How to Extend Equipment Life Expectancy with Regular Maintenance
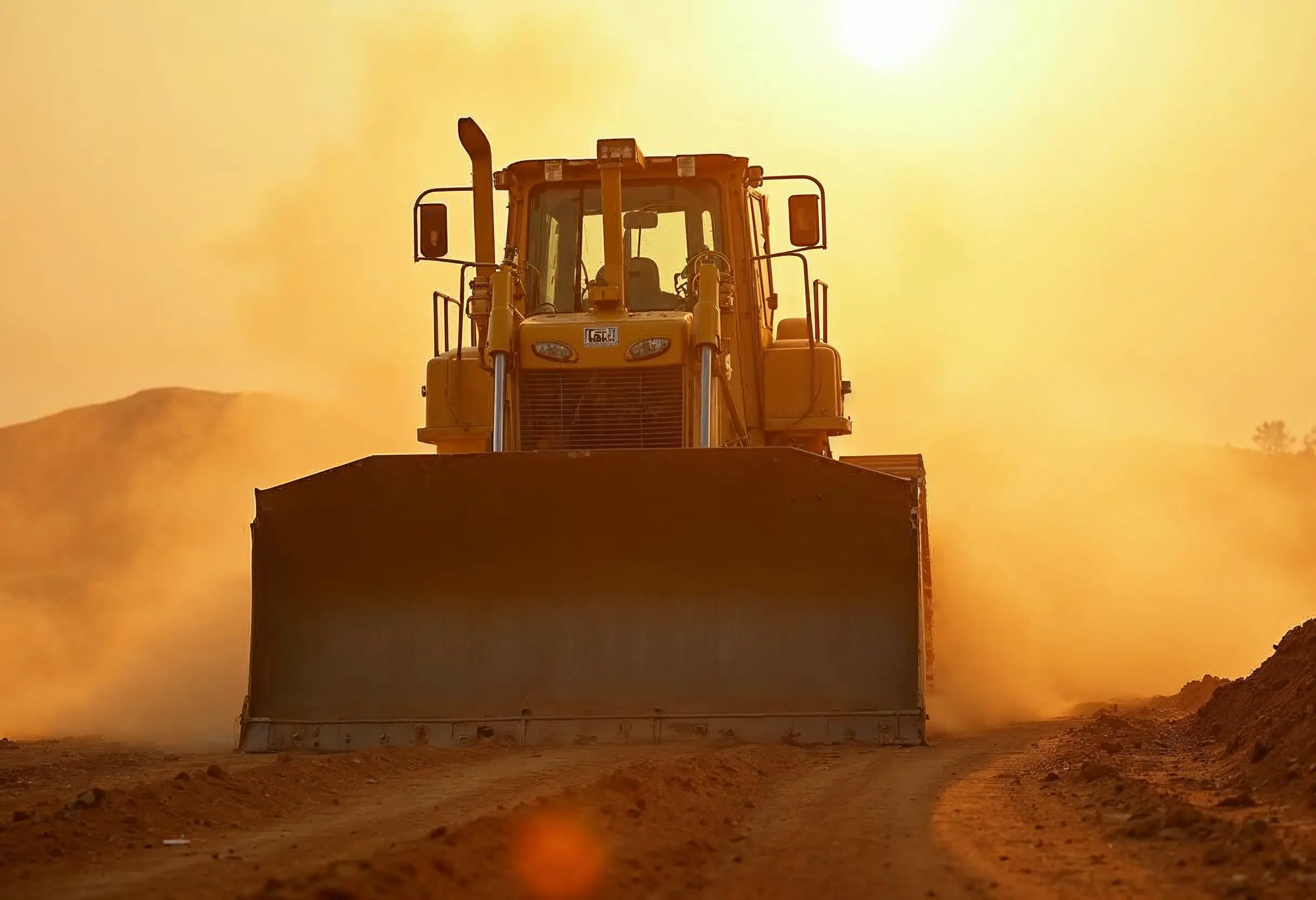
Studies show that effective preventive maintenance can extend your equipment life span by 20-30%, while poor maintenance practices can slash it in half. Yet many construction firms still treat maintenance as an afterthought rather than a strategic investment in operational efficiency.
Your heavy equipment represents a significant investment in your business. Through systematic maintenance of construction equipment and preventive maintenance strategies, you can protect this investment and maximize its return. The right maintenance approach doesn't just extend equipment lifespan—it reduces operating costs, prevents unexpected breakdowns, and improves overall site productivity and safety.
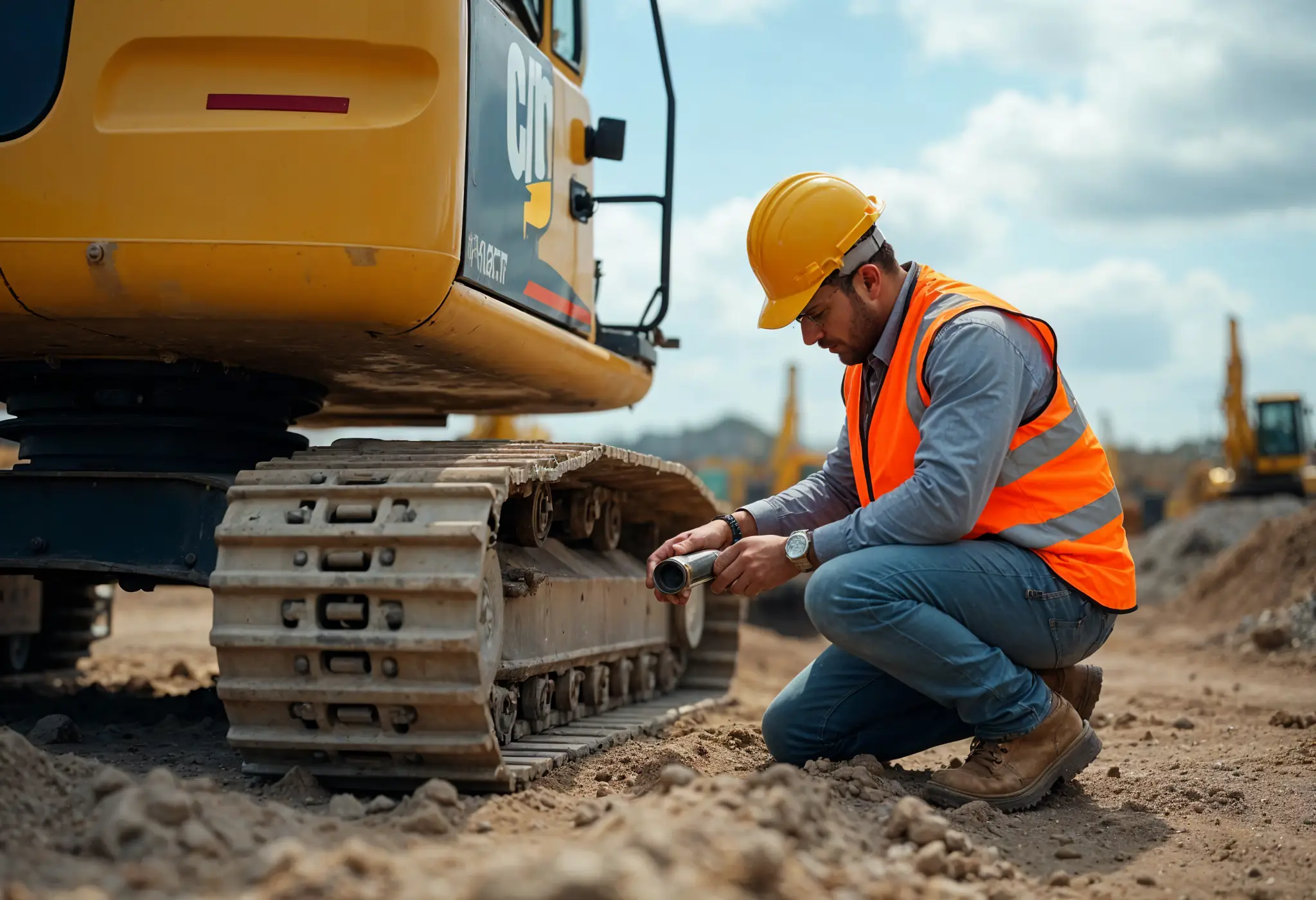
In this guide, you'll discover proven strategies to extend your equipment's service life, from essential maintenance procedures to cutting-edge monitoring technologies. Let's explore how to make your equipment last longer while performing better.
Essential Components of Equipment Care
Understanding your equipment's critical systems is fundamental to extending its service life. Studies show that wear rates can accelerate up to 10,000 times faster than intended when critical systems are neglected.
Critical Systems Overview
Your equipment's vital systems require focused attention to maintain optimal performance and reliability. Key areas include:
- Hydraulic systems and fluid management
- Power transmission components
- Electrical and control systems
- Structural integrity points
- Cooling and ventilation systems
Wear Points Identification
Abrasion stands out as the most frequent and rapid wear mechanism affecting your machinery's health. When dust particles are larger than the clearances between moving parts, they can embed into softer surfaces and create grooves in harder metal components. Your maintenance program should prioritize three critical factors: threshold hardness of contaminants, particle size, and concentration levels.
Environmental Impact Factors
Environmental conditions significantly influence your equipment's longevity. Exposure to extreme temperatures, abrasive materials, and irregular surfaces takes a considerable toll on machinery performance. Indoor equipment typically experiences a longer lifespan compared to outdoor equivalents. High humidity levels can lead to oxidation of components, causing them to heat up and deteriorate surrounding insulation.
Proper maintenance becomes even more critical when equipment operates in challenging environments. Studies indicate that well-performed preventive maintenance is one of the most important factors in maximizing equipment life.
Need expert guidance on protecting your equipment's critical systems? Contact MCH Parts for a free sourcing consultation and discover how to extend your machinery's service life.
Modern Maintenance Technologies
Today's maintenance technologies offer powerful tools to extend your equipment life expectancy. Recent studies show that 66% of companies now use computerized maintenance management systems (CMMS) to optimize their equipment care and improve equipment uptime.
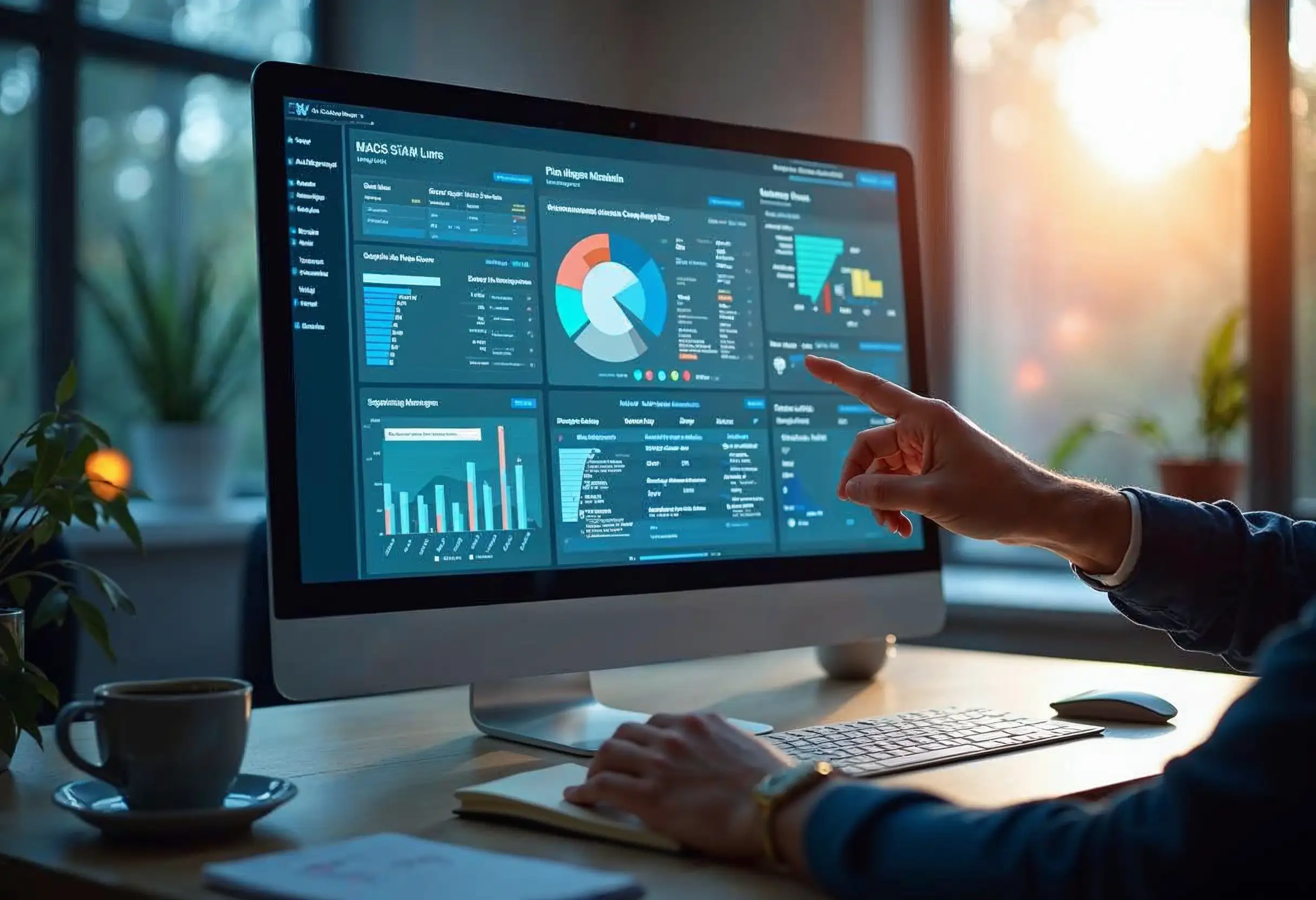
IoT Sensors and Machine Monitoring
Your equipment's health can now be continuously tracked through IoT sensors that monitor vital parameters in real-time. These smart sensors enable condition monitoring by measuring:
- Temperature fluctuations
- Vibration levels
- Pressure changes
- Oil conditions
- Electrical performance
This continuous machine monitoring helps you detect potential issues before they cause costly breakdowns, with studies showing that predictive maintenance can reduce equipment downtime by up to 30%.
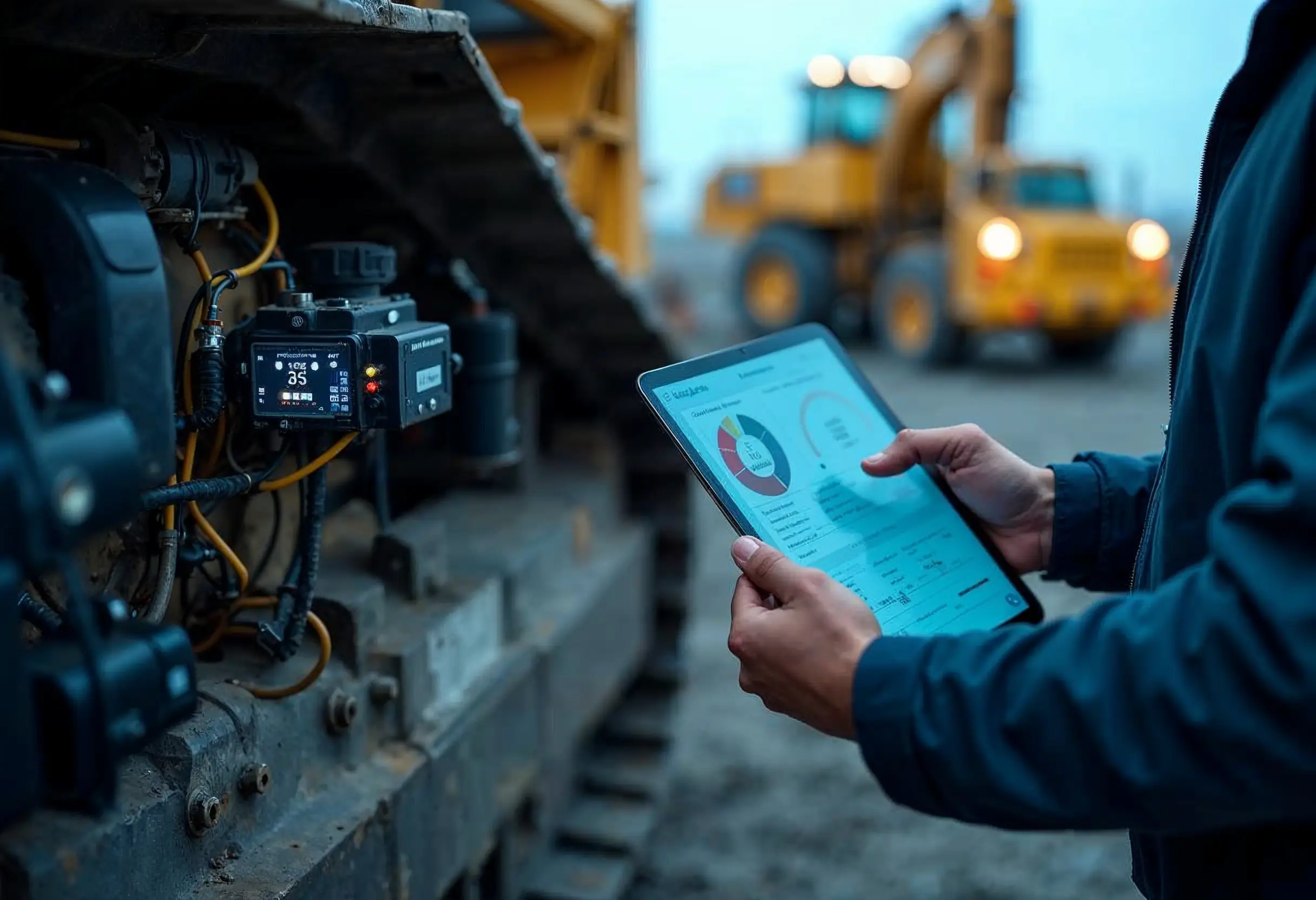
Maintenance Management Software
Modern CMMS solutions centralize all your maintenance information in one accessible database. These preventative maintenance software systems help you:
- Schedule preventive maintenance tasks
- Track work orders efficiently
- Manage inventory levels
- Monitor maintenance costs
- Generate compliance reports
The software can integrate with over 5,000 different web tools, allowing you to sync maintenance schedules with your team's calendars and streamline workflows. Some advanced systems, like CERDAAC, offer comprehensive solutions for maintenance planning and data analytics.
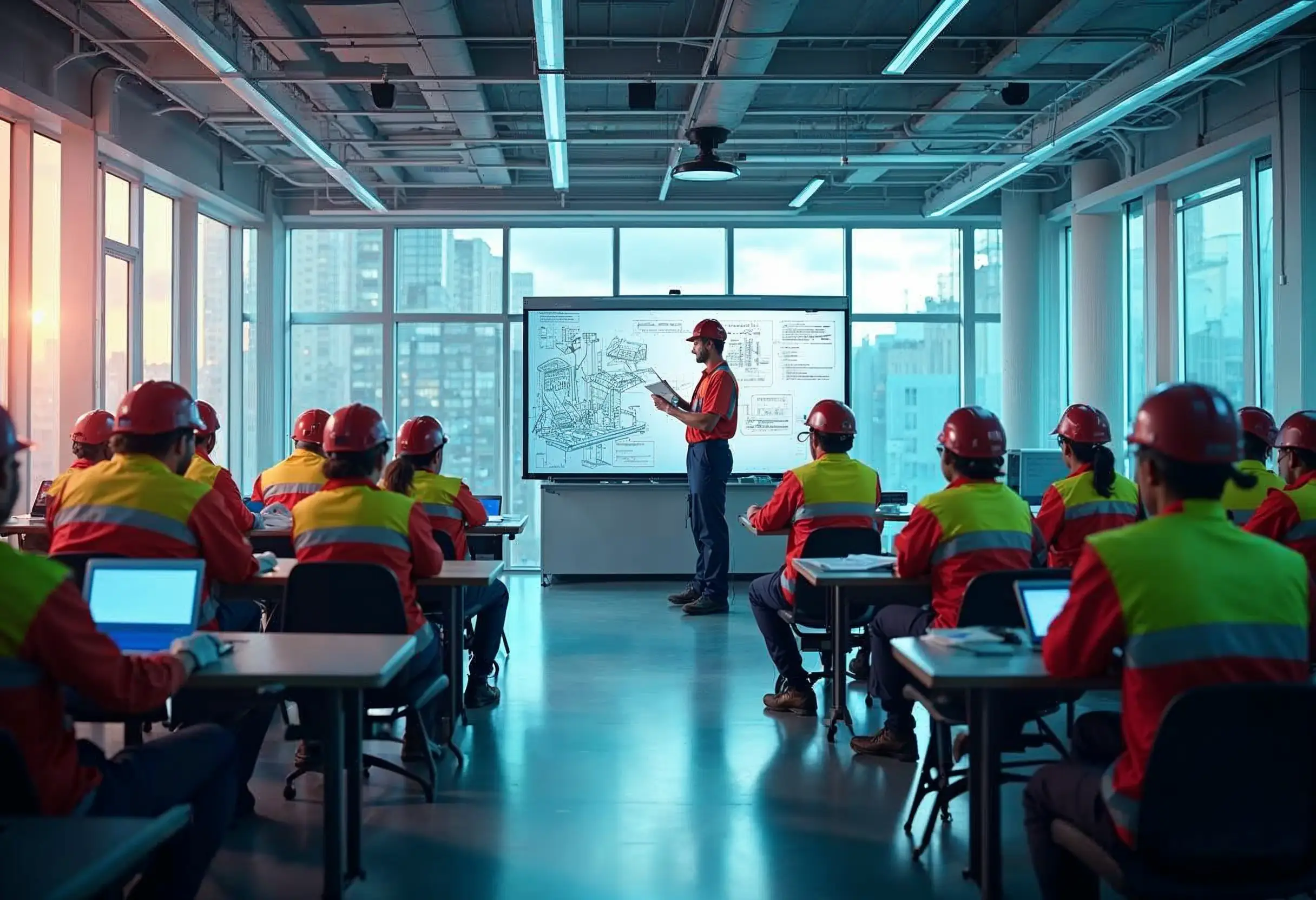
Digital Documentation Systems
Digital documentation eliminates paper-based record-keeping inefficiencies. Studies indicate that employees typically spend 20% of their time searching for information in traditional filing systems. With digital systems, you can:
Access Information Instantly: Find maintenance records, equipment manuals, and repair histories with a few clicks.
Track Maintenance History: Document all maintenance activities in a centralized location, making it easier to analyze patterns and predict future needs.
Ensure Compliance: Maintain detailed audit trails and automatically generate required documentation for regulatory compliance and safety.
Need help selecting the right maintenance technologies for your equipment? Contact MCH Parts for a free sourcing consultation and discover how to maximize your machinery's service life through condition-based maintenance and usage-based maintenance strategies.
Building a Preventive Maintenance Culture
Creating a strong maintenance culture is essential for maximizing your equipment life expectancy. Studies show that companies with comprehensive training programs achieve 218% higher income per employee than those without.
Staff Training Programs
Your maintenance technicians' expertise directly impacts equipment longevity. Proper training reduces operator-caused downtime by 18% and increases employee retention rates by 30-50%. A well-structured training program should include:
- Technical skill development
- Equipment-specific maintenance procedures
- Safety protocols and best practices
- Troubleshooting techniques
- Preventive maintenance strategies
Communication Protocols
Clear communication ensures maintenance tasks are planned and executed effectively. Implementing standardized communication procedures helps prevent unexpected breakdowns and repairs. Your communication system should establish clear channels between operators, maintenance teams, and management to track equipment health and maintenance schedules.
Accountability Systems
Implementing strong accountability measures helps track maintenance performance and ensure consistent equipment care. Digital documentation of maintenance activities allows for easy tracking of tasks and responsible parties. Service costs represent a significant portion of your fleet's budget, making it crucial to implement proper inspection protocols and hold teams accountable for equipment care.
By establishing clear responsibilities and empowering your operators with ownership of their equipment, you create a system where accountability drives better maintenance practices. This approach leads to improved equipment health monitoring and more efficient maintenance operations. Implementing an asset criticality ranking system can help prioritize maintenance efforts and resource management for optimal results.
Need guidance on building a strong maintenance culture for your equipment fleet? Contact MCH Parts for a free sourcing consultation and discover how to maximize your machinery's service life.
Component-Specific Maintenance Strategies
Proper component-specific maintenance is crucial for maximizing your equipment's service life. Studies show that implementing targeted maintenance strategies can reduce equipment failures by up to 30%.
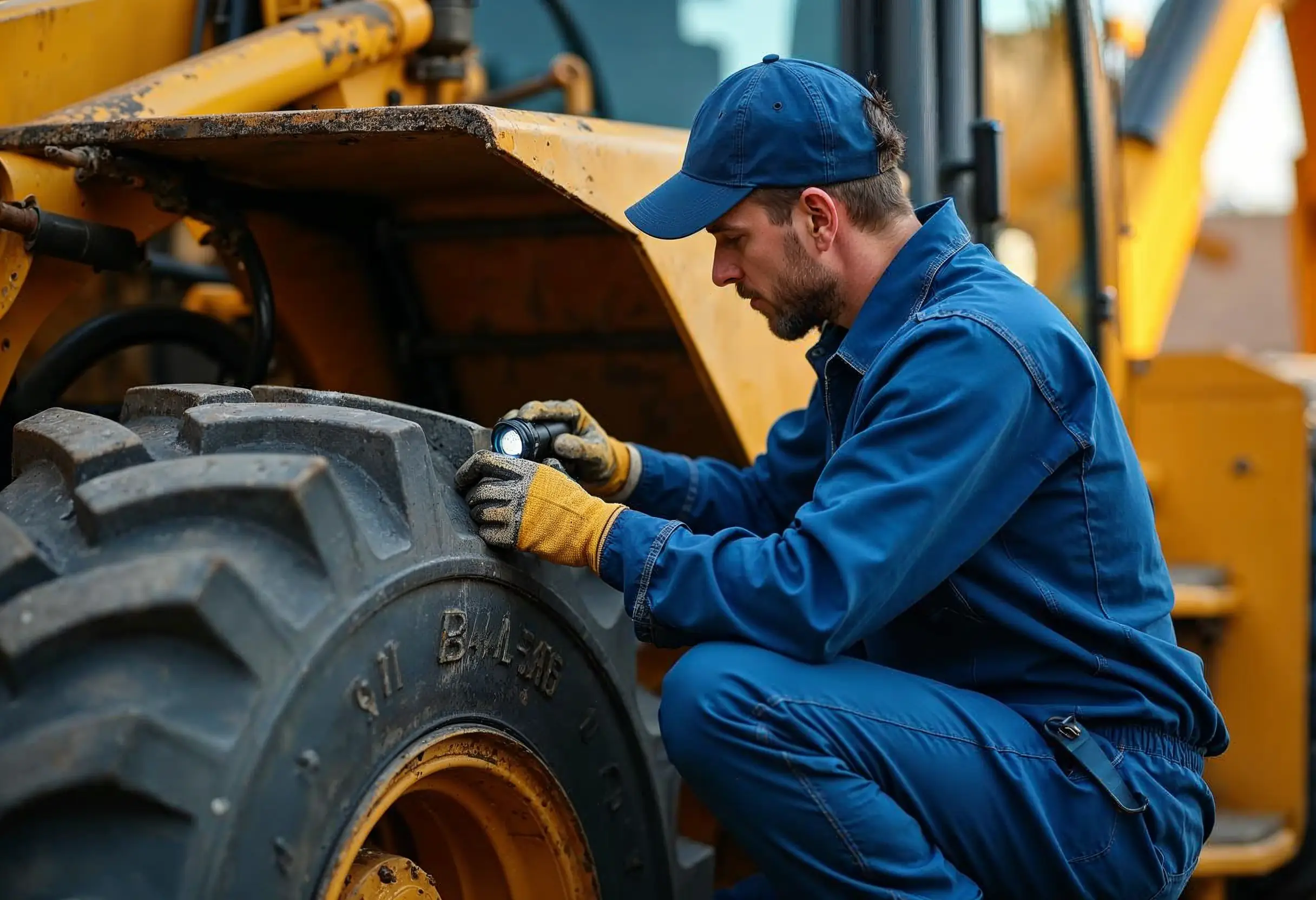
Hydraulic System Care
Your hydraulic system requires regular attention to prevent contamination and maintain optimal performance. Contaminated fluid stands as the primary culprit behind system failures. Implement these essential practices:
Regular Inspections: Check fluid levels, look for leaks, and inspect hoses for wear. Studies indicate that proper hydraulic maintenance can extend component life by up to 20%.
Fluid Management: Change hydraulic fluid after every 1,000 hours of operation. Always use the same type and brand of fluid to maintain system integrity.
Engine Maintenance Protocols
Your engine's longevity depends on consistent care and attention to maintenance schedules. Regular engine maintenance allows for early detection of potential issues. Key protocols include:
Oil Management: Follow manufacturer-recommended oil change intervals, typically between 7,000 to 10,000 miles. Monitor oil quality and levels regularly to prevent premature wear.
Cooling System: Maintain proper coolant levels and regularly inspect the radiator for debris or blockages that could affect performance.
Electrical System Upkeep
Your electrical system requires systematic maintenance to prevent unexpected failures. Studies show that preventive electrical maintenance can reduce downtime by up to 35-50%. Focus on:
Routine Inspections: Check all electrical connections, looking for signs of wear, corrosion, or loose connections.
Component Testing: Test emergency systems monthly and verify that all protective devices are functioning correctly.
Implementing a strategy for worn parts replacement based on regular inspections and predictive analytics can significantly extend your equipment's operational life.
Need expert guidance on maintaining your equipment's critical systems? Contact MCH Parts for a free sourcing consultation and discover how to maximize your machinery's service life.
Conclusion
Regular equipment maintenance stands as a crucial investment that directly impacts your bottom line. Research proves that systematic preventive maintenance extends equipment life by 20-30% while reducing unexpected breakdowns and operational costs.
Your maintenance strategy must address multiple aspects - from critical system care and wear point monitoring to implementing modern technologies and building a strong maintenance culture. Smart sensors, maintenance software, and digital documentation systems help track equipment health effectively, while proper staff training ensures consistent care across your fleet.
Component-specific maintenance protocols for hydraulic, engine, and electrical systems play a vital role in equipment longevity. Following manufacturer guidelines and maintaining detailed maintenance records helps prevent costly repairs and extends service life.
Success in equipment maintenance requires dedication to preventive care and attention to detail. By focusing on performance optimization and reliability, you can significantly improve your operational efficiency and equipment uptime. Consider reaching out to MCH Parts for a free sourcing machinery or parts consultation, ensuring your business benefits from top-tier equipment and service. Remember, each dollar invested in proper maintenance today saves multiple dollars in future repairs and replacement costs.
FAQs
Q1. How can I extend the lifespan of my equipment? Regular maintenance is key. This includes frequent lubrication, keeping machinery clean, routinely inspecting seals and filters, cleaning breathers, and maintaining detailed maintenance records. Implementing these practices can extend equipment life by 20-30%.
Q2. What role does technology play in equipment maintenance? Modern technologies like IoT sensors, maintenance management software, and digital documentation systems play a crucial role. They enable real-time monitoring of equipment health, efficient scheduling of maintenance tasks, and easy access to maintenance history, reducing downtime by up to 30%.
Q3. How important is staff training in equipment maintenance? Staff training is vital. Companies with comprehensive training programs achieve 218% higher income per employee than those without. Proper training reduces operator-caused downtime by 18% and increases employee retention rates by 30-50%.
Q4. What are some key maintenance strategies for specific equipment components? For hydraulic systems, regular fluid checks and changes are crucial. Engine maintenance involves following manufacturer-recommended oil change intervals and maintaining proper coolant levels. Electrical systems require regular inspections of connections and component testing. These targeted strategies can reduce equipment failures by up to 30%.
Q5. How does environmental impact affect equipment lifespan? Environmental conditions significantly influence equipment longevity. Exposure to extreme temperatures, abrasive materials, and irregular surfaces can take a considerable toll on machinery performance. Indoor equipment typically experiences a longer lifespan compared to outdoor equivalents. Proper maintenance becomes even more critical when equipment operates in challenging environments.
Read More
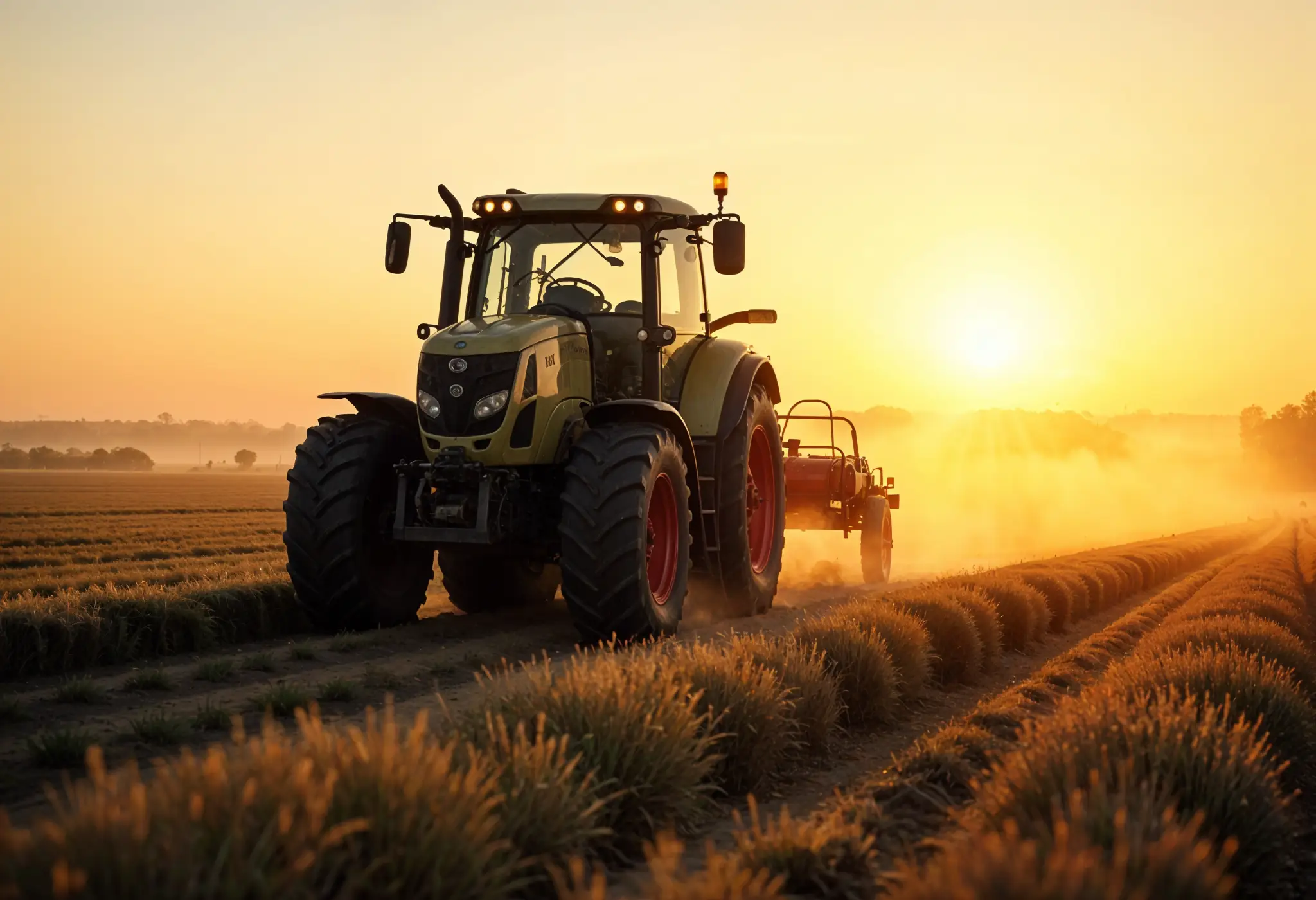
Top Hydraulic Components for Agricultural Equipment in 2025: Complete Guide
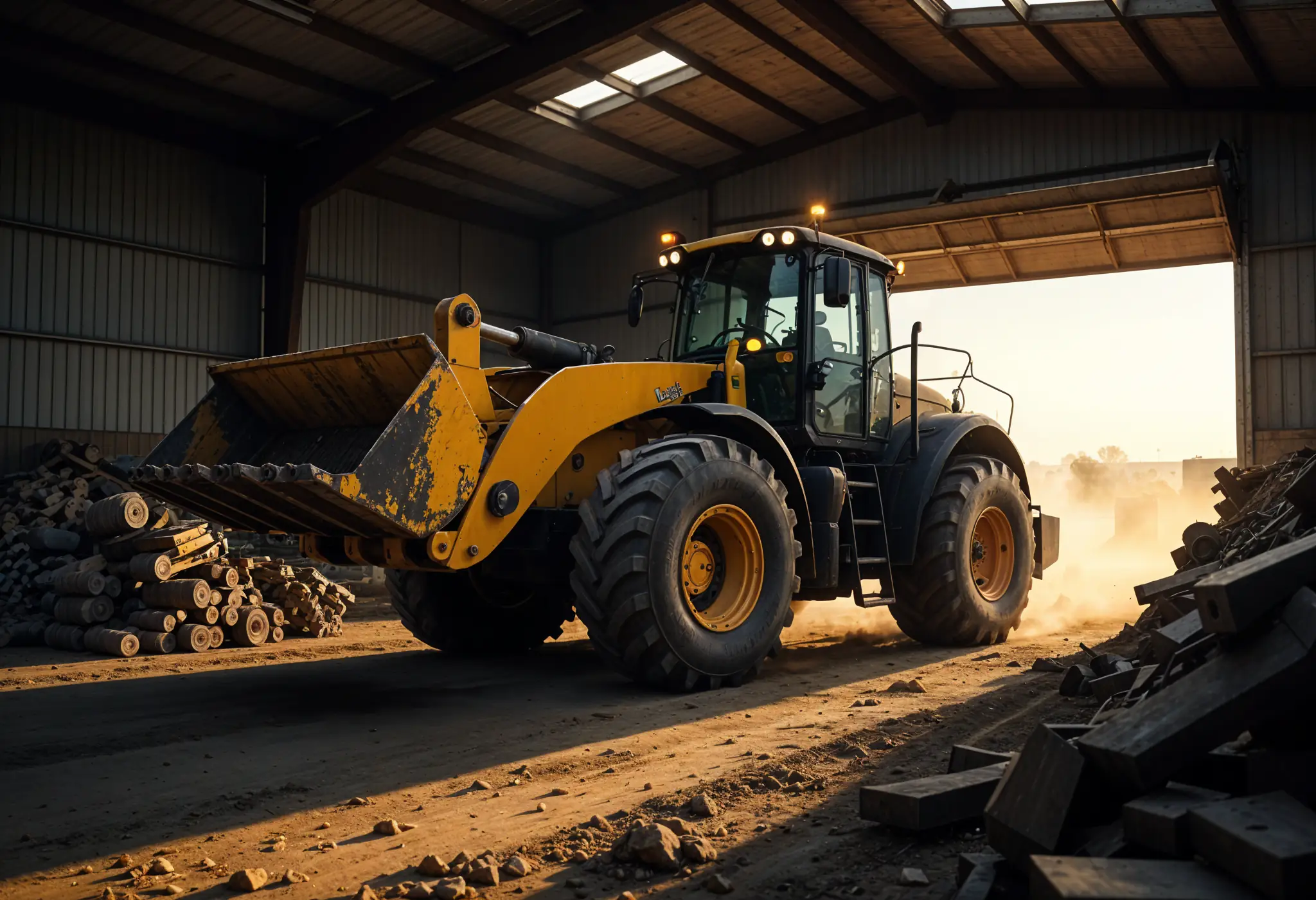
The Essential Farm Equipment Parts You Can't Afford to Run Out Of
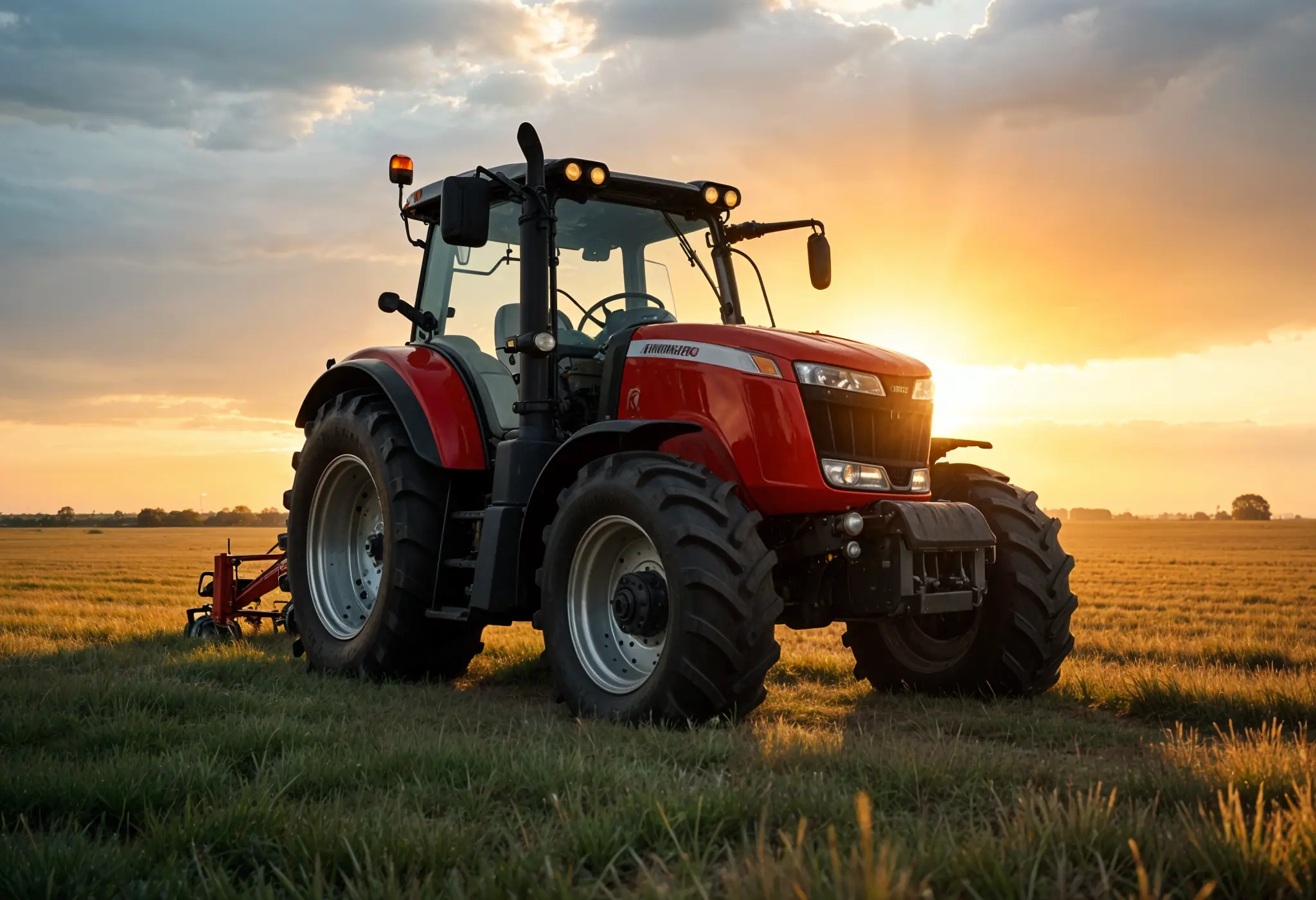
How to Service Farm Equipment: A Farmer's Guide to Zero Harvest Downtime
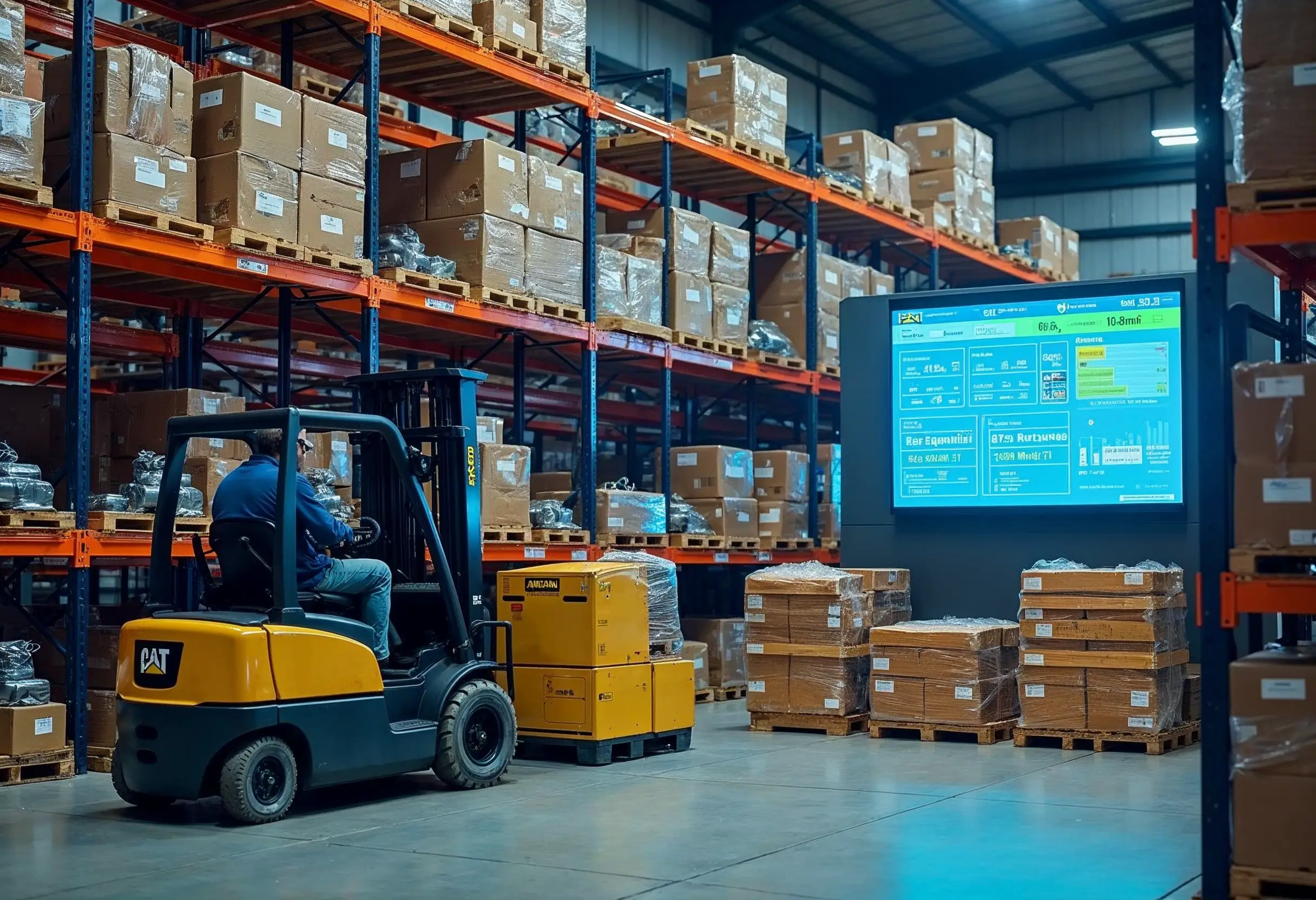
Construction Machinery Parts Suppliers: Expert Selection Guide
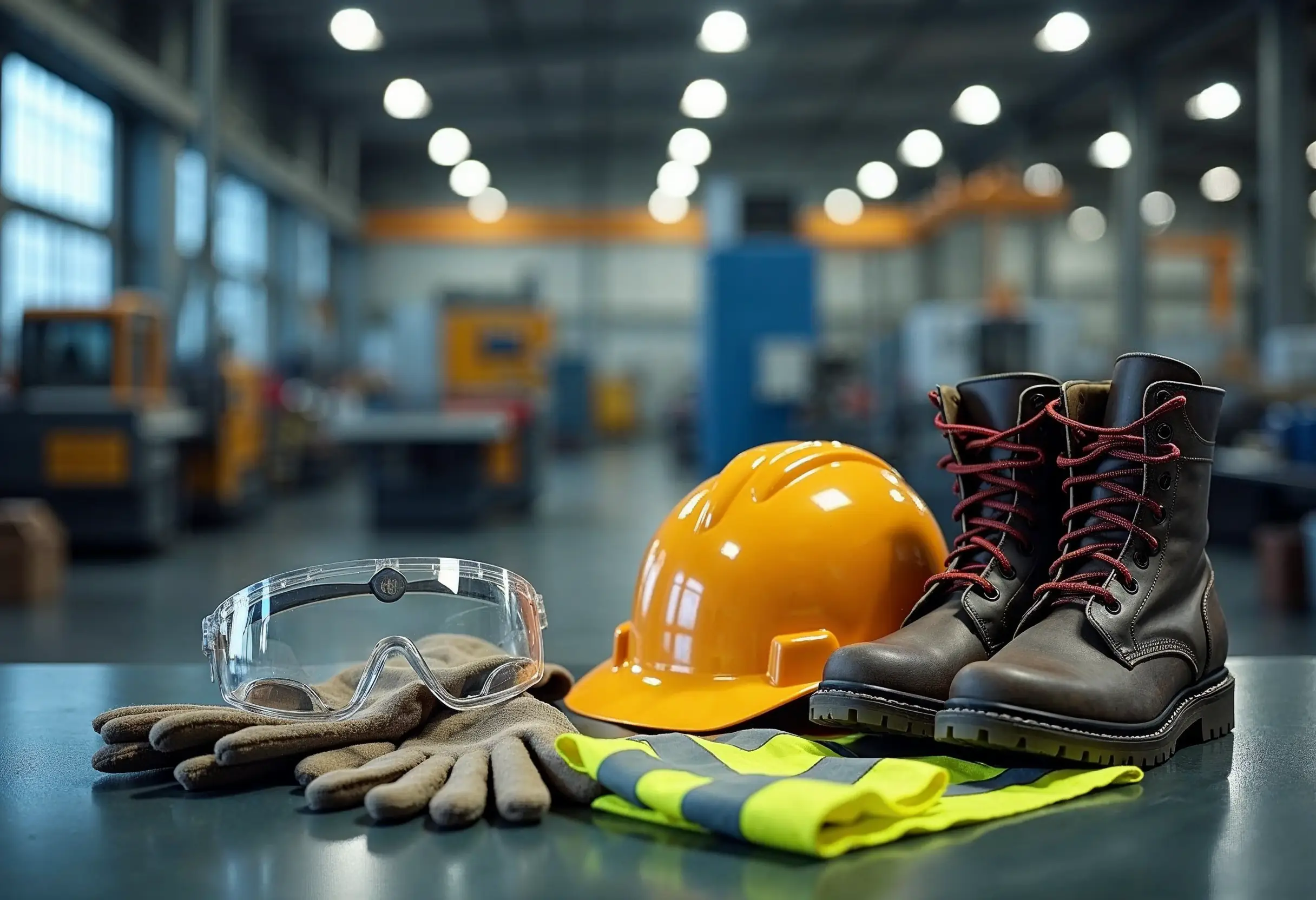
How to Apply Machine Safety Rules: From Selection to Installation
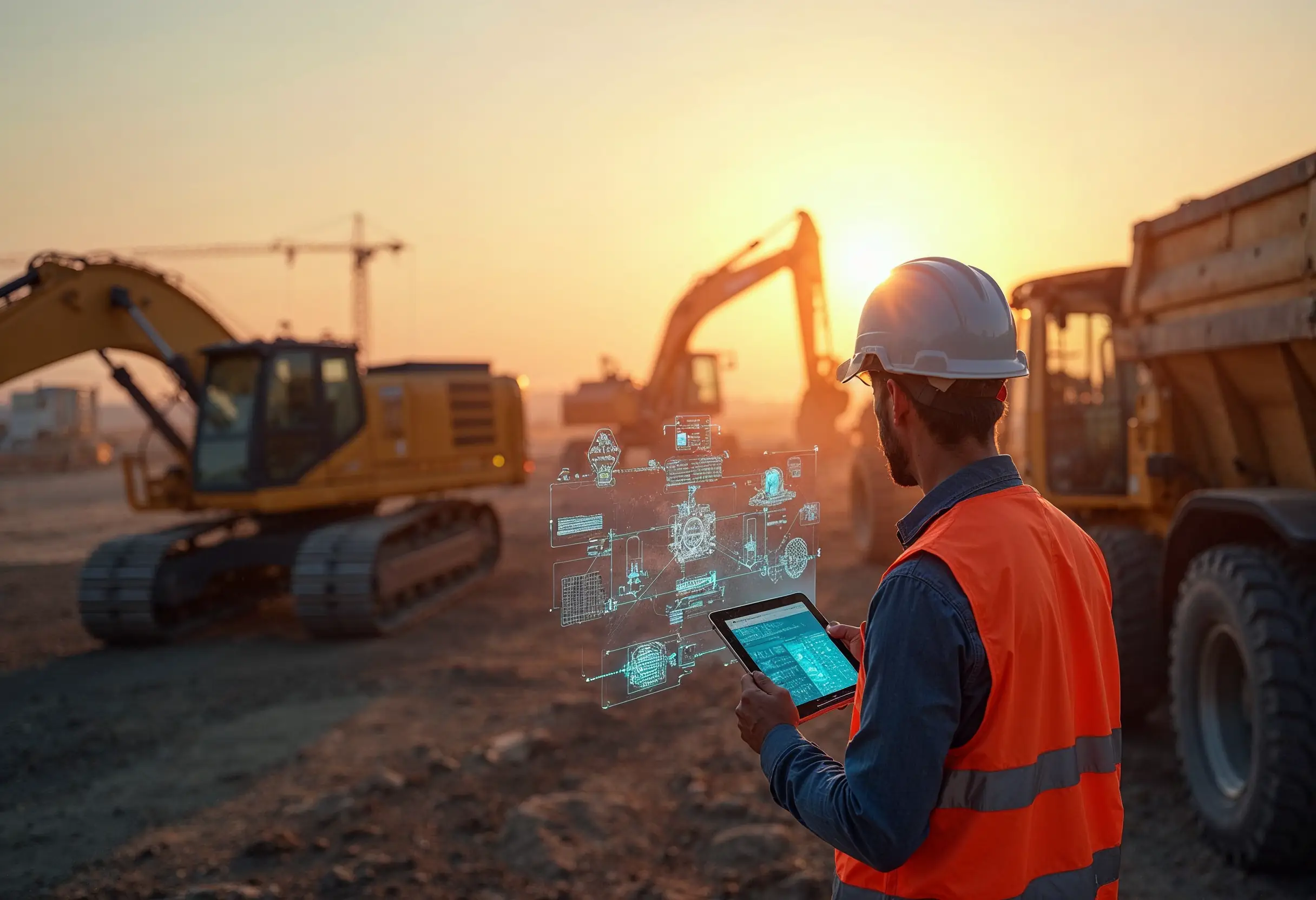
Smart Diagnostics Cut Heavy Equipment Failures by 73%
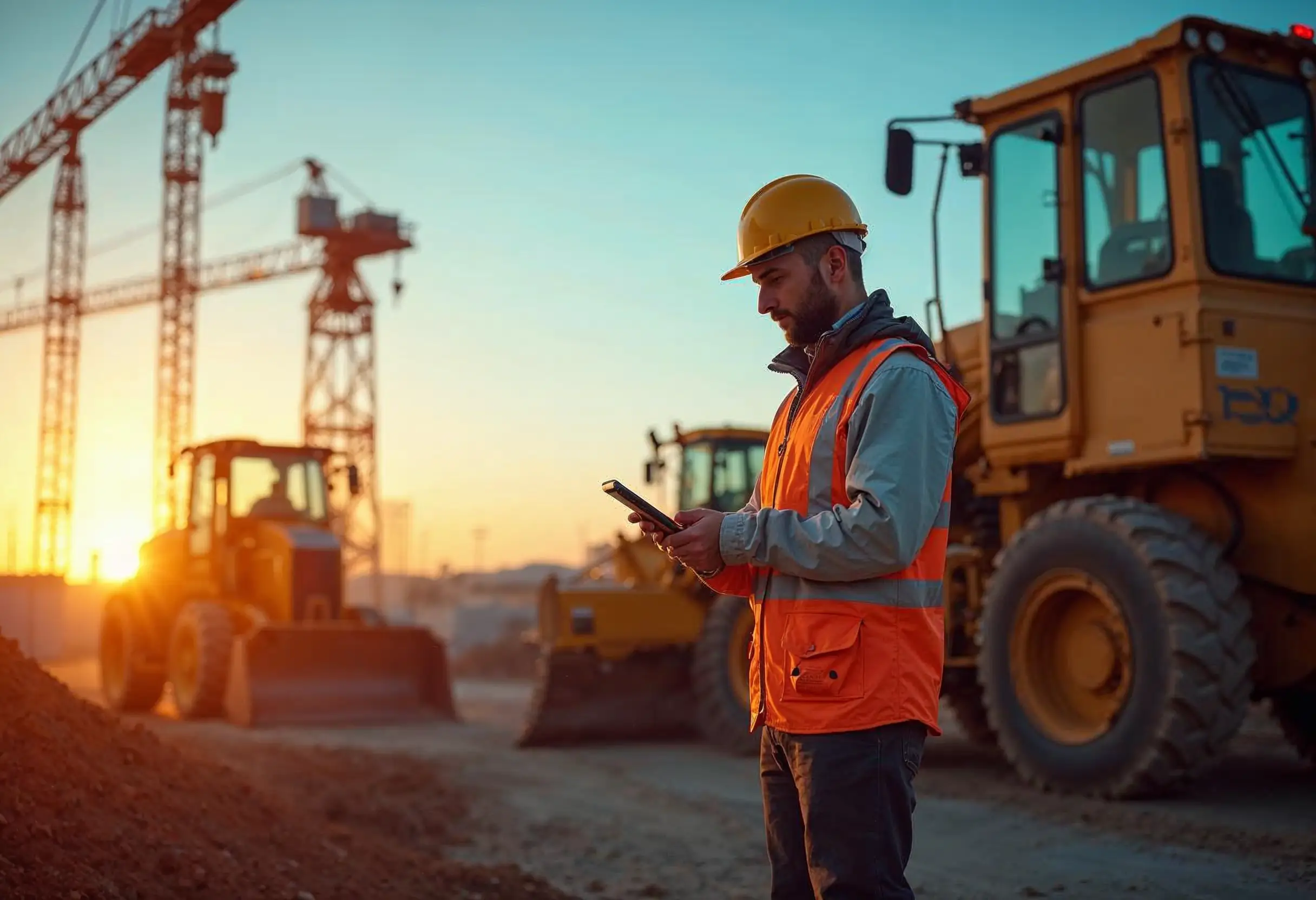
5 Ways to Assess the Environmental Impact of Heavy Construction Machinery
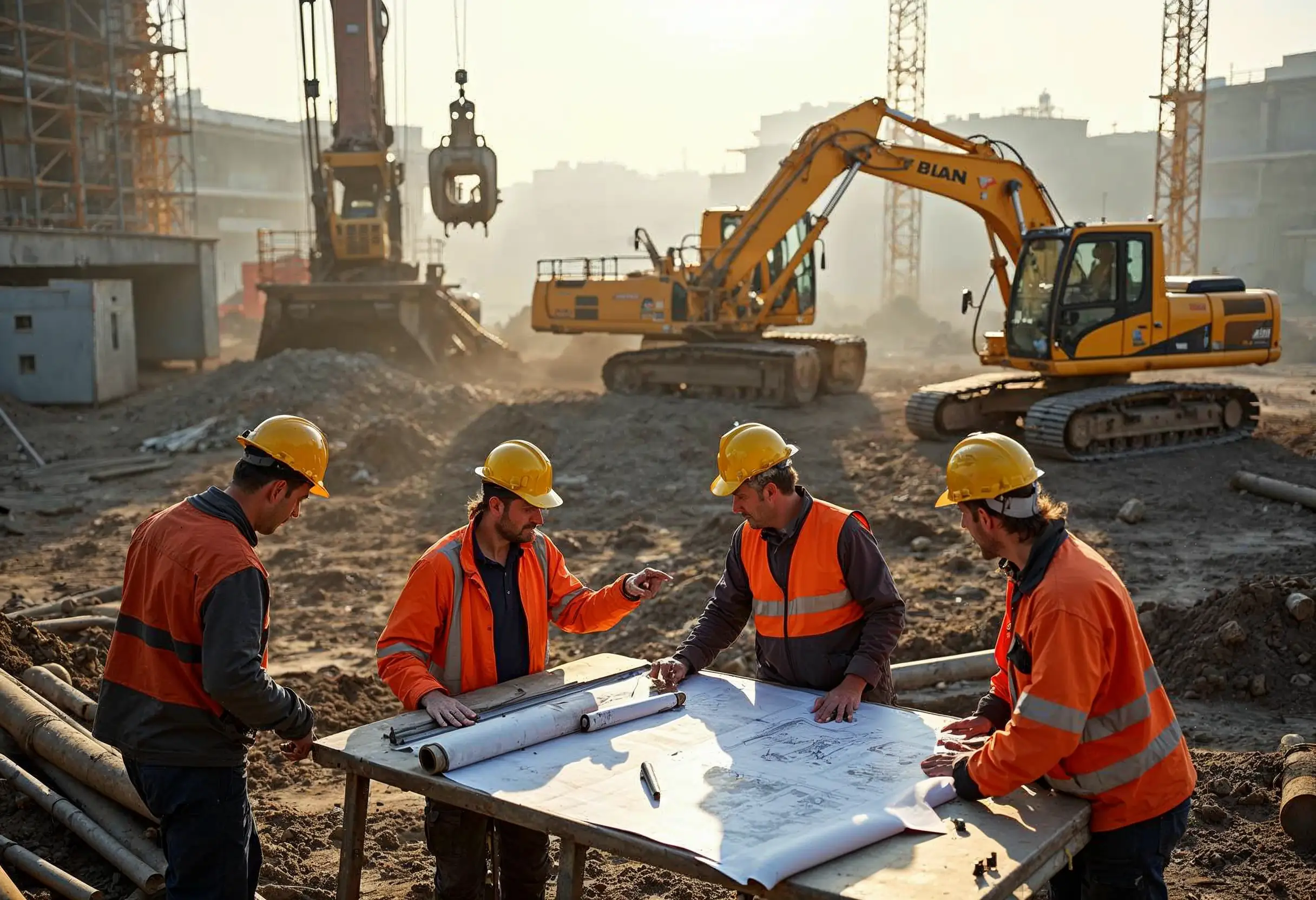
10 Smart Ways to Pick Construction Machinery for 2025 Projects
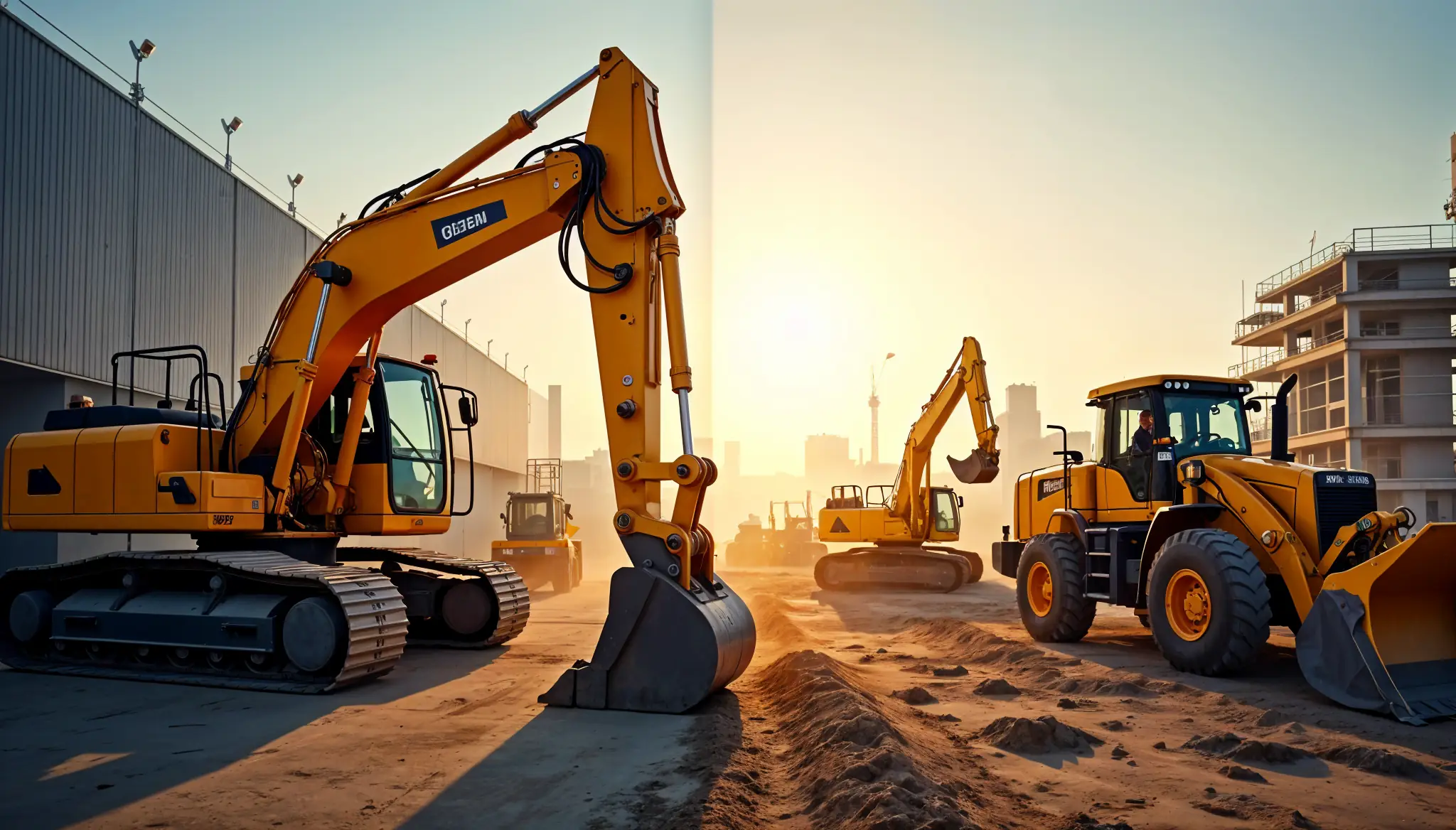
Rent vs Purchase Equipment: What Heavy Industry Experts Hide
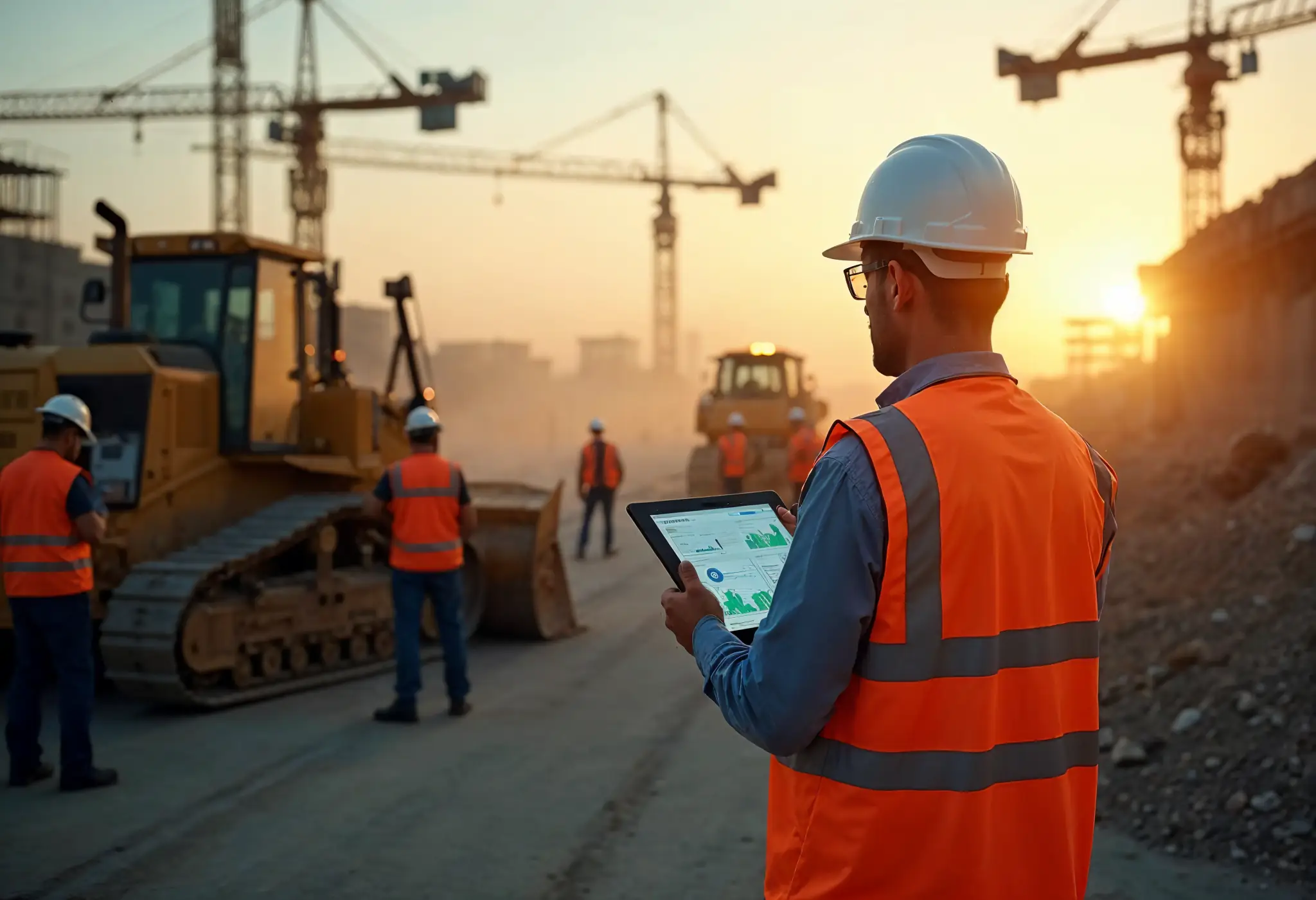
How to Implement a Construction Inventory Management System for Equipment Efficiency
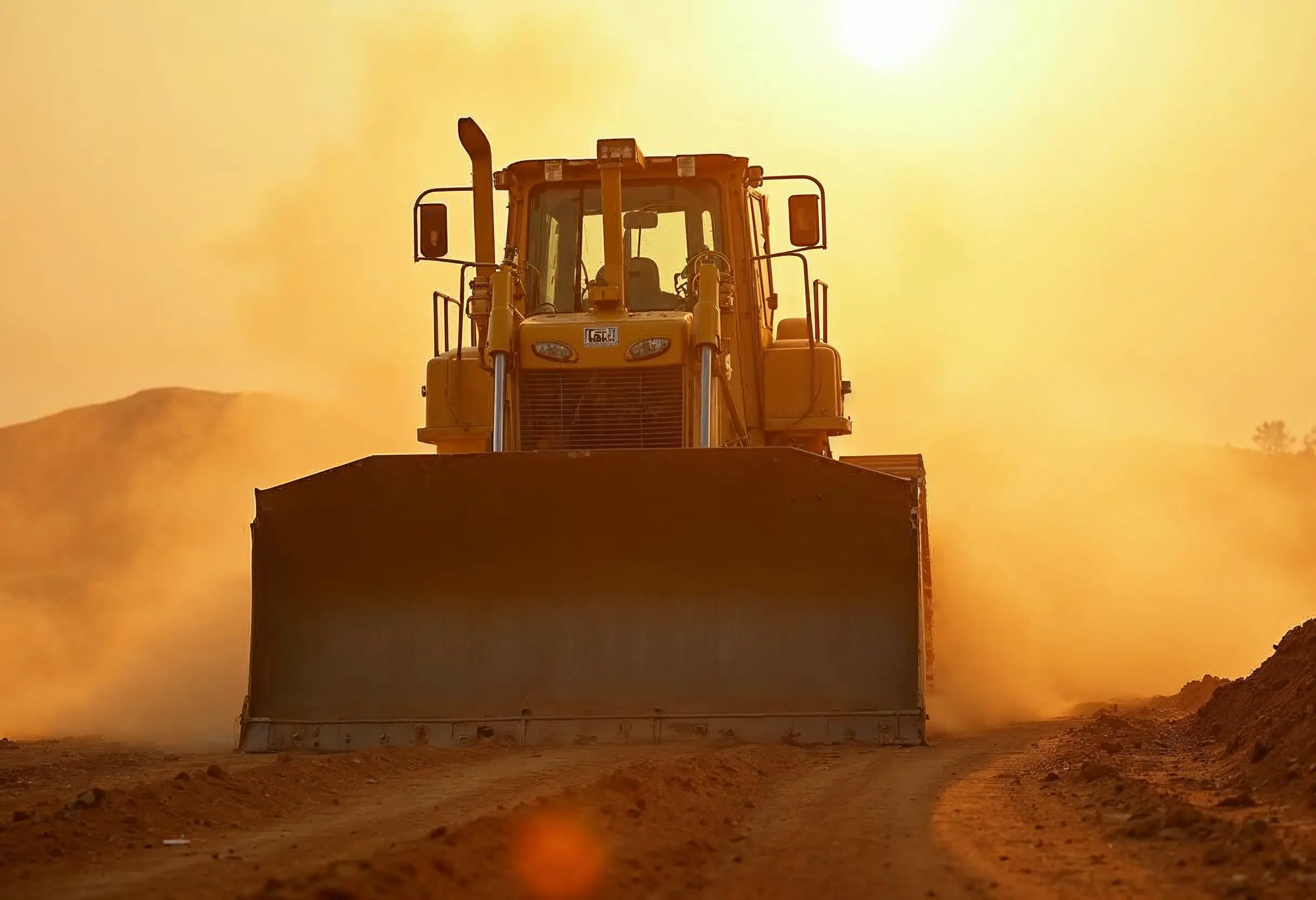
How to Extend Equipment Life Expectancy with Regular Maintenance
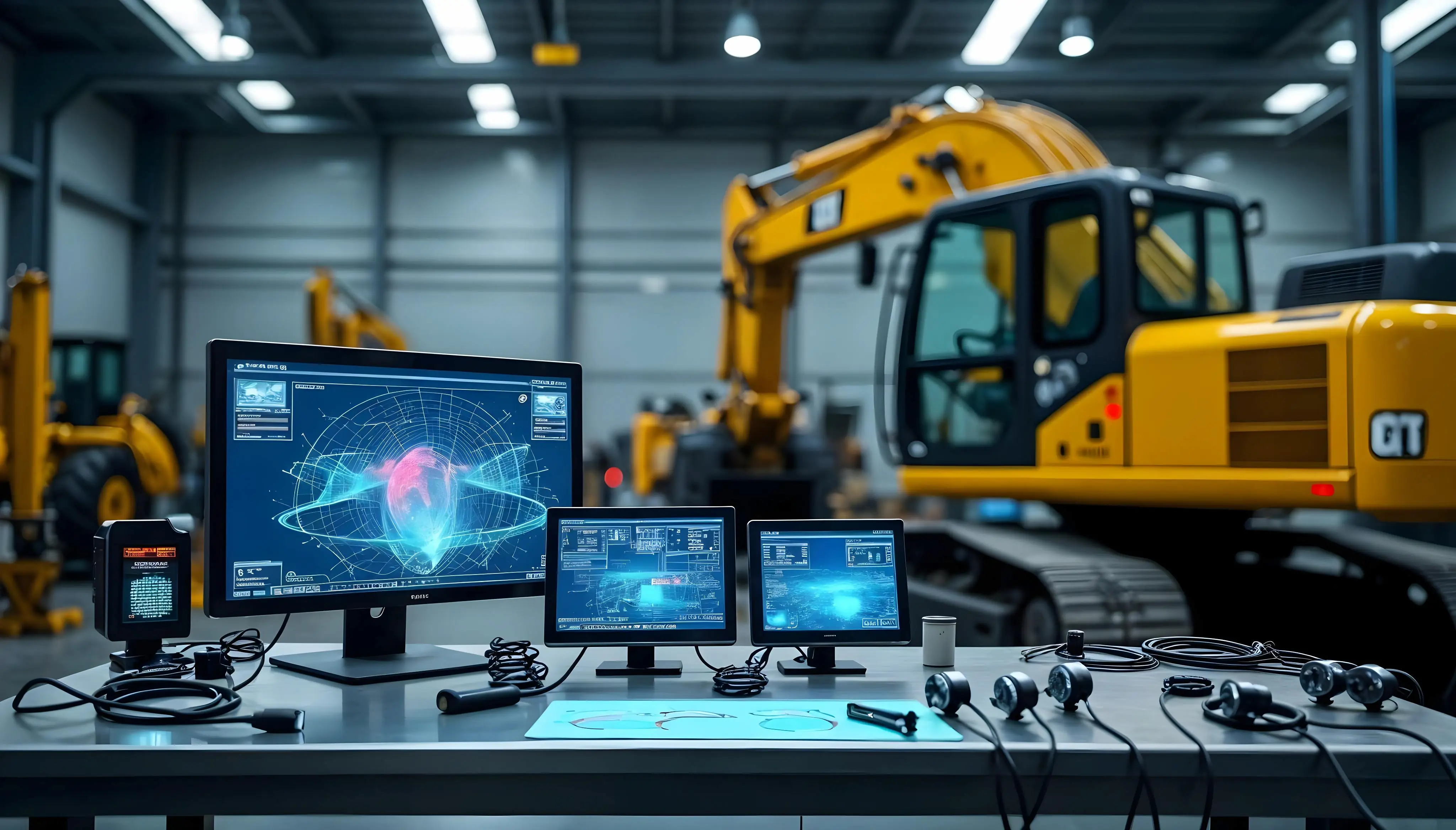
Advanced Heavy Equipment Diagnostic Tools: Ensuring Construction Machinery Quality
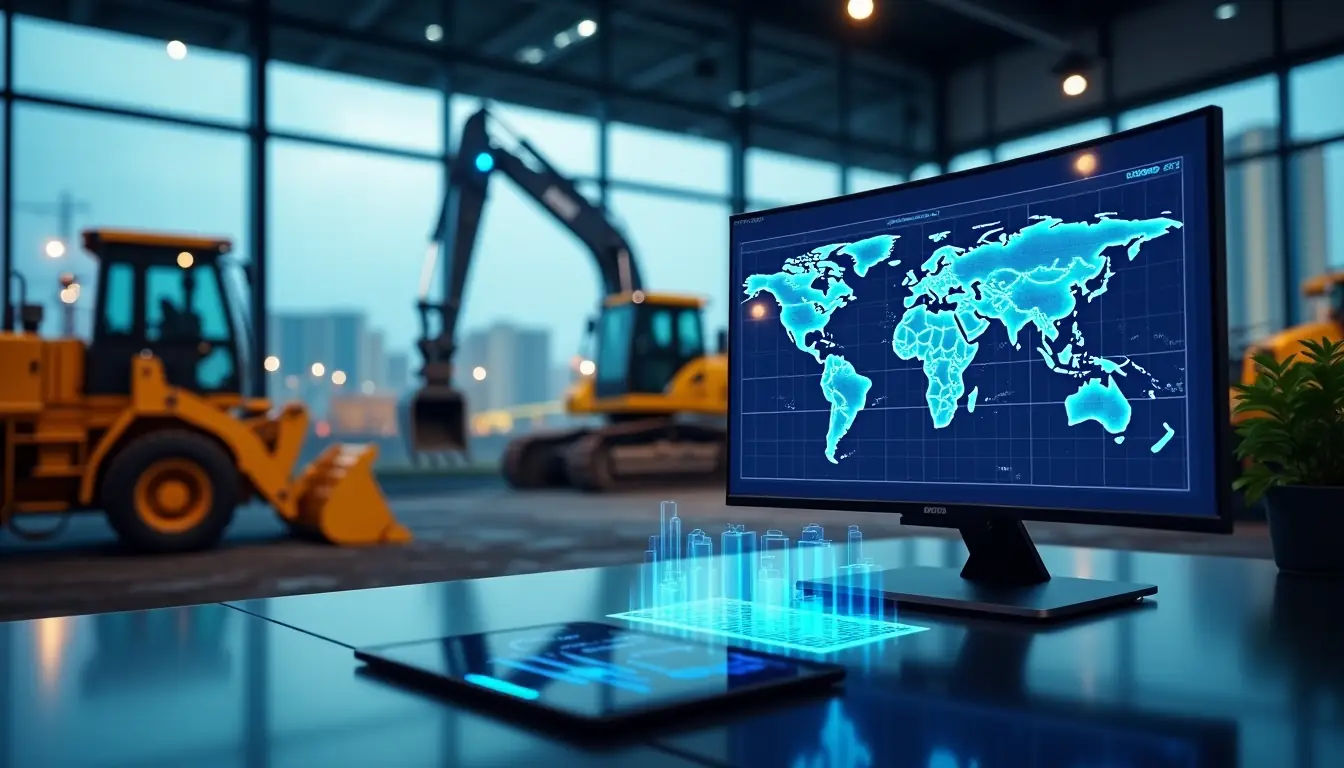
Essential Features Your Construction Equipment Inventory System Needs
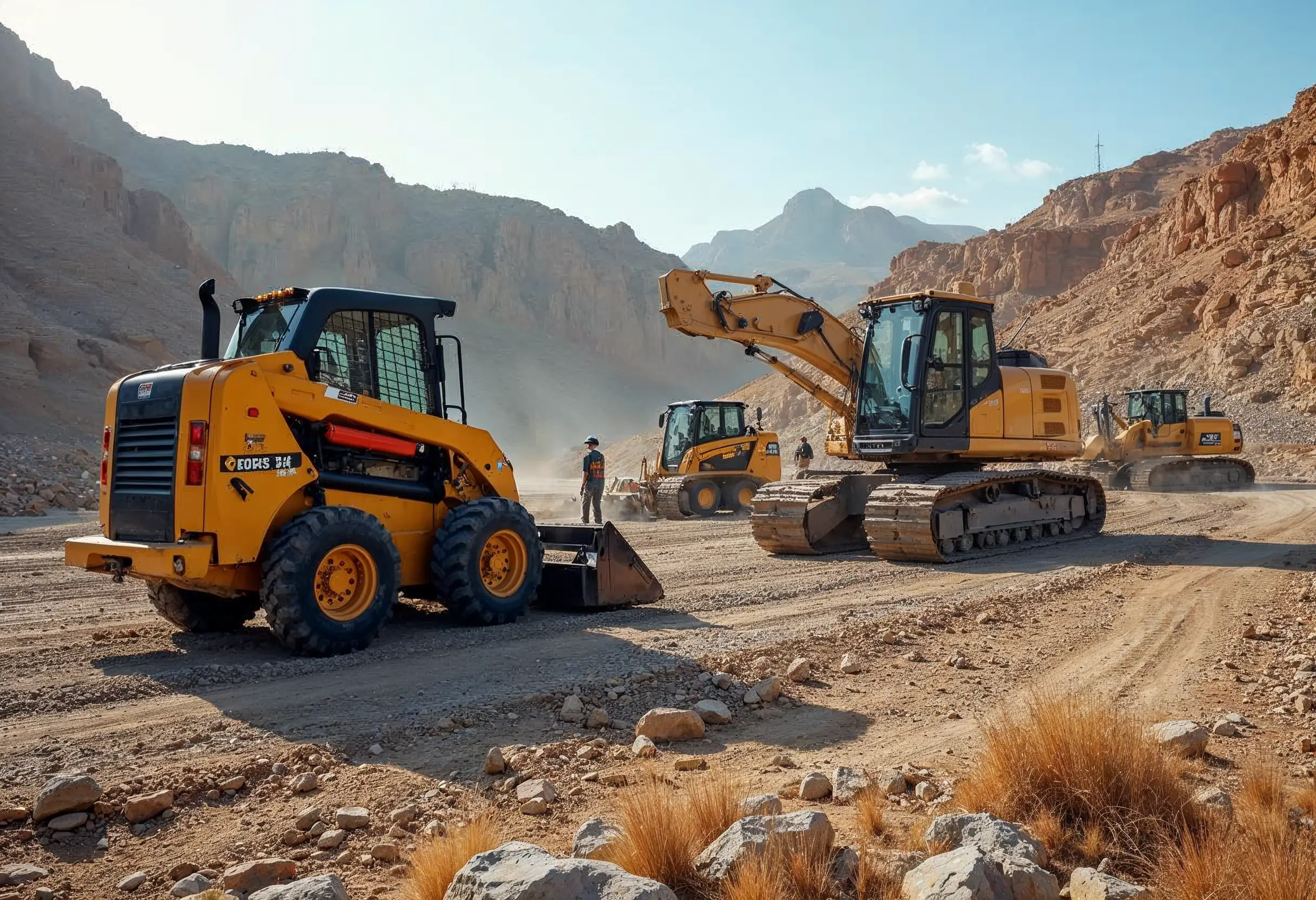
29 Quick Tips for Choosing Construction Equipment for Remote Locations
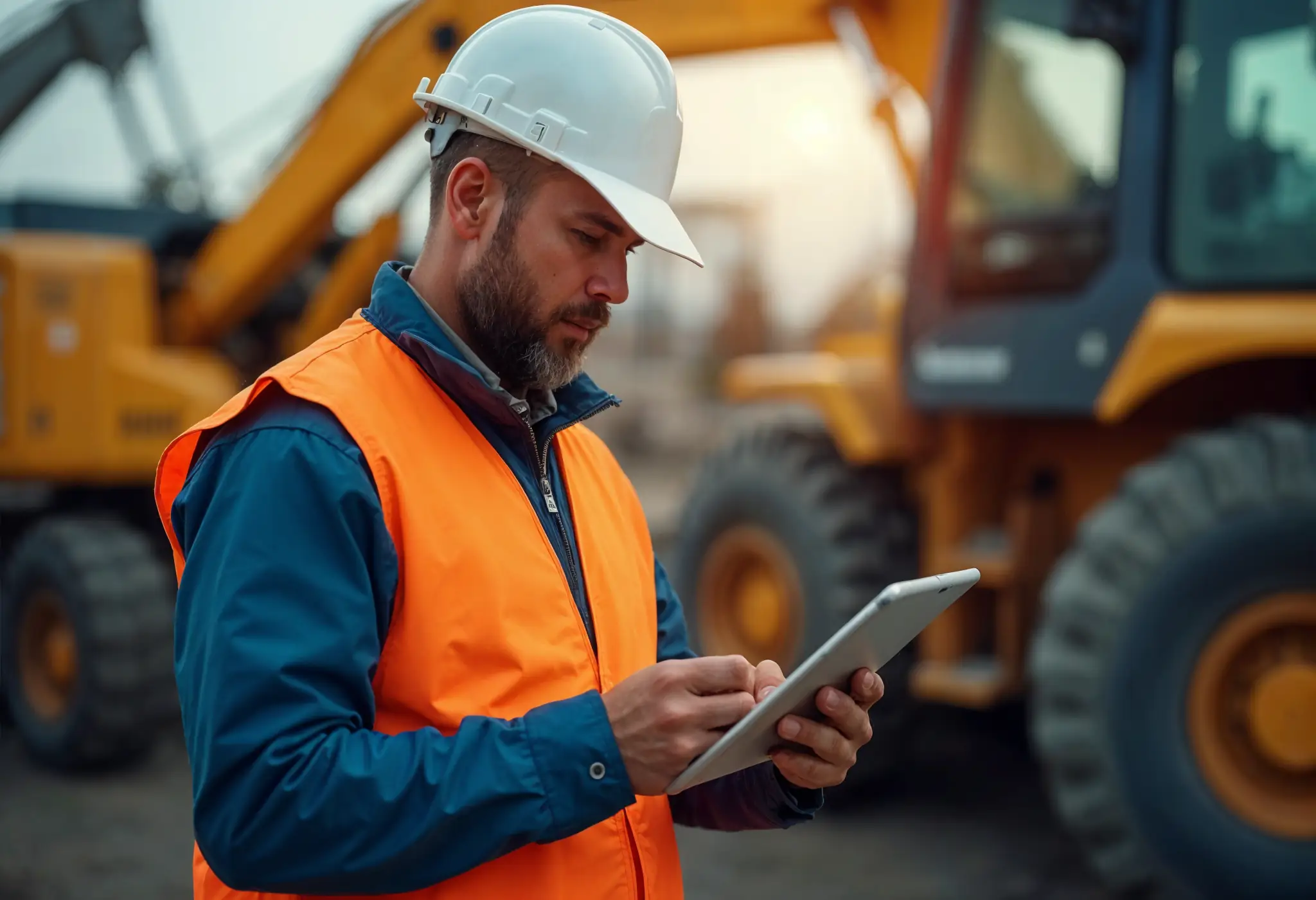
How to Select Construction Machinery with Optimal Equipment Maintenance in Mind
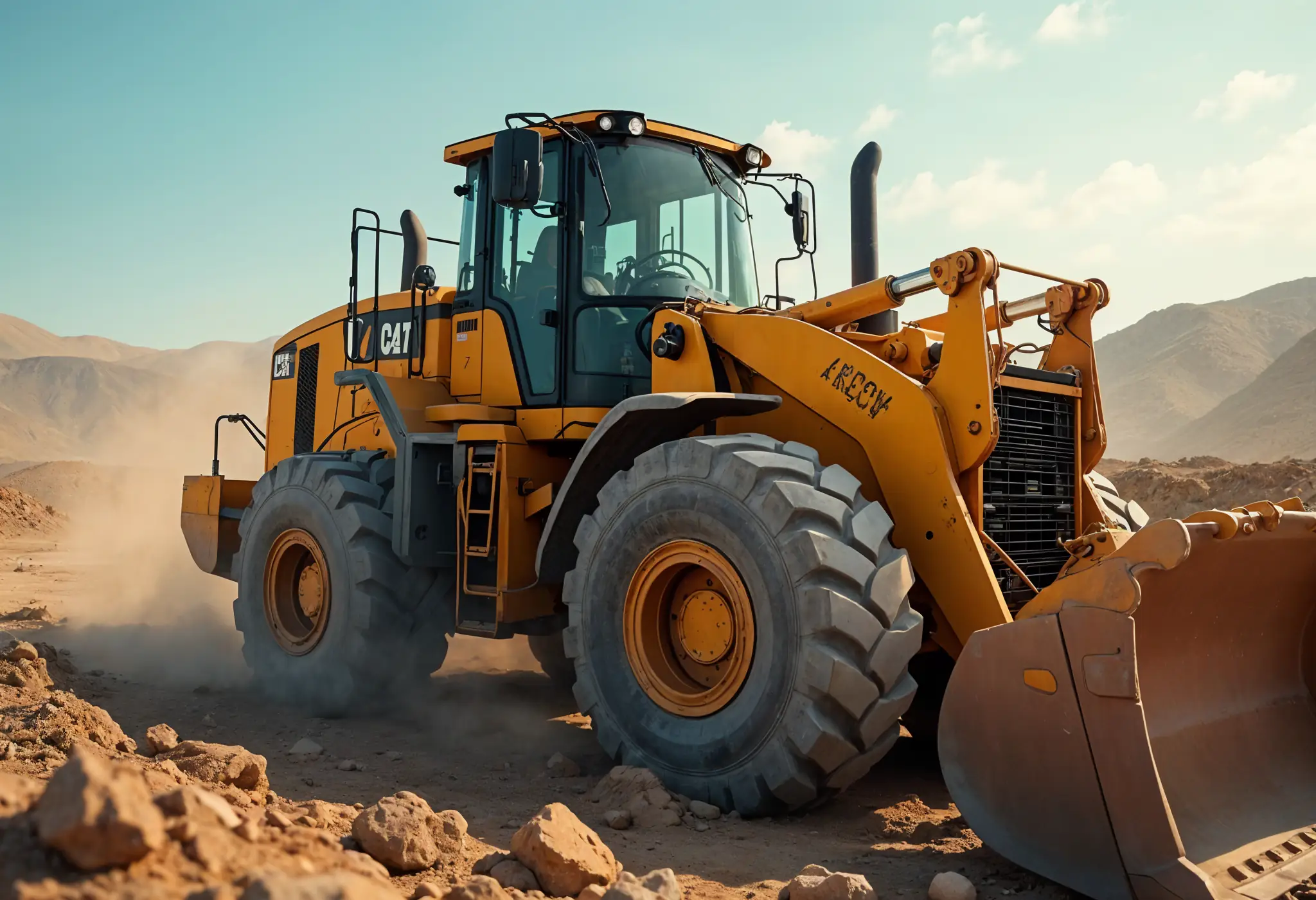
Top 25 Tips for Selecting Bulldozers for Construction Sites
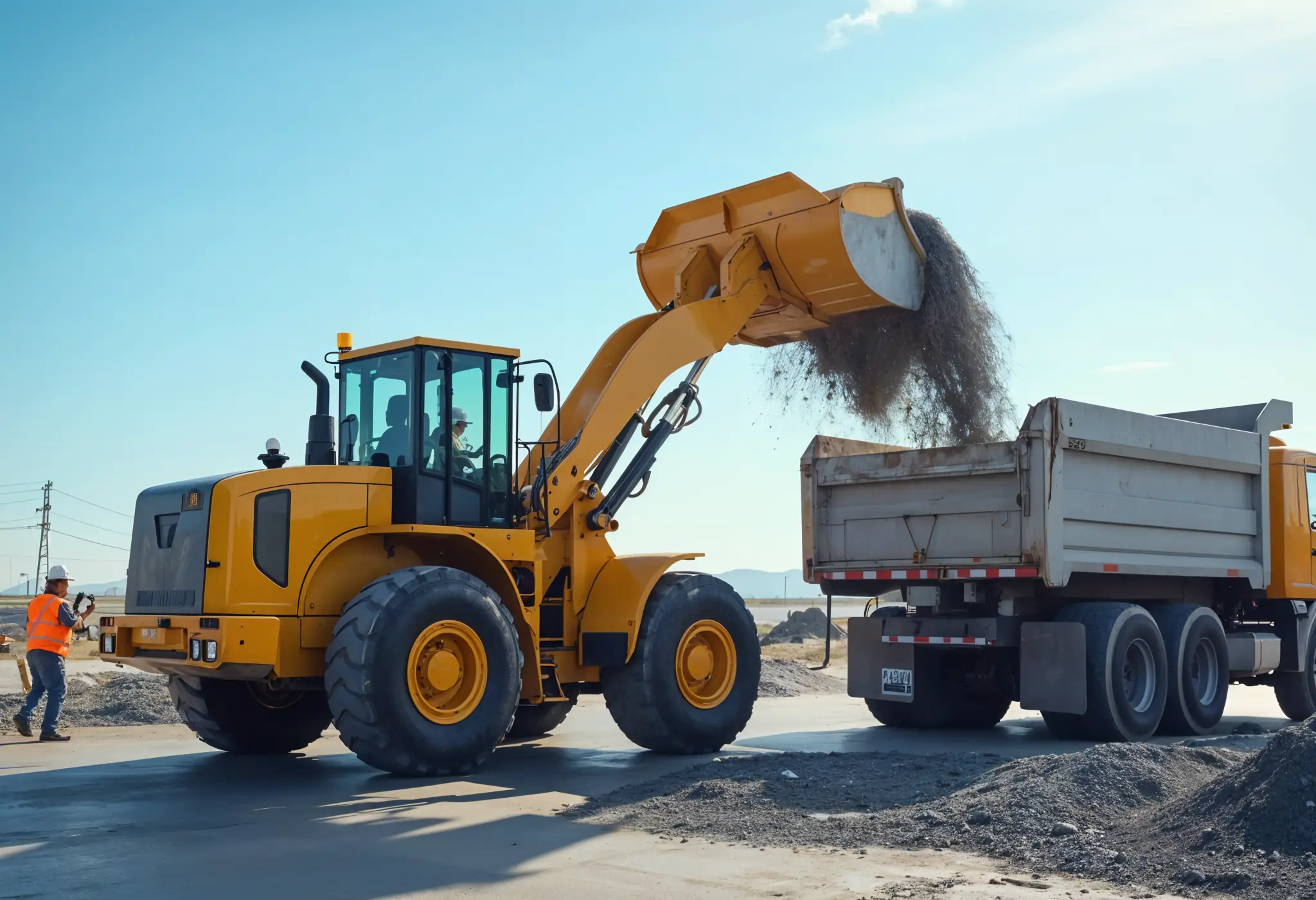
Which Construction Loader is Best for Your Project Needs?
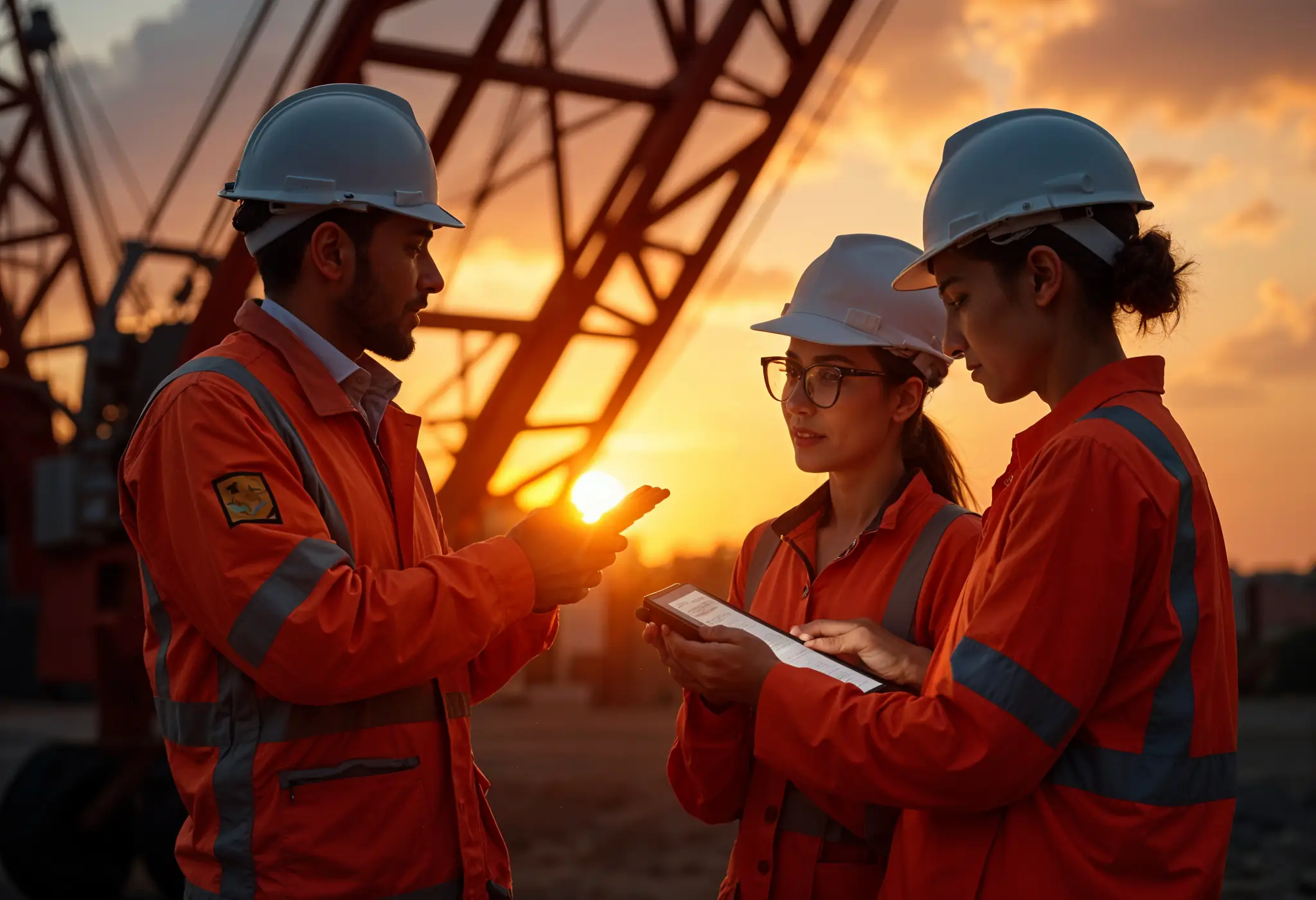
4 Key Steps to Form a Construction Machinery QC Team
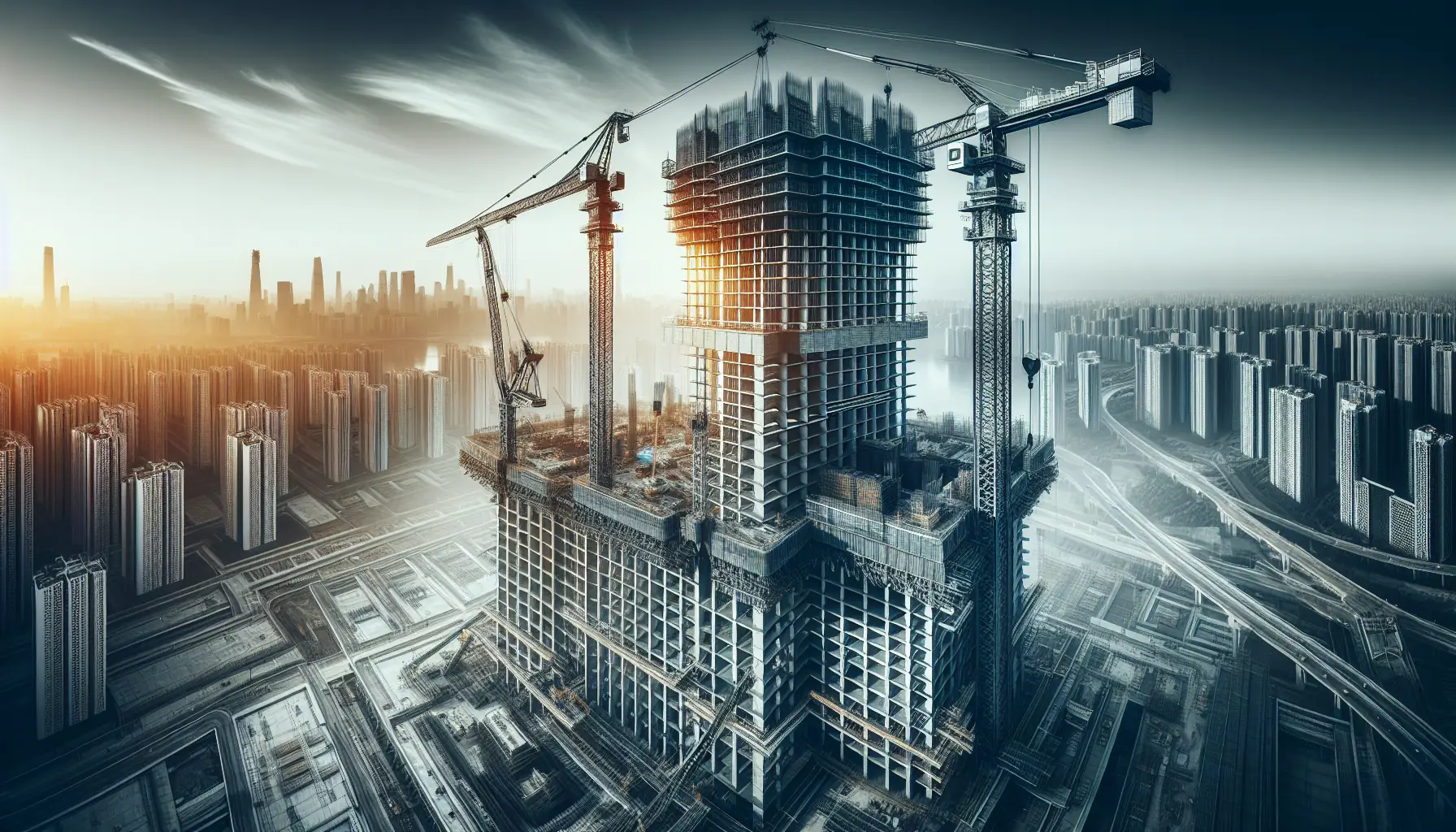
15 Essential Tips for Selecting the Perfect Crane for Construction
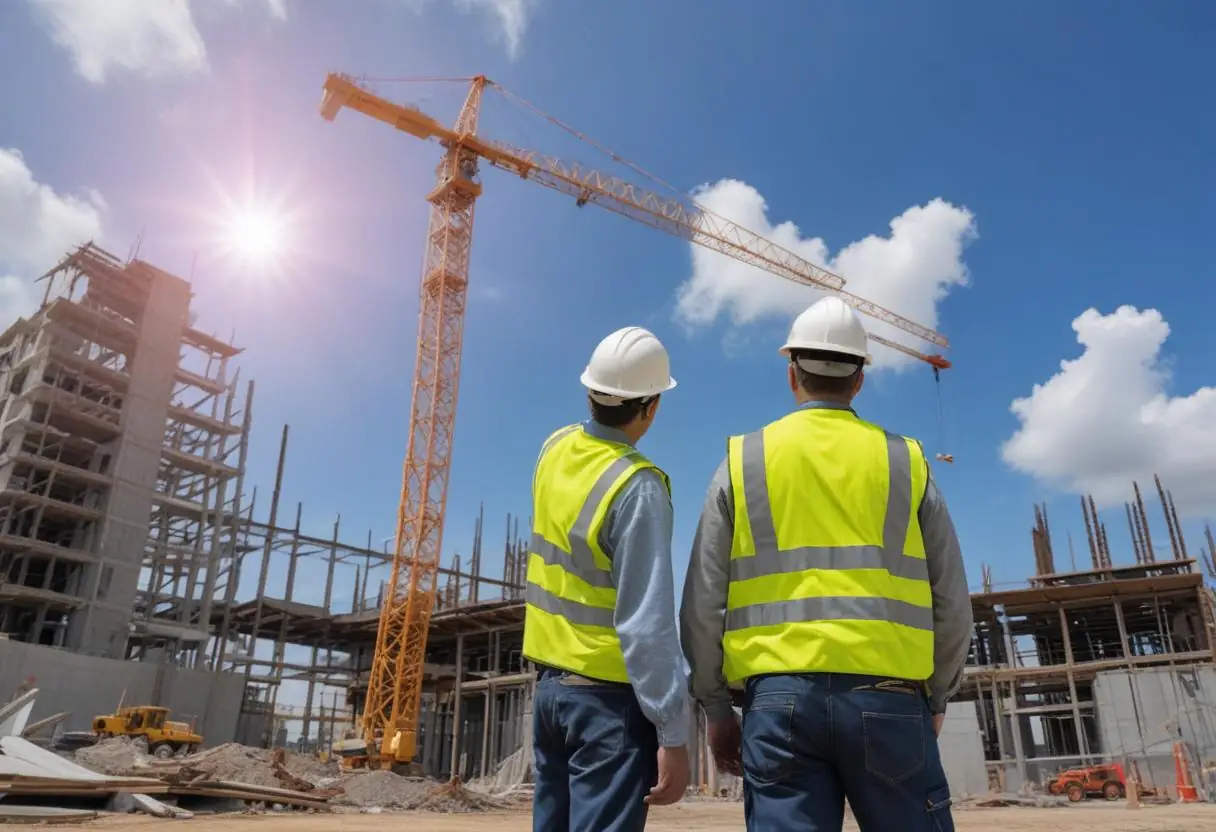
Maximize Savings: Multi-Purpose Construction Machinery for Lower Costs
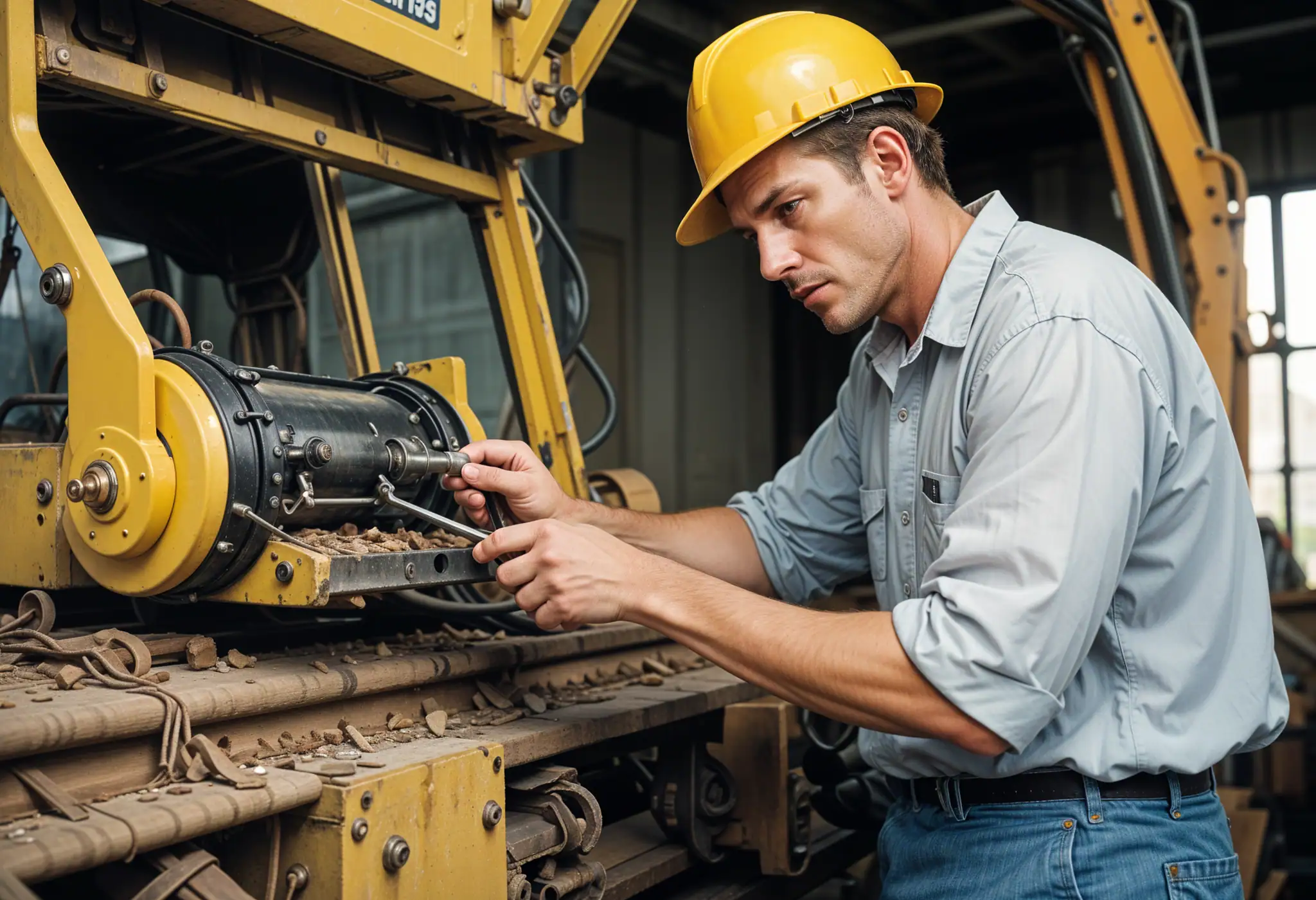
Affordable Heavy Equipment Parts: A Sourcing Guide
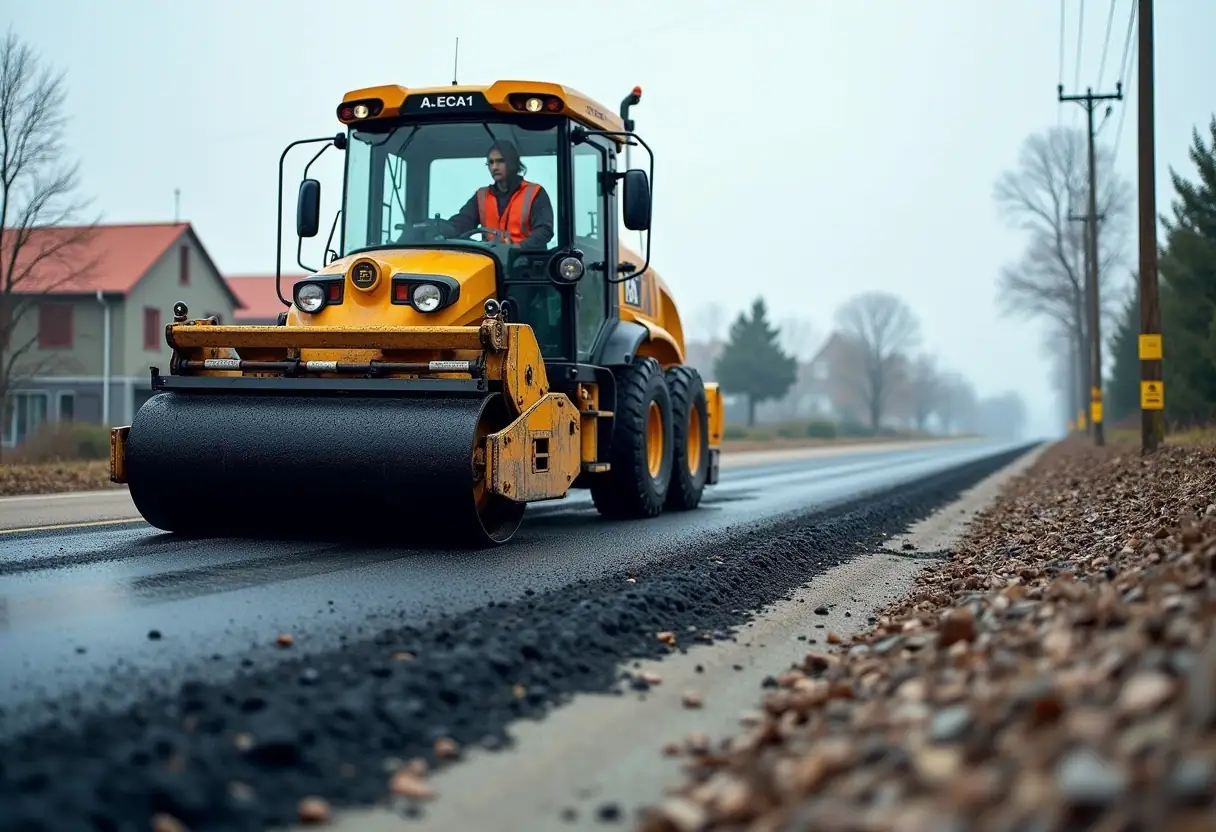
Choosing the Right Road Construction Equipment: A Complete Guide
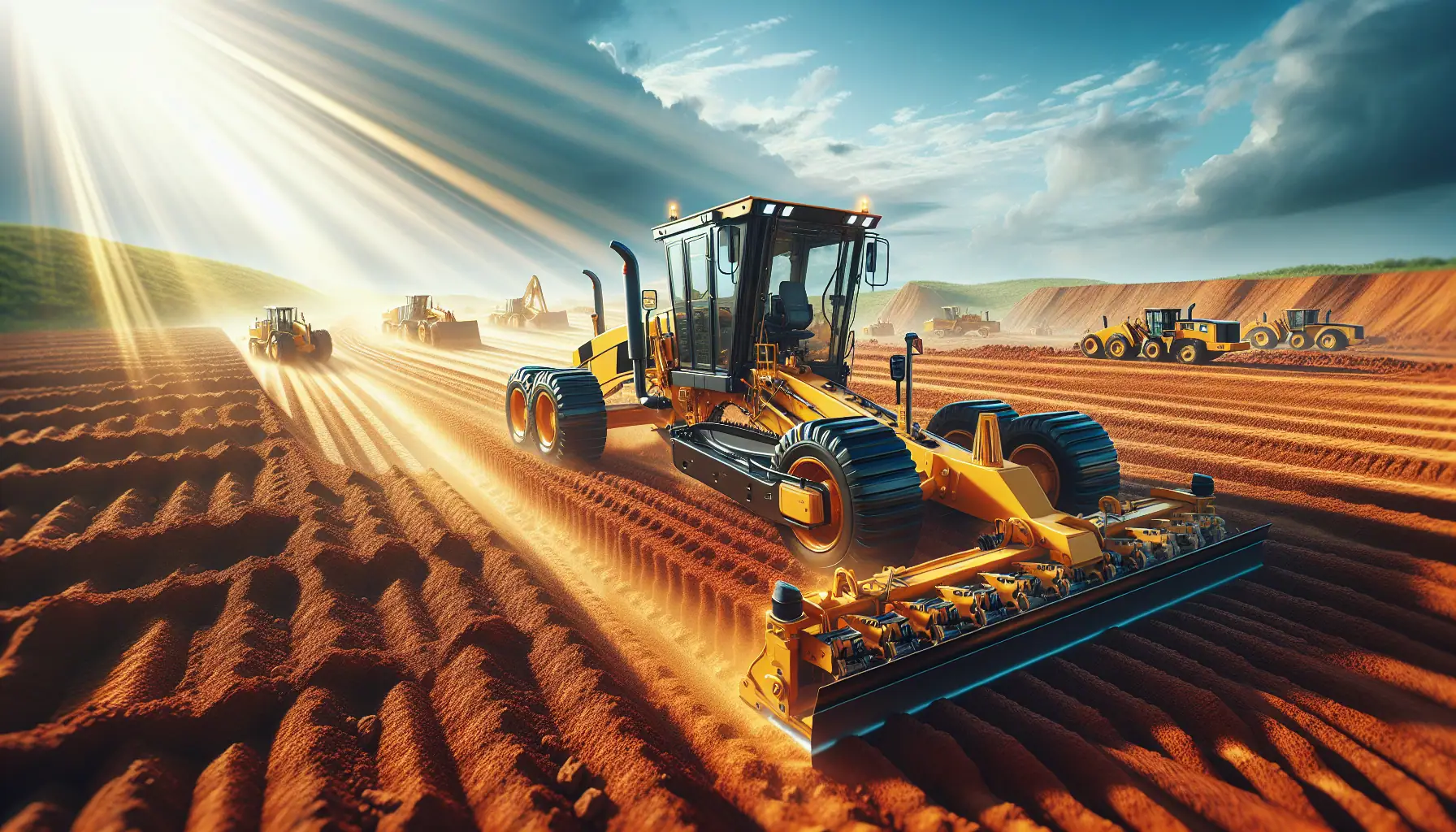
Motor Graders: Key Elements to Consider for Optimal Selection
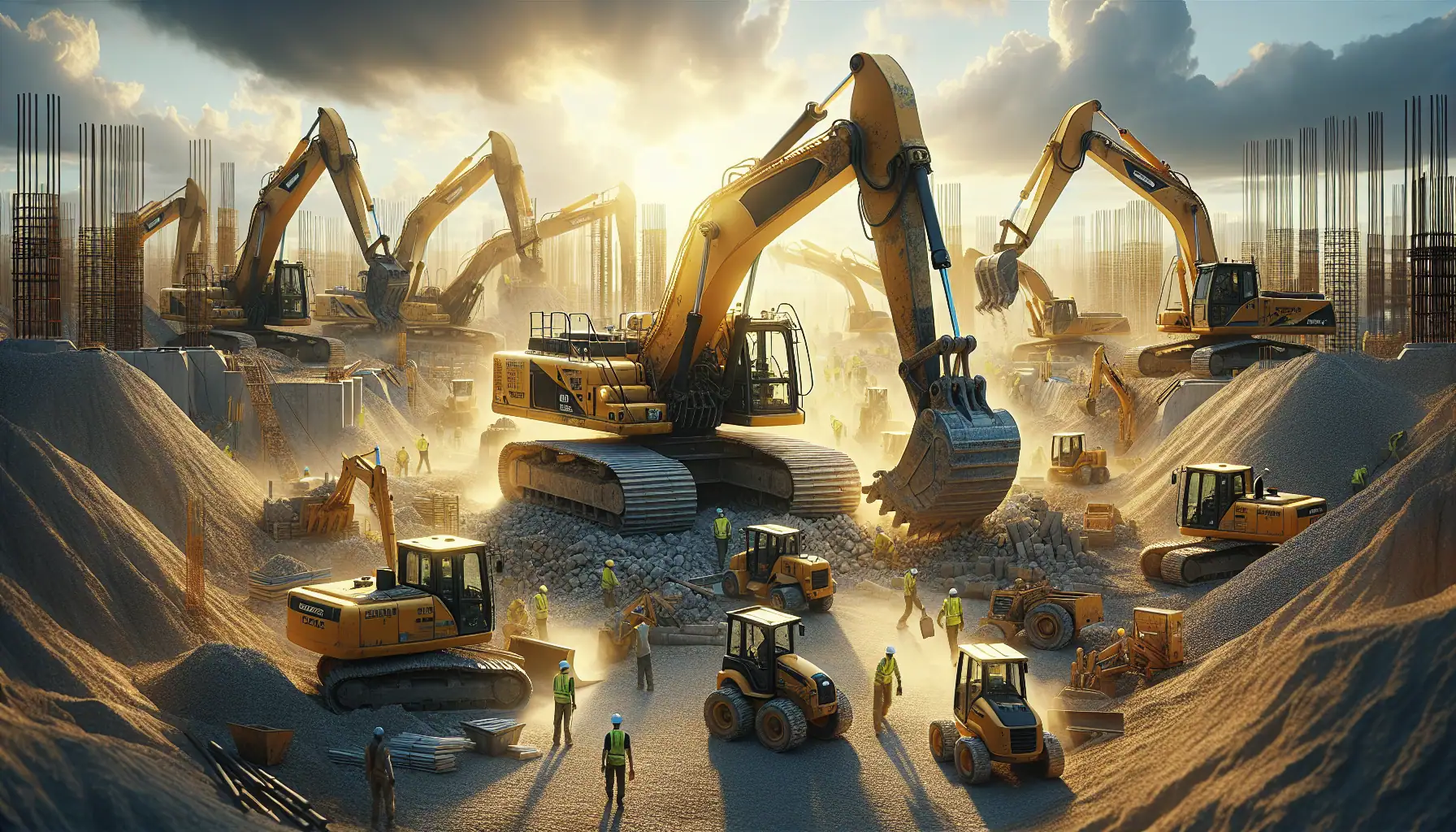
A Detailed Guide to Choosing Excavators for Construction Work
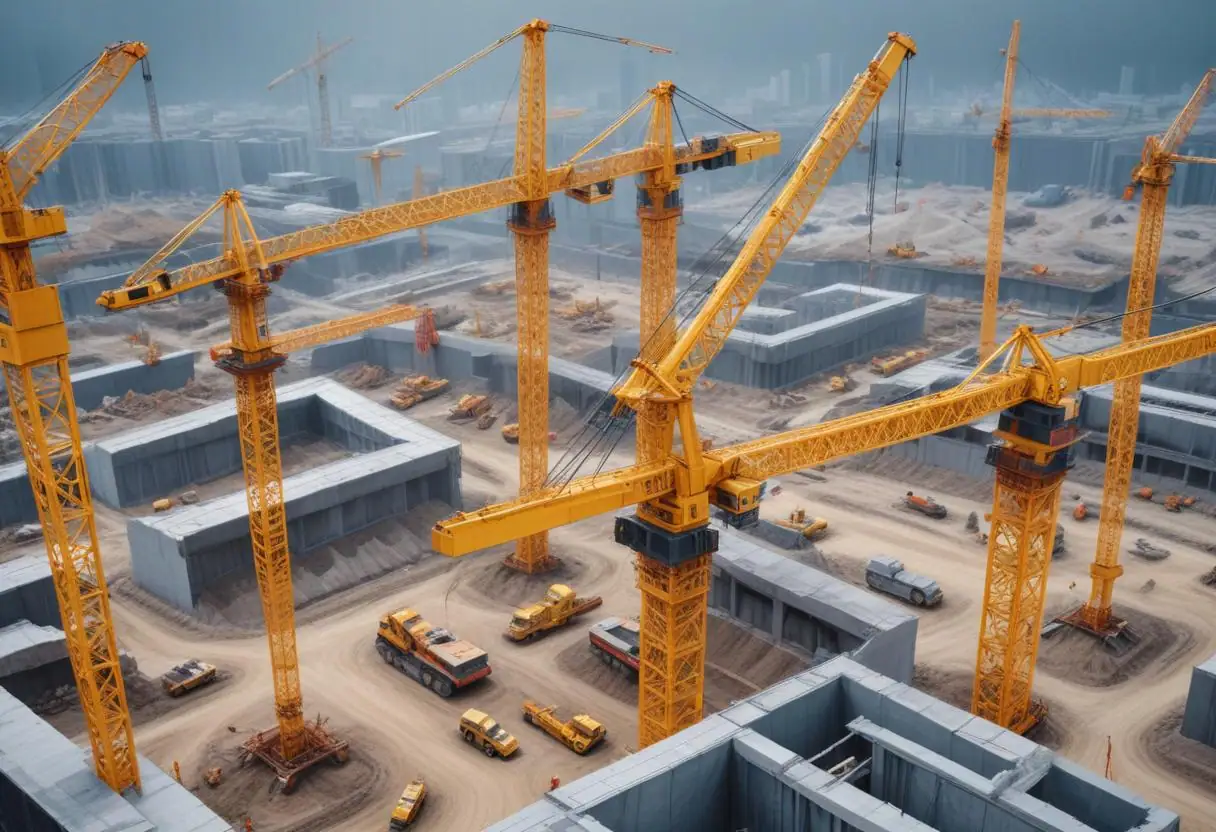
Top Tips for Choosing Cranes for Construction Projects
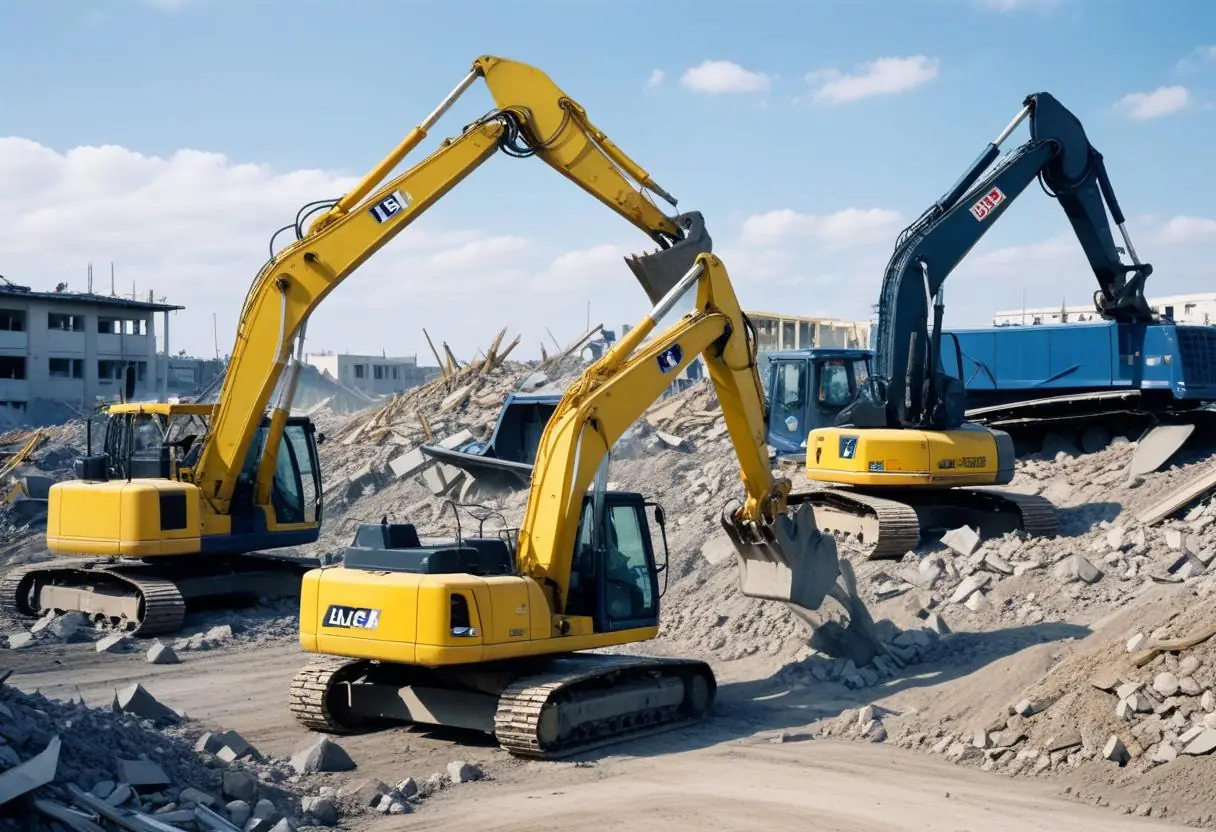
5 Top-Rated Demolition Machines for Construction Professionals
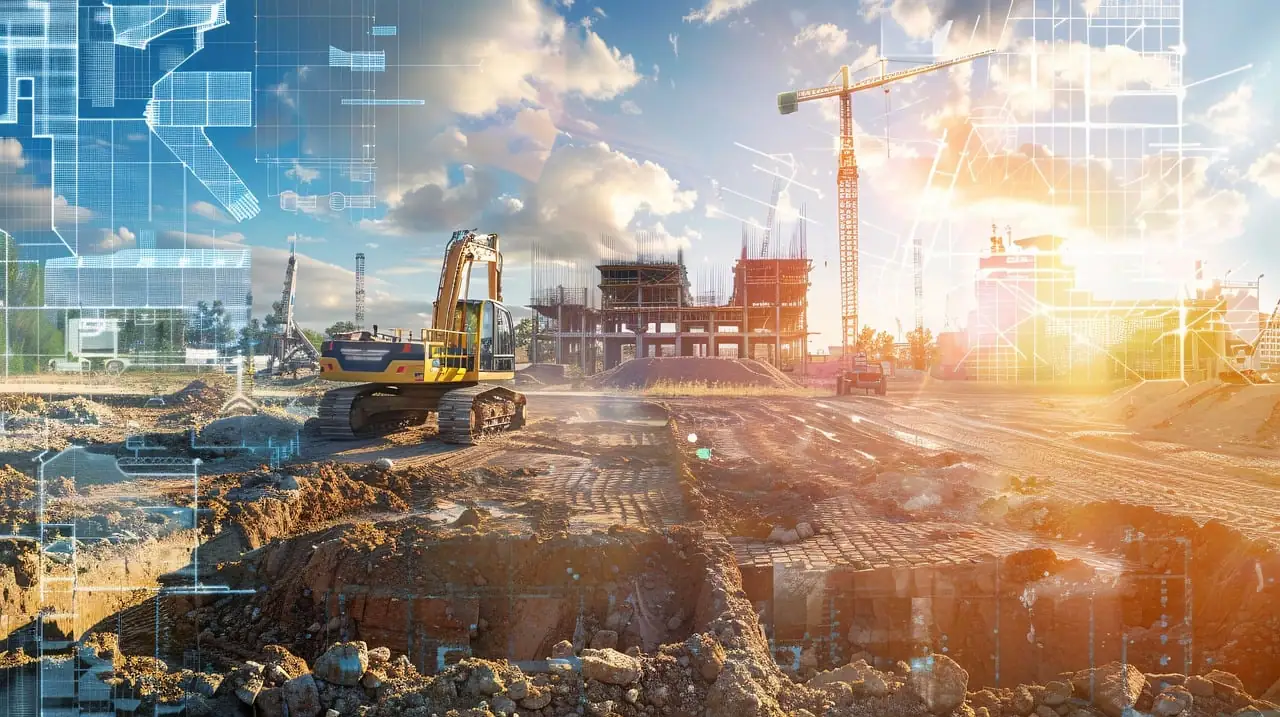
Expert Tips on Choosing Earthmoving Equipment for Large Projects
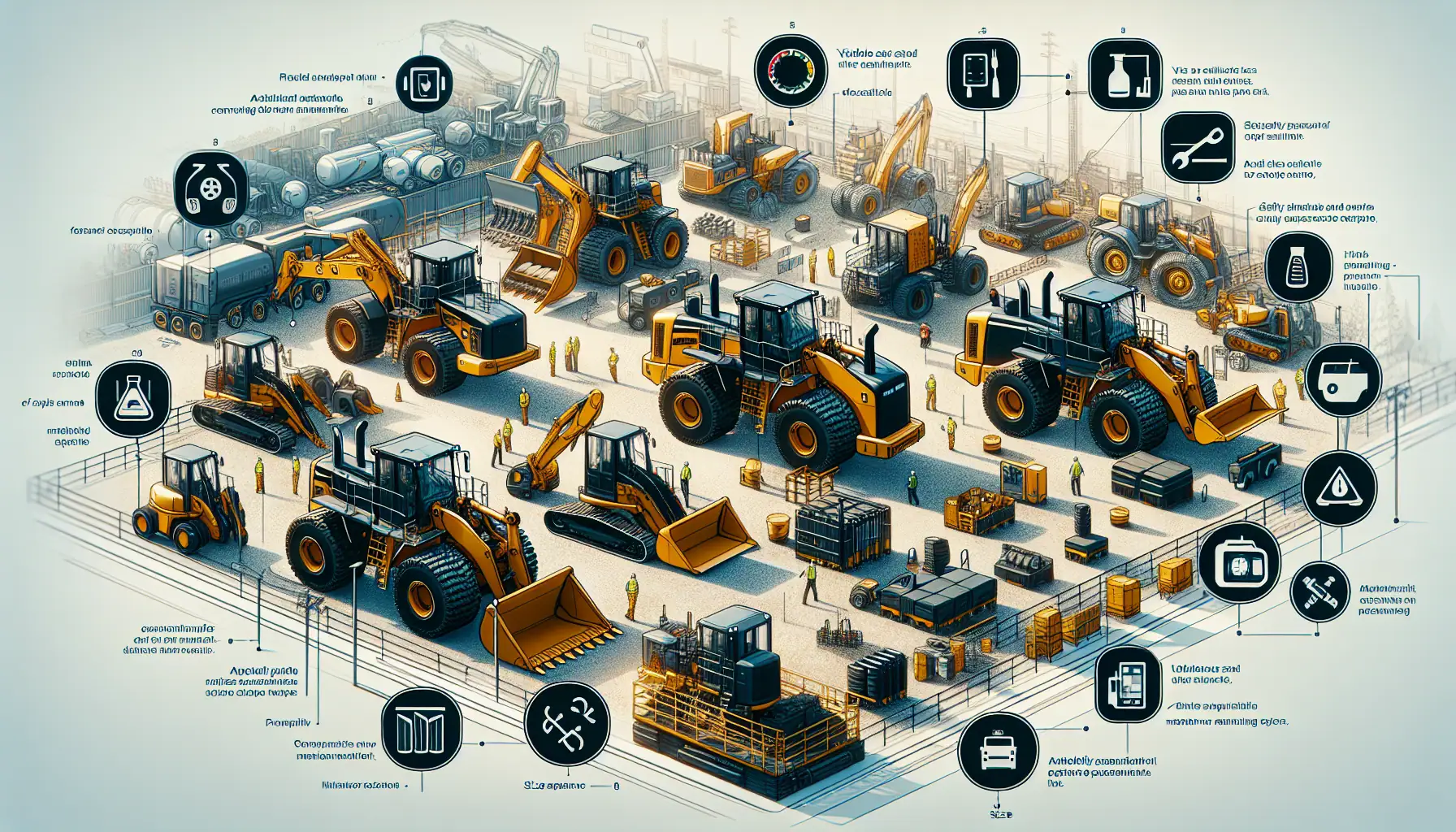
Top Functional Criteria for Selecting Heavy Construction Equipment
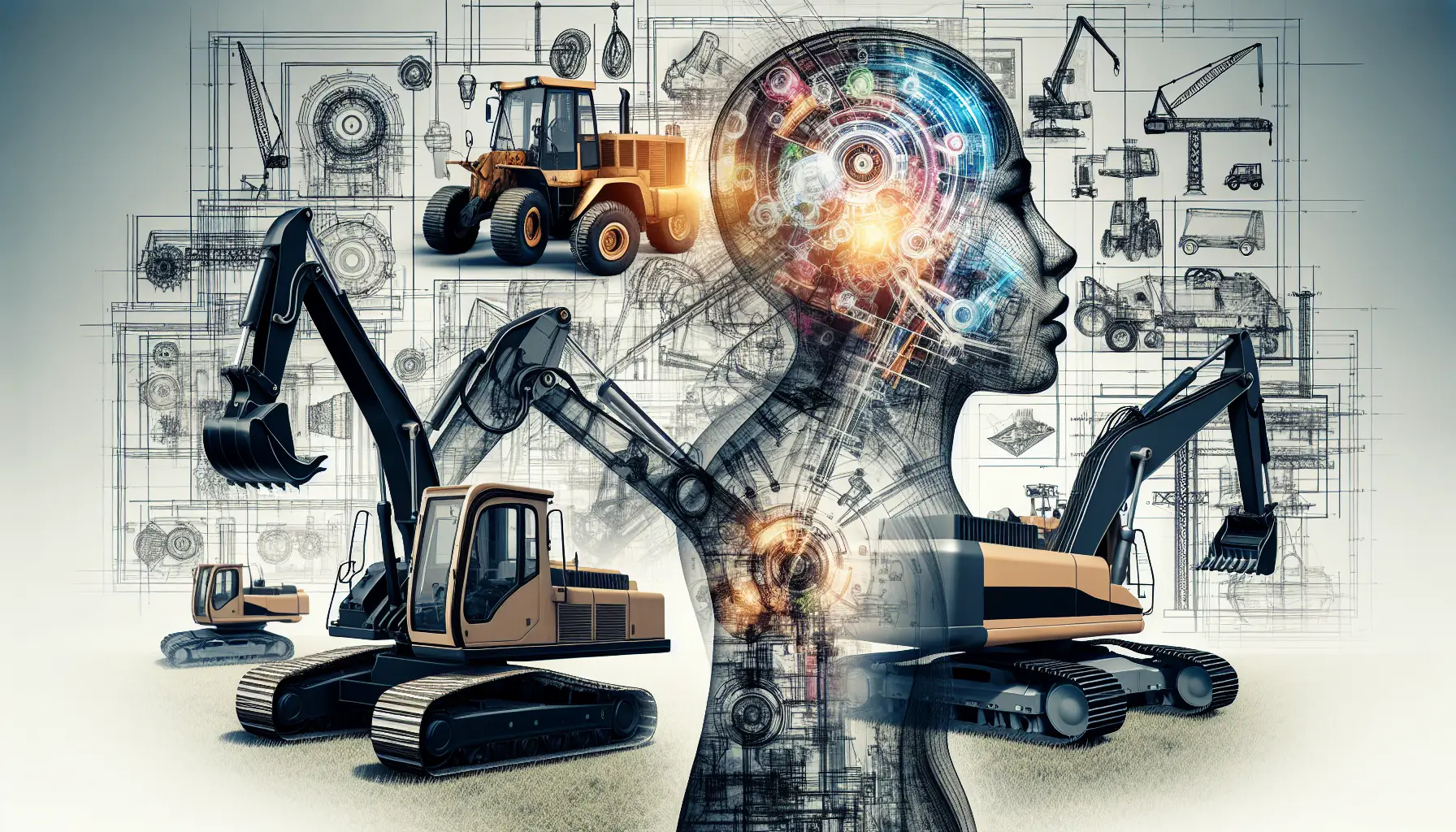
Construction Machinery: Detailed Guide to Equipment Specifications
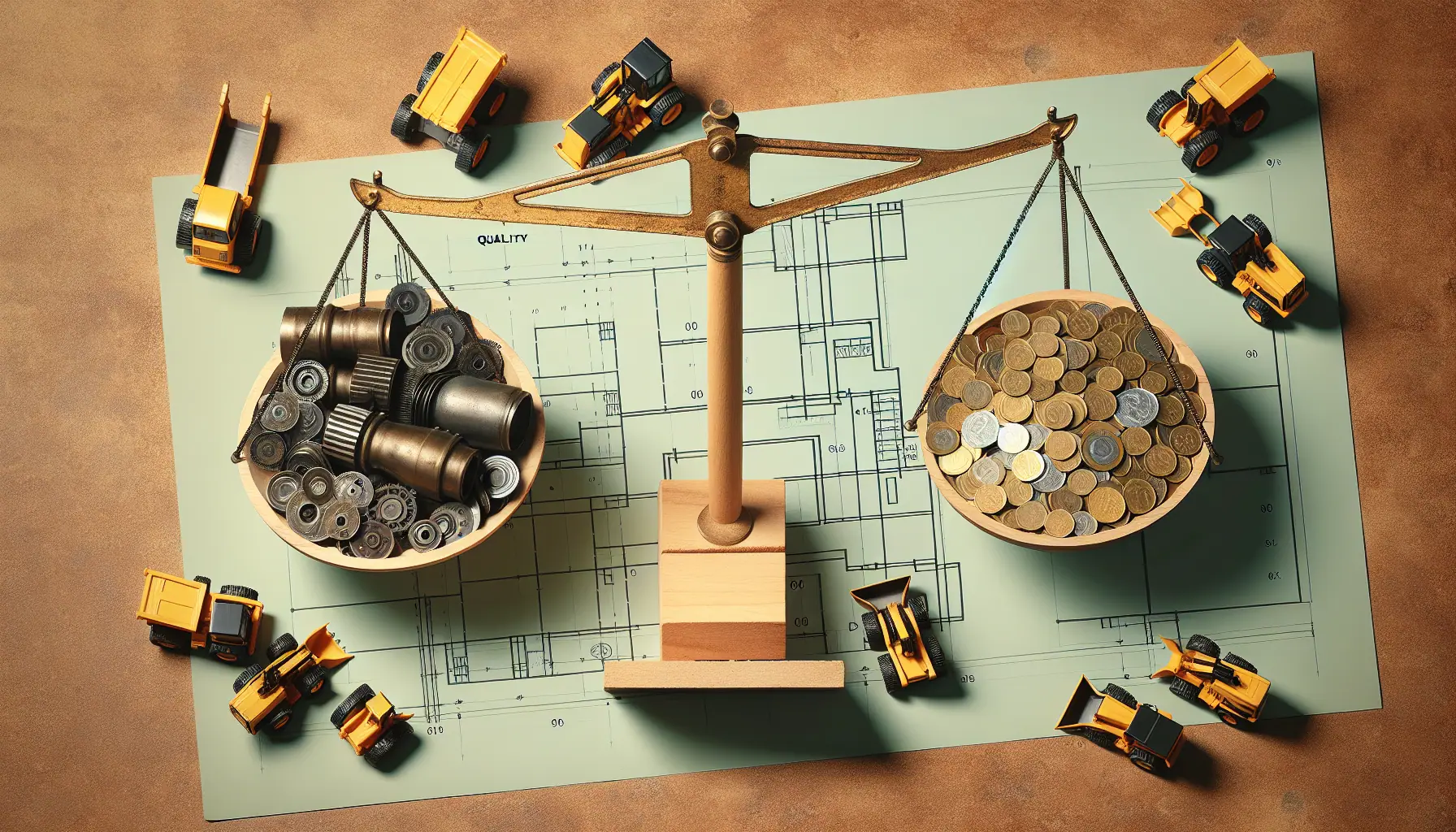
Heavy Machinery Prices: Key Factors in Cost and Quality Balance
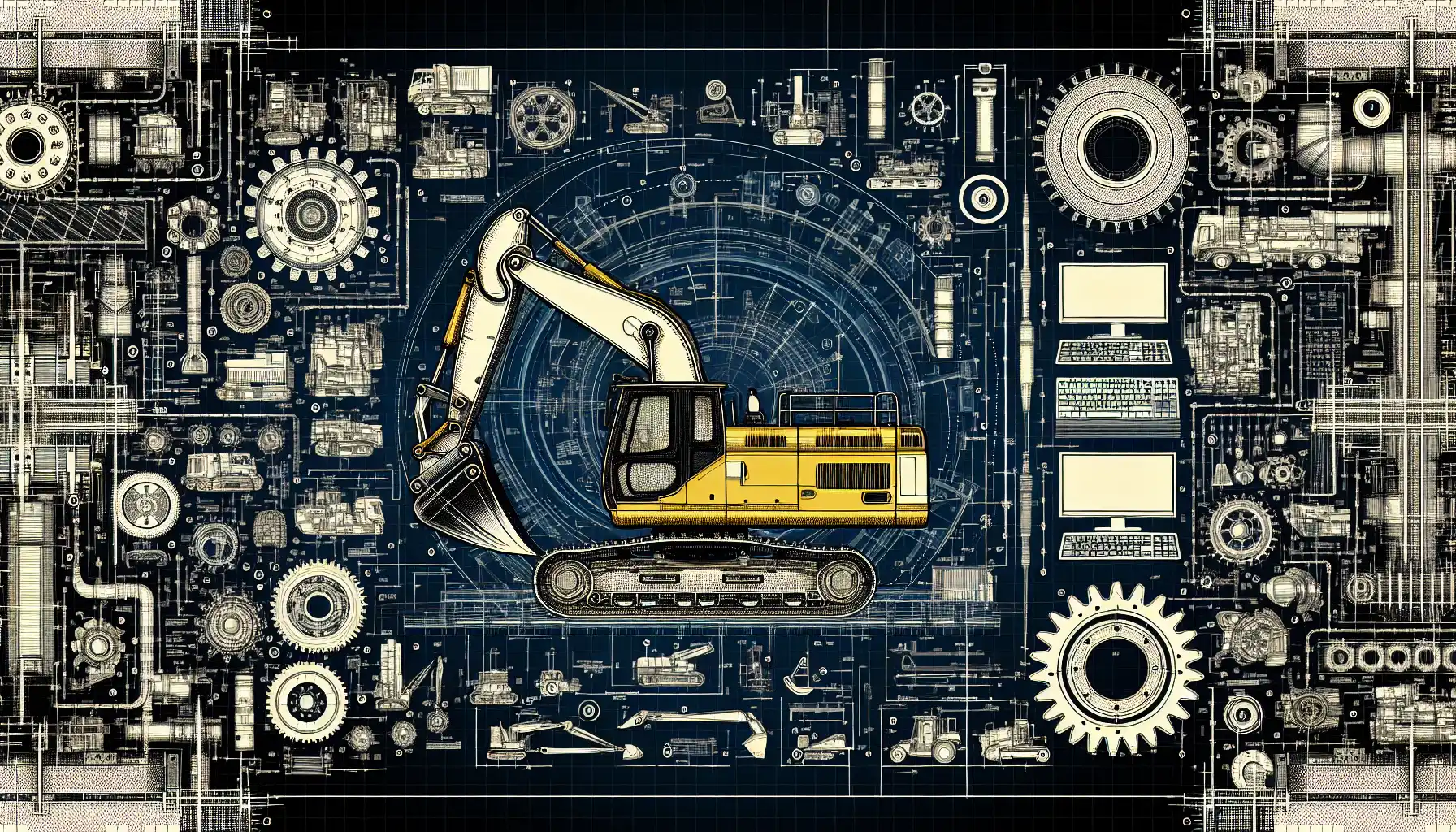
Best Construction Heavy Equipment Brands: Pros and Cons
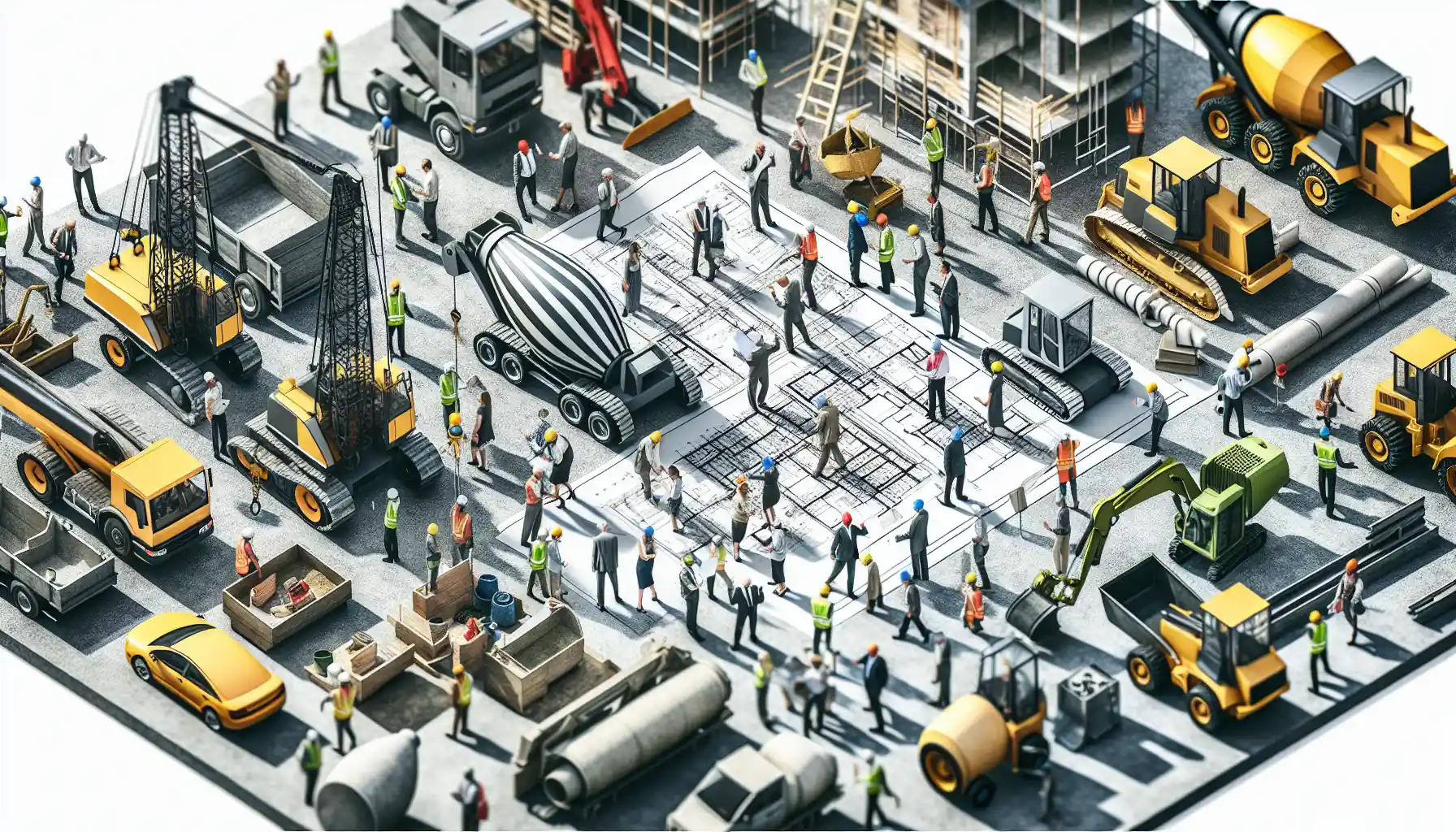
Construction Site Equipment: How to Determine Your Requirements
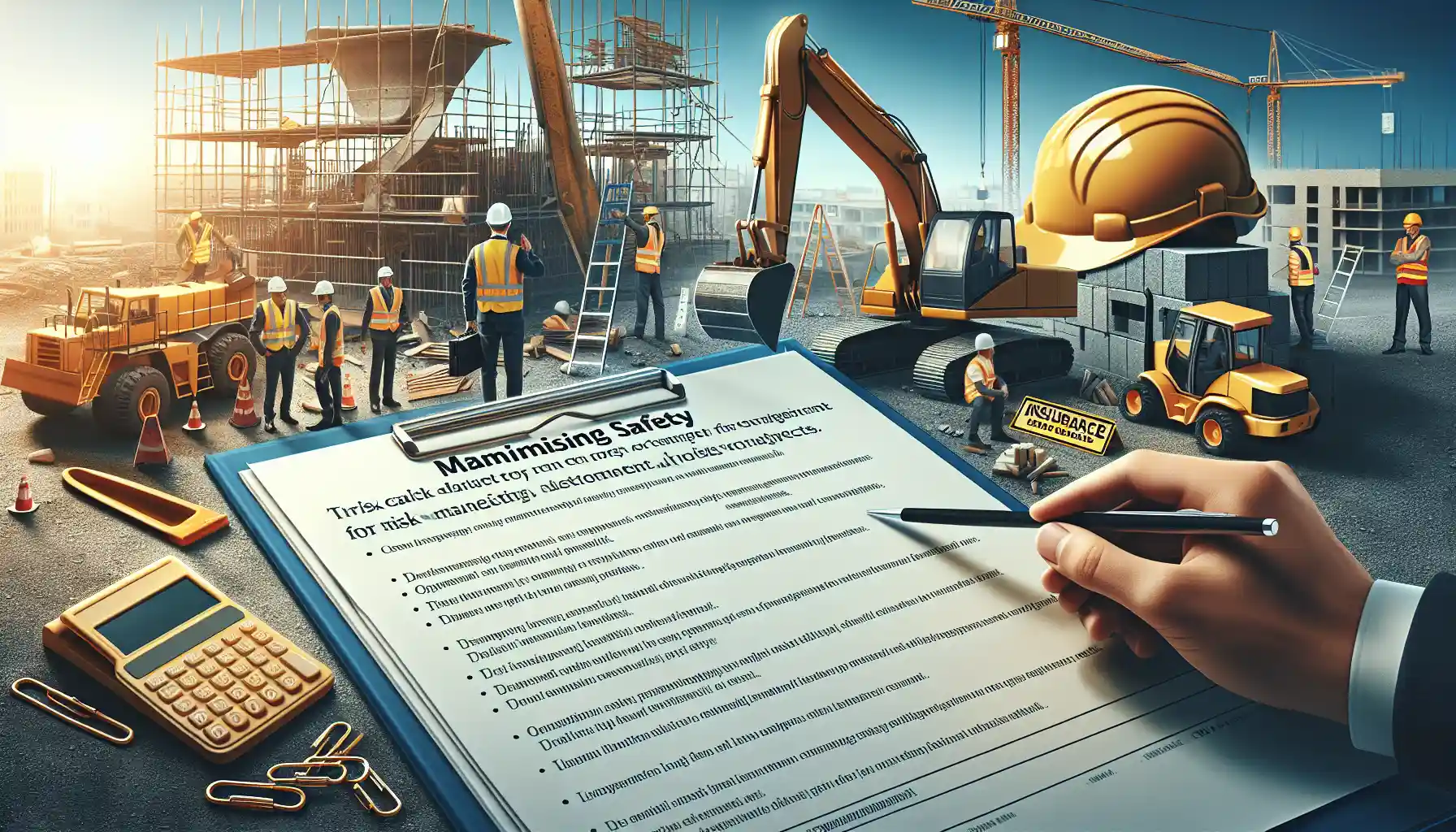
Maximizing Safety: Risk Management for Construction Projects
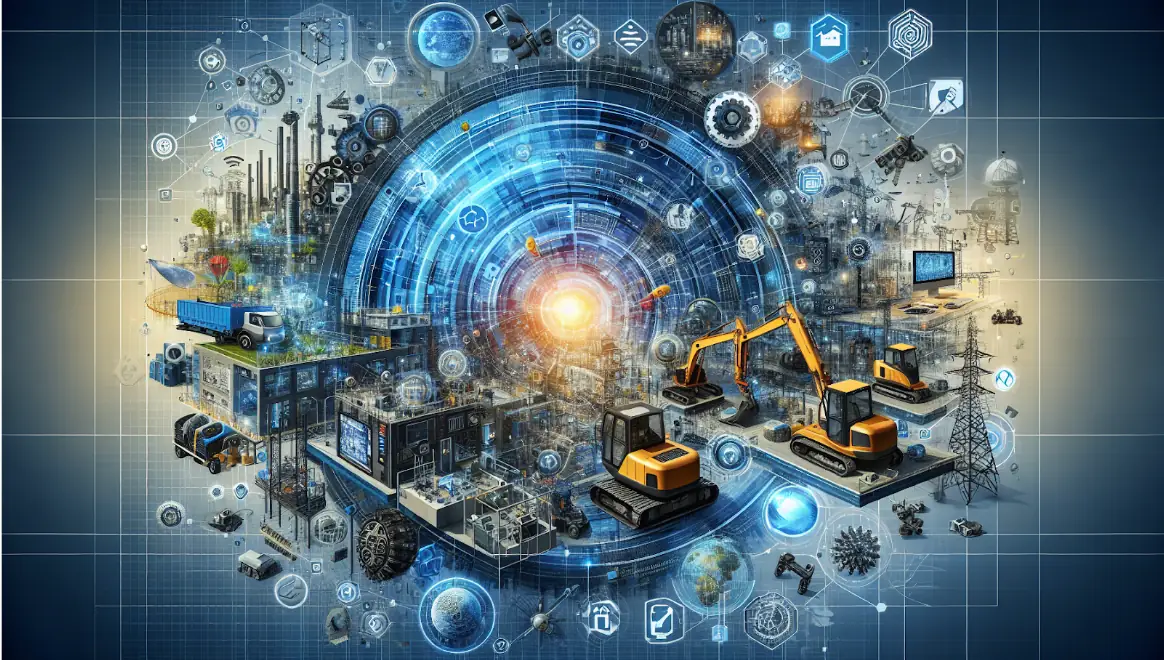
Innovations in Construction: Transforming Machinery and Equipment
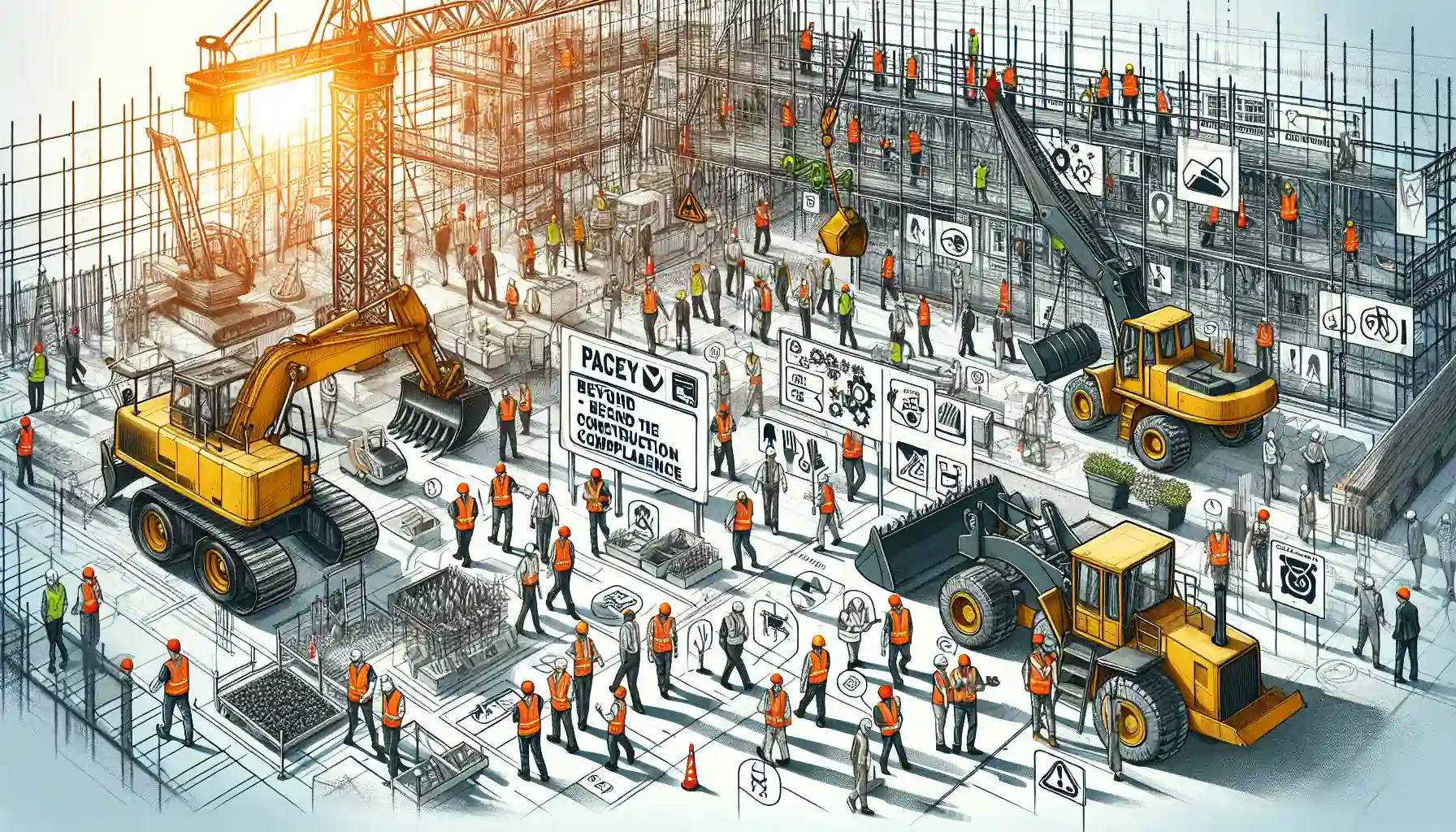
Heavy Equipment Safety: Beyond the Basics in Construction Compliance
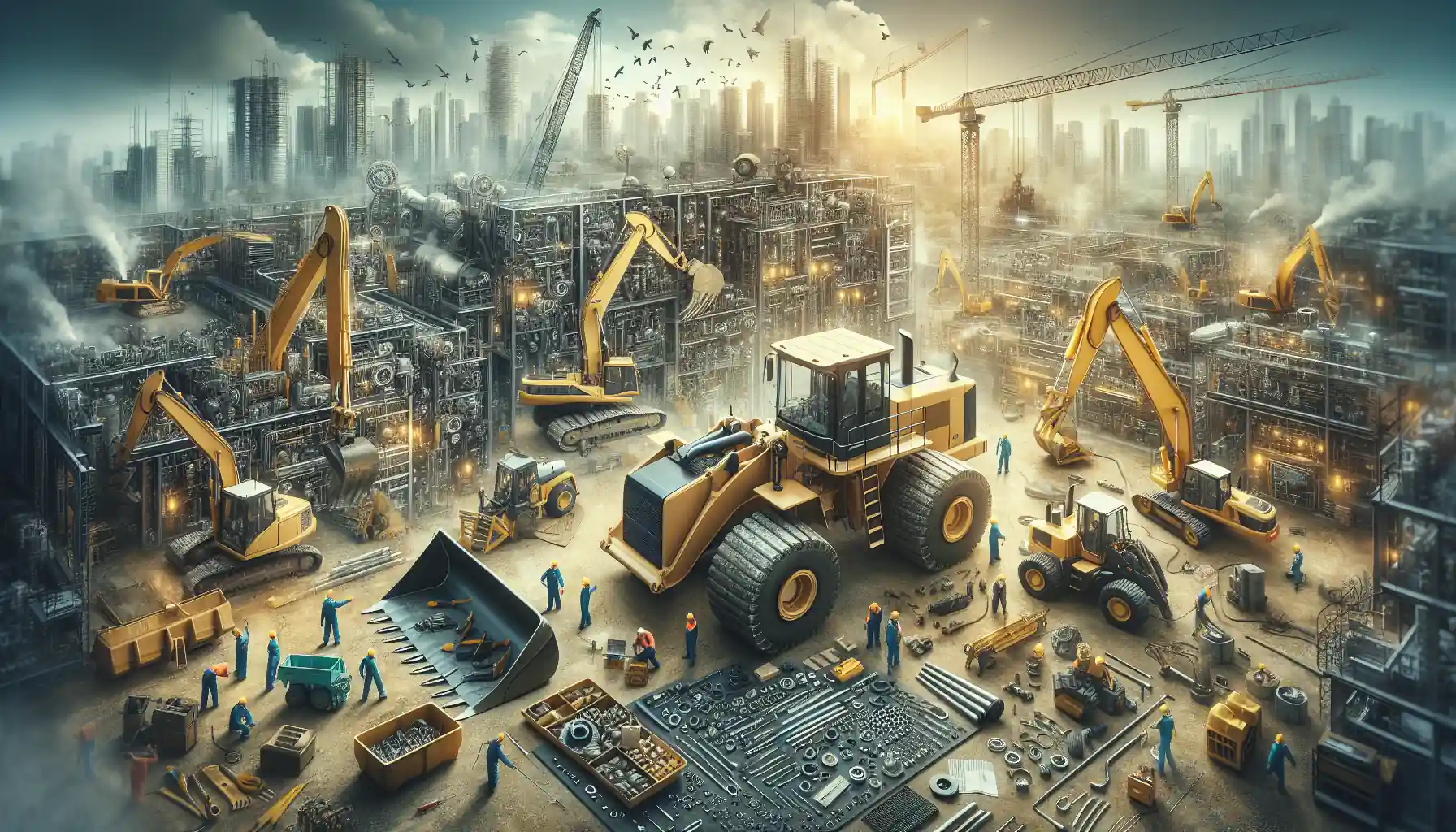
The Essential Handbook for Construction Equipment Repair and Maintenance
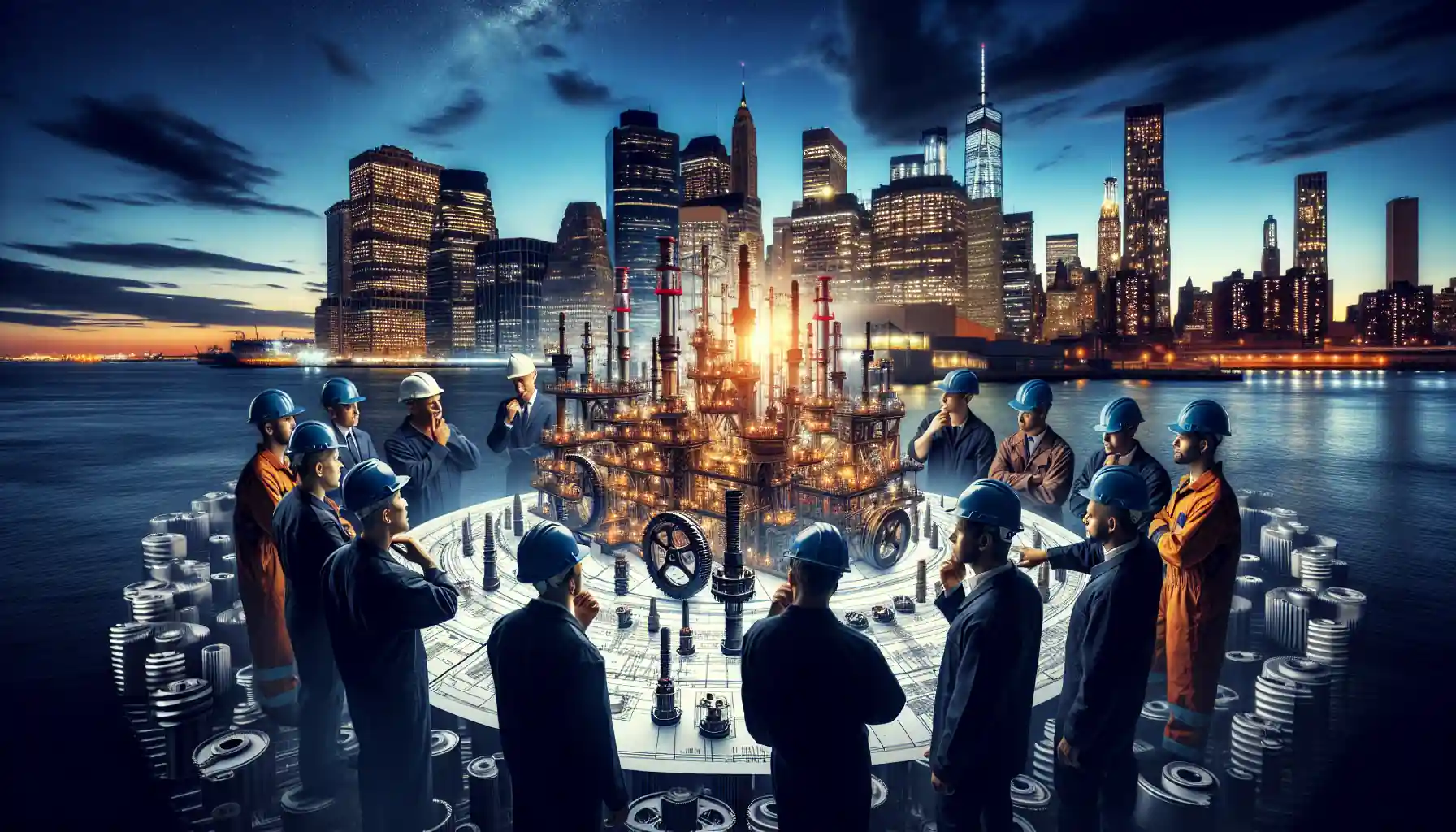
How to Efficiently Source Oil and Gas Machinery Parts in NYC
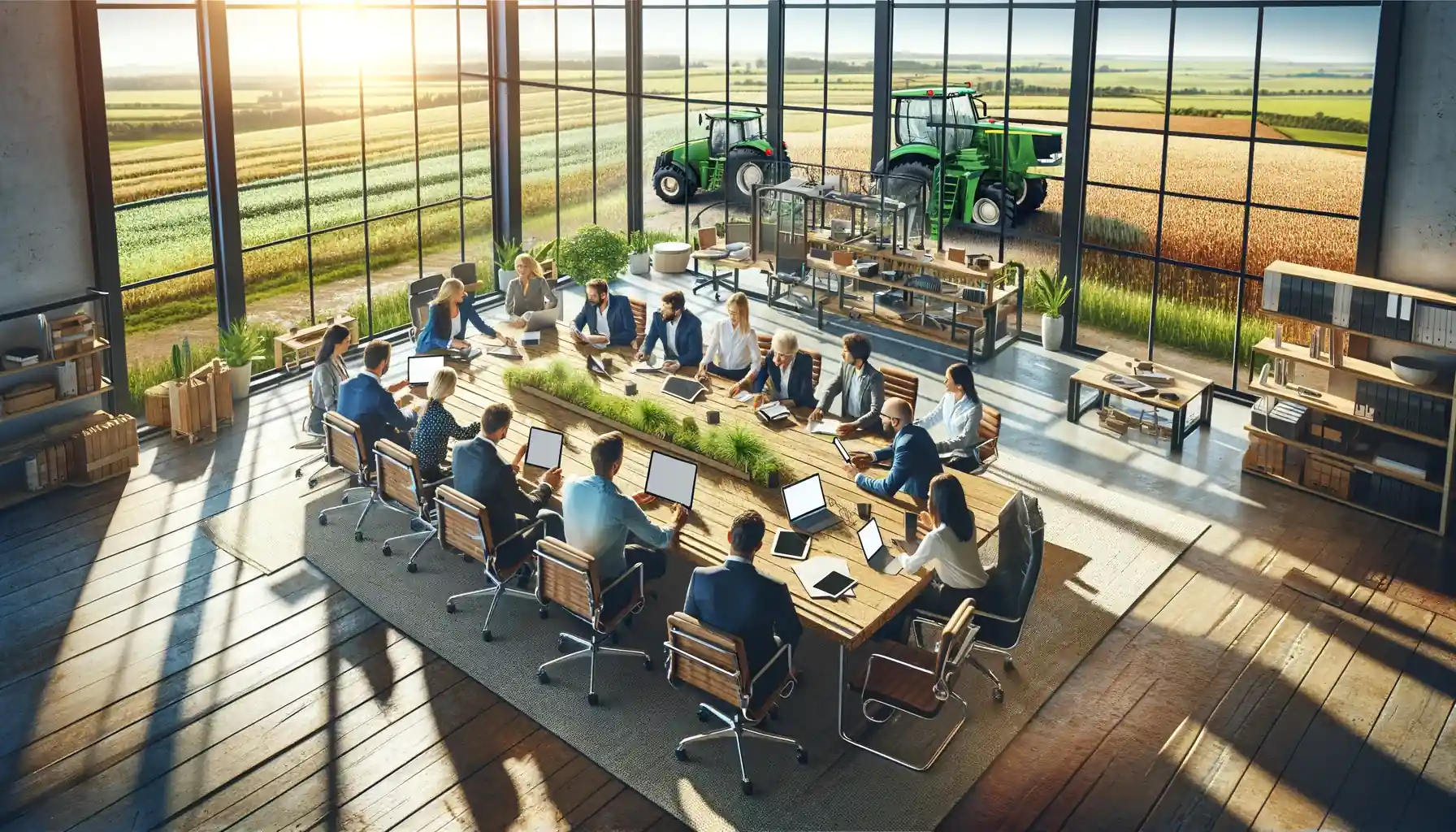
Essential Guide to Sourcing Agriculture Equipment Parts
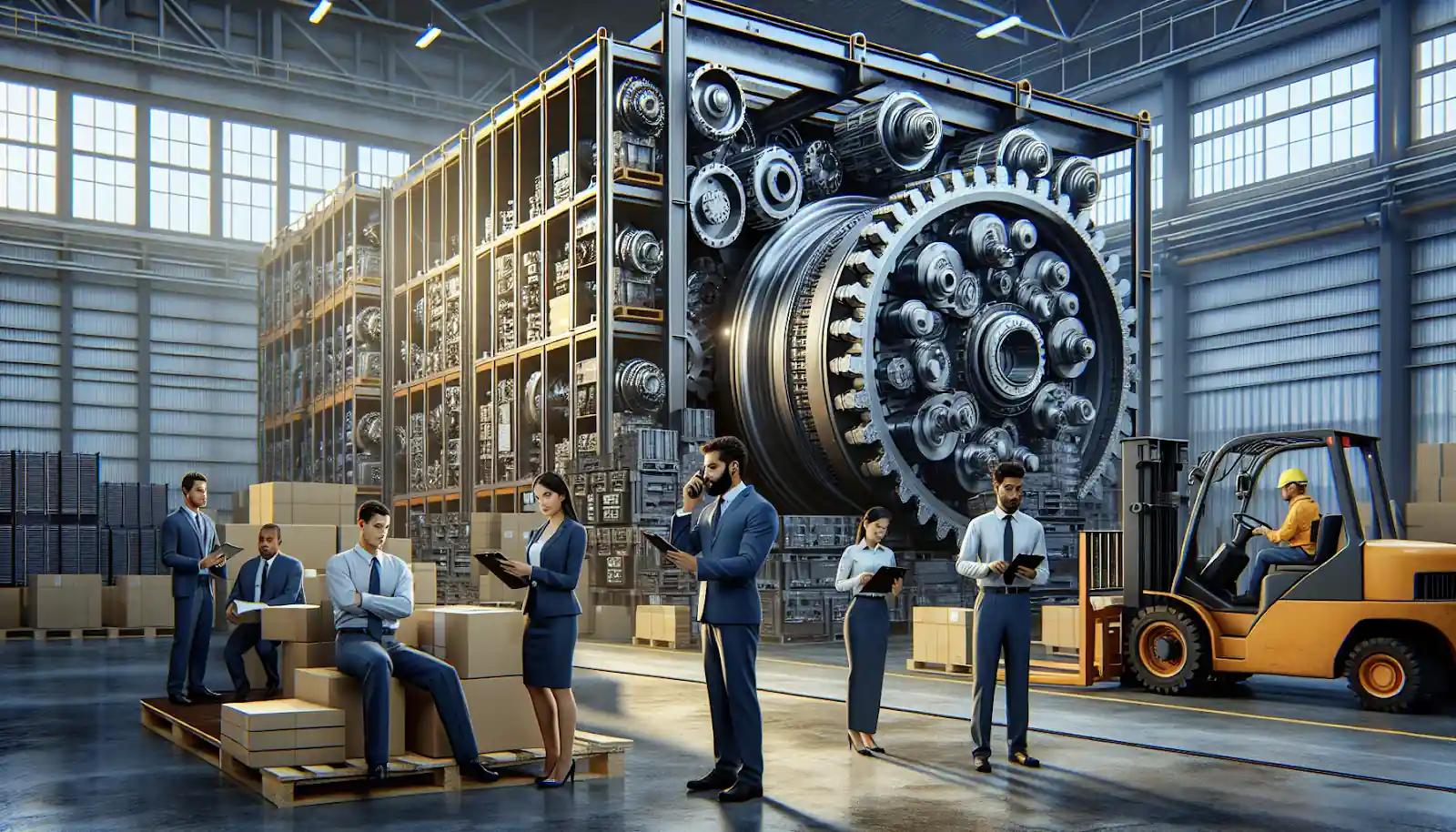
How to Source Mining Machinery Parts: Tips and Strategies
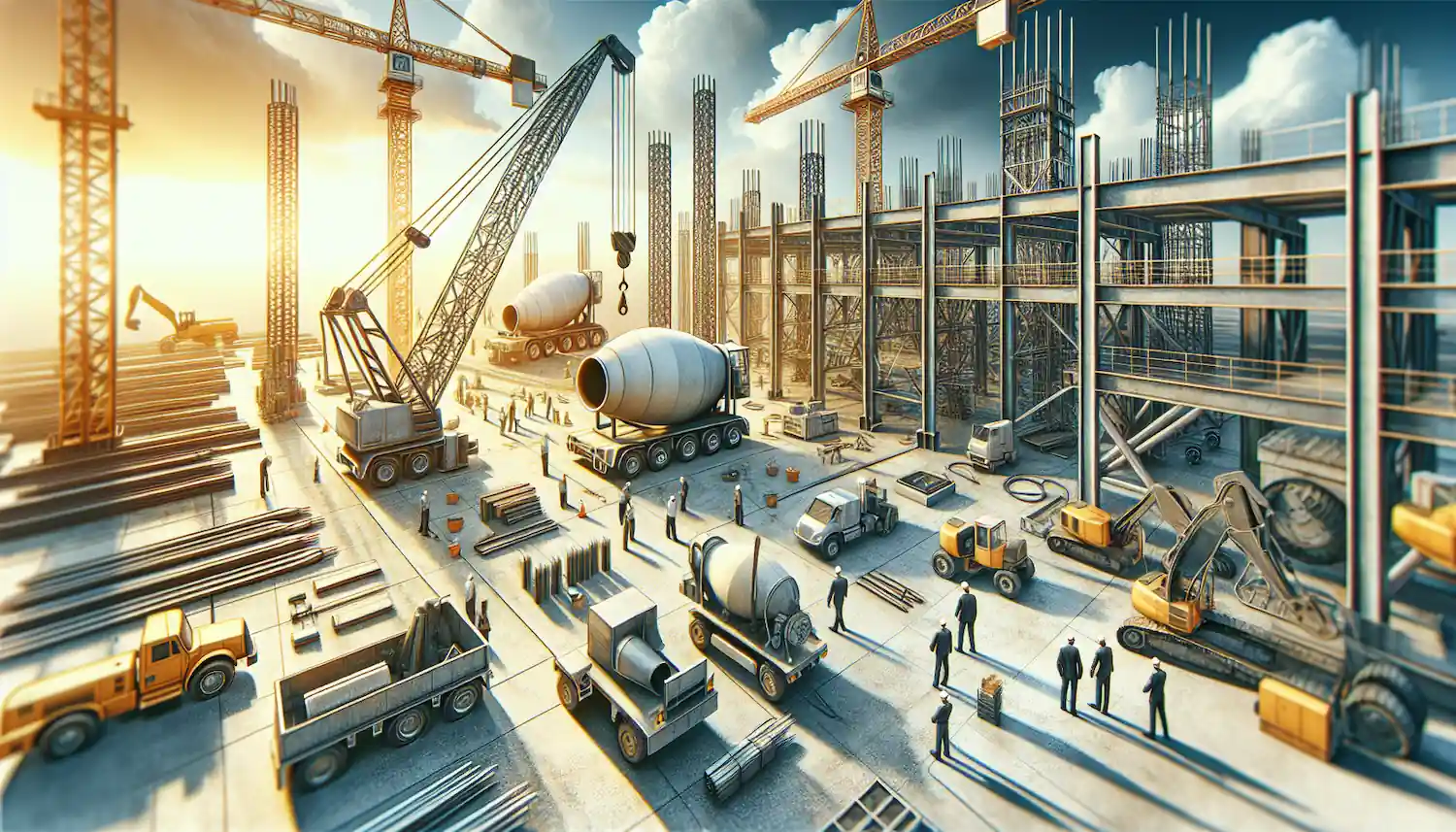