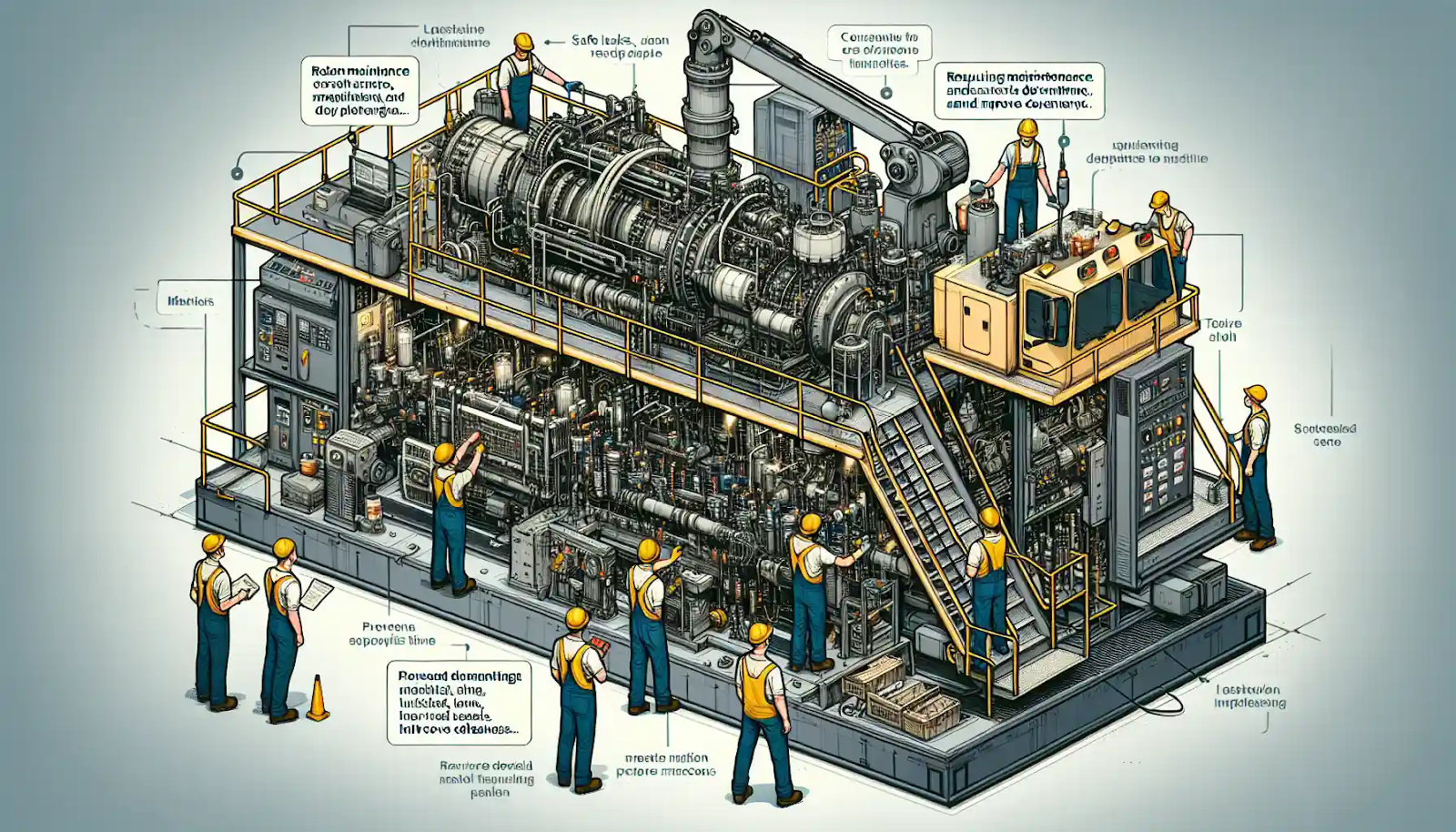
By conducting regular maintenance checks, including inspecting for fluid leaks, levels, functionality, and cleanliness, you ensure the productivity of your cost-effective equipment, prevent downtime, and maintain engine efficiency. This practice is at the heart of scheduled and condition-based maintenance, ensuring effective maintenance processes.
This approach not only improves the longevity of the equipment but also decreases safety risks, reduces potential costs, avoids project delays, and minimizes preventable injuries, addressing concerns of equipment downtime and lost productivity.
Moreover, regular maintenance and preventive measures are pivotal for the longevity, availability, cost-effectiveness, and safety of your equipment, helping to prevent litigation and embodying the principles of total productive maintenance.
Key Benefits of Regular Maintenance
- Risk Management the early identification of parts likely to break or need replacing through regular inspections allows for planning of repairs, reducing delays.
- Employee Safety: Equipment that is properly maintained poses fewer dangers, creating a safer working environment.
- Reduced Repair and Maintenance Expense: Addressing issues early can avoid expensive repairs or part replacements.
- Increased Equipment Lifespan keeping parts in good condition through regular maintenance extends the lifespan of heavy equipment.
- Boosting Resale Value equipment that is regularly maintained retains its value better, facilitating easier sales when upgrading.
- Productivity and Cost Savings enhancing preventive maintenance procedures can reduce repair costs by up to 25% and save on replacements or disposals.
- Efficiency preventing downtime through regular maintenance not only allows machine operators to be assigned productive tasks but also enhances the production capacity, improving overall efficiency.
- Compliance: Regular maintenance ensures compliance with local and federal laws, safeguarding against legal issues.
- Safer Operation: Ensuring that construction equipment is safer to operate, thus avoiding accidents.
- Greater Efficiency: Keeping construction equipment operating as intended through regular maintenance improves overall efficiency.
Addressing Unplanned Downtime and Budget Concerns
- Frequency of Unplanned Downtime: Equipment breakdowns, accounting for 42% of the $50 million annually lost due to unplanned downtime, highlight the need for effective maintenance.
- Maintenance Budgets: The tendency of construction companies to overspend on maintenance, with poor issue recognition costing US businesses $21 million a year, underscores the importance of efficient repair and maintenance strategies.
Challenges in Construction Machinery Maintenance
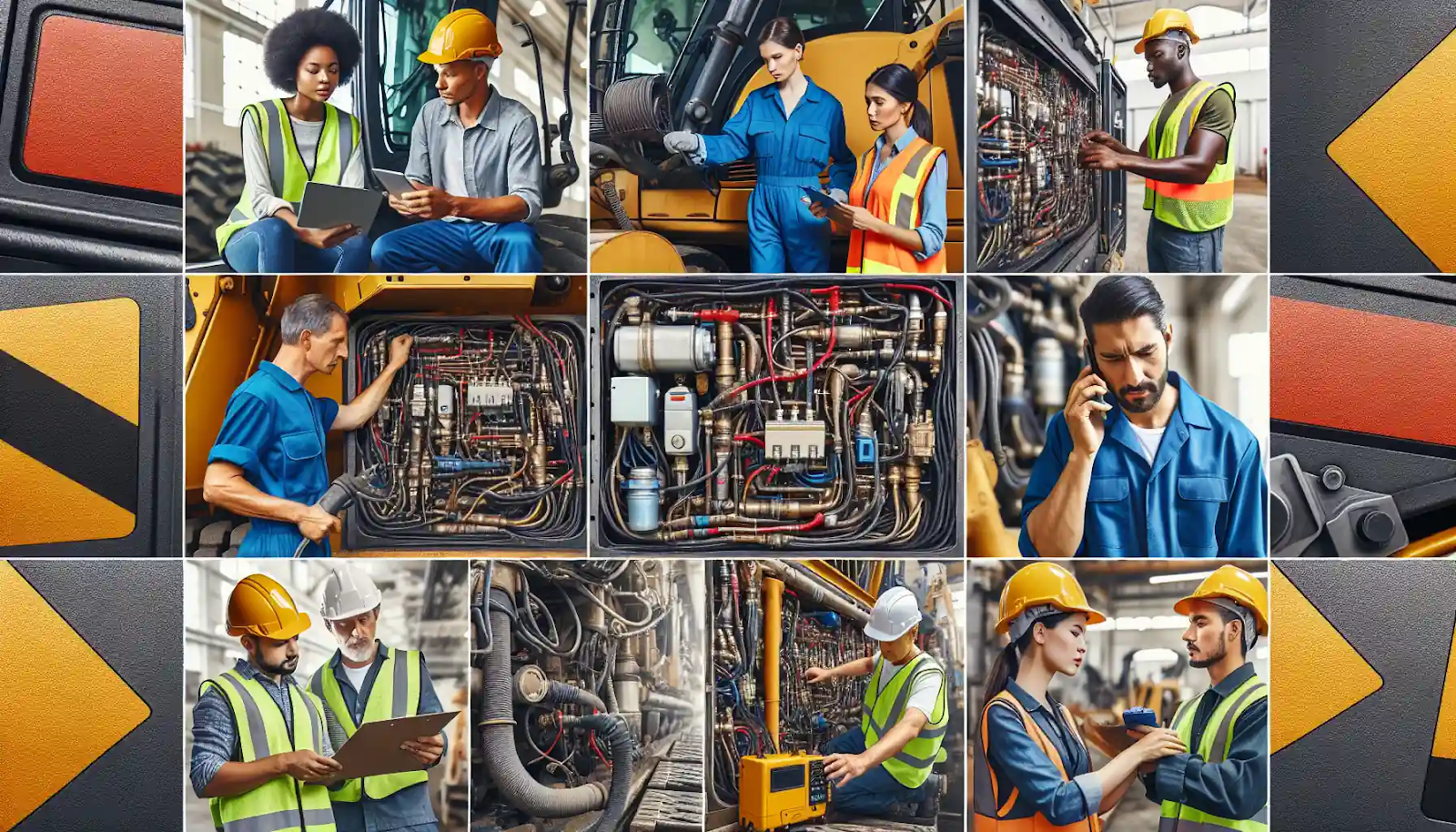
Hydraulics and Contamination
- Contaminants: Water, dirt, metal, and dust can infiltrate hydraulic systems, causing various issues.
- Prevention: Regular fluid inspection and maintenance are crucial to avoid these problems.
Electrical System Failures
- Causes: Loose connections, contaminants, insulation issues, and power overloads can lead to electrical failures.
- Solutions implementing proper safety training, risk assessments, and using voltage regulators and cord insulation can mitigate these risks.
Undercarriage Maintenance
- Common Issues: Leakage, damaged tracks, misalignment, insufficient lubrication, and overloading can significantly damage undercarriage components.
- Maintenance Tips: Regular maintenance tasks and thorough inspections are essential for sustaining undercarriage performance.
Metal Corrosion
- Risks: Corrosion and rust can lead to equipment malfunction, especially in humid environments.
- Preventive Measures: Utilizing rust and corrosion inhibitors can minimize the equipment's exposure to corrosive substances.
Heating System Malfunctions
- Common Causes clogged air filters, faulty thermostats, malfunctioning blower motors, and coolant system leaks can lead to heating malfunctions.
- Maintenance Advice: Regular checks and maintenance of these components are vital, especially during colder months.
Mechanical Failures
- Root Causes: Poor maintenance, wear and tear, and operator error often lead to mechanical failures.
- Strategy: Implementing a proactive maintenance schedule can help in mitigating these issues.
Prioritizing Service Tasks
- Struggle: Maintenance teams often face difficulties in prioritizing service tasks effectively.
- Approach: Developing a clear prioritization strategy can help in addressing this challenge.
Data Management for Maintenance
- Importance: Accurate documentation is crucial for assessing the effectiveness of a maintenance plan.
- Method implementing a reliable data management system, such as advanced CMS software, can provide valuable insights into equipment performance and maintenance needs, enhancing operational efficiency.
Traditional Equipment Management Problems
- Inaccuracies manual processes, including inaccurate logs and failure to comply with calibration standards, can lead to inefficiencies.
- Solution adopting digital solutions for equipment management, focusing on maintenance management, can reduce the risk of errors and significantly improve operational efficiency.
Tracking and Security
- Risk high risk of theft and misplacement poses a significant challenge in tracking construction machinery.
- Strategy utilizing advanced tracking technologies can help in mitigating these risks and improving equipment security.
Maintenance Cost Concerns
- Budget Impact while regular maintenance is essential, unscheduled maintenance due to neglect or sudden equipment failure can be significantly more costly.
- Financial Planning: Developing a comprehensive maintenance budget can help manage these expenses effectively.
In addressing these challenges, you can ensure the reliability and efficiency of your construction equipment.
For further assistance and a free consultation on sourcing construction machinery or parts, consider contacting MCH Parts for expert advice and a free quote.
Advanced Technologies for Maintenance and Repair
Construction Equipment Management Software
Construction equipment management software like Autodesk Build, Workyard, TruckIT, SiteSense, and ONE-KEY revolutionize how information is centralized and equipment is tracked, offering a comprehensive solution for efficient equipment management with enhanced work order management capabilities.
24/7 Repair Services and Custom Solutions
MCH Parts provides round-the-clock repair services, ensuring quick response times and availability for on-site and in-house service and repair on all major brands of mobile equipment. MCH Parts's replacement parts guarantee prompt and efficient service.
Service Agreements and Maintenance Alerts
MCH Parts exemplifies the proactive approach to construction equipment maintenance with service agreements that alert customers when it's time for maintenance, guiding them on proper maintenance and servicing practices to enhance equipment longevity and performance.
Remote Monitoring and Support
The integration of connected devices and remote communication technologies enables equipment manufacturers to monitor the performance of their machines in real-time, offering immediate support to customers. This innovation significantly reduces the need for on-site repairs, minimizing downtime and enhancing operational efficiency.
Sustainable Practices and Technologies
The shift towards sustainability is evident in the adoption of biofuels, electric power, and hybrid engines in construction equipment. These technologies not only contribute to environmental conservation but also open new avenues for specialized maintenance and repair services.
Remote-Controlled and Drone Technology
Remote-controlled equipment and drones are transforming the construction industry by allowing operators to perform tasks from a safe distance and gather real-time data on-site, respectively. These technologies improve safety, reduce operational costs, and boost productivity.
Predictive Analytics and IoT
Leveraging IoT and predictive machine learning models streamlines operations, reduces maintenance costs, and prevents downtime. This advanced analytical approach enables a more efficient and predictive maintenance strategy.
Electric-Powered Equipment Advantages
Electric-powered construction equipment offers significant benefits, such as reduced noise levels and zero emissions, making them ideal for nighttime operations in urban areas and indoor use.
Virtual Equipment Dealerships and AR
Virtual equipment dealerships are enhancing their online presence through augmented reality technologies. AR enables remote consultations and facilitates machine repairs, improving customer service and convenience.
Automation, Telematics, and Future Developments
Advancements in automation, telematics, and the integration of AI in heavy equipment design are leading to increased precision, efficiency, and safety. Telematics systems, such as CASE's SiteWatch System and KubotaNow Telematics, offer real-time monitoring, predictive maintenance, and valuable customer insights.
Asset Management Software and Tracking Technologies
Asset management software automates manual processes and eliminates the use of spreadsheets, providing accurate data for efficient equipment tracking. Techniques such as barcode, QR codes, or RFID offer real-time location updates, aiding in theft prevention and maintenance scheduling, ultimately increasing equipment performance.
For further assistance and a free consultation on sourcing construction machinery or parts, consider contacting MCH Parts for expert advice and a free quote.
Conclusion
The strategies laid out underscore the importance of regular maintenance routines, the utilization of advanced technologies, and strategic procurement decisions between repairing or replacing equipment to optimize operational efficiency and extend the lifespan of valuable assets. Incorporating repair machinery techniques and equipment maintenance cost estimates into these strategies further enhances the ability to make informed decisions.
These practices are fundamental not only for cost savings but also for adhering to safety standards and enhancing project delivery timelines, painting a vivid picture of the critical balance required in construction equipment management, influenced by strategic procurement strategies.
Incorporating these guidelines into your maintenance plans will undoubtedly yield noticeable improvements in performance and cost management.
For further enhancement of your equipment management strategies and to ensure your business benefits from top-tier equipment and service, reach out to MCH PARTS, a leading industrial equipment supplier. A free sourcing construction machinery or parts consultation.
Our expertise can provide you with the essential support needed to keep your operations running smoothly and efficiently.
FAQs
1. What does an equipment maintenance checklist entail?
An equipment maintenance checklist is a vital tool that ensures machinery, equipment, or facilities are operational, safe, and efficient. It includes a detailed set of tasks that should be performed regularly to maintain the equipment's good working condition and safety.
2. What constitutes an equipment maintenance procedure?
An equipment maintenance procedure encompasses the application of specific maintenance techniques and processes, including routine inspections and the necessary corrective repairs equipment to keep equipment in optimal working condition. This involves maintaining the functionality and reliability of the assets.
Read More
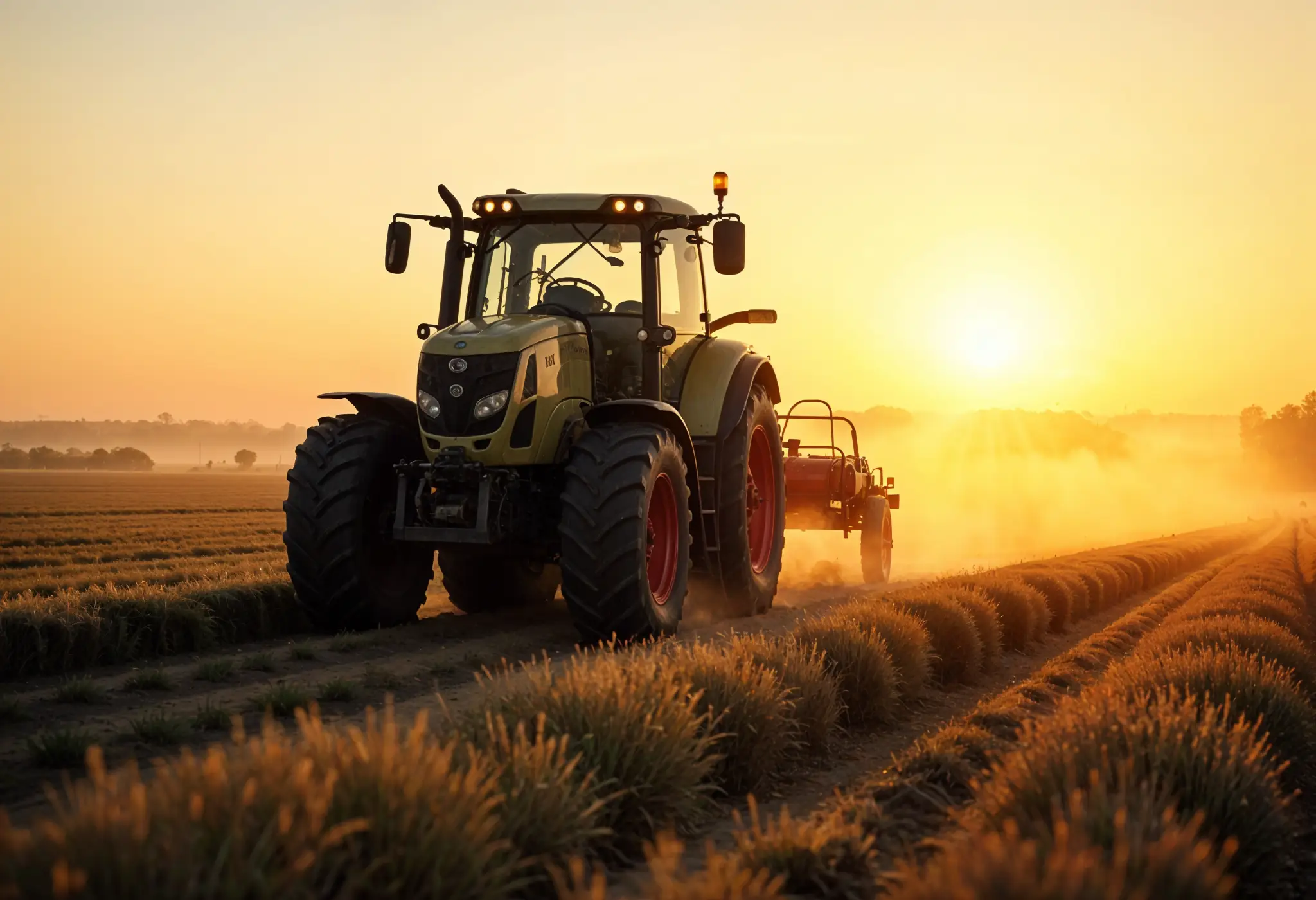
Top Hydraulic Components for Agricultural Equipment in 2025: Complete Guide
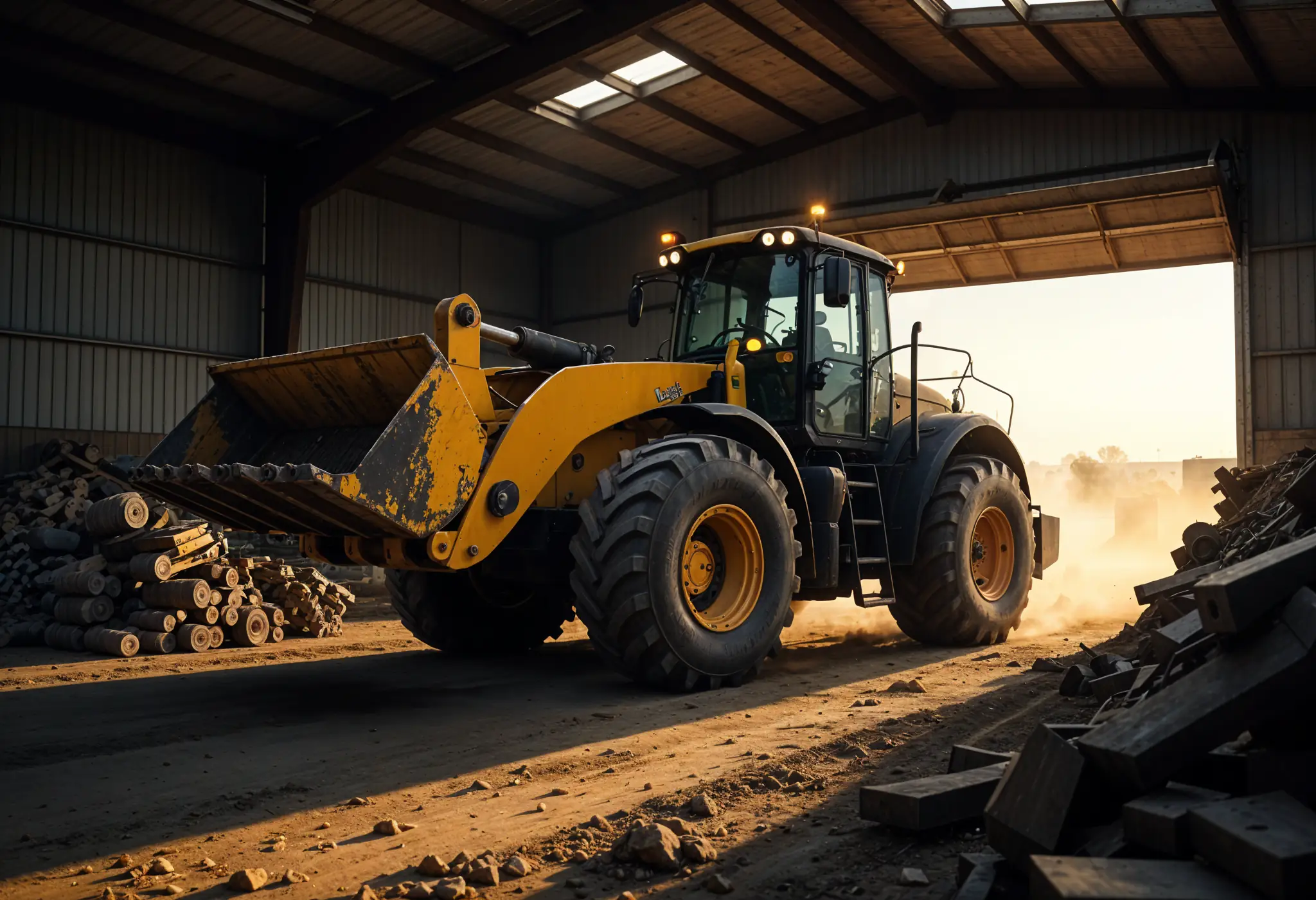
The Essential Farm Equipment Parts You Can't Afford to Run Out Of
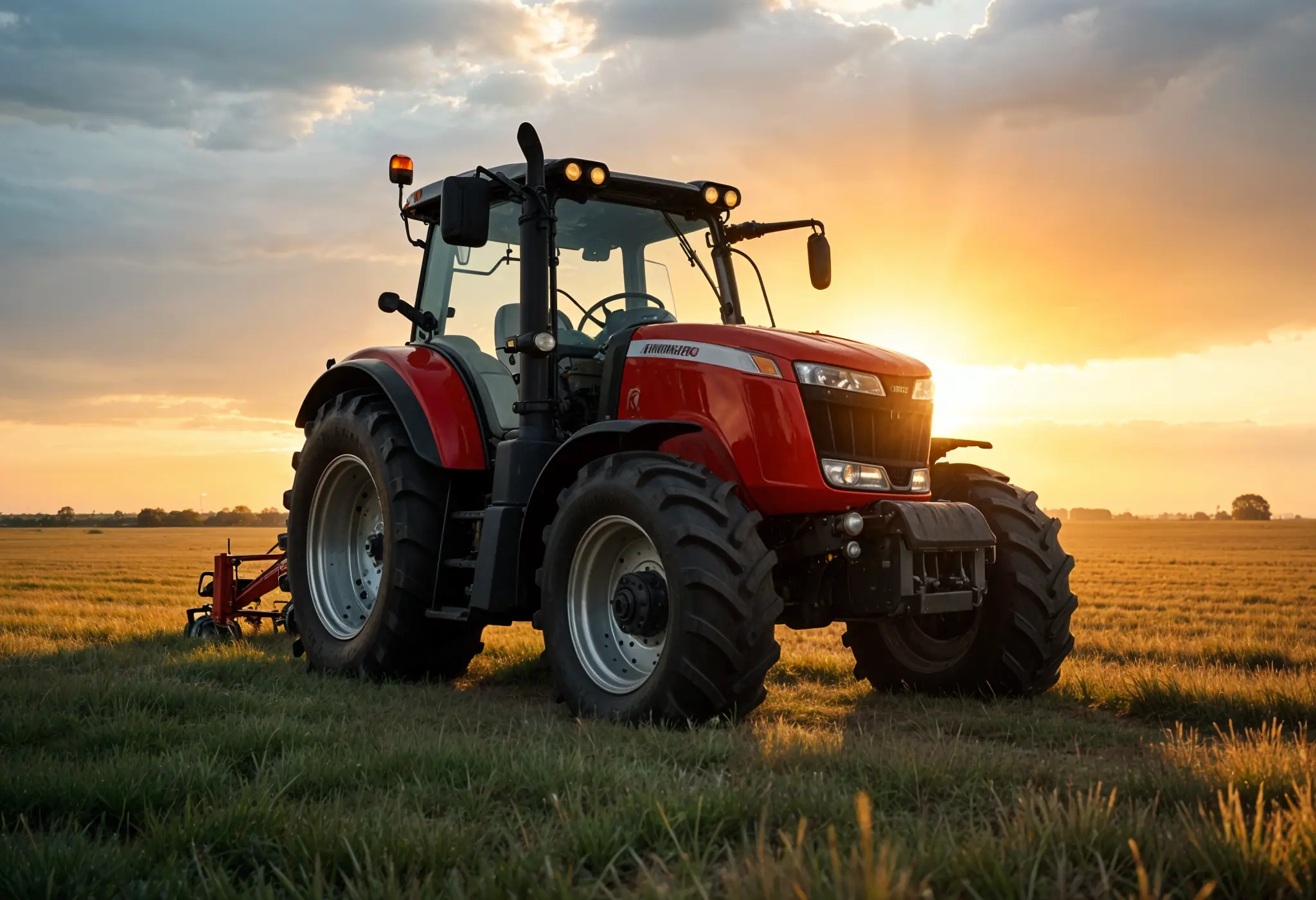
How to Service Farm Equipment: A Farmer's Guide to Zero Harvest Downtime
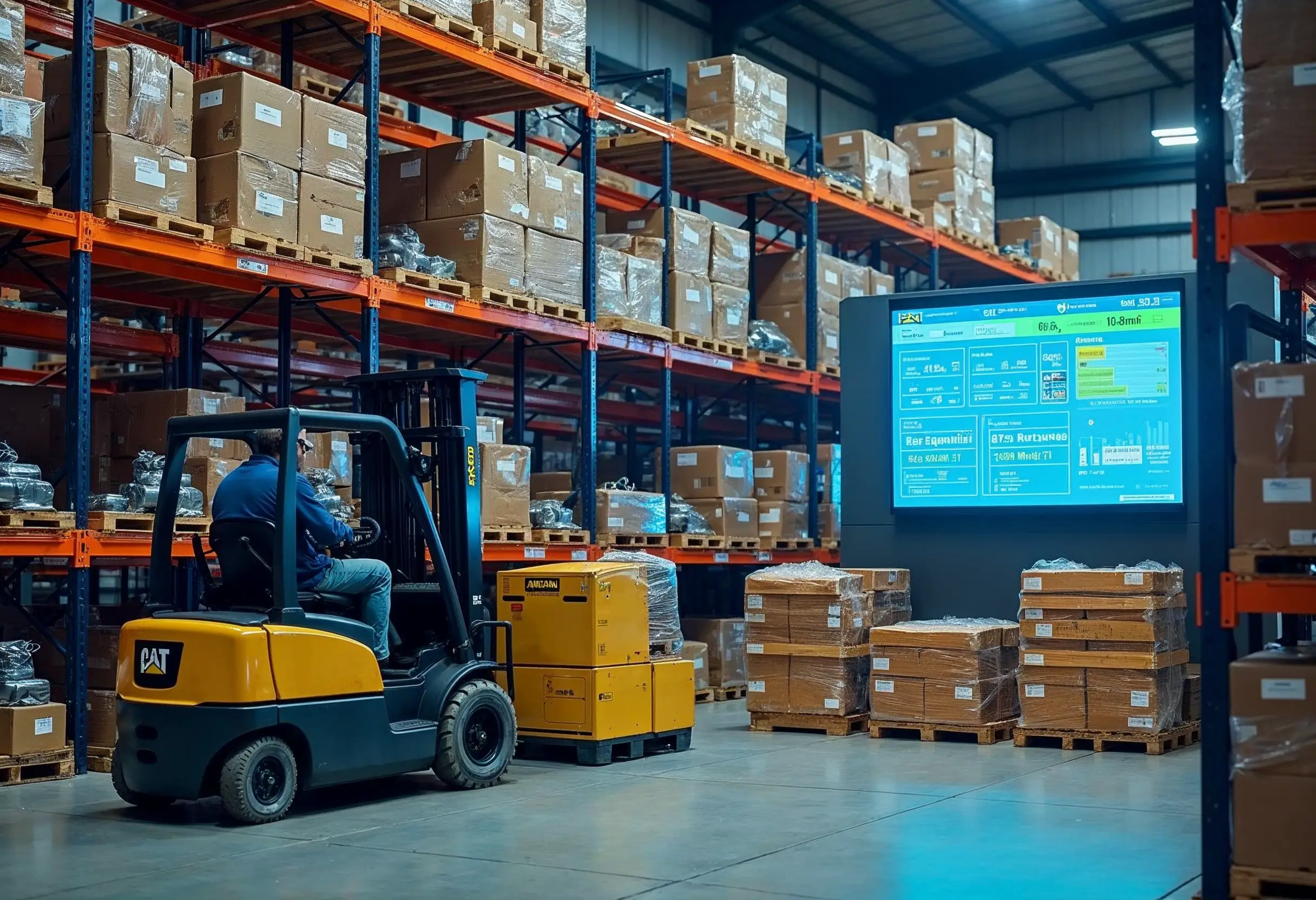
Construction Machinery Parts Suppliers: Expert Selection Guide
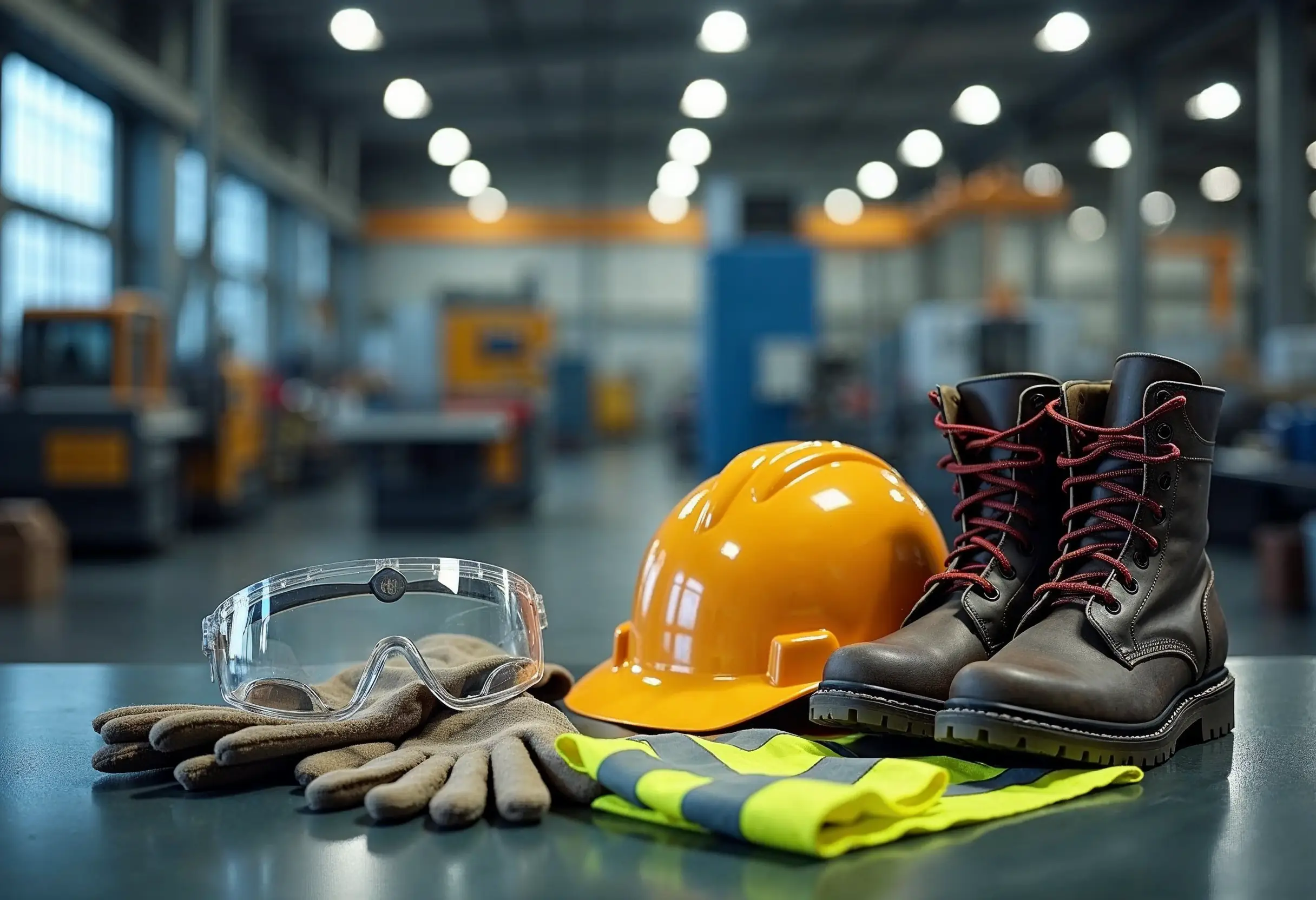
How to Apply Machine Safety Rules: From Selection to Installation
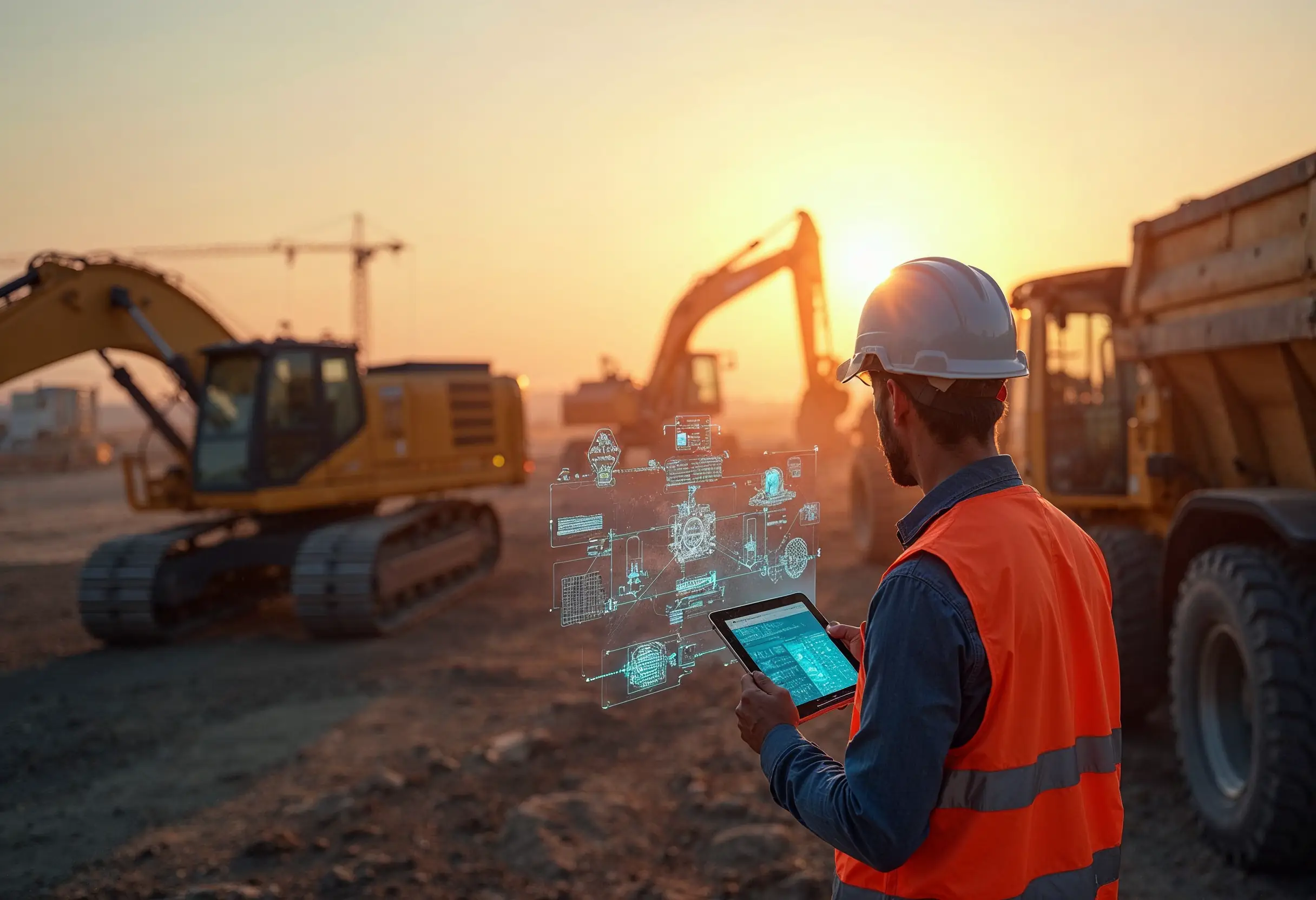
Smart Diagnostics Cut Heavy Equipment Failures by 73%
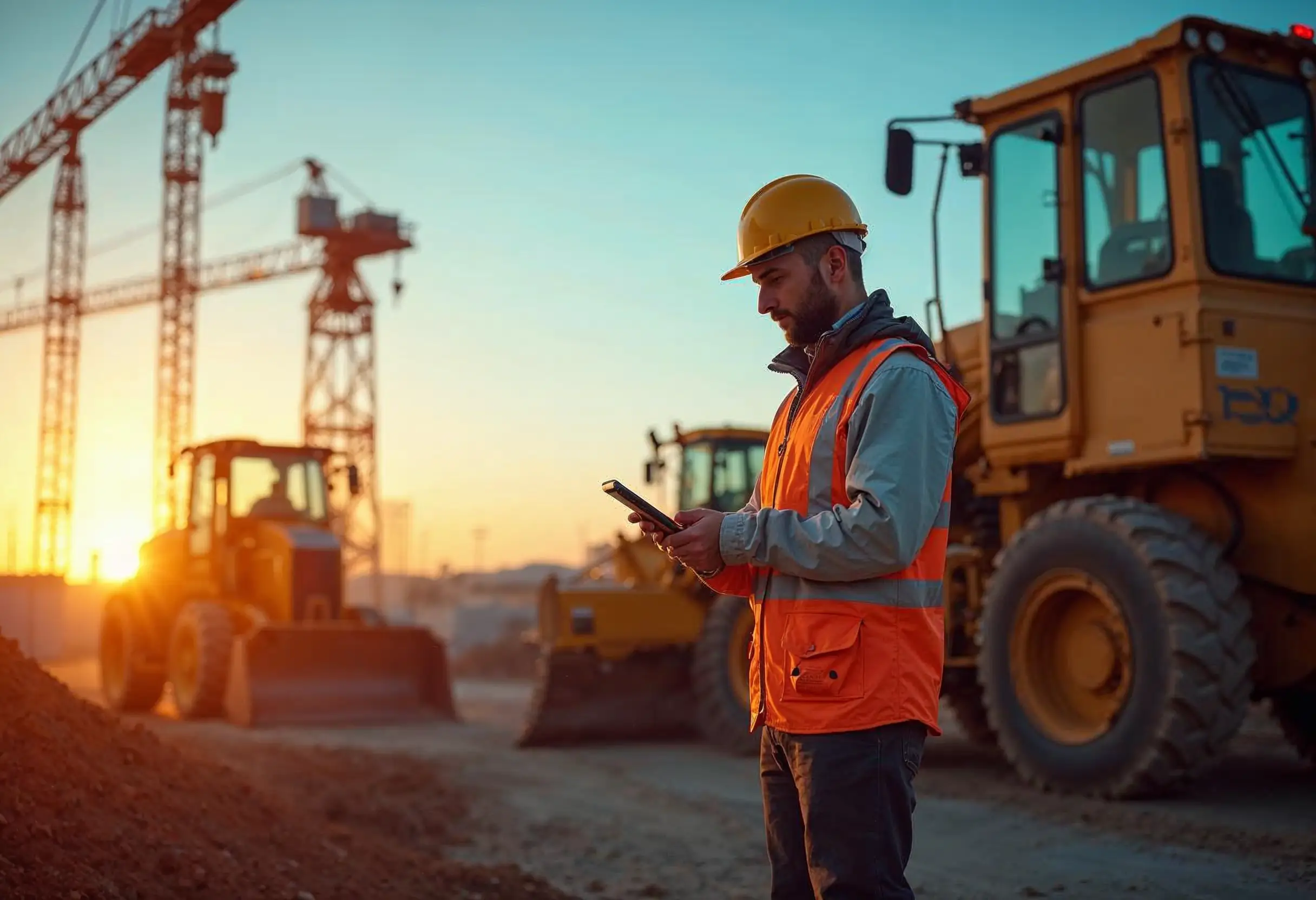
5 Ways to Assess the Environmental Impact of Heavy Construction Machinery
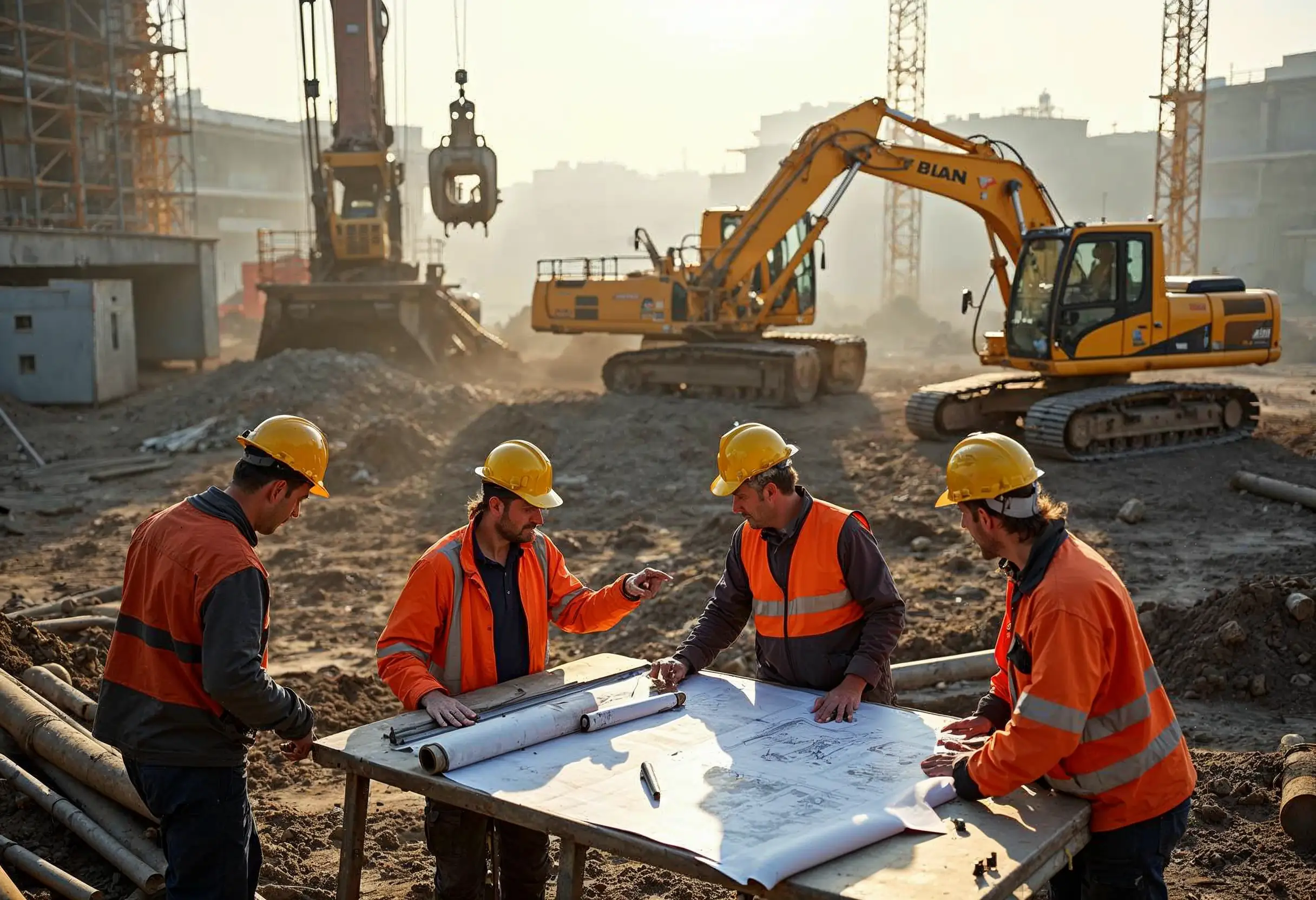
10 Smart Ways to Pick Construction Machinery for 2025 Projects
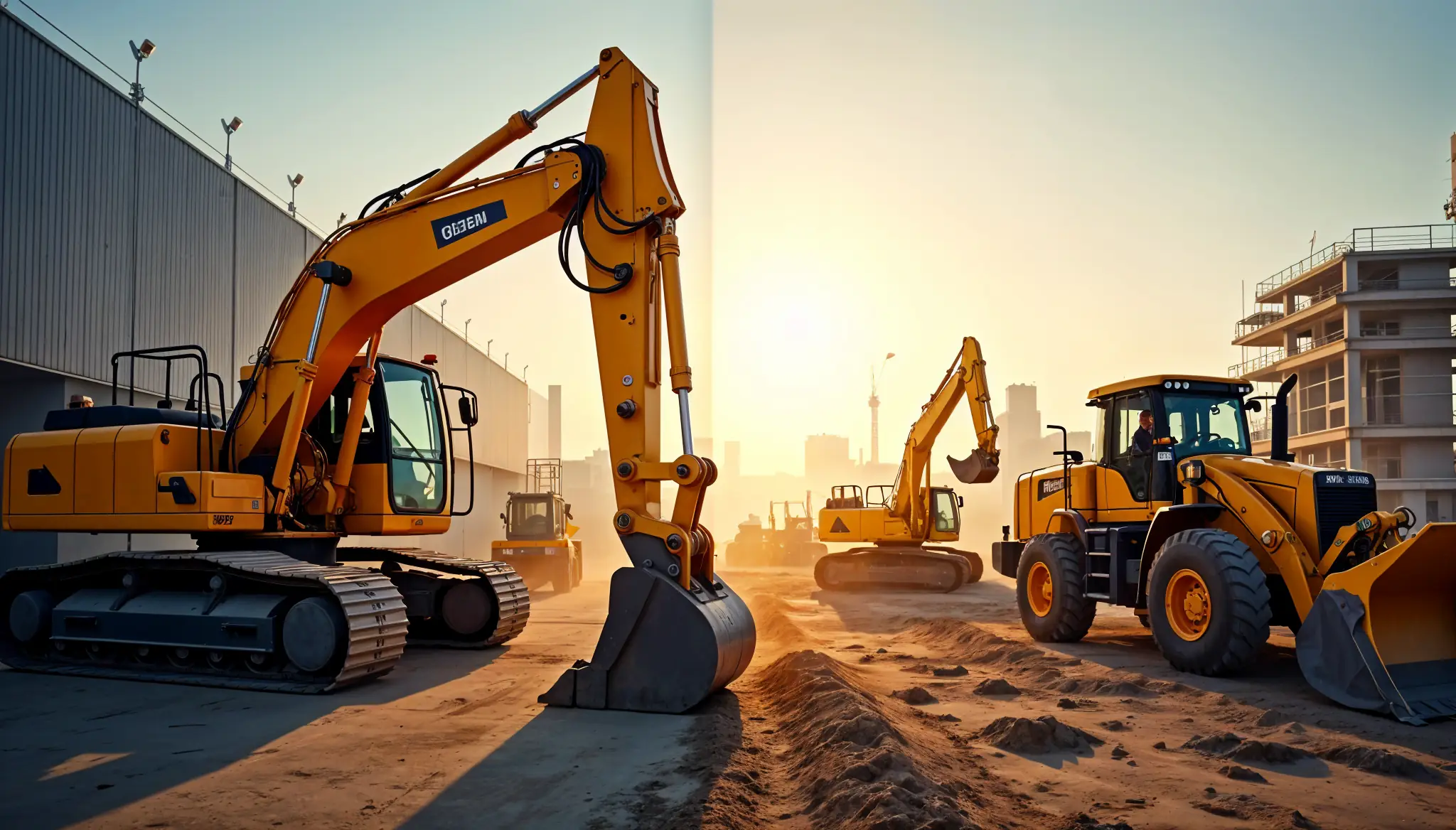
Rent vs Purchase Equipment: What Heavy Industry Experts Hide
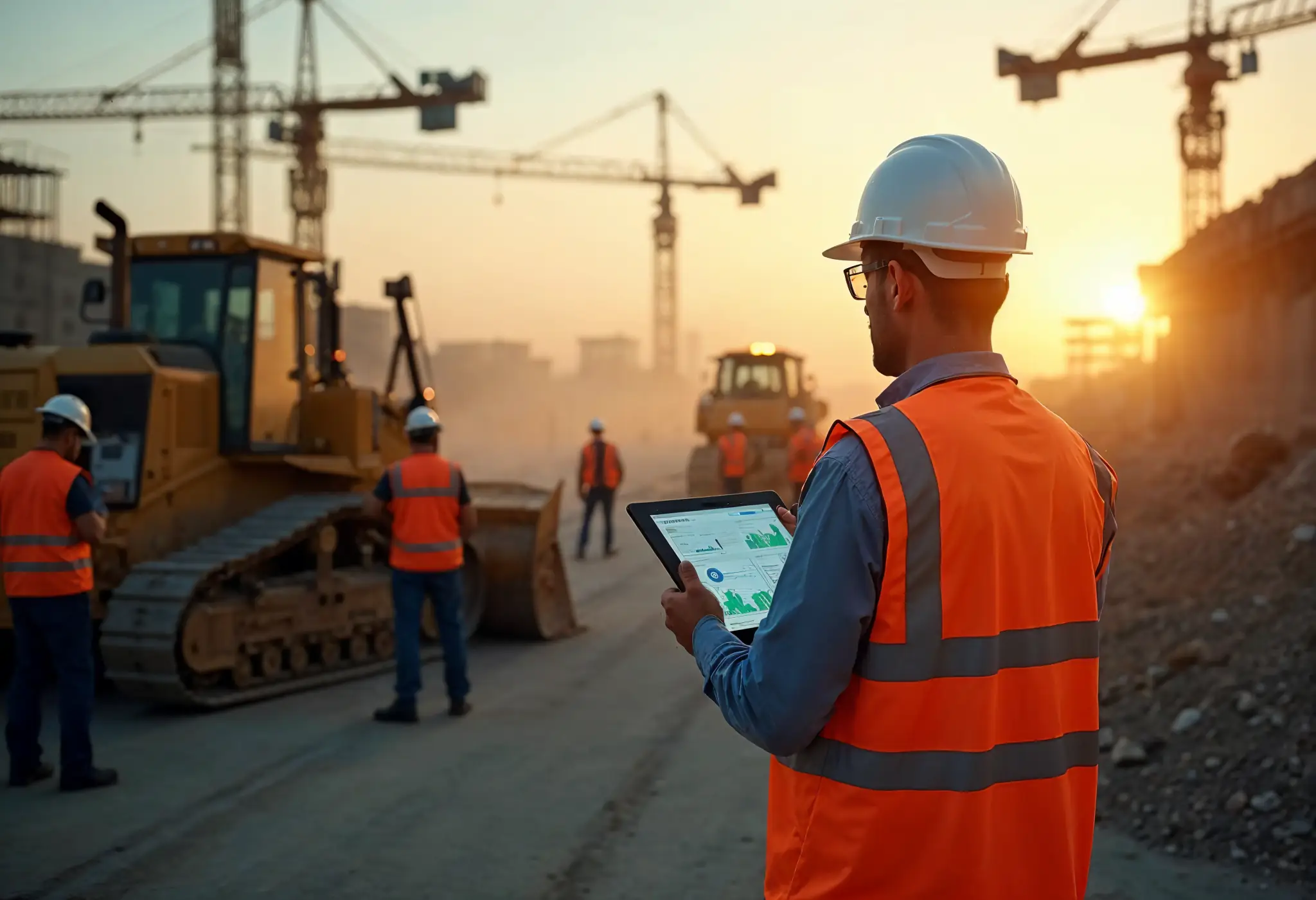
How to Implement a Construction Inventory Management System for Equipment Efficiency
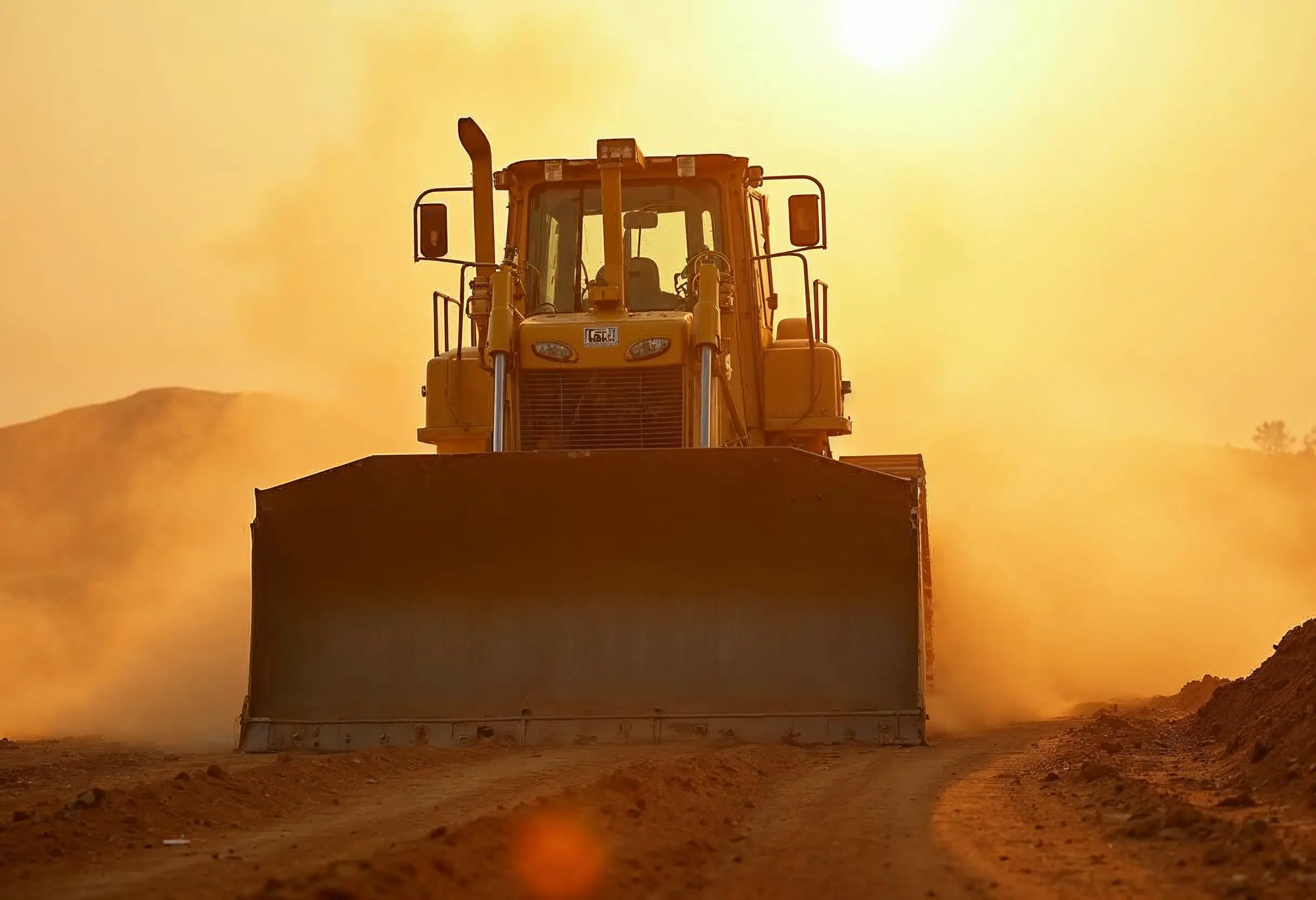
How to Extend Equipment Life Expectancy with Regular Maintenance
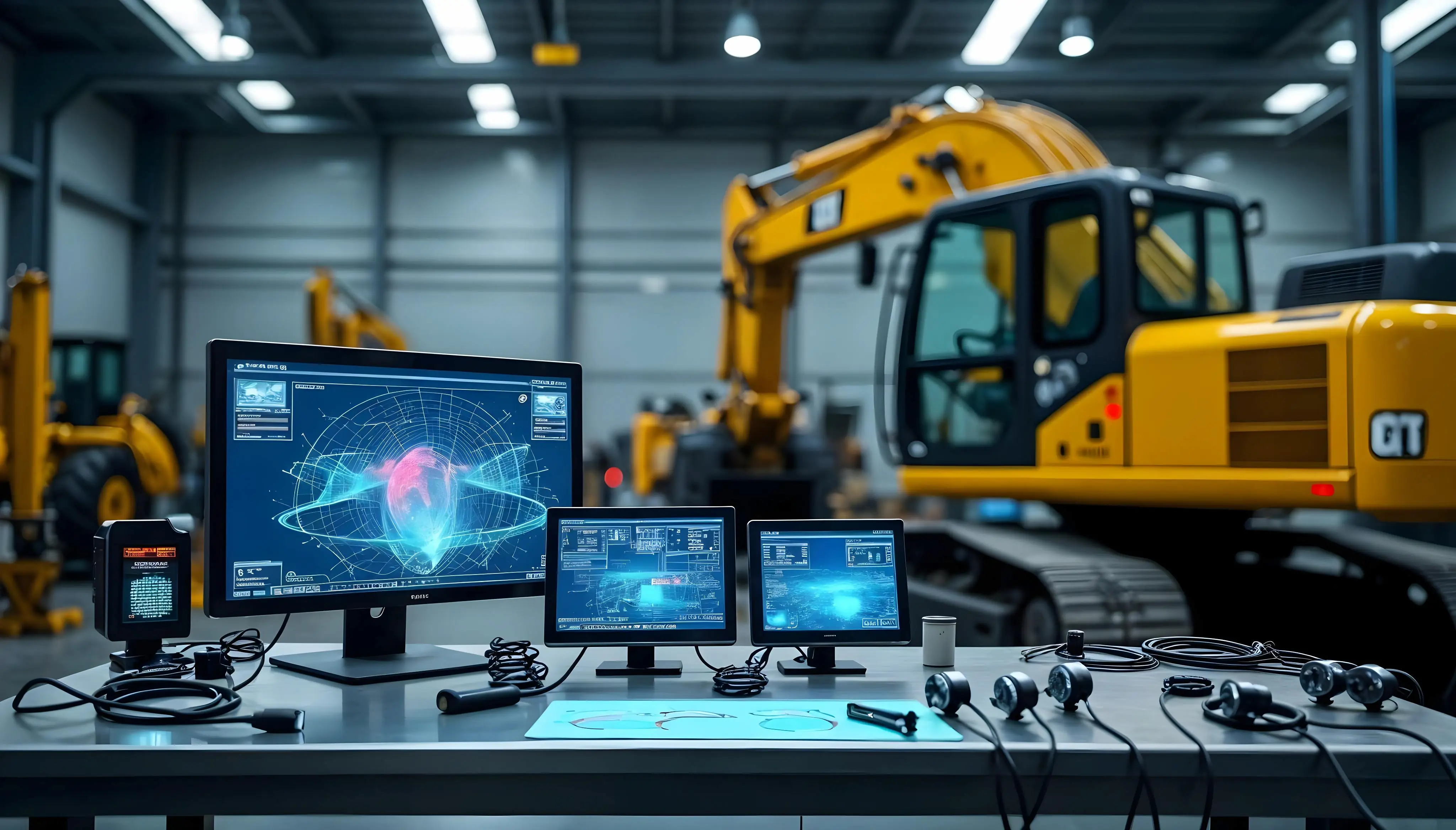
Advanced Heavy Equipment Diagnostic Tools: Ensuring Construction Machinery Quality
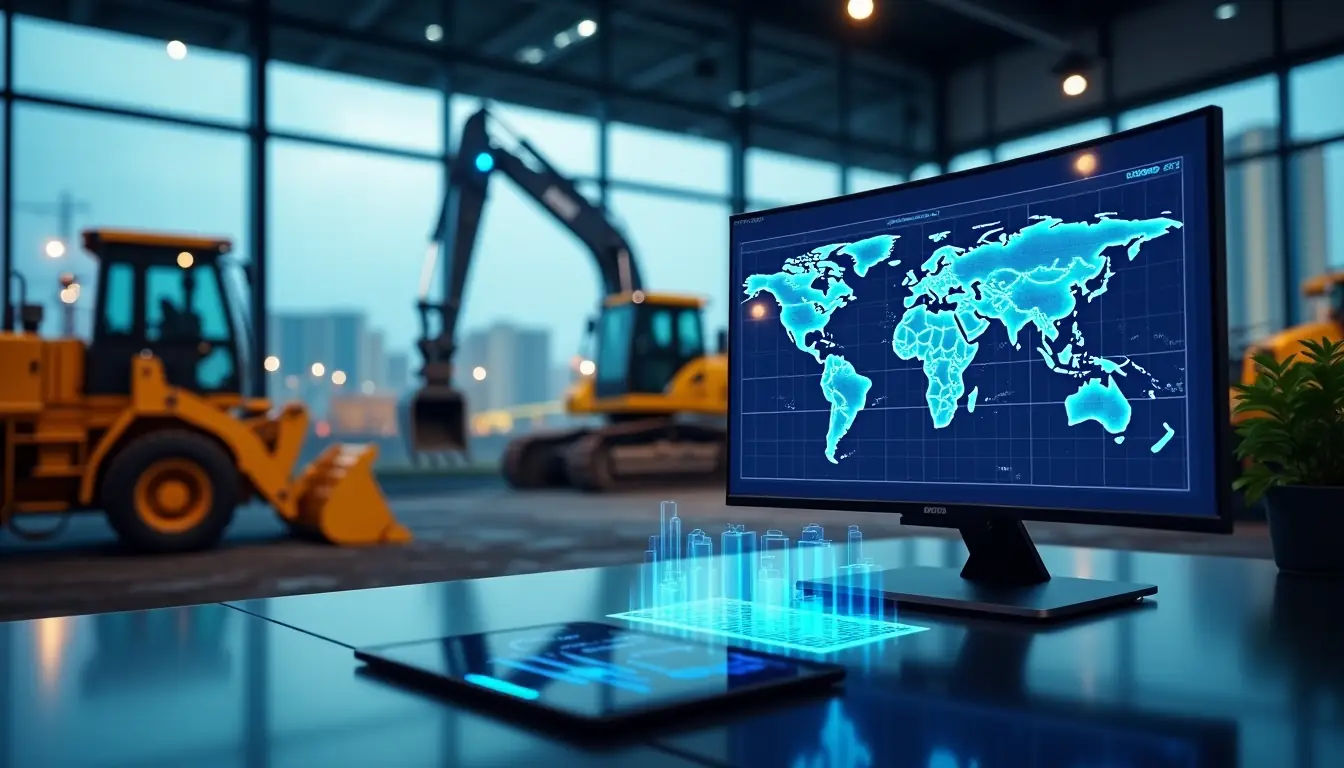
Essential Features Your Construction Equipment Inventory System Needs
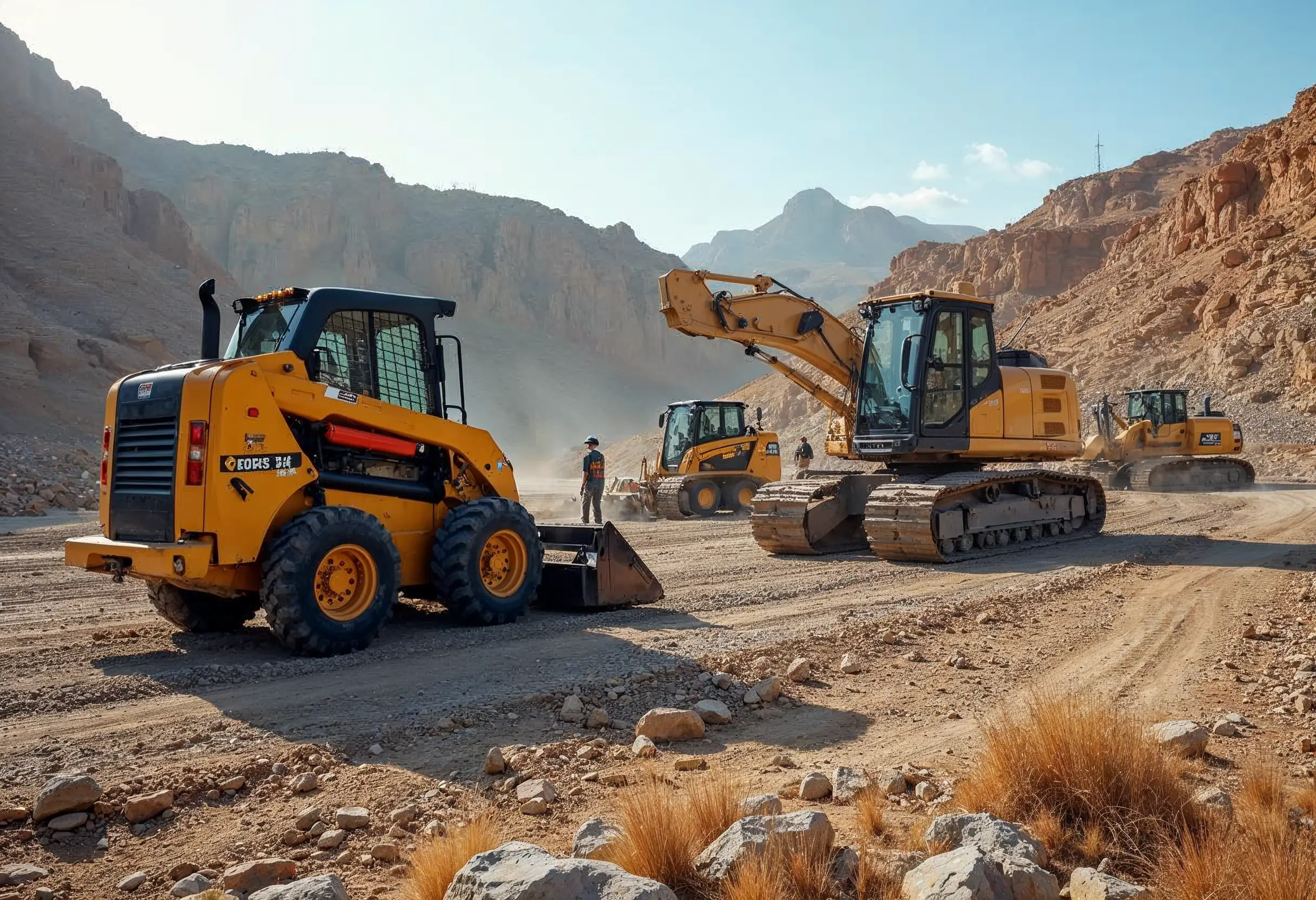
29 Quick Tips for Choosing Construction Equipment for Remote Locations
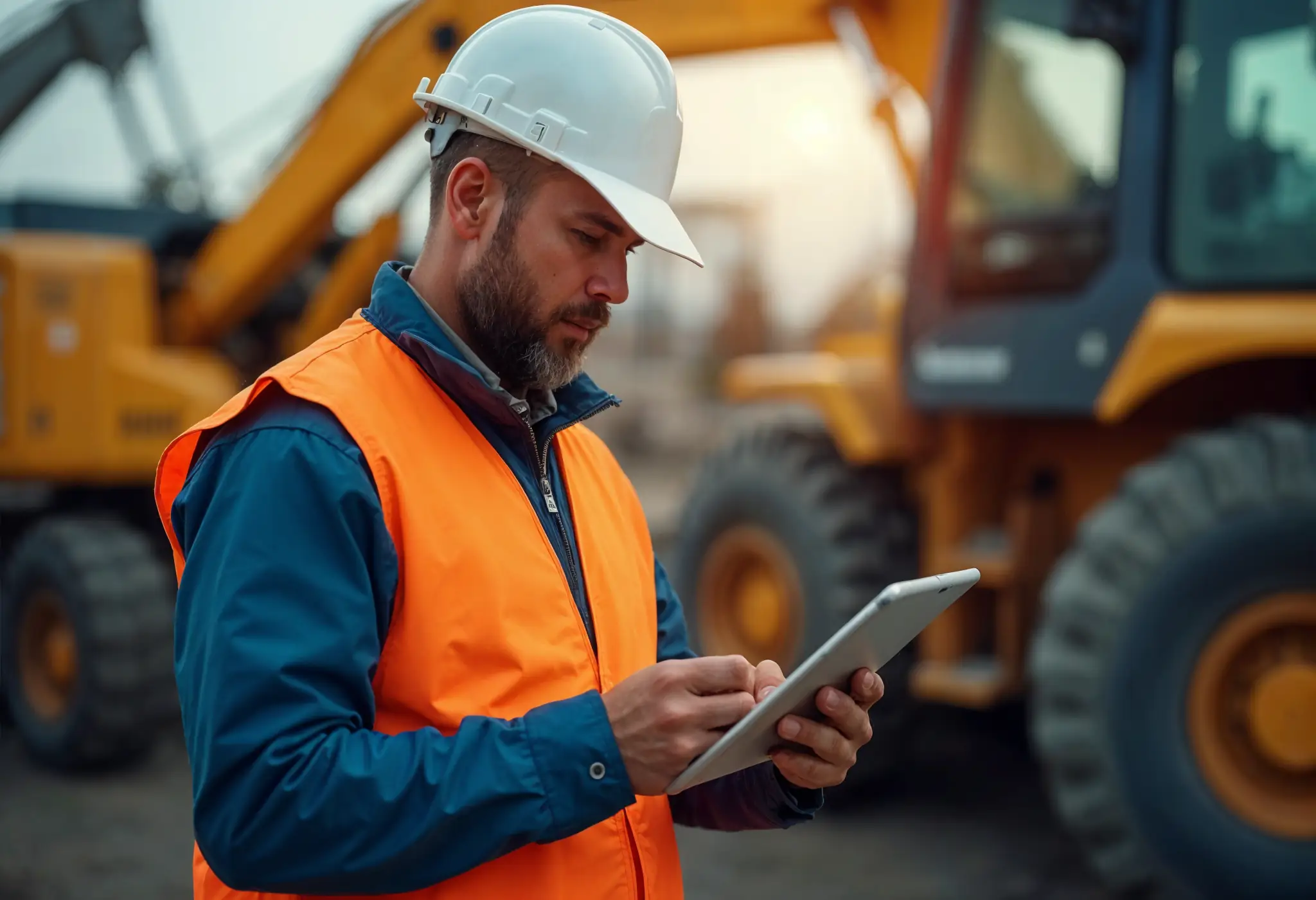
How to Select Construction Machinery with Optimal Equipment Maintenance in Mind
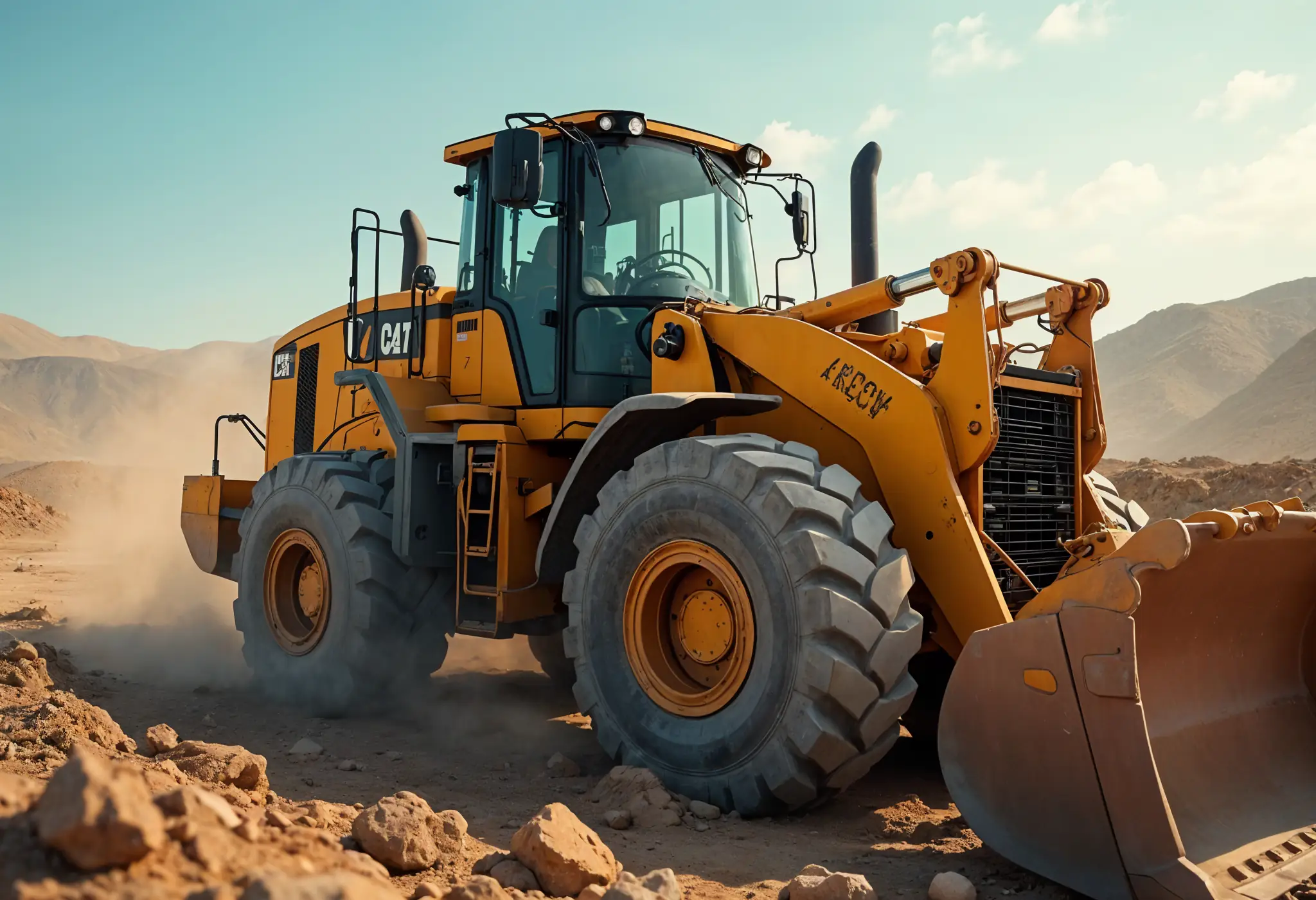
Top 25 Tips for Selecting Bulldozers for Construction Sites
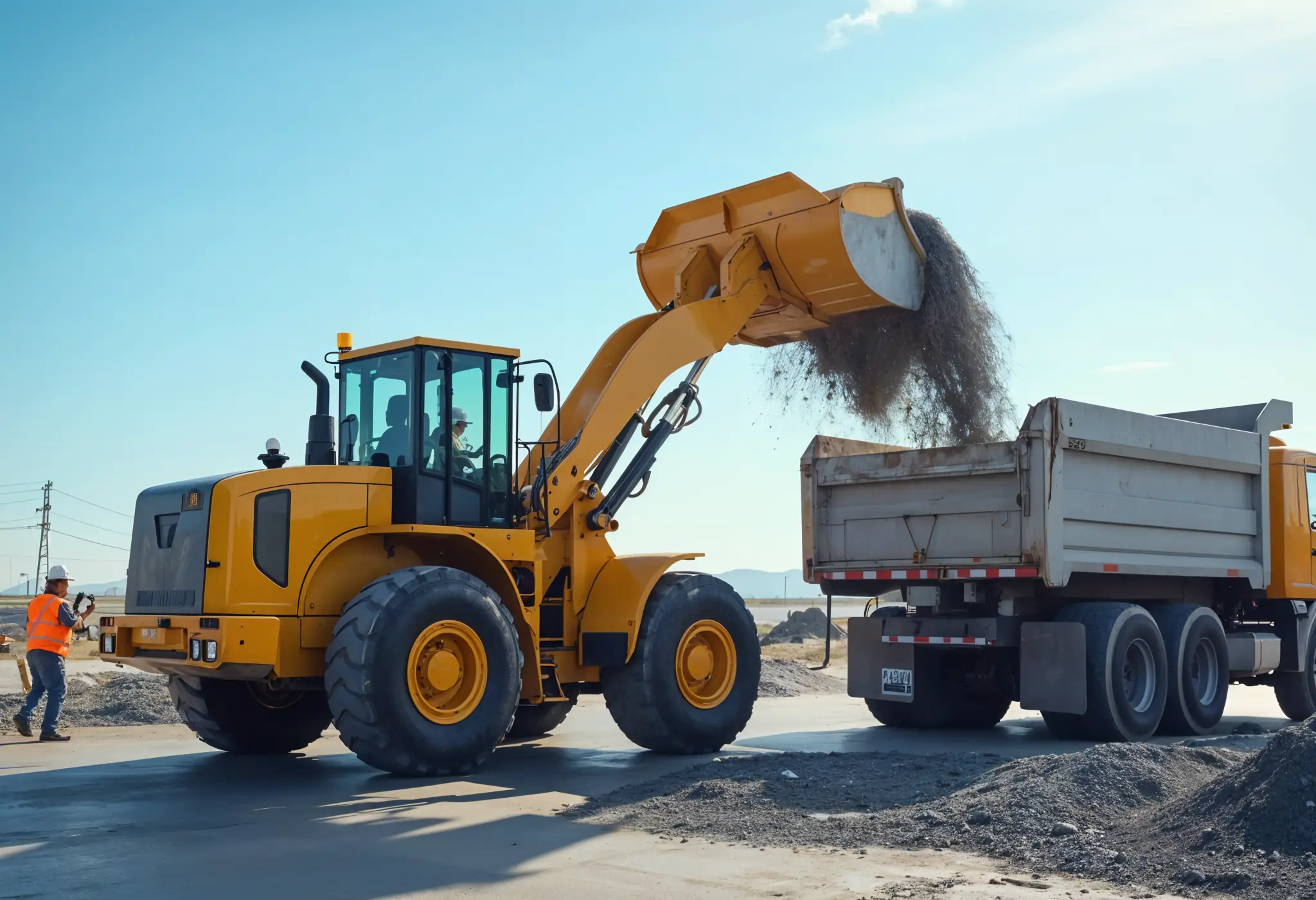
Which Construction Loader is Best for Your Project Needs?
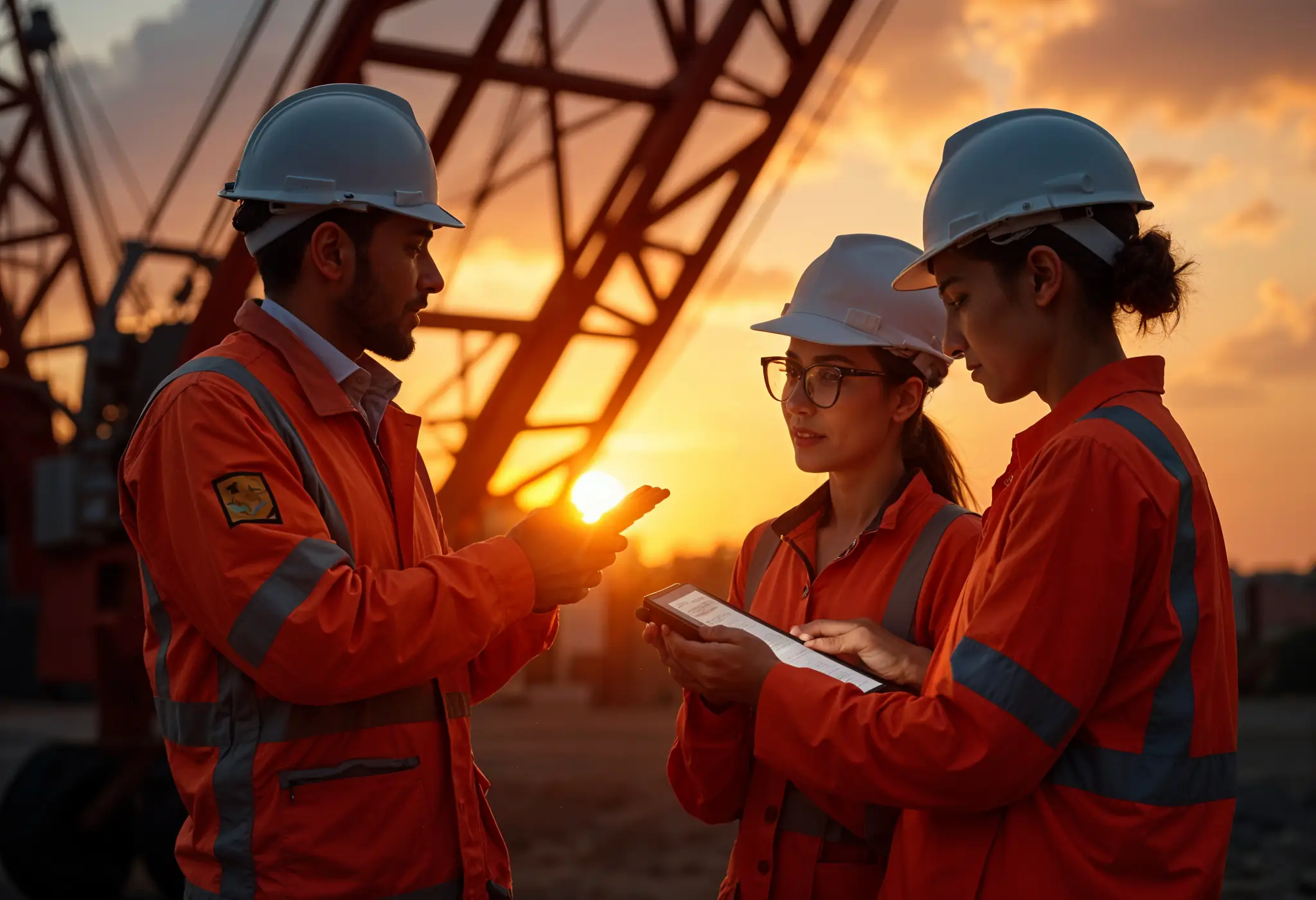
4 Key Steps to Form a Construction Machinery QC Team
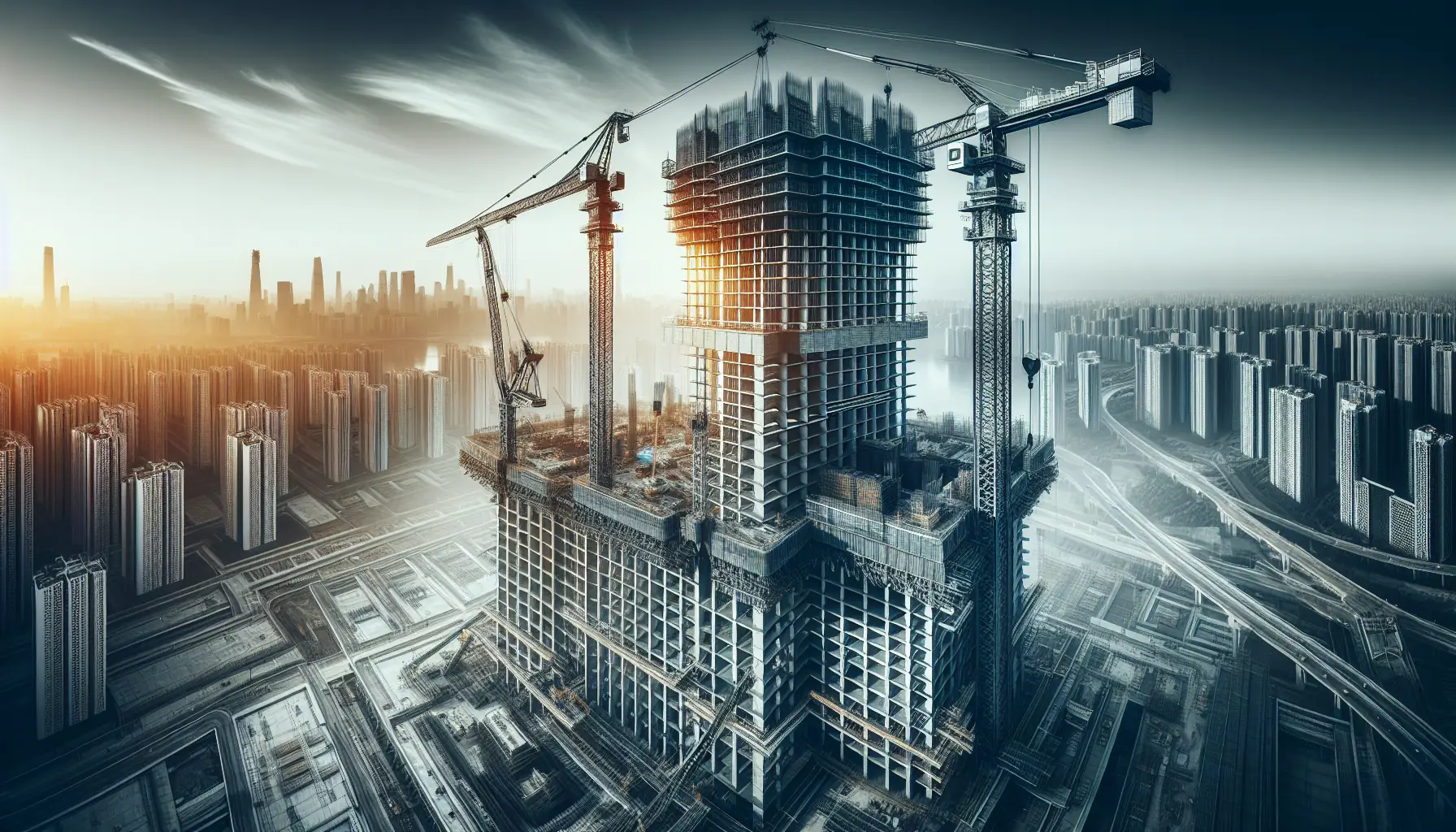
15 Essential Tips for Selecting the Perfect Crane for Construction
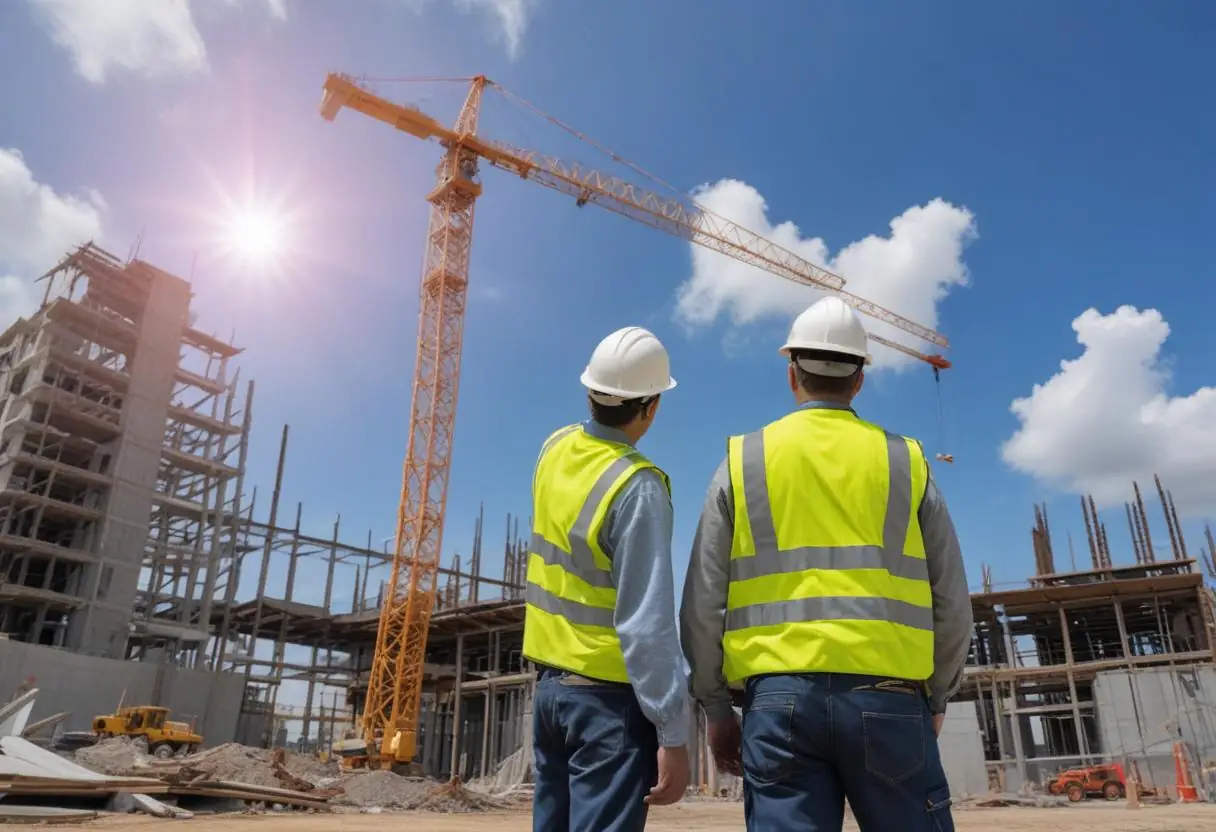
Maximize Savings: Multi-Purpose Construction Machinery for Lower Costs
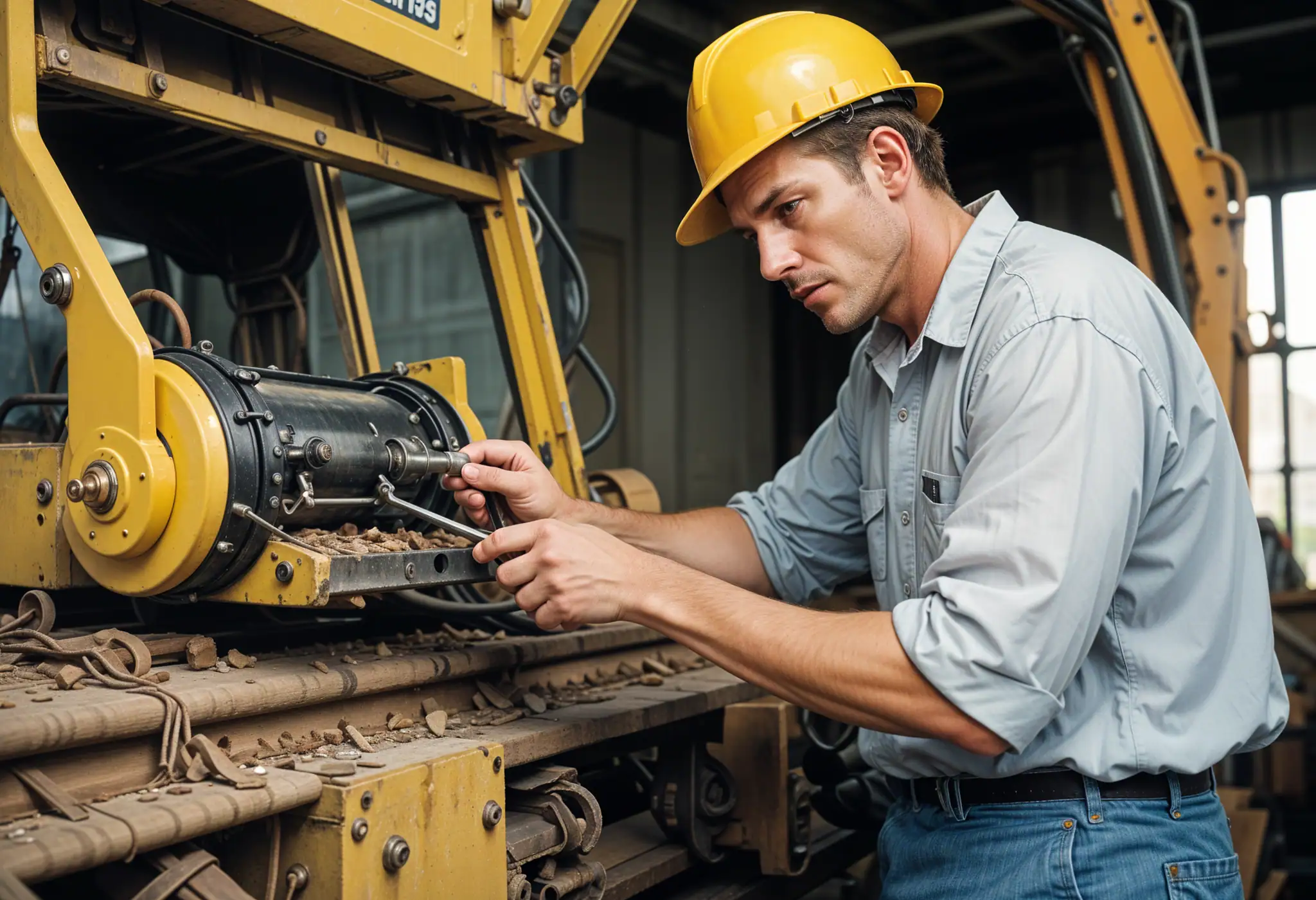
Affordable Heavy Equipment Parts: A Sourcing Guide
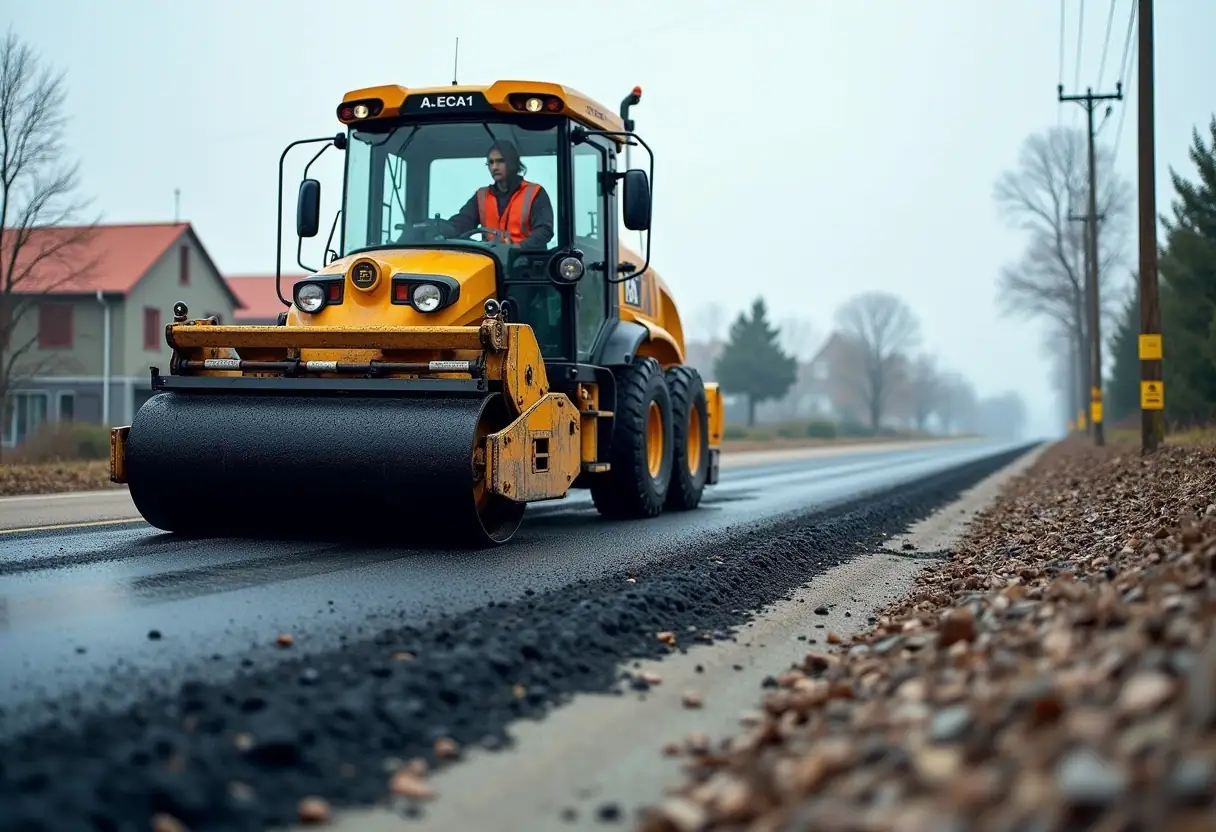
Choosing the Right Road Construction Equipment: A Complete Guide
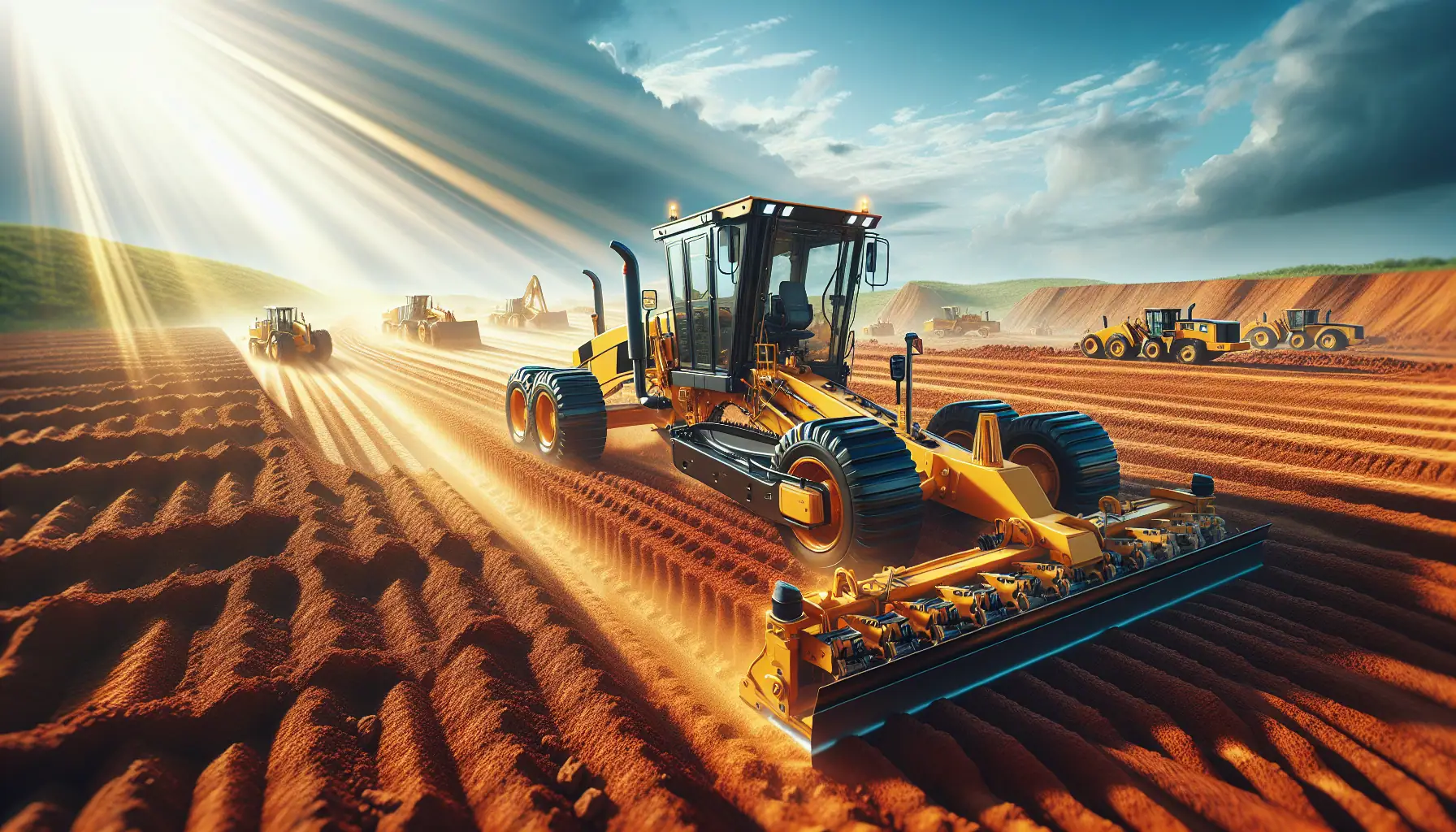
Motor Graders: Key Elements to Consider for Optimal Selection
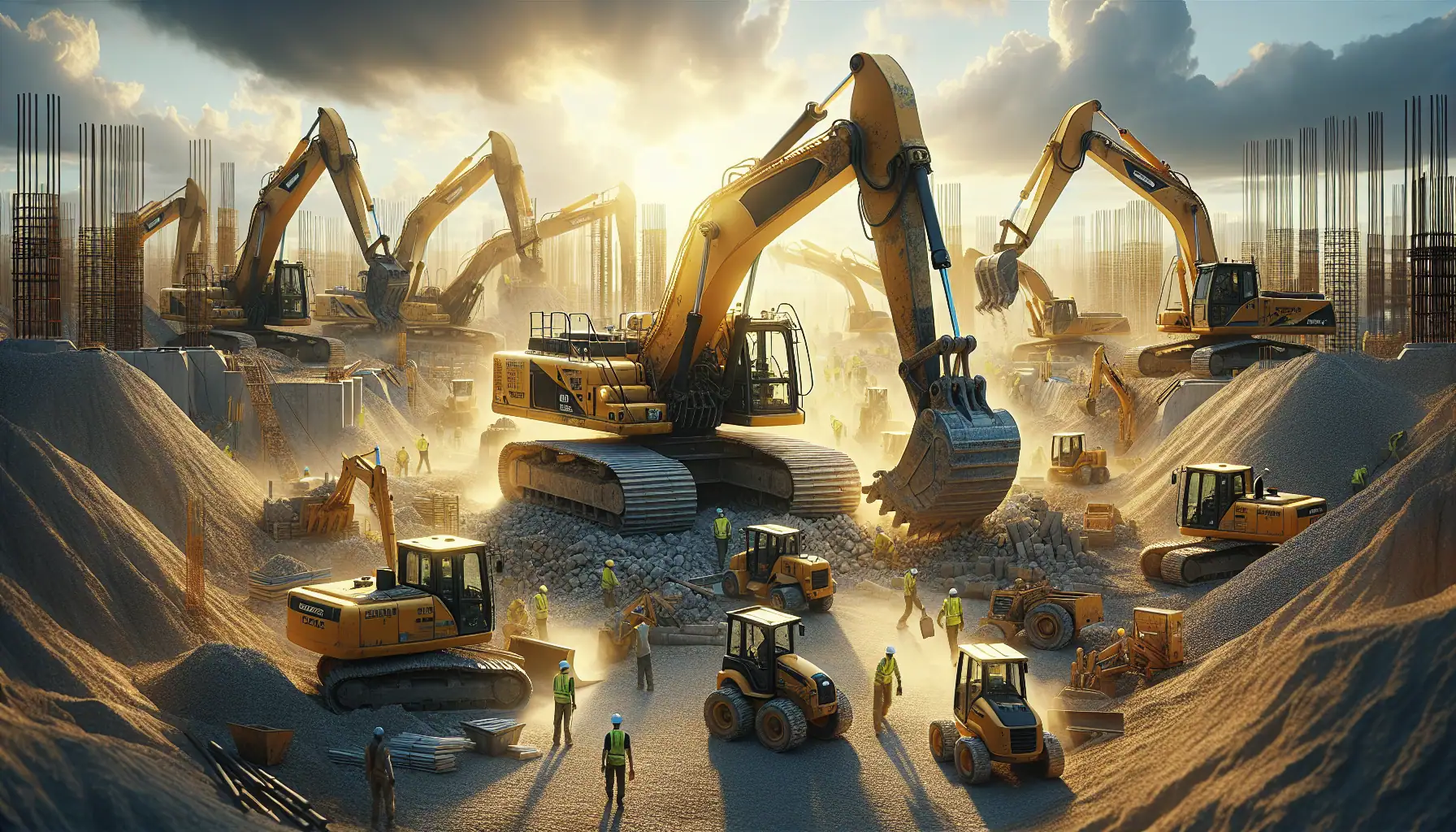
A Detailed Guide to Choosing Excavators for Construction Work
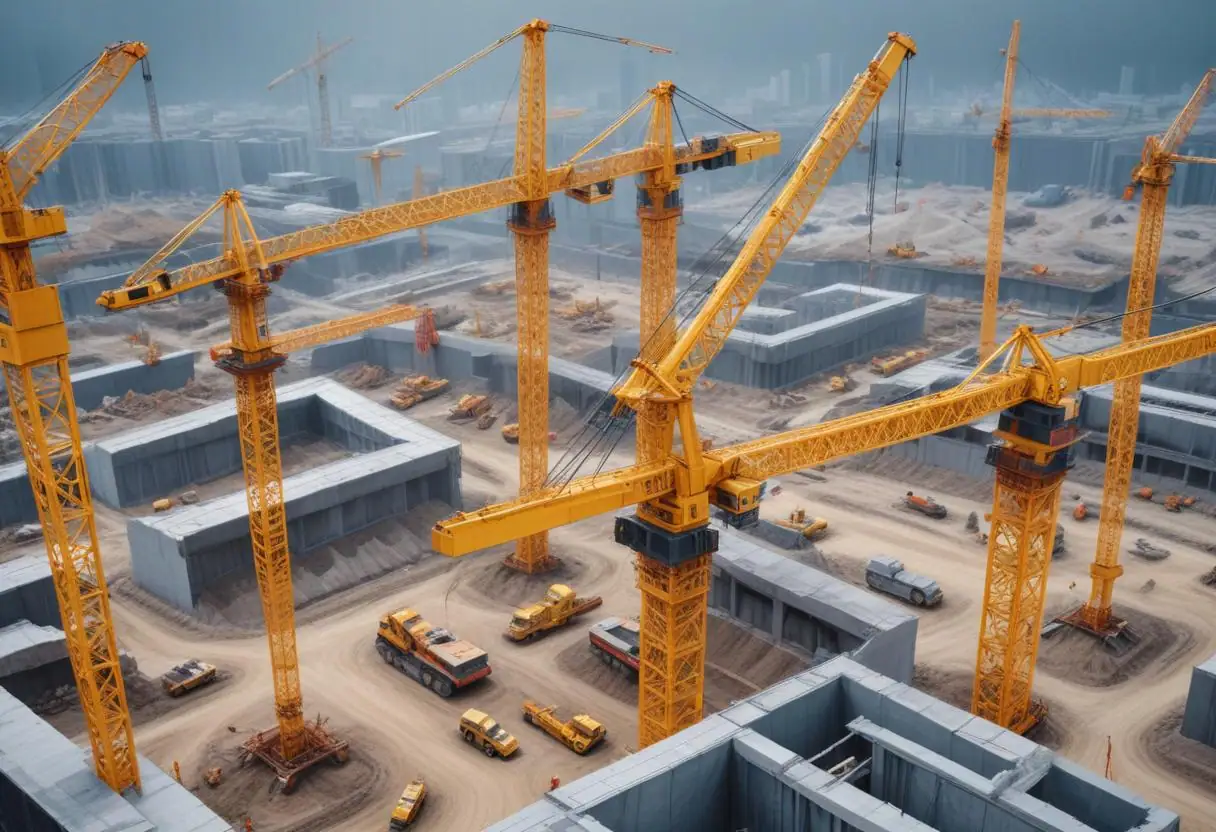
Top Tips for Choosing Cranes for Construction Projects
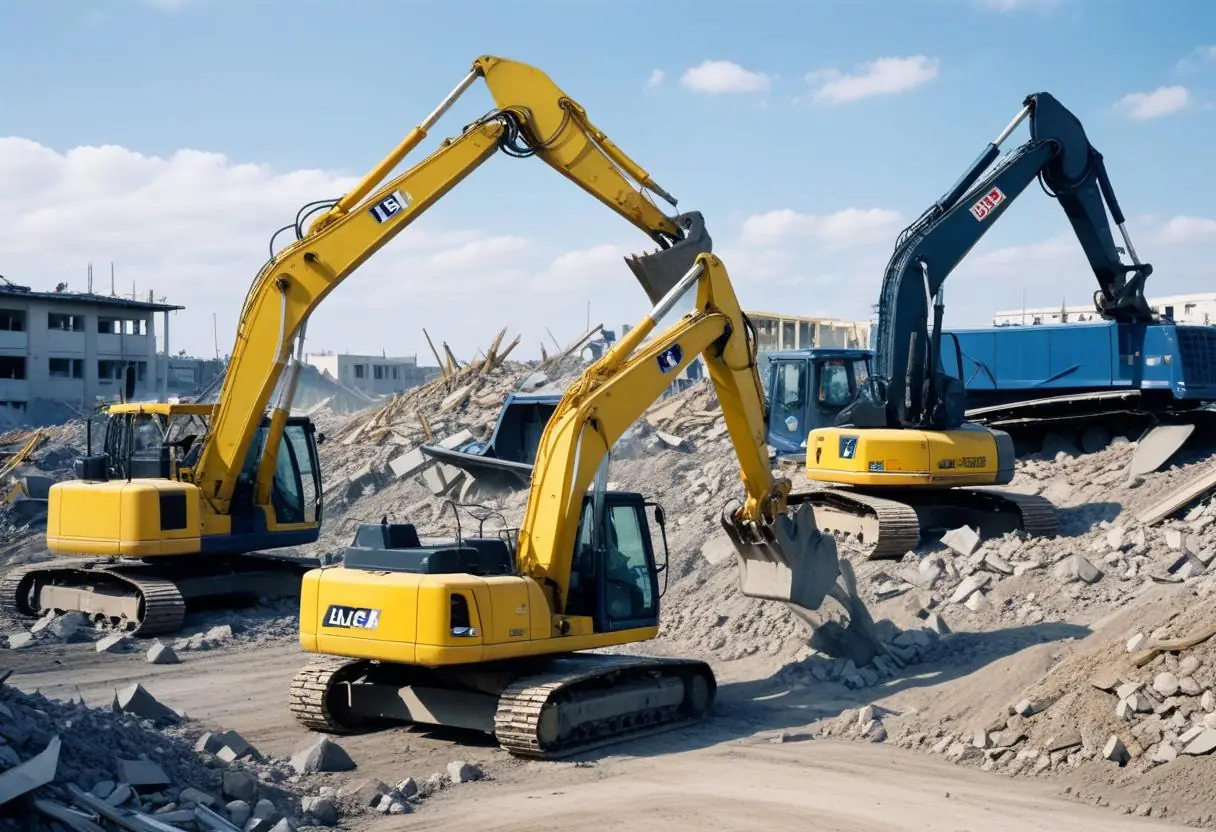
5 Top-Rated Demolition Machines for Construction Professionals
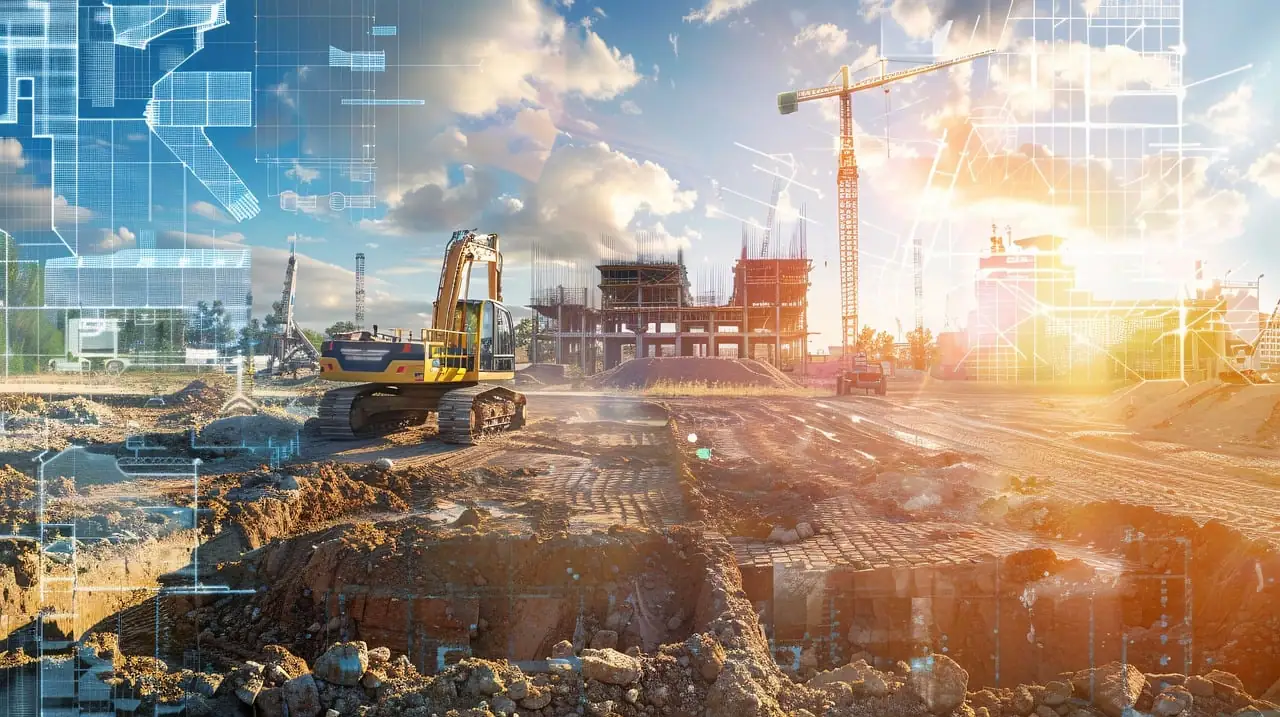
Expert Tips on Choosing Earthmoving Equipment for Large Projects
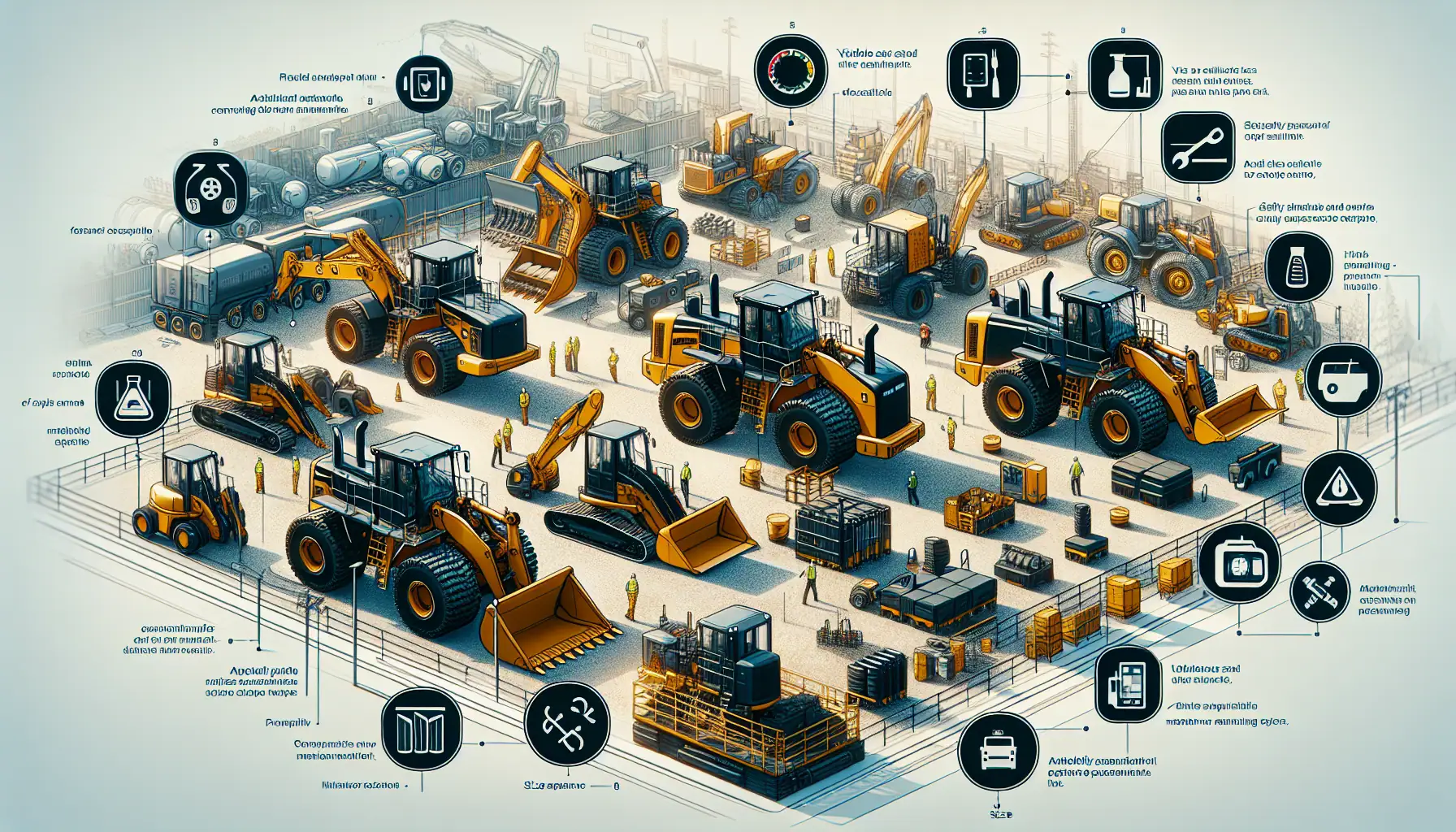
Top Functional Criteria for Selecting Heavy Construction Equipment
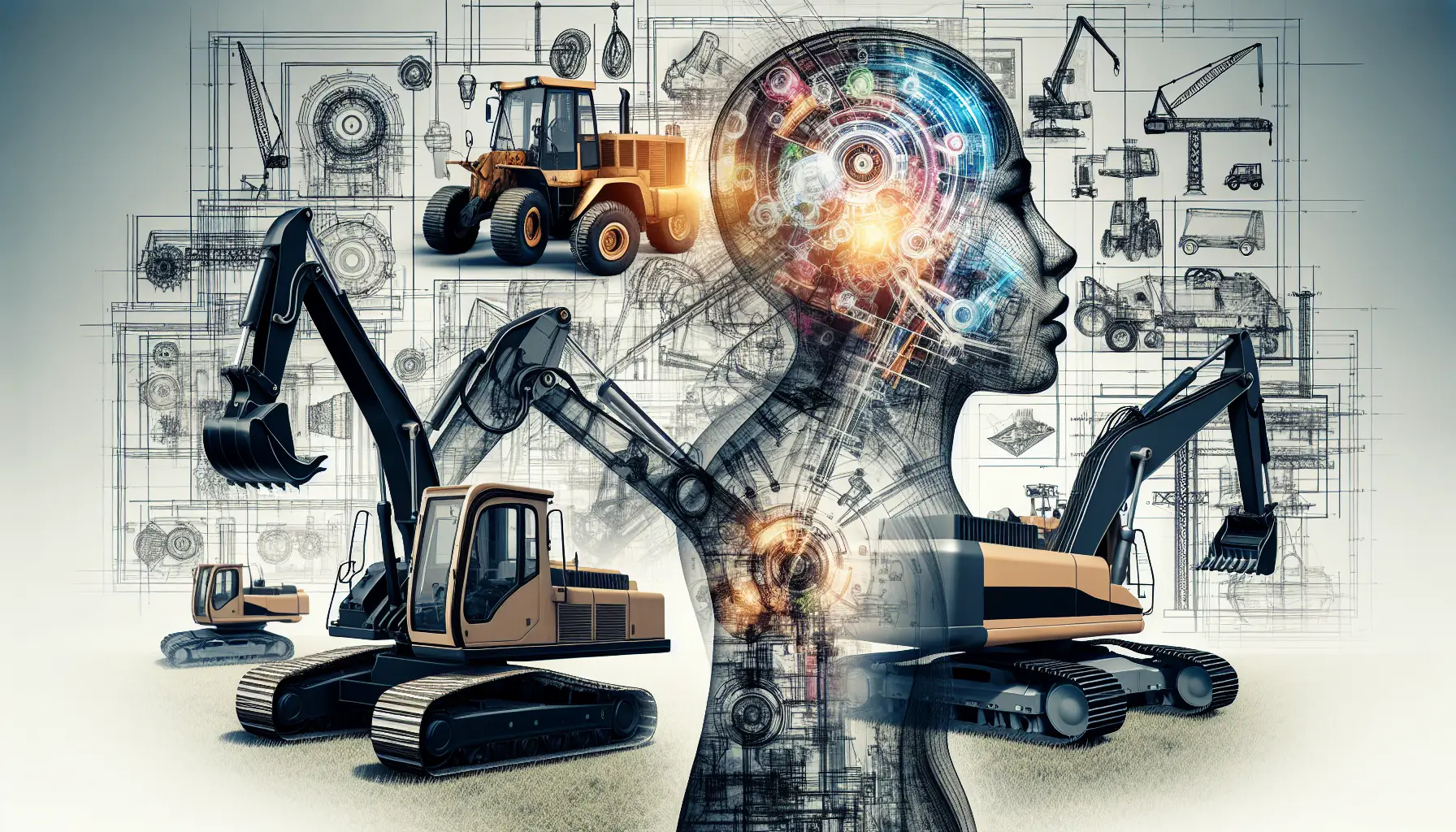
Construction Machinery: Detailed Guide to Equipment Specifications
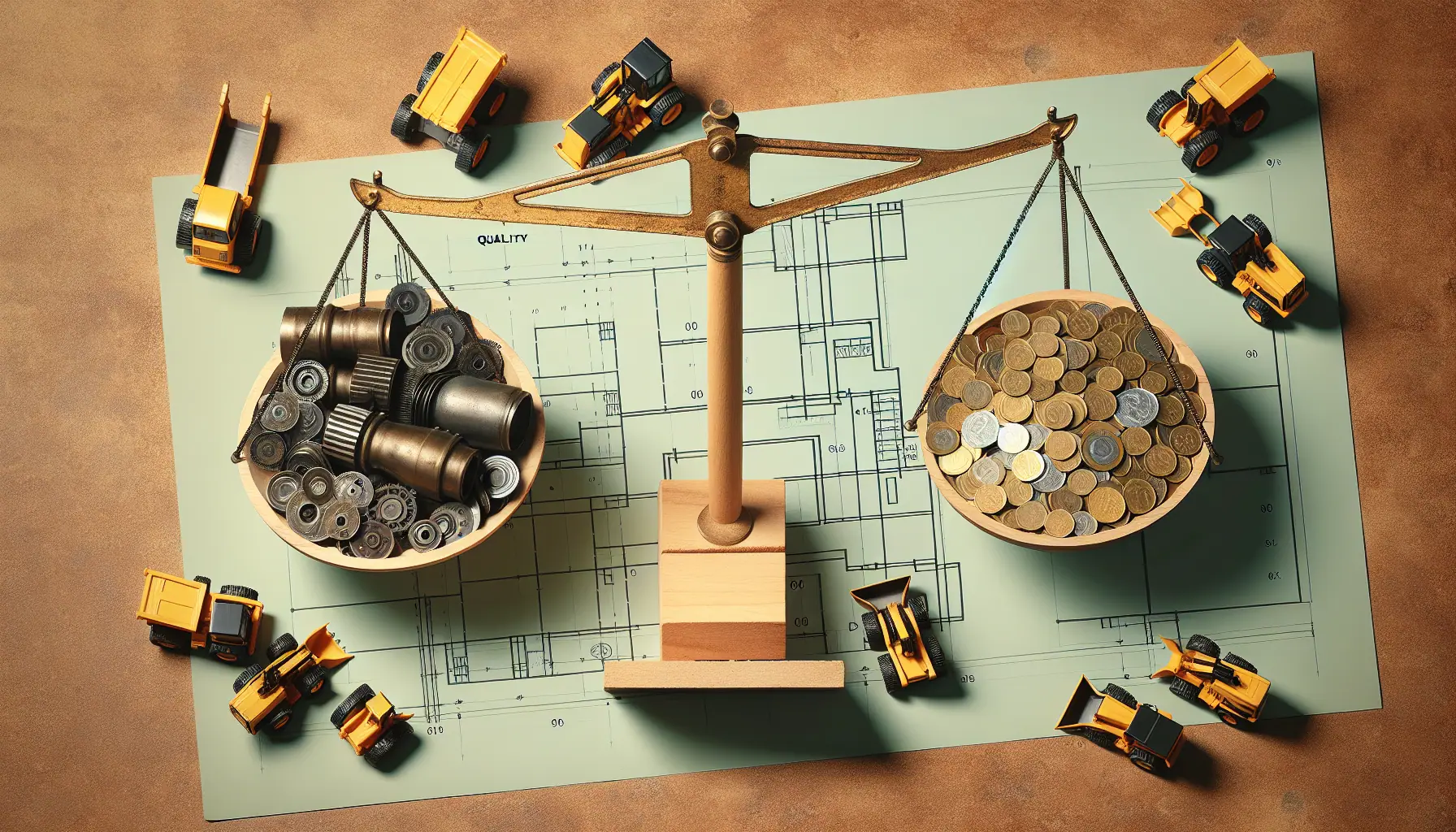
Heavy Machinery Prices: Key Factors in Cost and Quality Balance
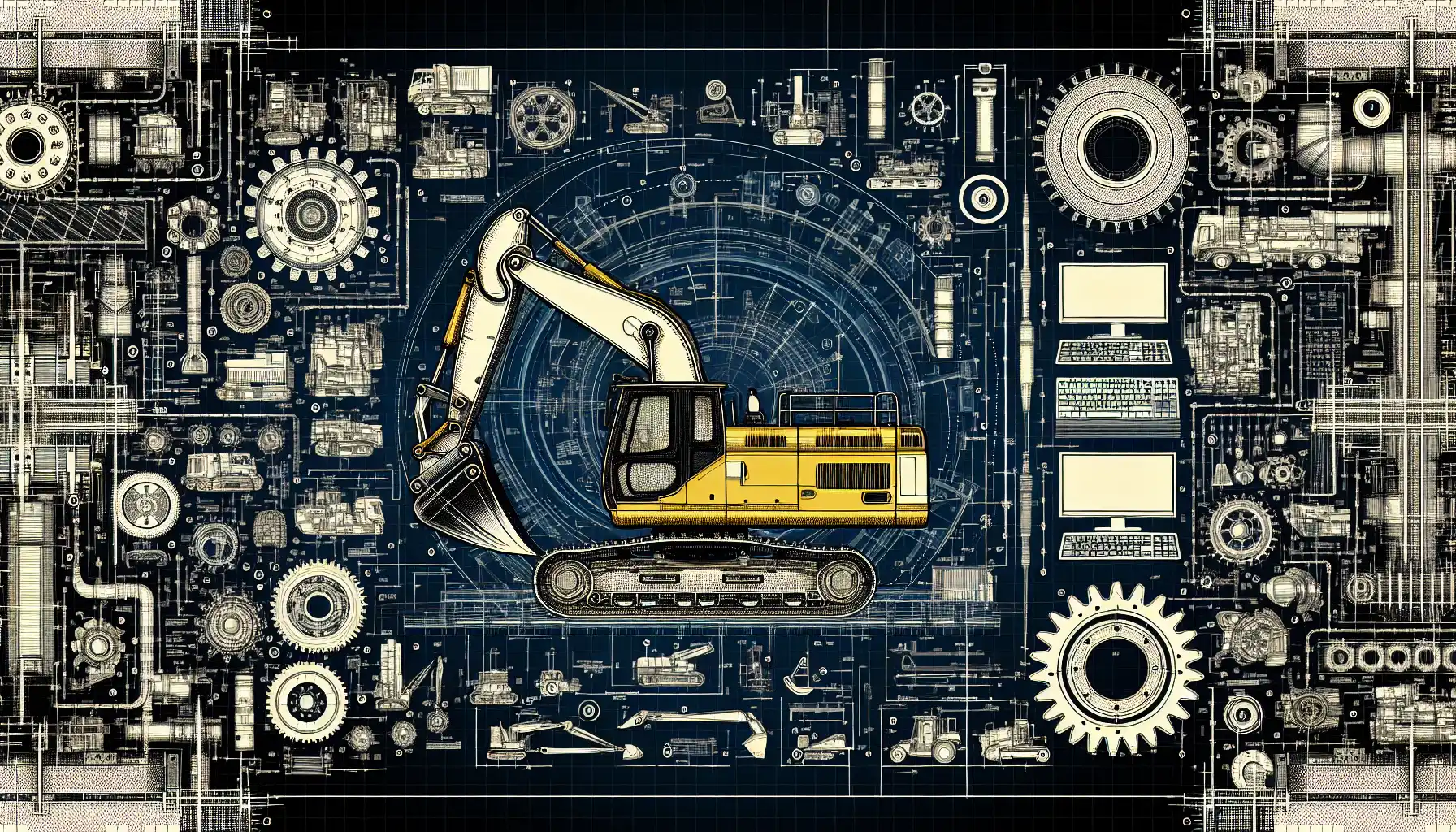
Best Construction Heavy Equipment Brands: Pros and Cons
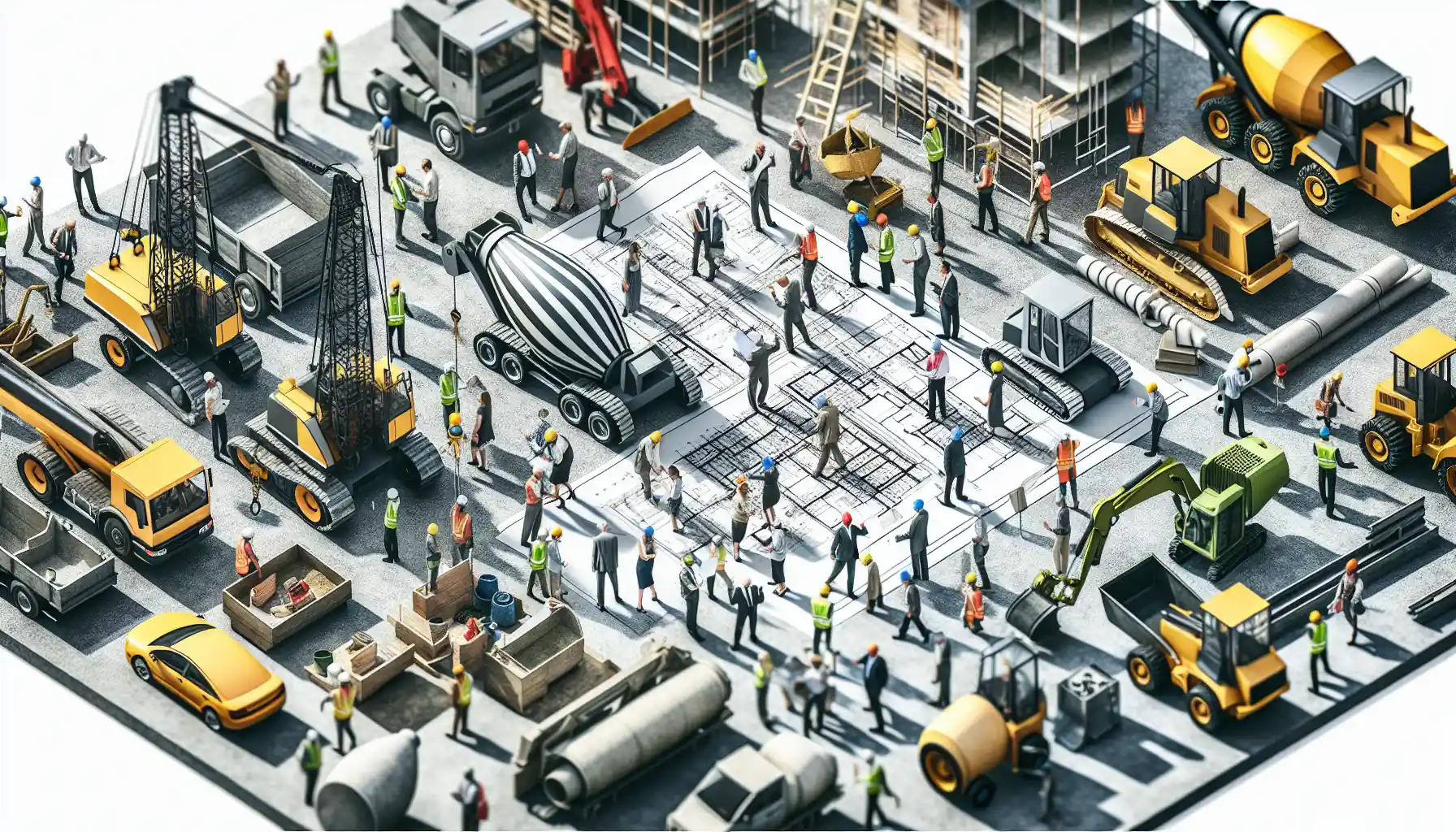
Construction Site Equipment: How to Determine Your Requirements
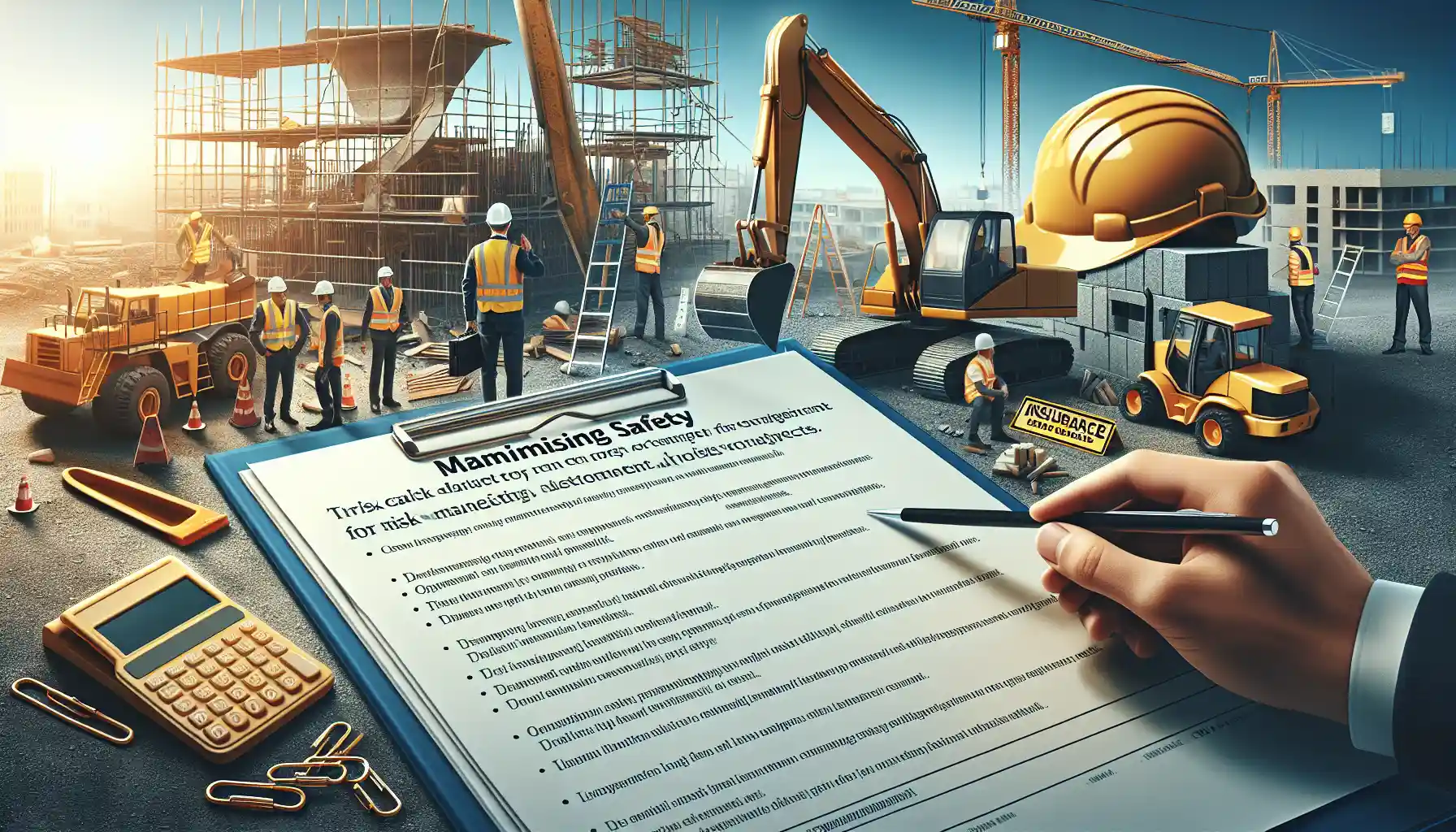
Maximizing Safety: Risk Management for Construction Projects
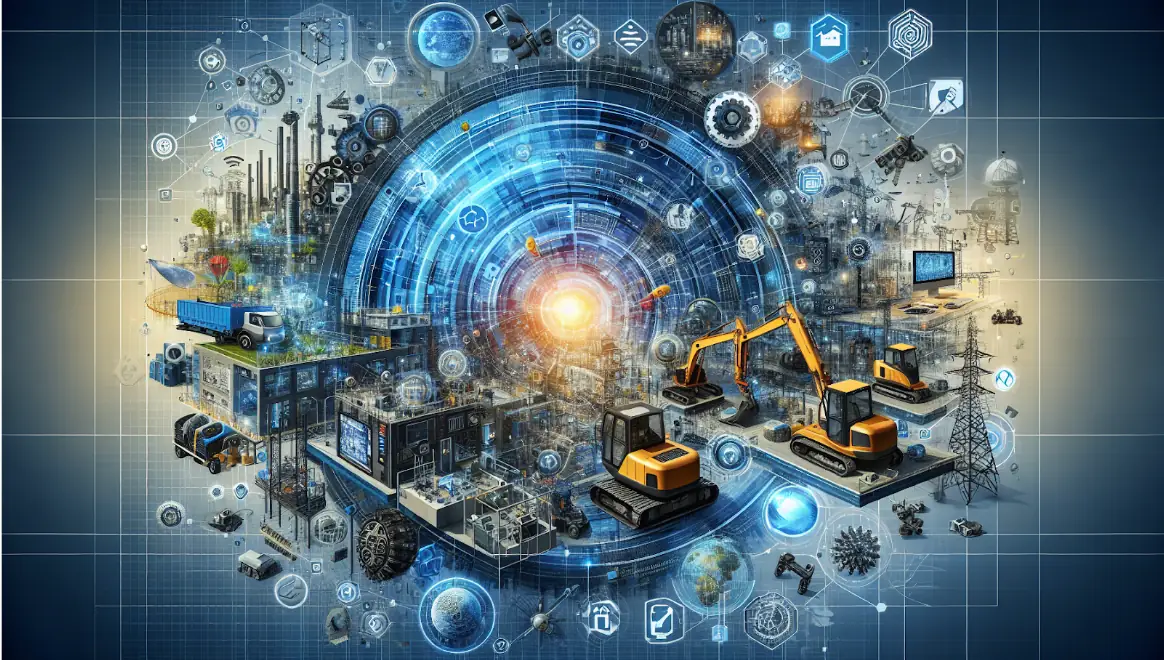
Innovations in Construction: Transforming Machinery and Equipment
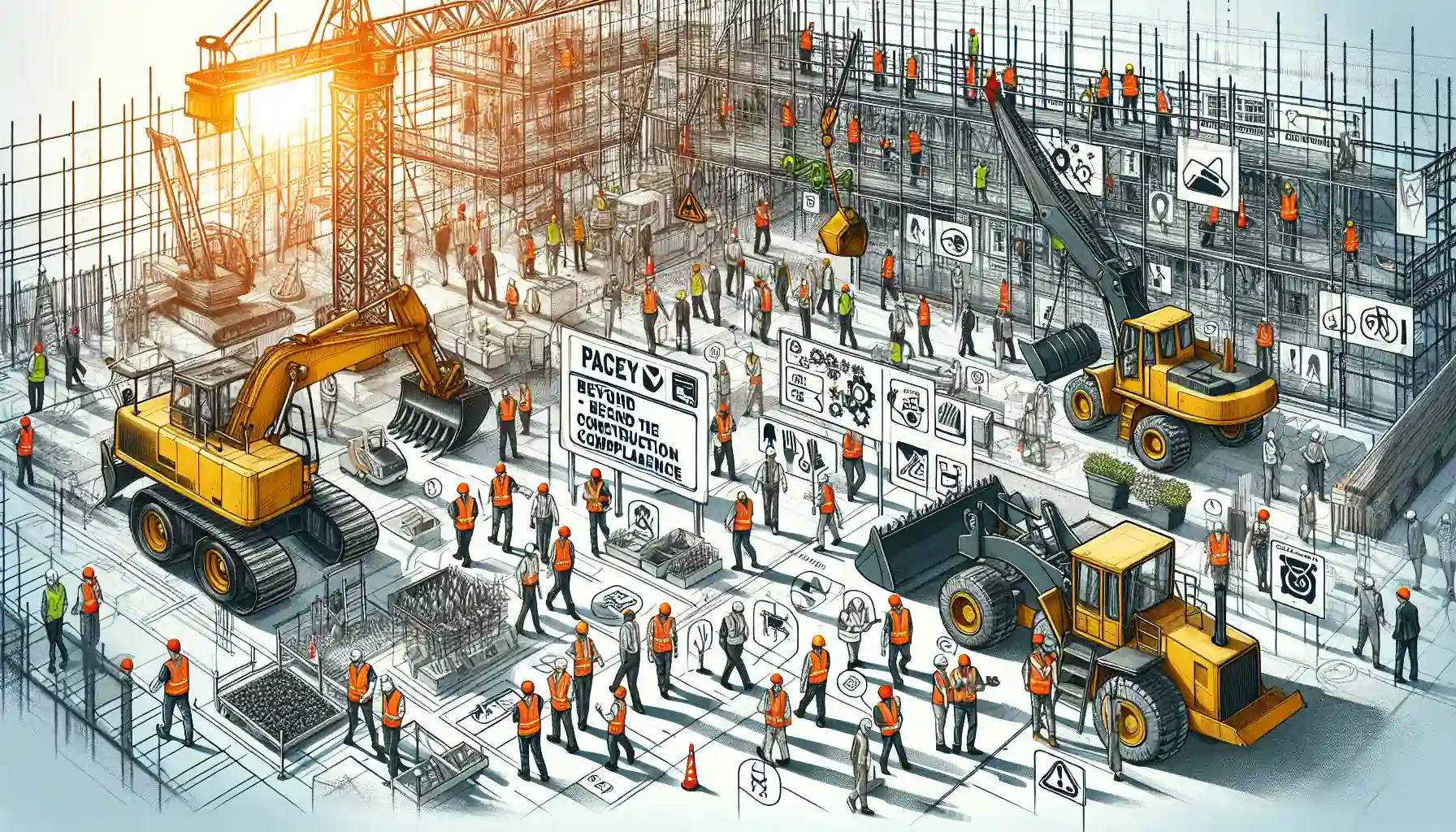
Heavy Equipment Safety: Beyond the Basics in Construction Compliance
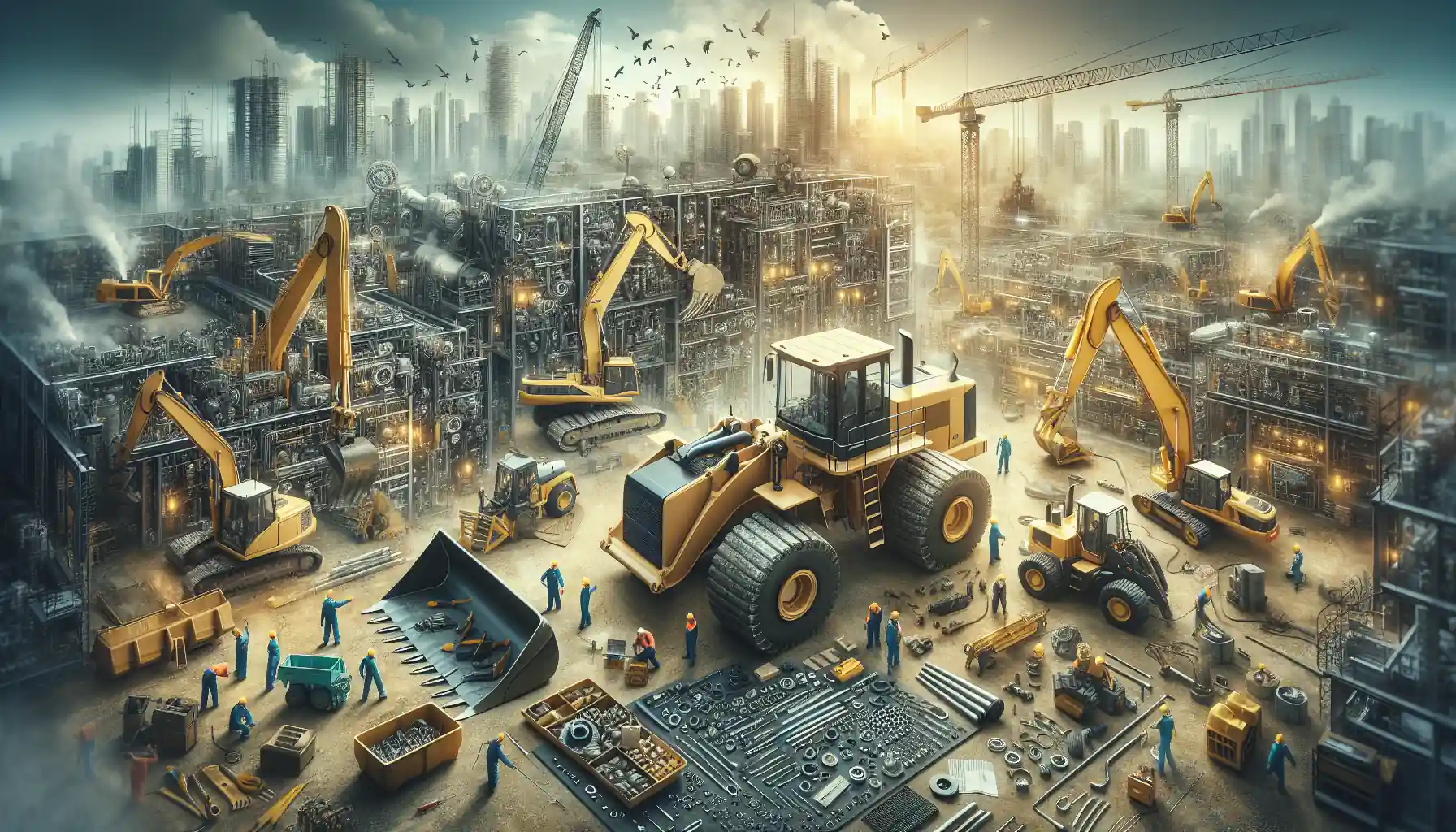
The Essential Handbook for Construction Equipment Repair and Maintenance
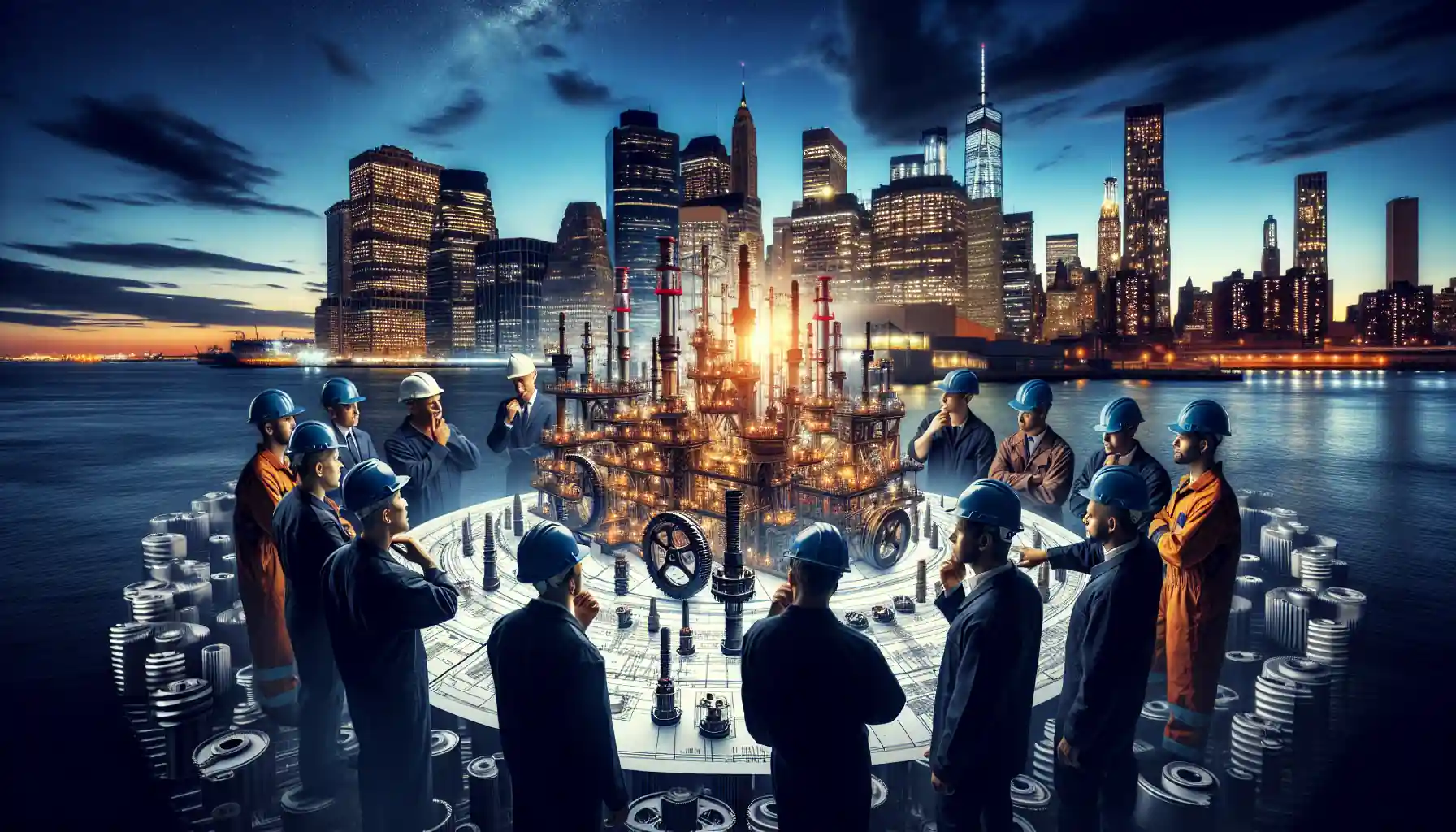
How to Efficiently Source Oil and Gas Machinery Parts in NYC
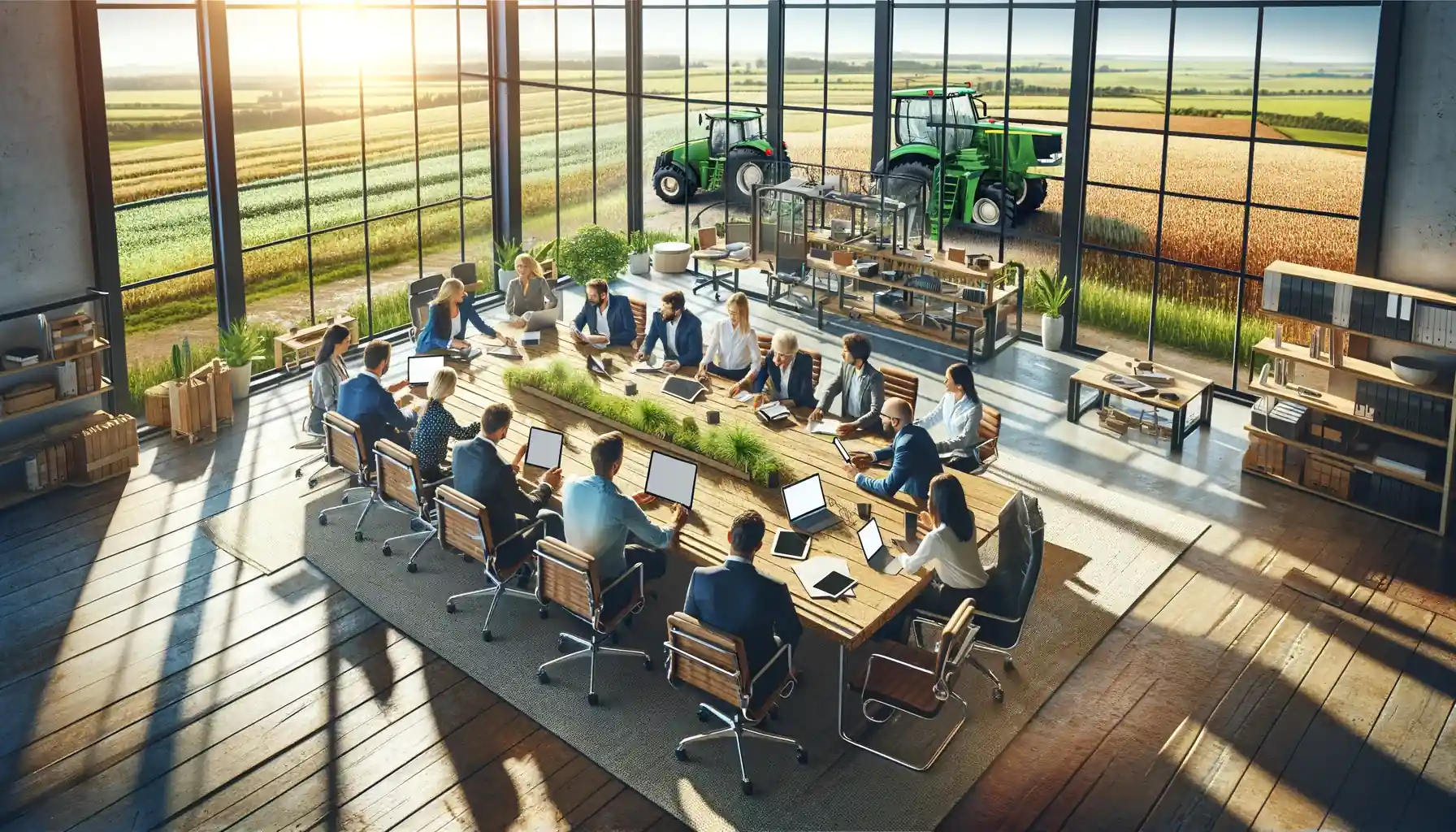
Essential Guide to Sourcing Agriculture Equipment Parts
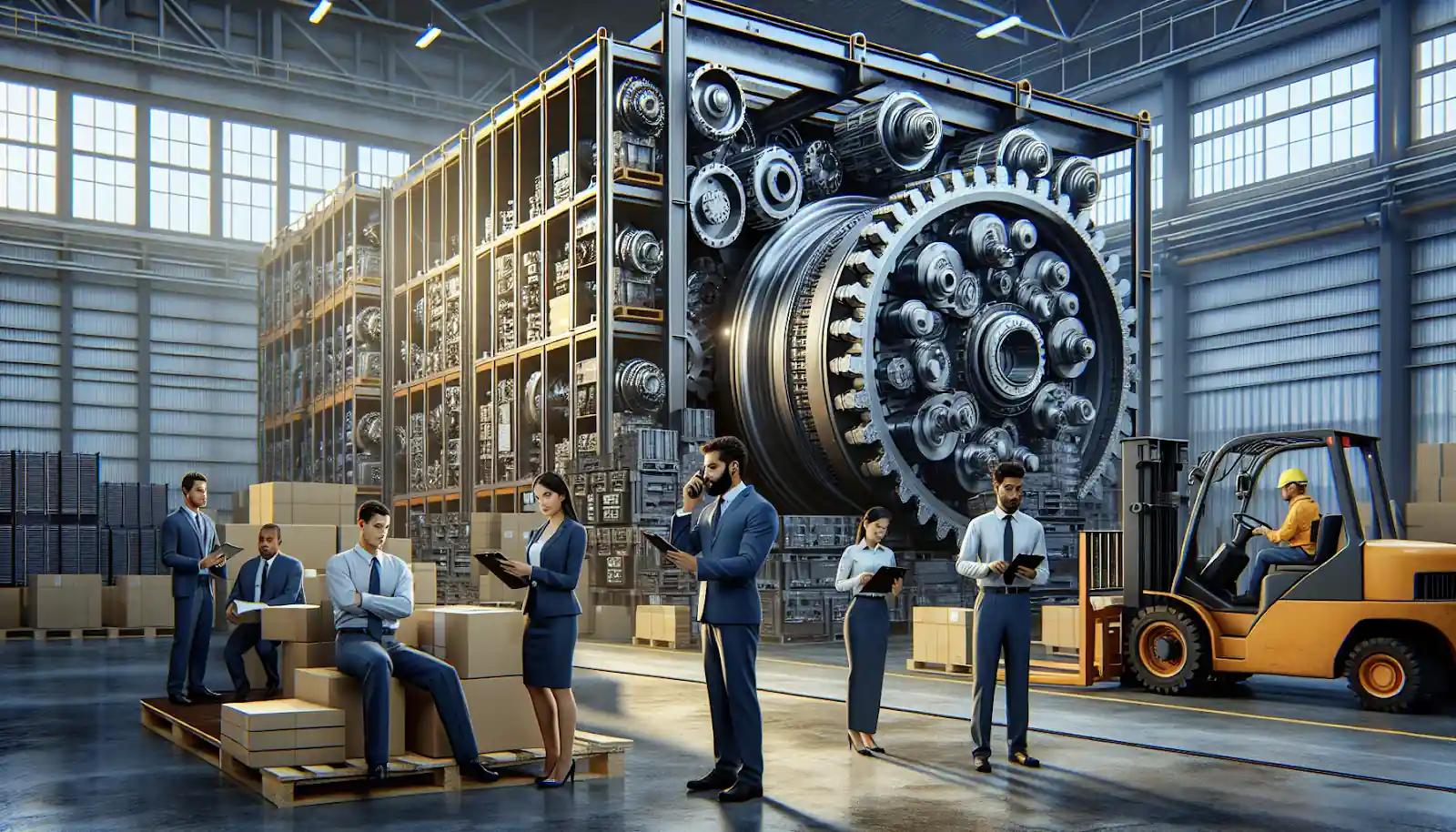
How to Source Mining Machinery Parts: Tips and Strategies
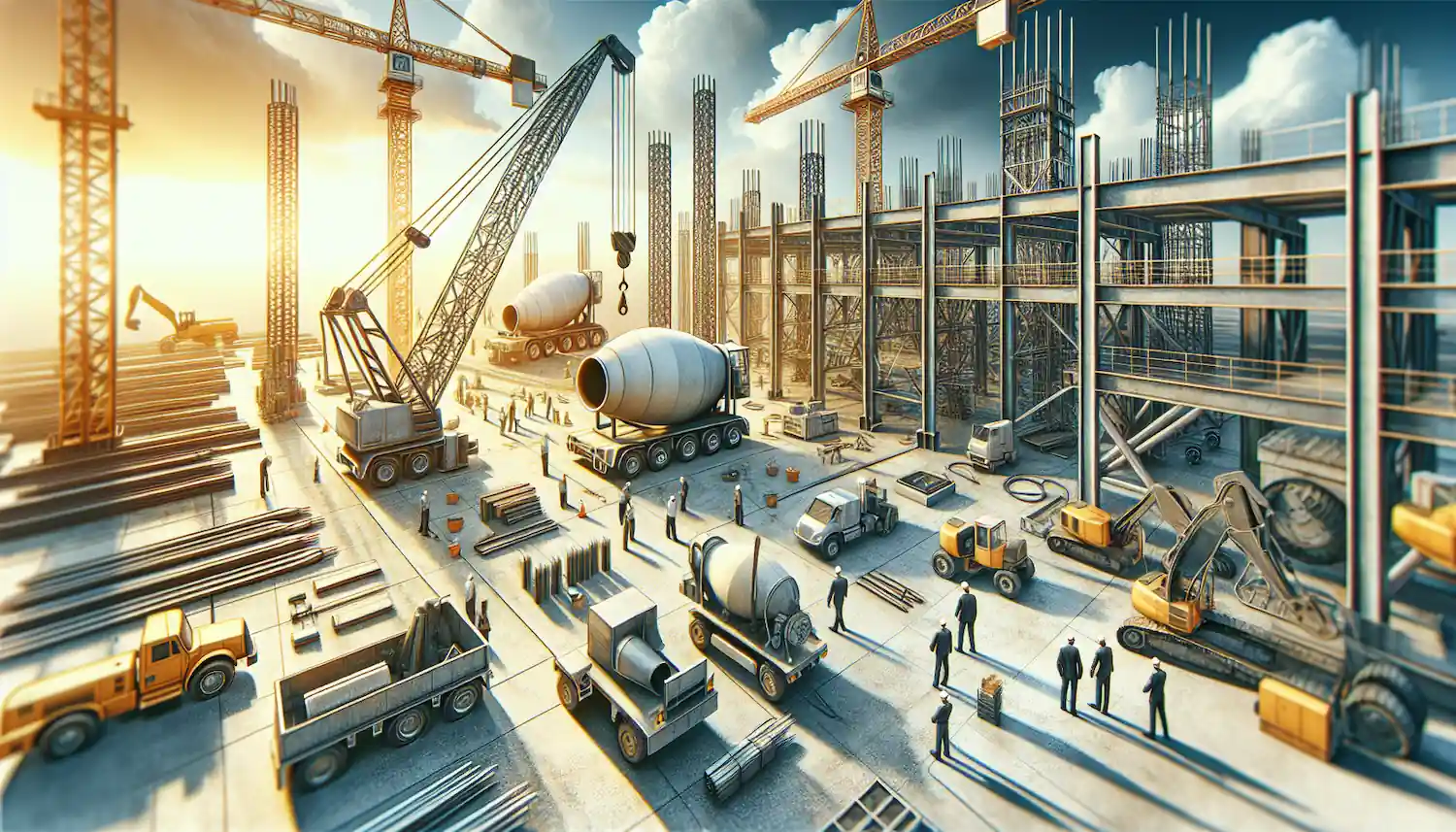