How to Select Construction Machinery with Optimal Equipment Maintenance in Mind
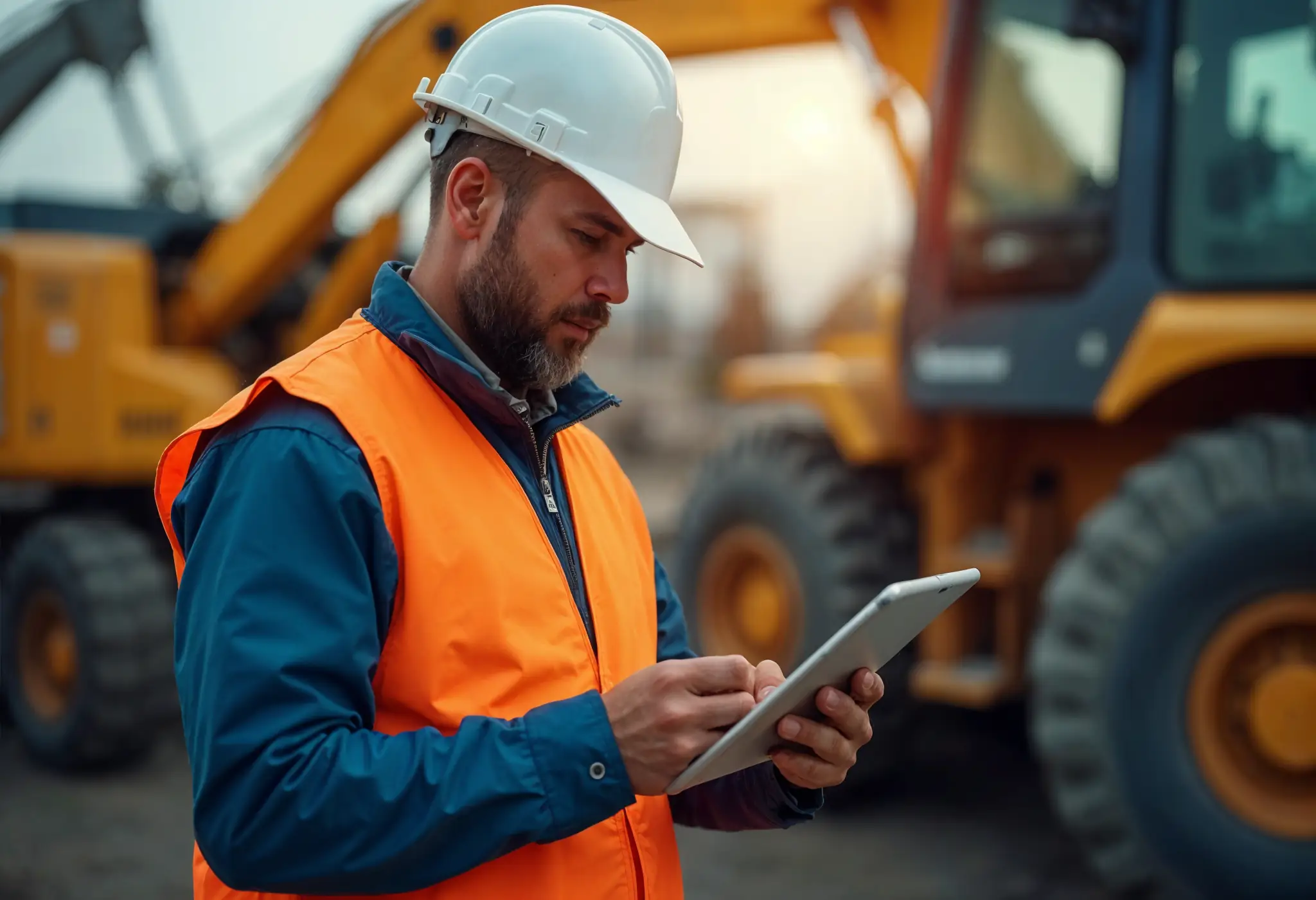
Your equipment maintenance programs play a vital role in machinery reliability and performance. The maintenance of machinery impacts everything from daily operations to long-term profitability, making it essential to consider maintenance requirements during the selection process.
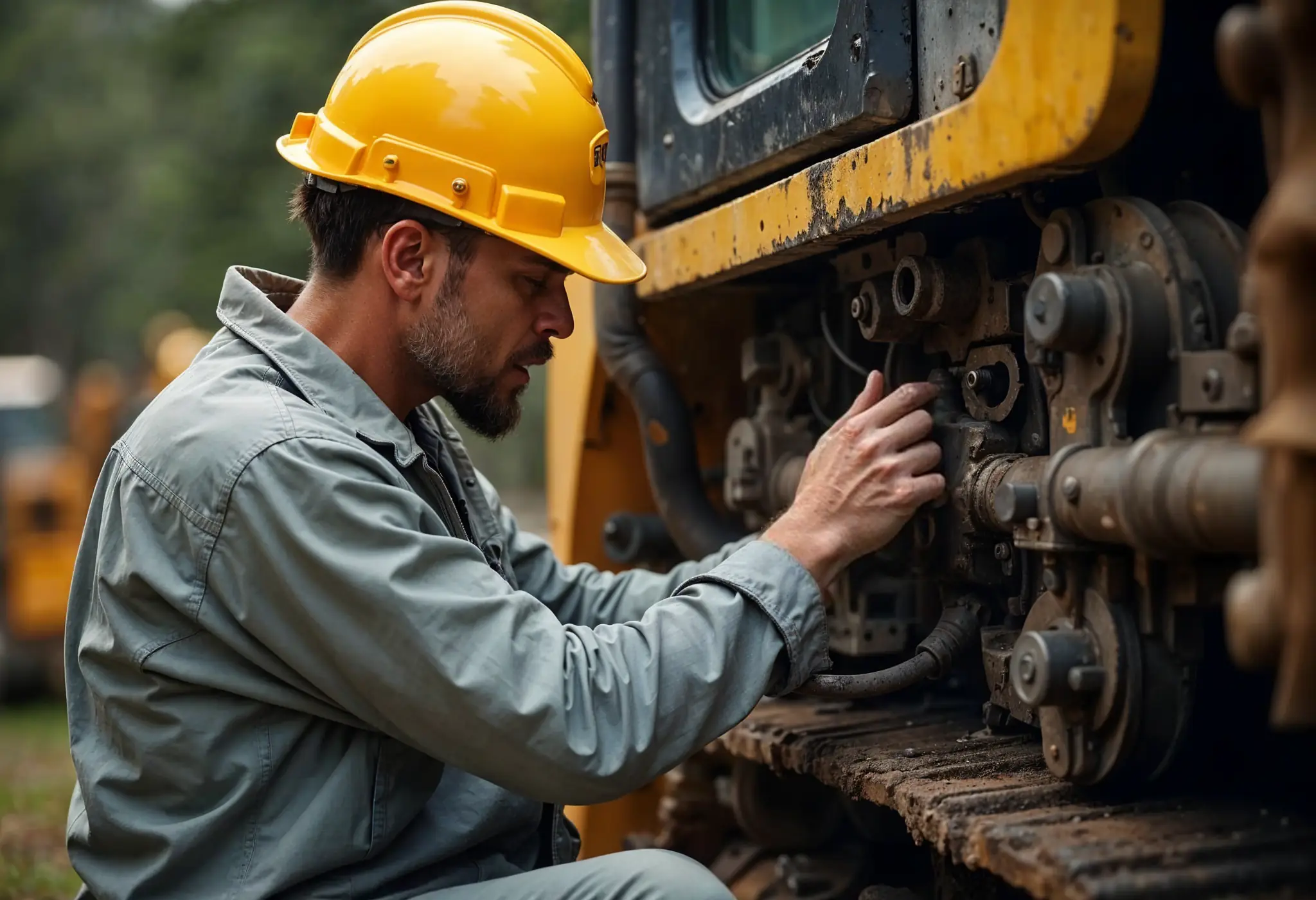
This guide will help you understand how to evaluate maintenance needs, identify design features that simplify upkeep, leverage modern technology for preventive maintenance, and prepare your team for optimal equipment care. You will discover practical approaches to select construction machinery that aligns with your maintenance capabilities and business goals.
Evaluating Maintenance Requirements During Equipment Selection
When evaluating construction machinery, proper maintenance documentation and support systems are crucial factors that can significantly impact your long-term operational success. Studies show that equipment maintenance costs typically represent 15-25% of total enterprise equipment costs annually, making it a critical consideration in your selection process.
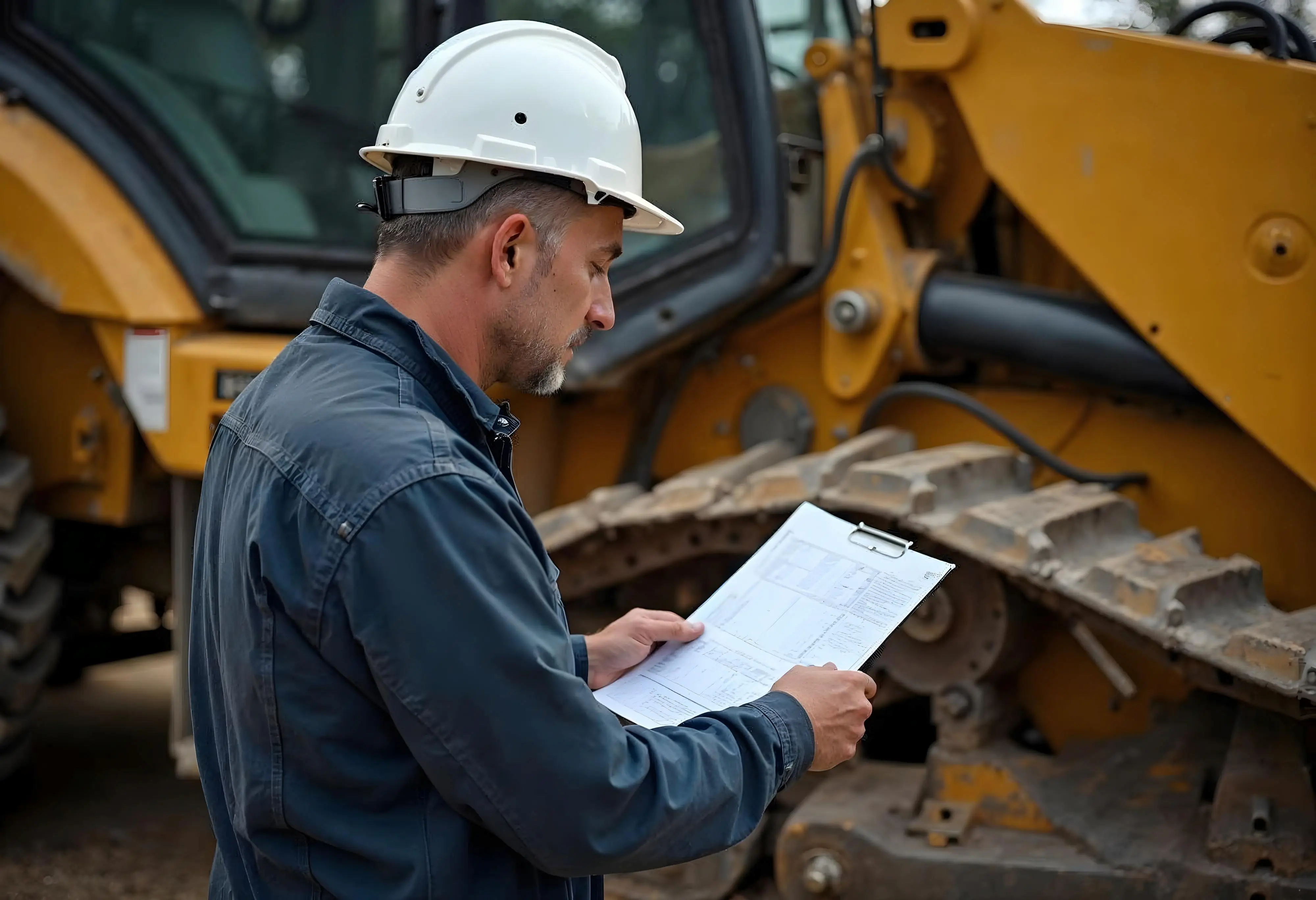
Assessing Maintenance History and Documentation
Your equipment maintenance tracking should include comprehensive documentation of all maintenance activities. A well-maintained machine history card helps you:
- Track preventive maintenance schedules and activities
- Document parts replacements and construction equipment repairs
- Record technician observations and recommendations
- Monitor equipment downtime patterns
- Ensure regulatory compliance
Analyzing Parts Availability and Support Network
The availability of spare parts and a reliable support network directly influences your equipment's operational efficiency. Research indicates that having proper documentation of spares consumption allows you to estimate the rate of demand for spare parts with higher accuracy. When evaluating your support network, consider the manufacturer's parts distribution system and third-party maintenance providers, which can reduce costs by 50-90% on hardware maintenance.
Calculating Total Cost of Ownership Including Maintenance
Your equipment's price tag represents less than 10% of its total lifetime cost, with maintenance and repair fees having at least five times more relevance. Consider these key components when calculating TCO:
- Regular Maintenance - Cleaning, inspection, lubrication costs
- Reactive Repairs - Unexpected breakdown expenses
- Downtime Impact - Lost production and labor costs
- Parts Replacement - Inventory and procurement expenses
For expert guidance on optimizing your equipment maintenance program and accessing reliable parts support, contact MCH Parts for a free sourcing machinery consultation and quote.
Design Features That Optimize Maintenance Efficiency
Smart design features in modern construction equipment can significantly reduce your maintenance time and costs. When selecting machinery, understanding these design elements helps you make informed decisions that optimize your maintenance efficiency.
Accessibility of Key Components
Equipment accessibility directly impacts your maintenance efficiency and safety. Well-designed machinery provides clear access to critical components, reducing maintenance time and improving technician safety. Studies show that proper component accessibility can reduce maintenance time by up to 50% compared to poorly designed equipment. Your maintenance personnel should be able to easily reach all service points without compromising their safety or requiring complex disassembly procedures.
Modular Design Benefits
Modular construction in equipment design offers remarkable advantages for your maintenance operations. Key benefits include:
- Standardization of components reducing inventory costs
- Quick component replacement minimizing downtime
- Enhanced product reliability through independent testing
- Simplified scaling and upgrades as needed
Research indicates that modular design can decrease manufacturing lead times and enhance productivity through simultaneous production processes. This approach allows you to easily customize and upgrade specific modules according to your requirements while maintaining consistent quality standards.
Built-in Diagnostic Systems
Modern equipment comes equipped with sophisticated diagnostic capabilities that revolutionize your equipment maintenance approach.
Diagnostic Feature Benefit:
- Real-time Monitoring - Continuous equipment health tracking
- Fault Detection - Early warning of potential issues
- Auto-correction - Self-initiated failure containment
- Root Cause Analysis - Reduced troubleshooting time
These systems can reduce your diagnostic time significantly, with studies showing up to 70% reduction in energy consumption through efficient monitoring and maintenance.
For expert guidance on selecting equipment with optimal maintenance features and accessing reliable diagnostic tools, contact MCH Parts for a free sourcing machinery consultation and quote.
Technology Integration for Preventive Maintenance
The integration of smart technology into your construction machinery transforms traditional maintenance approaches into data-driven strategies. IoT sensors and advanced analytics are revolutionizing how you monitor and maintain your equipment fleet, with studies showing up to 50% reduction in unplanned downtime and 20-40% extension in machinery life.
IoT Sensors and Real-time Monitoring
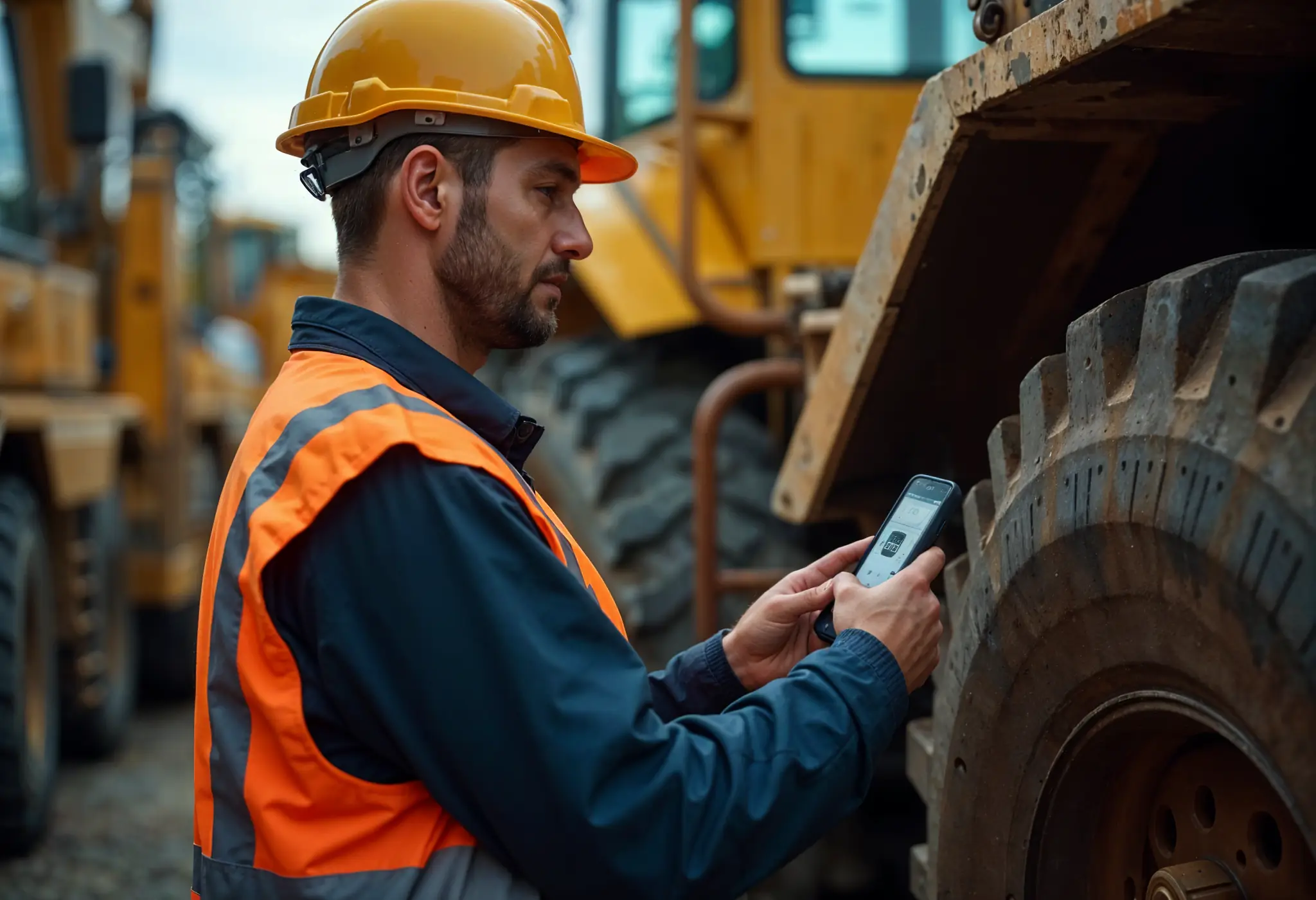
Your equipment's health can now be continuously monitored through sophisticated IoT sensors that measure critical parameters like temperature, vibration, and pressure. These sensors provide real-time alerts to your cloud platform, enabling instant visibility across multiple job sites. Consider these proven benefits:
Monitoring Aspect Business Impact:
- Real-time Alerts - Immediate issue identification
- Performance Tracking - Optimized equipment utilization
- Fuel Management - Reduced operational costs
- Location Monitoring - Enhanced fleet coordination
Maintenance Management Software Compatibility
Modern Computerized Maintenance Management Systems (CMMS) seamlessly integrate with your IoT infrastructure, creating a unified platform for equipment oversight. The software automatically generates work orders when sensors detect potential issues, streamlining your maintenance workflow. These systems can process data from various sources, including:
- Thermographic tools and vibration sensors
- SCADA and PLC systems
- Building Management Systems (BMS)
Data Analytics Capabilities
Your maintenance decisions become more precise with advanced analytics capabilities. The system continuously analyzes equipment data to predict potential failures and optimize maintenance schedules. Studies indicate that predictive maintenance analytics can significantly improve efficiency by gathering and analyzing equipment data in real-time.
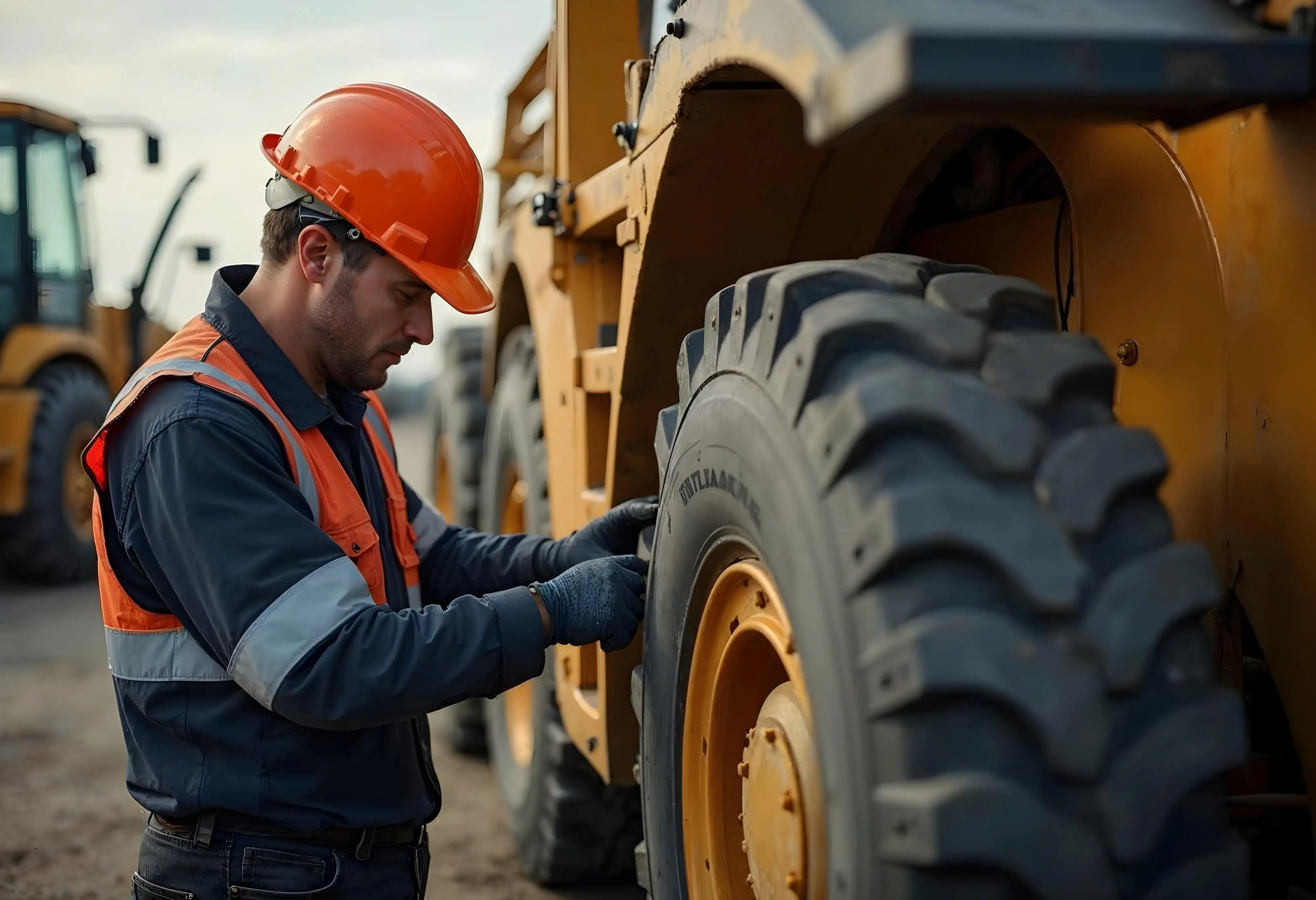
Through data analytics, you can:
- Create predictive models for equipment performance
- Optimize maintenance schedules based on actual usage
- Reduce operational costs through better resource allocation
- Identify safety issues before they become critical
For expert guidance on implementing IoT-enabled maintenance solutions and accessing reliable monitoring systems, contact MCH Parts for a free sourcing machinery consultation and quote.
Training and Operator Considerations
Your investment in proper training and expertise development directly influences machinery longevity and operational efficiency. Studies show that skilled equipment operators can reduce fuel consumption by 10-12% daily compared to untrained personnel.
Operator Training Requirements
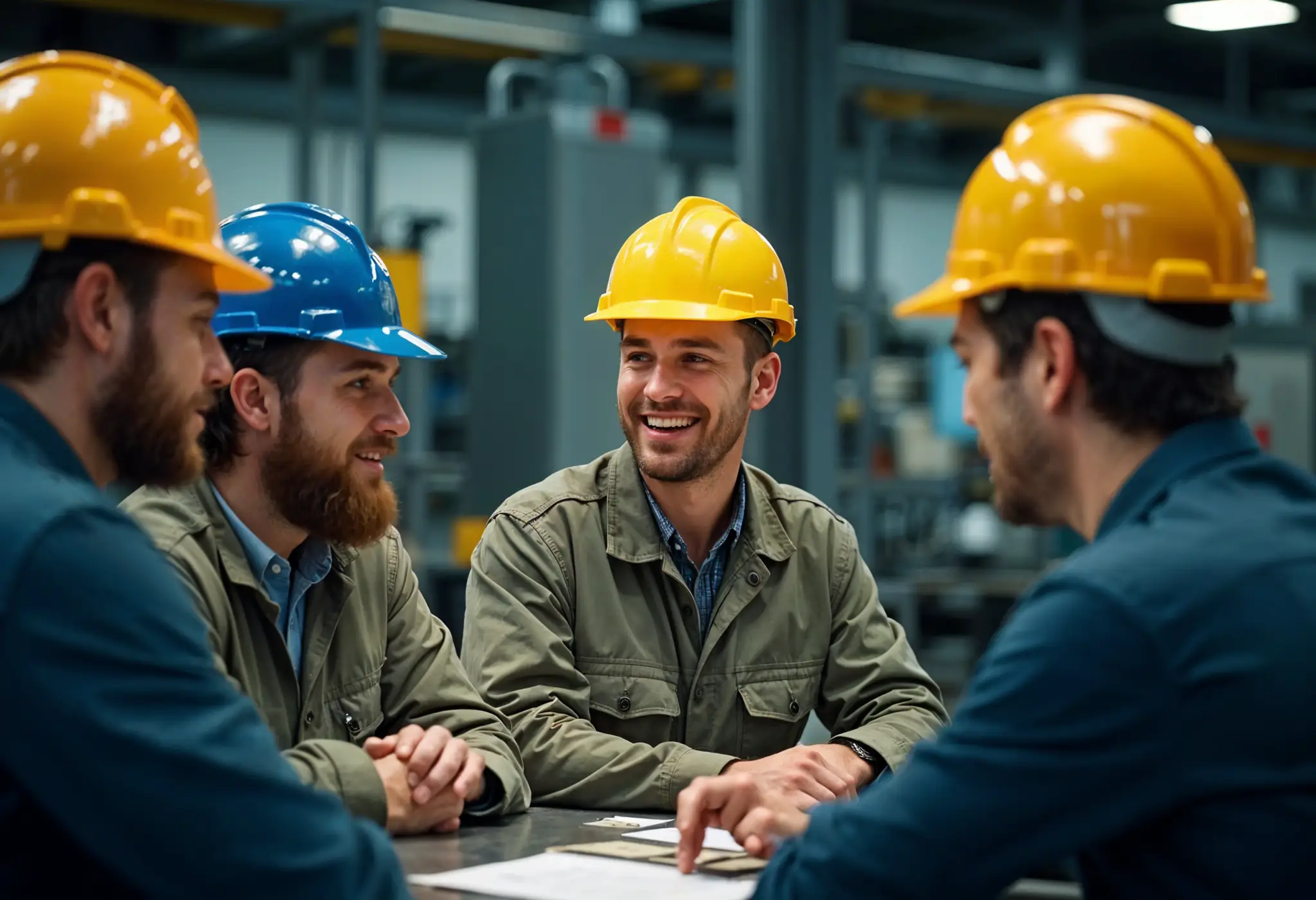
Proper operator certification and training are fundamental to your equipment's optimal performance. A trained operator can reduce cycle times by three to four seconds, significantly increasing your profit margin over time. Essential requirements include:
- High school diploma or GED for basic qualification
- Completion of heavy equipment training program
- Specific certifications for specialized equipment
- Regular safety protocol updates
Maintenance Staff Expertise Needs
Your maintenance technicians require comprehensive technical knowledge and continuous learning opportunities. Research indicates that through proper training, maintenance staff can reduce equipment downtime by identifying potential issues early.
Training Area Business Impact:
- Technical Skills - 50-90% reduction in hardware maintenance costs
- Safety Protocols - Decreased accident rates
- Diagnostic Expertise - Faster problem resolution
- Preventive Maintenance - Extended equipment lifespan
Documentation and Support Resources
Implementing robust documentation systems ensures consistent maintenance practices across your team. Studies show that proper maintenance records help demonstrate compliance with safety protocols and environmental guidelines. Your documentation strategy should focus on:
Training Materials: Comprehensive guides and checklists that ensure consistent maintenance procedures across shifts.
Digital Resources: Modern CMMS software that helps track training completion and certification renewals.
Knowledge Repository: A centralized system capturing maintenance best practices and troubleshooting techniques, which can reduce diagnostic time by up to 70%.
For expert guidance on developing comprehensive training programs and accessing reliable maintenance documentation systems, contact MCH Parts for a free sourcing machinery consultation and quote.
Conclusion
Smart machinery selection paired with proper equipment maintenance strategies creates a strong foundation for construction business success. Through this comprehensive guide, you learned essential aspects of equipment selection that directly impact your maintenance efficiency and operational costs.
Your equipment selection process now includes critical evaluation points:
- Documentation and support systems assessment
- Analysis of design features that simplify maintenance
- Integration of preventive maintenance technology
- Development of proper training programs
Research shows that these strategic approaches can reduce your maintenance costs by 15-25% annually while extending equipment life by 20-40%. Proper documentation, skilled operators, and advanced monitoring systems work together to minimize downtime and maximize your return on investment.
Consider reaching out to MCH Parts for a free sourcing machinery or parts consultation, ensuring your business benefits from top-tier equipment and service. Making informed decisions about construction machinery today helps secure your operational efficiency tomorrow.
FAQs
1. How should one go about selecting construction equipment for a project?
When choosing construction equipment, consider the overall cost of the project. Each piece of equipment contributes to the total expense. Key considerations include the equipment's versatility, adaptability, fuel consumption, and potential costs.
2. What criteria should be considered when selecting construction equipment?
Selection should be based on several factors including the equipment's versatility, maintainability, operational efficiency, frequency of part replacement, and the initial cost of the equipment.
3. What are the main types of maintenance strategies for machinery?
There are three primary maintenance strategies:
- Preventive maintenance: Regular and periodic maintenance based on time schedules.
- Corrective maintenance: Maintenance that is performed when an issue is identified.
- Predetermined maintenance: Maintenance that adheres to a manufacturer's specified schedule.
4. What are some effective tips for ensuring proper maintenance of machinery?
To maintain machinery effectively:
- Regularly inspect for wear and damage.
- Keep the machinery clean to prevent build-up that can lead to issues.
- Adhere to a strict maintenance schedule.
- Frequently use tested lubricants to reduce friction and wear.
- Protect components during storage to prevent environmental damage.
- Keep detailed records of maintenance schedules.
- Ensure you have a thorough understanding of your equipment's functions and requirements.
Read More
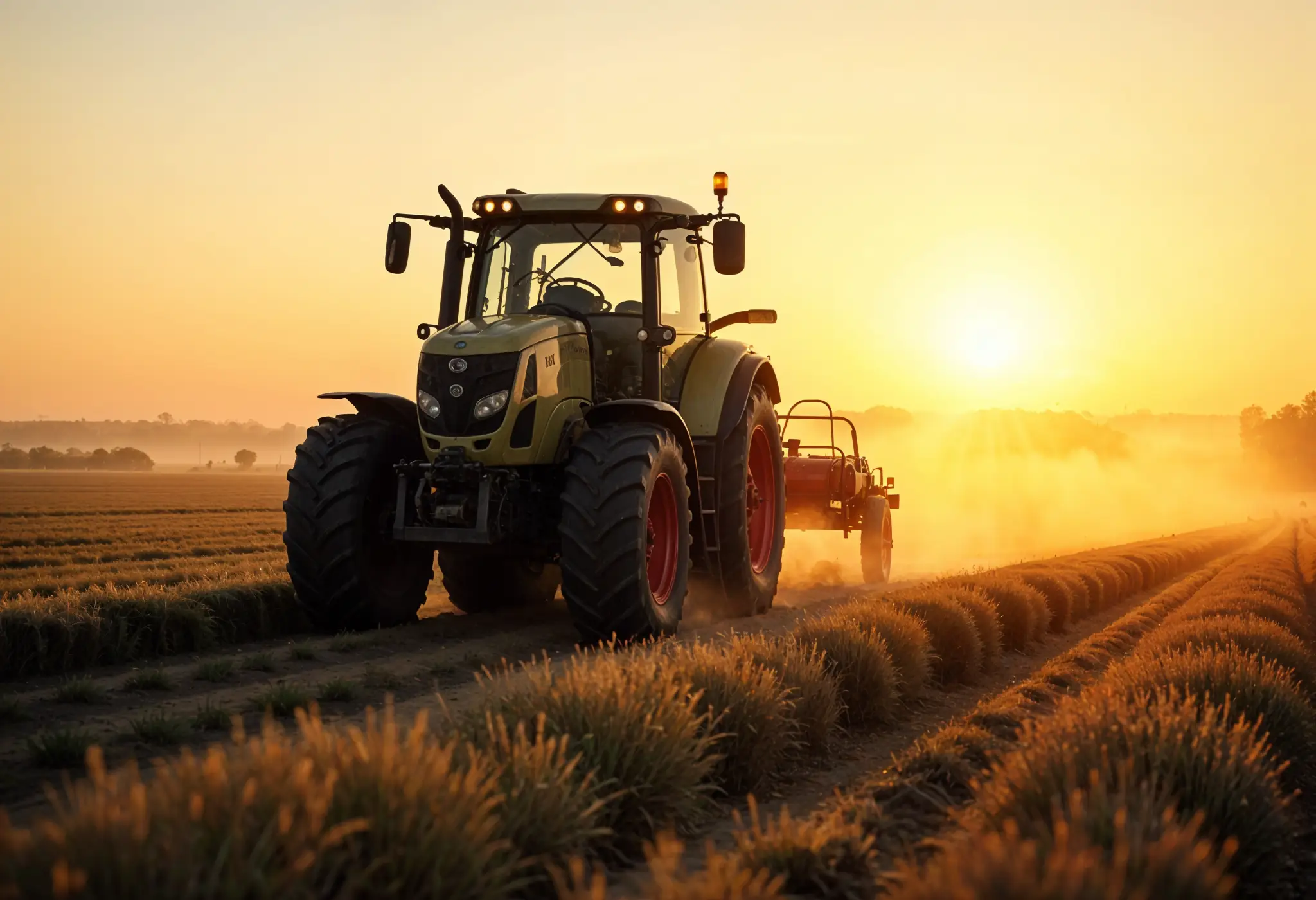
Top Hydraulic Components for Agricultural Equipment in 2025: Complete Guide
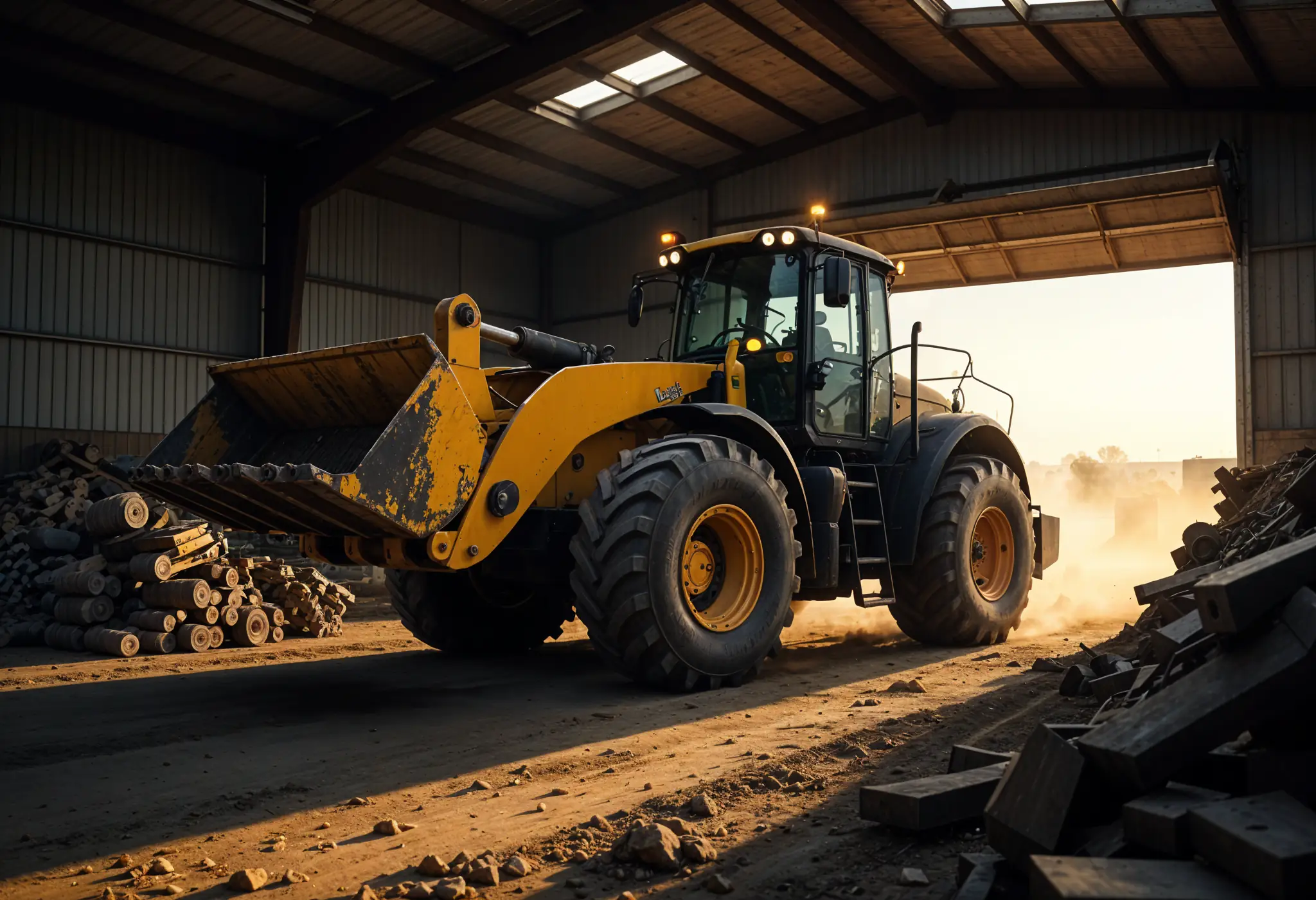
The Essential Farm Equipment Parts You Can't Afford to Run Out Of
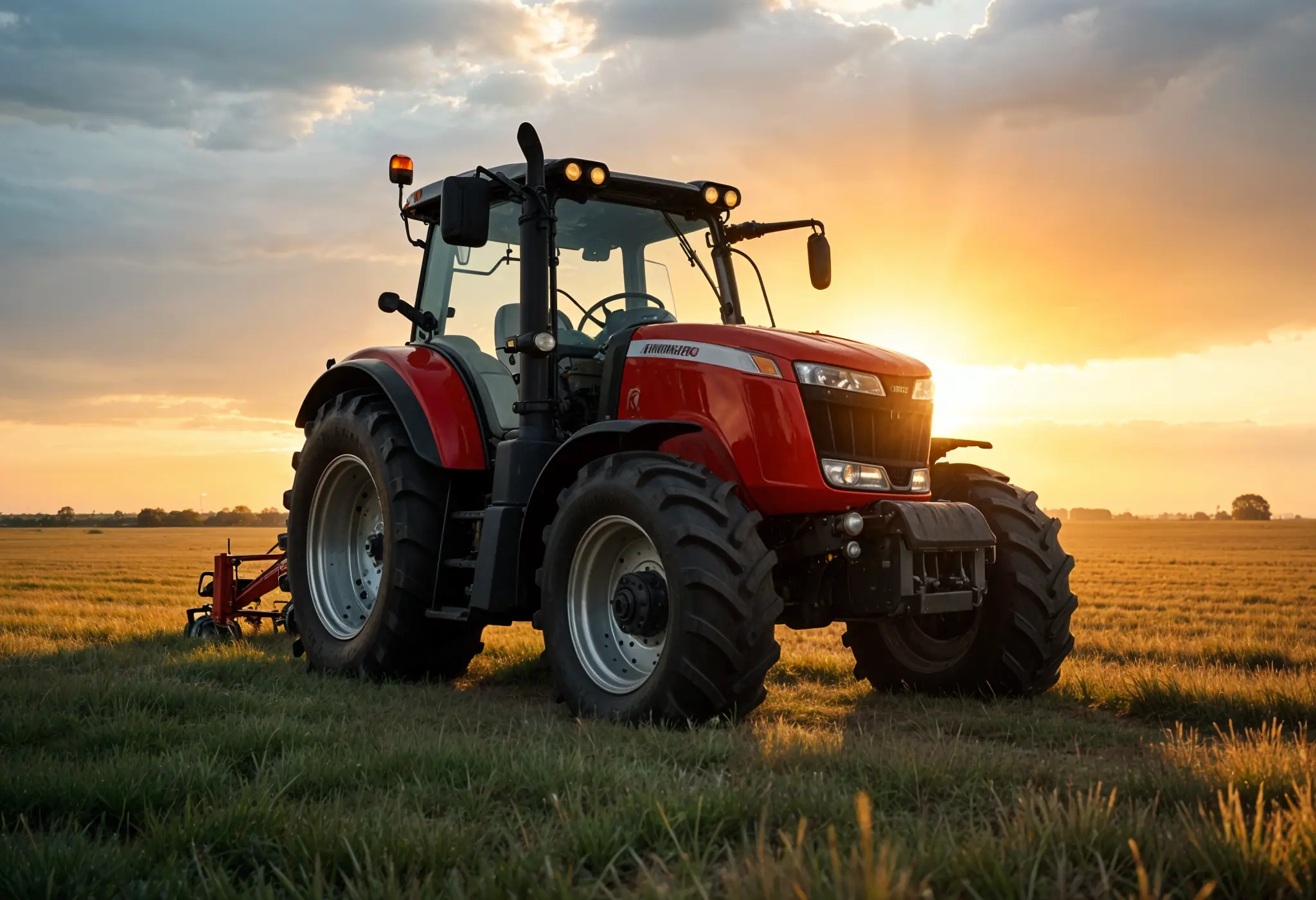
How to Service Farm Equipment: A Farmer's Guide to Zero Harvest Downtime
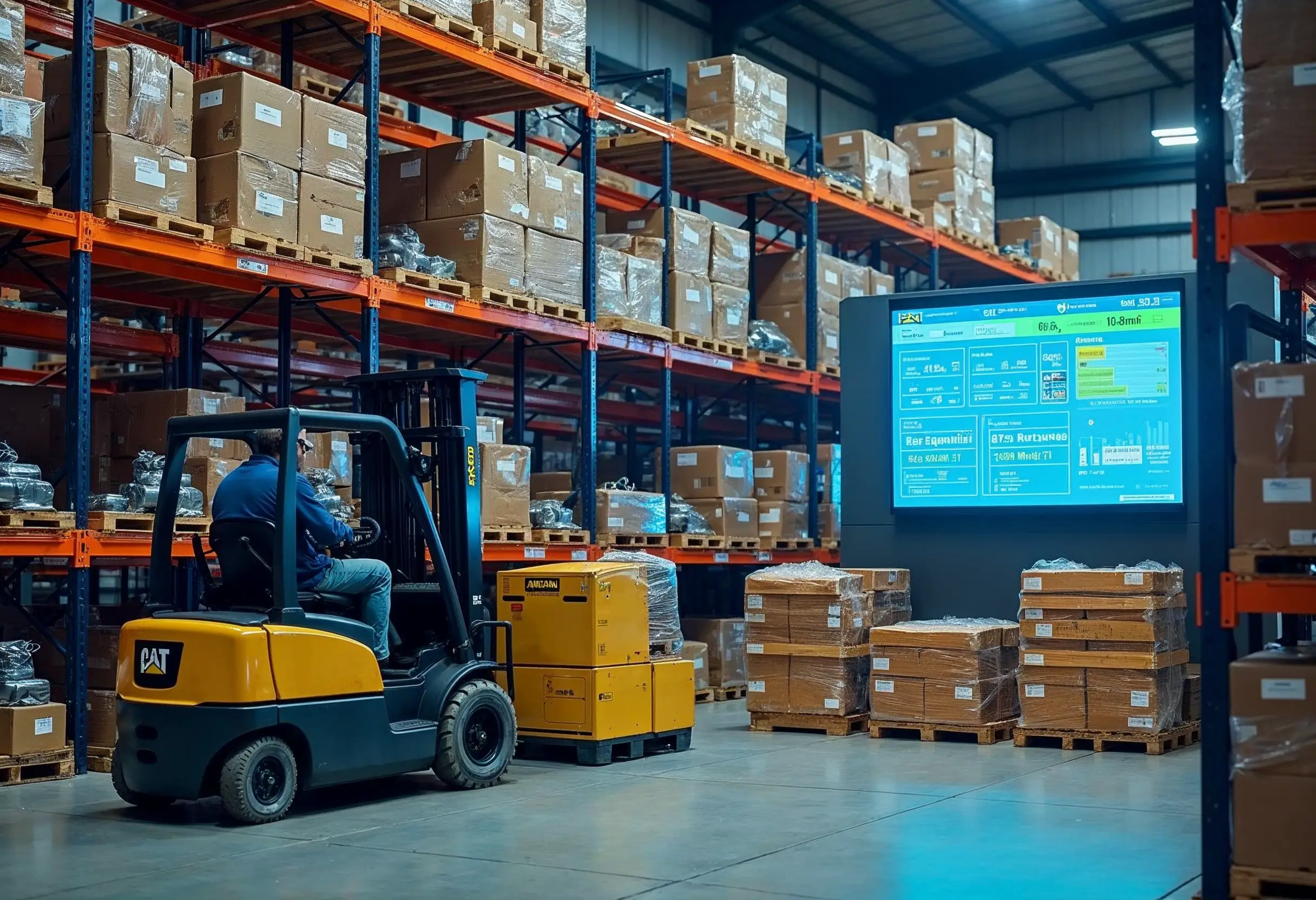
Construction Machinery Parts Suppliers: Expert Selection Guide
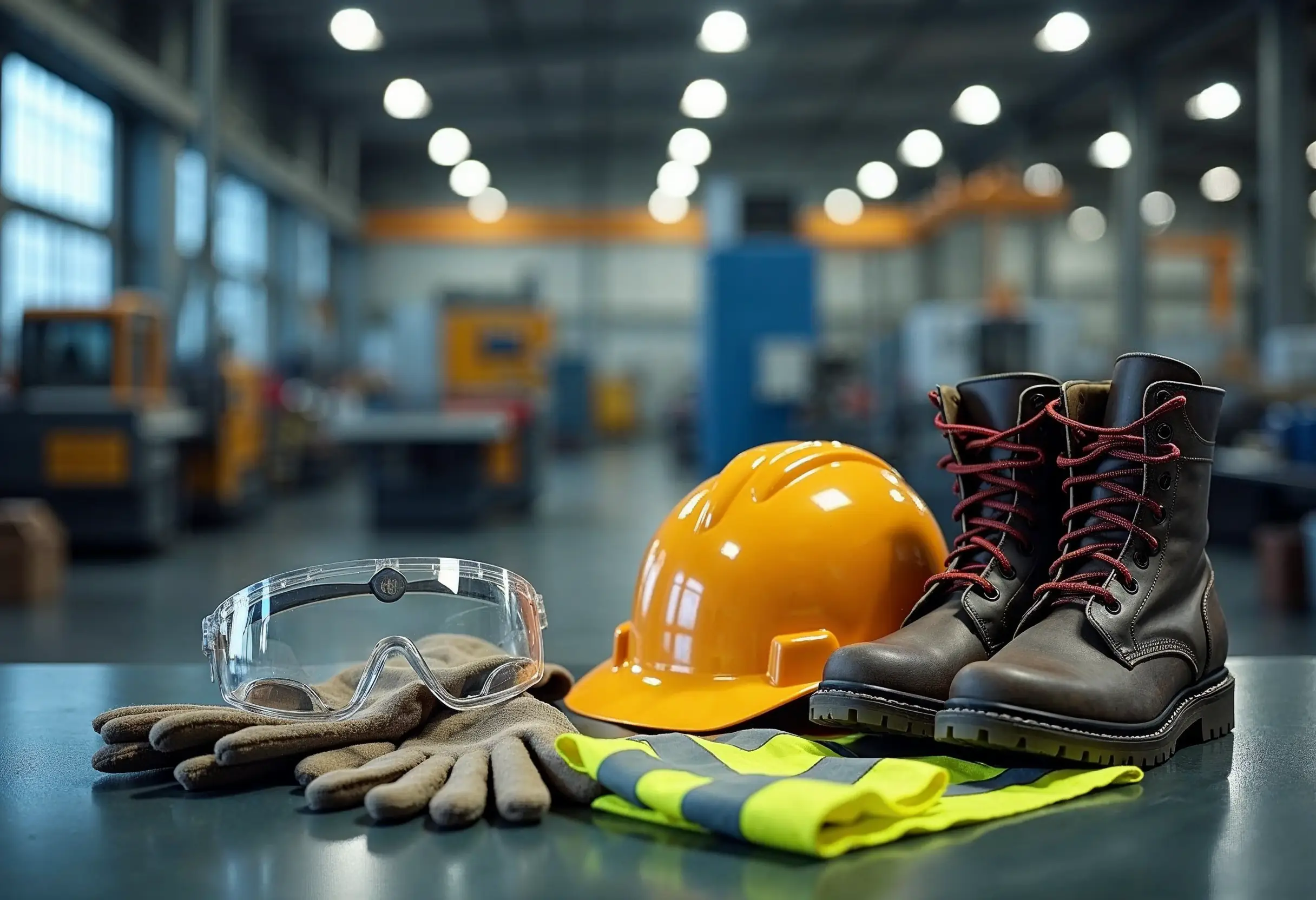
How to Apply Machine Safety Rules: From Selection to Installation
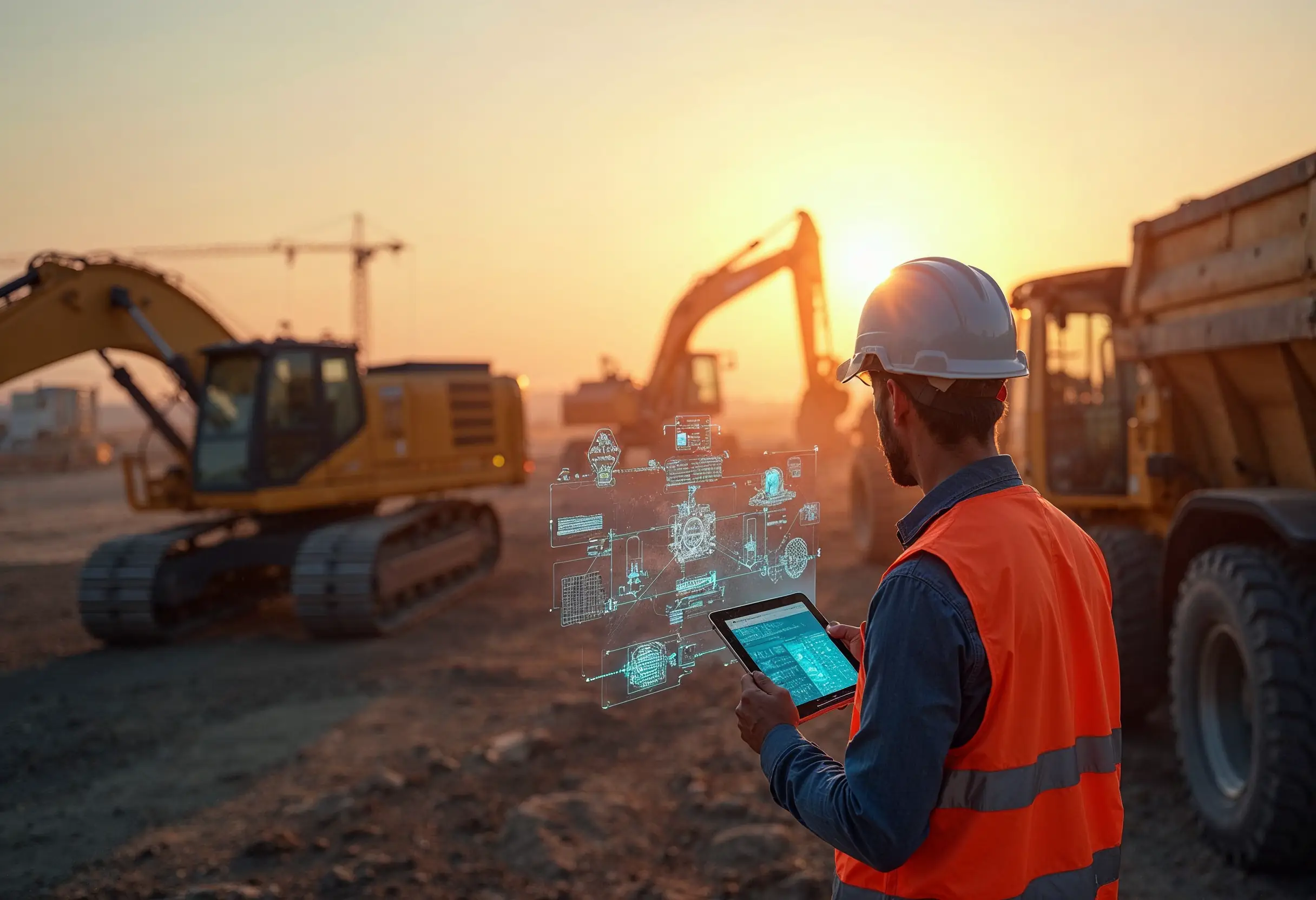
Smart Diagnostics Cut Heavy Equipment Failures by 73%
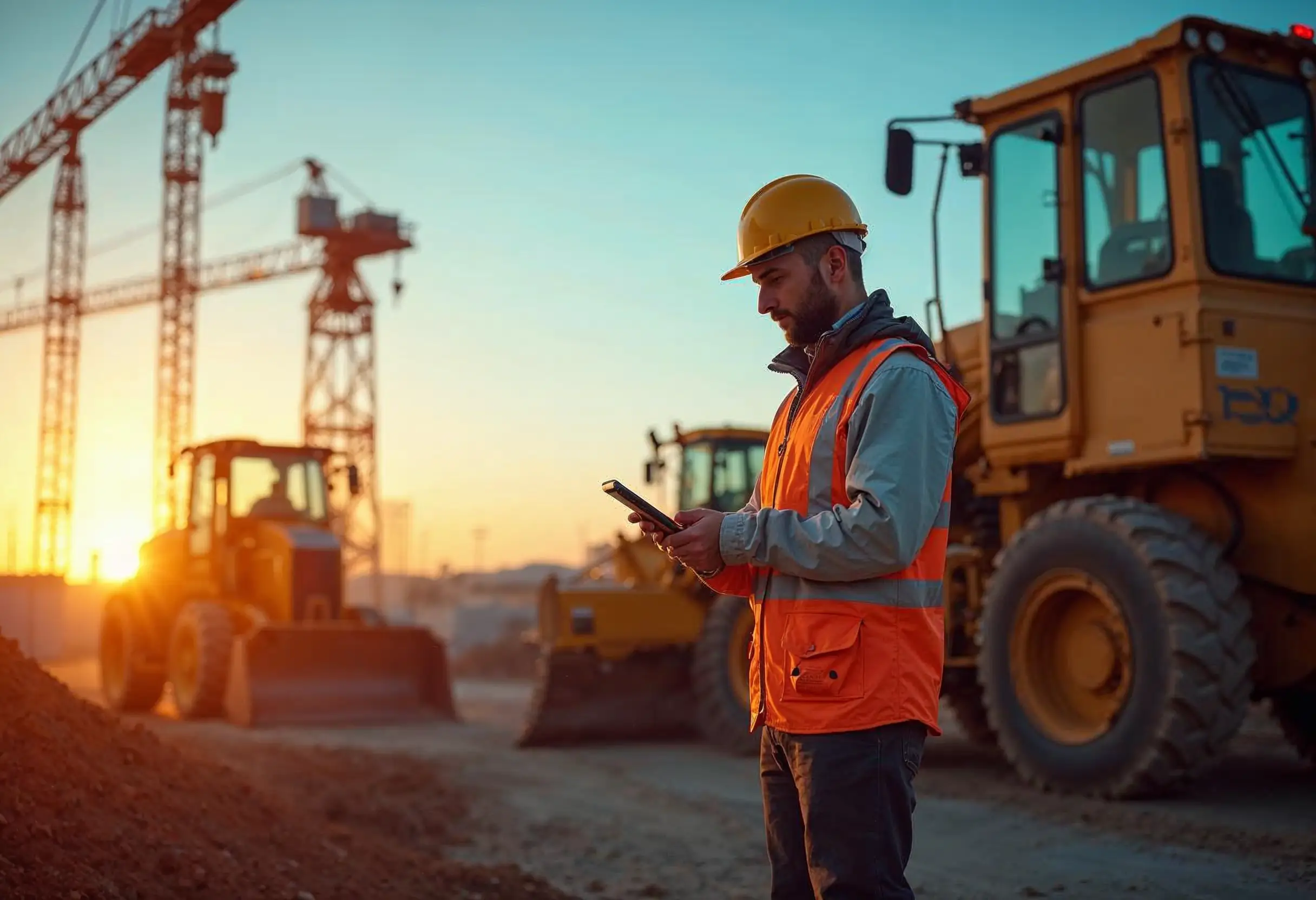
5 Ways to Assess the Environmental Impact of Heavy Construction Machinery
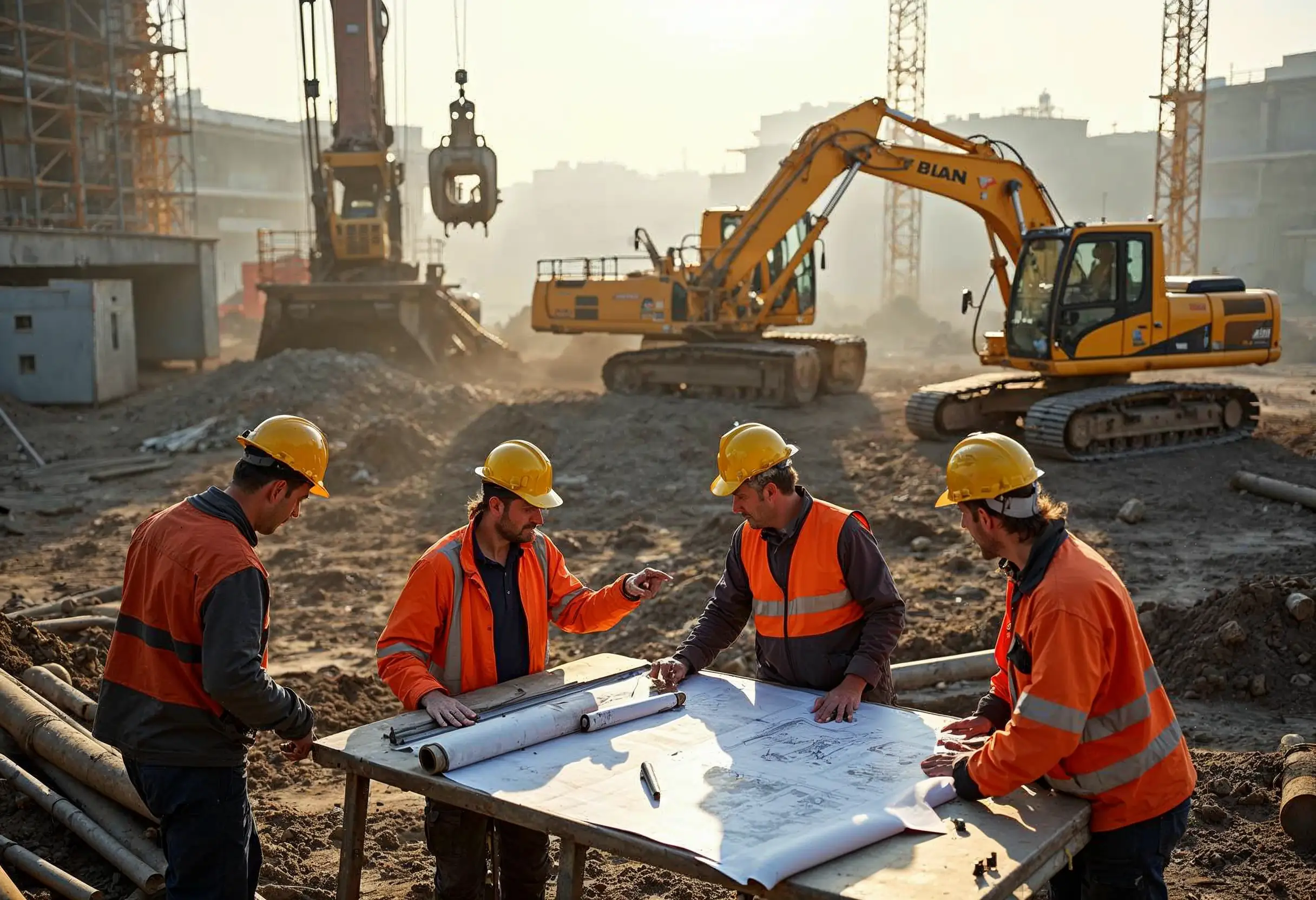
10 Smart Ways to Pick Construction Machinery for 2025 Projects
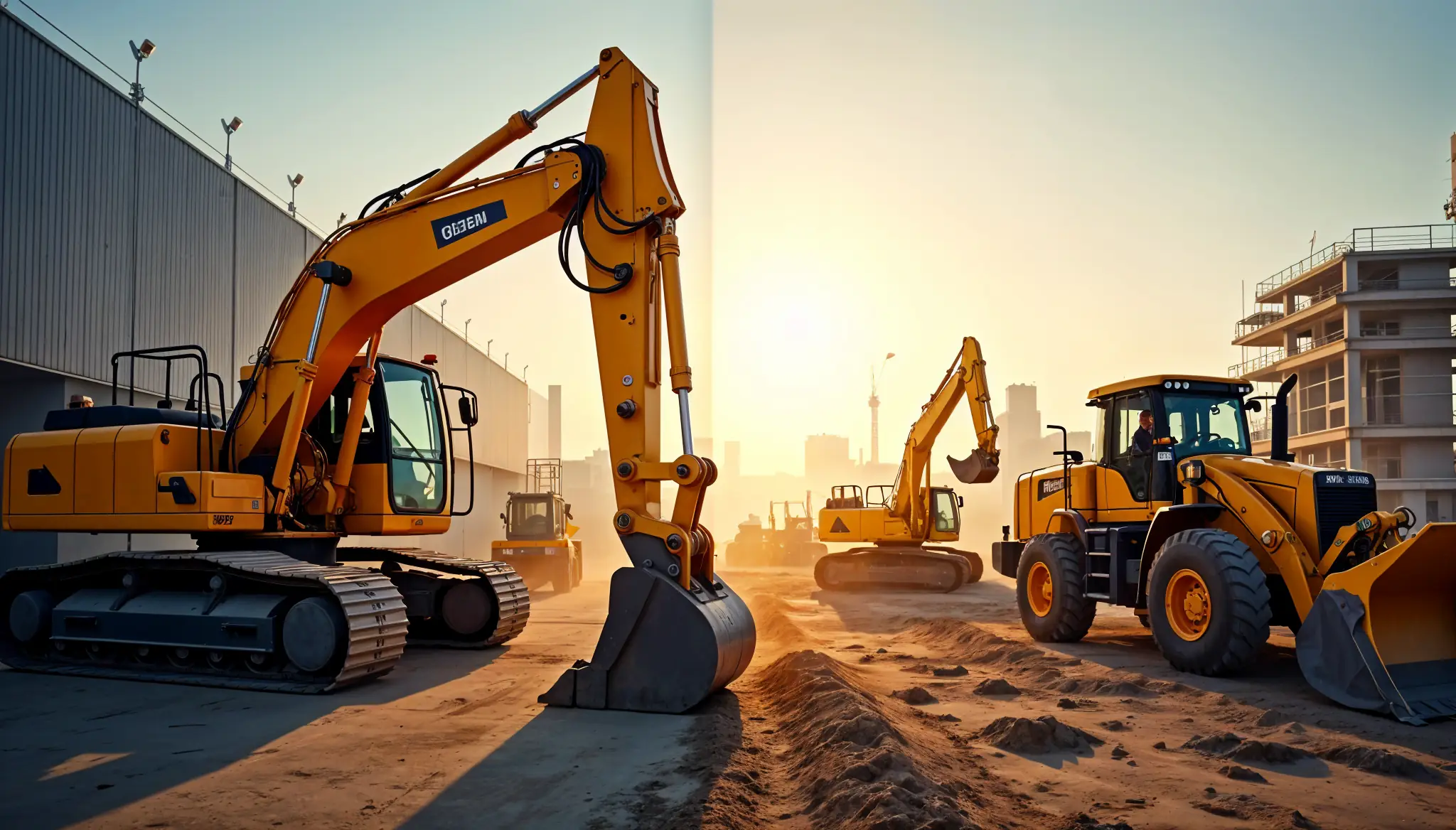
Rent vs Purchase Equipment: What Heavy Industry Experts Hide
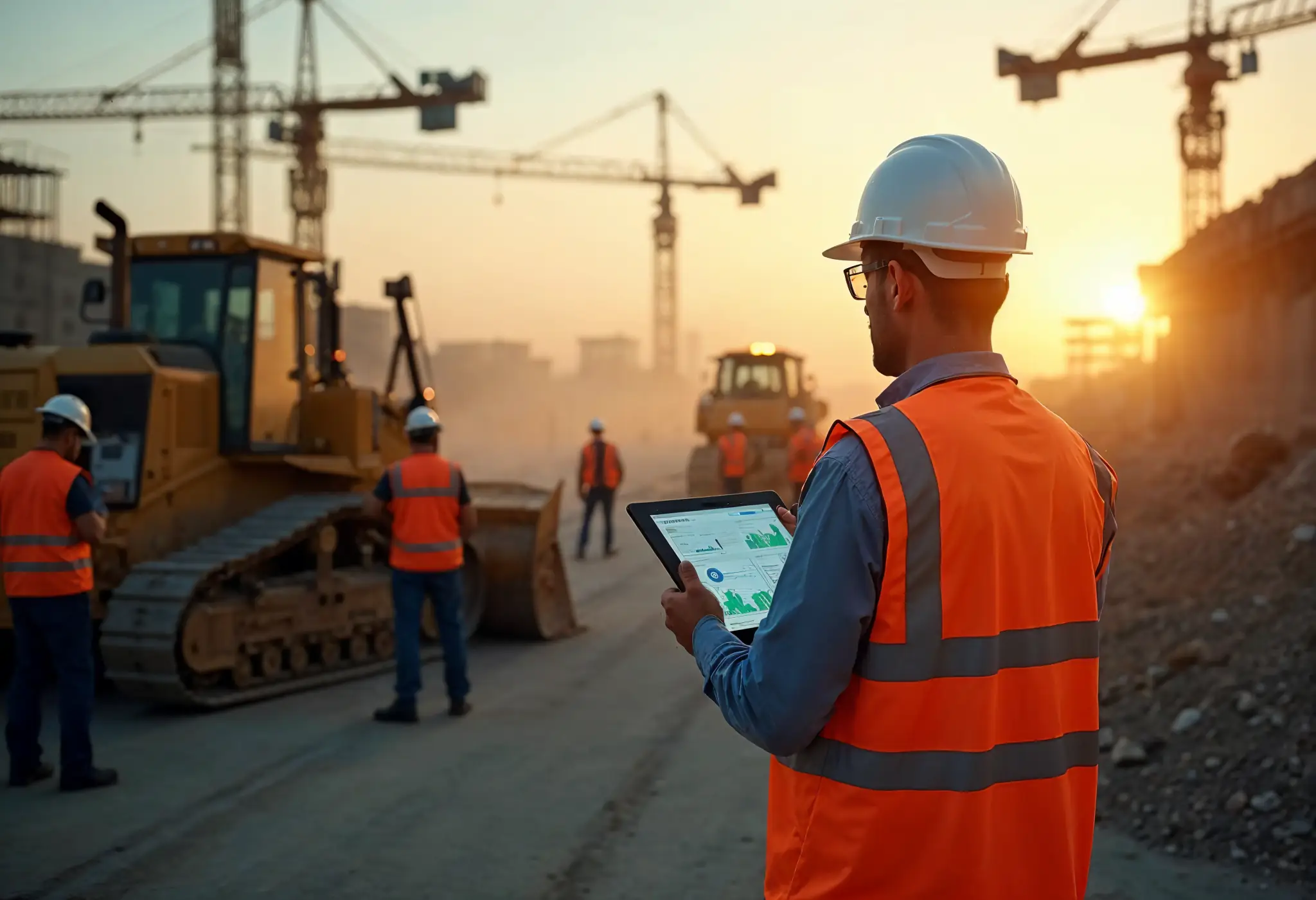
How to Implement a Construction Inventory Management System for Equipment Efficiency
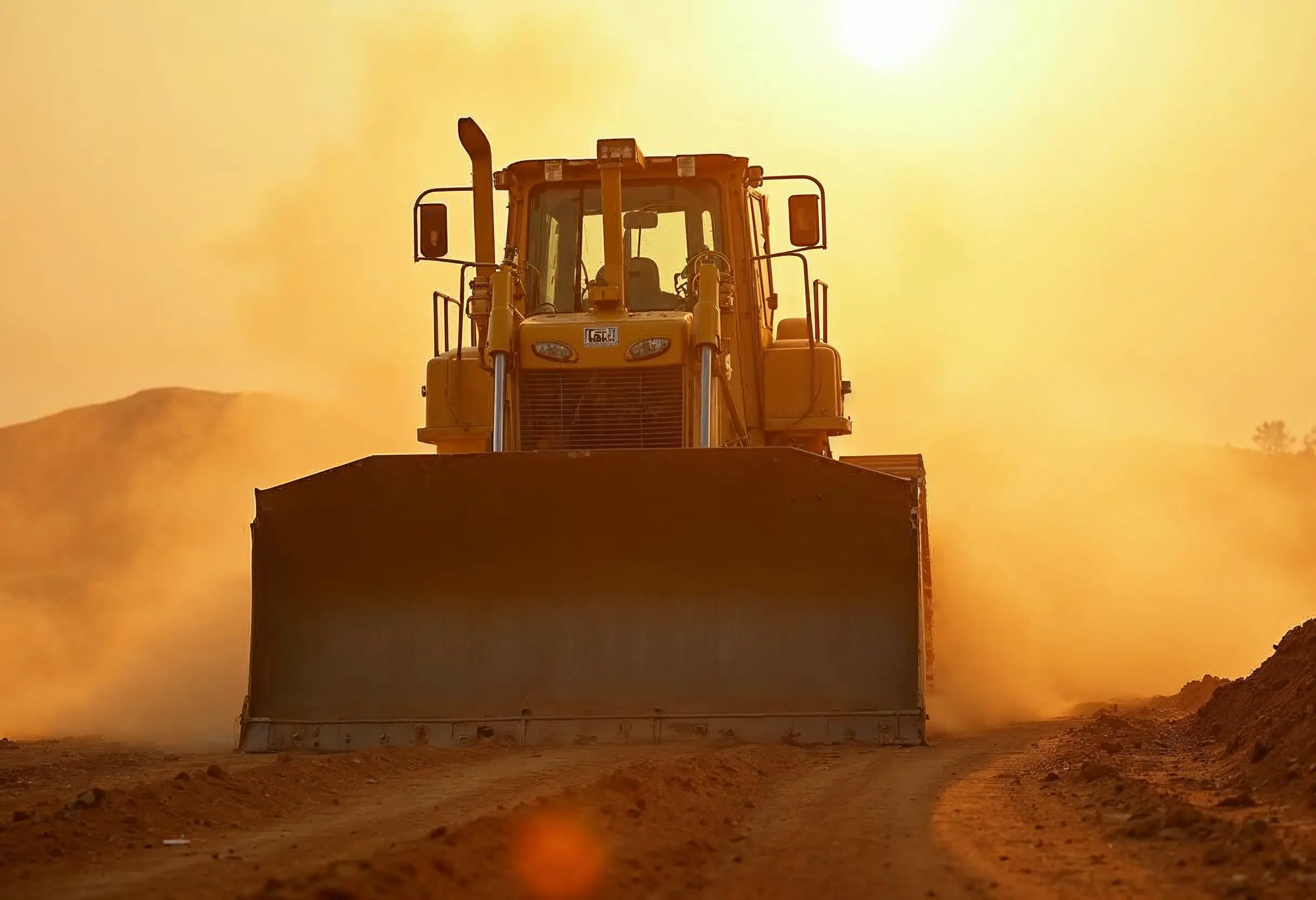
How to Extend Equipment Life Expectancy with Regular Maintenance
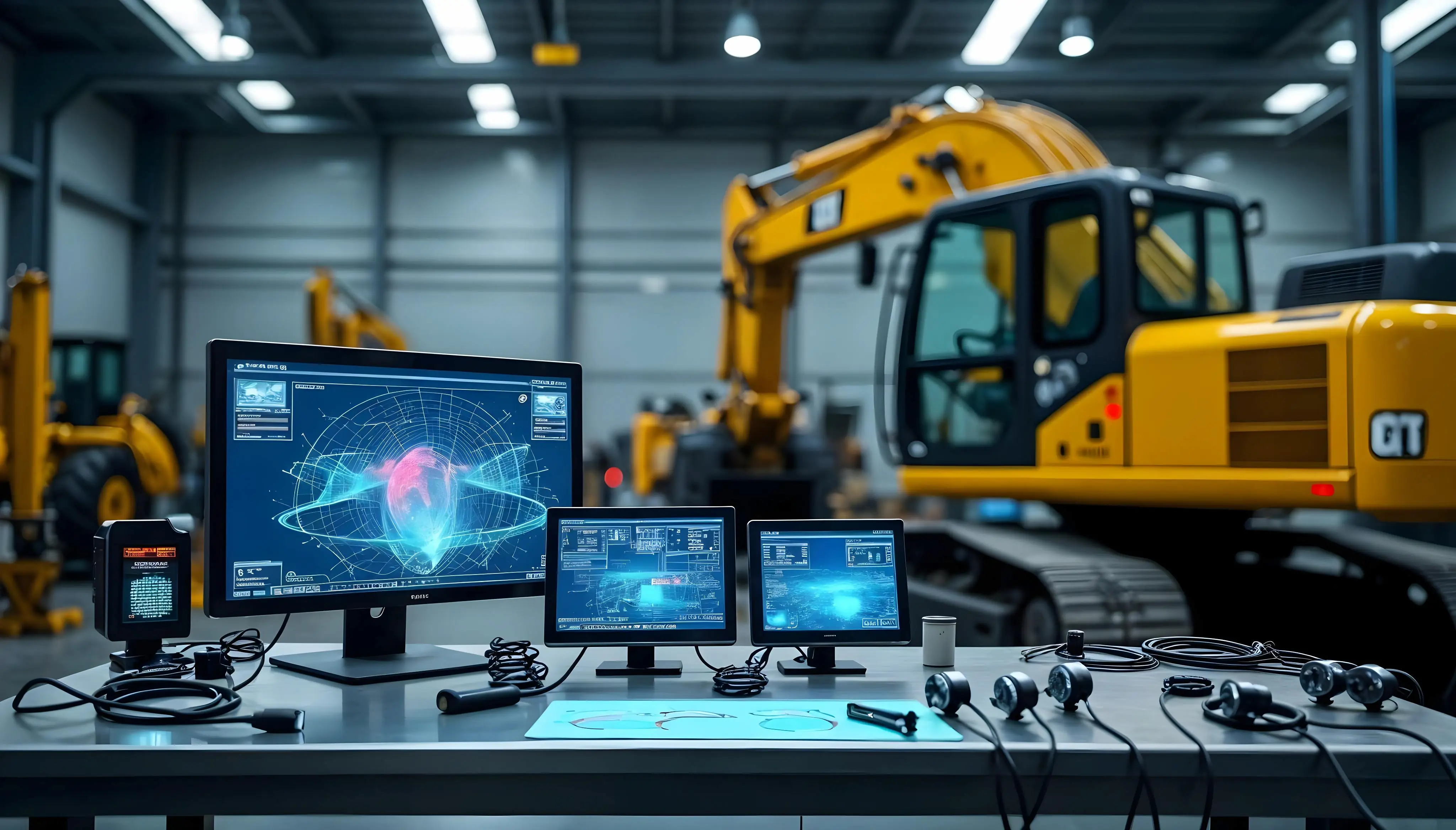
Advanced Heavy Equipment Diagnostic Tools: Ensuring Construction Machinery Quality
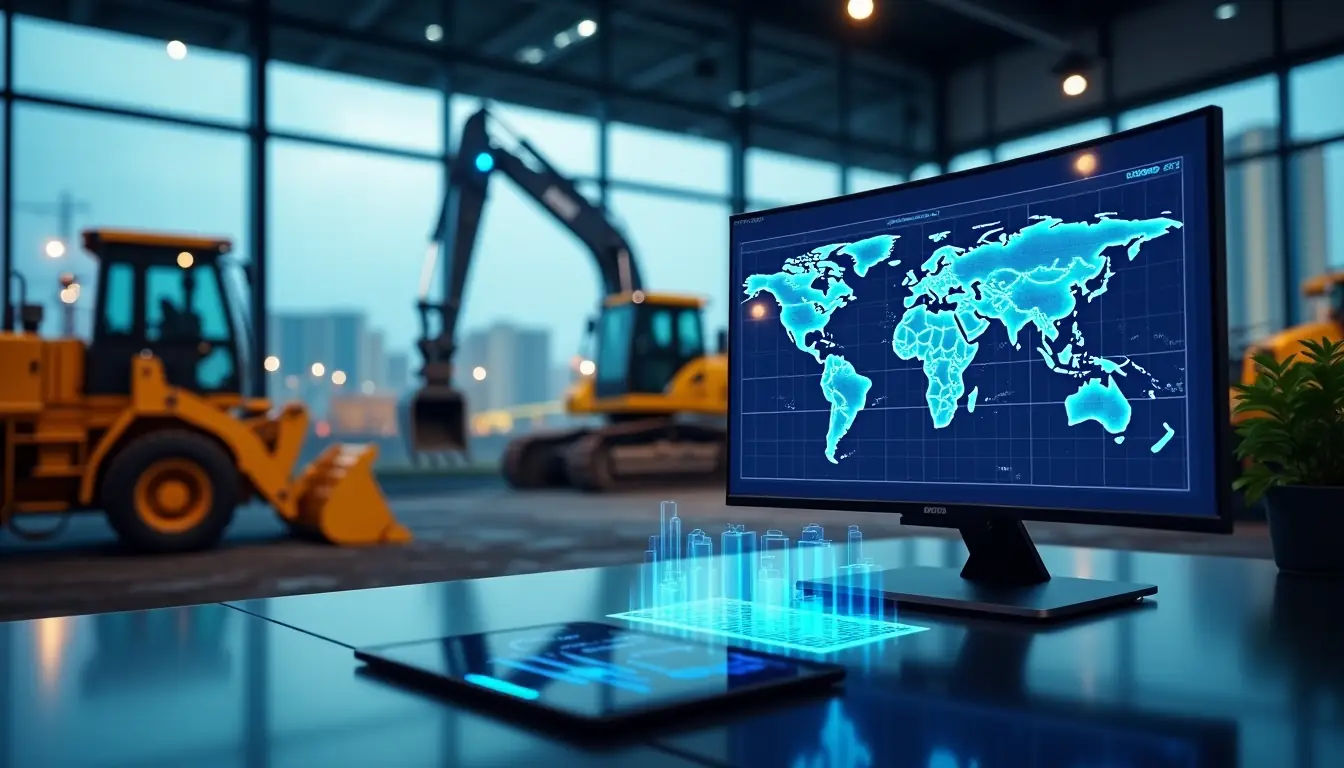
Essential Features Your Construction Equipment Inventory System Needs
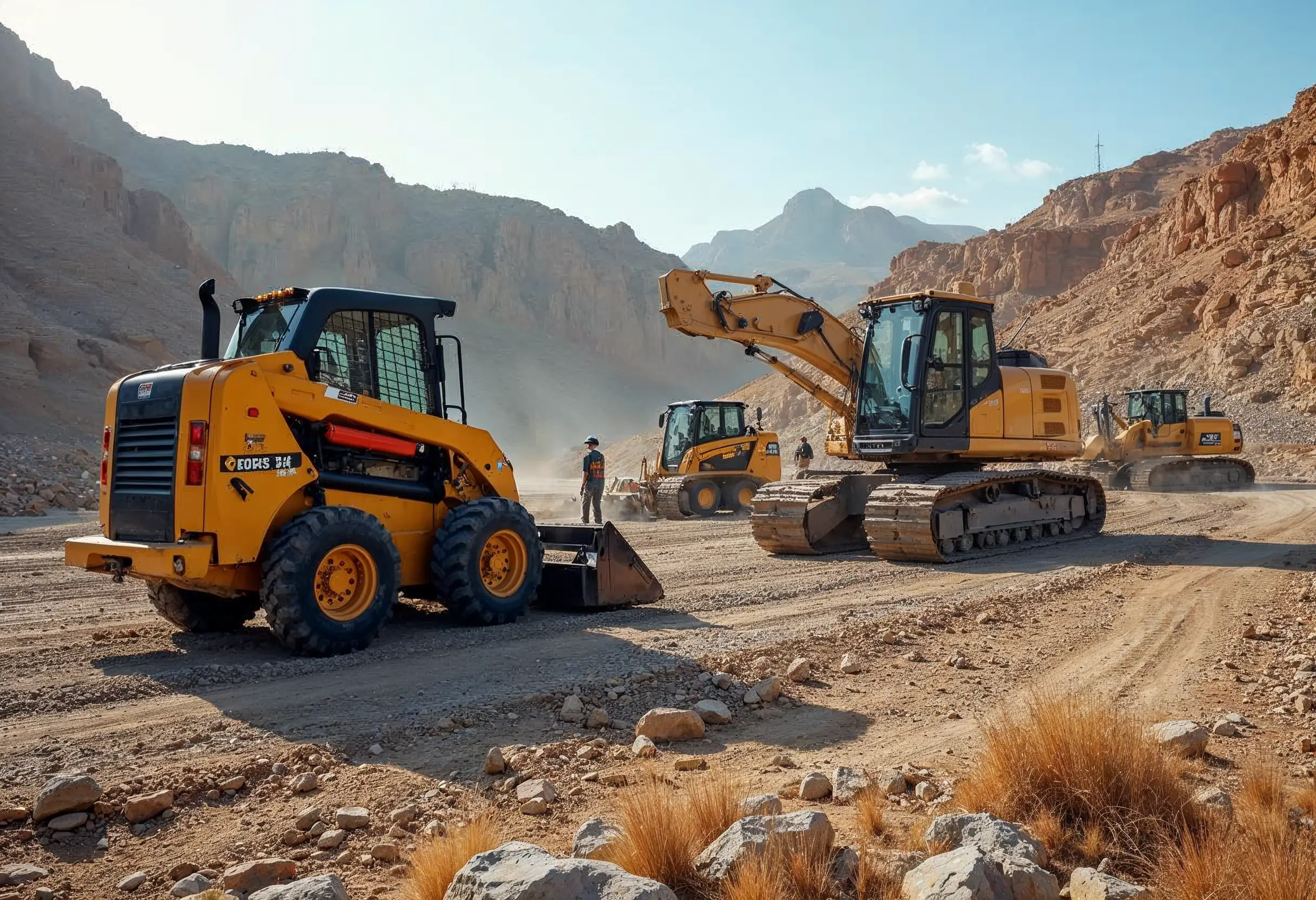
29 Quick Tips for Choosing Construction Equipment for Remote Locations
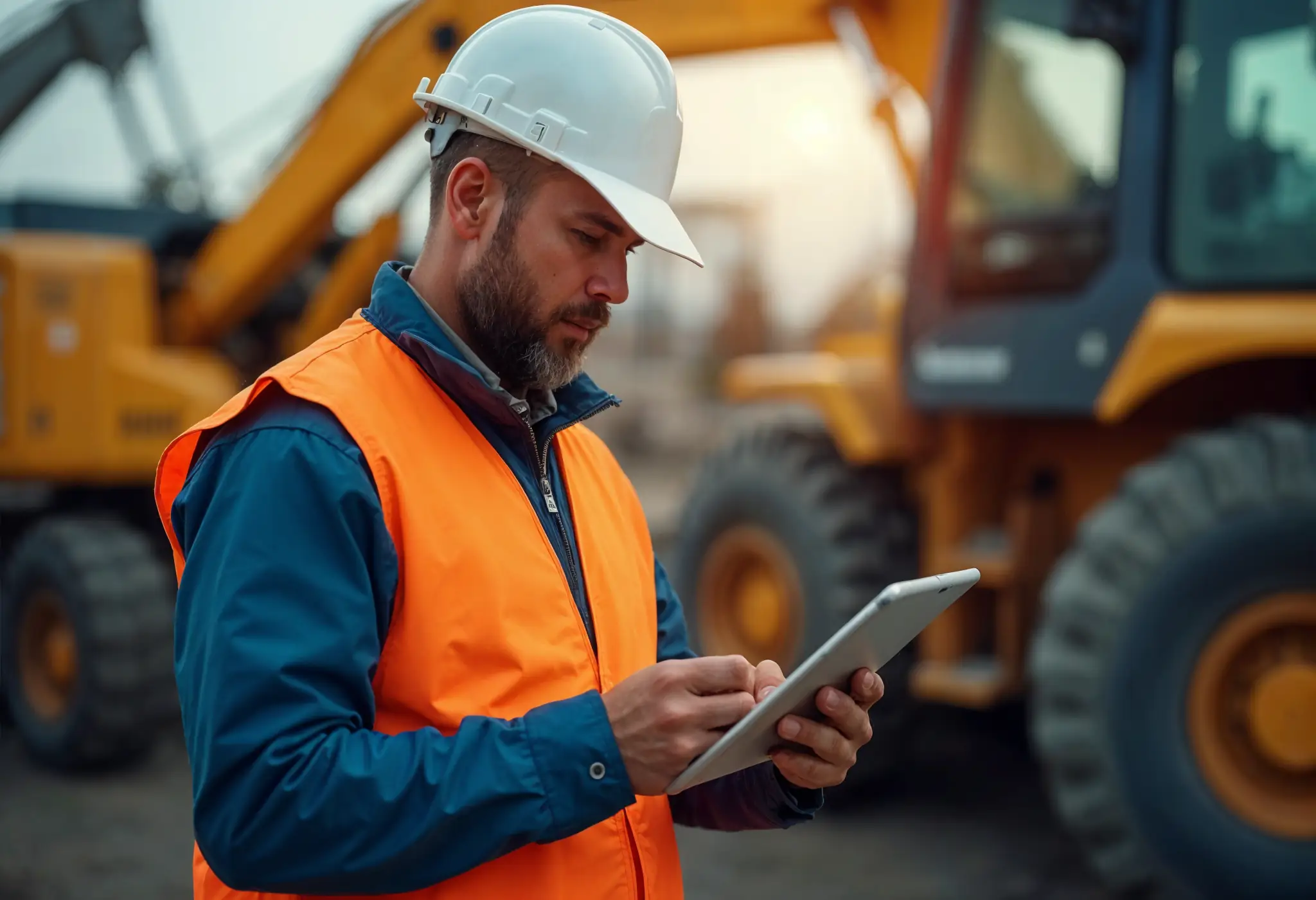
How to Select Construction Machinery with Optimal Equipment Maintenance in Mind
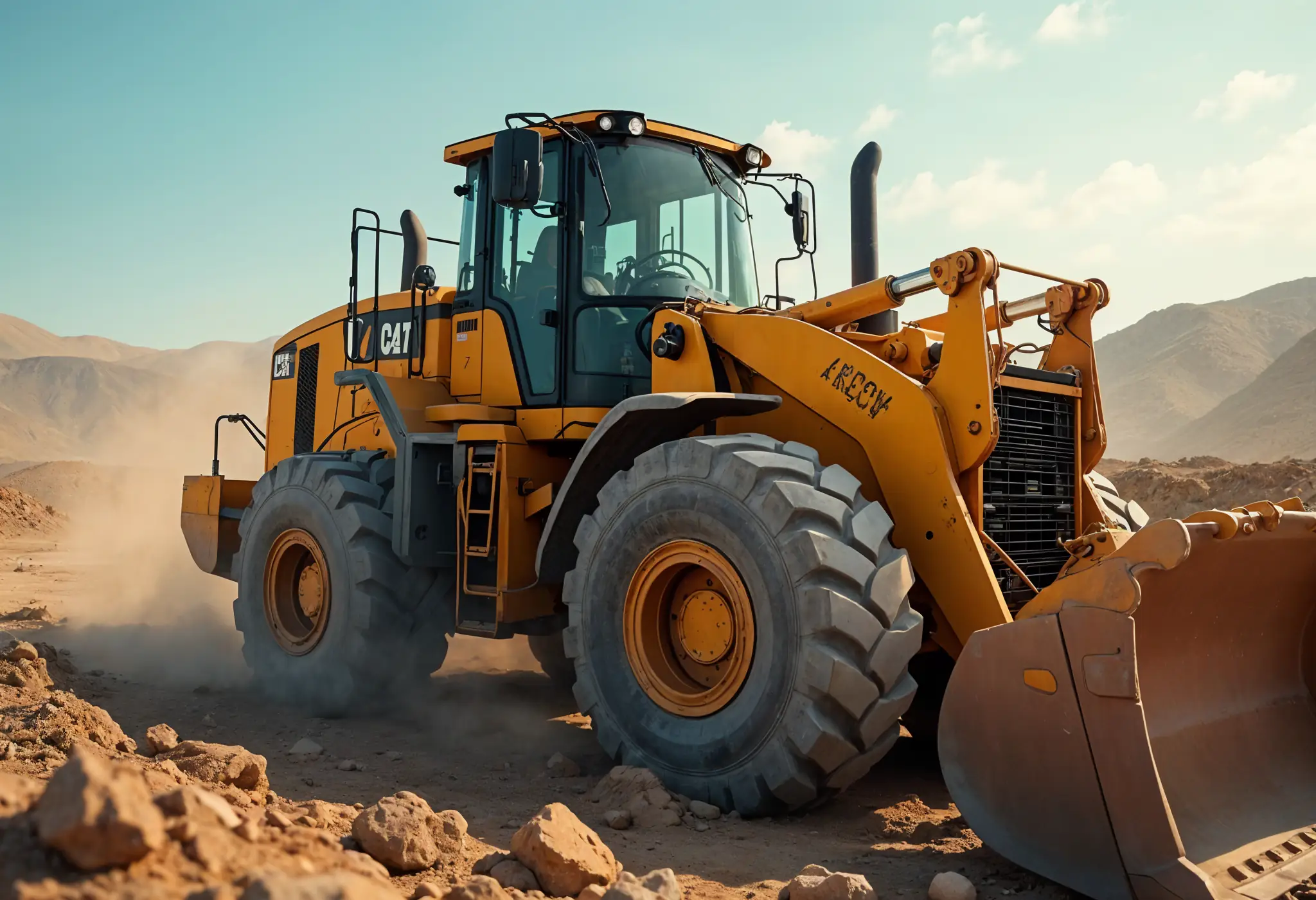
Top 25 Tips for Selecting Bulldozers for Construction Sites
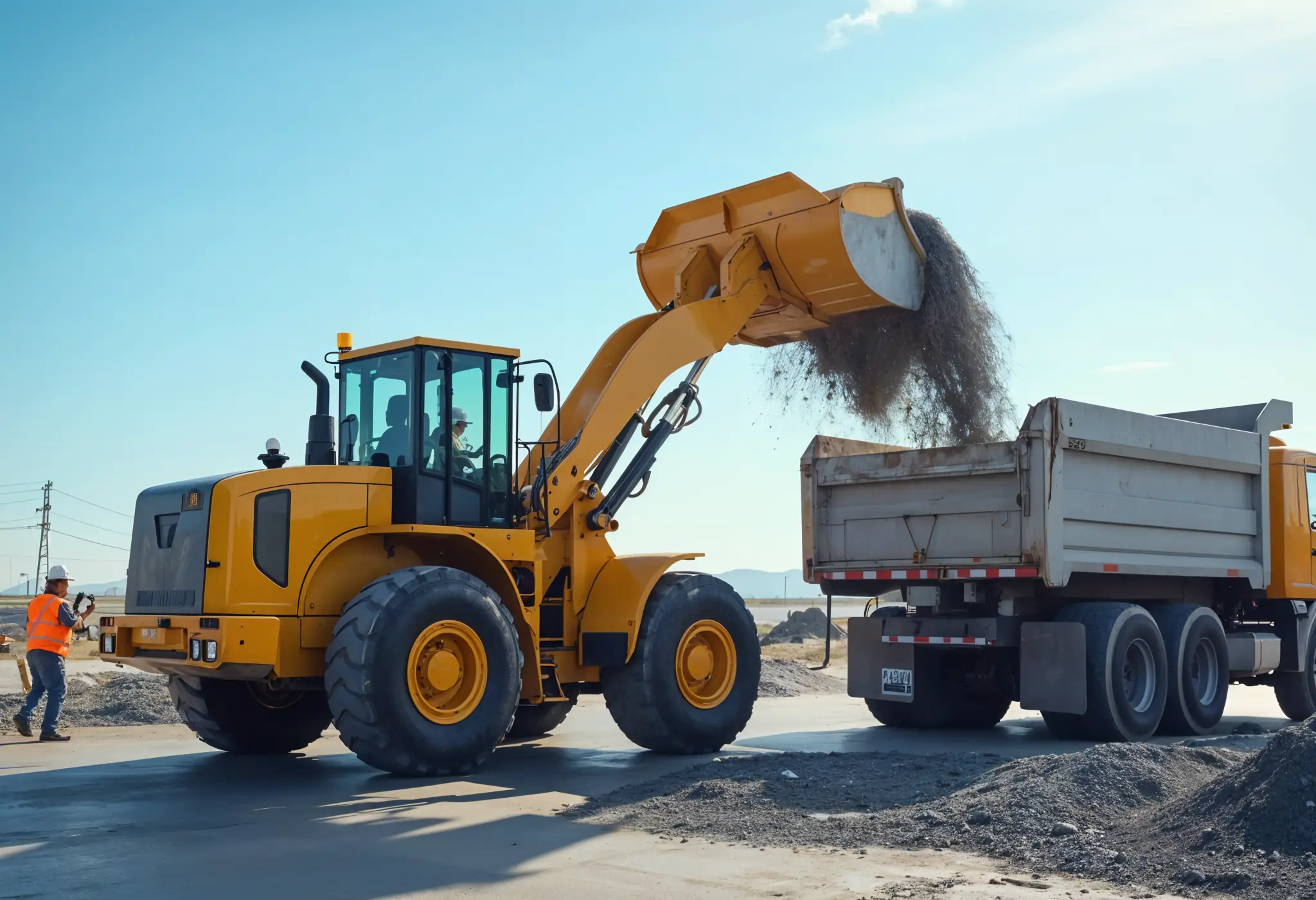
Which Construction Loader is Best for Your Project Needs?
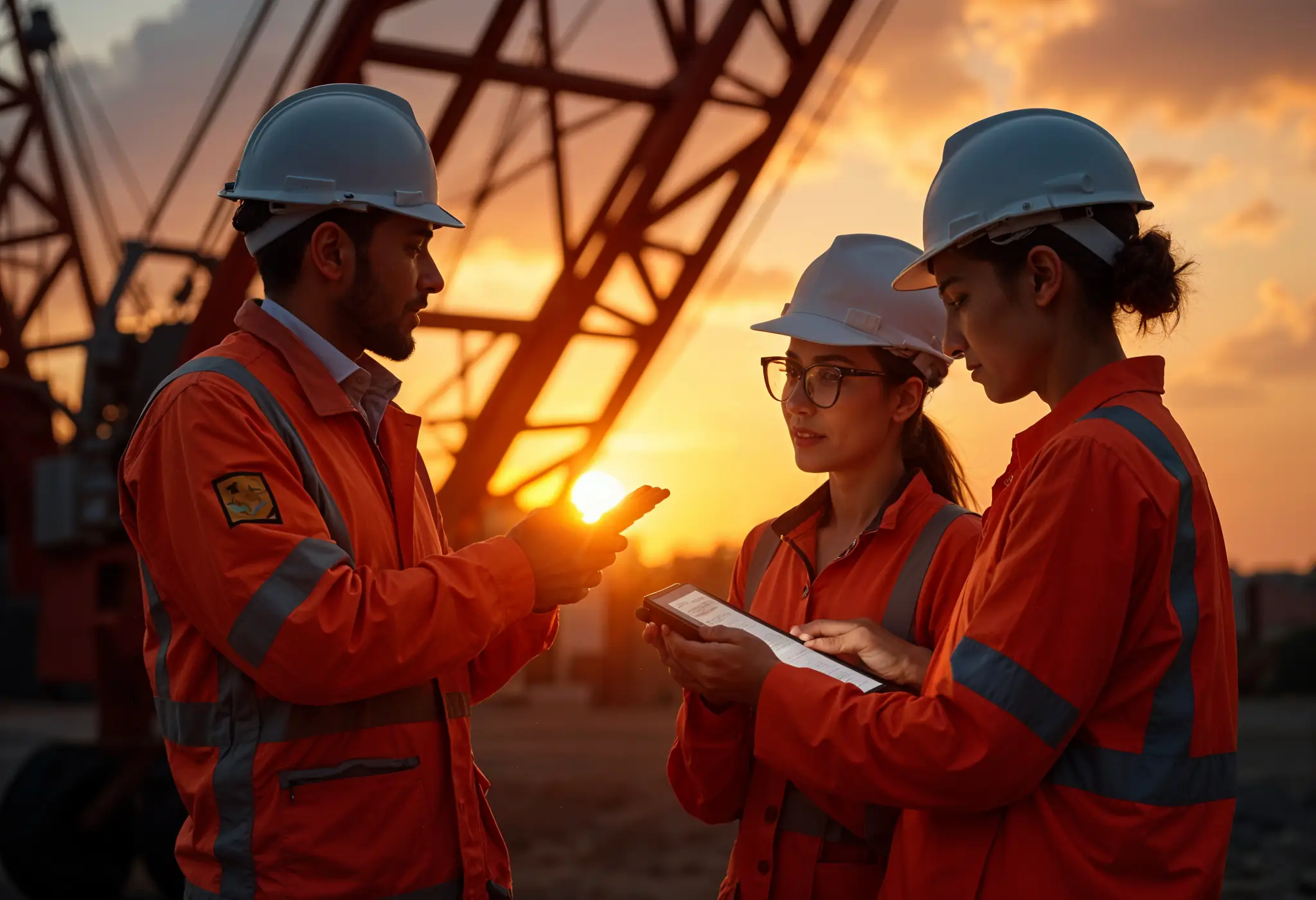
4 Key Steps to Form a Construction Machinery QC Team
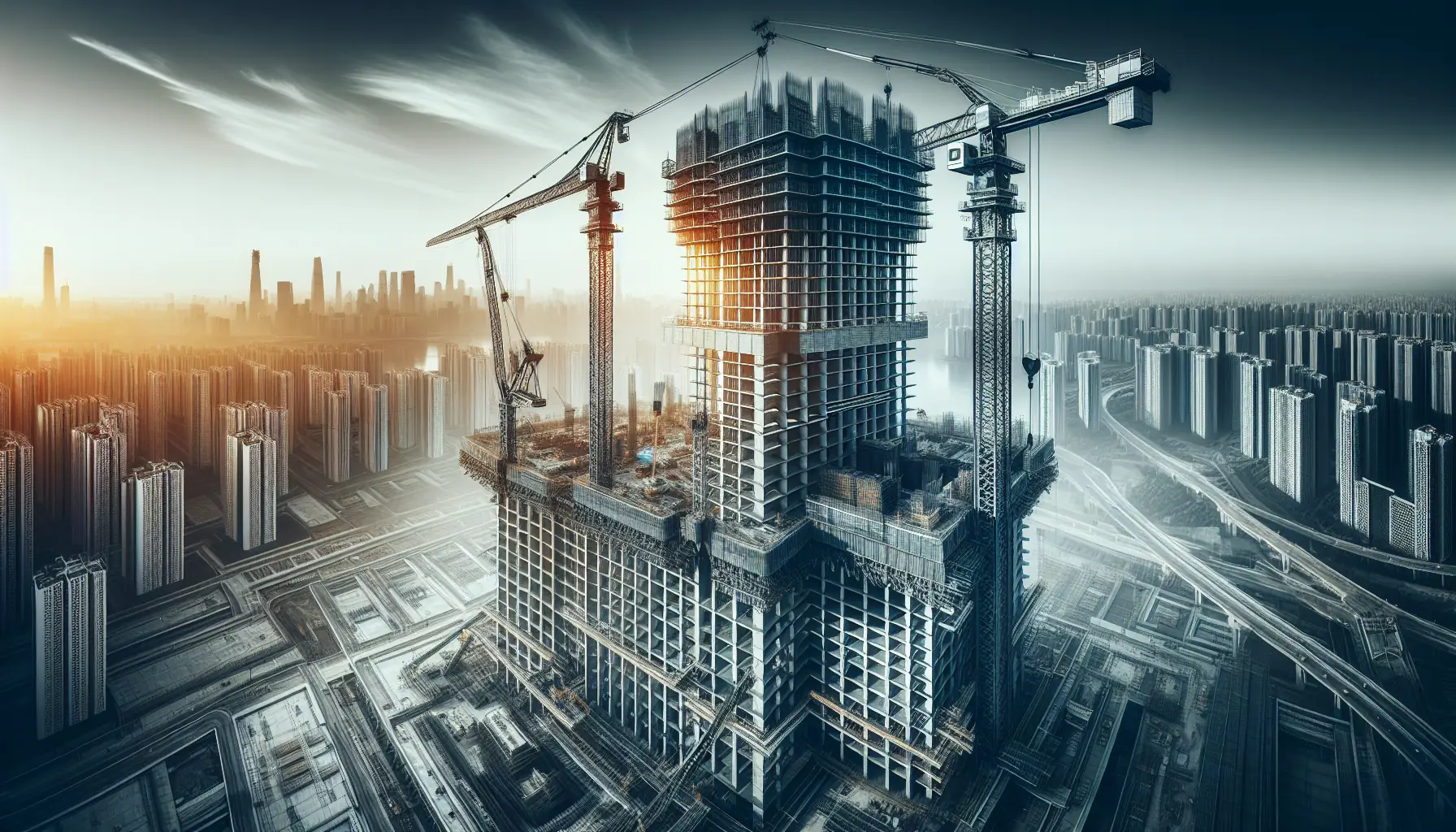
15 Essential Tips for Selecting the Perfect Crane for Construction
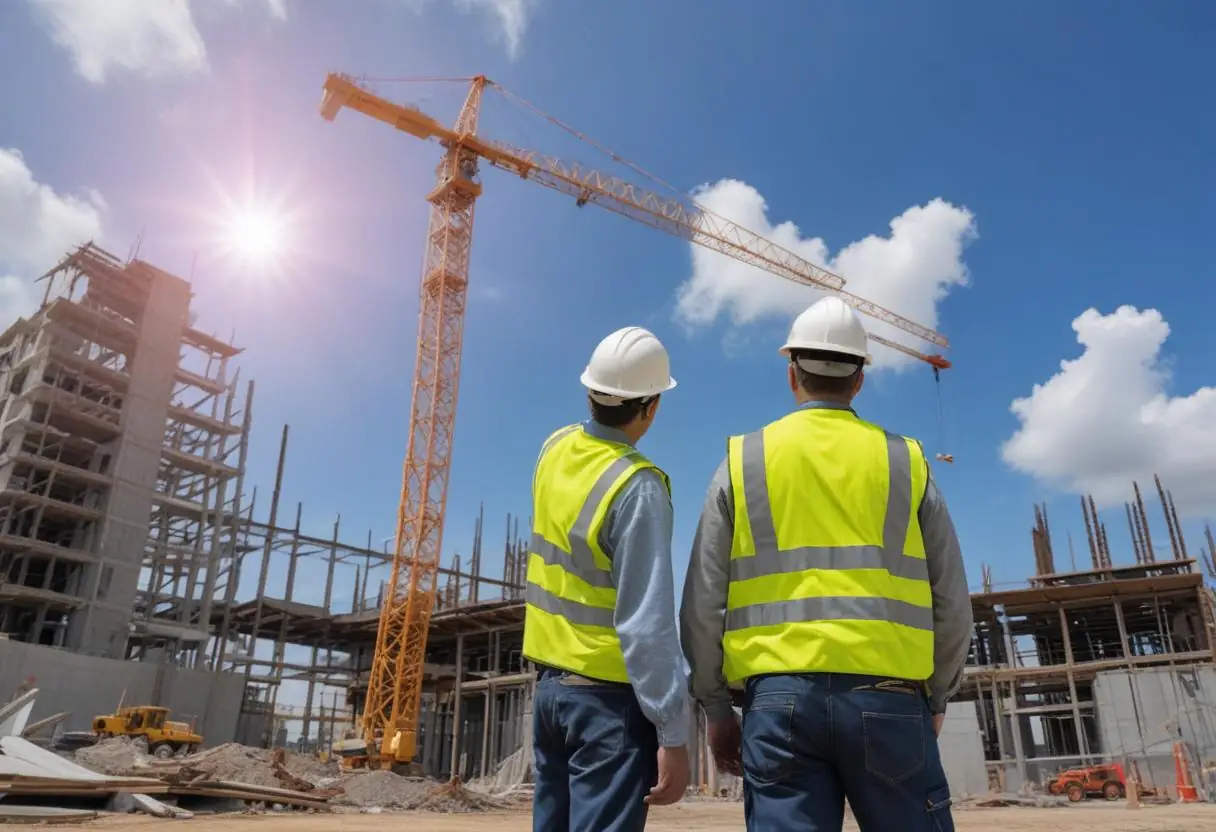
Maximize Savings: Multi-Purpose Construction Machinery for Lower Costs
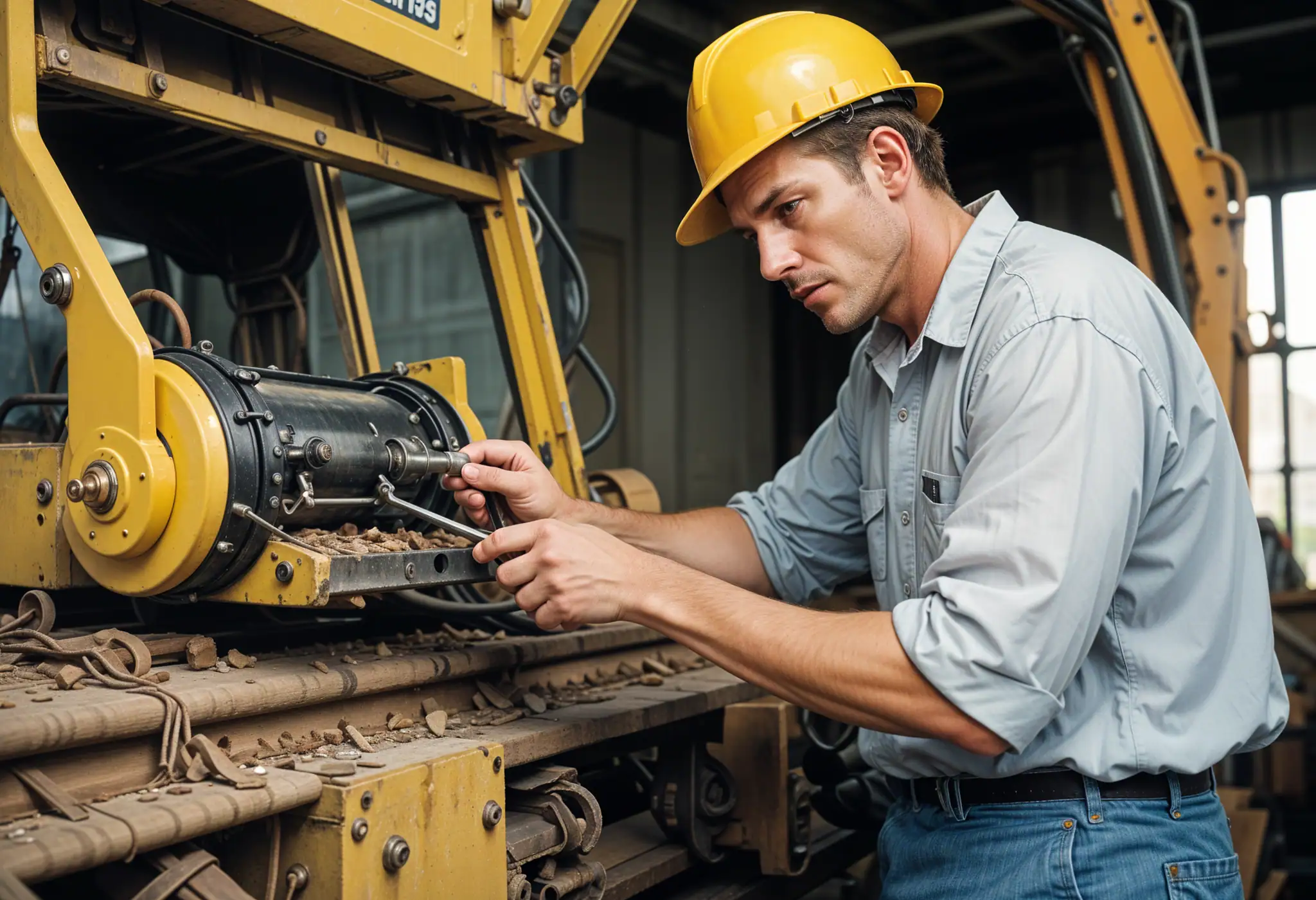
Affordable Heavy Equipment Parts: A Sourcing Guide
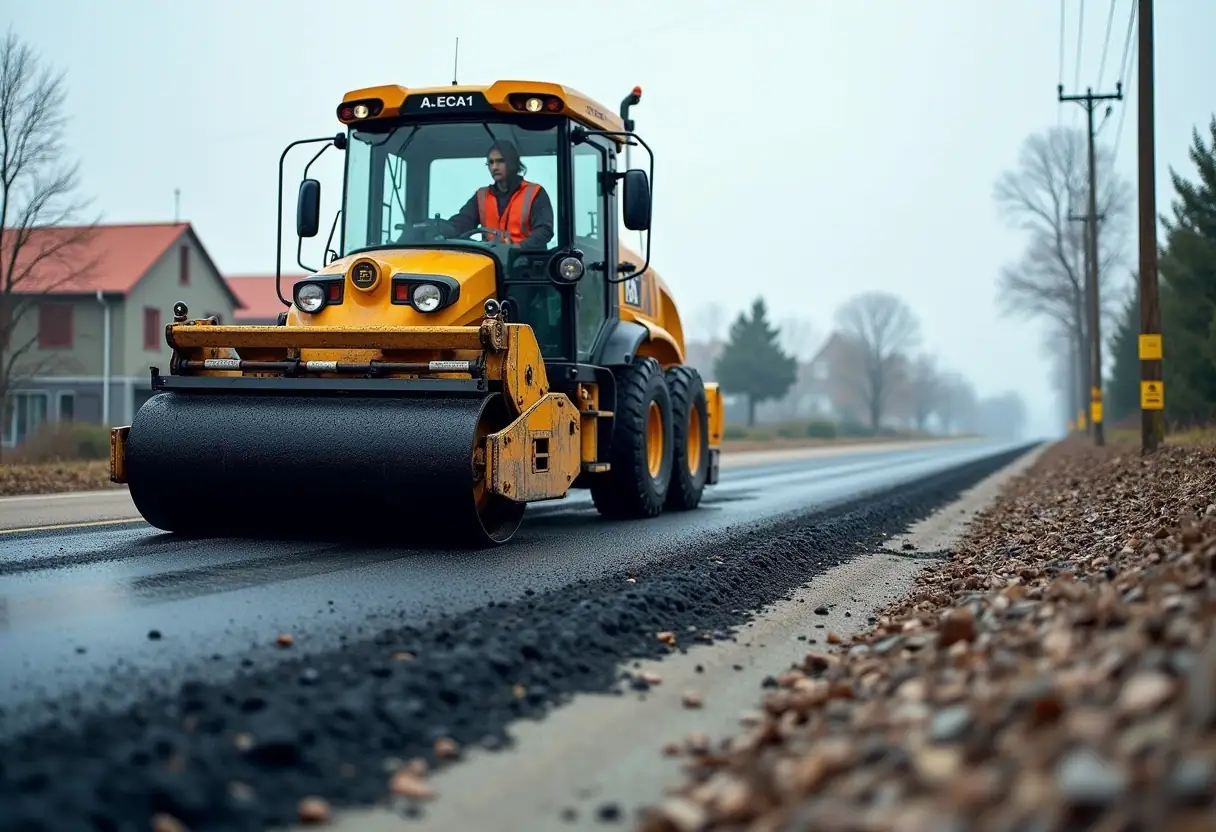
Choosing the Right Road Construction Equipment: A Complete Guide
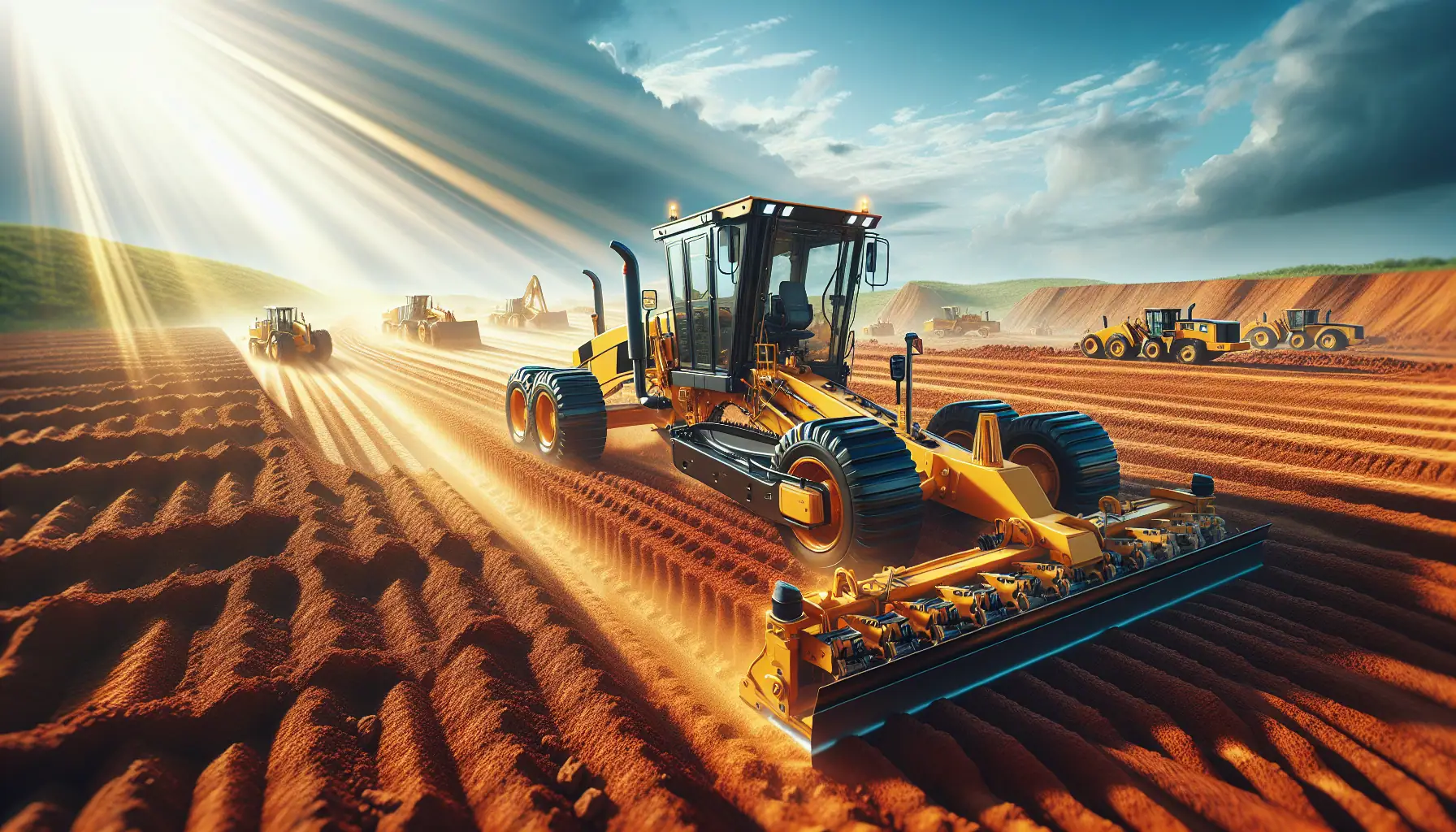
Motor Graders: Key Elements to Consider for Optimal Selection
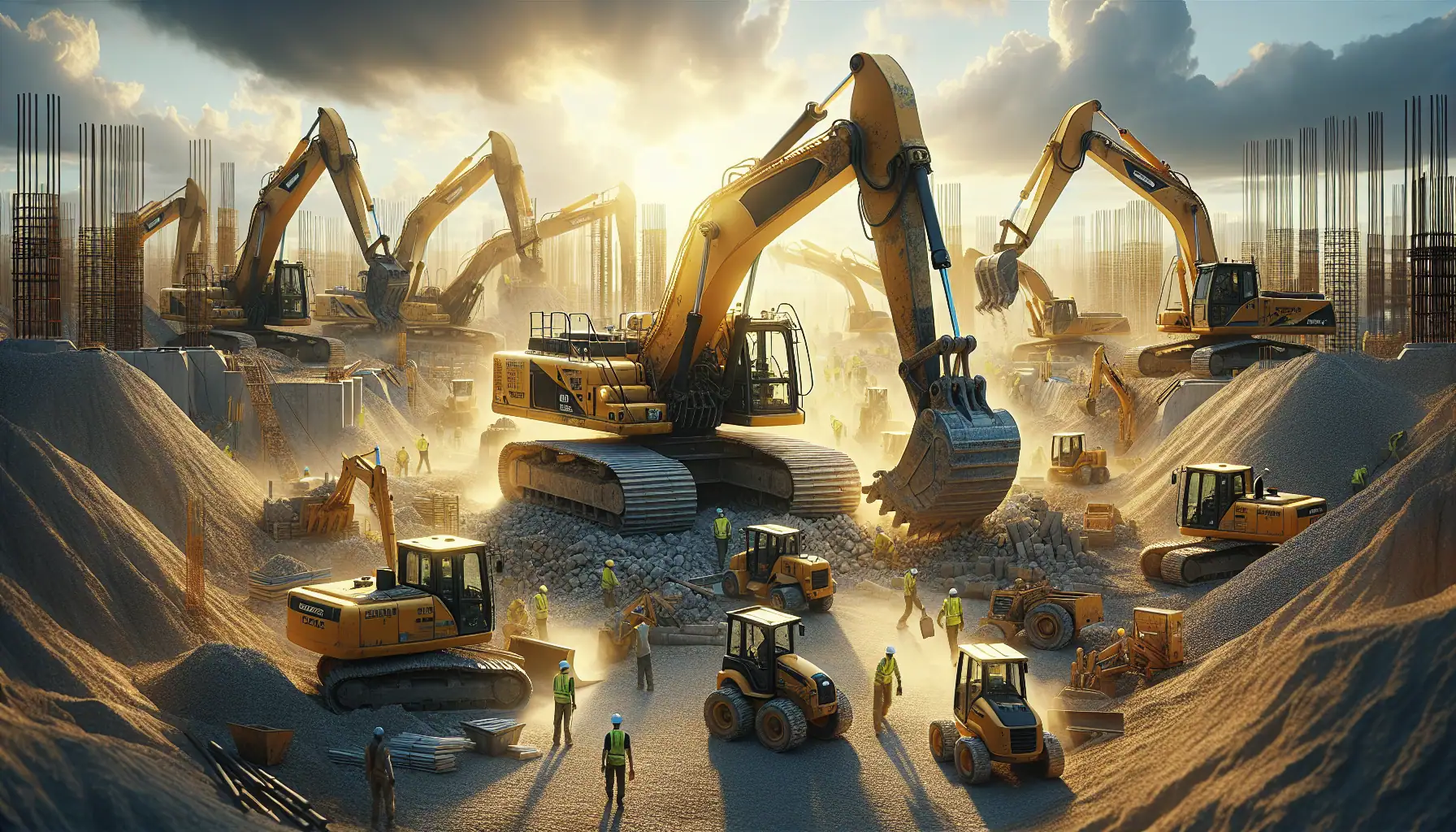
A Detailed Guide to Choosing Excavators for Construction Work
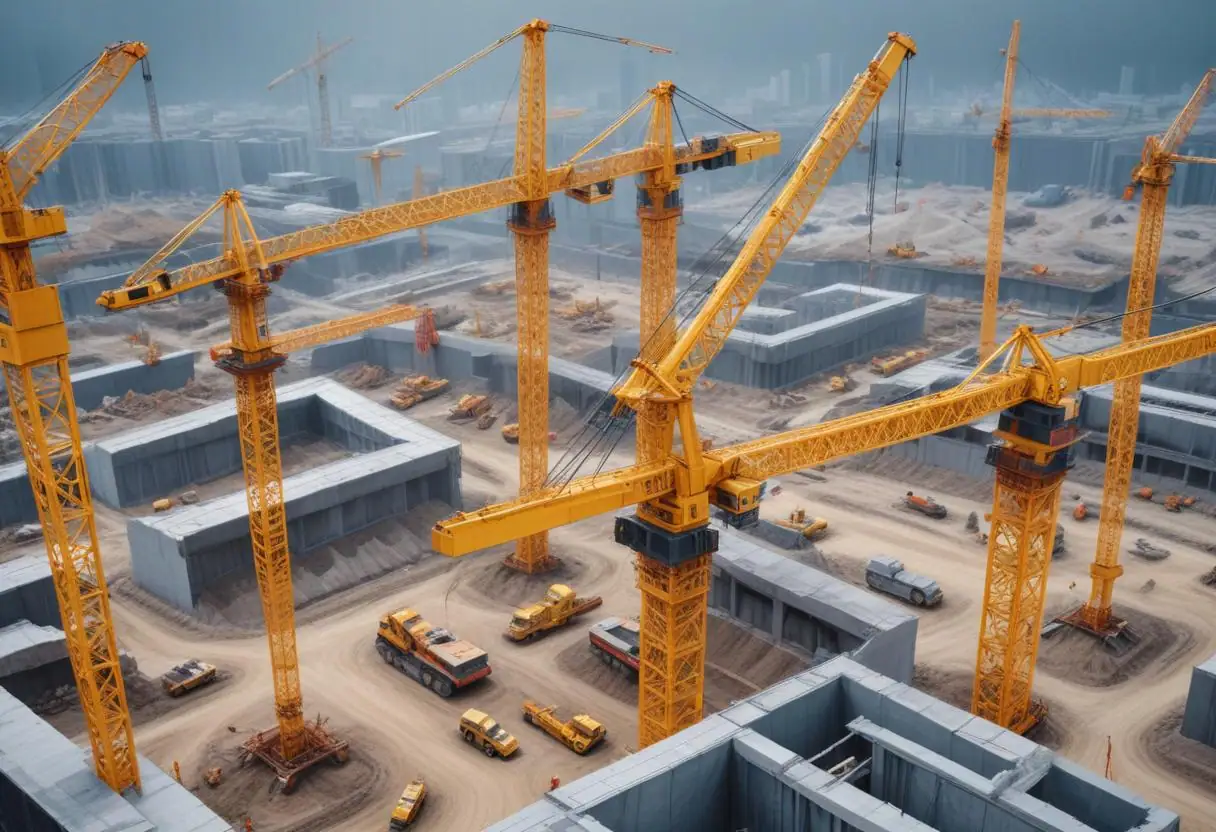
Top Tips for Choosing Cranes for Construction Projects
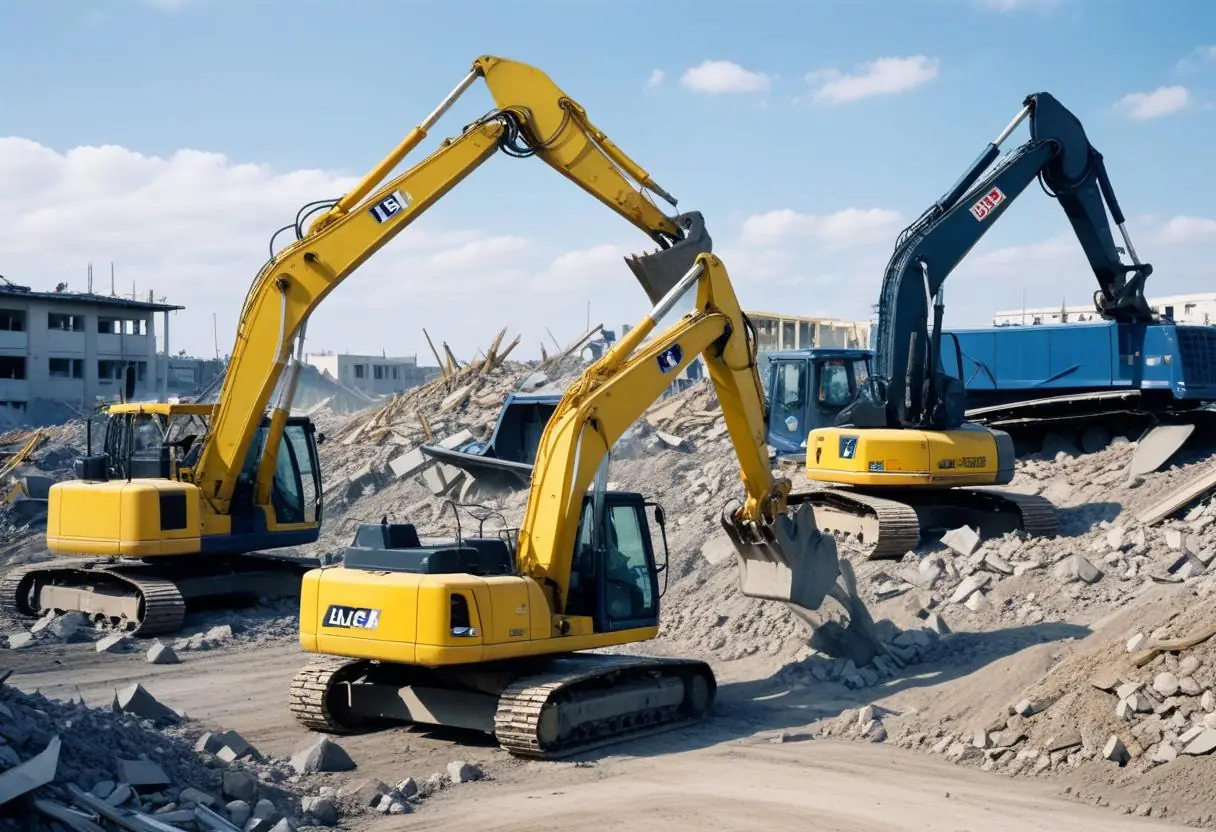
5 Top-Rated Demolition Machines for Construction Professionals
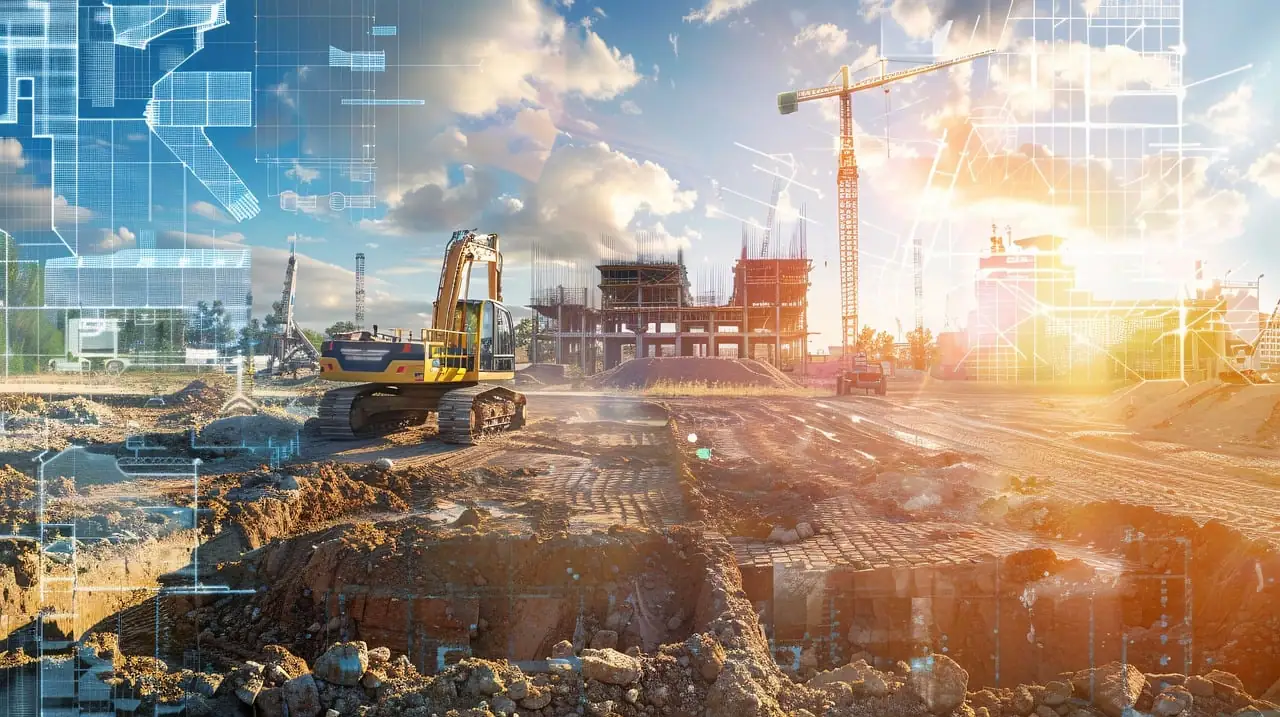
Expert Tips on Choosing Earthmoving Equipment for Large Projects
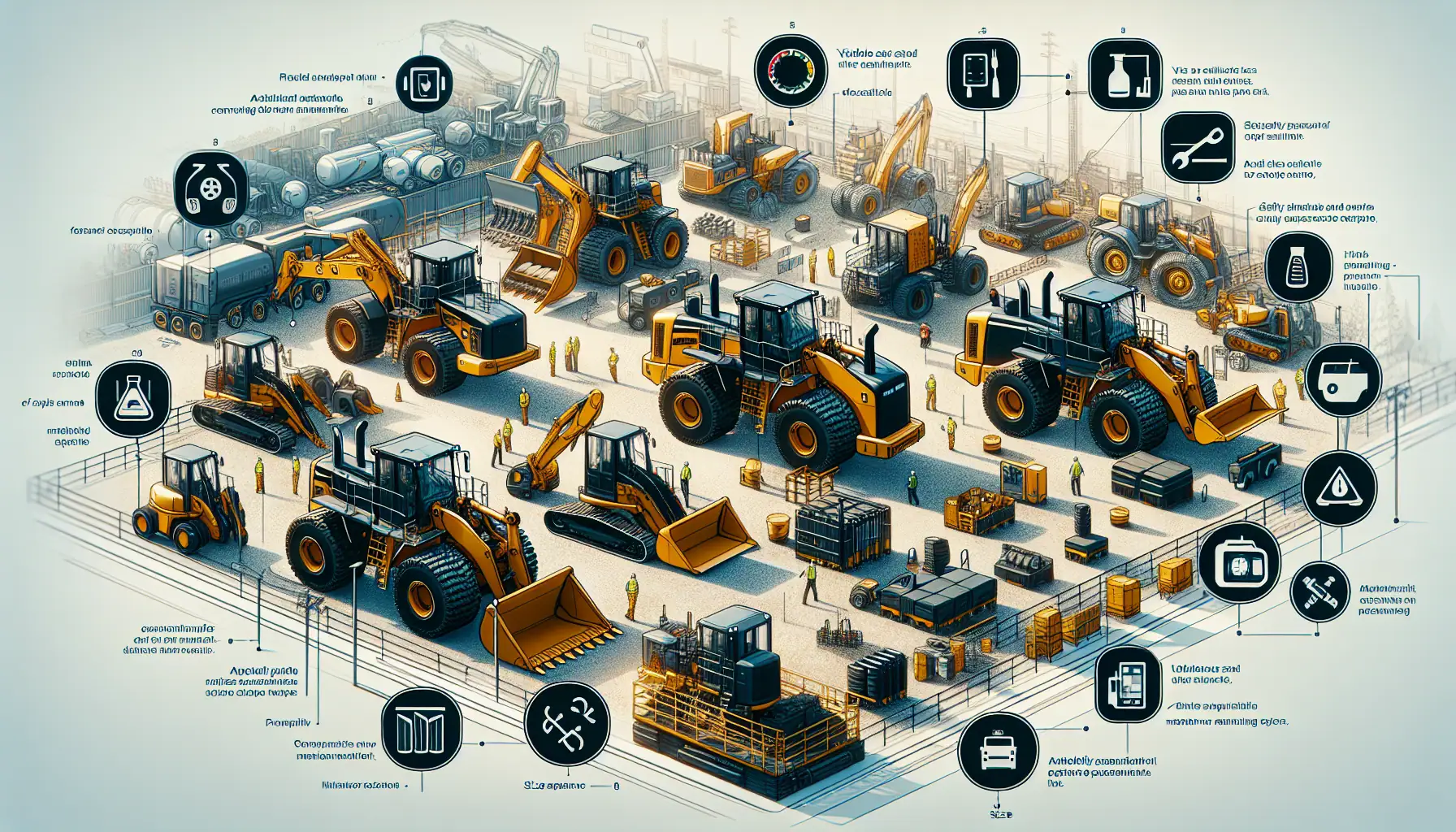
Top Functional Criteria for Selecting Heavy Construction Equipment
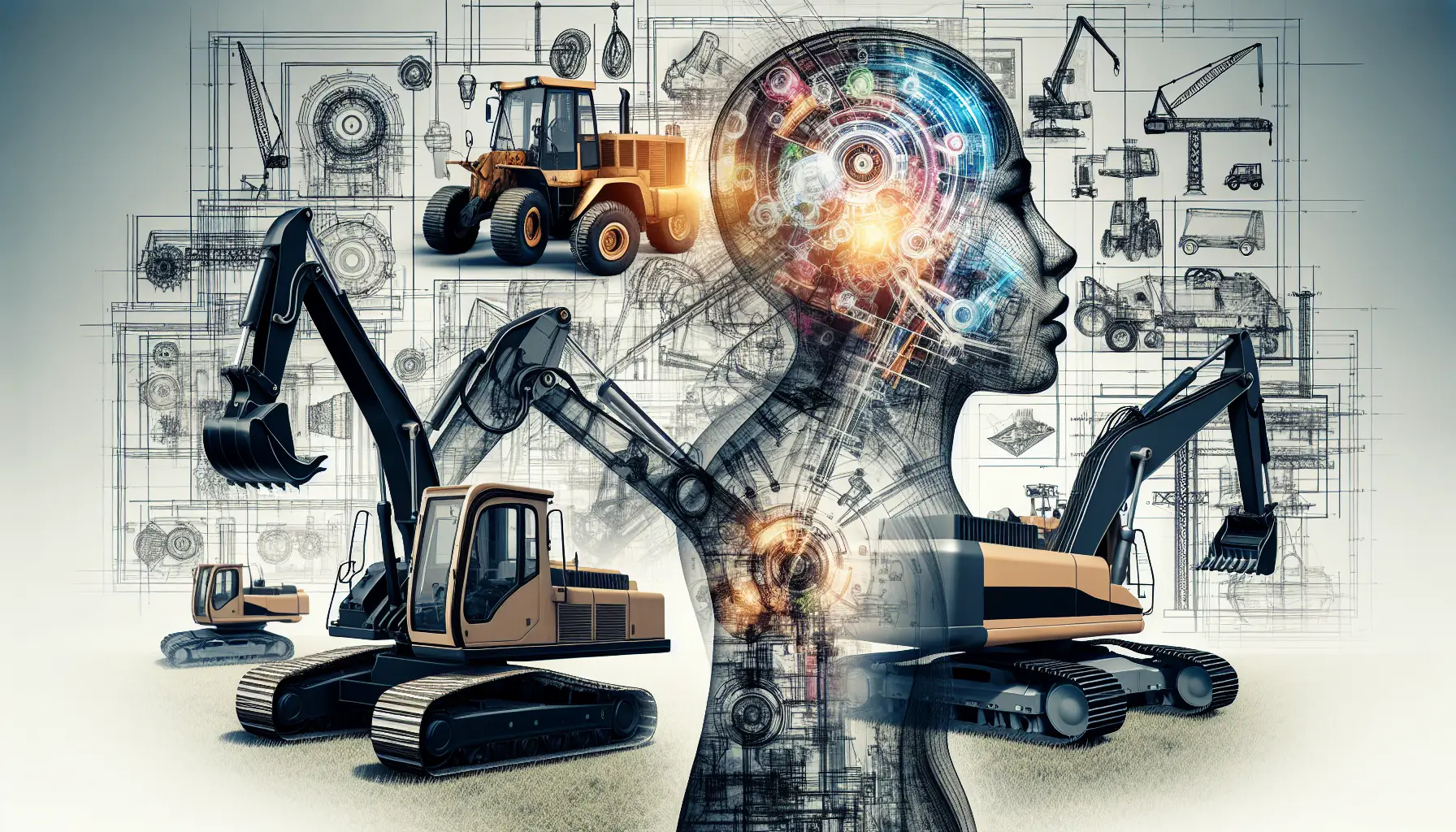
Construction Machinery: Detailed Guide to Equipment Specifications
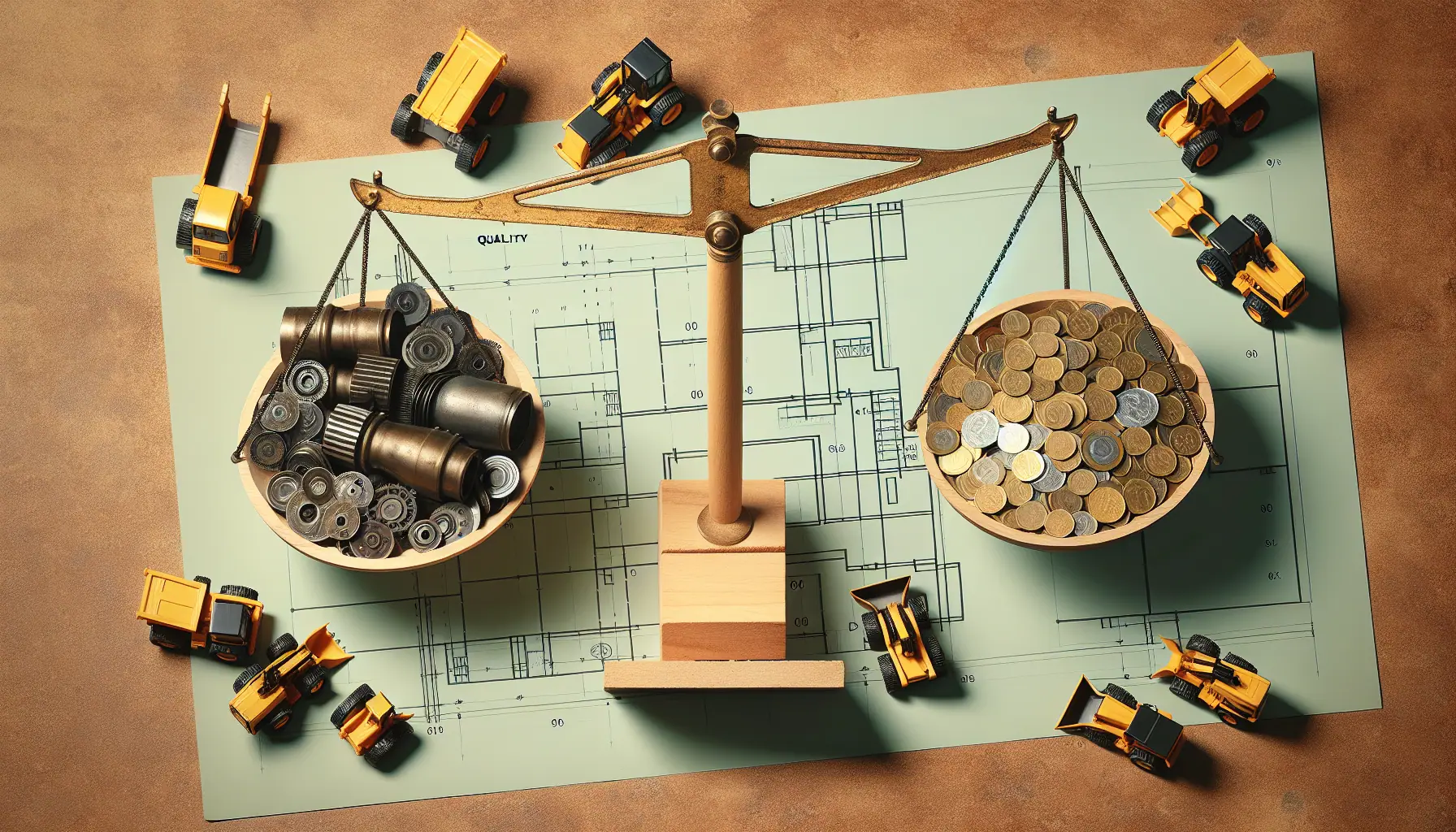
Heavy Machinery Prices: Key Factors in Cost and Quality Balance
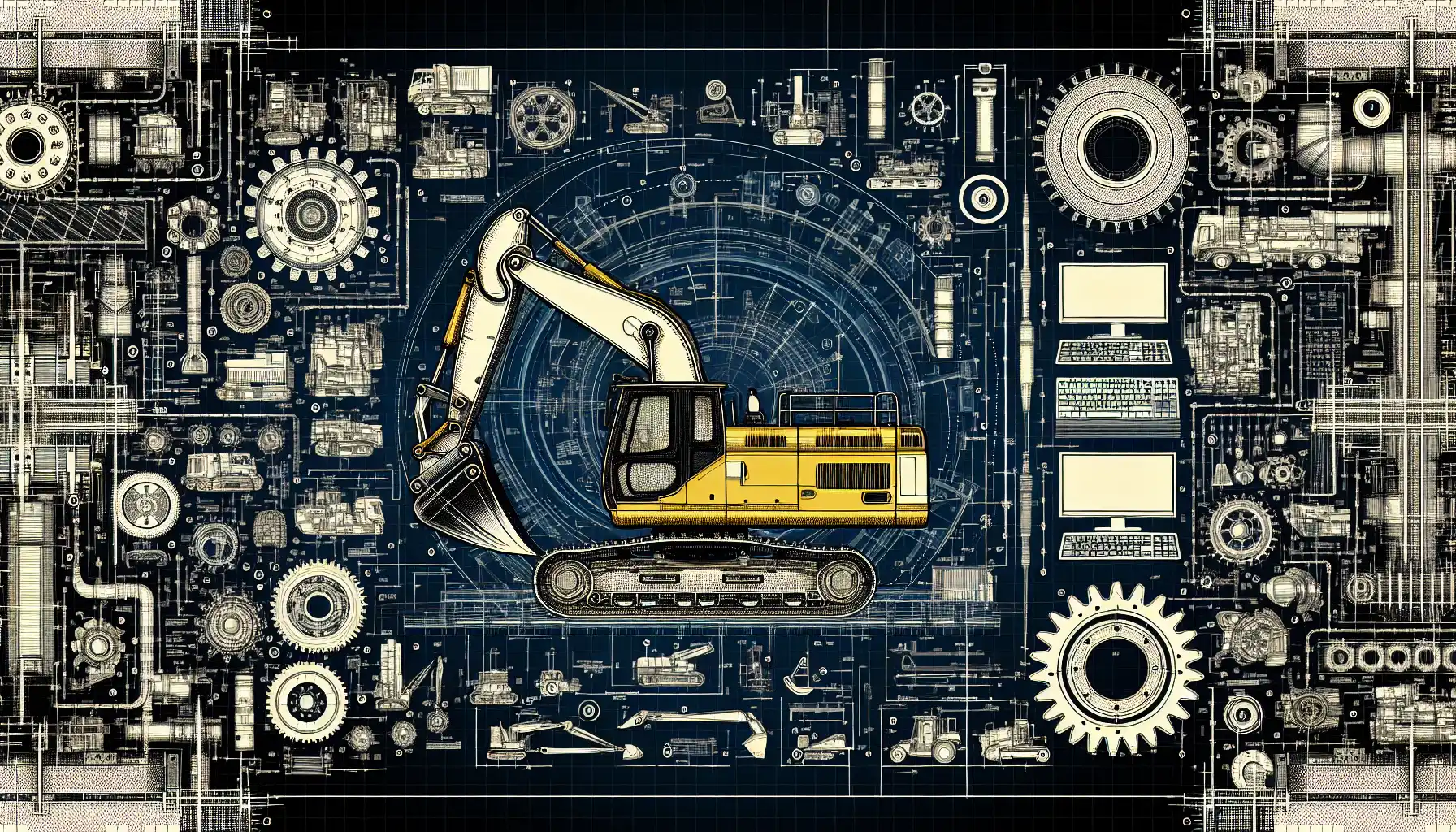
Best Construction Heavy Equipment Brands: Pros and Cons
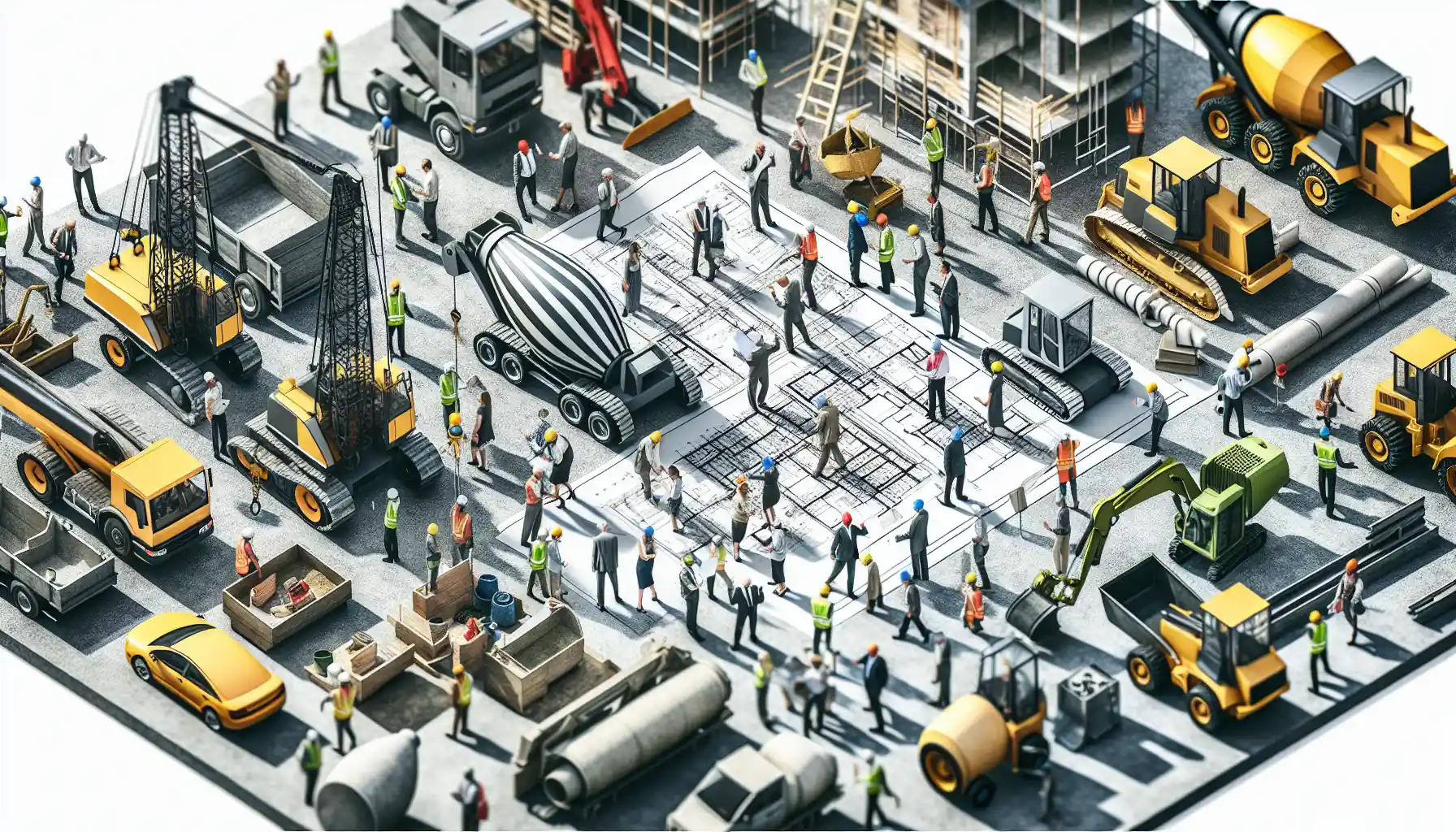
Construction Site Equipment: How to Determine Your Requirements
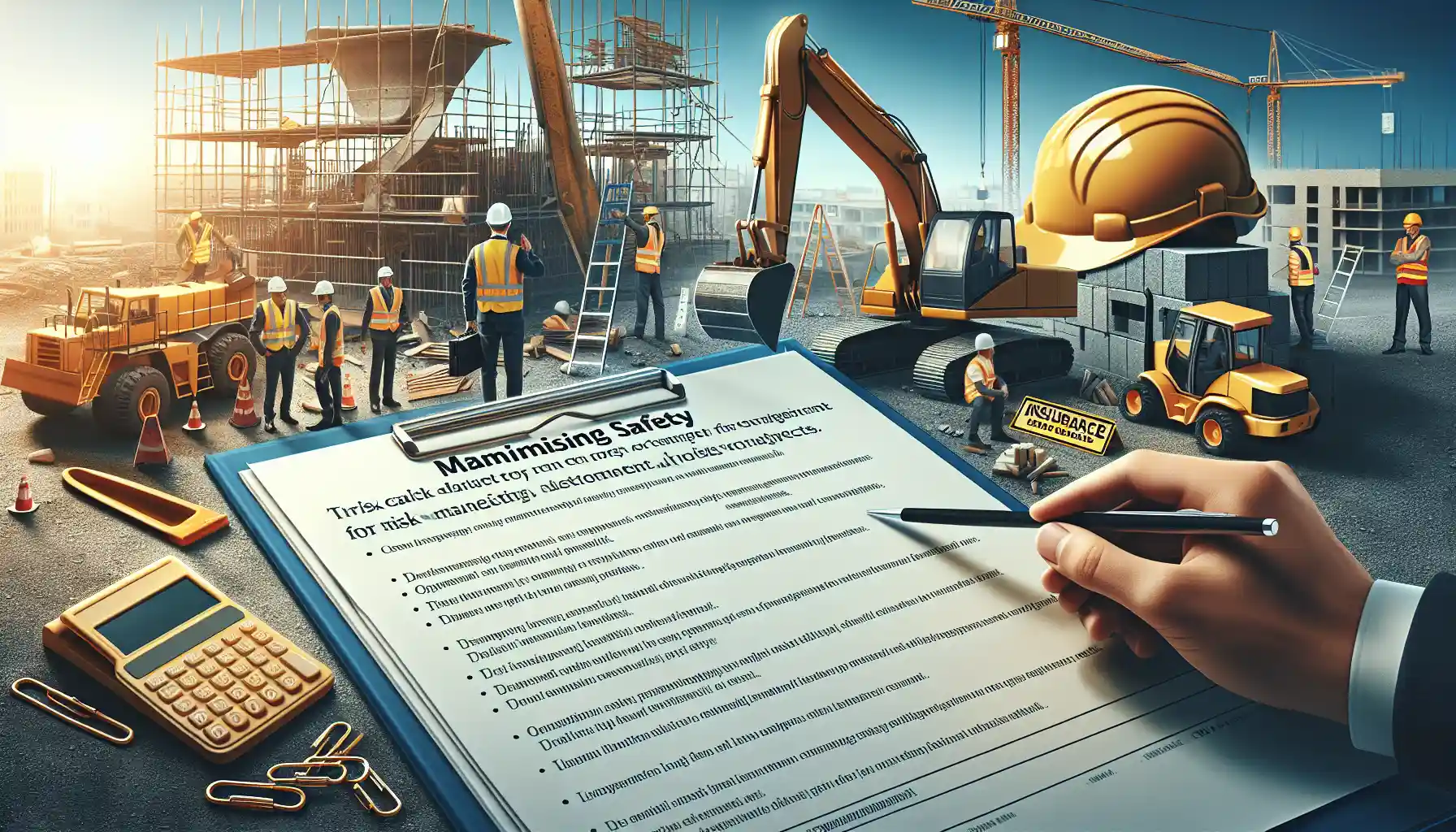
Maximizing Safety: Risk Management for Construction Projects
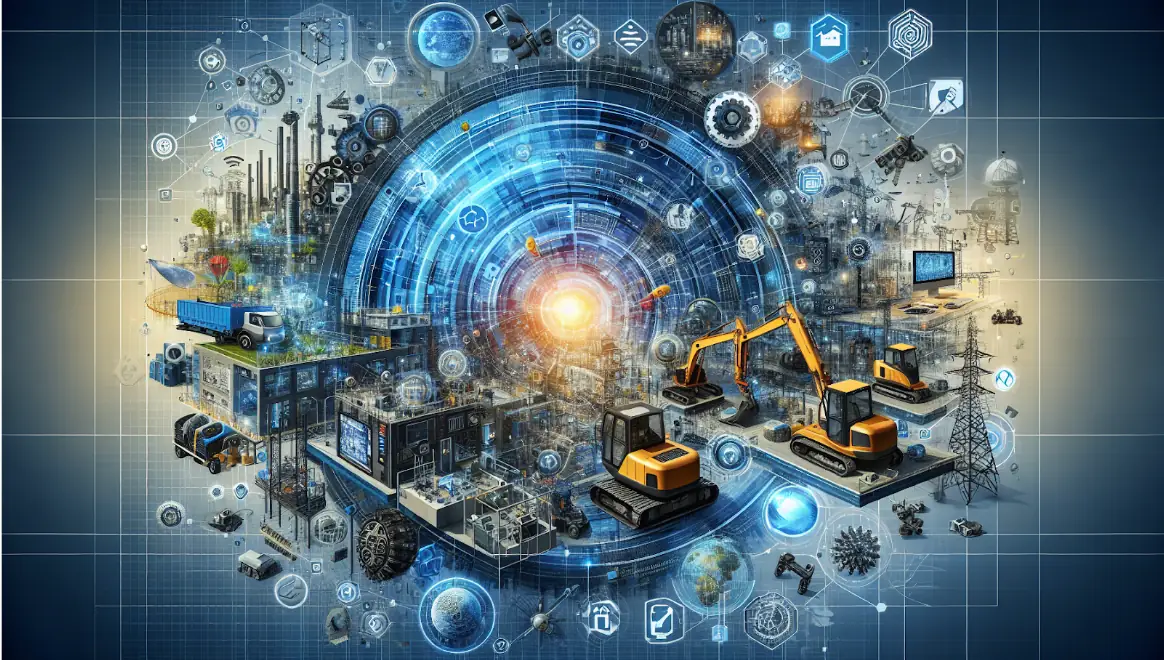
Innovations in Construction: Transforming Machinery and Equipment
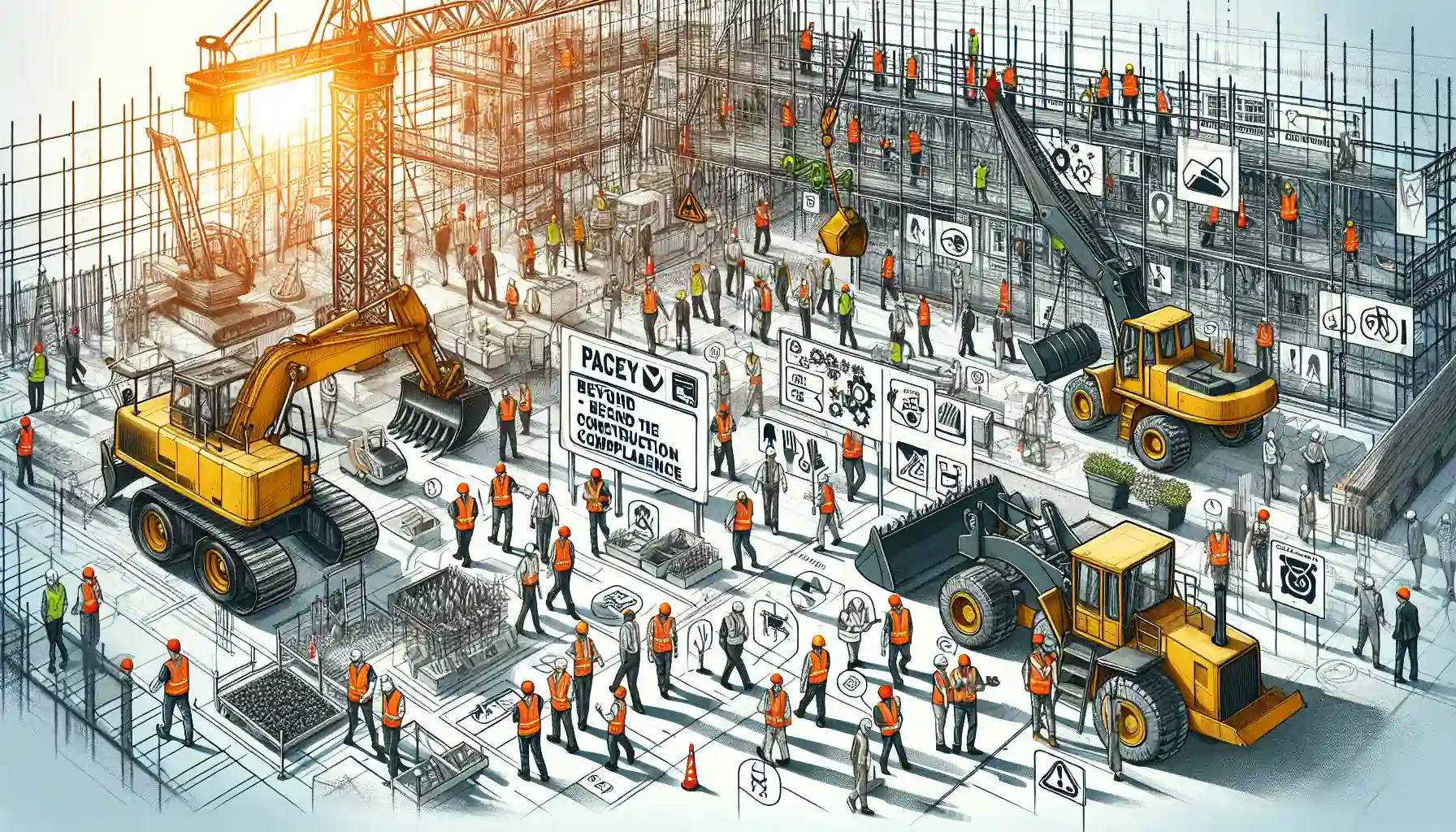
Heavy Equipment Safety: Beyond the Basics in Construction Compliance
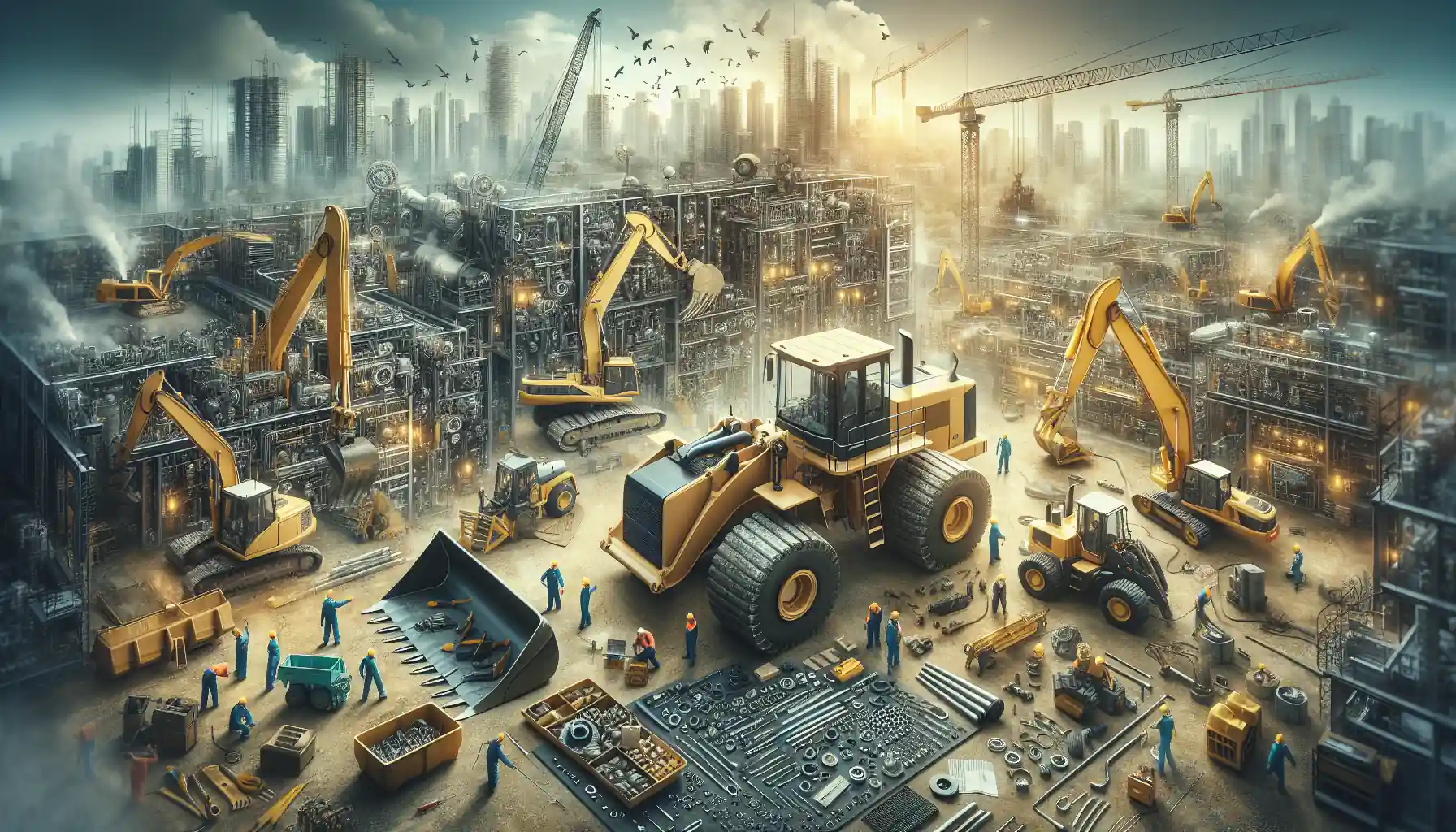
The Essential Handbook for Construction Equipment Repair and Maintenance
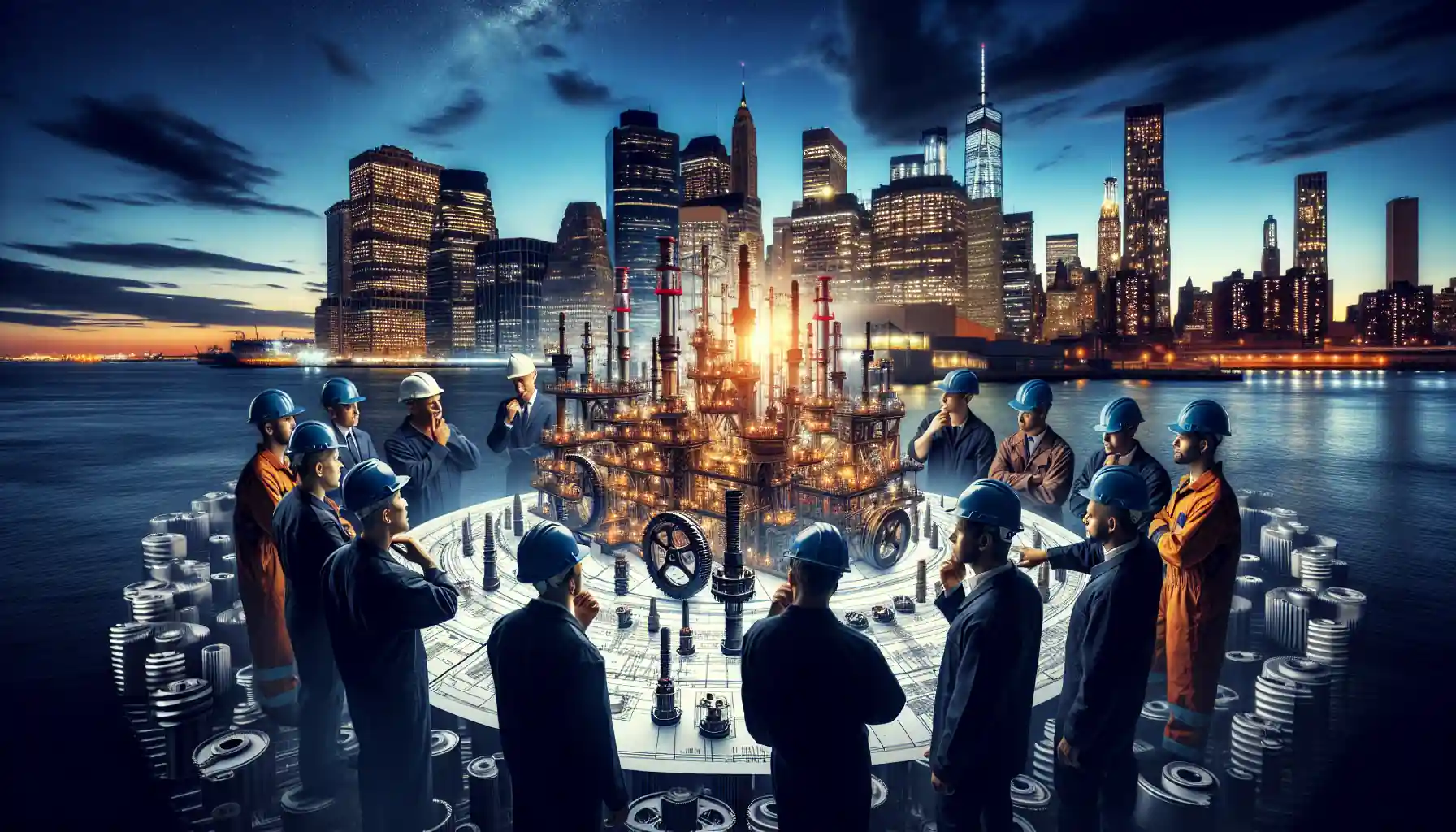
How to Efficiently Source Oil and Gas Machinery Parts in NYC
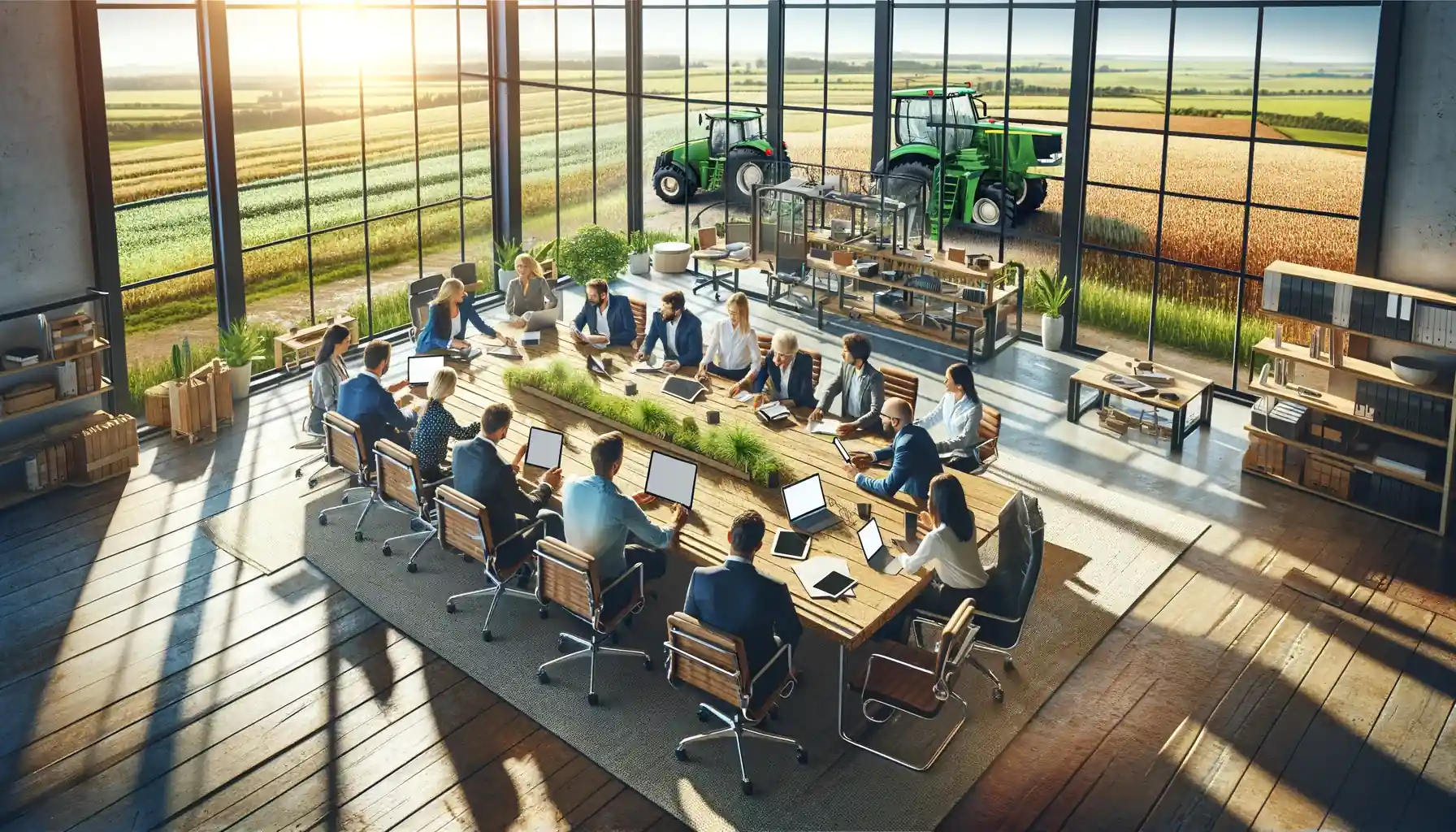
Essential Guide to Sourcing Agriculture Equipment Parts
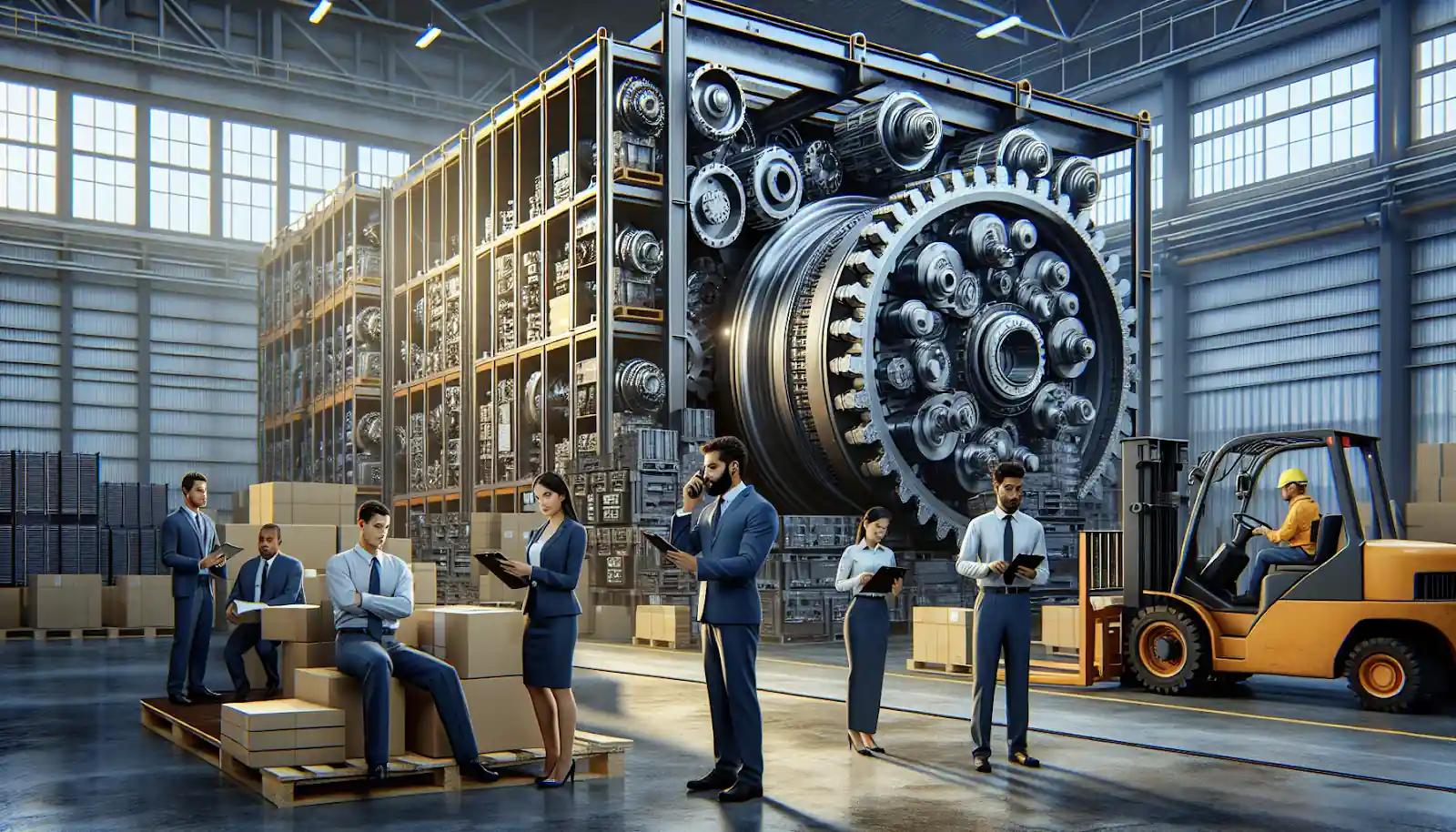
How to Source Mining Machinery Parts: Tips and Strategies
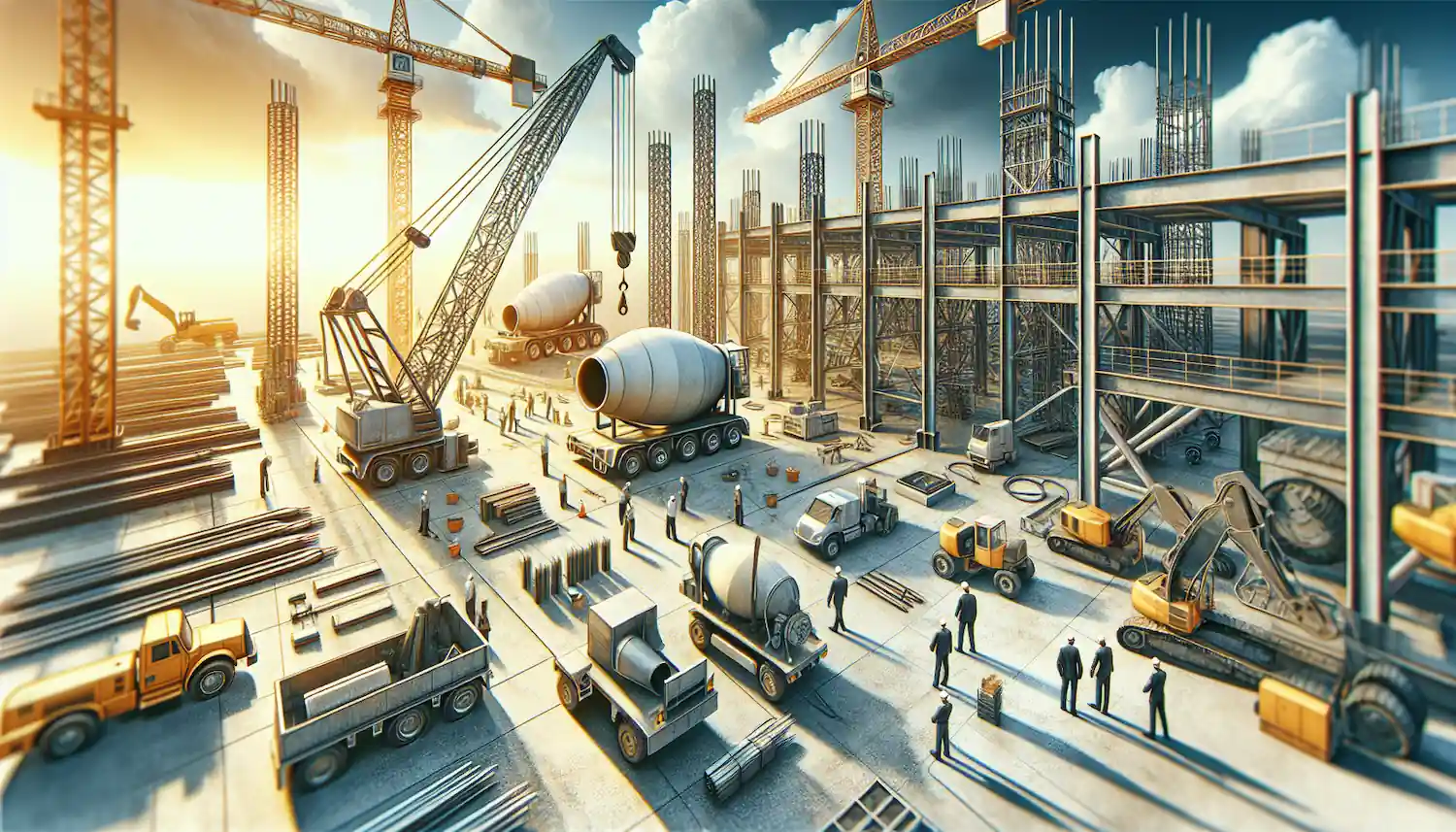