4 Key Steps to Form a Construction Machinery QC Team
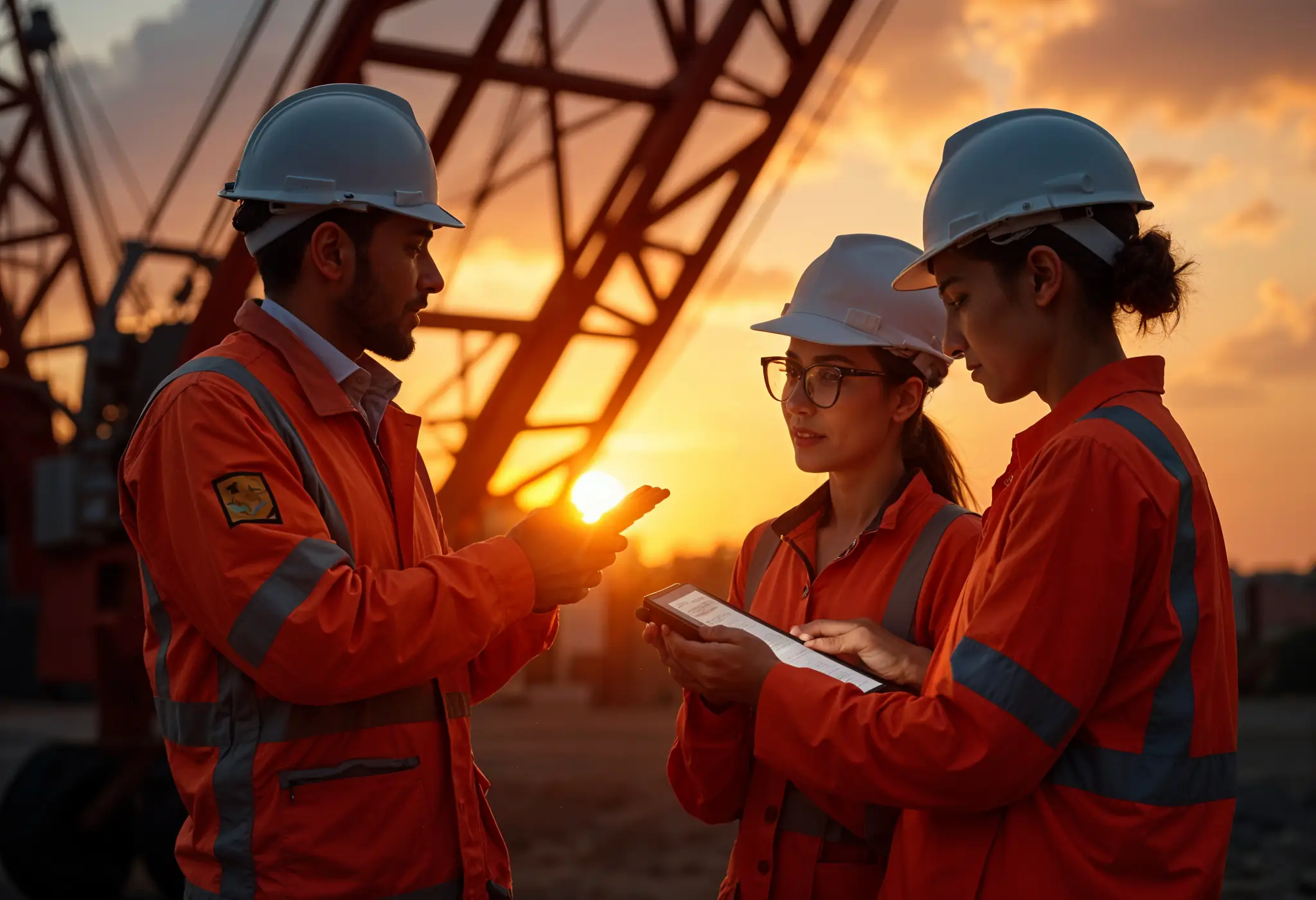
In this guide, we'll explore the essential steps to form a construction quality control team that drives excellence. You'll discover how to define roles and responsibilities, establish comprehensive construction quality control plan, and implement training strategies to empower your team. We'll also delve into the latest technological advancements that are revolutionizing construction site quality control.
By the end, you'll have the knowledge to create a quality control manager construction team that ensures your projects stand out in the competitive construction landscape.
Defining Roles and Responsibilities
To establish an effective construction quality control team, it's crucial to clearly define the roles and responsibilities of key team members. This ensures that everyone understands their part in maintaining high-quality standards throughout the project.
Quality Manager
.webp)
The Quality Manager plays a pivotal role in the construction quality control team. They are responsible for developing and implementing quality control procedures, ensuring compliance with industry standards, and overseeing all quality-related activities on the project. Their duties include preparing and maintaining the quality assurance manual, conducting internal and external audits, and monitoring the disposition of nonconformance reports. The Quality Manager also coordinates with the site Quality Control Manager and procurement team to ensure all quality control measures are properly implemented.
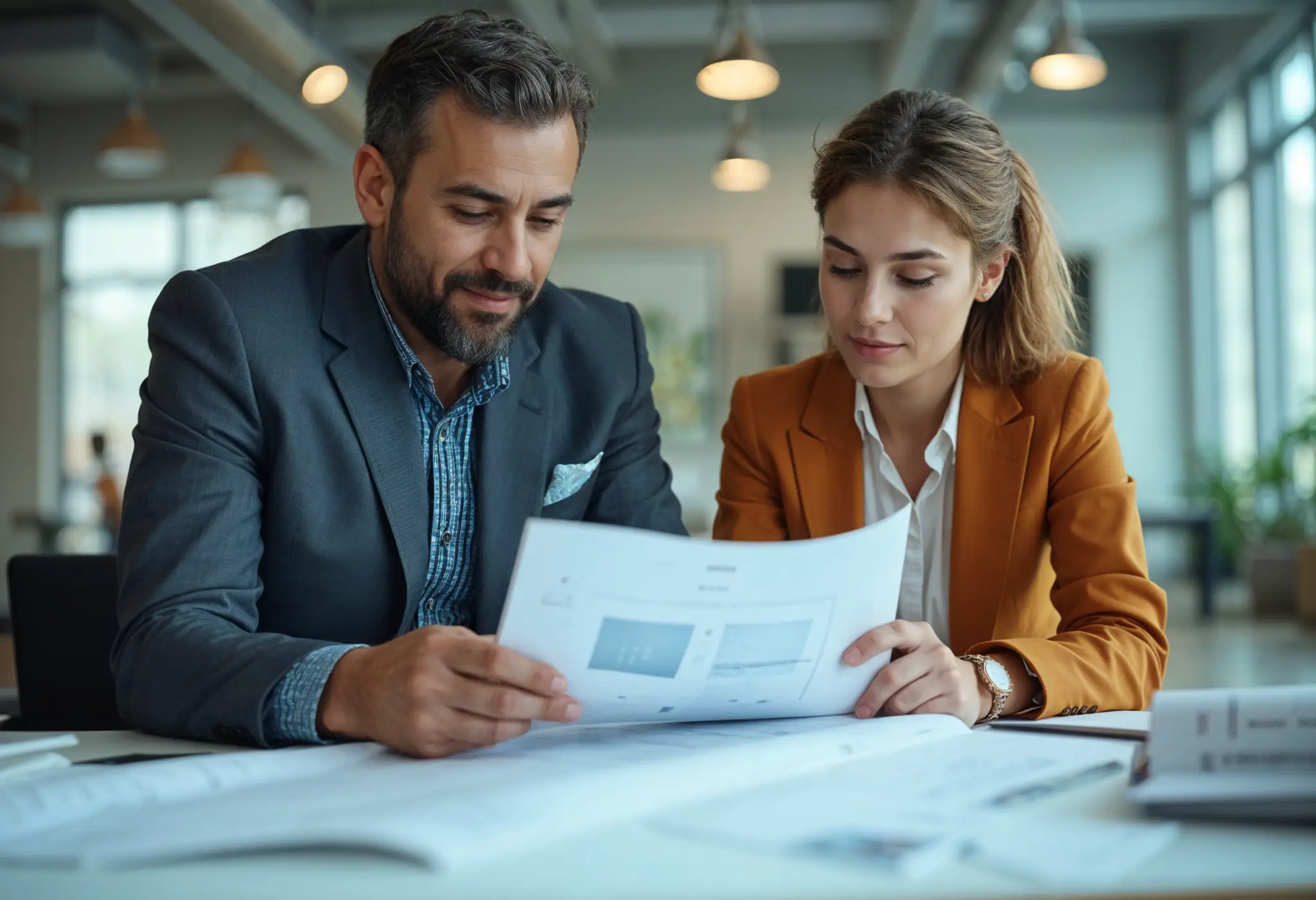
Project Manager
The Project Manager oversees the entire construction project, including quality control aspects. They are responsible for providing adequate resources for quality assurance and demonstrating a commitment to quality throughout the project. Project Managers work closely with the Quality Manager to ensure that quality standards are met and that any issues are addressed promptly. They also play a crucial role in communicating quality requirements to all stakeholders, including subcontractors and suppliers.
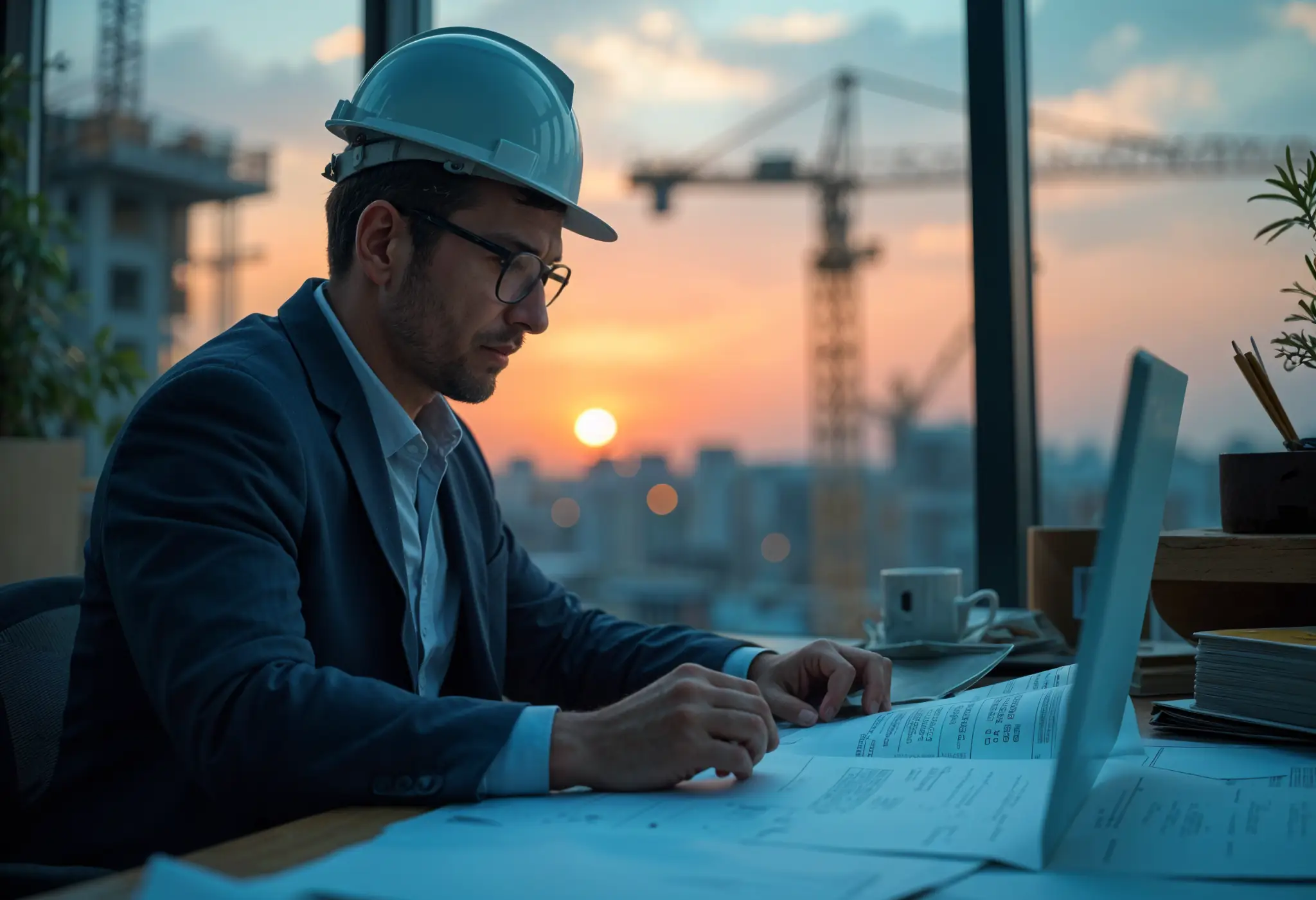
Superintendent
The Superintendent serves as the eyes and ears of the contractor on the construction site, ensuring that work meets the required quality standards on a day-to-day basis. They are responsible for conducting quality inspections, accurately assessing subcontractor performance, and ensuring that quality standards are achieved before approving work completion. Superintendents have the authority to stop work if it may adversely affect quality or cover up a defect, and they can direct the removal and replacement of any non-conforming work.
By clearly defining these roles and responsibilities, you can create a strong foundation for your construction quality control team. This structure helps ensure that quality standards are maintained throughout the project, leading to better outcomes and increased client satisfaction.
To learn more about forming an effective construction quality control team or to get a free sourcing machinery or parts consultation, contact MCH Parts today.
Establishing Quality Control Procedures
To ensure construction quality control, it's crucial to establish comprehensive procedures. These procedures serve as guidelines for maintaining consistent quality standards across projects and aligning with industry regulations.
Inspection Protocols
Developing robust inspection protocols is essential for effective quality control. Create a standardized checklist that outlines specific components and functions to be inspected for each piece of equipment. This ensures consistency and thoroughness in evaluations. Regular inspections help identify potential hazards, such as worn brakes or faulty electrical systems, reducing the risk of accidents and injuries.
Documentation Requirements
Proper documentation is vital for maintaining quality control records. Implement a system to document all quality control activities, including inspection results, test data, and corrective actions taken. This documentation serves as evidence of compliance and can be crucial for audits or legal matters. Consider using quality control software to streamline the process and provide real-time visibility into project quality.
Corrective Action Plans
Establish clear procedures for addressing non-conformances and quality issues. Develop a corrective action plan that outlines steps to identify, document, and rectify problems. This plan should be specific, measurable, attainable, relevant, and time-bound (S.M.A.R.T.). Include a root cause analysis process to determine the underlying causes of issues and prevent their recurrence.
By implementing these quality control procedures, you can enhance safety, increase efficiency, and reduce maintenance costs on your construction site. Remember to regularly review and update these procedures to ensure they remain effective and aligned with industry standards.
To learn more about establishing effective quality control procedures or to get a free sourcing machinery or parts consultation, contact MCH Parts today.
Implementing Training and Communication Strategies
To ensure effective quality control in construction projects, it's crucial to implement robust training programs and establish clear communication channels. These strategies help maintain high standards and promote collaboration among team members.
Quality Control Training Programs
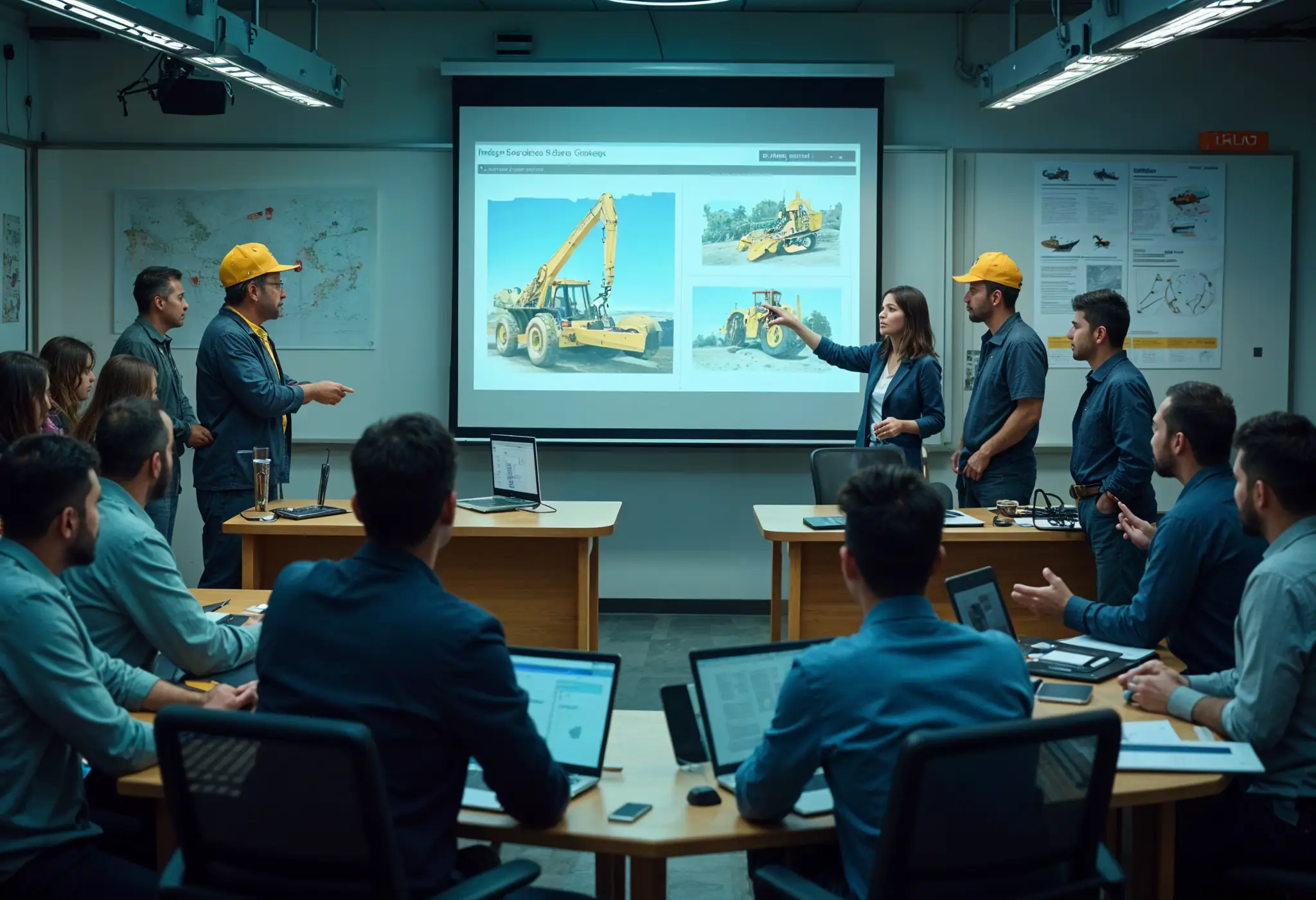
Investing in quality control training programs is essential for developing a skilled workforce. These programs equip workers with the knowledge and skills needed to conduct audits, inspections, and performance evaluations effectively. Many organizations offer specialized courses tailored to the construction industry.
For instance, the Construction Quality Management for Contractors (CQM-C) course, created by the U.S. Army Corps of Engineers and other organizations, is designed for construction professionals working in the public sector. This two-day course covers quality control processes, supplier quality, and inspections. Upon completion, participants are considered qualified to work as Quality Control Managers by U.S. Army Corps of Engineers standards.
Another valuable option is the Manager of Quality/Organizational Excellence Certification offered by the American Society for Quality. This certification is suitable for professionals tasked with ensuring quality within their organizations, including those in the construction industry.
Team Communication Channels
Effective communication is vital for maintaining quality standards on construction sites. Establishing clear communication channels helps prevent misunderstandings, reduces errors, and promotes collaboration among team members.
Regular team meetings provide a platform for open dialog and ensure that all members understand their roles and responsibilities. These meetings allow for sharing updates, discussing challenges, and collaborating on solutions.
Leveraging technology can greatly enhance communication within construction teams. Using communication tools such as instant messaging platforms or quality control software allows for real-time information sharing and efficient collaboration, even when team members are geographically dispersed.
To learn more about implementing effective training and communication strategies or to get a free sourcing machinery or parts consultation, contact MCH Parts today.
Leveraging Technology for Quality Management
In today's construction landscape, technology plays a crucial role in enhancing construction quality control. By implementing advanced software solutions, contractors can streamline processes, improve communication, and ensure adherence to quality standards.
Quality Management Software
Quality management software has become an essential tool for construction quality control teams. These digital platforms offer a centralized repository for project documents, inspection checklists, and quality control procedures. With features like real-time field reporting and photo documentation, quality control managers can quickly identify and address issues on the construction site.
One of the key benefits of quality management software is its ability to reduce rework and associated costs. According to a recent report, errors, including deficiencies and rework, can add 5% to the total project cost. By implementing a robust quality control system, contractors can significantly minimize these expenses and improve overall project efficiency.
Mobile Inspection Tools
.webp)
Mobile inspection tools have revolutionized the way quality control teams operate on construction sites. These applications allow inspectors to conduct thorough assessments using their smartphones or tablets, eliminating the need for paper-based checklists and manual data entry.
With mobile inspection apps, quality control managers can easily document issues, attach photos or videos, and assign tasks to team members for prompt resolution. This real-time communication helps prevent miscommunication, which is responsible for 48% of rework in the construction industry.
To learn more about leveraging technology for quality management or to get a free sourcing machinery or parts consultation, contact MCH Parts today.
Conclusion
To wrap up, forming a top-notch construction machinery quality control team is key to ensuring project success and safety. By clearly defining roles, setting up solid procedures, and investing in training, companies can build a team that maintains high standards throughout the construction process. The use of cutting-edge technology, like quality management software and mobile inspection tools, further enhances the team's ability to spot and fix issues quickly.
The steps outlined in this guide provide a strong foundation to create a quality control team that stands out in the competitive construction landscape. By putting these practices into action, companies can boost productivity, cut down on errors, and deliver outstanding results.
Consider reaching out to MCH Parts for a free sourcing machinery or parts consultation, ensuring your business benefits from top-tier equipment and service. With a well-formed quality control team and the right tools, construction projects can achieve new levels of excellence and client satisfaction.
FAQs
What are the steps involved in building a quality control team?
To develop a team dedicated to quality control, start by setting clear objectives and standards. Recruit and train individuals who align with these goals. Foster a culture of teamwork and open communication, acknowledge and reward high-quality work, and promote ongoing improvement and innovation.
What are the five critical steps in quality control?
The five essential components of quality control include:
- Product Design Analysis: Ensuring collaboration between the design and production teams.
- Raw Material Inspection: Setting quality standards for suppliers.
- In-Process Quality Control: Monitoring and adjusting processes during production.
- Finished Product Inspection: Assessing products post-manufacture for quality.
- Quality Audits: Regularly reviewing and improving quality control measures.
What are the four steps to create an effective quality control process?
Creating an efficient quality control plan involves:
- Identifying relevant quality standards.
- Developing a detailed quality control plan.
- Implementing the plan and evaluating its effectiveness.
- Adjusting the quality control plan as necessary to enhance its efficiency.
What are the phases of quality control in construction management?
Quality control in construction management encompasses several stages, including ensuring the accuracy and usefulness of information, managing document control and changes during the construction, overseeing procurement, conducting field inspections and testing, and performing the final review of the facility.
Read More
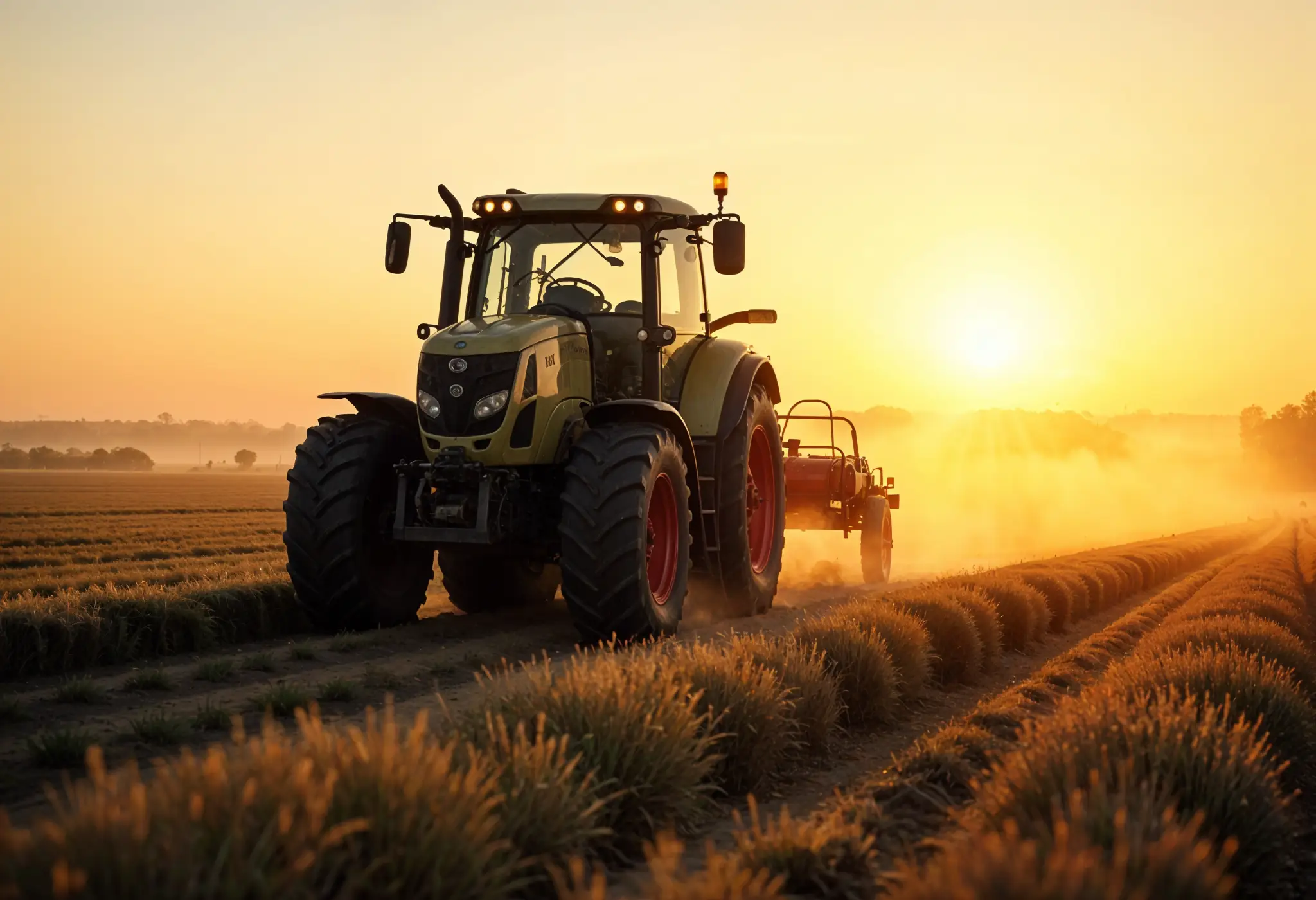
Top Hydraulic Components for Agricultural Equipment in 2025: Complete Guide
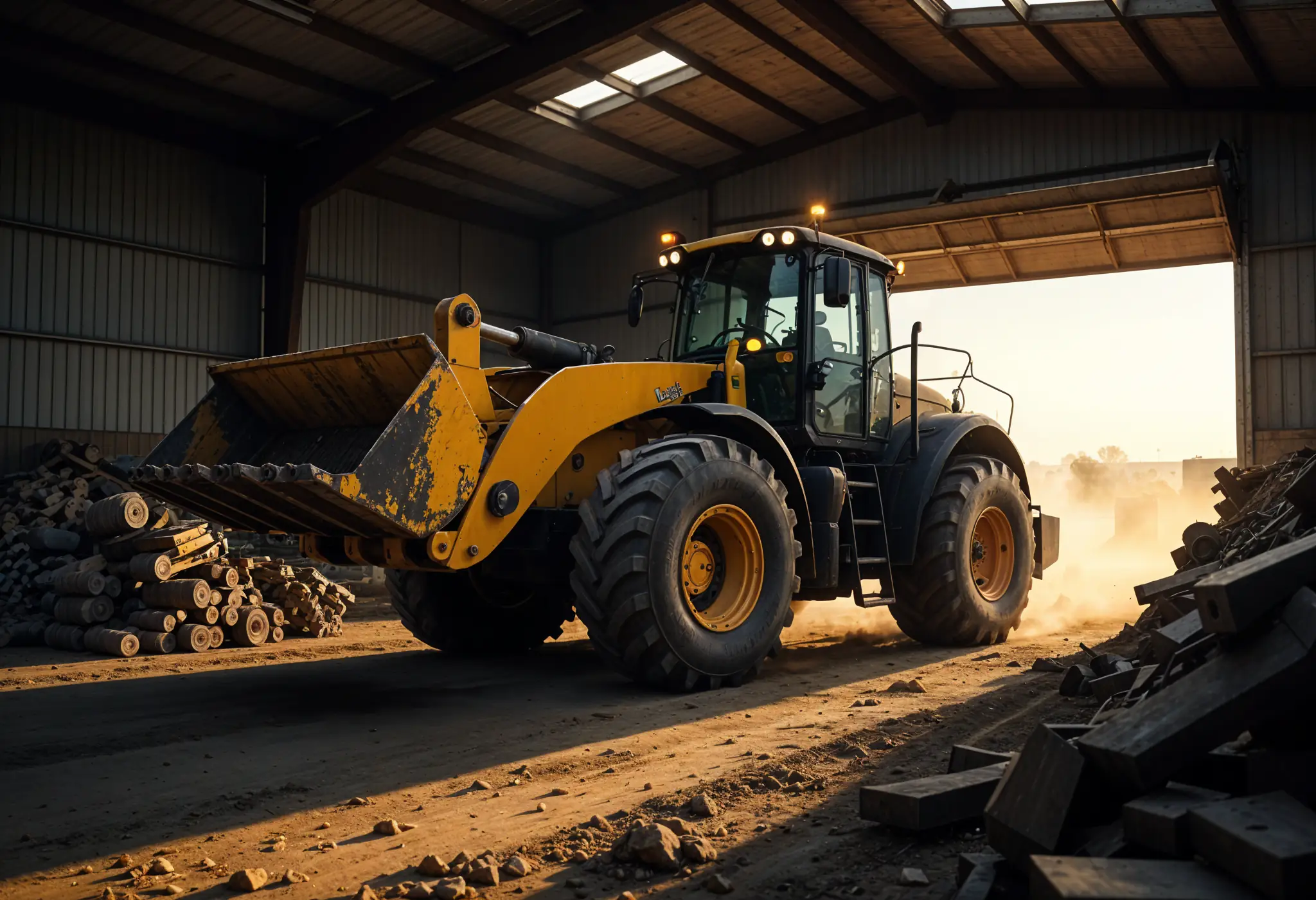
The Essential Farm Equipment Parts You Can't Afford to Run Out Of
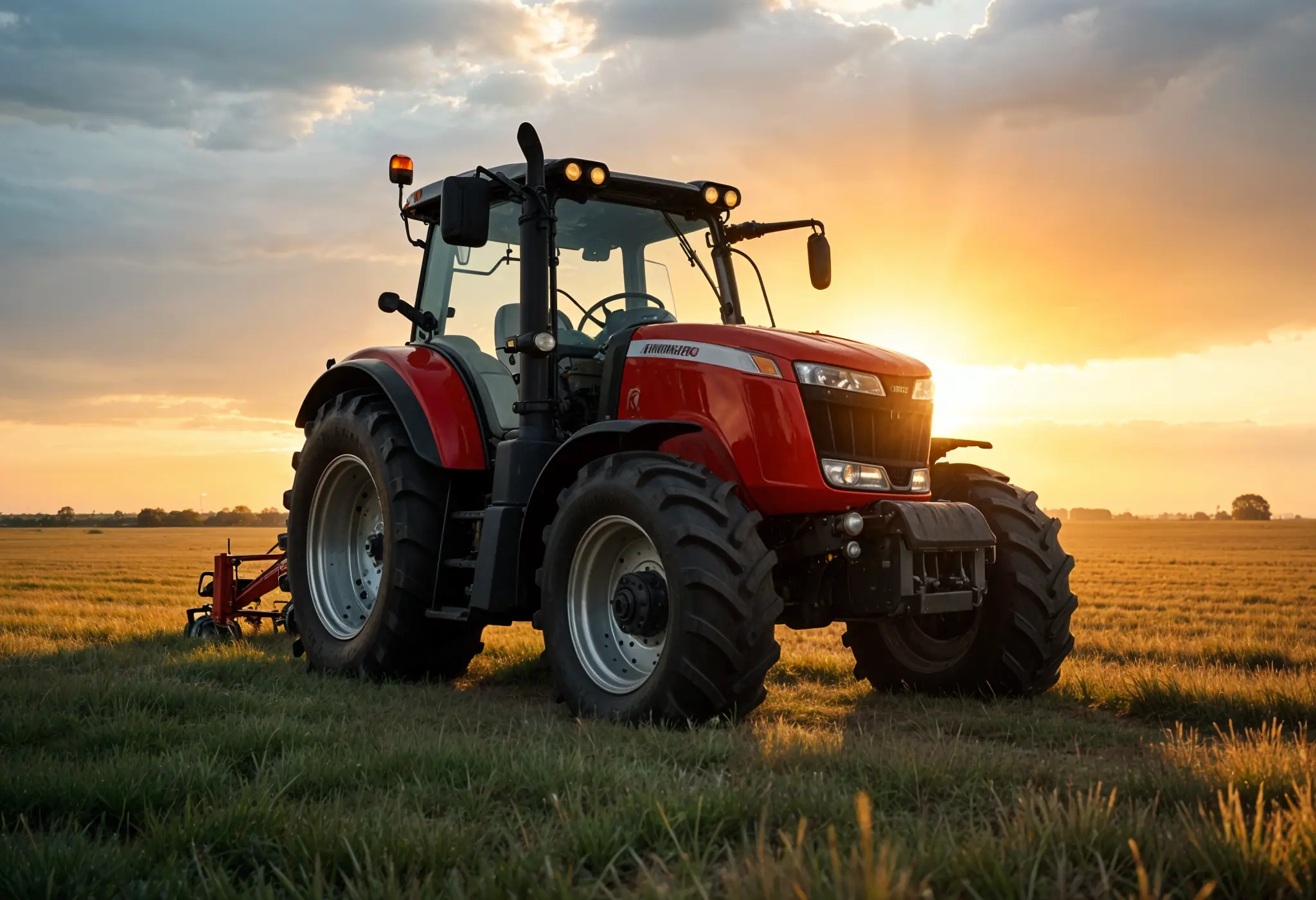
How to Service Farm Equipment: A Farmer's Guide to Zero Harvest Downtime
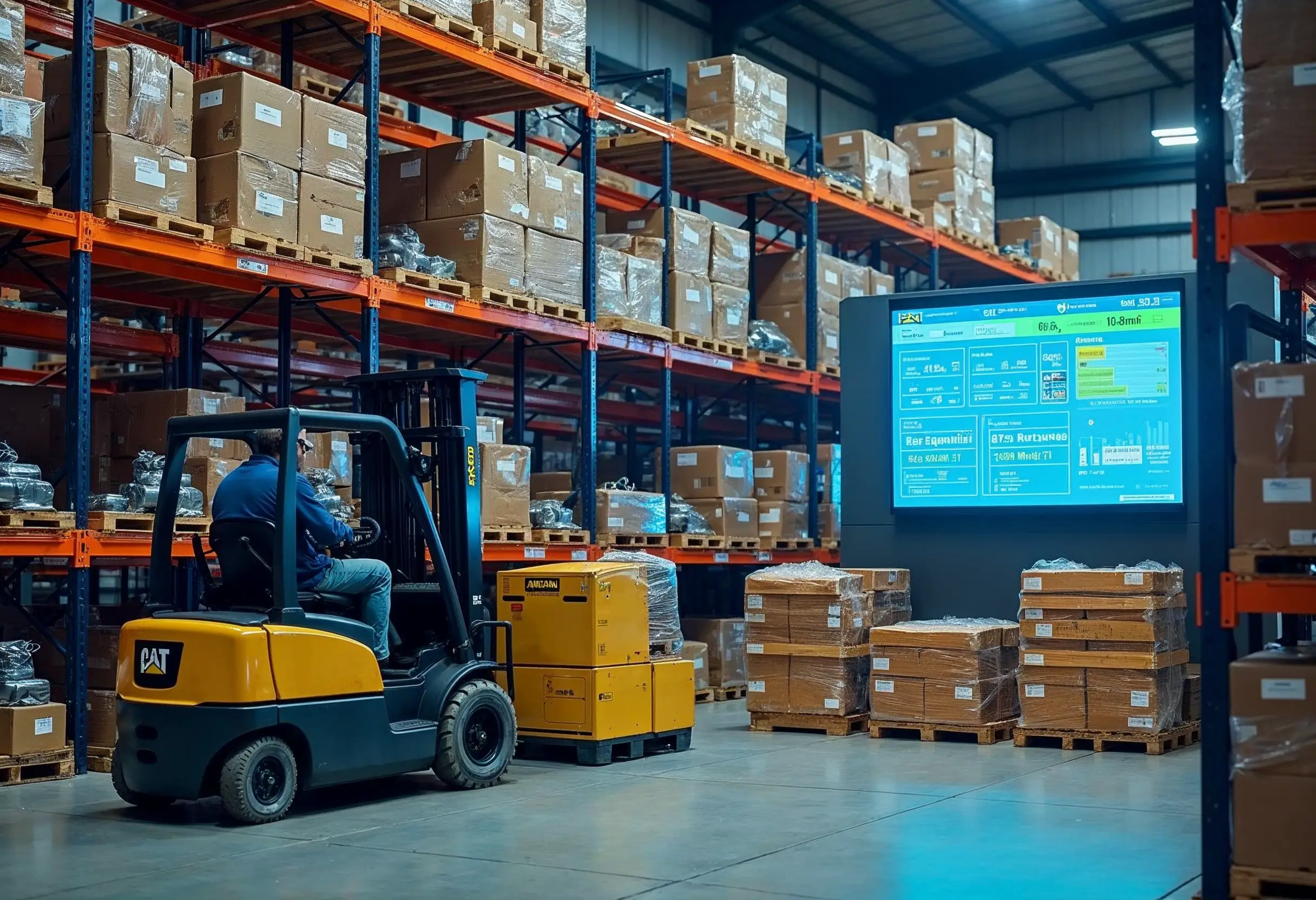
Construction Machinery Parts Suppliers: Expert Selection Guide
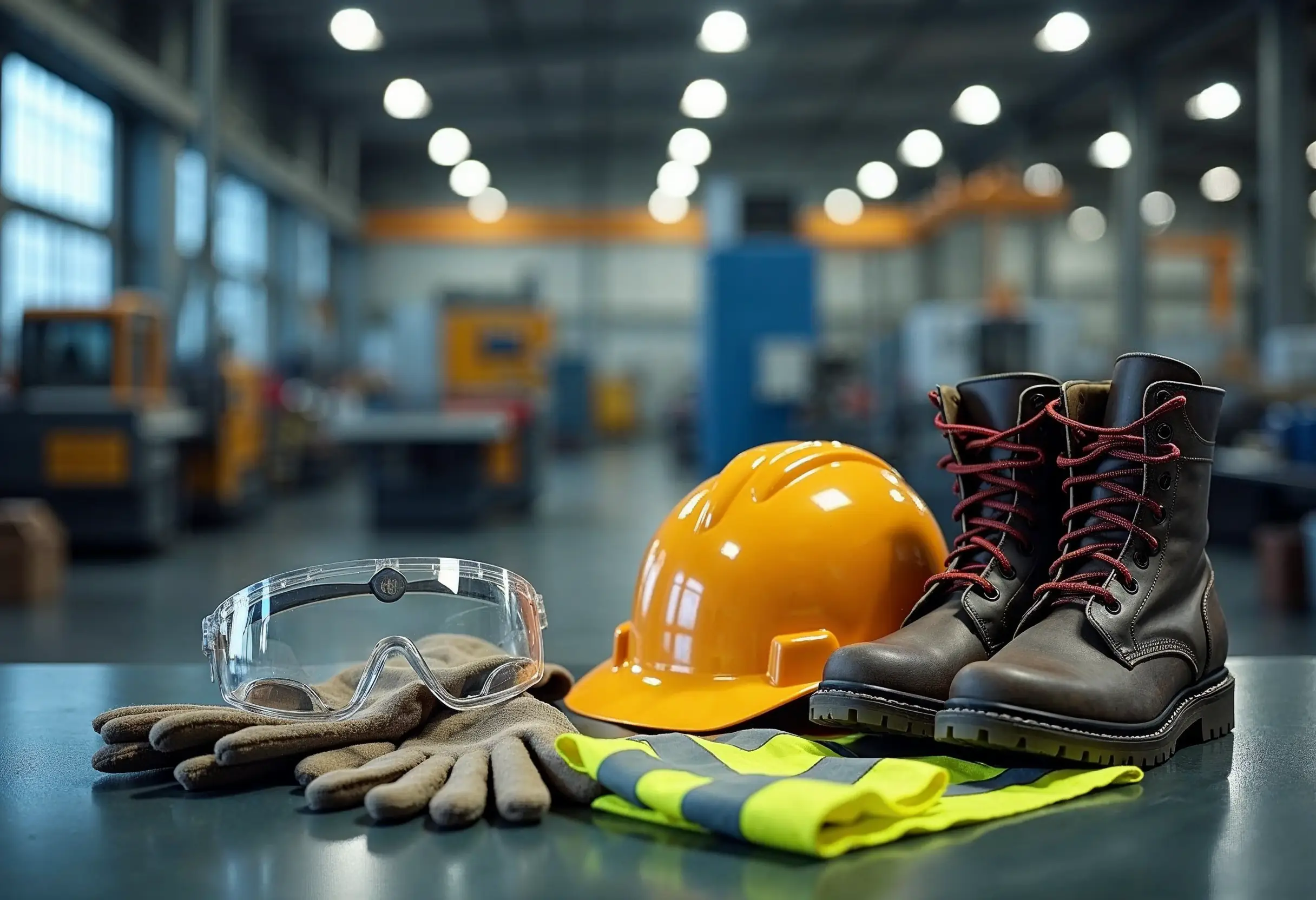
How to Apply Machine Safety Rules: From Selection to Installation
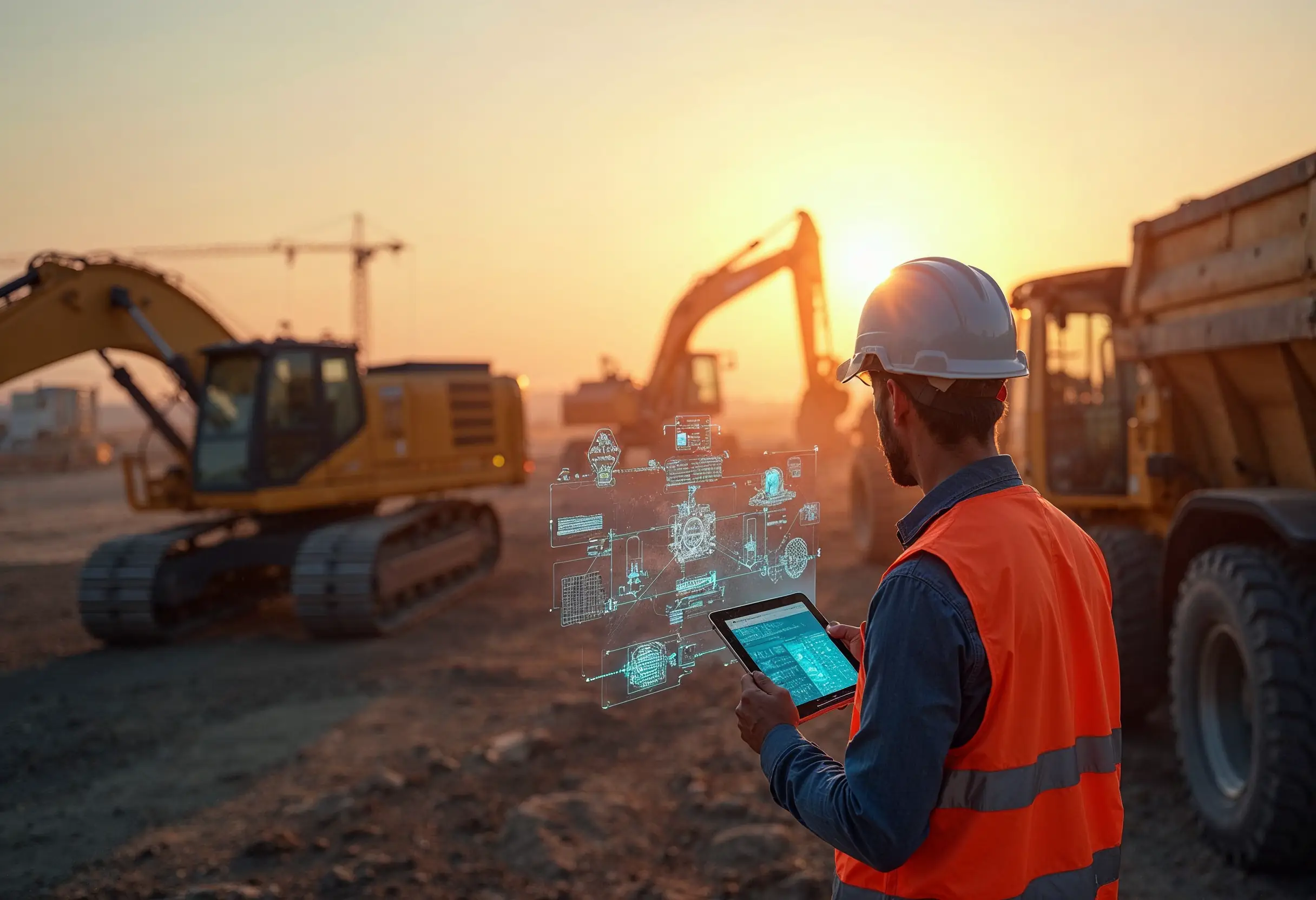
Smart Diagnostics Cut Heavy Equipment Failures by 73%
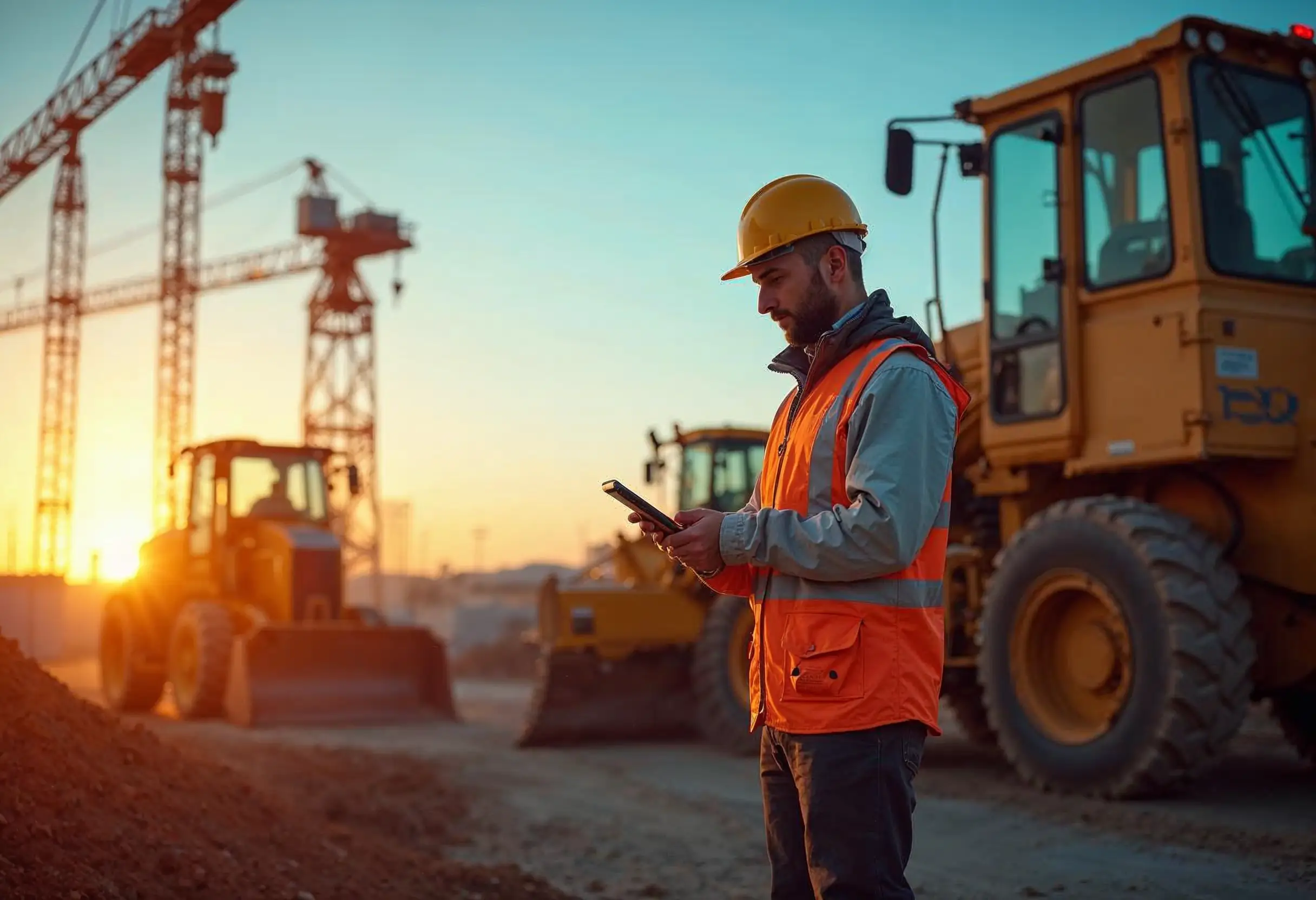
5 Ways to Assess the Environmental Impact of Heavy Construction Machinery
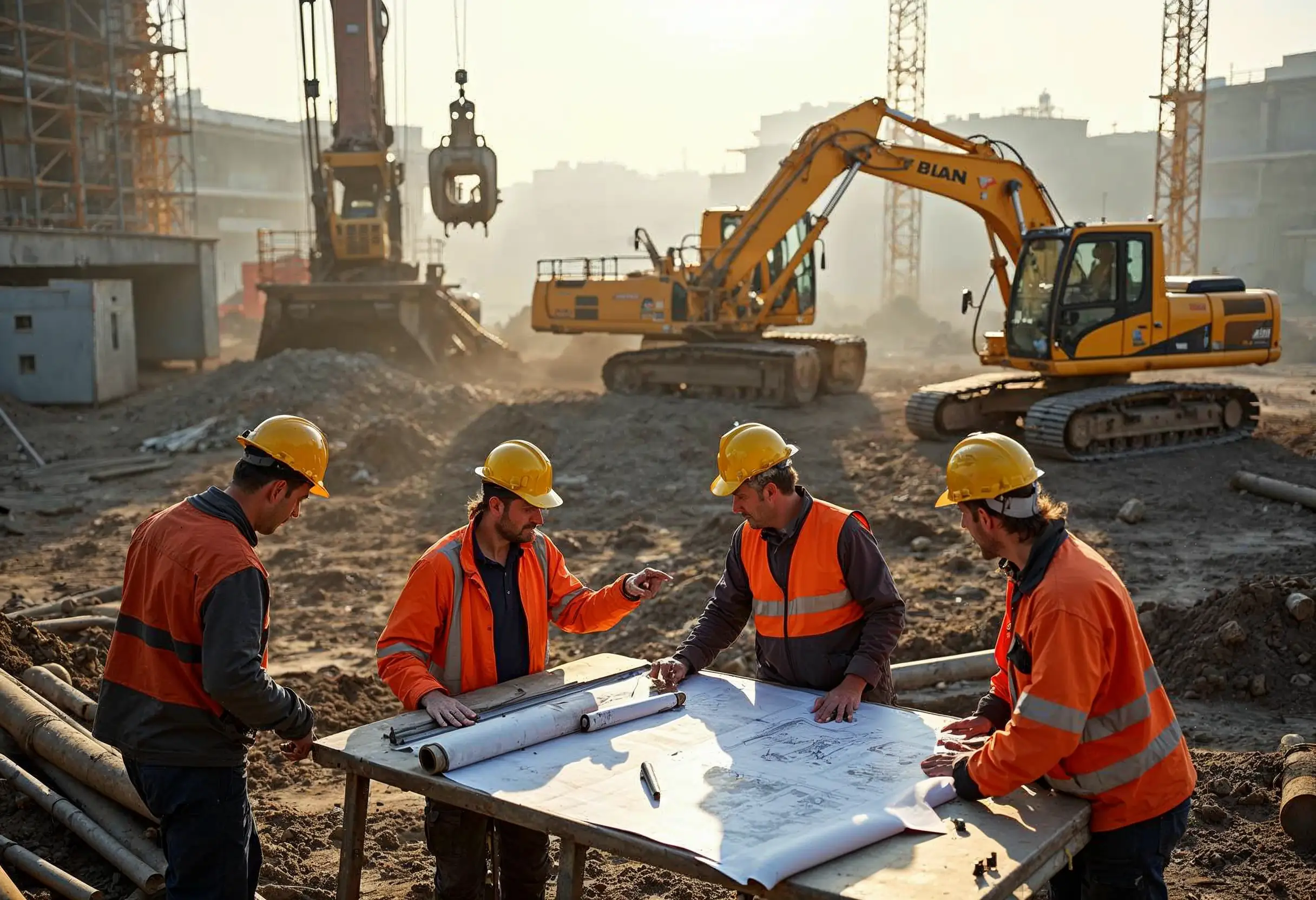
10 Smart Ways to Pick Construction Machinery for 2025 Projects
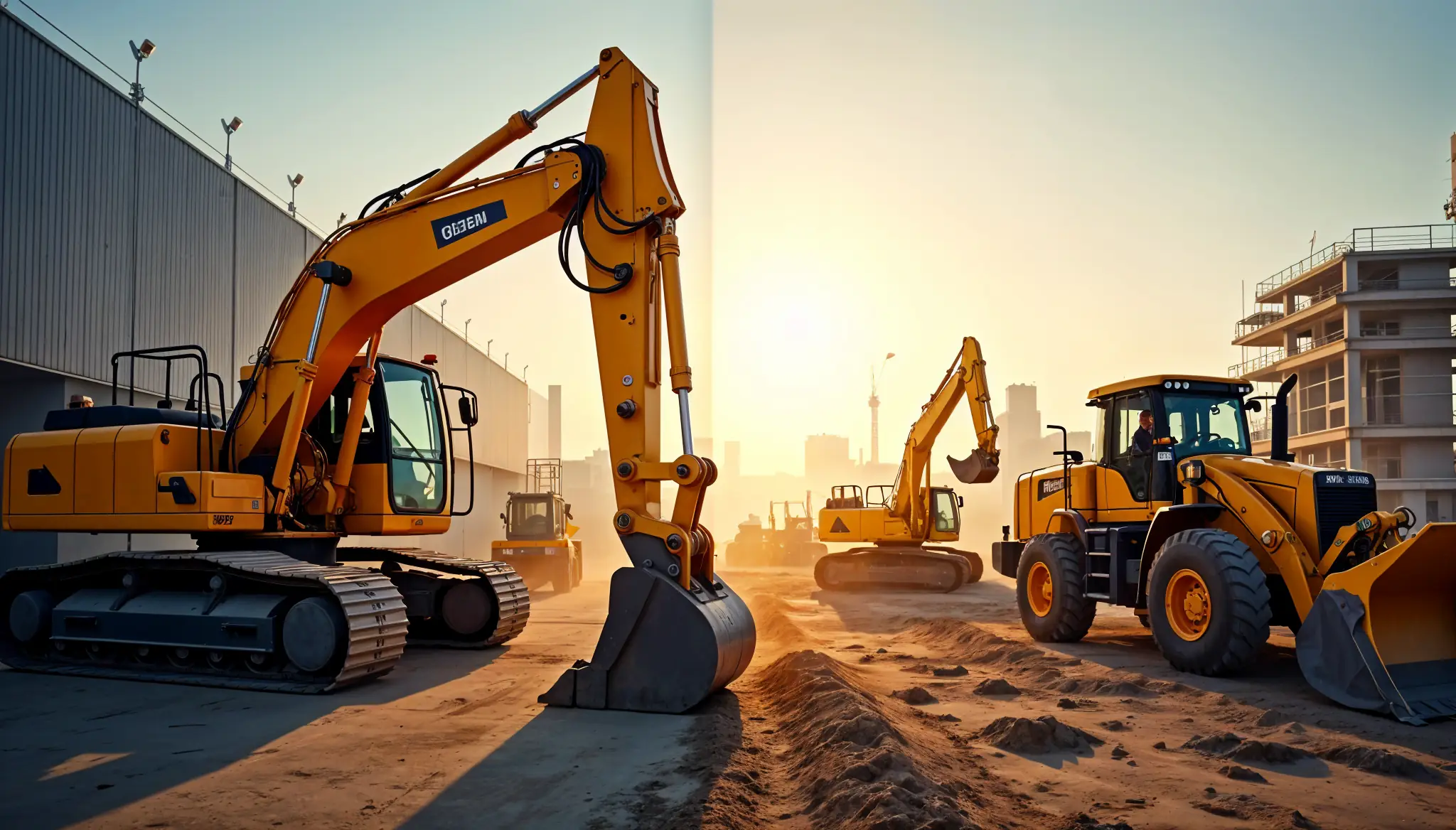
Rent vs Purchase Equipment: What Heavy Industry Experts Hide
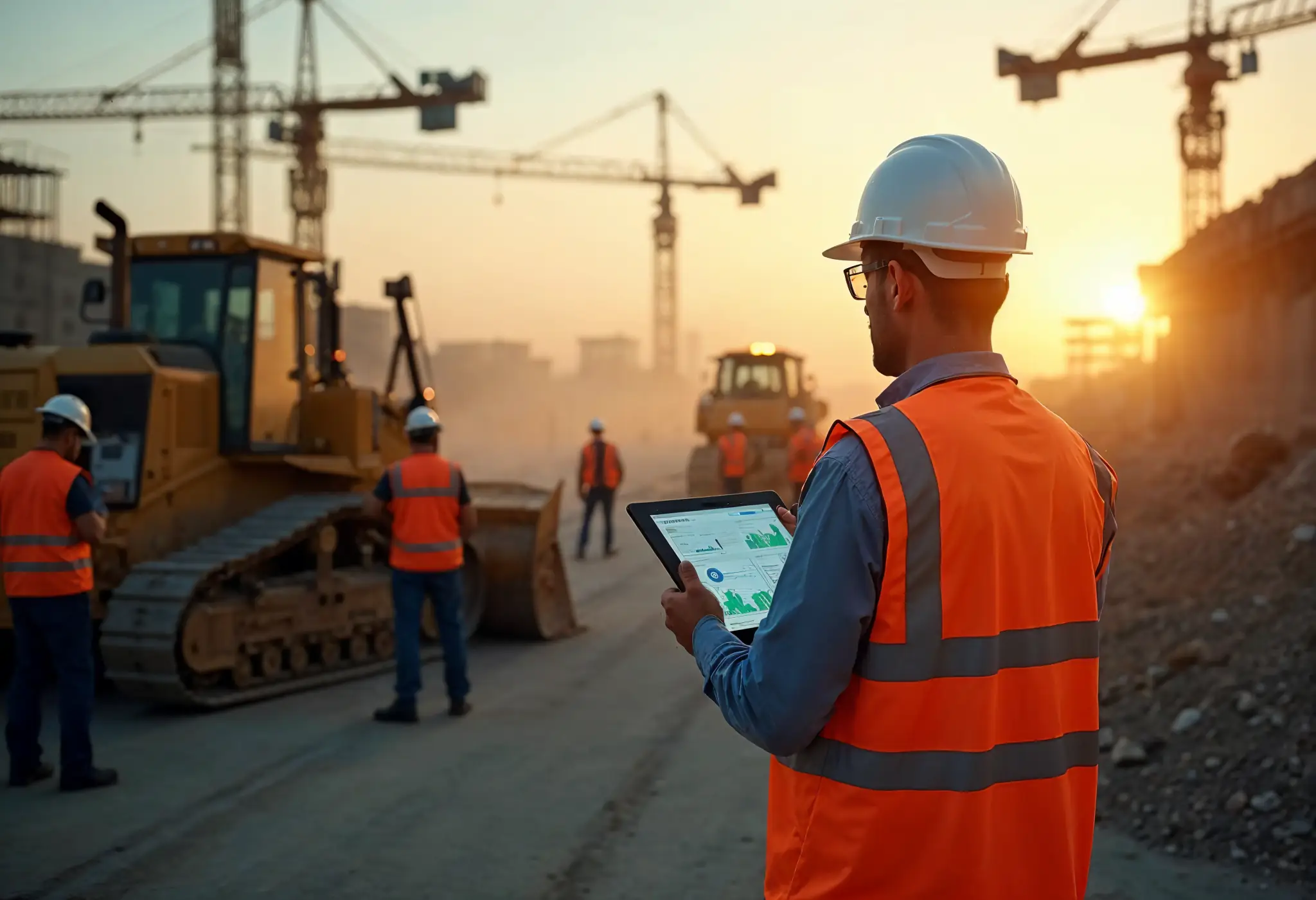
How to Implement a Construction Inventory Management System for Equipment Efficiency
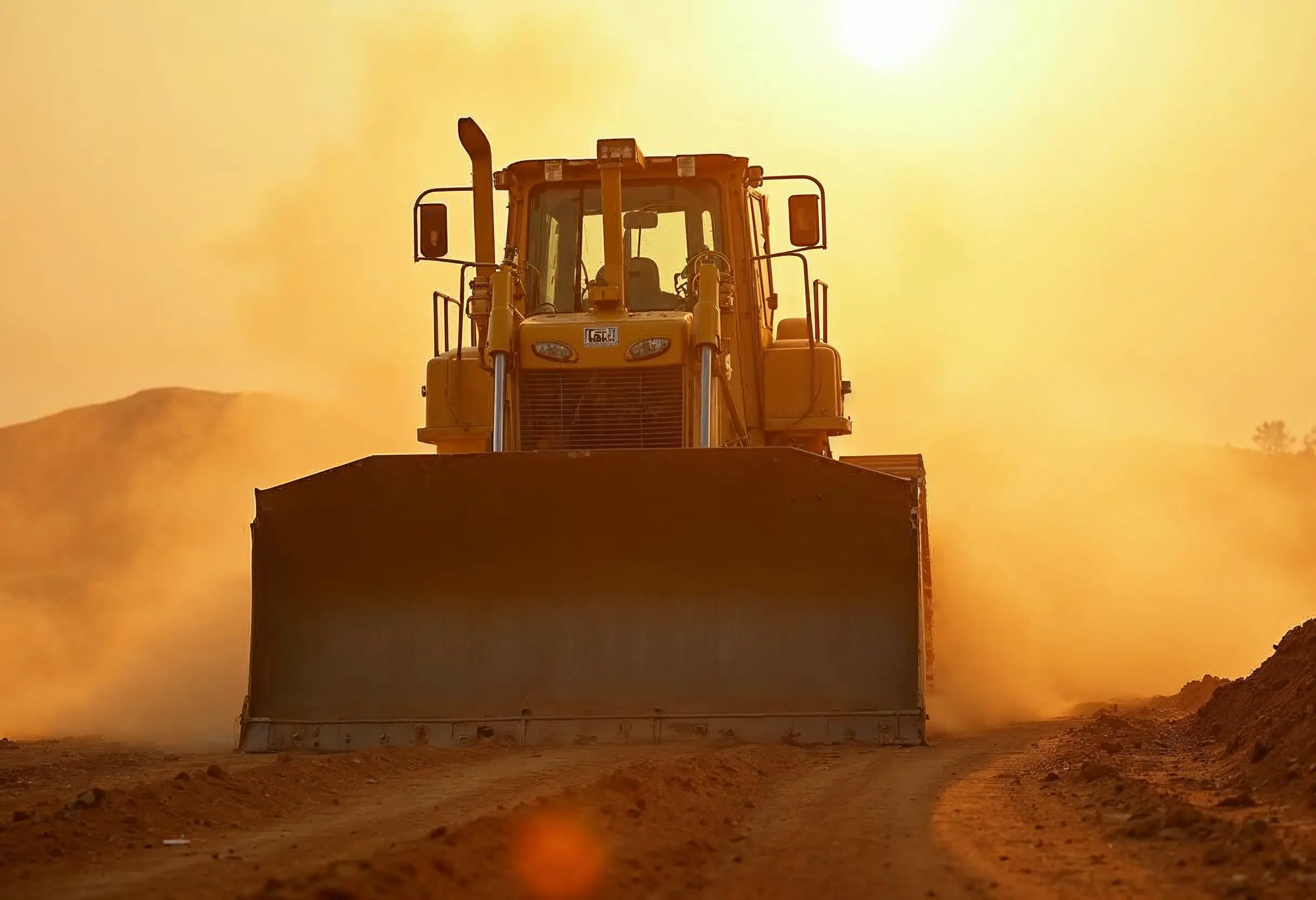
How to Extend Equipment Life Expectancy with Regular Maintenance
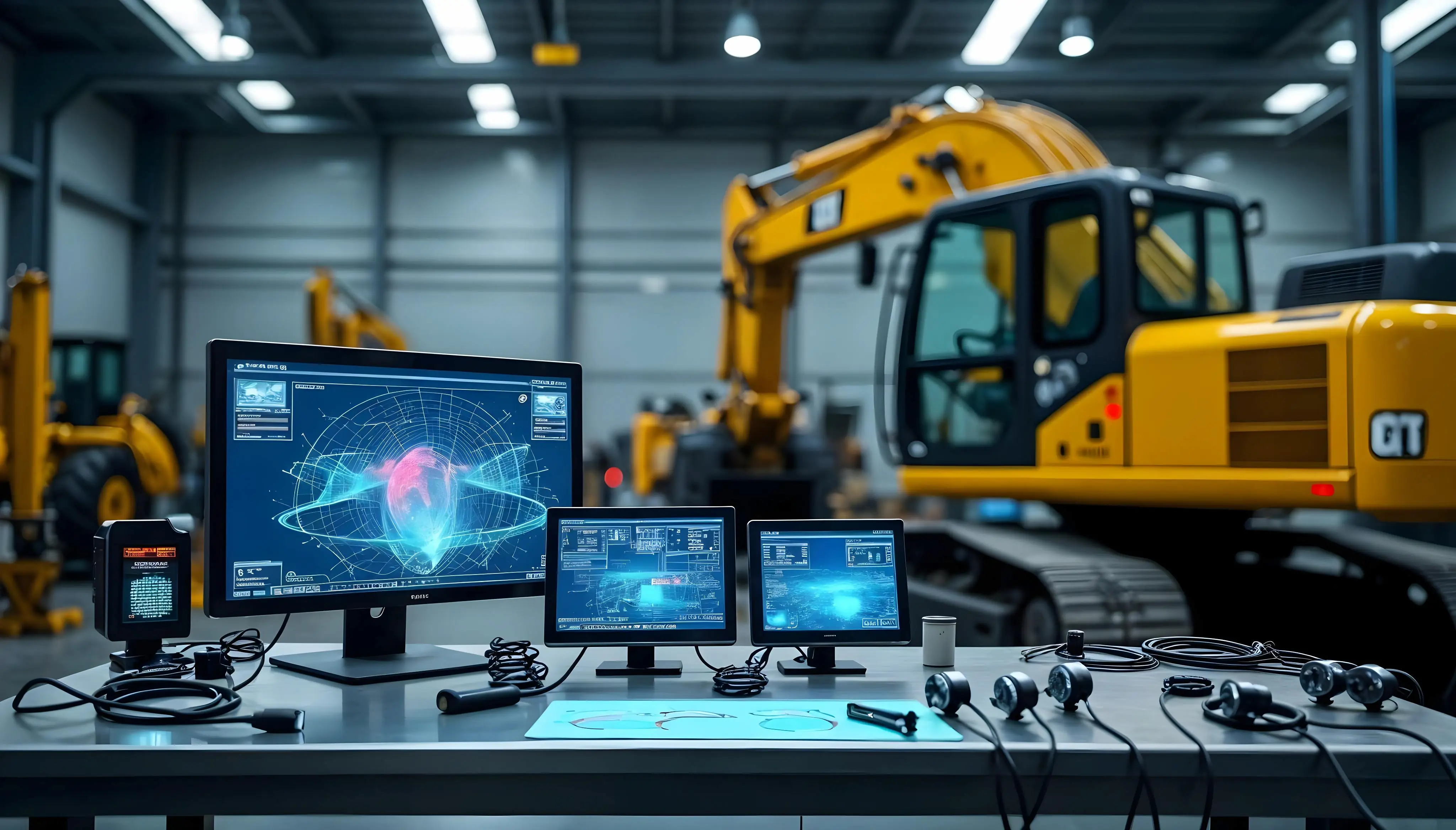
Advanced Heavy Equipment Diagnostic Tools: Ensuring Construction Machinery Quality
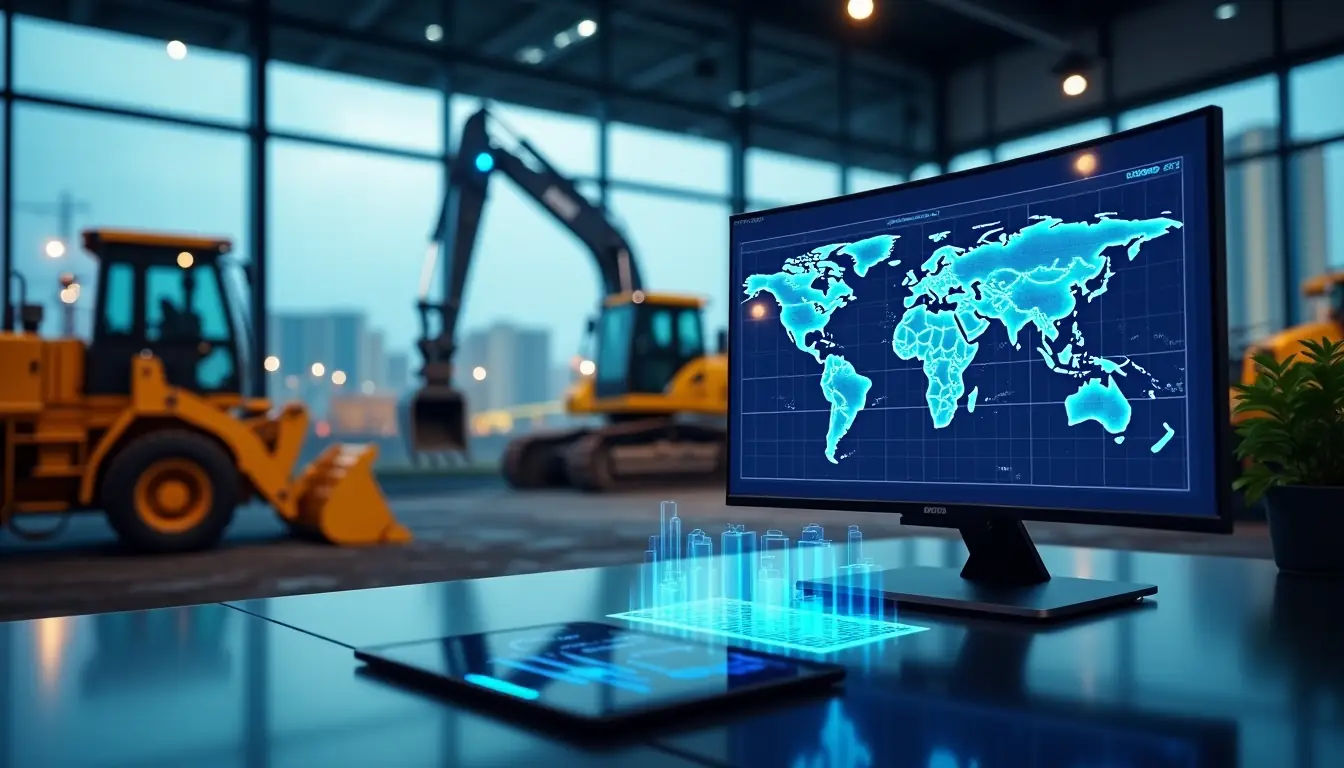
Essential Features Your Construction Equipment Inventory System Needs
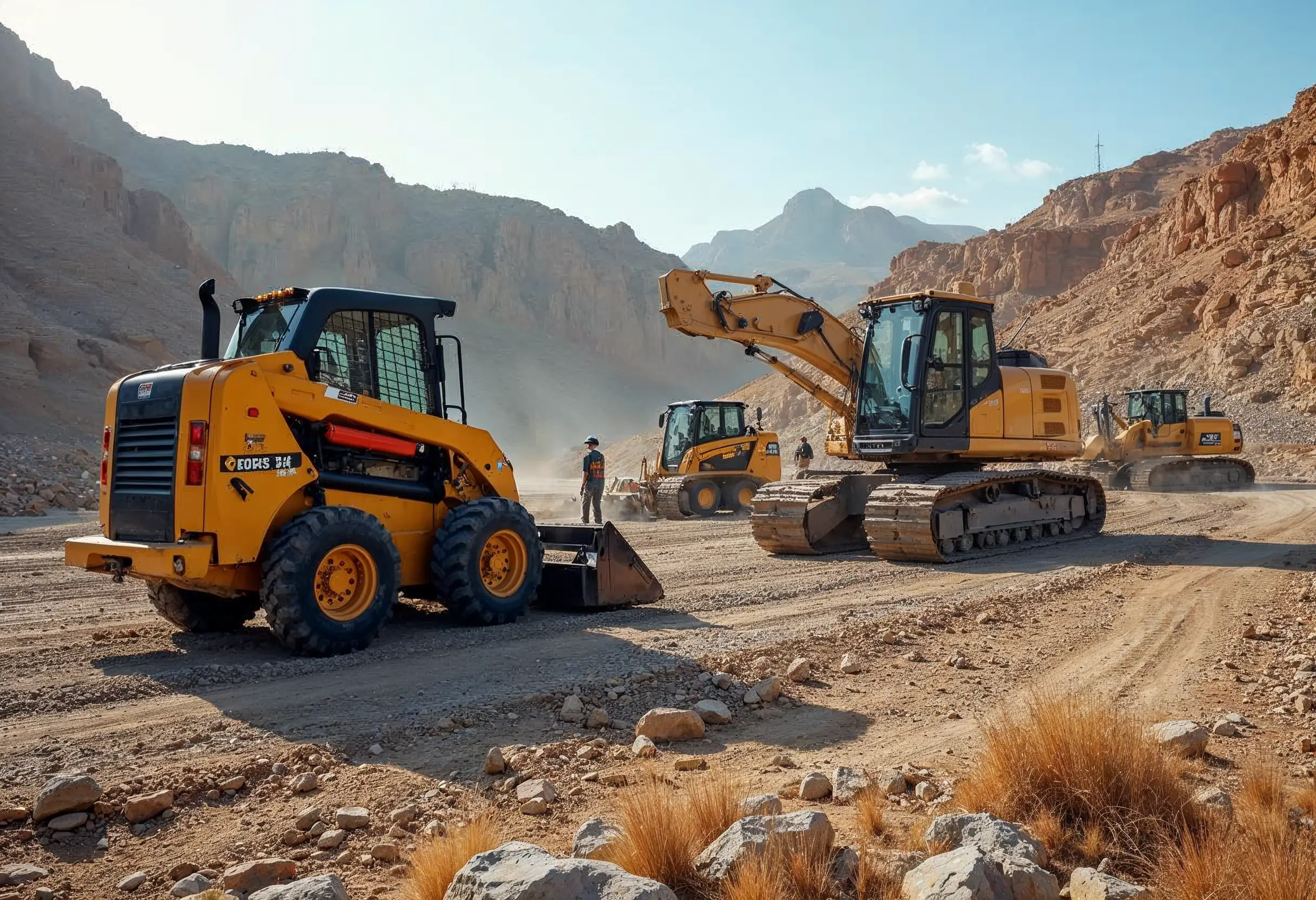
29 Quick Tips for Choosing Construction Equipment for Remote Locations
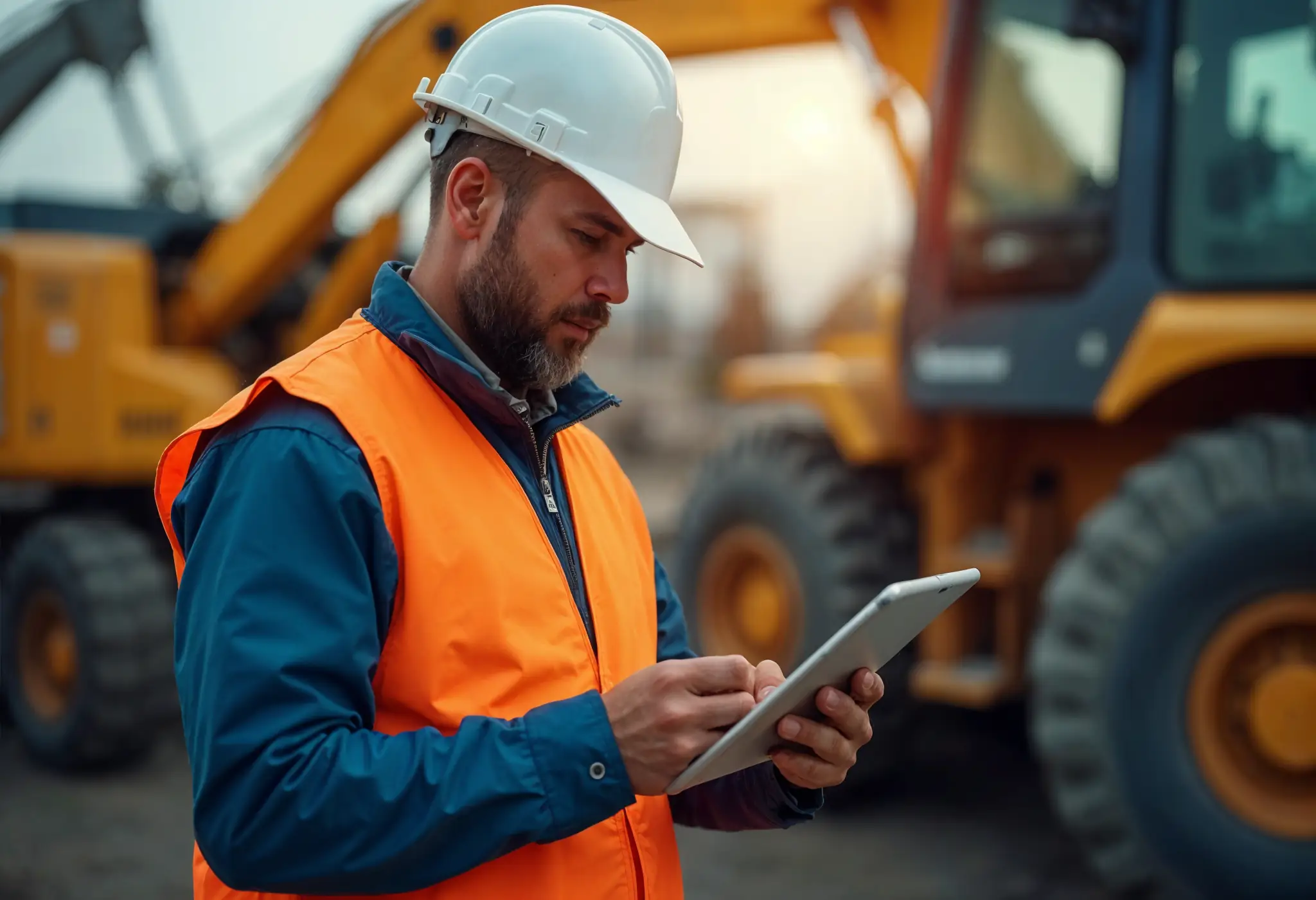
How to Select Construction Machinery with Optimal Equipment Maintenance in Mind
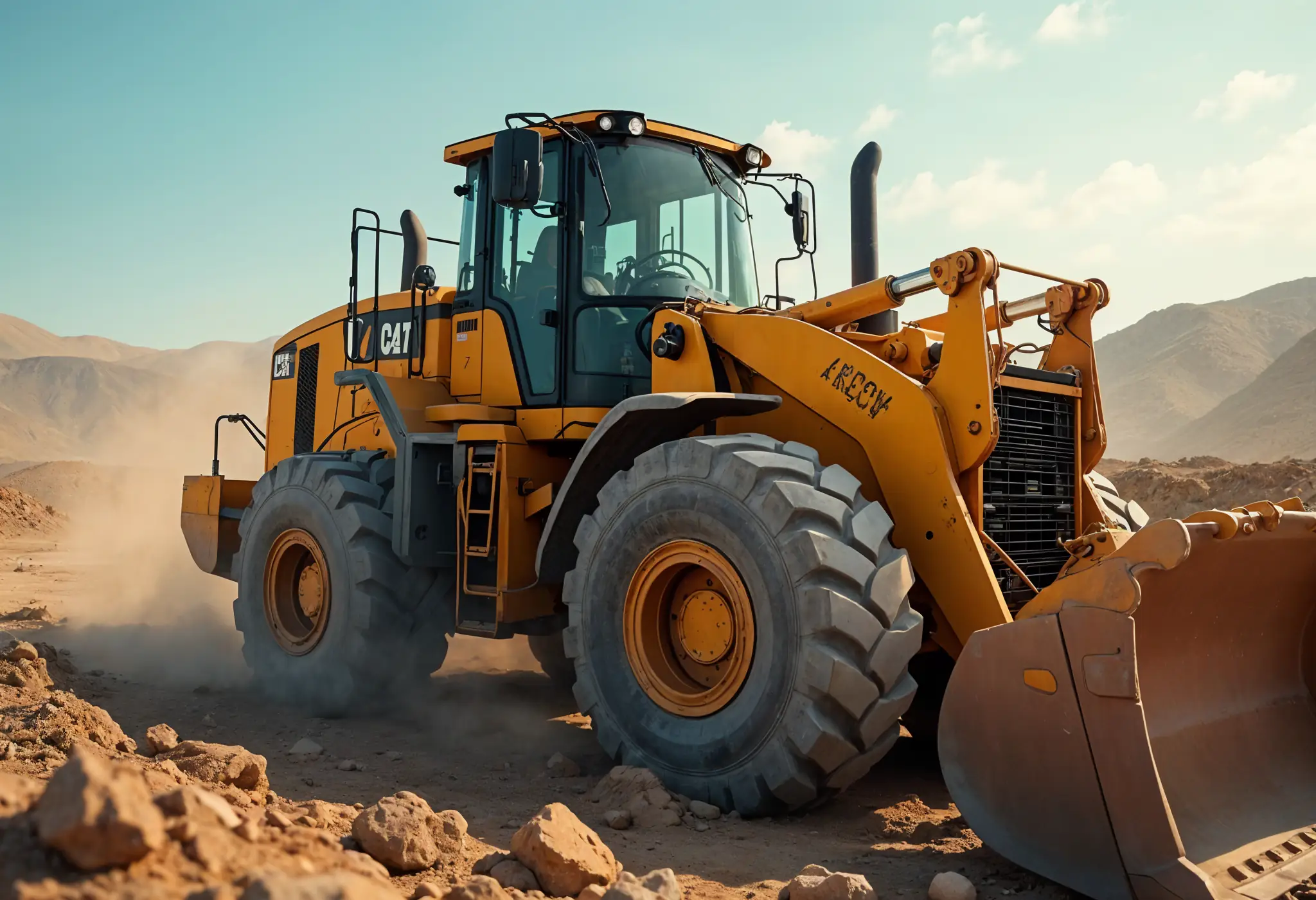
Top 25 Tips for Selecting Bulldozers for Construction Sites
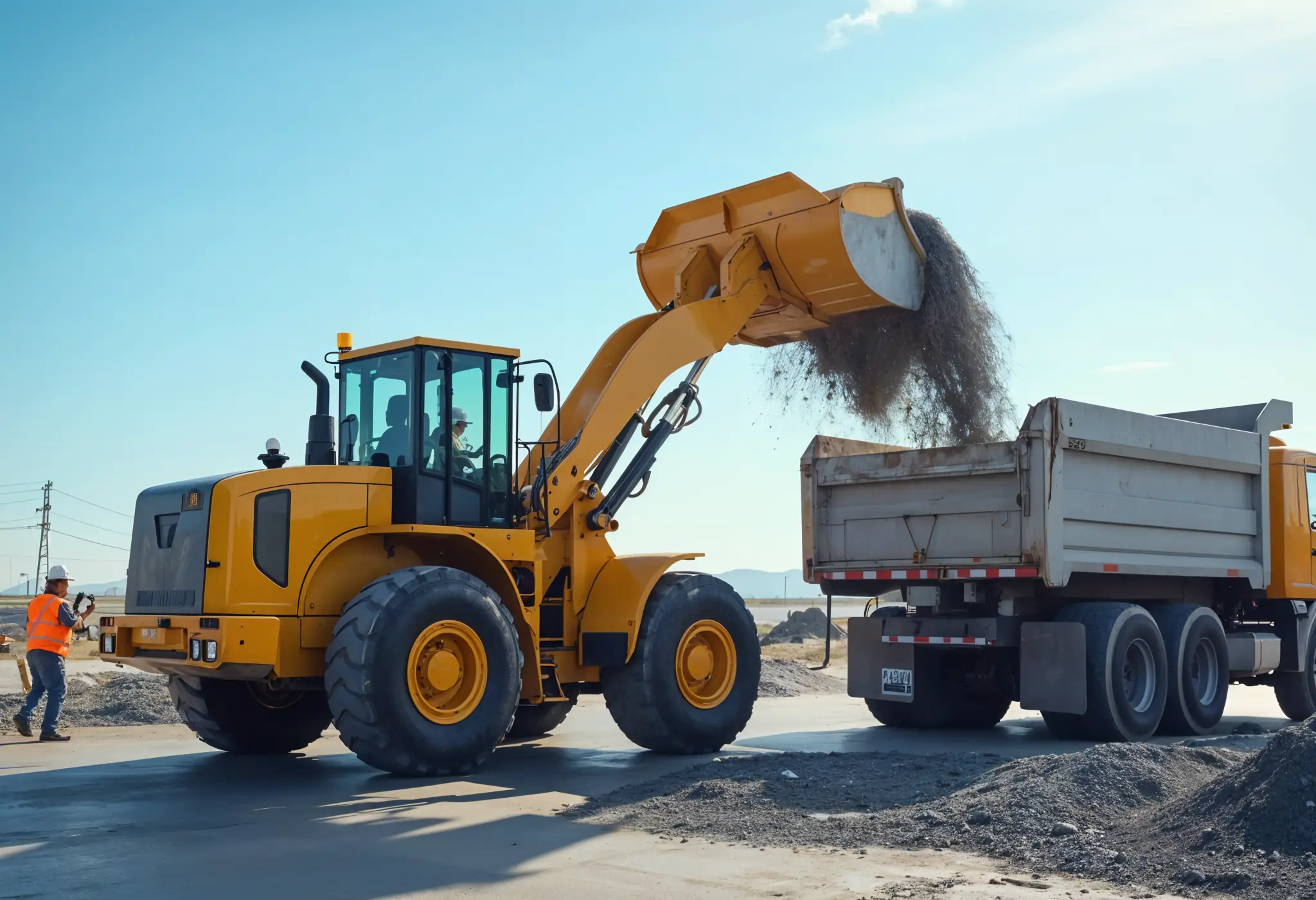
Which Construction Loader is Best for Your Project Needs?
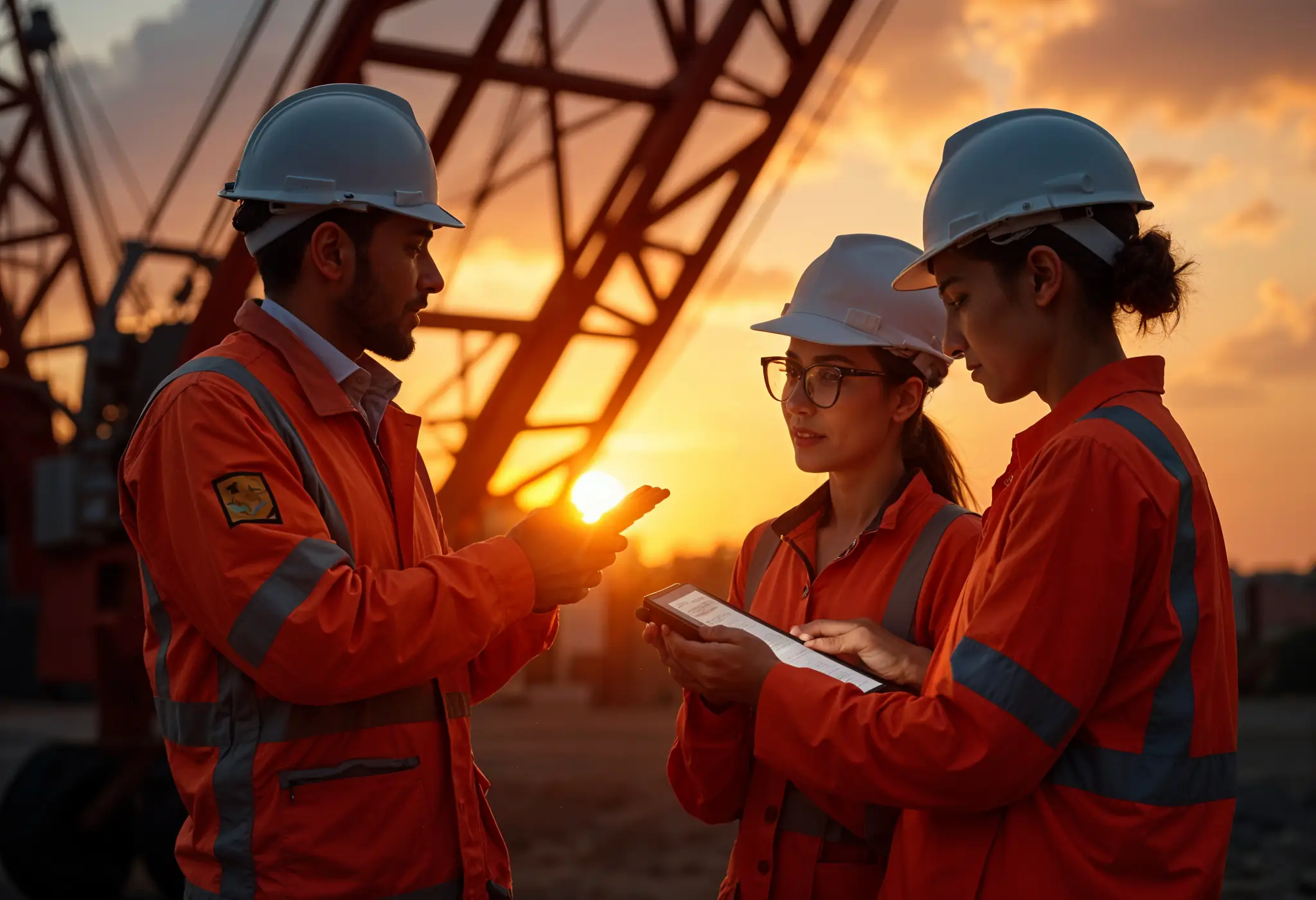
4 Key Steps to Form a Construction Machinery QC Team
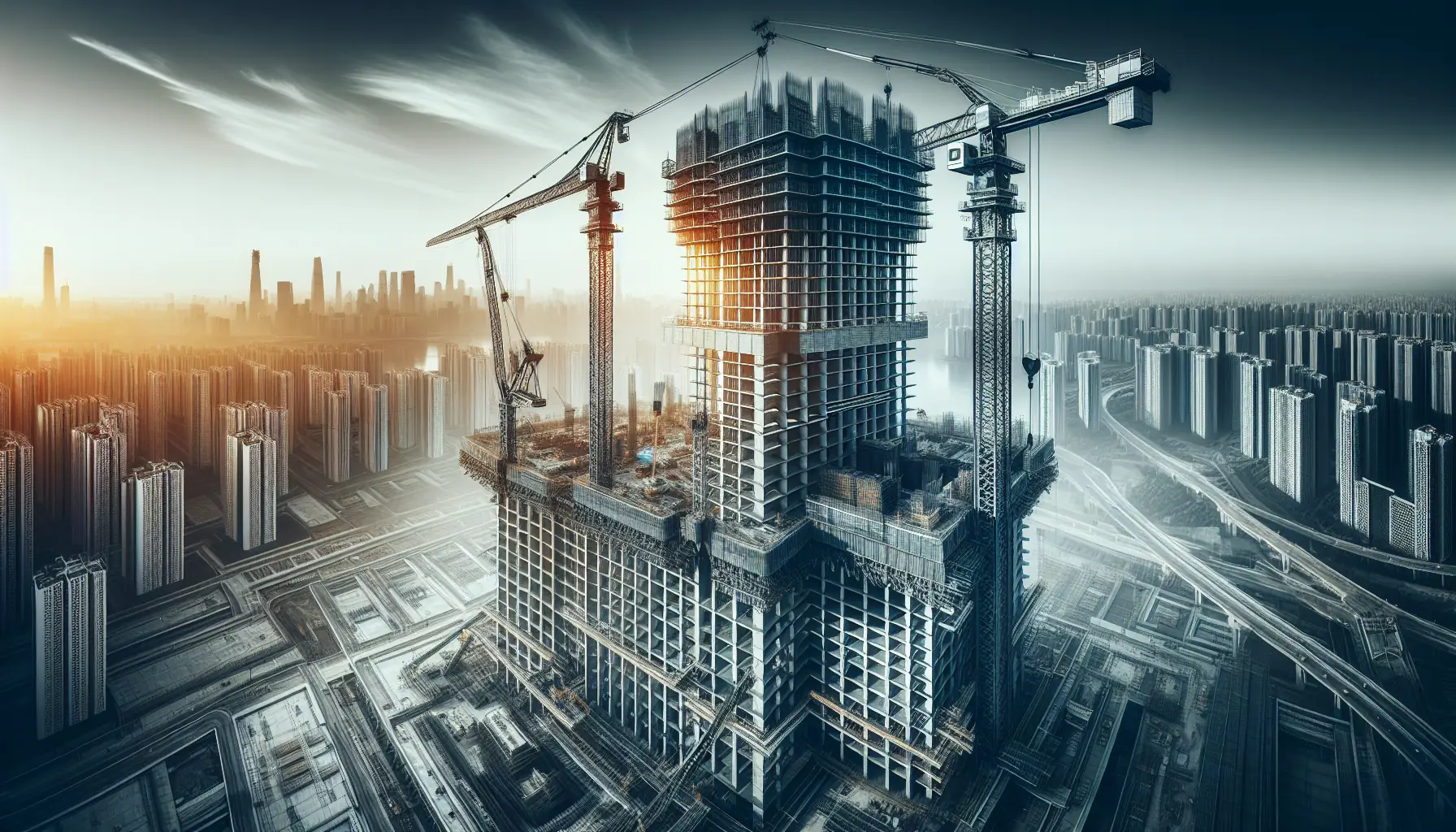
15 Essential Tips for Selecting the Perfect Crane for Construction
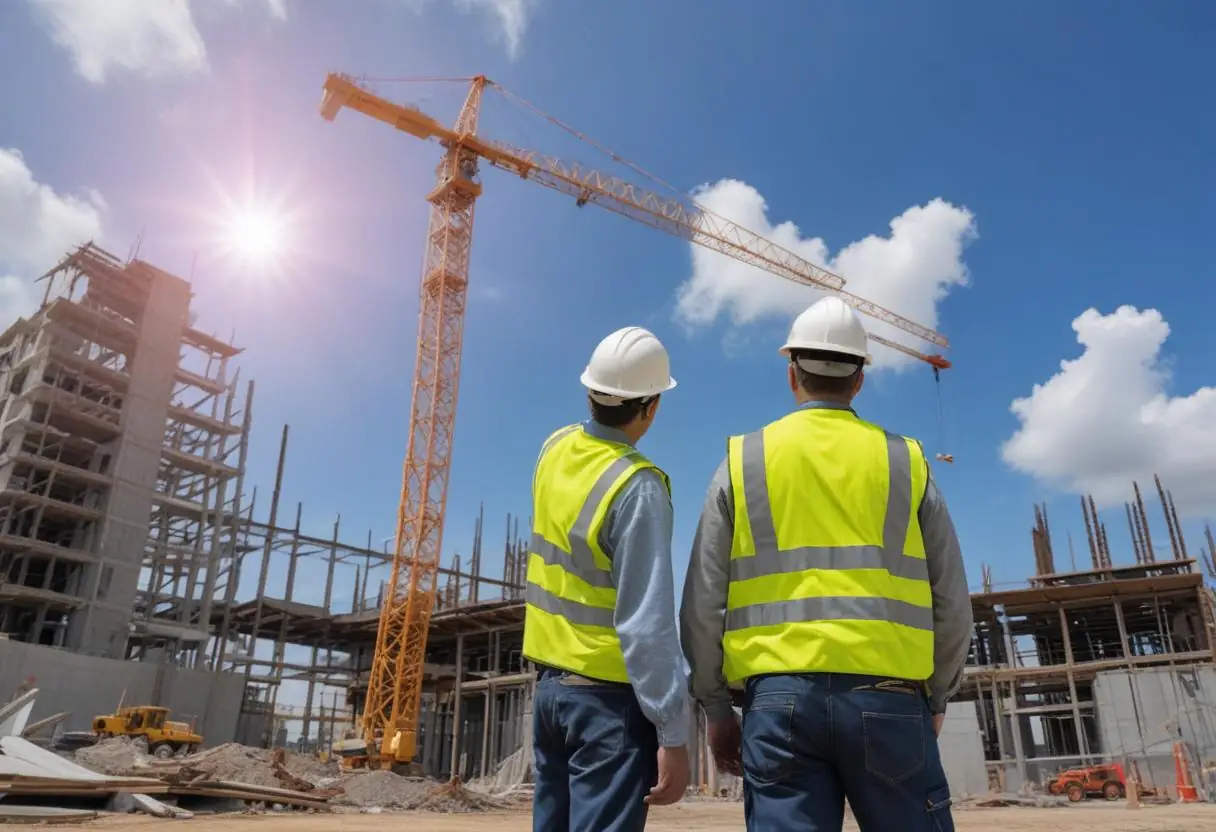
Maximize Savings: Multi-Purpose Construction Machinery for Lower Costs
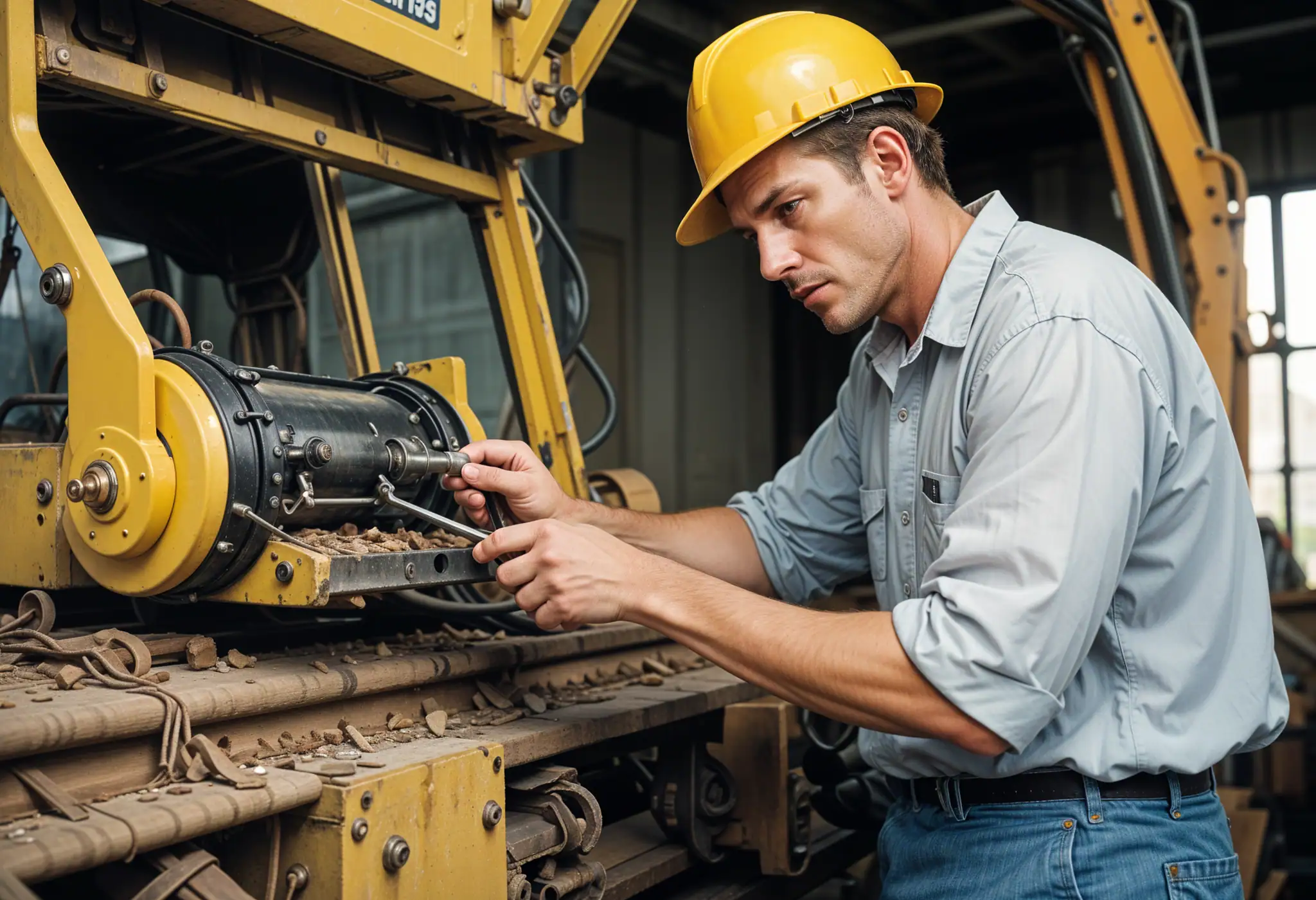
Affordable Heavy Equipment Parts: A Sourcing Guide
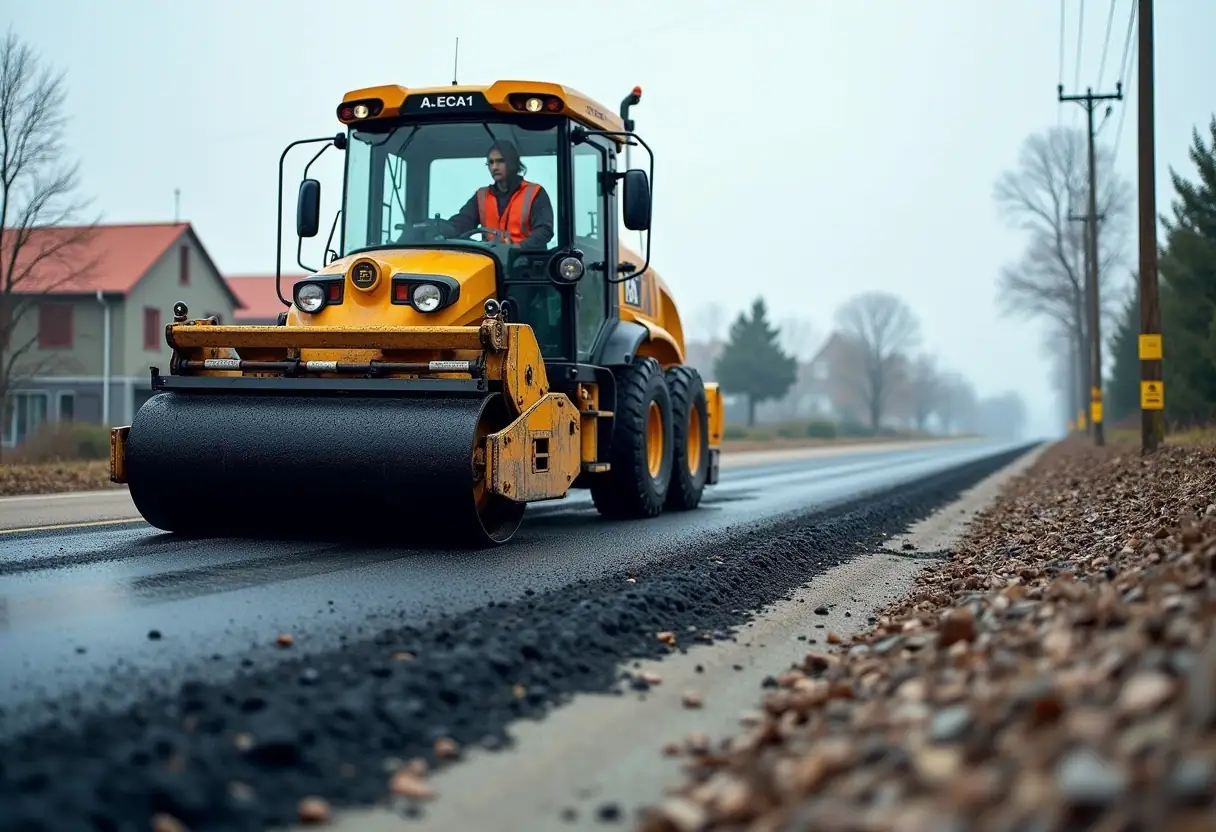
Choosing the Right Road Construction Equipment: A Complete Guide
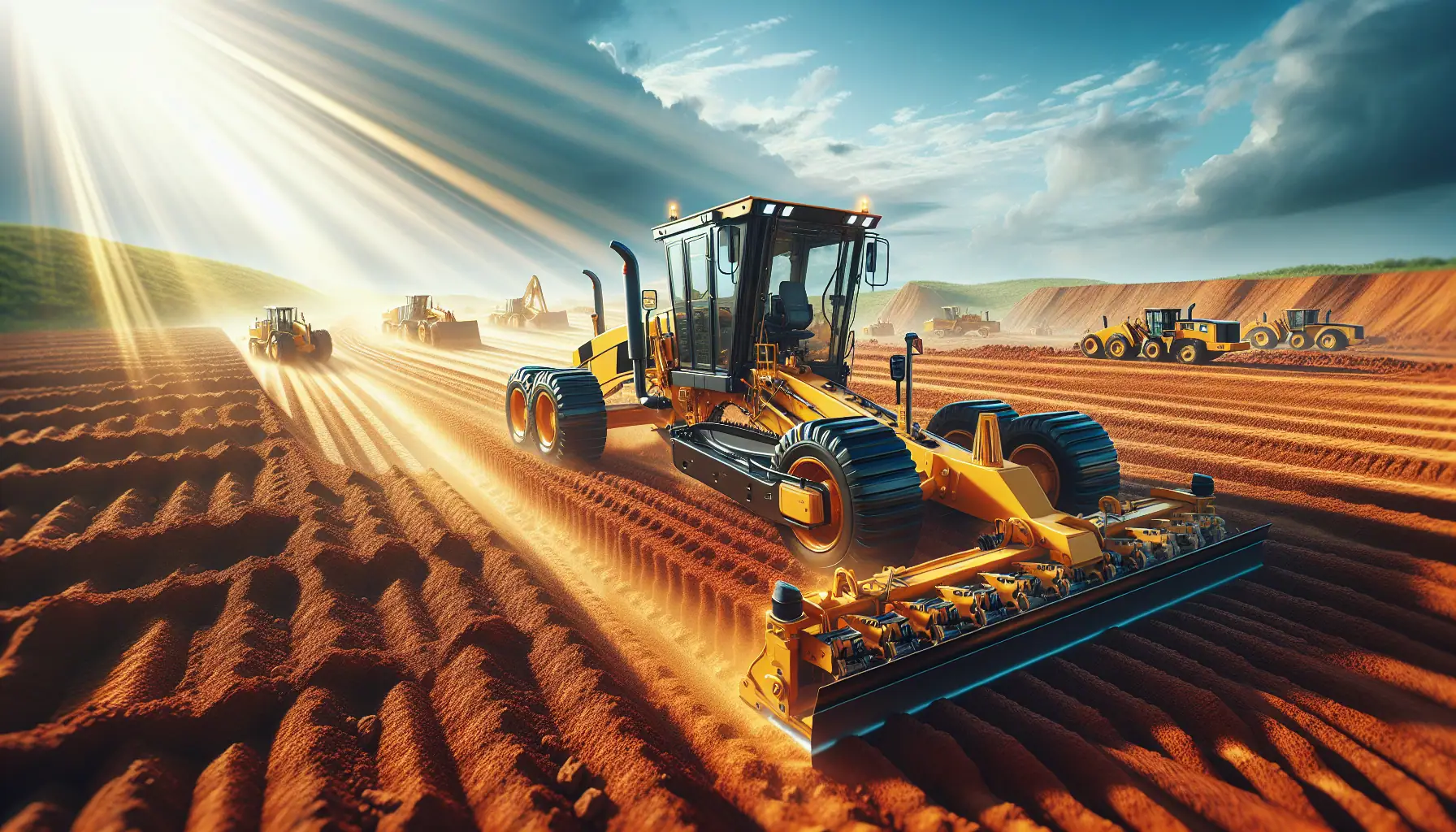
Motor Graders: Key Elements to Consider for Optimal Selection
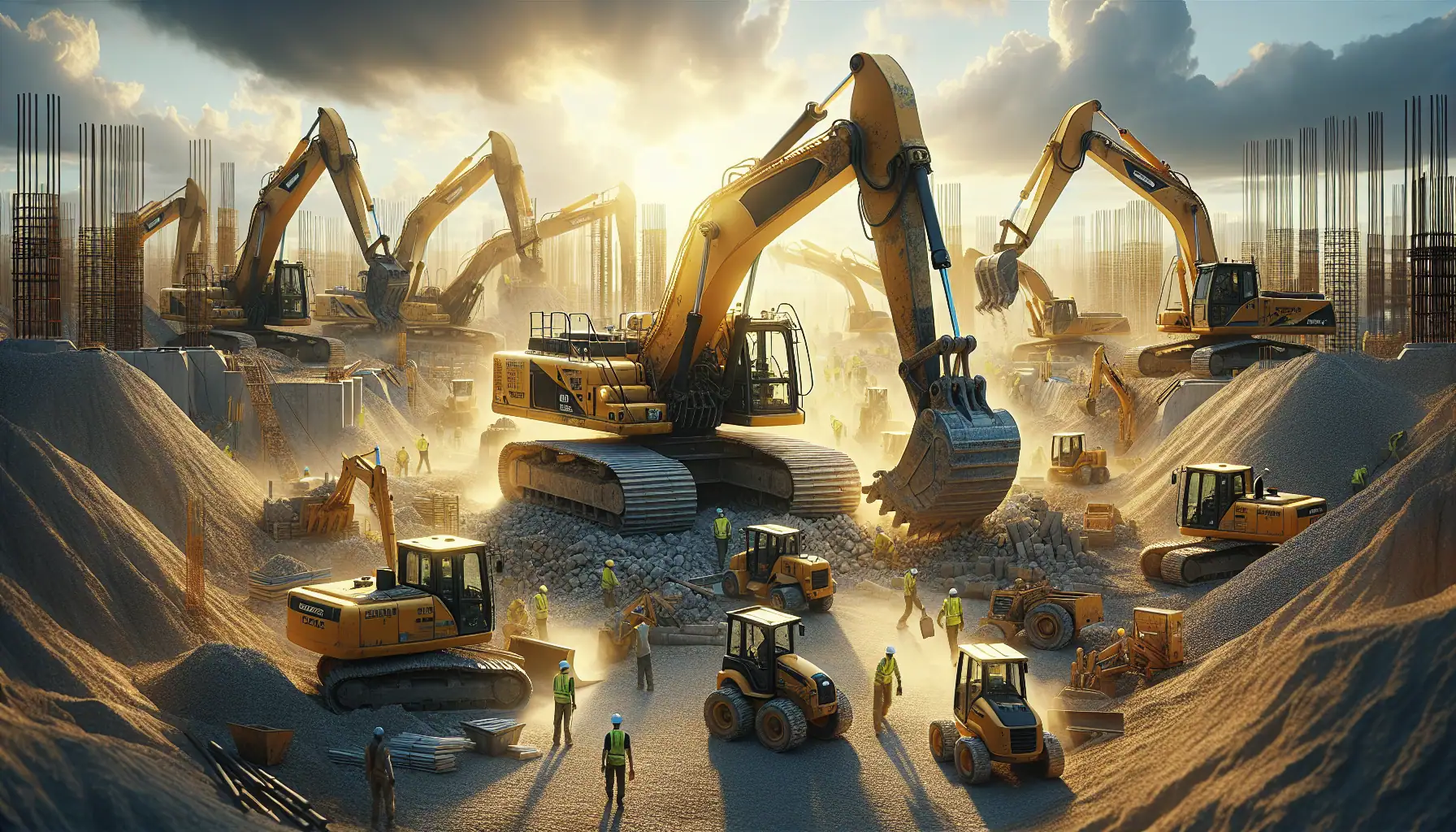
A Detailed Guide to Choosing Excavators for Construction Work
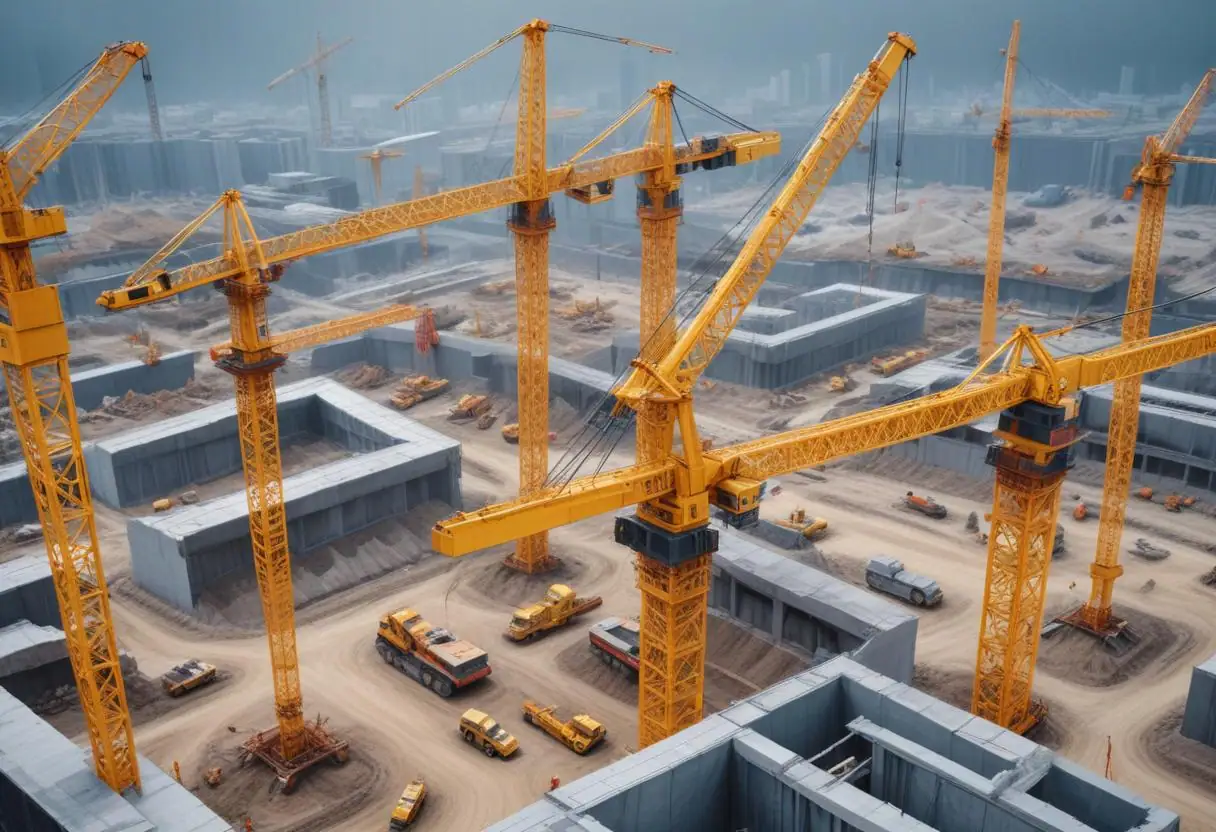
Top Tips for Choosing Cranes for Construction Projects
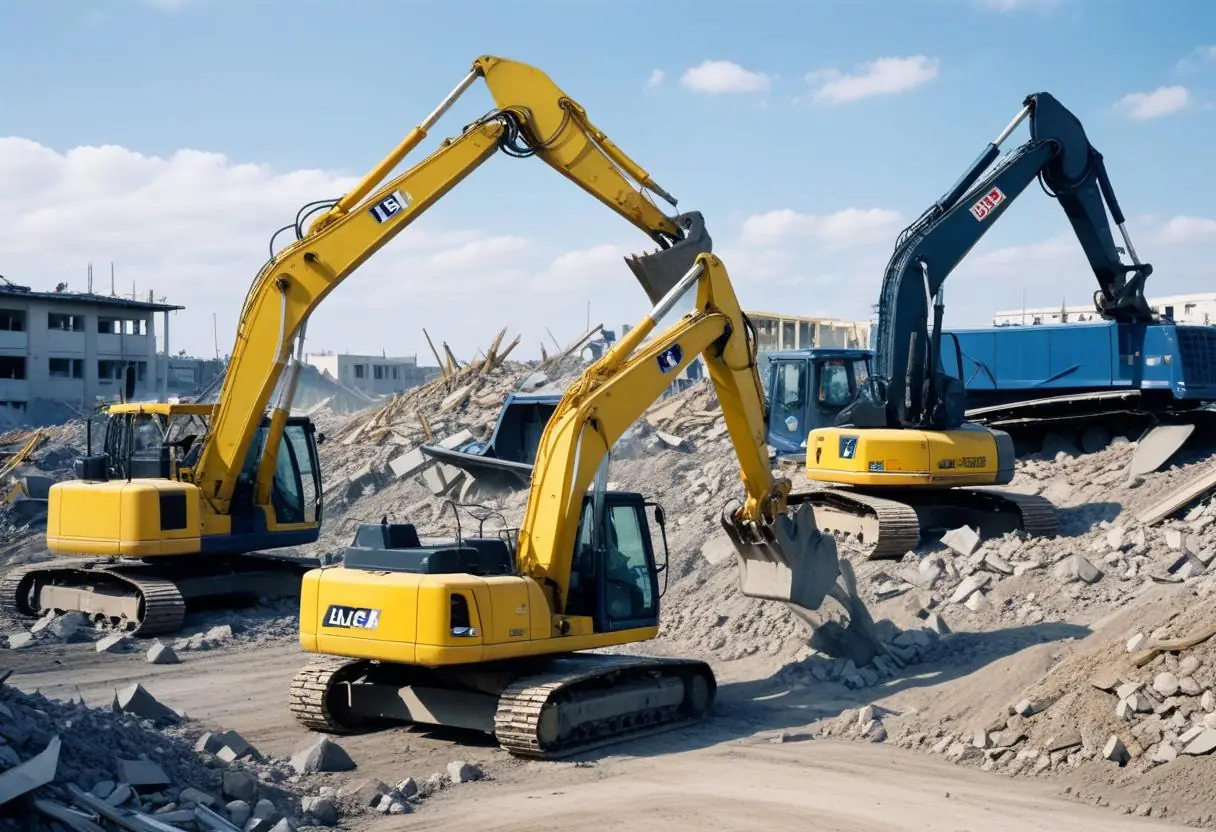
5 Top-Rated Demolition Machines for Construction Professionals
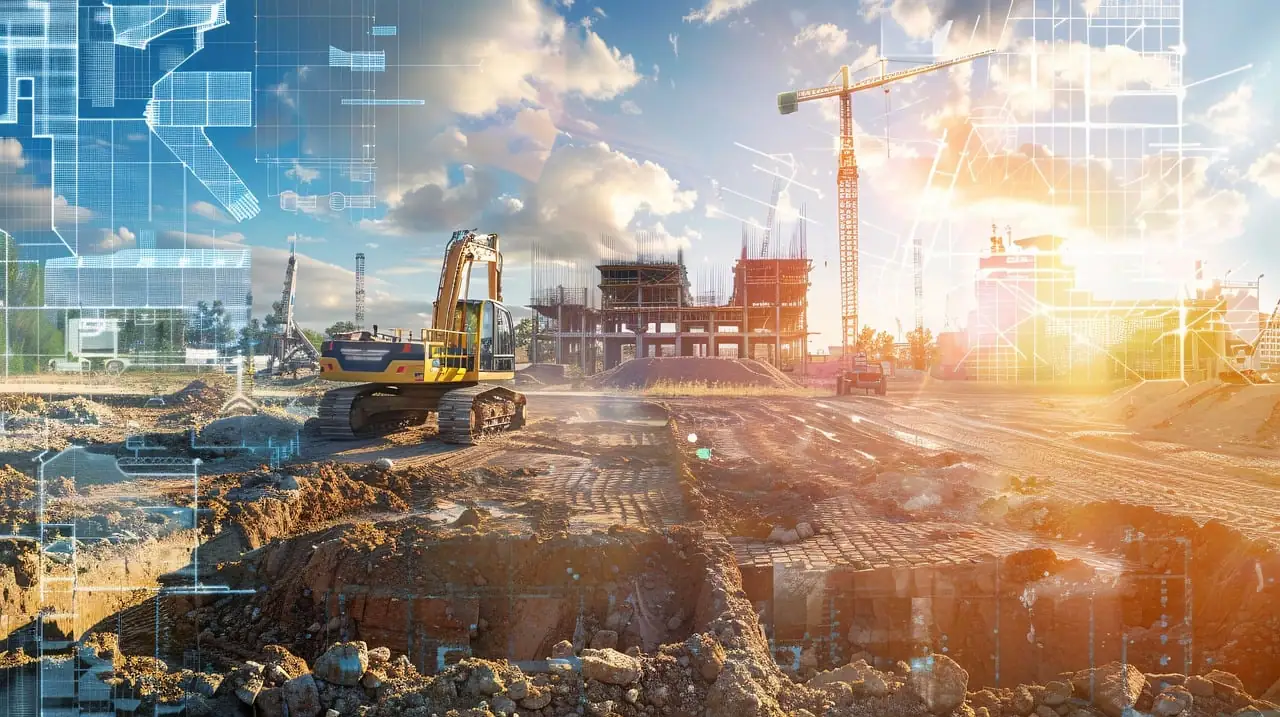
Expert Tips on Choosing Earthmoving Equipment for Large Projects
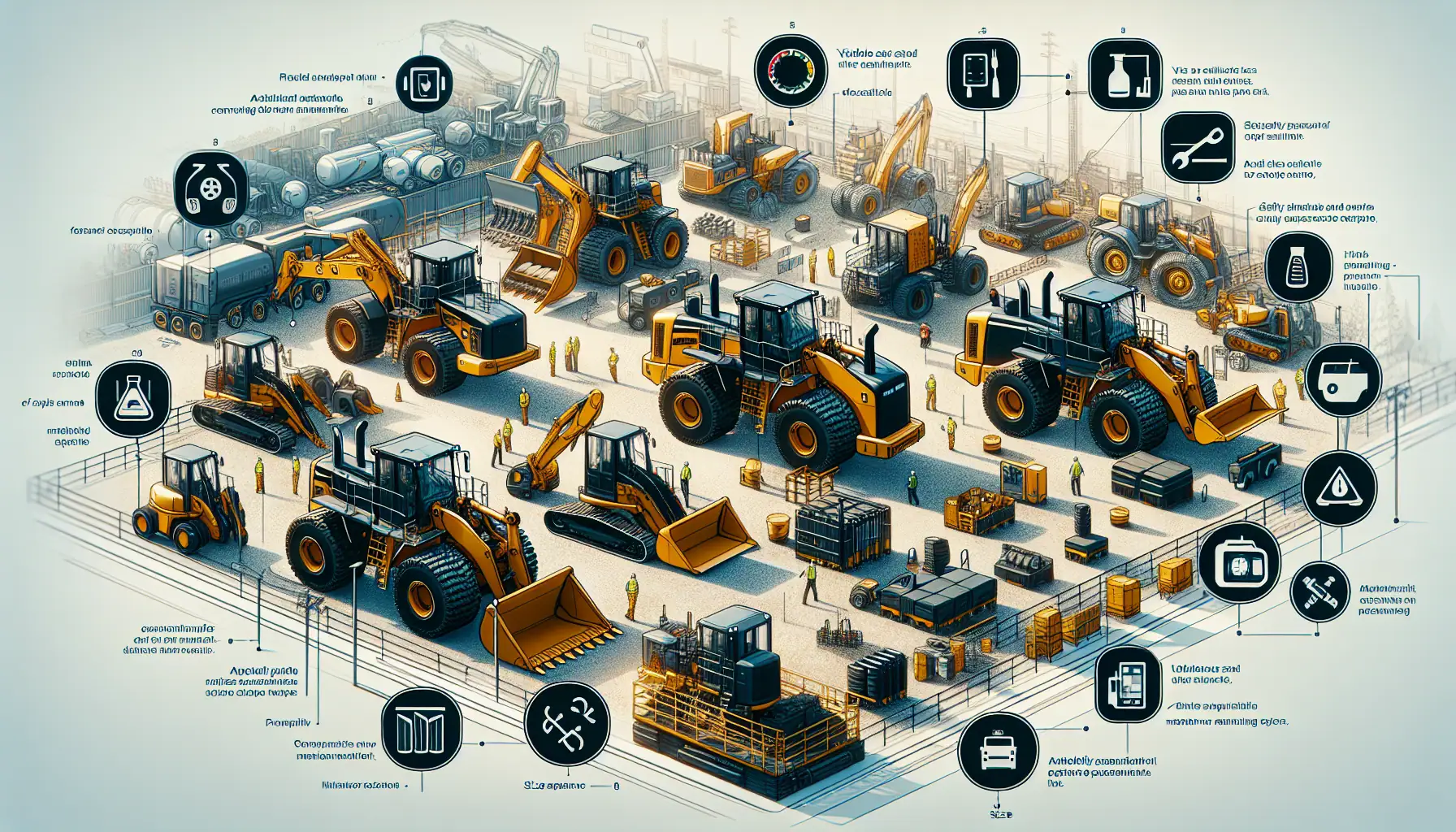
Top Functional Criteria for Selecting Heavy Construction Equipment
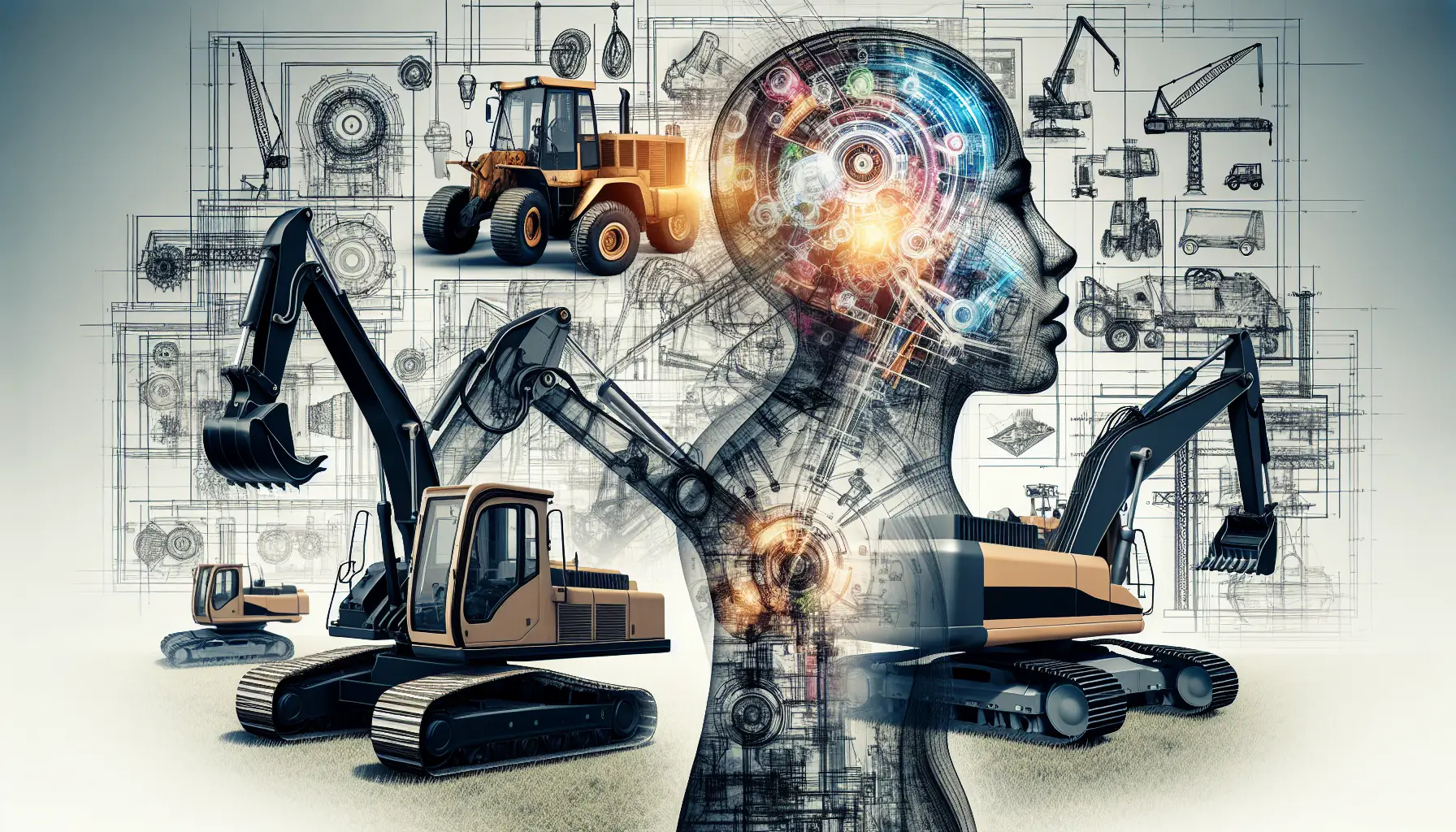
Construction Machinery: Detailed Guide to Equipment Specifications
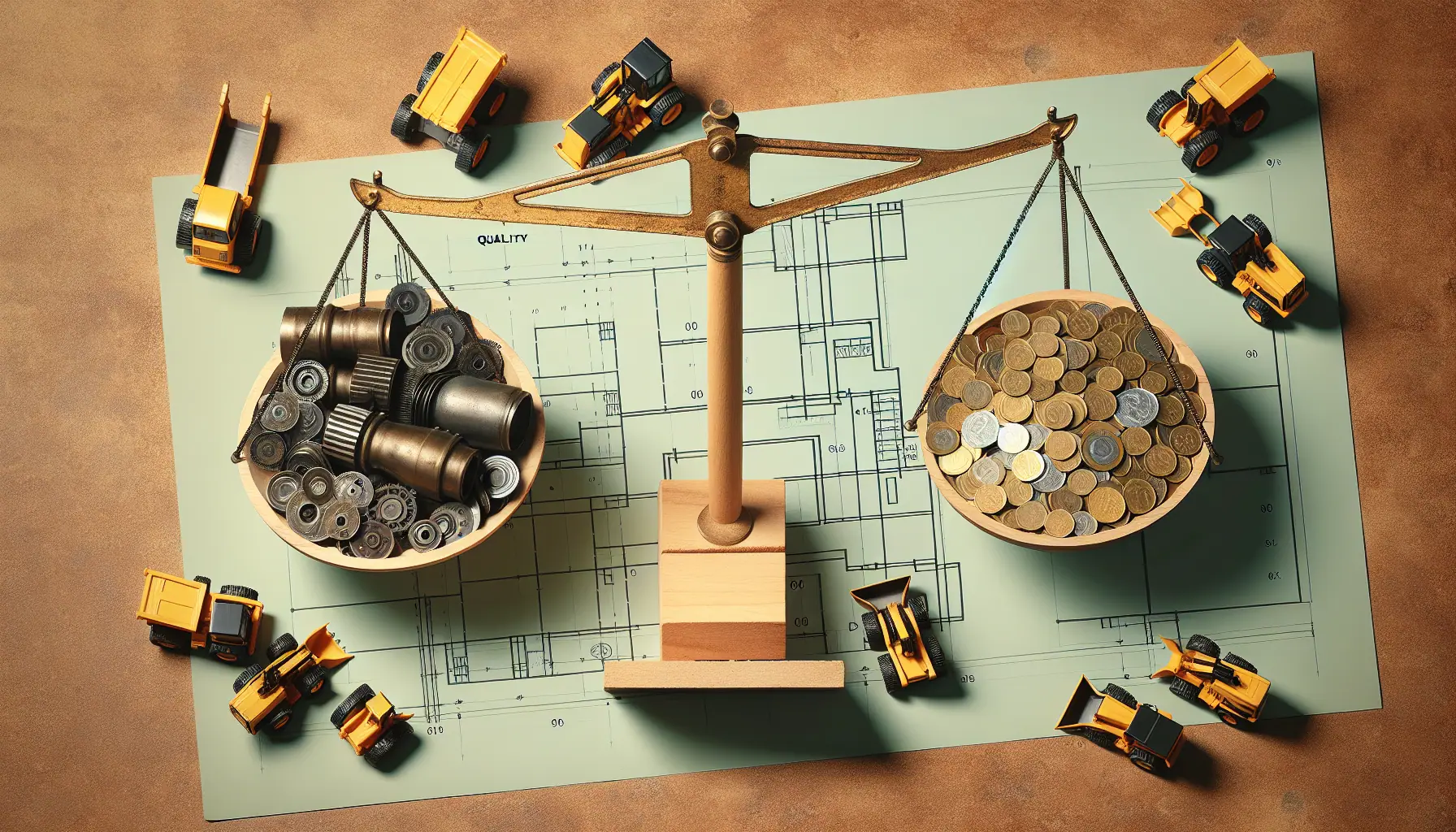
Heavy Machinery Prices: Key Factors in Cost and Quality Balance
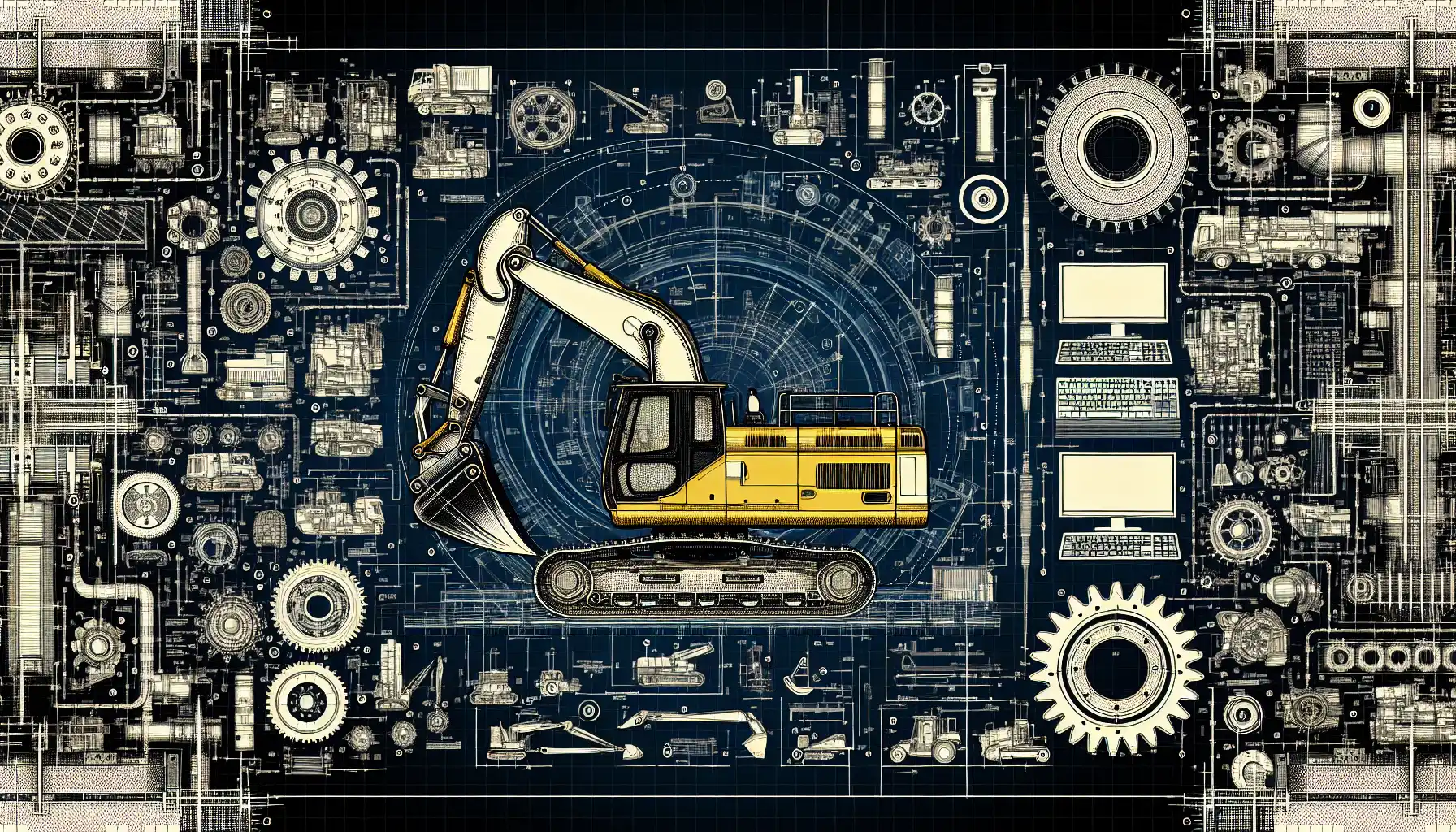
Best Construction Heavy Equipment Brands: Pros and Cons
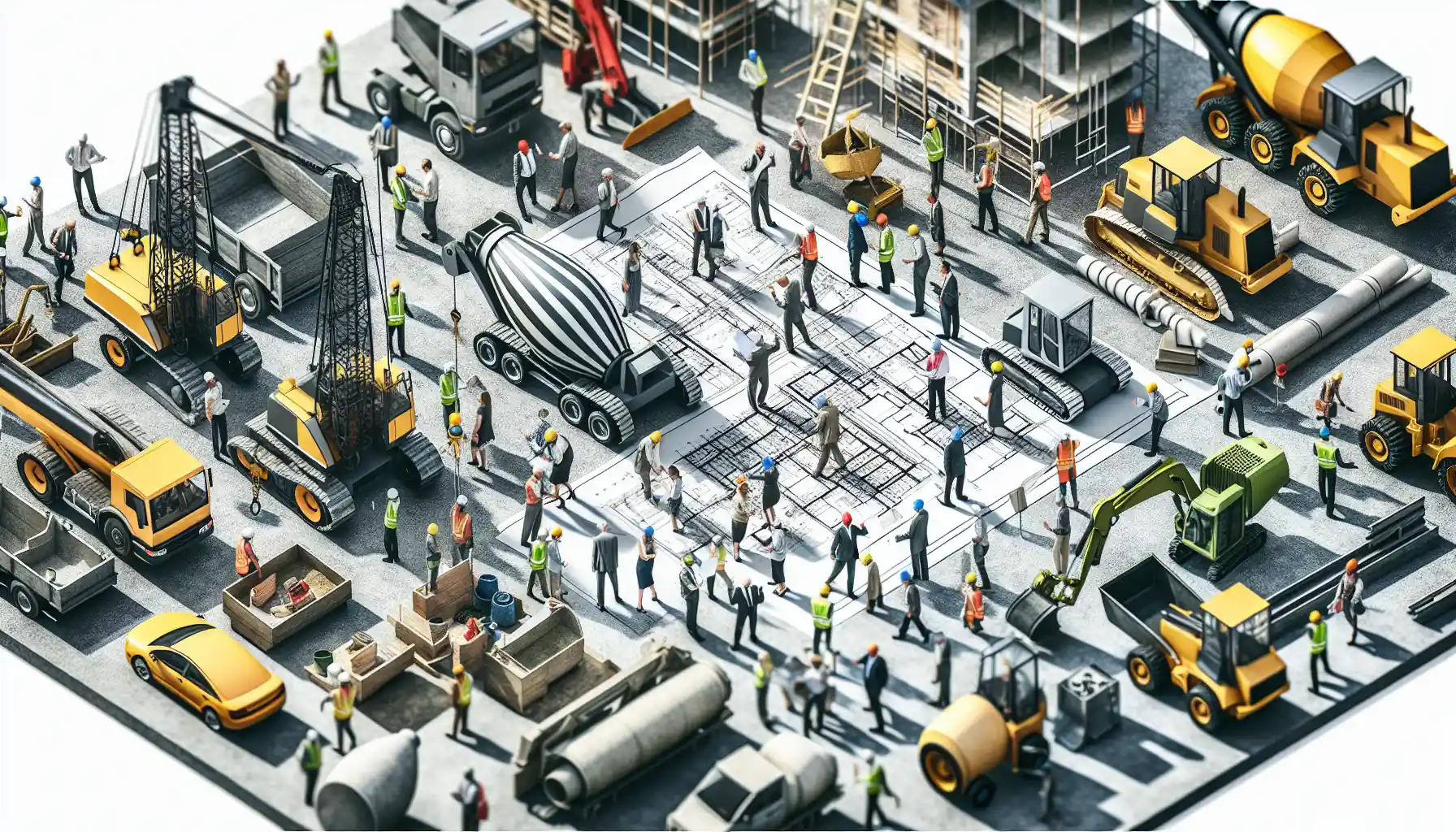
Construction Site Equipment: How to Determine Your Requirements
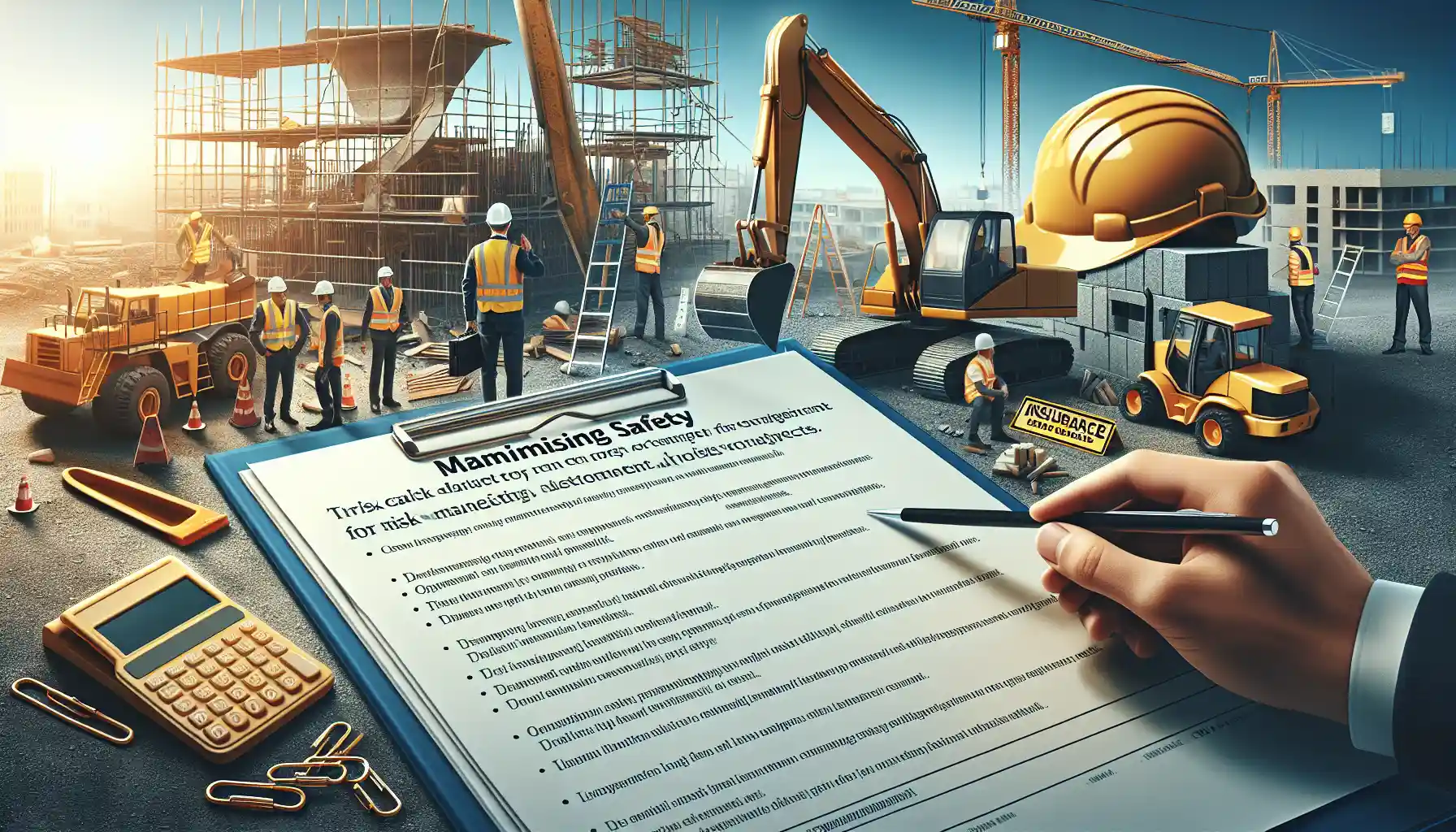
Maximizing Safety: Risk Management for Construction Projects
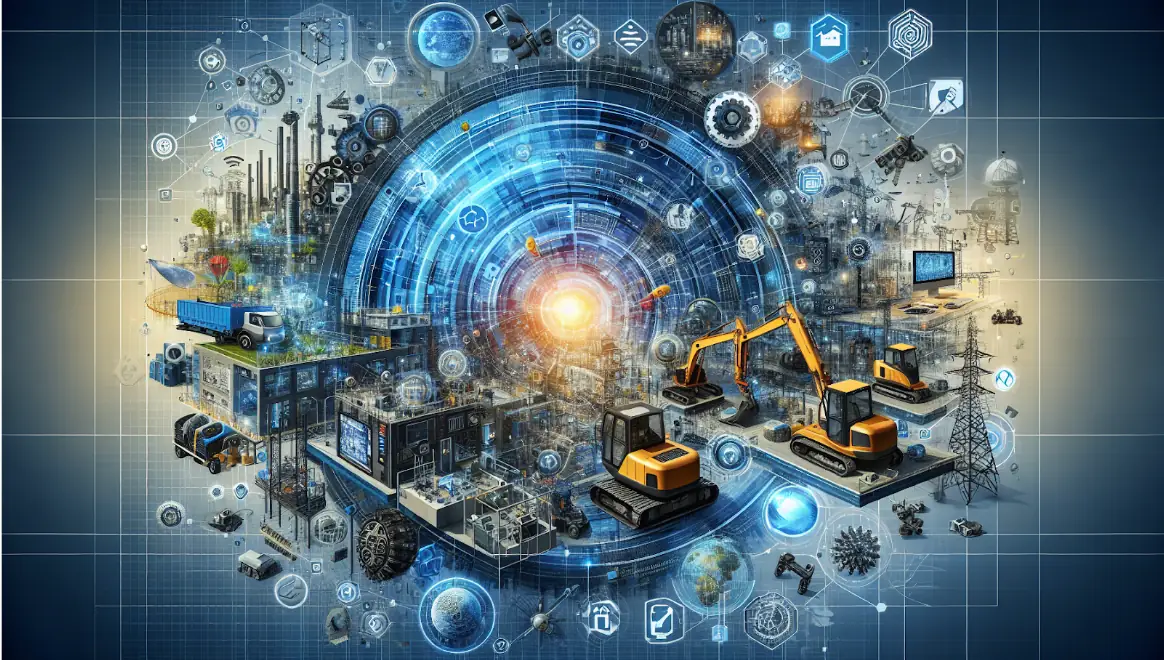
Innovations in Construction: Transforming Machinery and Equipment
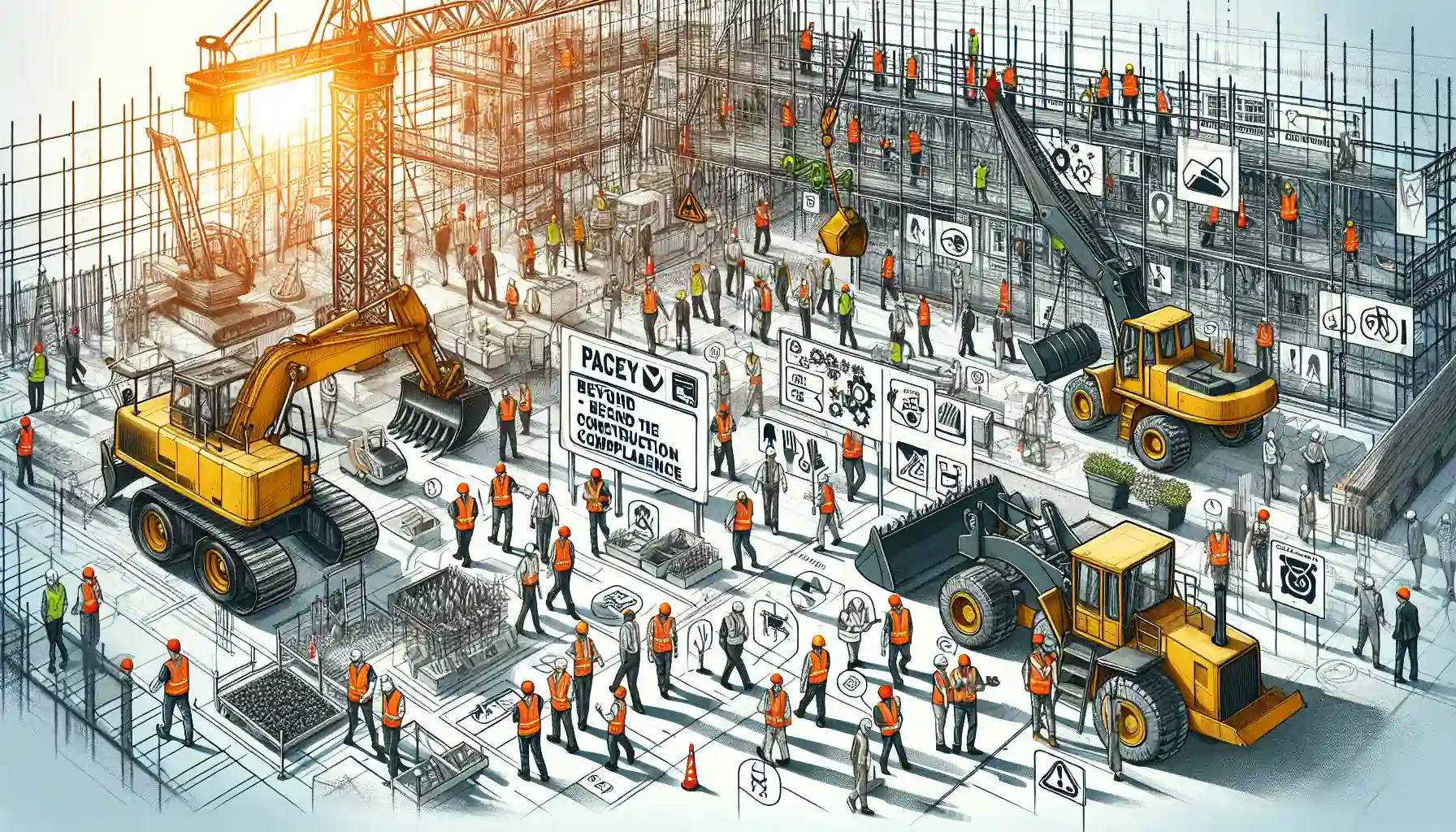
Heavy Equipment Safety: Beyond the Basics in Construction Compliance
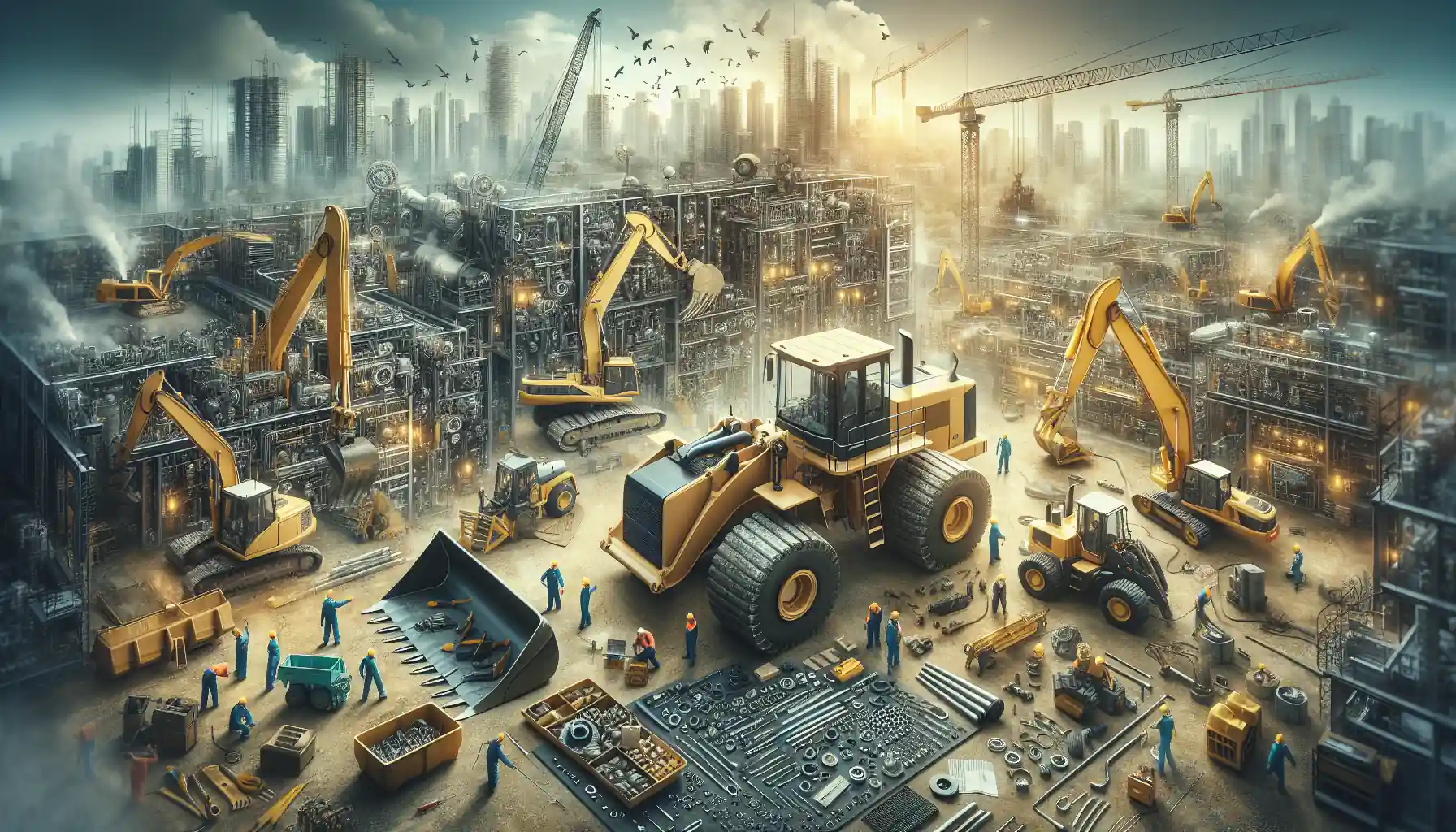
The Essential Handbook for Construction Equipment Repair and Maintenance
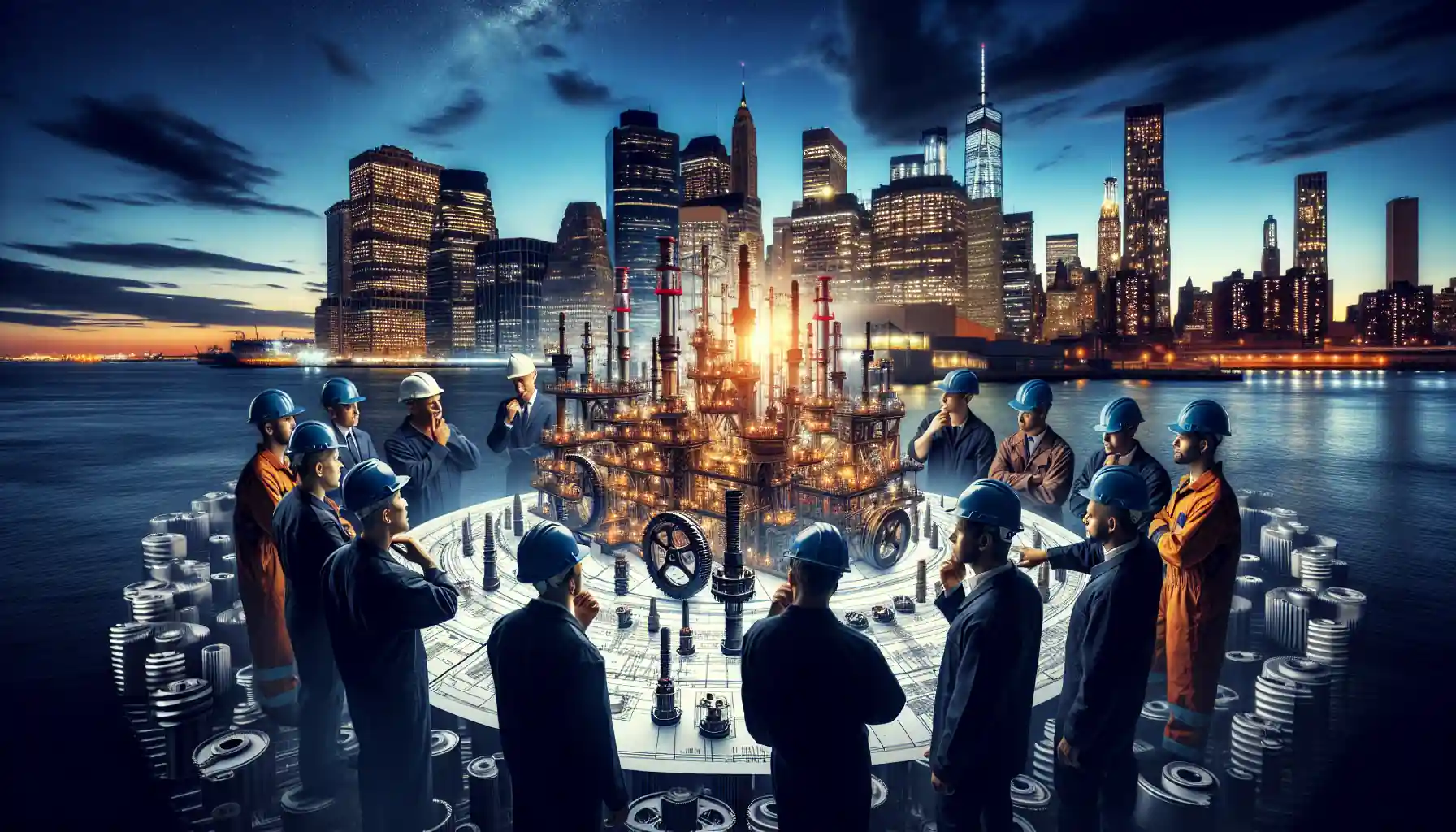
How to Efficiently Source Oil and Gas Machinery Parts in NYC
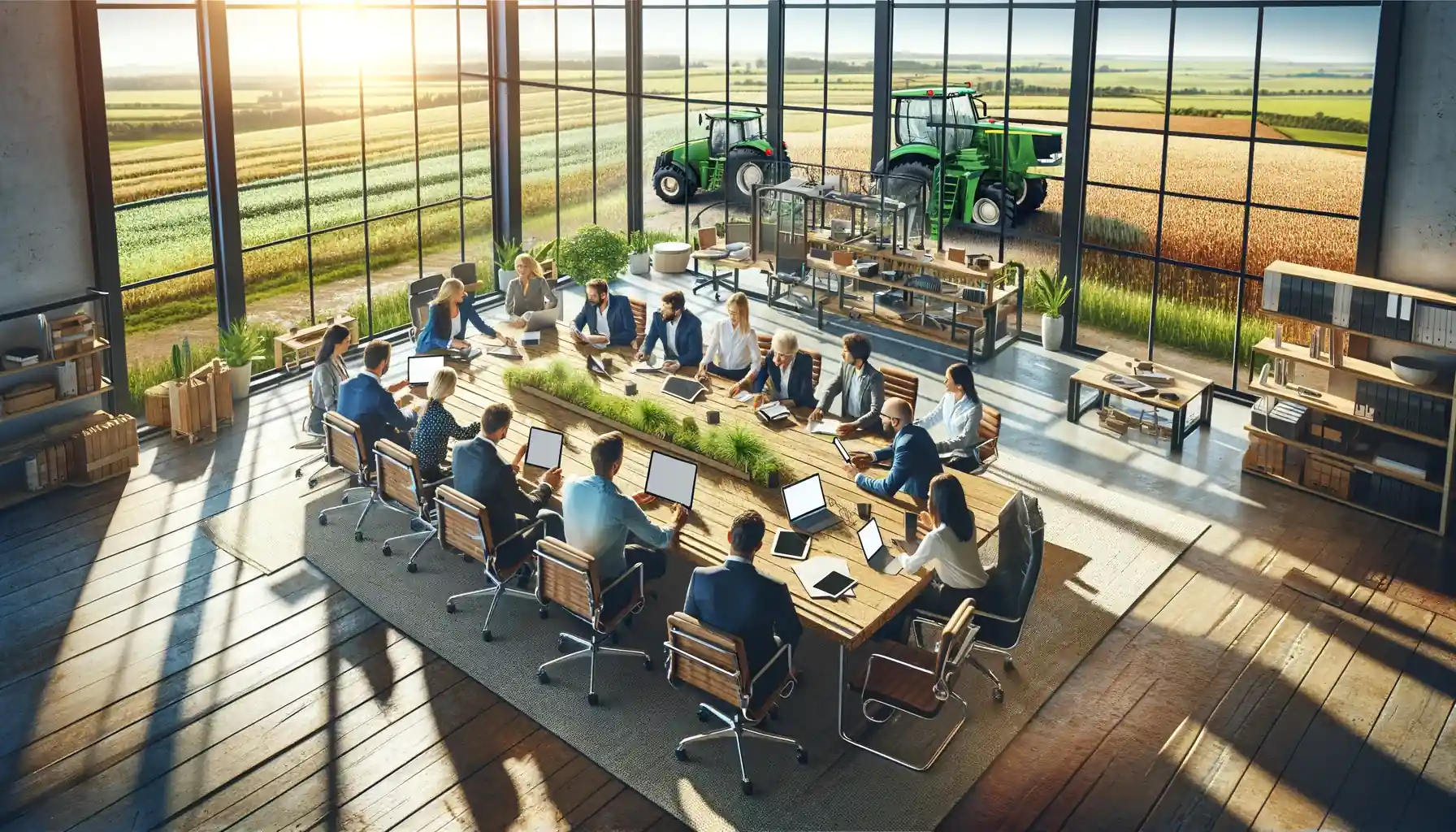
Essential Guide to Sourcing Agriculture Equipment Parts
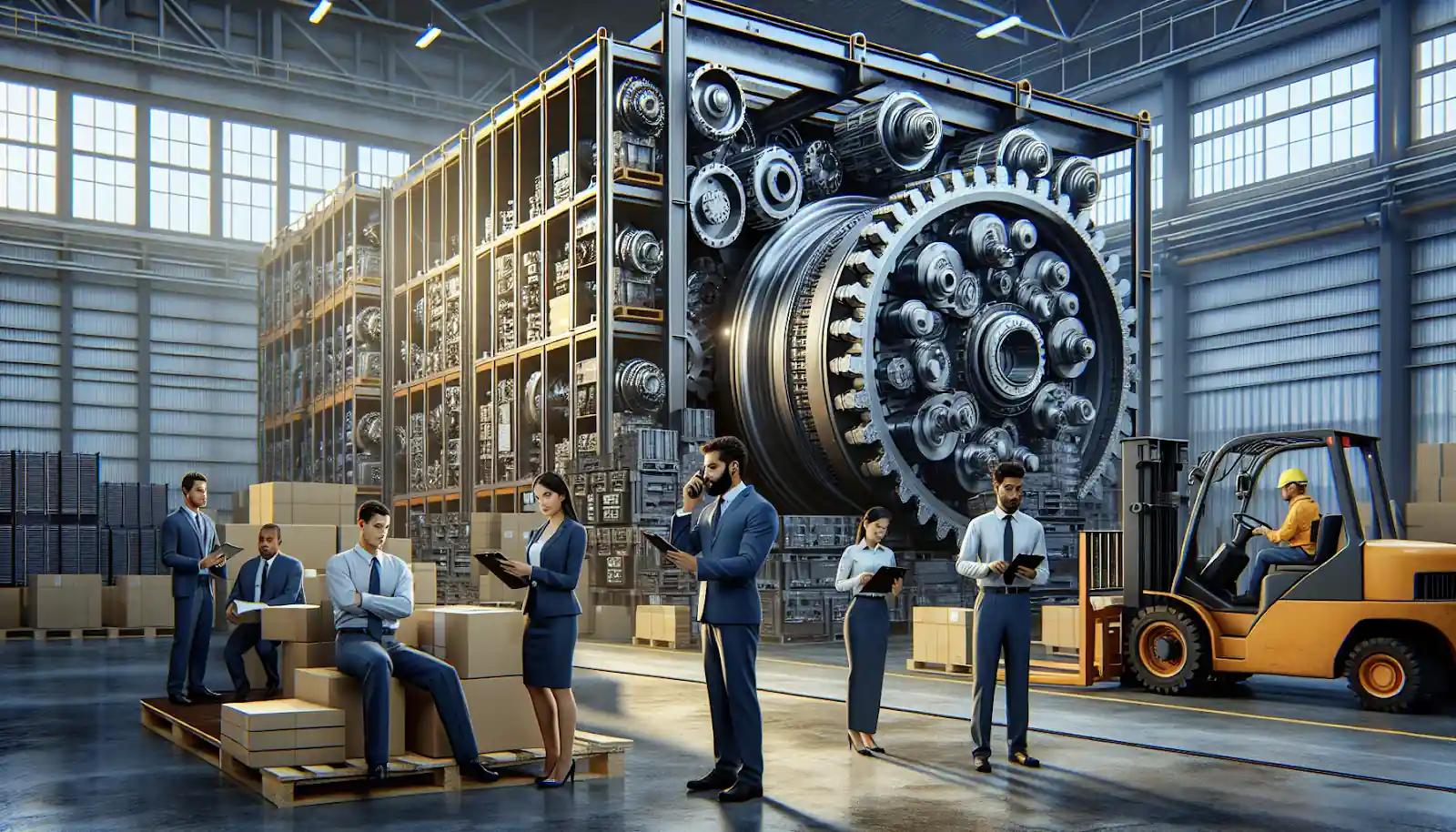
How to Source Mining Machinery Parts: Tips and Strategies
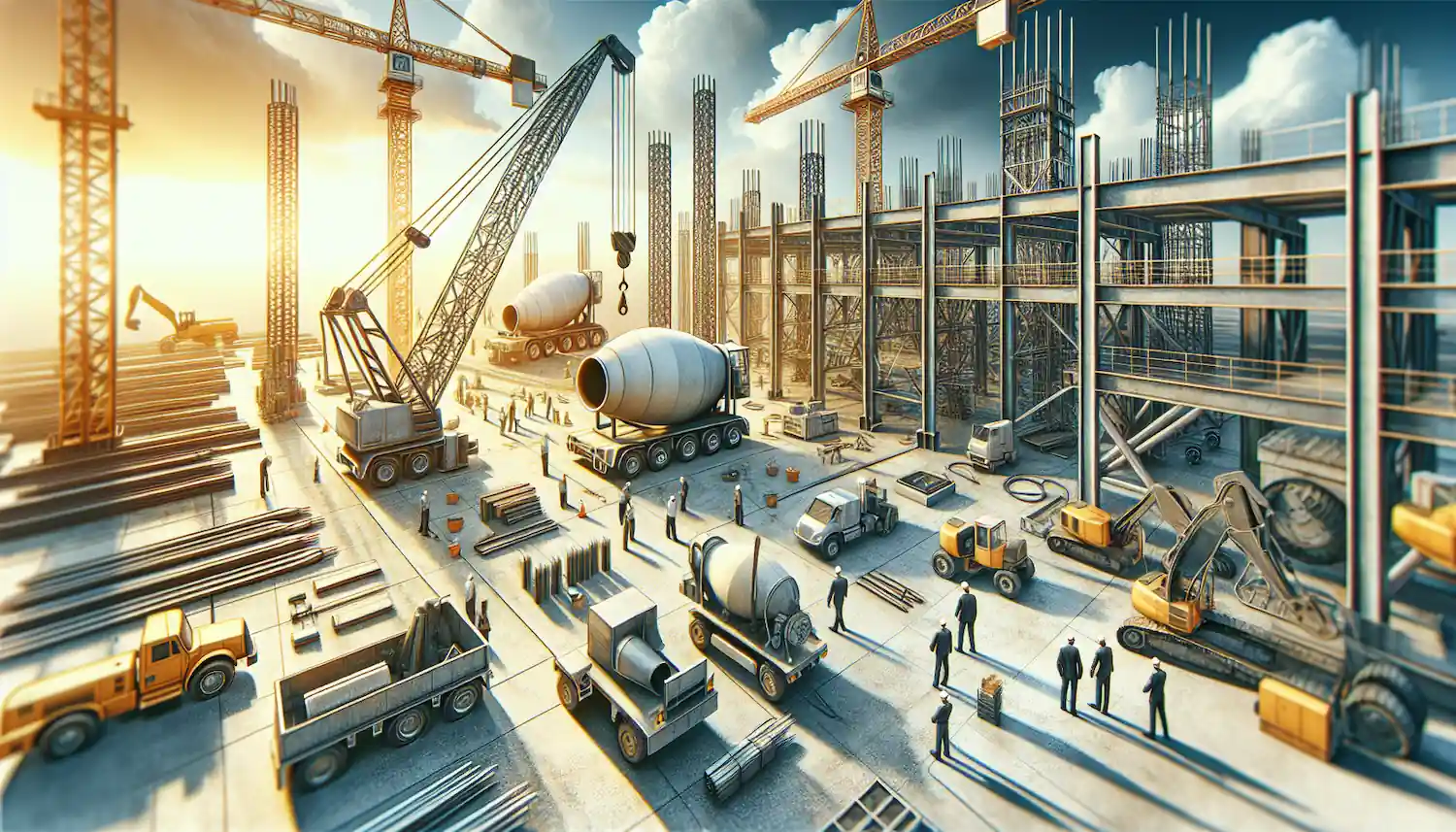