29 Quick Tips for Choosing Construction Equipment for Remote Locations
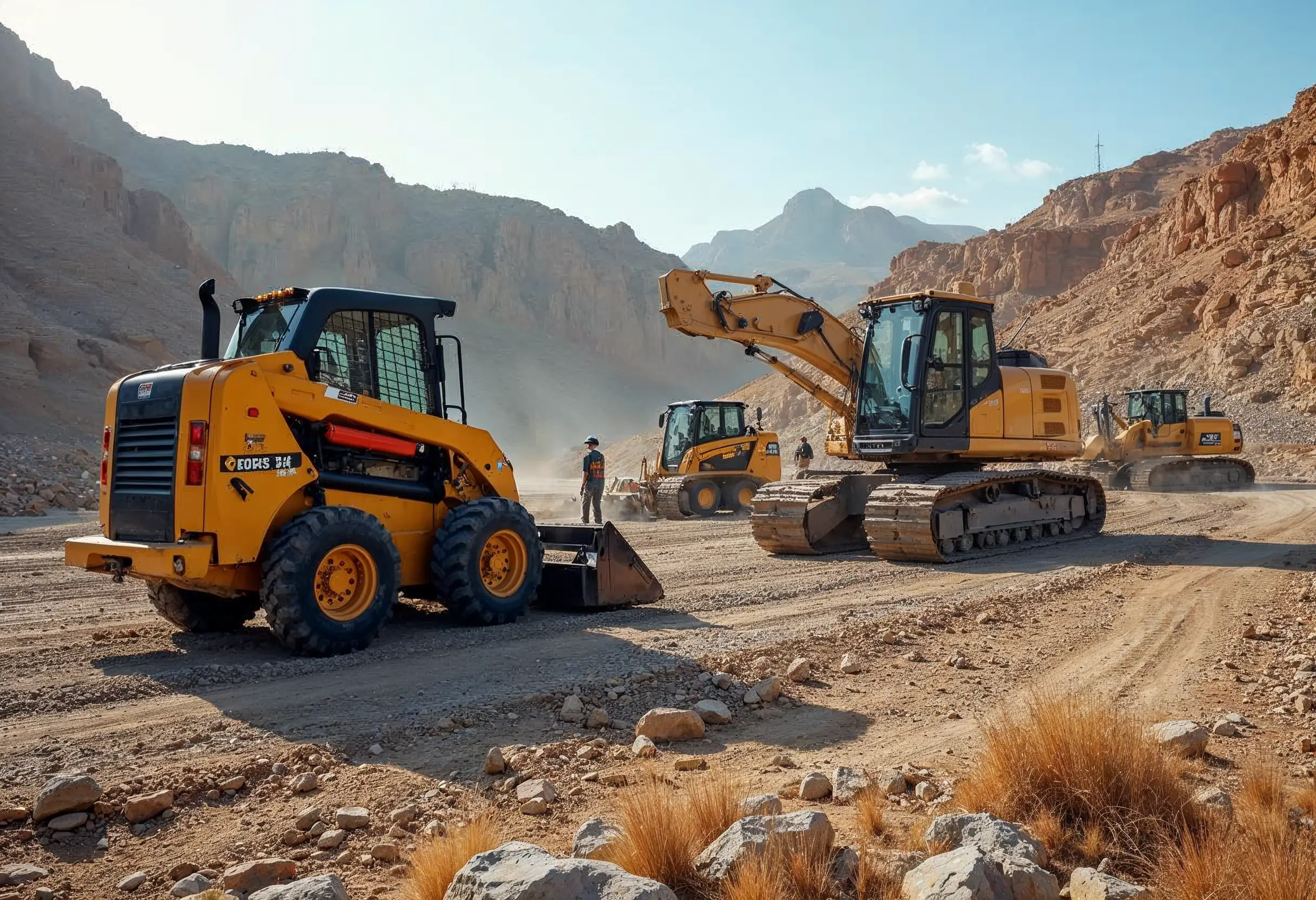
This construction equipment management guide will walk you through proven strategies for selecting the right machinery for your remote operations, helping you avoid costly mistakes and ensure project success. Let's explore the essential factors you need to consider for optimal equipment reliability and longevity.
Essential Equipment Selection Criteria for Remote Sites
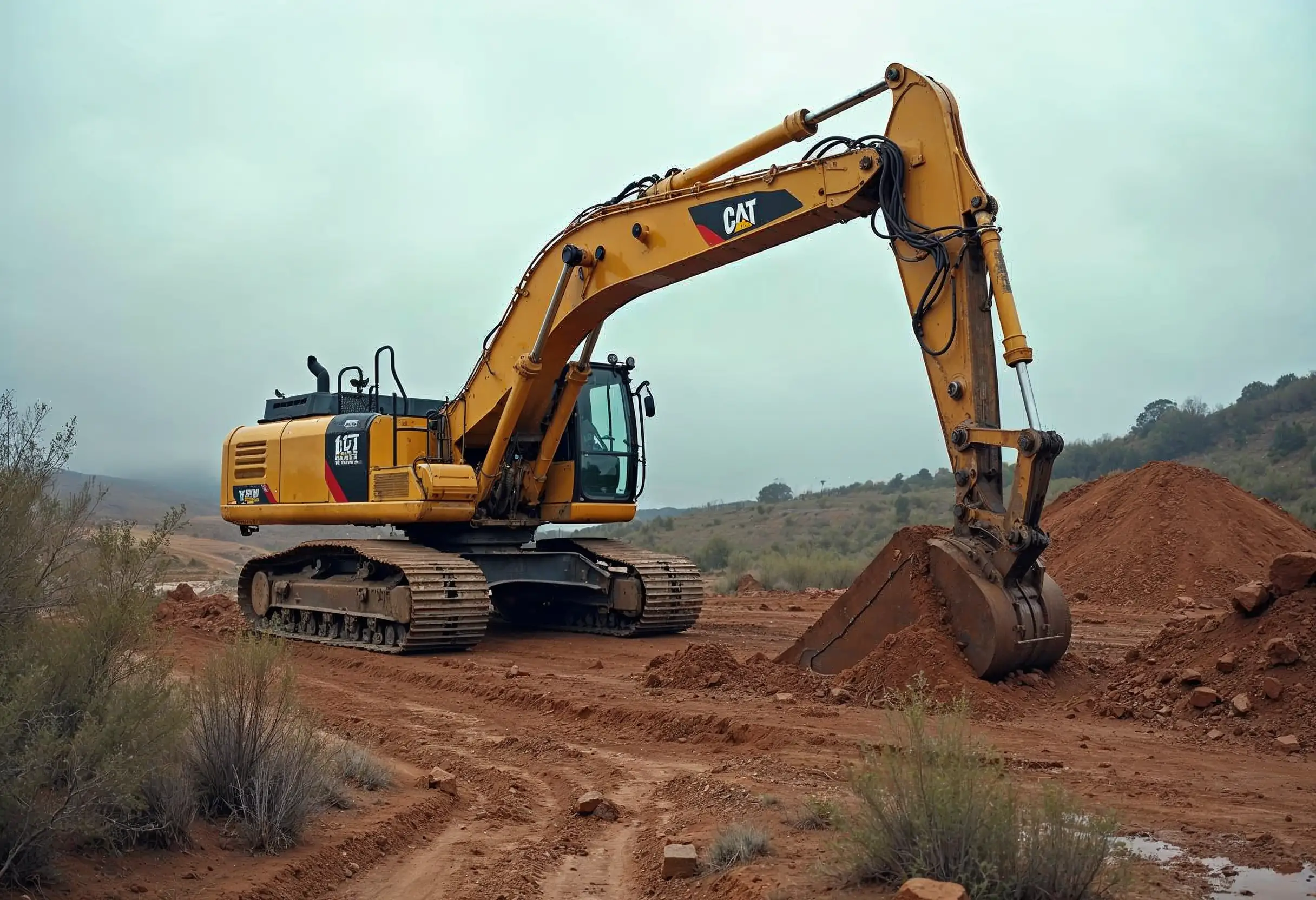
Selecting the right equipment for remote construction sites requires a strategic approach that goes beyond standard considerations. Modern construction equipment comes with advanced features that can significantly impact your remote operations' success and overall equipment reliability.
Evaluating Equipment Reliability and Durability
When choosing construction equipment for remote locations, durability becomes your primary concern. Modern machines are designed with sophisticated components that can withstand extreme conditions. Look for reliability equipment with:
- Sealed electronic systems in protected areas
- Advanced hydraulic protection systems
- Reinforced structural components
- Weather-resistant wiring and connections
These features contribute to improved machine reliability and equipment longevity, crucial factors for remote operations.
Fuel Efficiency and Power Source Considerations
Your remote site's power management strategy is crucial for uninterrupted operations. Remote fuel tanks can reduce operational costs and improve efficiency by providing on-site fuel access. Consider equipment with advanced power solutions that offer operational flexibility. Solar-powered charging stations can now be deployed without electrical work or permitting, giving you sustainable power options for electric equipment and enhancing overall equipment functionality.
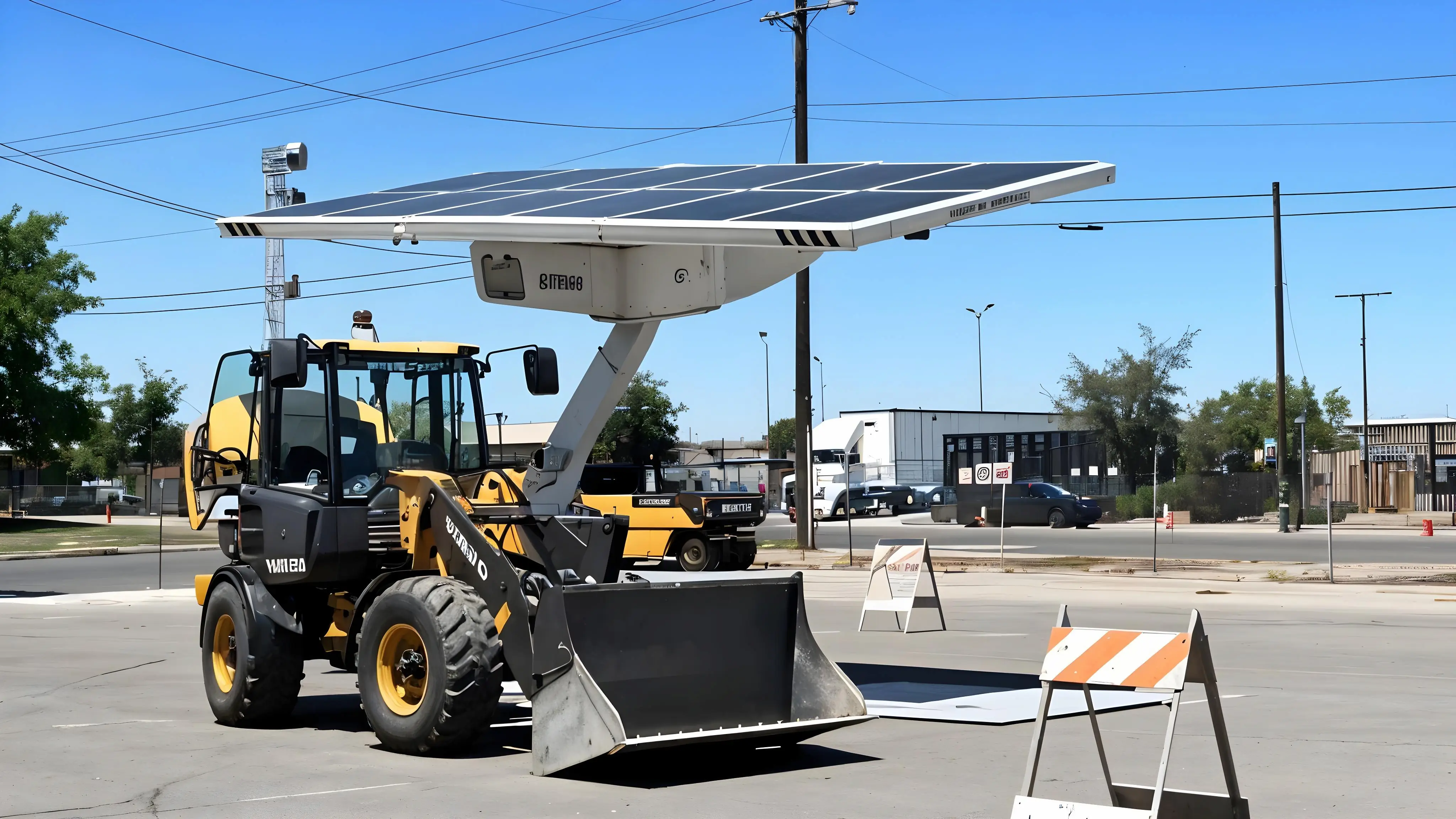
Multi-Purpose Equipment Selection
Versatile equipment reduces your logistics burden in remote locations. Excavators stand out as one of the most adaptable pieces of machinery, capable of handling multiple tasks including digging, lifting, transporting, demolition, and grading. Similarly, skid-steer loaders offer exceptional versatility with various attachments, making them ideal for remote sites where minimizing equipment count is crucial.
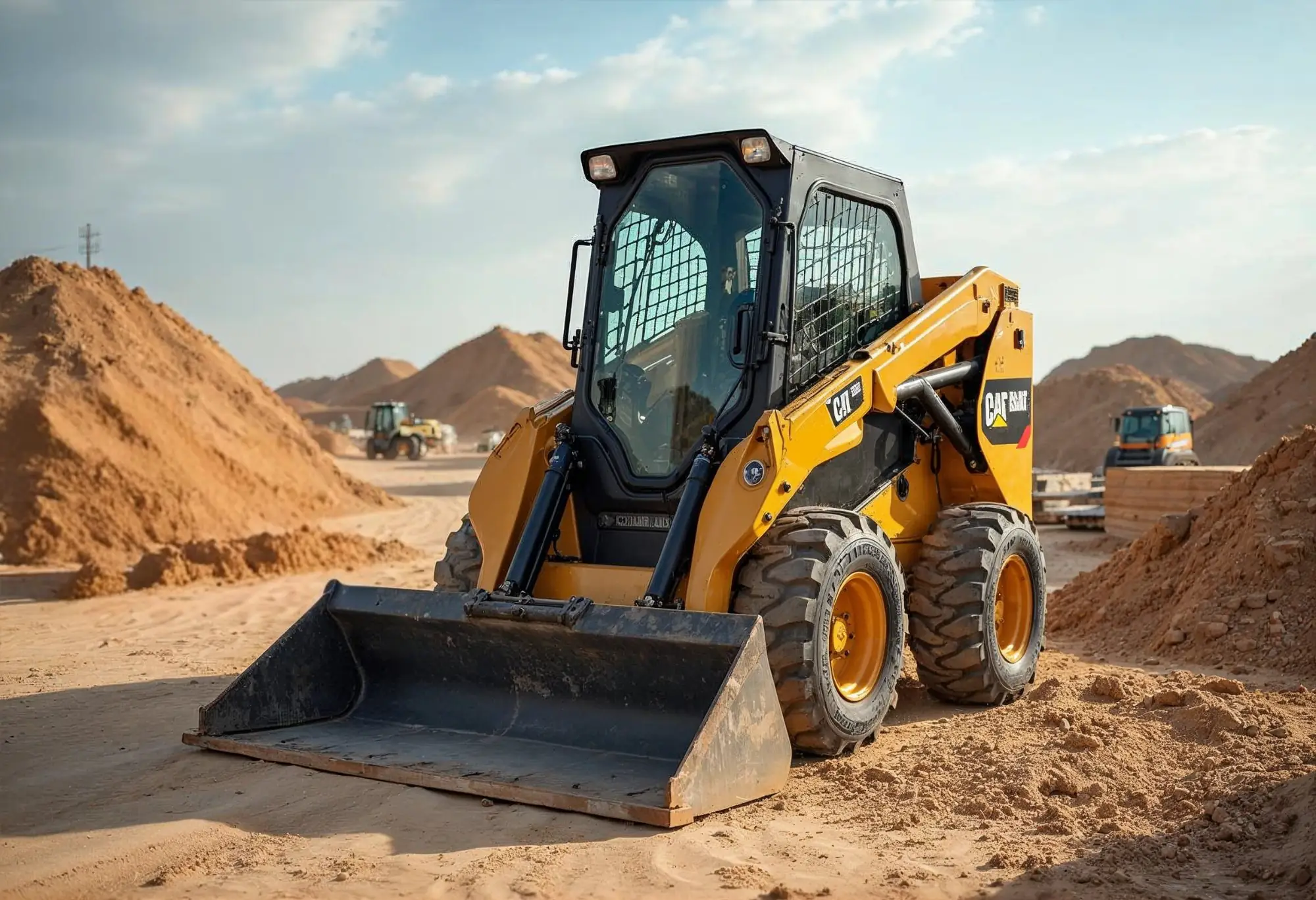
Remote operation capabilities add another dimension to your equipment's versatility. Modern remote control solutions can operate from up to 100 meters away, allowing you to maintain safe operations in challenging conditions while improving visibility and operational efficiency.
Need expert guidance on selecting the right equipment for your remote construction project? Contact MCH Parts for a free sourcing machinery consultation and quote to ensure you make the most informed decision for your specific needs and develop an effective equipment reliability strategy.
Transportation and Logistics Planning
Transporting heavy equipment to remote locations requires meticulous planning and specialized expertise. According to industry data, transport costs can increase significantly with long-distance travel, adding substantial time and fuel expenses to your project budget.
Equipment Size and Transportation Constraints
Your equipment's dimensions and weight directly impact transportation methods and costs. Different machines require specific trailer types - from flatbeds for small equipment to removable goosenecks (RGN) that can stretch more than 65 feet for larger machinery. Consider these key transportation factors:
- Load weight distribution requirements
- Height and width restrictions for routes
- Specialized trailer needs for oversized equipment
- Equipment securing protocols
Access Route Assessment and Planning
Proper route planning is crucial for remote site access. Studies show that rescue operations frequently require vehicles to access areas located outside the transportation network. Your route assessment should include:
- Initial road network evaluation
- Terrain passability mapping
- Bridge and overpass clearance verification
- Alternative route identification
Equipment Assembly and Disassembly Requirements
Some equipment may require partial disassembly for transport, especially when dealing with height restrictions or weight limitations. Container shipping often necessitates equipment breakdown and reassembly, which should factor into your logistics timeline and resource allocation.
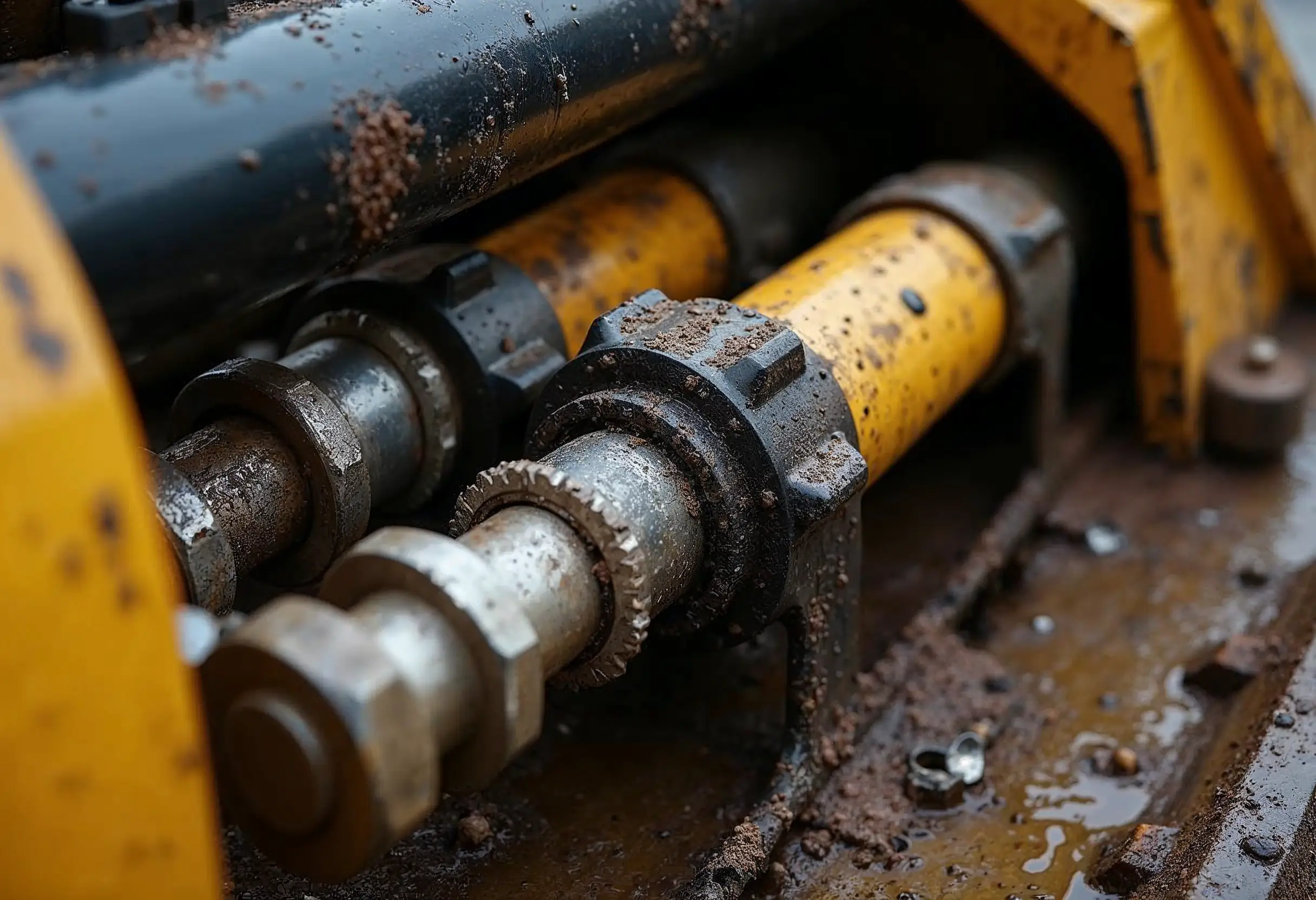
For specialized guidance on transporting your heavy equipment to remote locations and accessing reliable parts support, contact MCH Parts for a free sourcing machinery consultation and quote.
Maintenance and Repair Strategies
Maintaining your construction equipment in remote locations requires a strategic approach to prevent costly downtime. According to industry data, inventory and purchasing staff have the largest impact on maintenance productivity compared to any other support group. Effective construction equipment maintenance is crucial for ensuring equipment reliability and operational efficiency.
On-Site Maintenance Capabilities
Your remote site maintenance strategy should include comprehensive monitoring systems. Modern IoT integration and data analytics can now alert you if something is off at your operation, helping you streamline processes and improve safety across projects. Implementing predictive maintenance programs can reduce inventory carrying costs by 20% and improve equipment availability by 15%.
Condition monitoring and equipment diagnostics play a vital role in maintaining equipment functionality. By leveraging these technologies, you can enhance your equipment reliability solutions and minimize unexpected breakdowns.
Critical Spare Parts Inventory
Managing your critical spare parts inventory effectively is crucial for remote operations. Essential items to maintain on-site include:
- Fuel, oil, and air filters
- Hydraulic hoses and fittings
- Batteries and electrical components
- Engine parts like starters and alternators
- Track pads with bolts (for tracked machines)
Studies show that carrying costs typically represent 25% of inventory value per year, making it essential to optimize your stock levels without compromising operational readiness. Effective spare parts management is key to reducing maintenance costs and ensuring equipment dependability.
Emergency Repair Protocols
Your emergency response plan should follow these critical steps:
- Isolate the immediate source of danger
- Notify the chain of command
- Assess damage and plan repairs
- Execute repair process while maintaining safety protocols
Remote monitoring solutions can help you detect potential issues before they become emergencies, with systems capable of alerting you via email, text, or voice call when readings fall outside preset thresholds. This proactive approach contributes to equipment breakdown prevention and failure prediction.
For expert guidance on optimizing your equipment maintenance program and accessing reliable parts support, contact MCH Parts for a free sourcing machinery consultation and quote. They can assist you in developing comprehensive maintenance agreements tailored to your remote location needs.
Equipment Redundancy and Backup Planning
Equipment redundancy stands as your first line of defense against costly downtime in remote construction sites. Research shows that equipment redundancy can ensure near 100% uptime for critical operations, significantly enhancing overall equipment reliability.
Identifying Critical Equipment Needs
Your redundancy strategy should align with equipment criticality. Studies indicate that critical equipment needs redundancy, while ancillary equipment can operate without it. Consider implementing:
- Full redundancy for safety-critical systems
- Standby equipment for high-priority operations
- Backup units for essential machinery
- Remote monitoring capabilities for critical assets
Remote operation technology now enables you to control equipment from up to 300 feet away, providing additional operational flexibility and safety benefits. This technology enhances equipment performance monitoring and contributes to improved equipment utilization.
Backup Power Solutions
Power reliability becomes crucial in remote locations, where outages can lead to significant economic losses. Your backup power strategy should include:
- Primary generator systems
- Secondary power sources
- Automatic transfer switches
- Remote monitoring capabilities
Natural gas, propane, or diesel generators can serve as your primary backup source, with selection depending on fuel availability and startup requirements. Modern backup systems feature automatic activation during outages, with transfer times as fast as 0.8 milliseconds.
Alternative Equipment Options
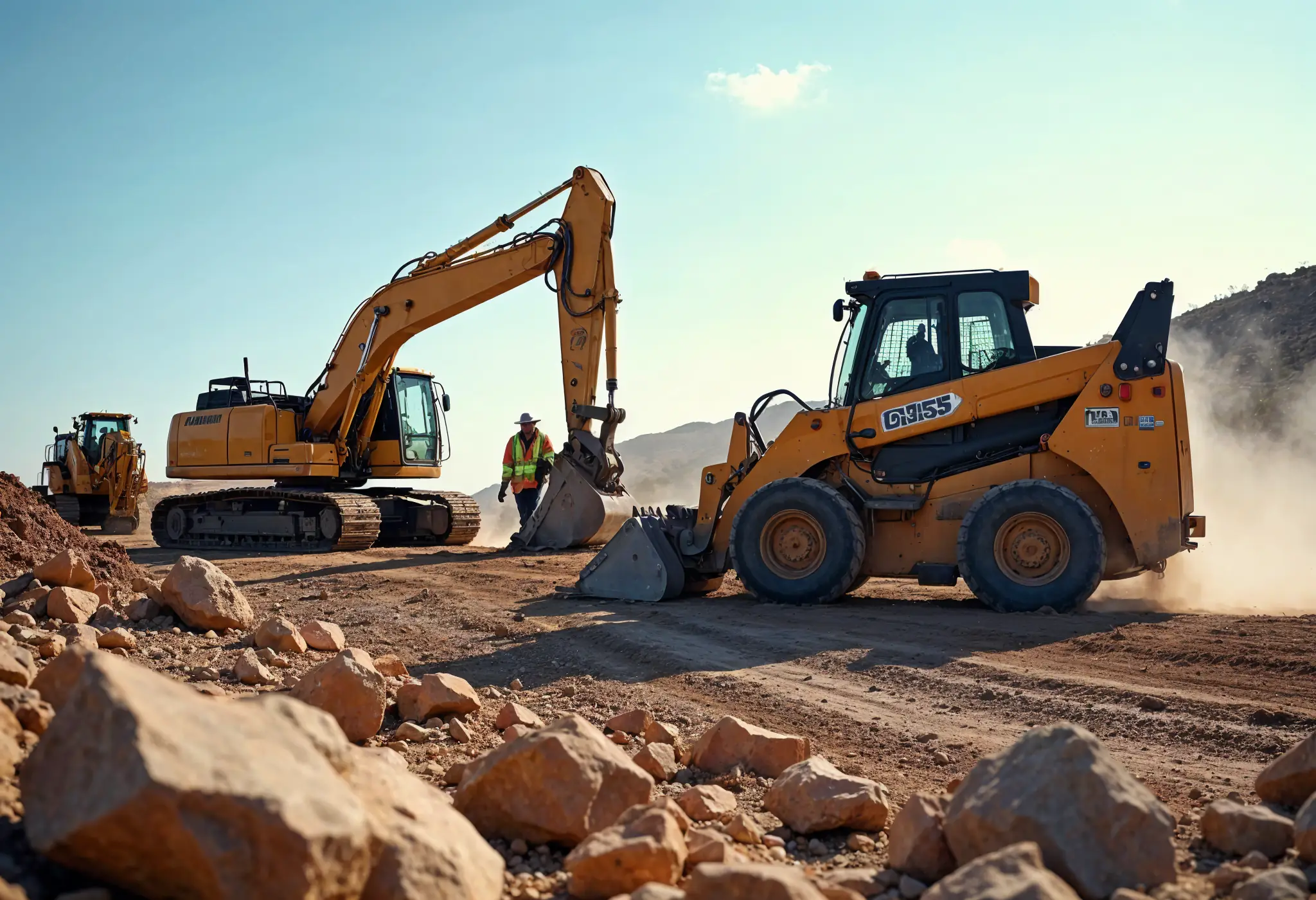
Implementing a multi-layered approach to equipment redundancy provides optimal protection. Vendor-managed inventory helps reduce downtime by ensuring backup equipment is readily available on-site or in consignment. Your alternative equipment strategy should consider:
Remote operation capabilities now allow you to control multiple machines from a single platform, enhancing your operational flexibility. GPS tracking systems help monitor equipment location and usage patterns, enabling proactive maintenance scheduling and theft prevention. These technologies contribute to improved equipment performance and overall construction equipment management.
For expert guidance on implementing the right redundancy strategy and accessing reliable equipment alternatives, contact MCH Parts for a free sourcing machinery consultation and quote.
Conclusion
Successful remote construction projects depend heavily on smart equipment choices and strategic planning. Your equipment decisions directly impact project timelines, operational costs, and overall success rates in remote locations.
Smart maintenance strategies, combined with proper redundancy planning, help prevent costly downtime that could otherwise halt your entire operation. Modern technology offers additional advantages through remote monitoring, preventive maintenance, and advanced control systems that maximize your equipment efficiency and reliability.
Remember that each remote site presents unique challenges requiring careful consideration of transportation logistics, maintenance capabilities, and backup solutions. Consider reaching out to MCH Parts for a free sourcing machinery or parts consultation, ensuring your business benefits from top-tier equipment and service. Their expertise can help you develop a comprehensive equipment reliability strategy tailored to your specific remote location considerations.
FAQs
What should be considered when selecting construction equipment?
When choosing construction equipment, it's important to evaluate several factors including the cost and scope of the project, the conditions of the job site, the size of the equipment, available attachments, and the necessary training and certifications for operation. Additionally, consider the requirements for marking, site grading, landscaping, demolition, and material transportation. Equipment reliability, maintainability, and operational efficiency should also be key considerations in the selection process.
What are the key factors to consider for the selection of construction equipment?
Key considerations for selecting construction equipment include economic factors such as purchase and operating costs, company-specific policies on equipment ownership, site-specific conditions that affect equipment usability, and equipment-specific attributes like the availability of spare parts. Equipment reliability, maintenance costs, and the potential for equipment breakdown prevention should also be factored into the decision-making process.
On what basis should equipment be selected for construction projects?
Equipment selection for construction should be based on environmental factors at the work site, such as temperature and terrain. Considerations should also include the preferred noise level and ground impact as per client specifications to ensure the equipment performs optimally under the project conditions. Additionally, factors such as equipment longevity, maintainability, and the availability of maintenance agreements should be taken into account to ensure long-term operational efficiency.
How can construction equipment be effectively tracked?
To effectively track construction equipment, implement a five-step system: start by creating a comprehensive list using an inventory management system, attach barcodes and QR codes to tools, categorize or bundle tools as needed, monitor the movement of items across different locations, and establish a system for timely reordering of tools and equipment. Utilizing equipment reliability software and IoT integration can further enhance tracking capabilities and contribute to improved construction equipment management.
Read More
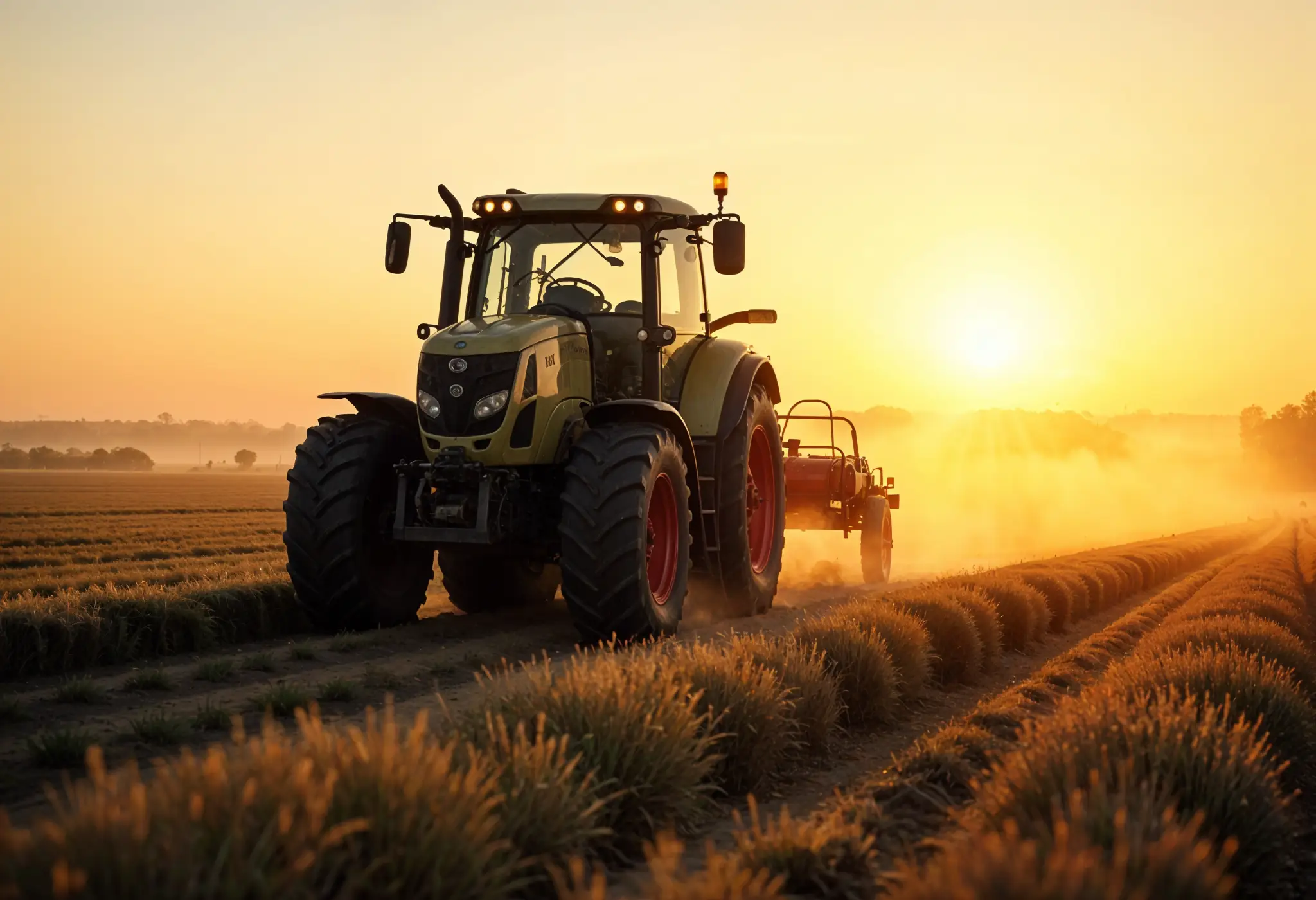
Top Hydraulic Components for Agricultural Equipment in 2025: Complete Guide
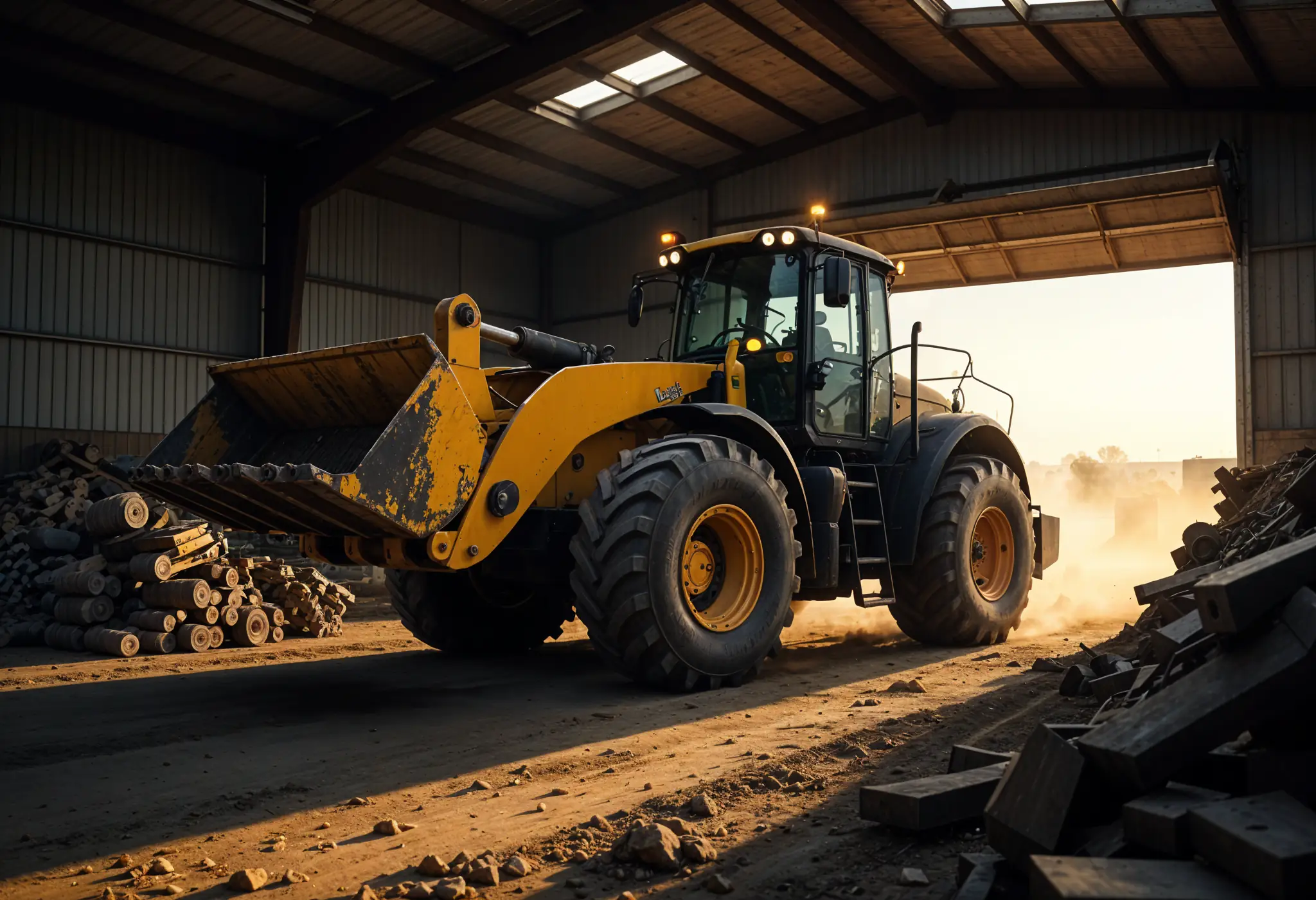
The Essential Farm Equipment Parts You Can't Afford to Run Out Of
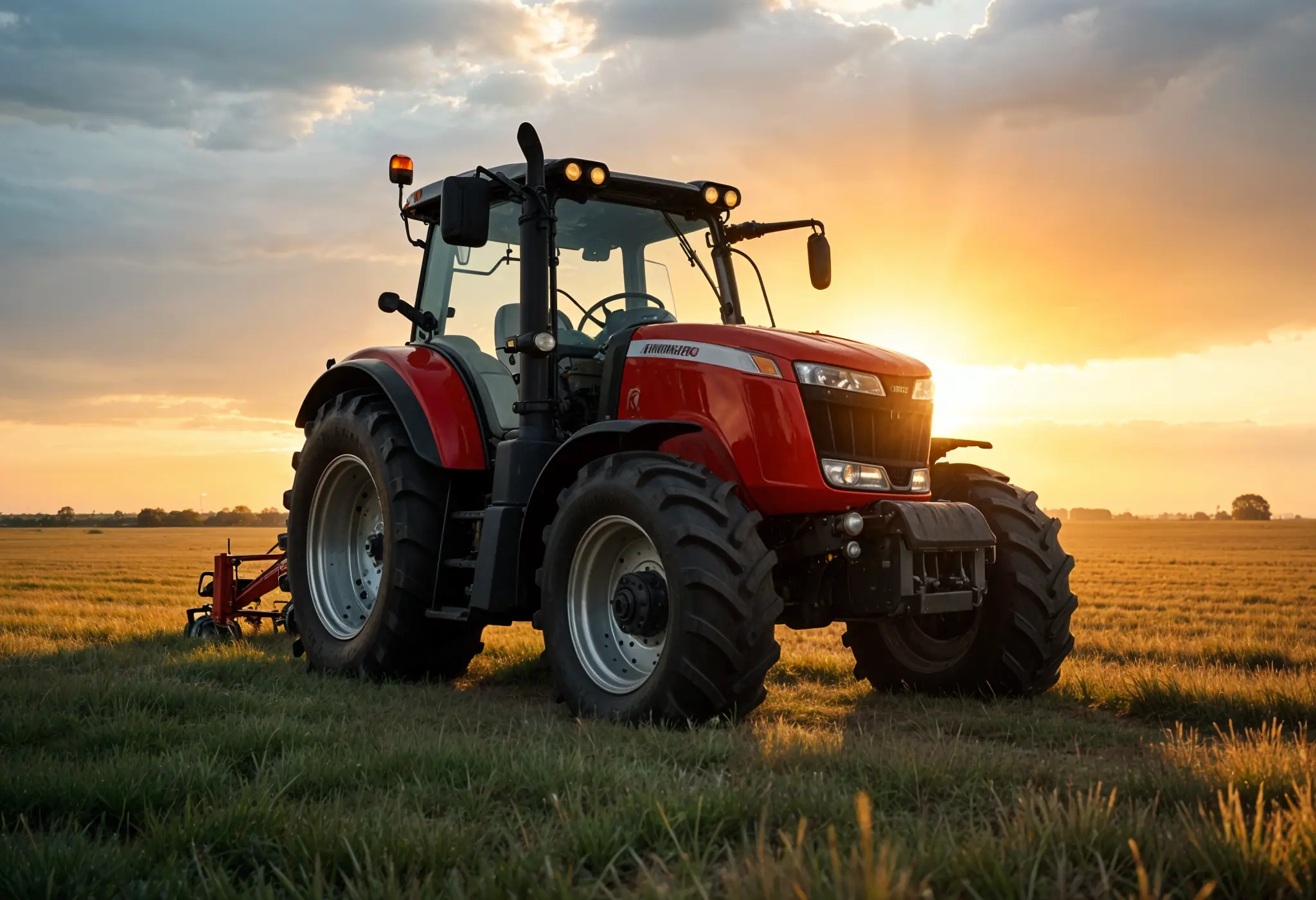
How to Service Farm Equipment: A Farmer's Guide to Zero Harvest Downtime
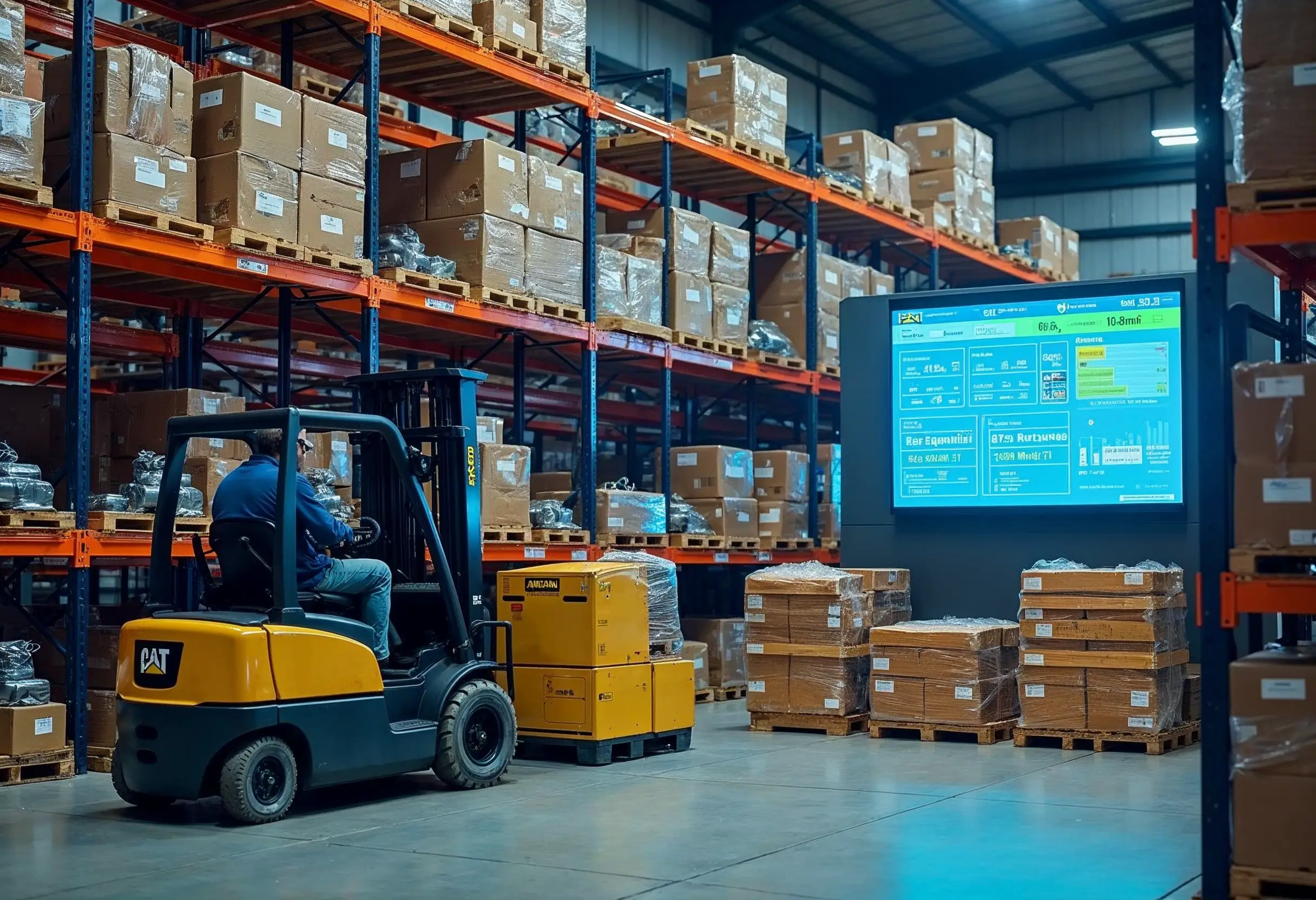
Construction Machinery Parts Suppliers: Expert Selection Guide
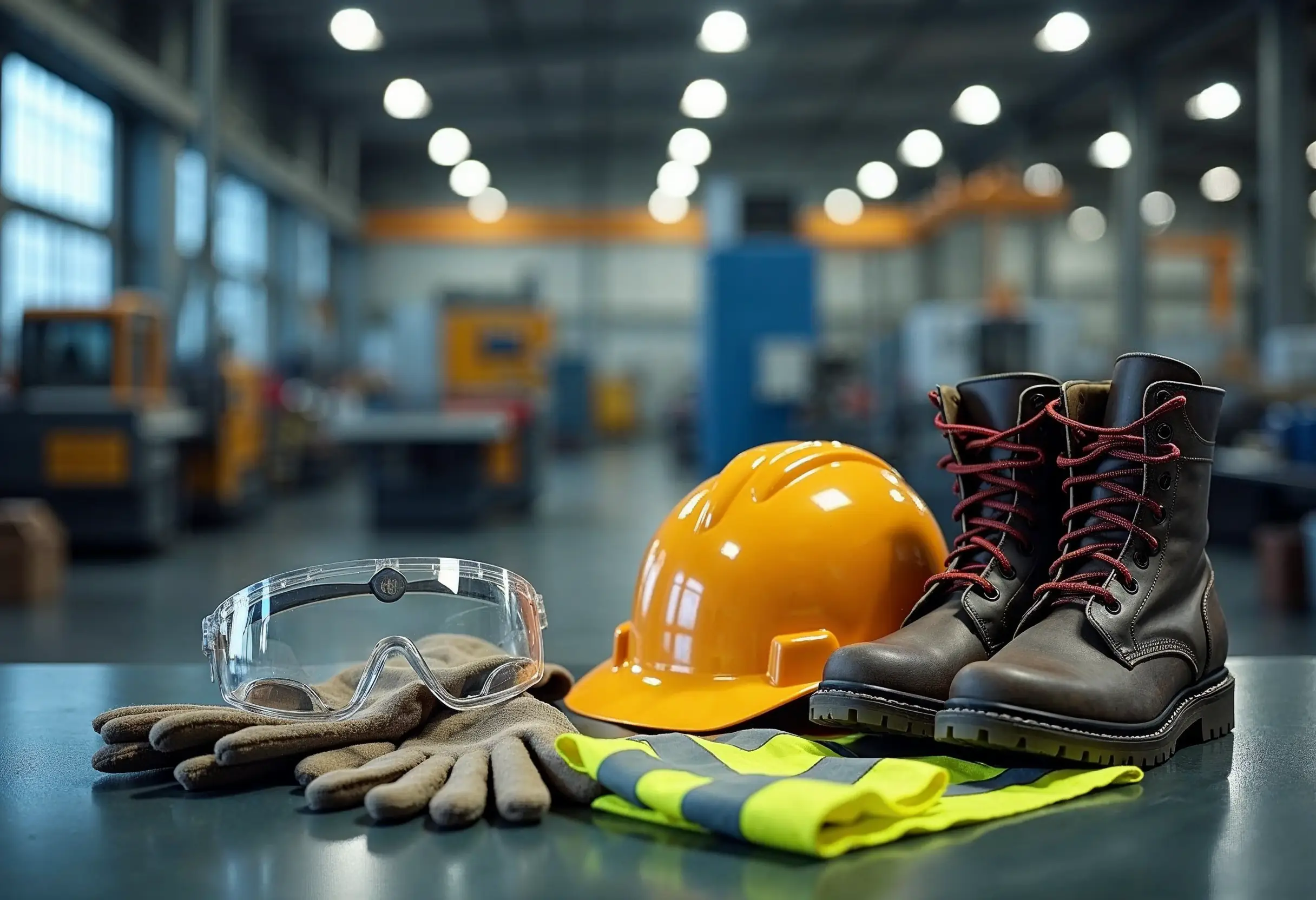
How to Apply Machine Safety Rules: From Selection to Installation
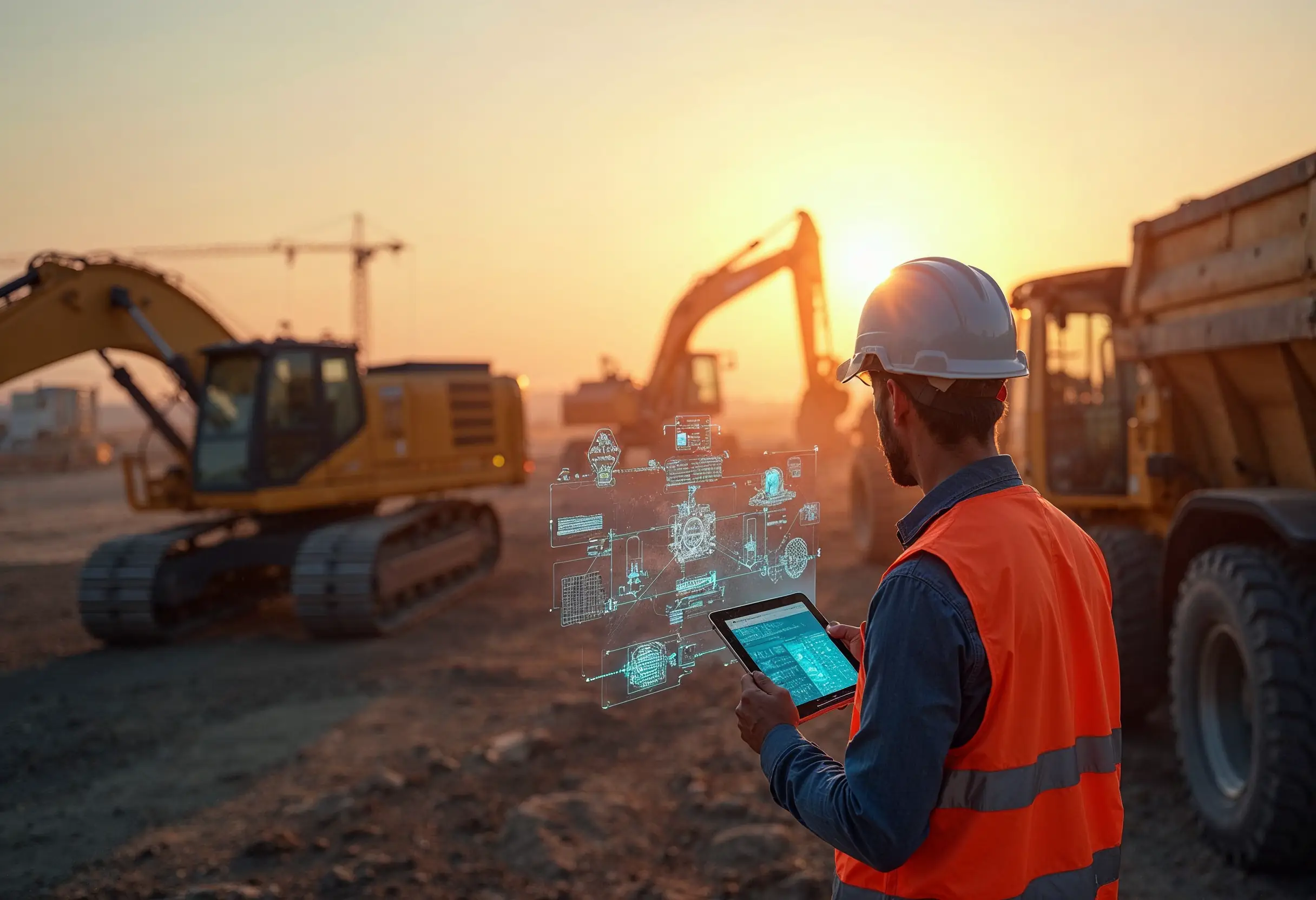
Smart Diagnostics Cut Heavy Equipment Failures by 73%
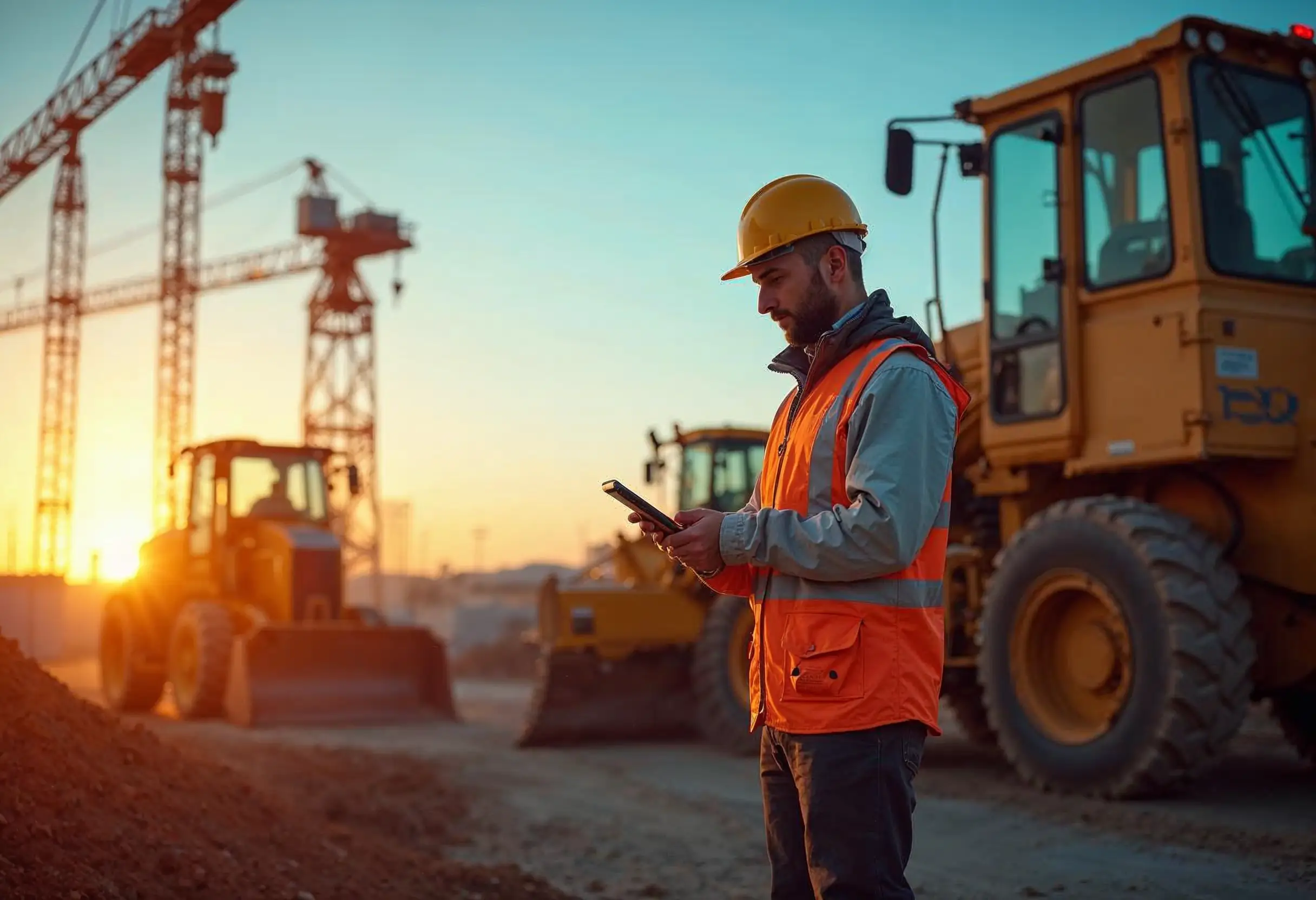
5 Ways to Assess the Environmental Impact of Heavy Construction Machinery
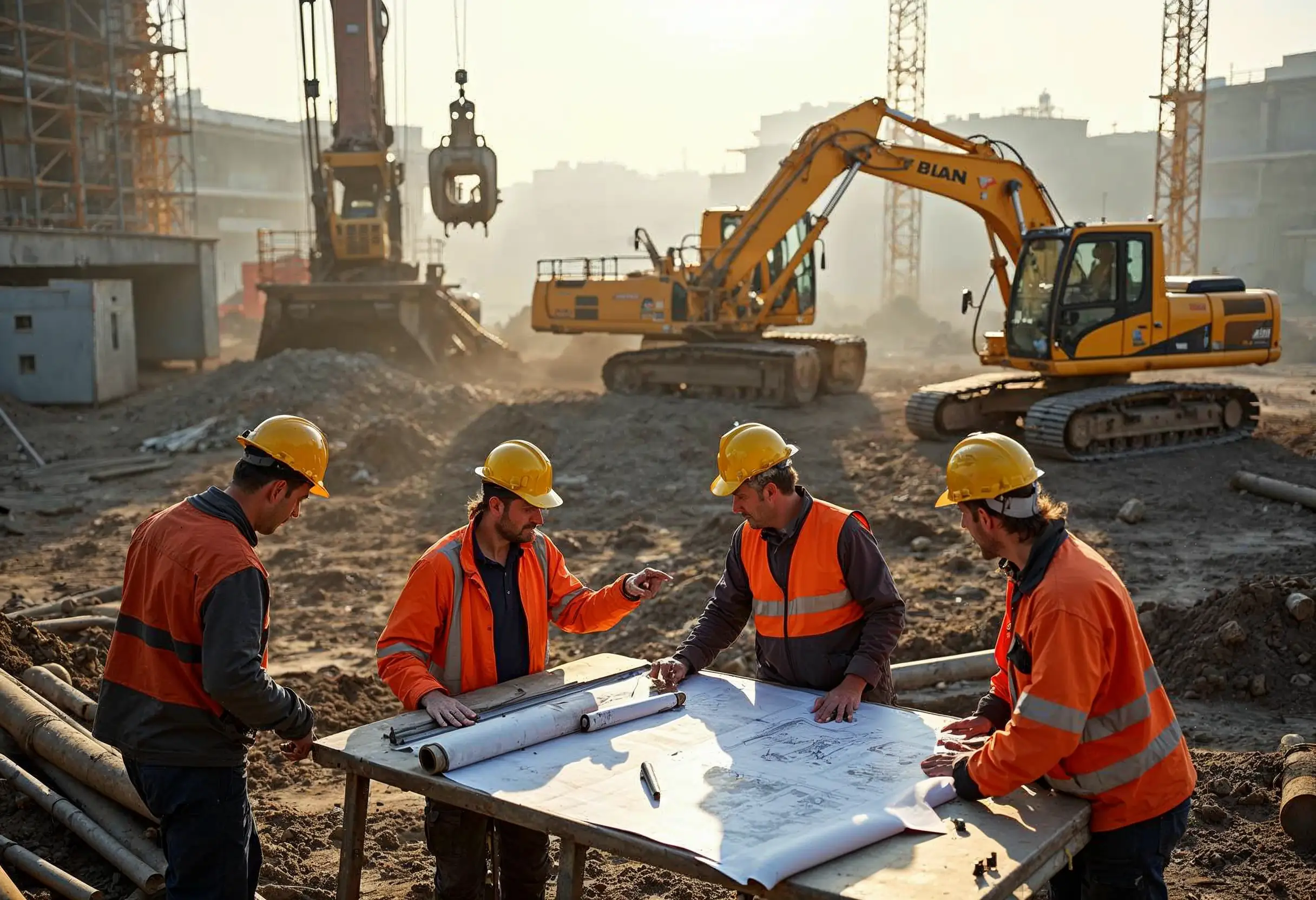
10 Smart Ways to Pick Construction Machinery for 2025 Projects
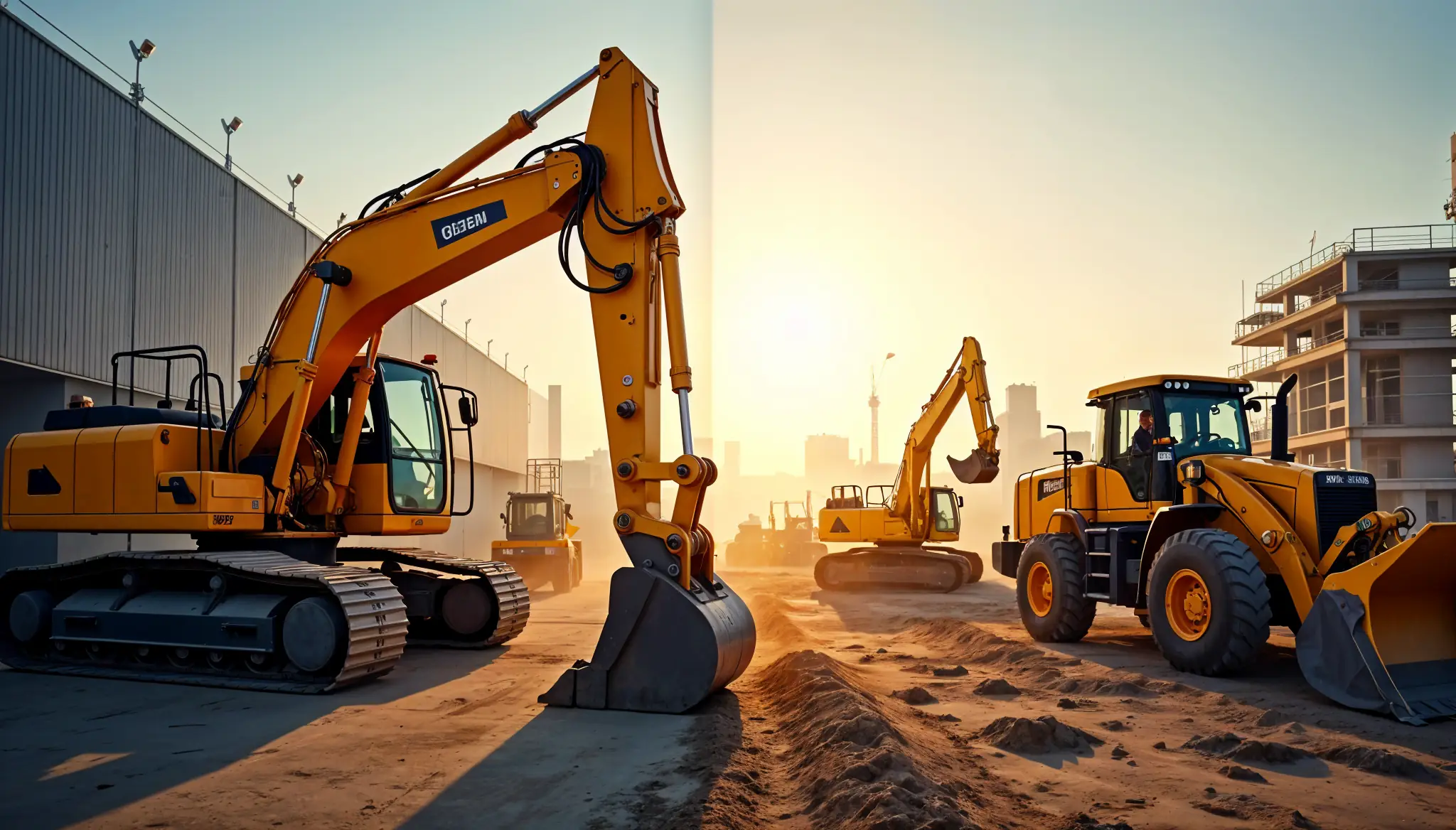
Rent vs Purchase Equipment: What Heavy Industry Experts Hide
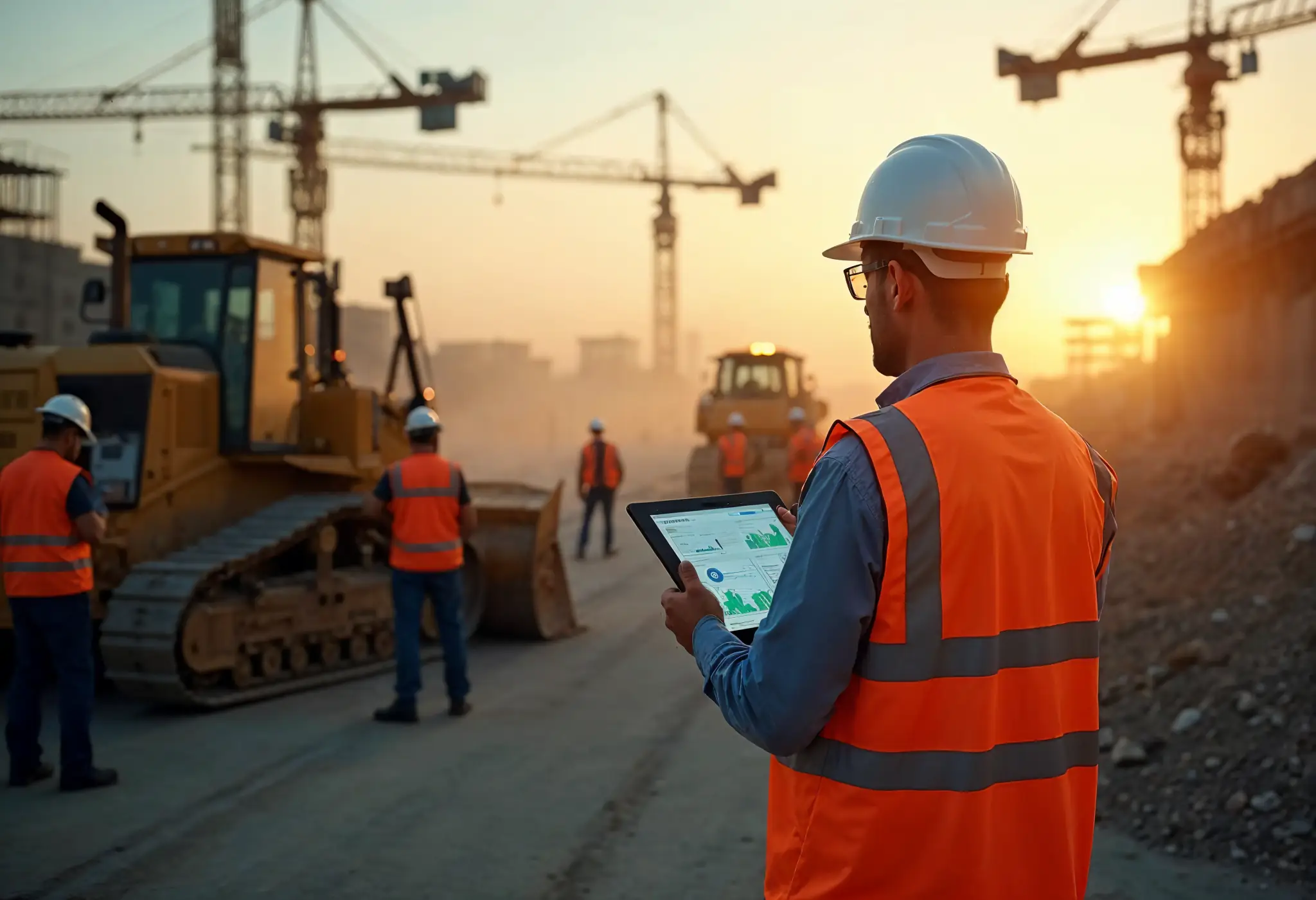
How to Implement a Construction Inventory Management System for Equipment Efficiency
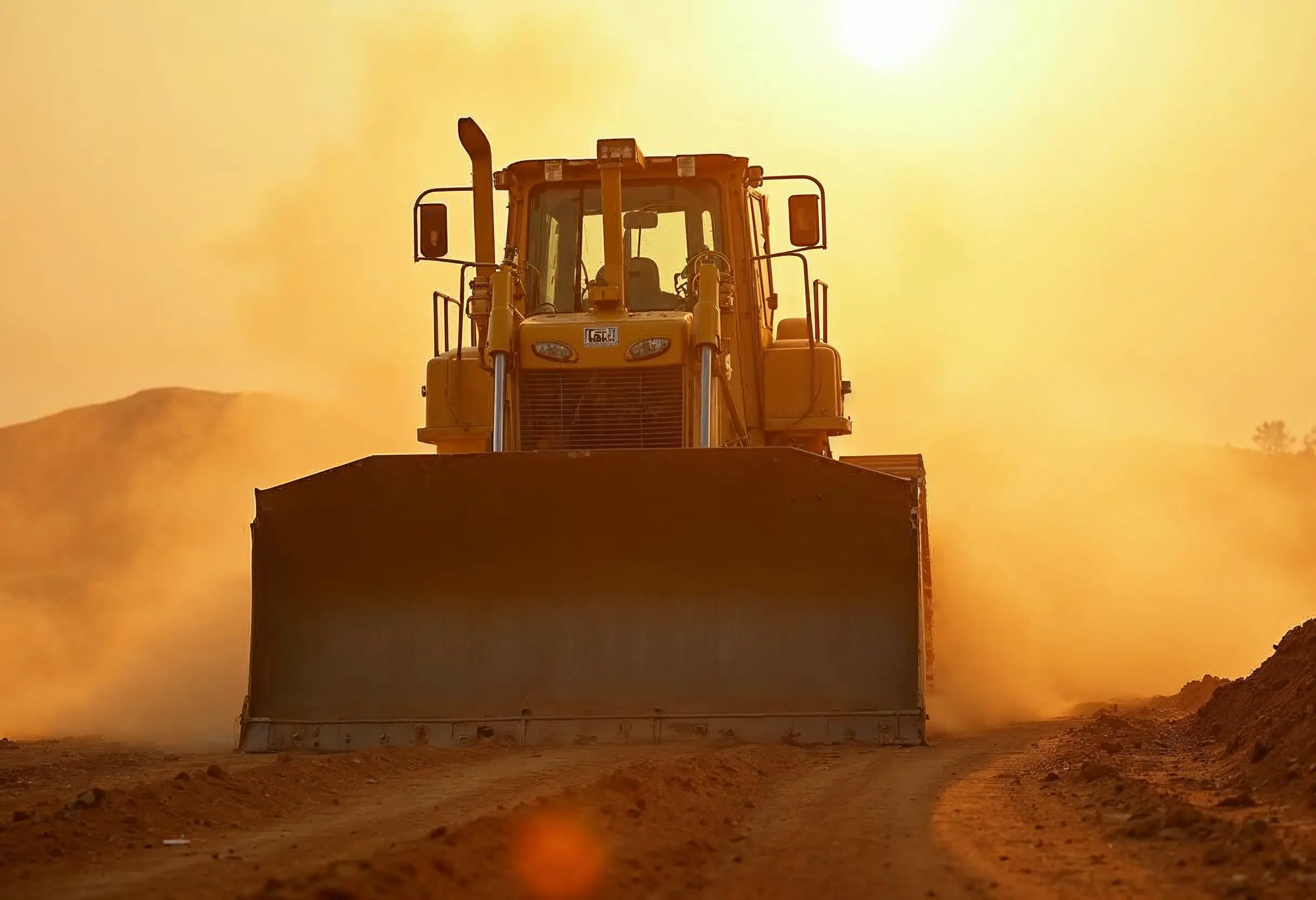
How to Extend Equipment Life Expectancy with Regular Maintenance
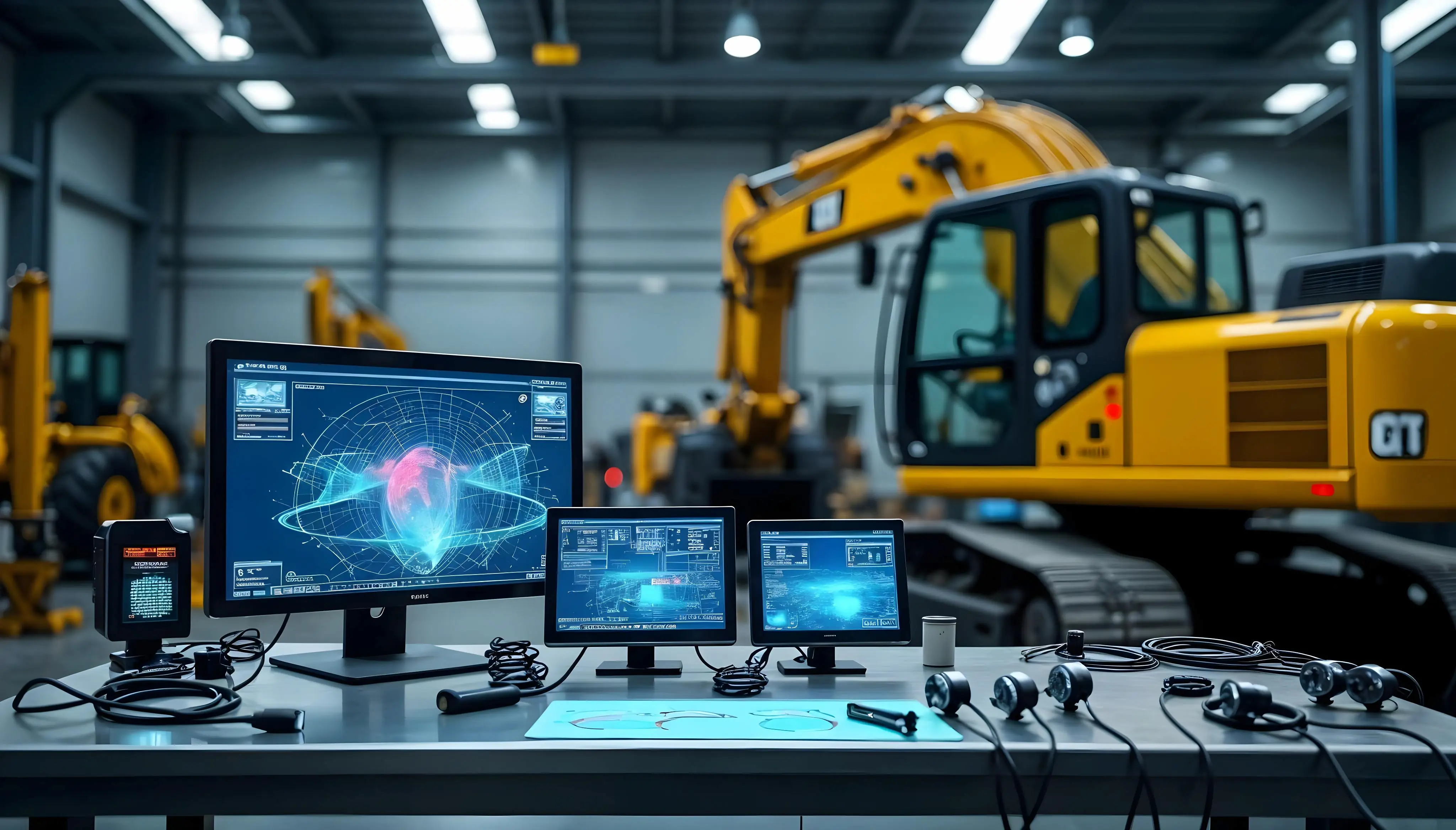
Advanced Heavy Equipment Diagnostic Tools: Ensuring Construction Machinery Quality
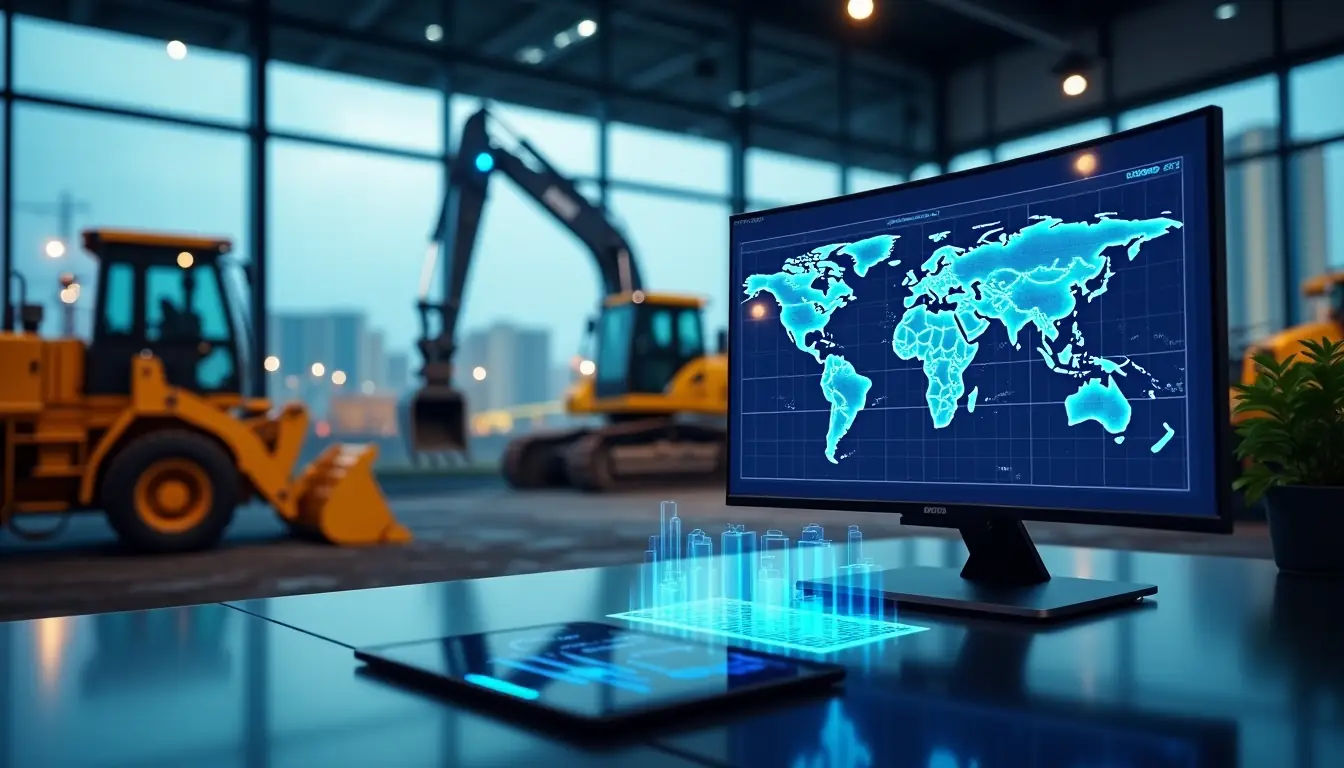
Essential Features Your Construction Equipment Inventory System Needs
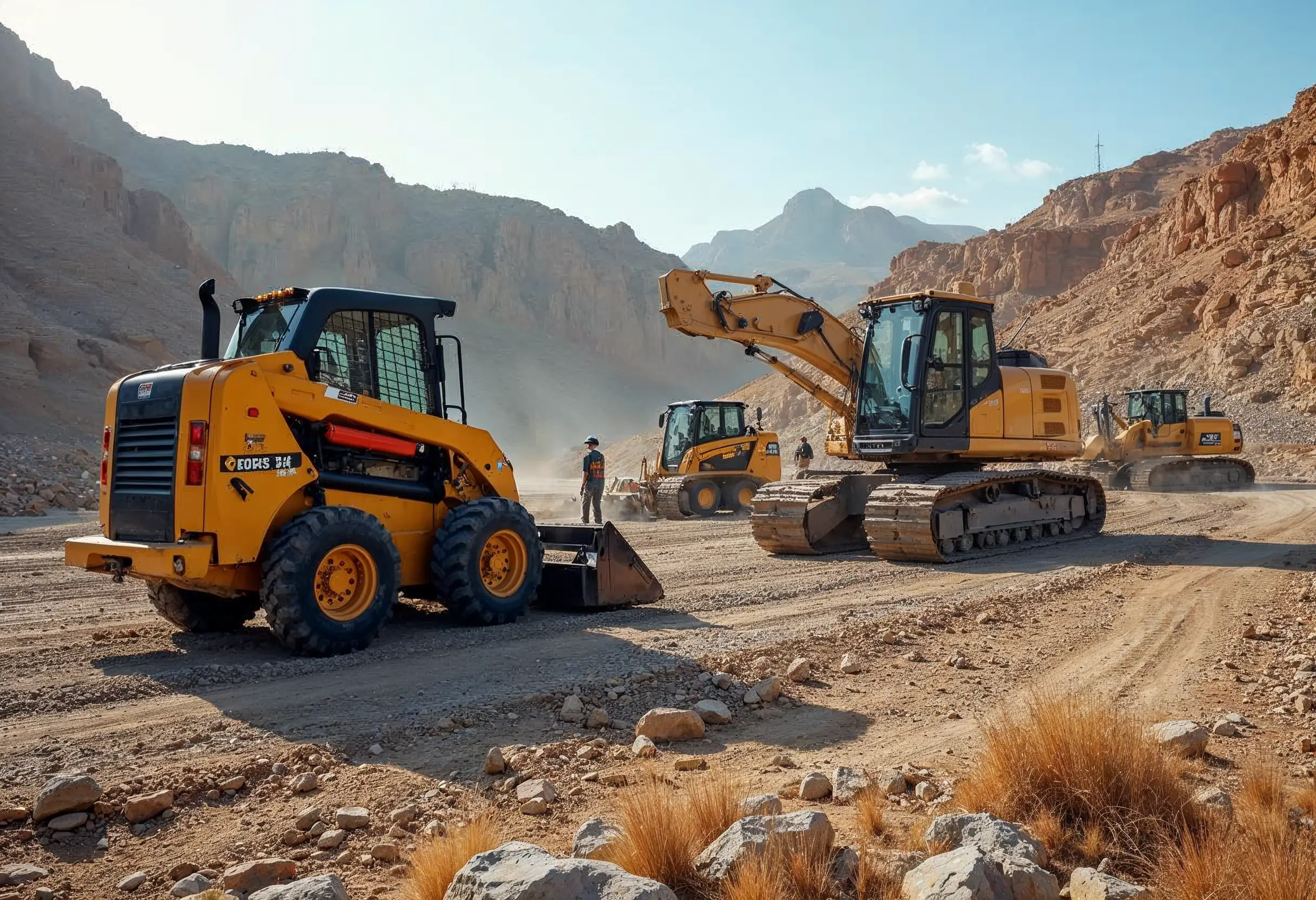
29 Quick Tips for Choosing Construction Equipment for Remote Locations
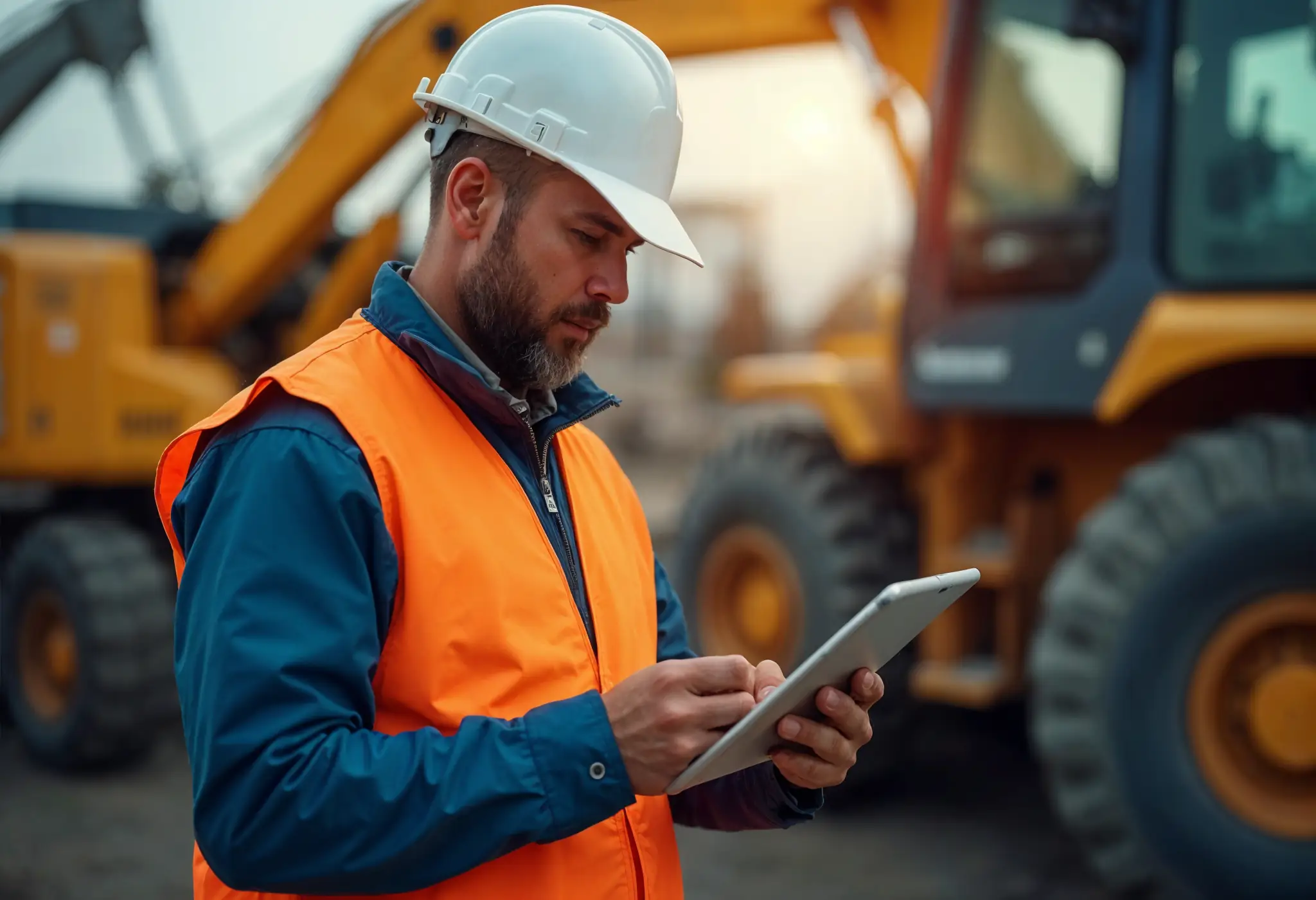
How to Select Construction Machinery with Optimal Equipment Maintenance in Mind
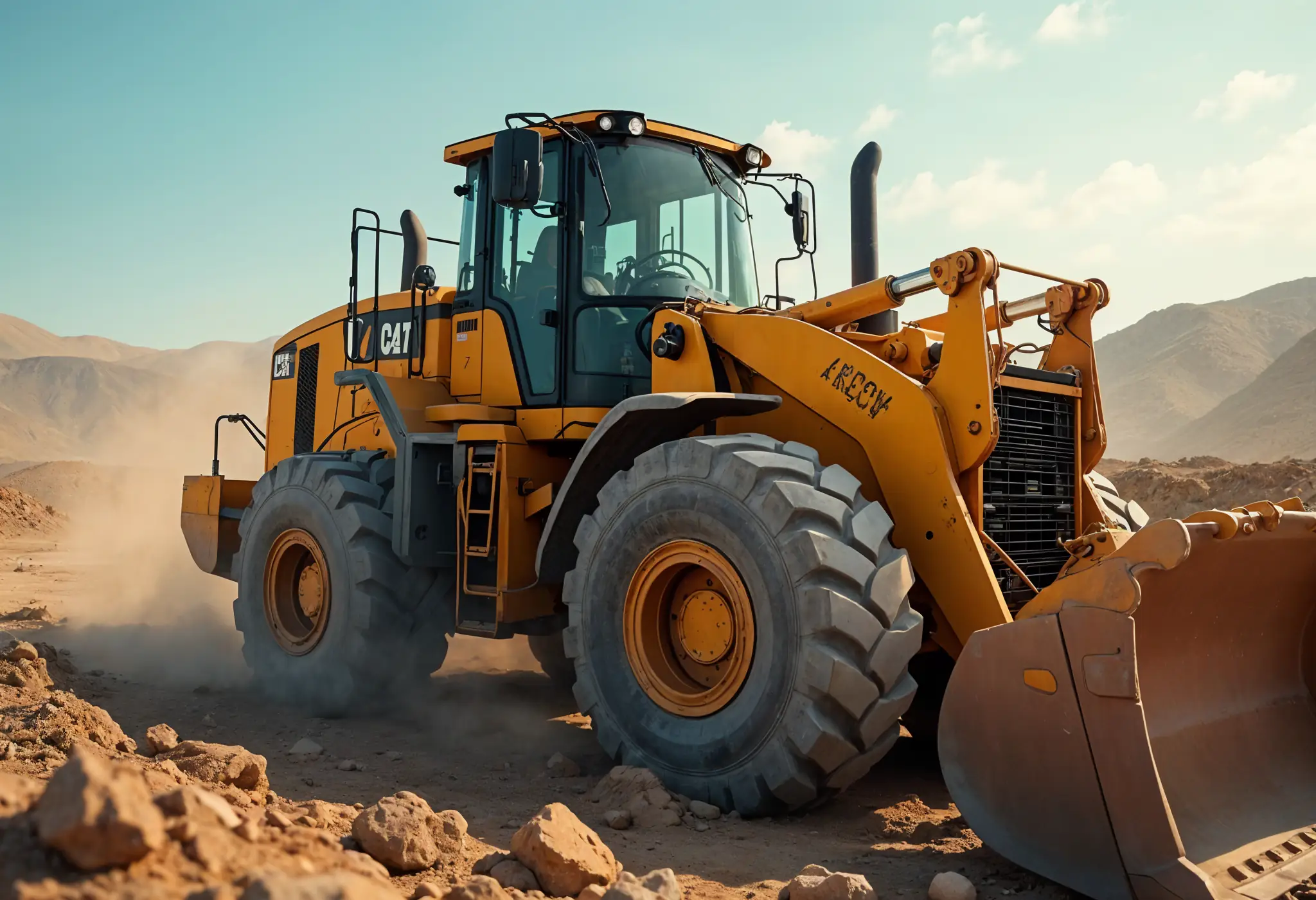
Top 25 Tips for Selecting Bulldozers for Construction Sites
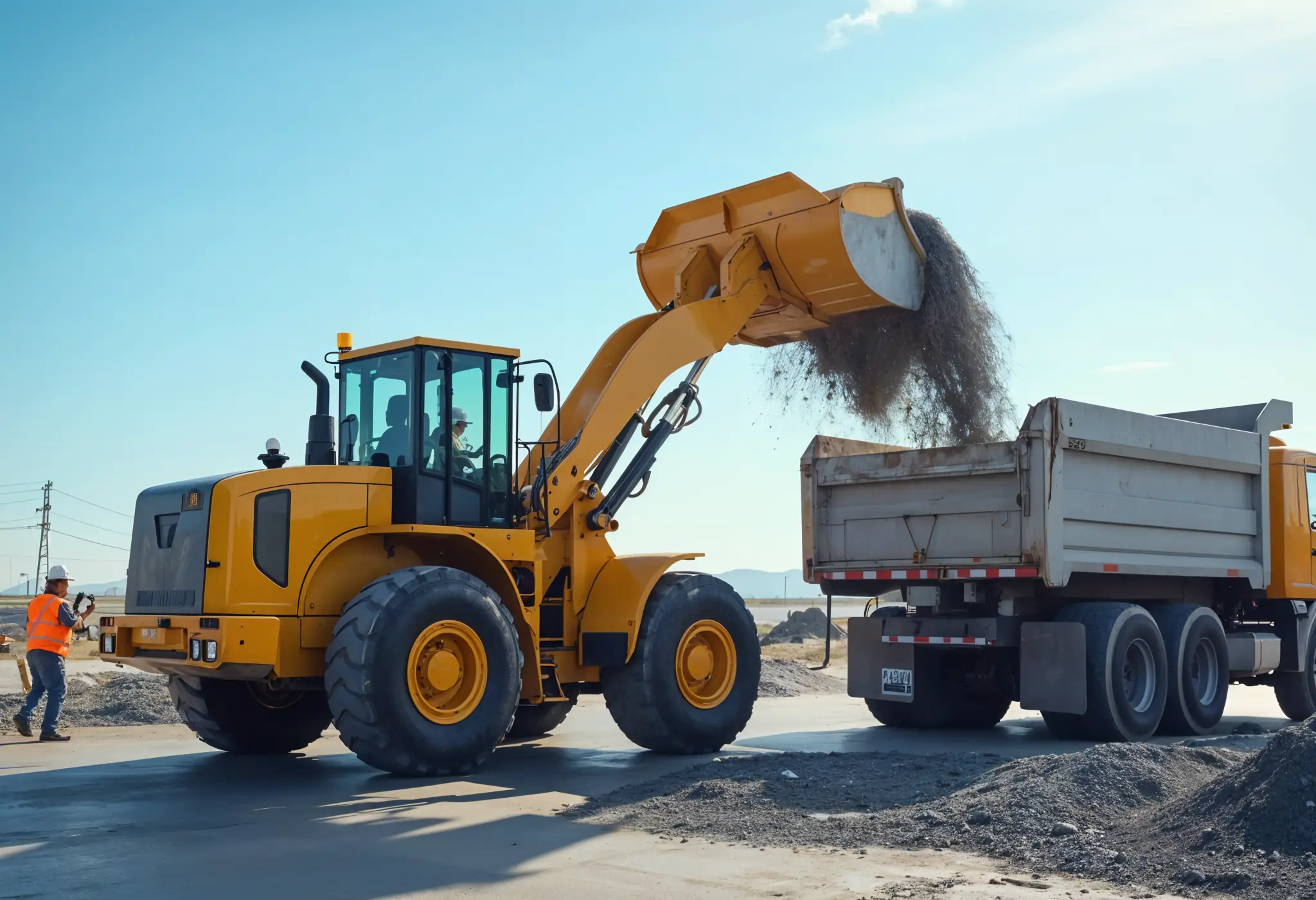
Which Construction Loader is Best for Your Project Needs?
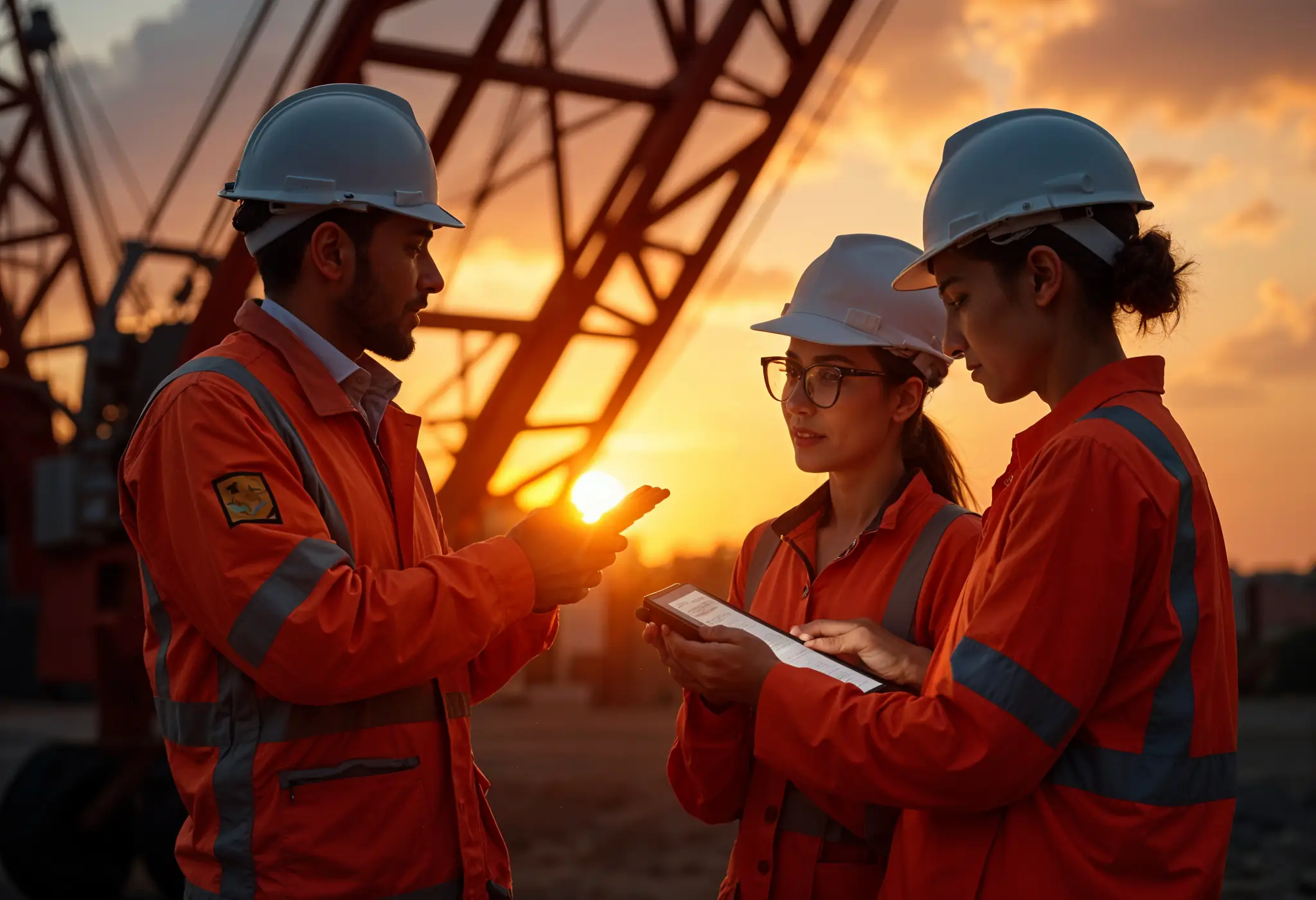
4 Key Steps to Form a Construction Machinery QC Team
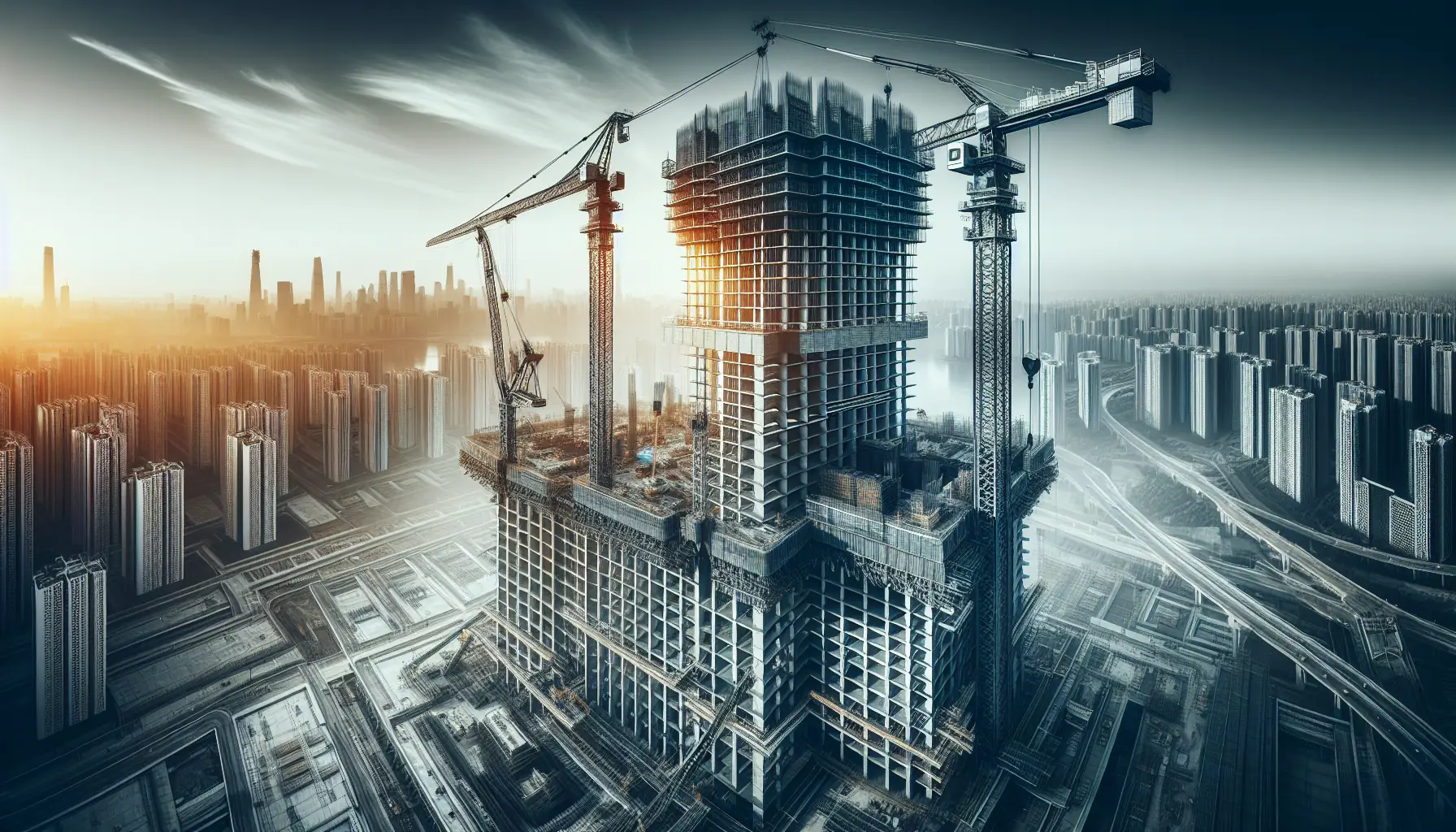
15 Essential Tips for Selecting the Perfect Crane for Construction
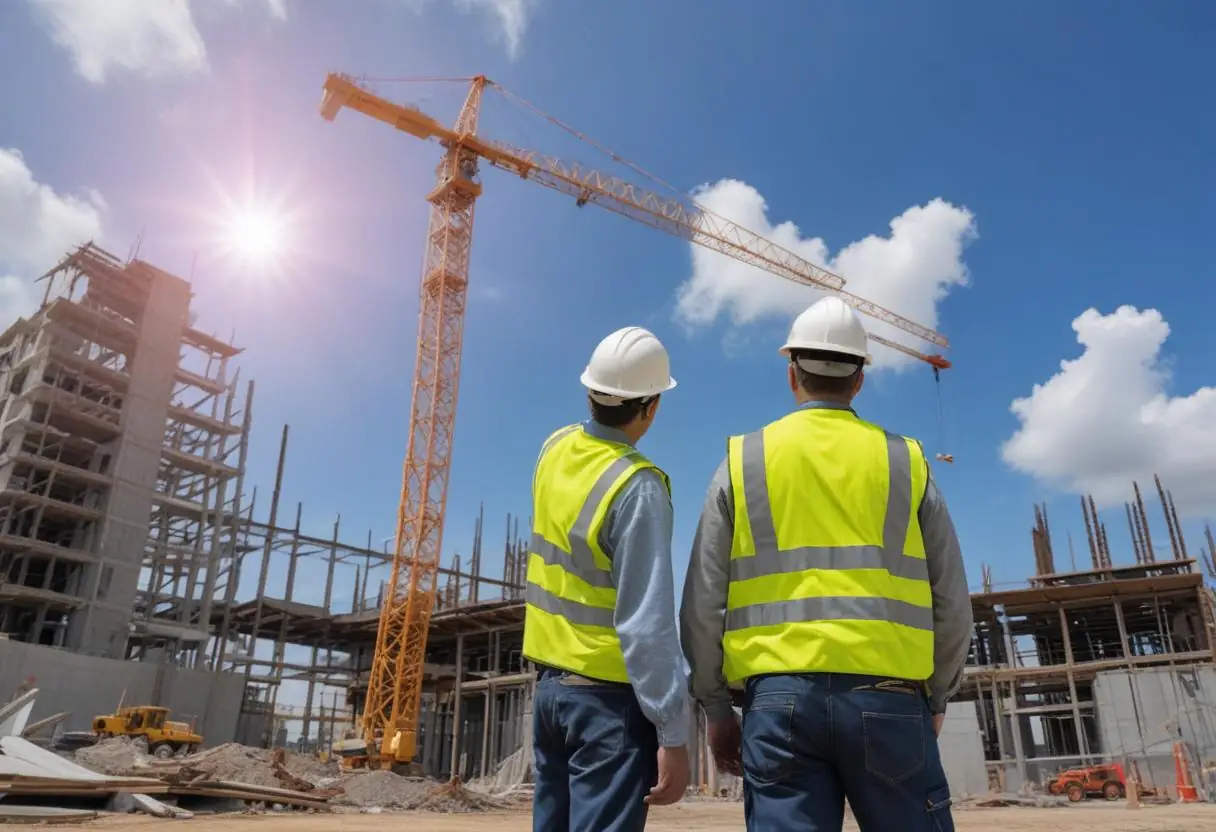
Maximize Savings: Multi-Purpose Construction Machinery for Lower Costs
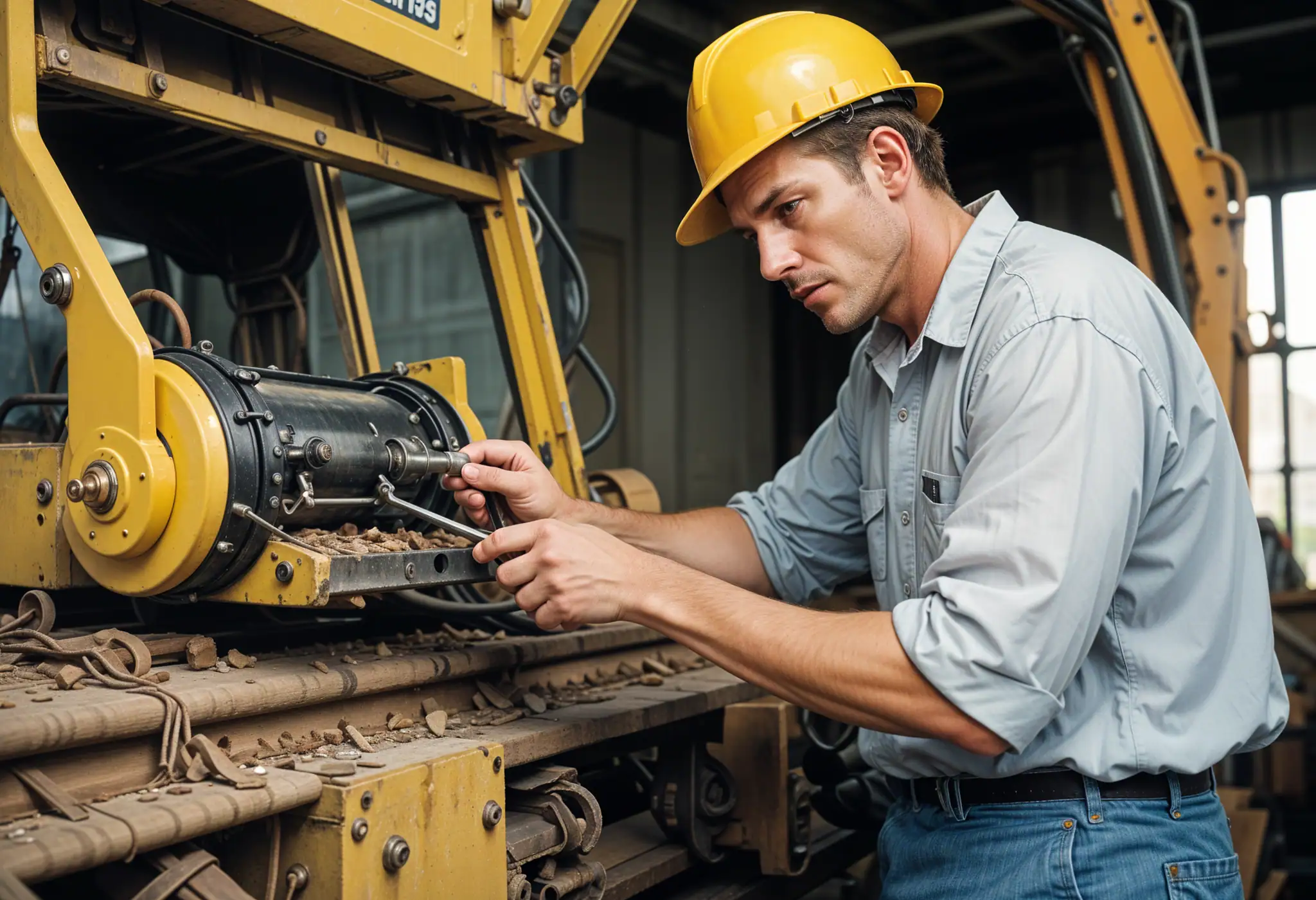
Affordable Heavy Equipment Parts: A Sourcing Guide
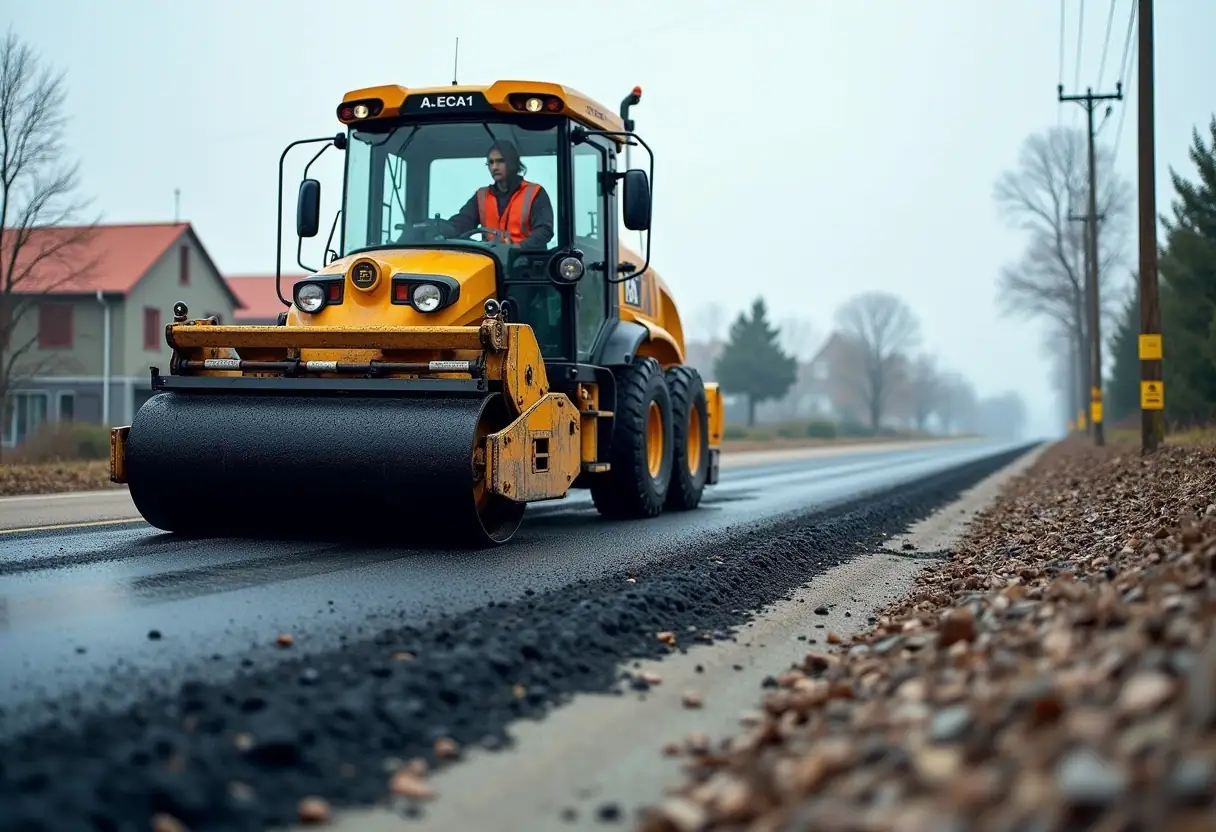
Choosing the Right Road Construction Equipment: A Complete Guide
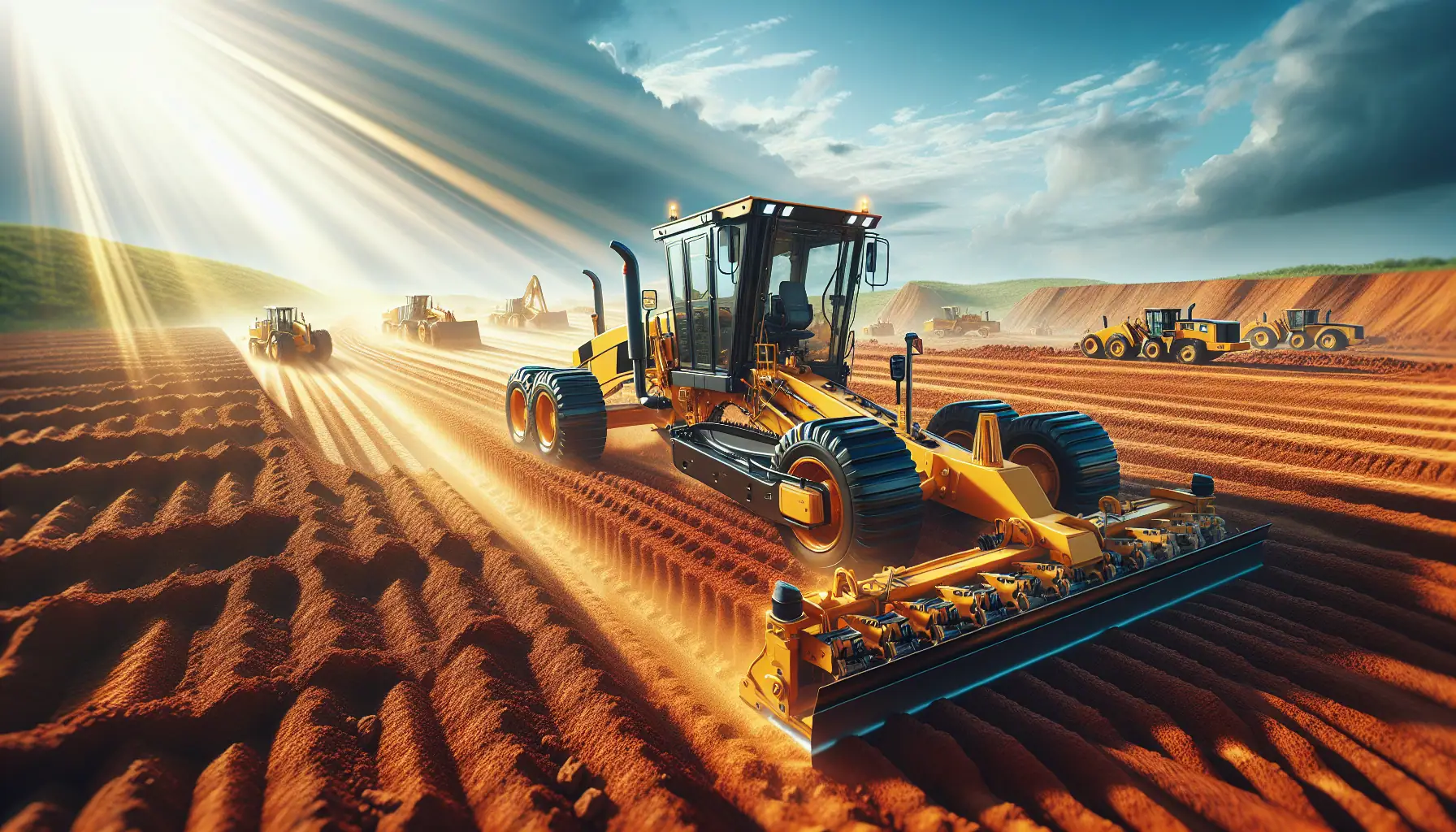
Motor Graders: Key Elements to Consider for Optimal Selection
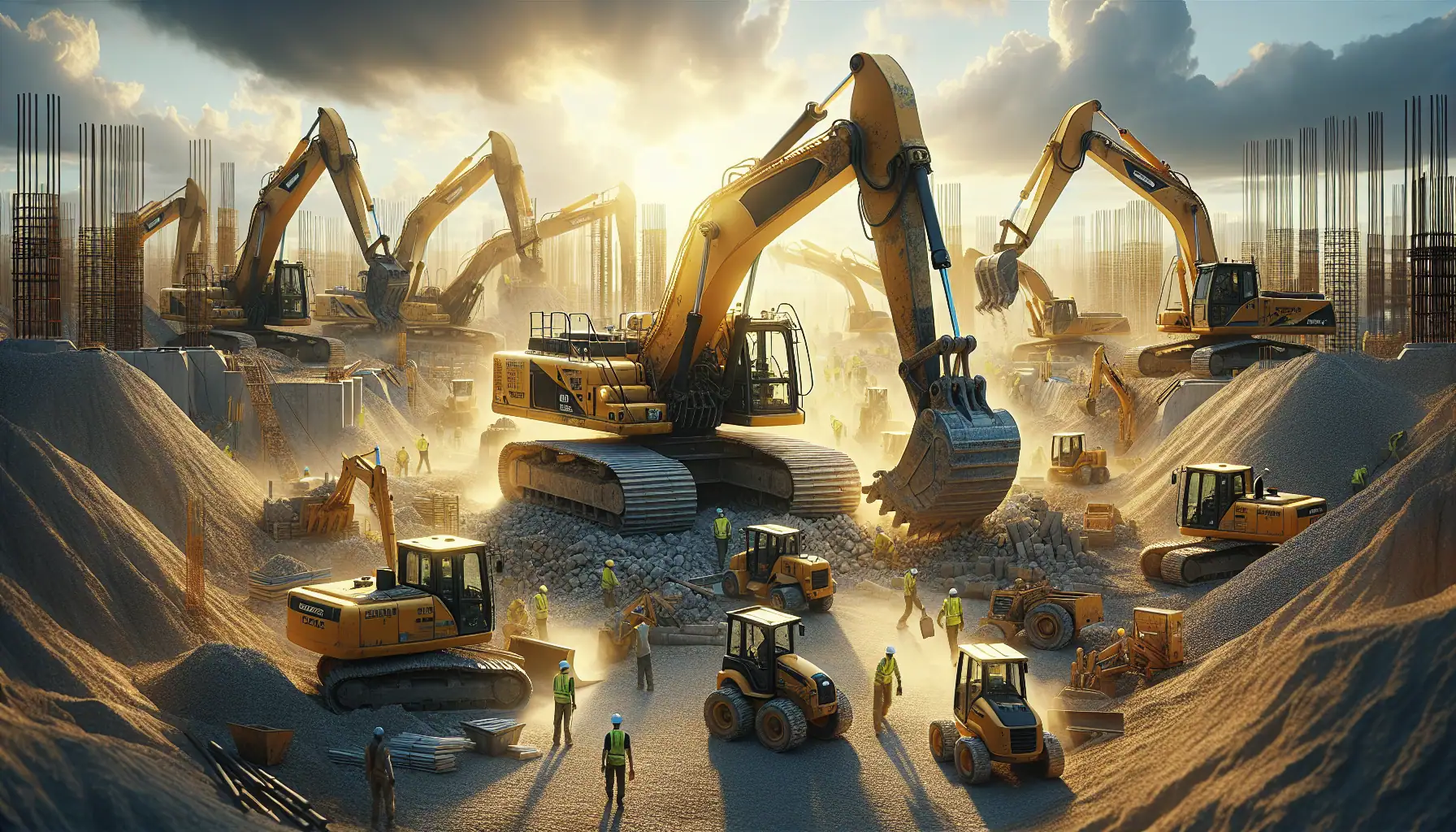
A Detailed Guide to Choosing Excavators for Construction Work
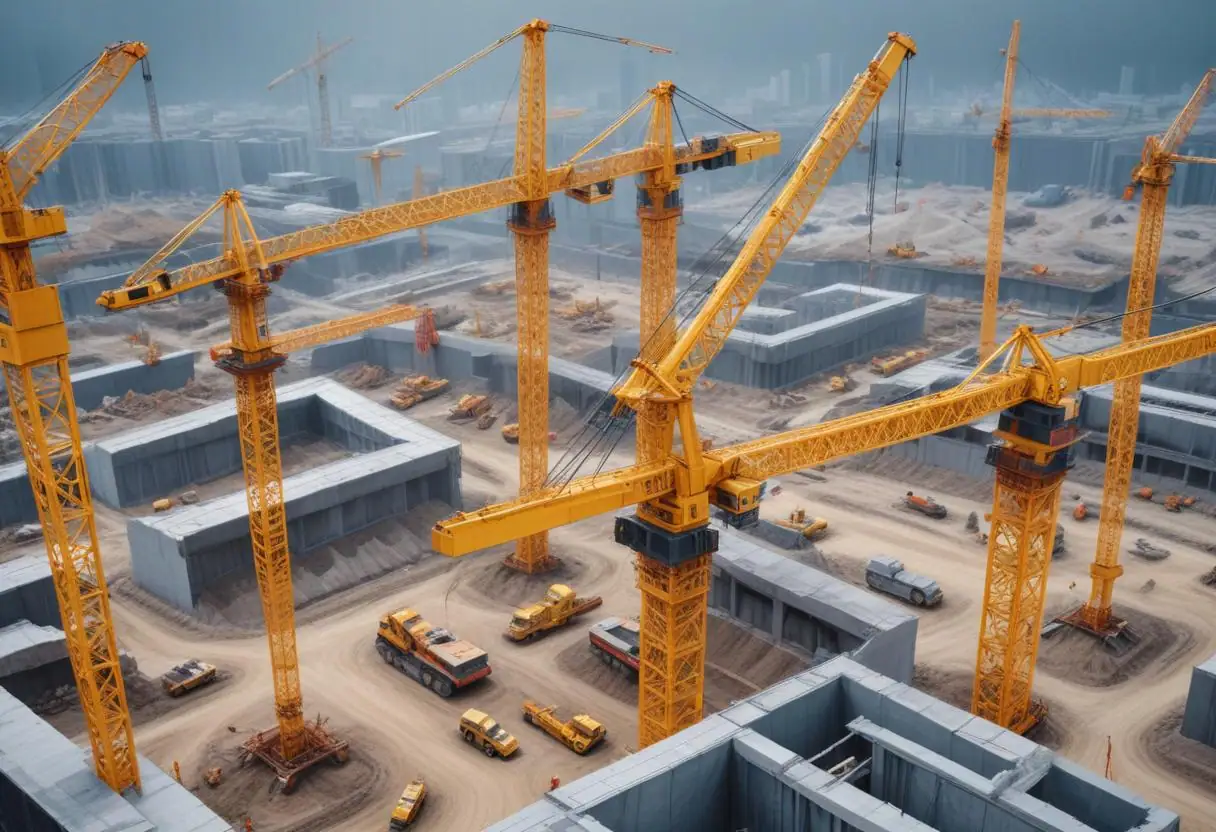
Top Tips for Choosing Cranes for Construction Projects
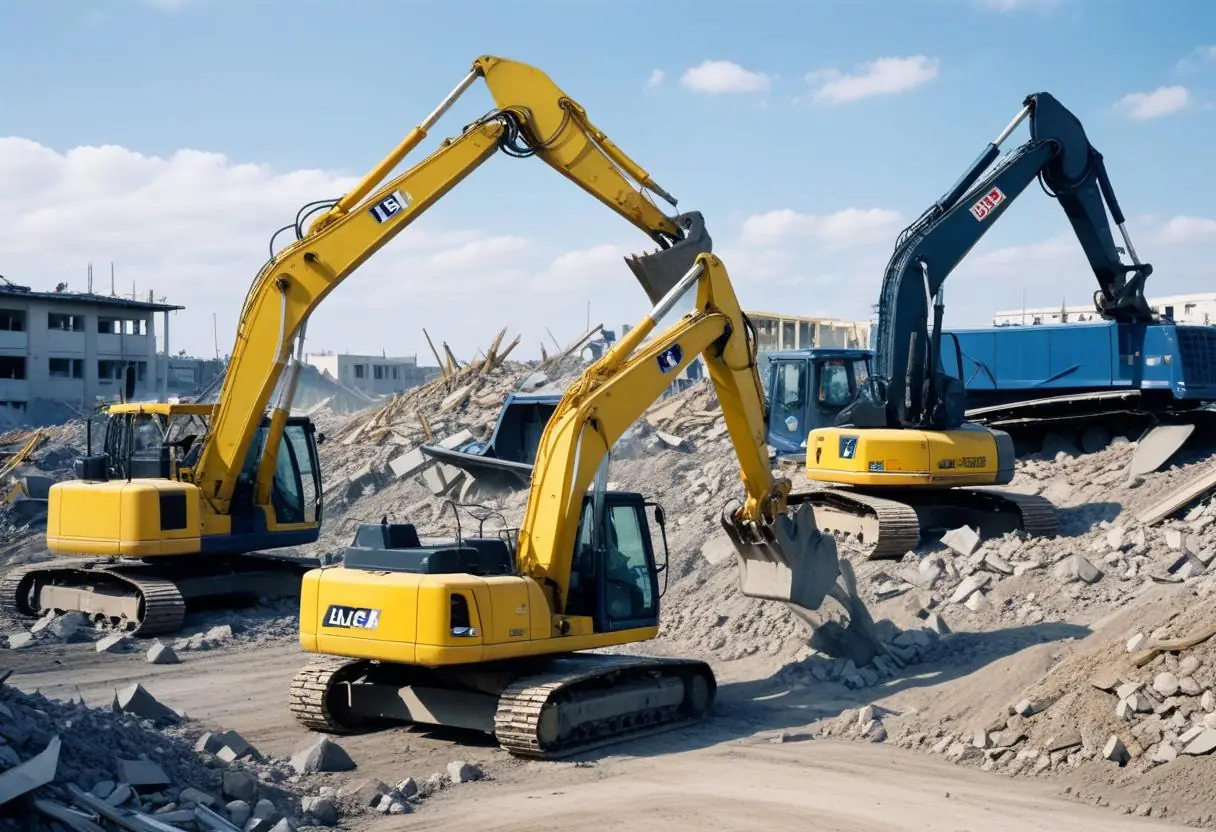
5 Top-Rated Demolition Machines for Construction Professionals
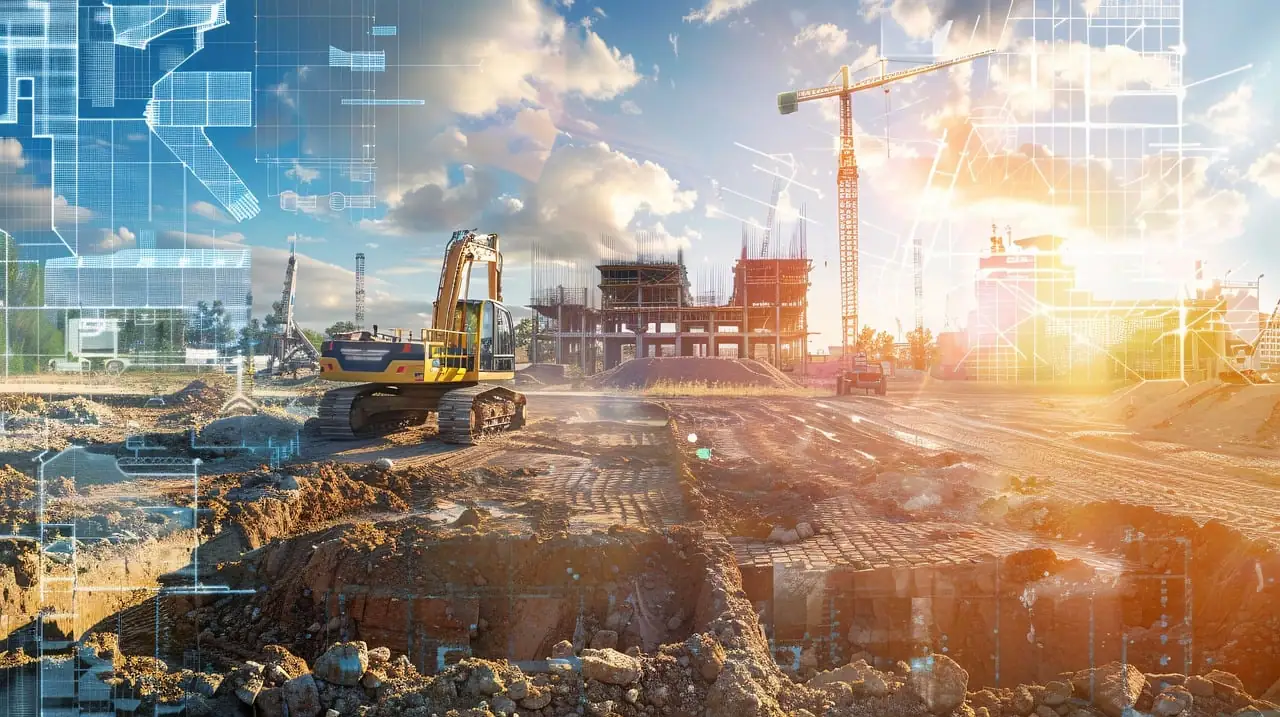
Expert Tips on Choosing Earthmoving Equipment for Large Projects
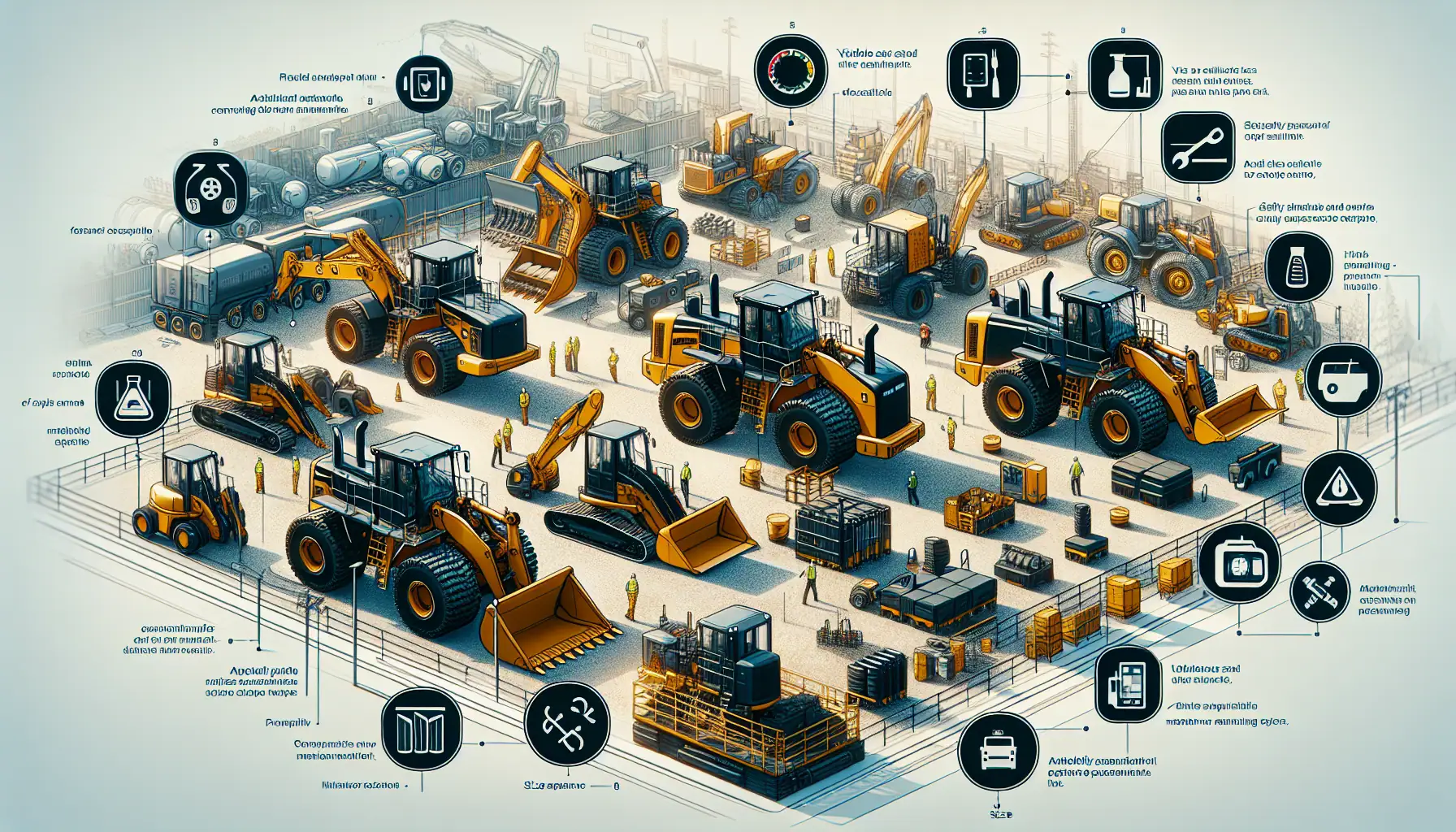
Top Functional Criteria for Selecting Heavy Construction Equipment
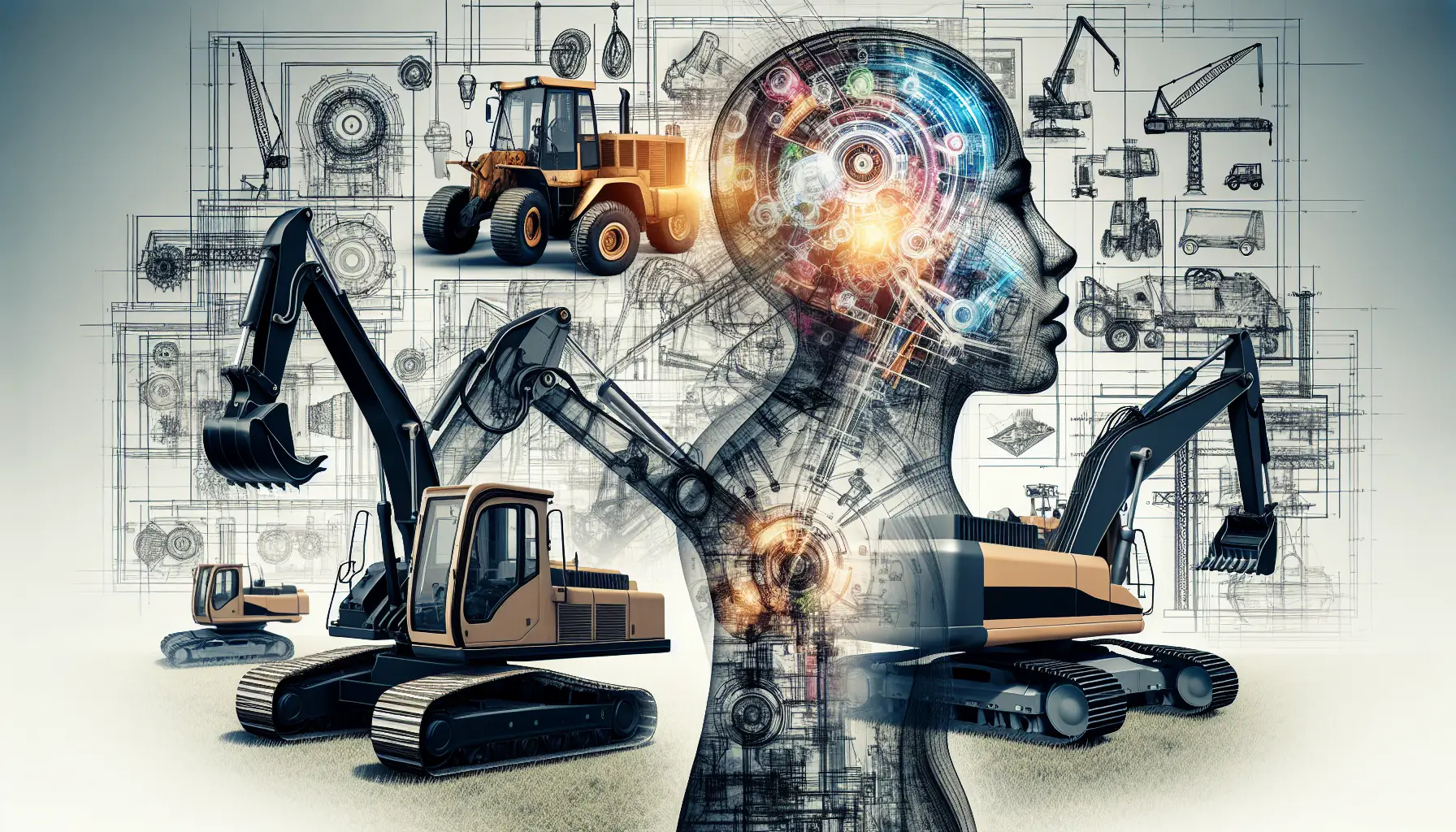
Construction Machinery: Detailed Guide to Equipment Specifications
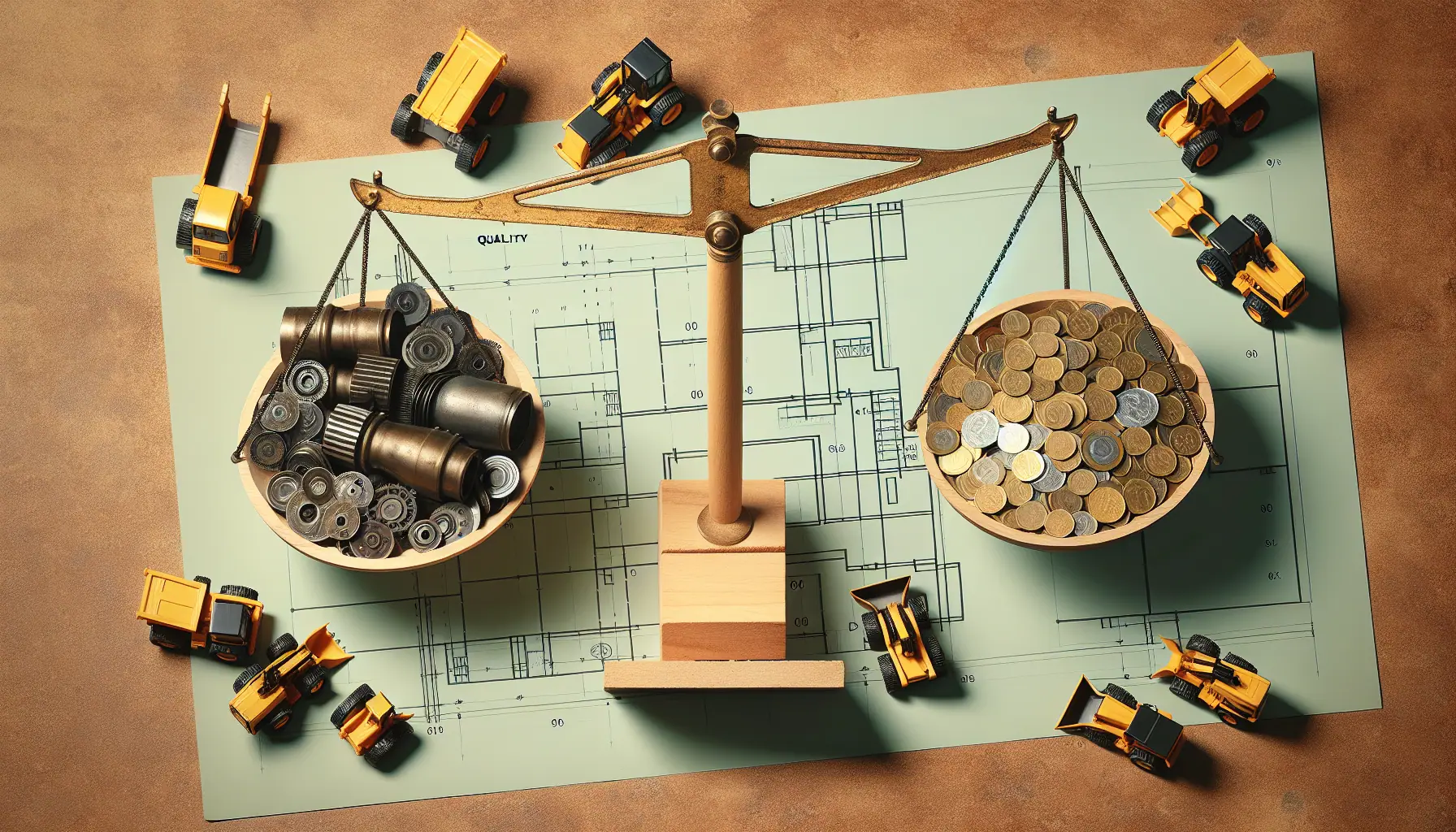
Heavy Machinery Prices: Key Factors in Cost and Quality Balance
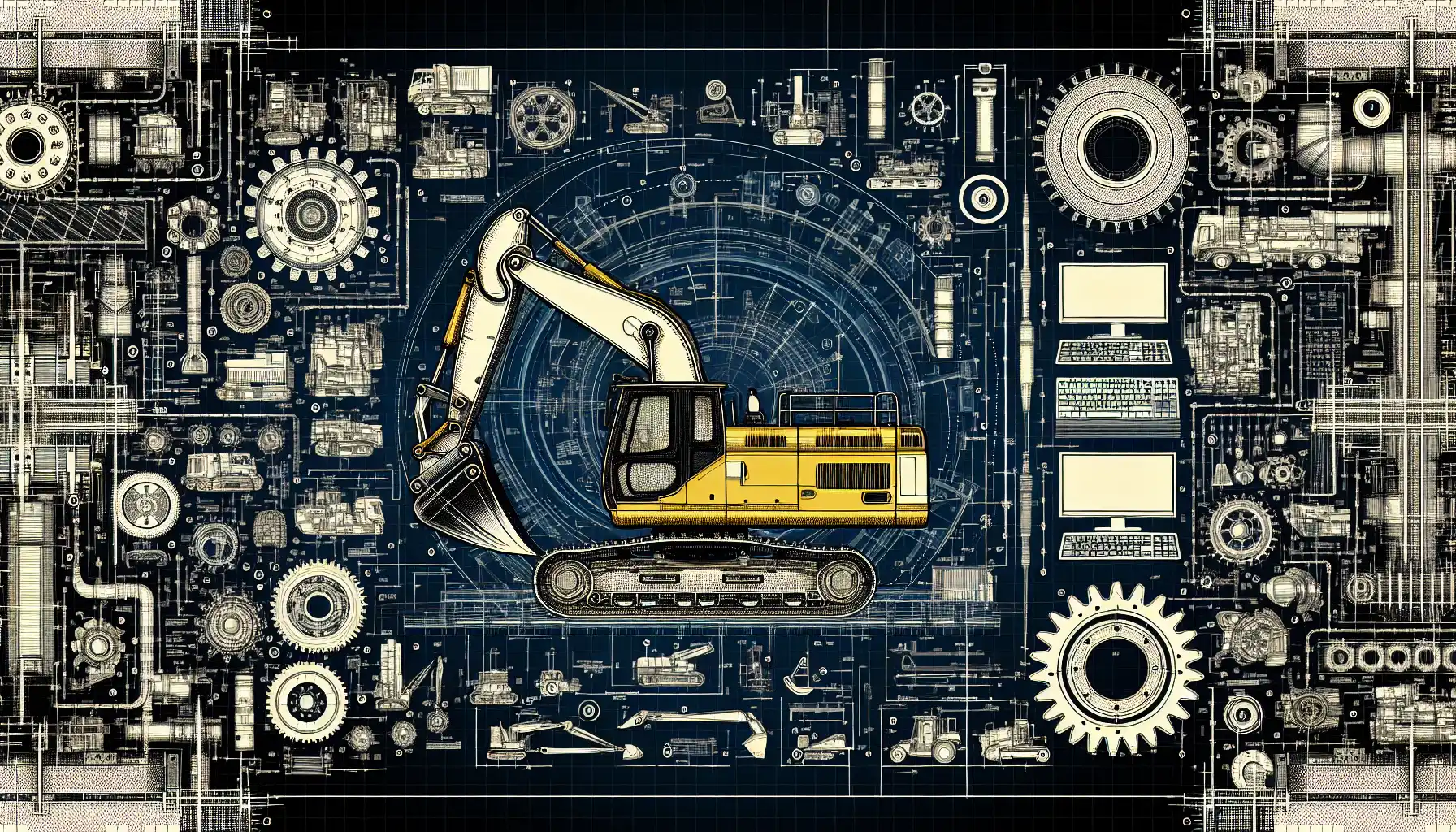
Best Construction Heavy Equipment Brands: Pros and Cons
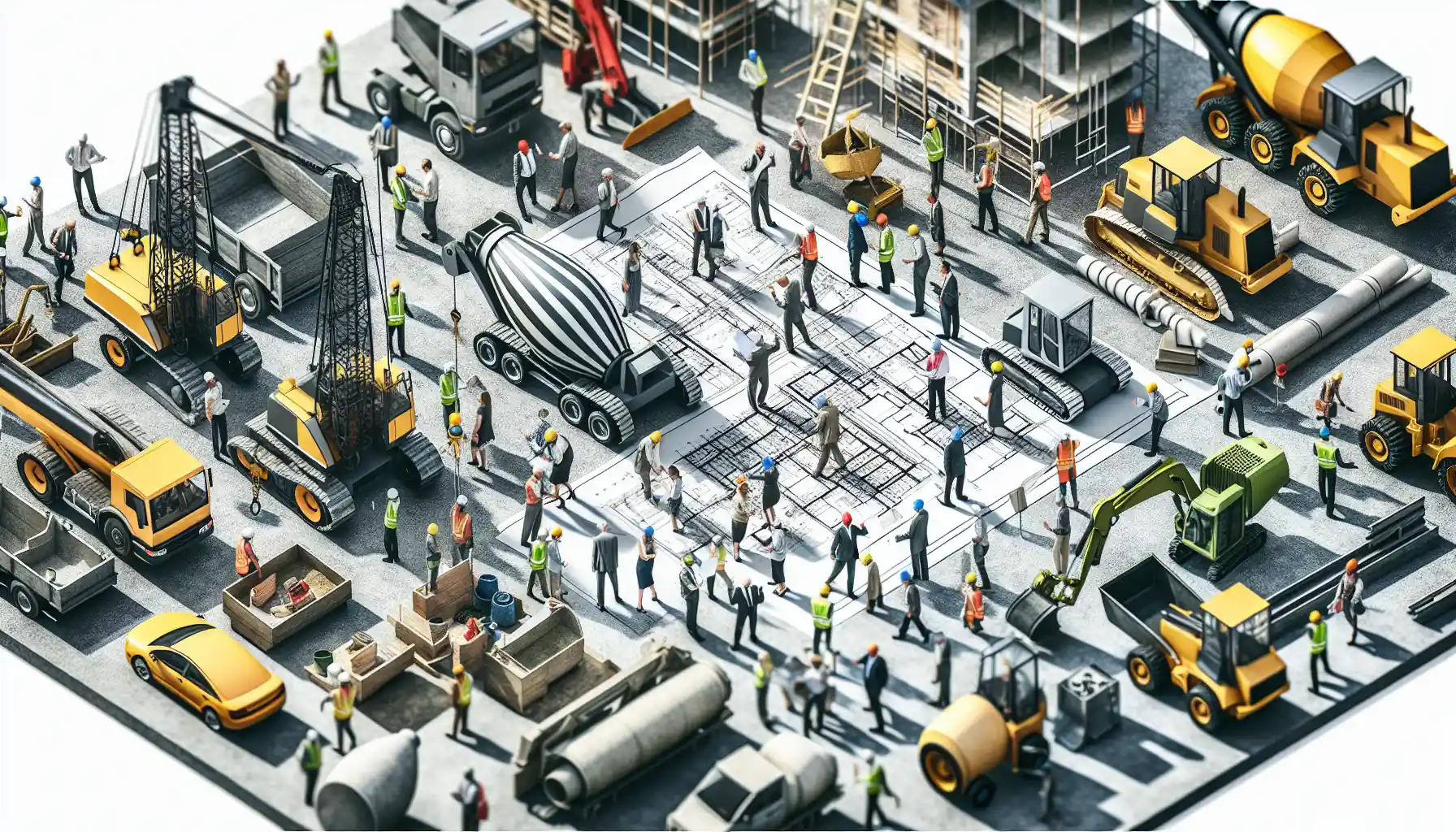
Construction Site Equipment: How to Determine Your Requirements
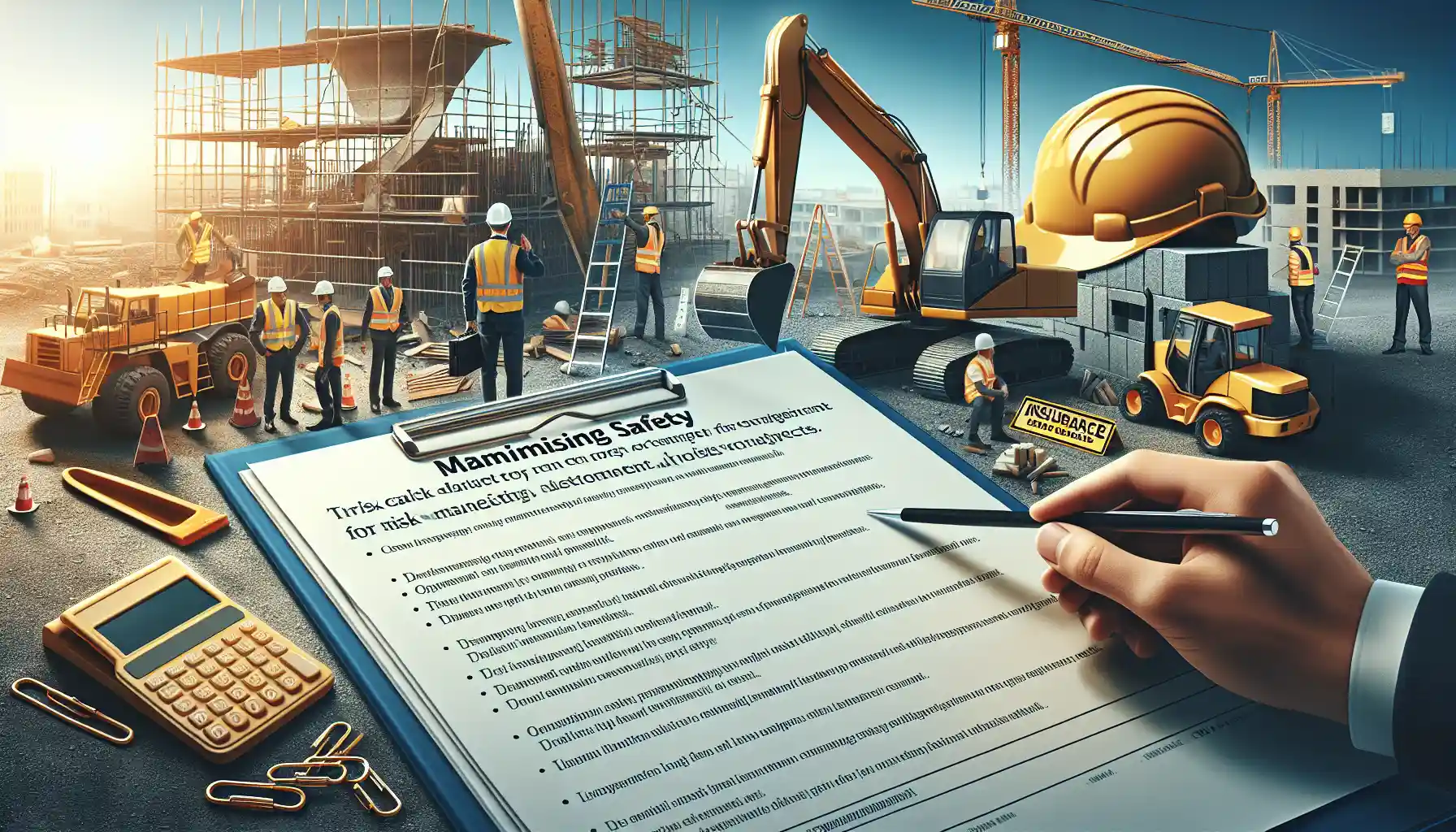
Maximizing Safety: Risk Management for Construction Projects
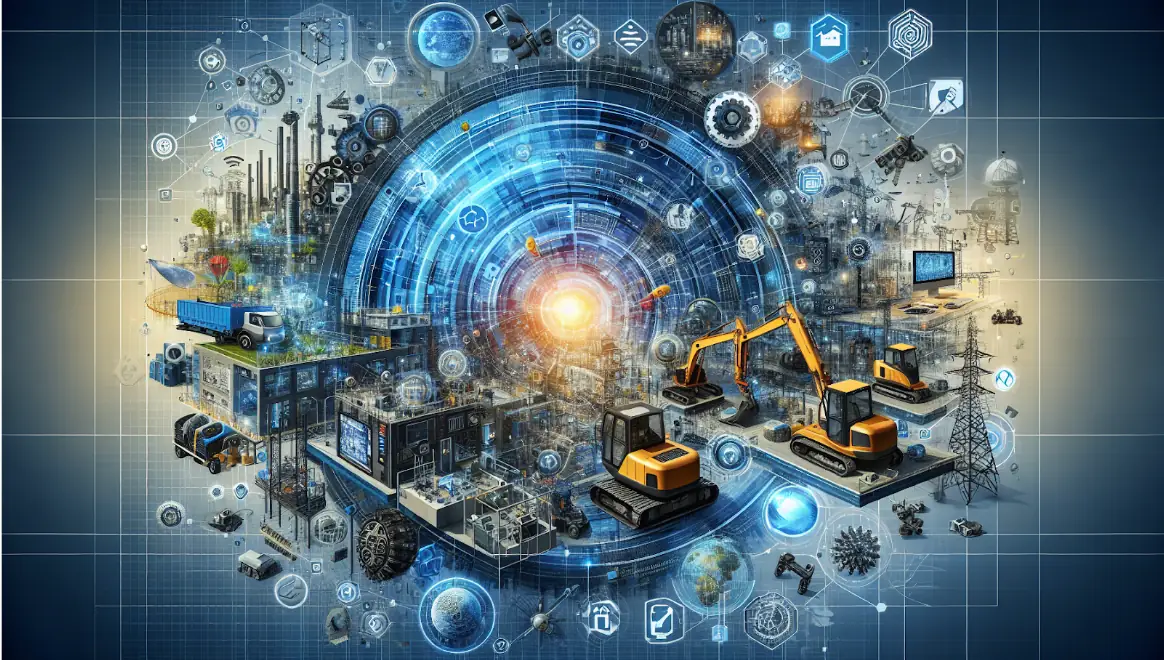
Innovations in Construction: Transforming Machinery and Equipment
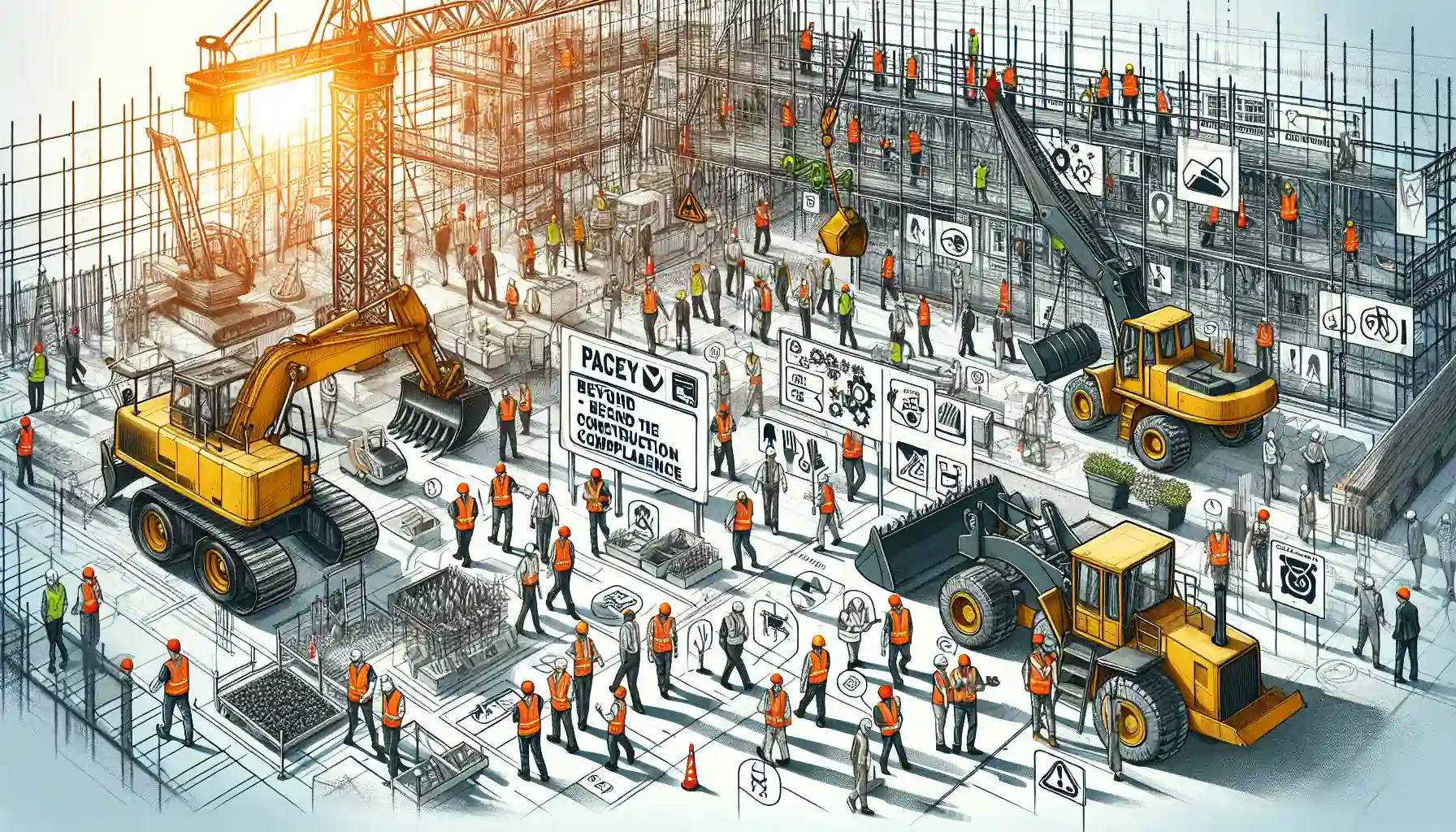
Heavy Equipment Safety: Beyond the Basics in Construction Compliance
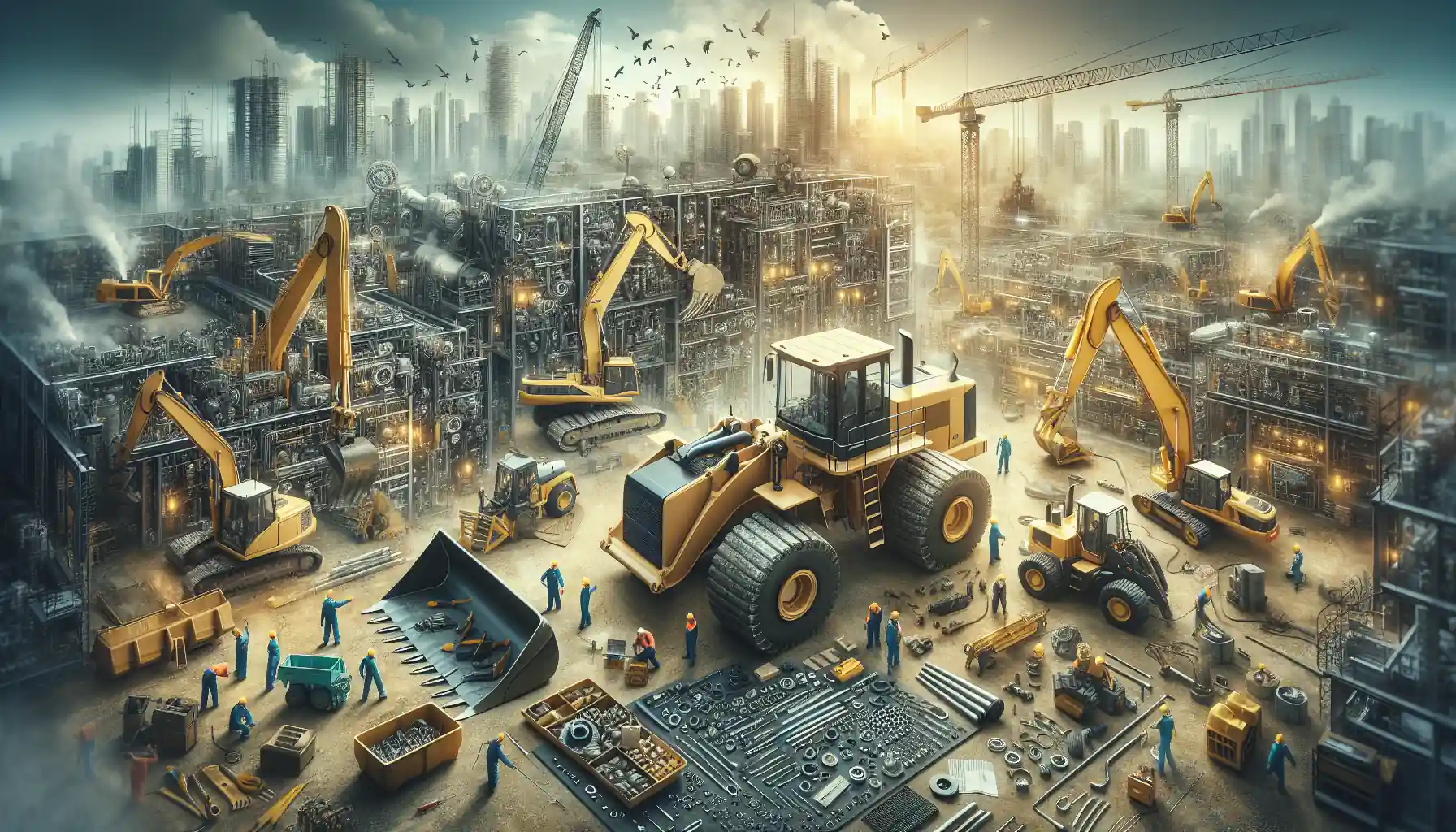
The Essential Handbook for Construction Equipment Repair and Maintenance
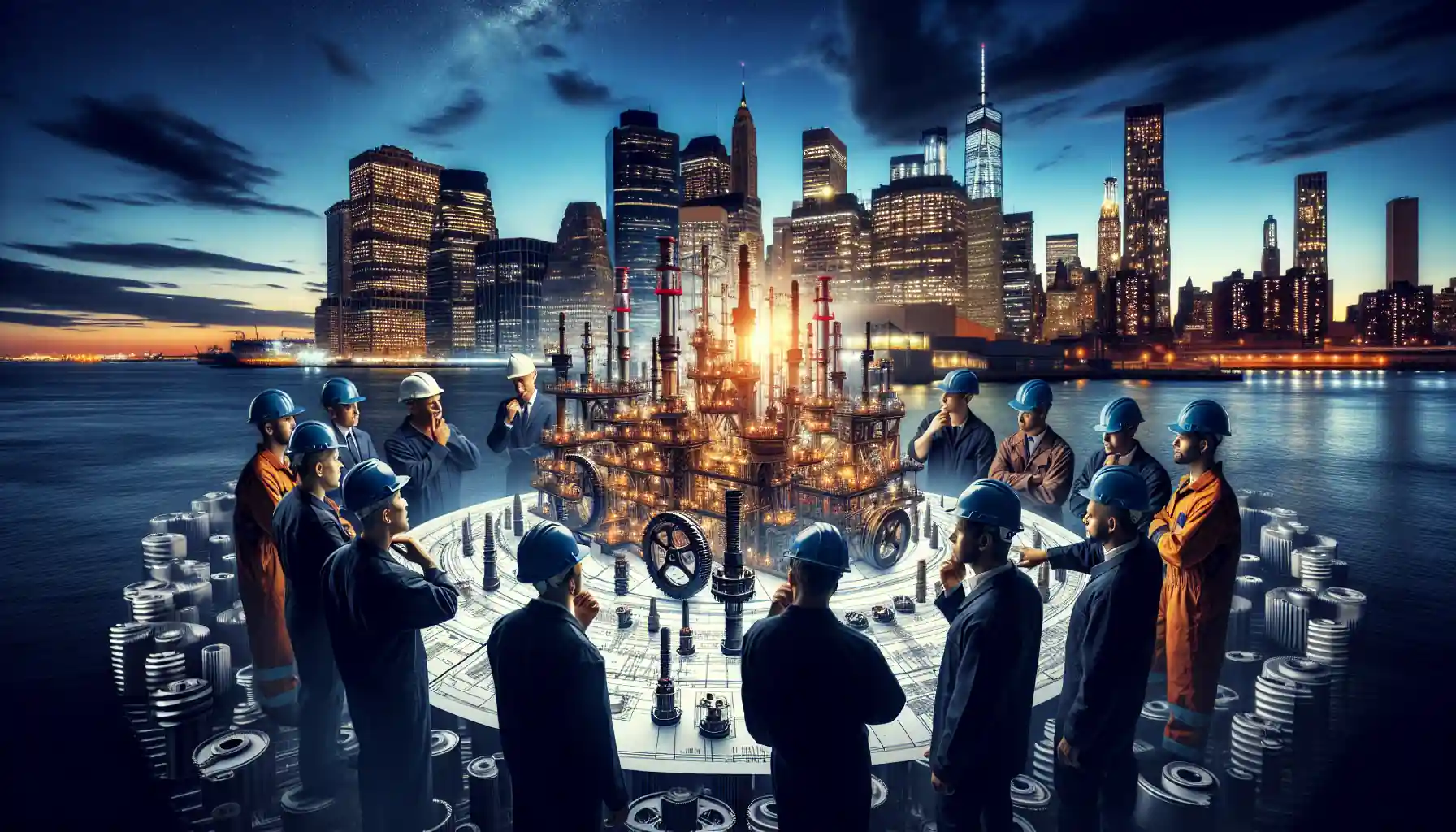
How to Efficiently Source Oil and Gas Machinery Parts in NYC
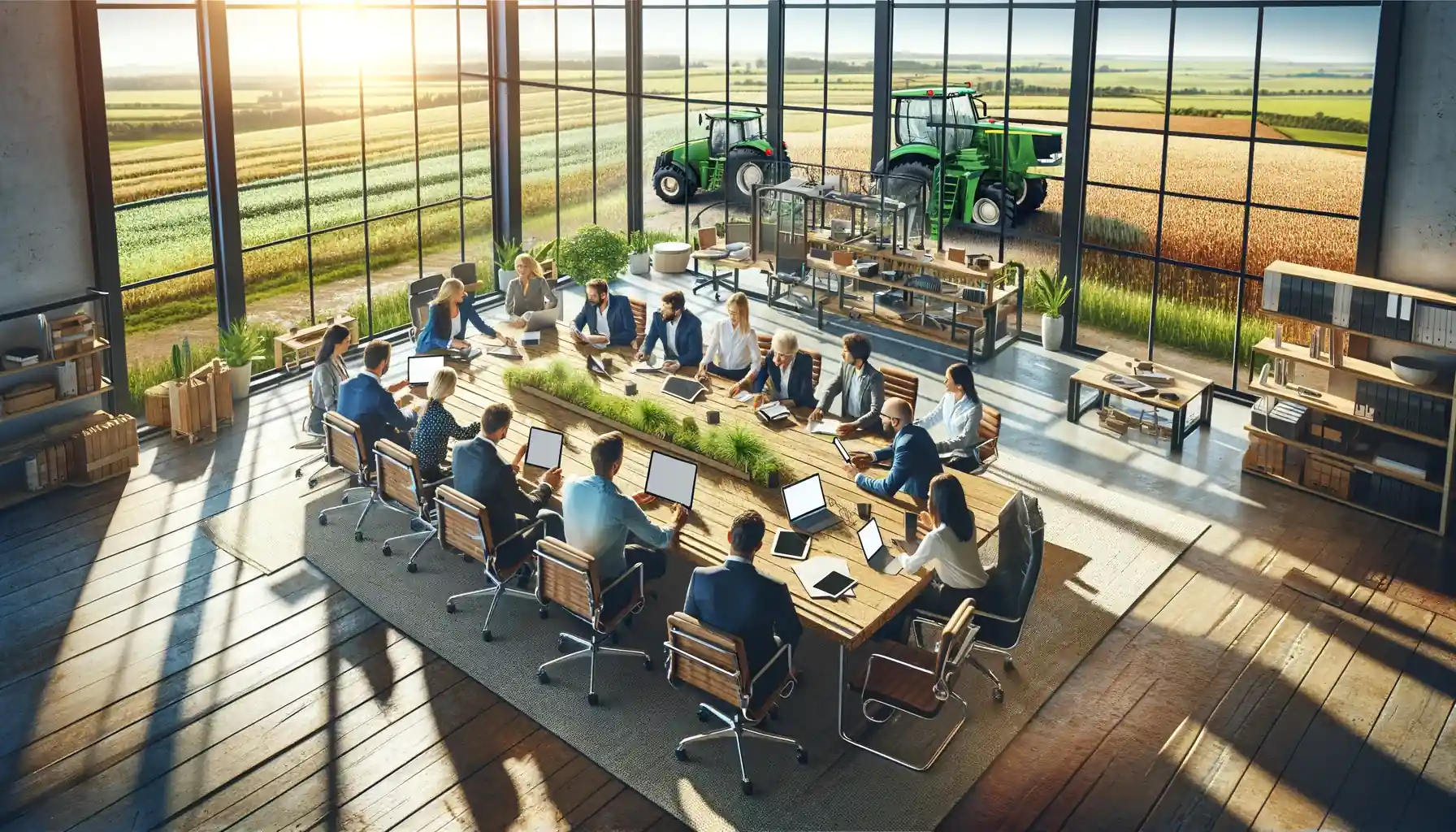
Essential Guide to Sourcing Agriculture Equipment Parts
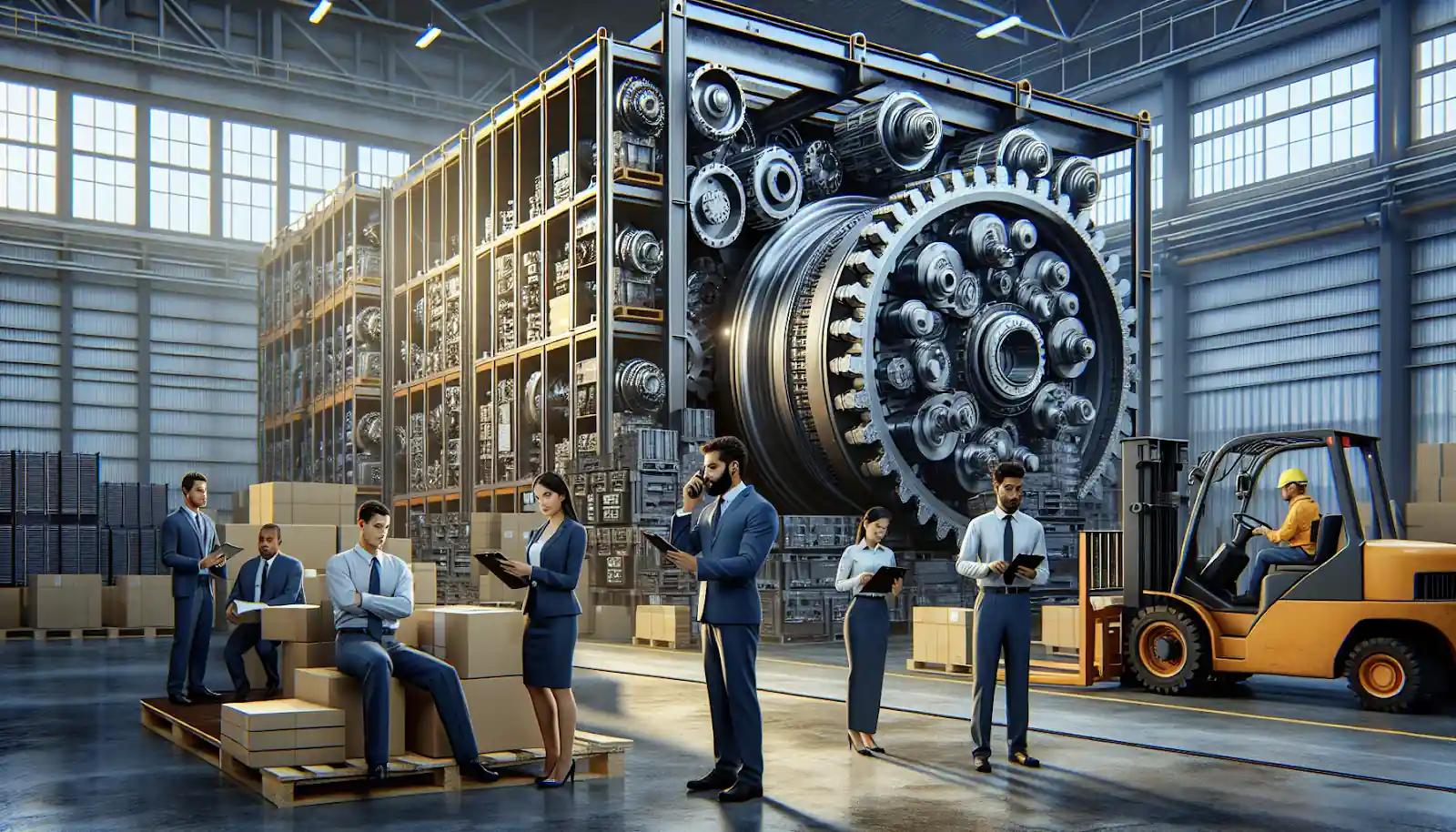
How to Source Mining Machinery Parts: Tips and Strategies
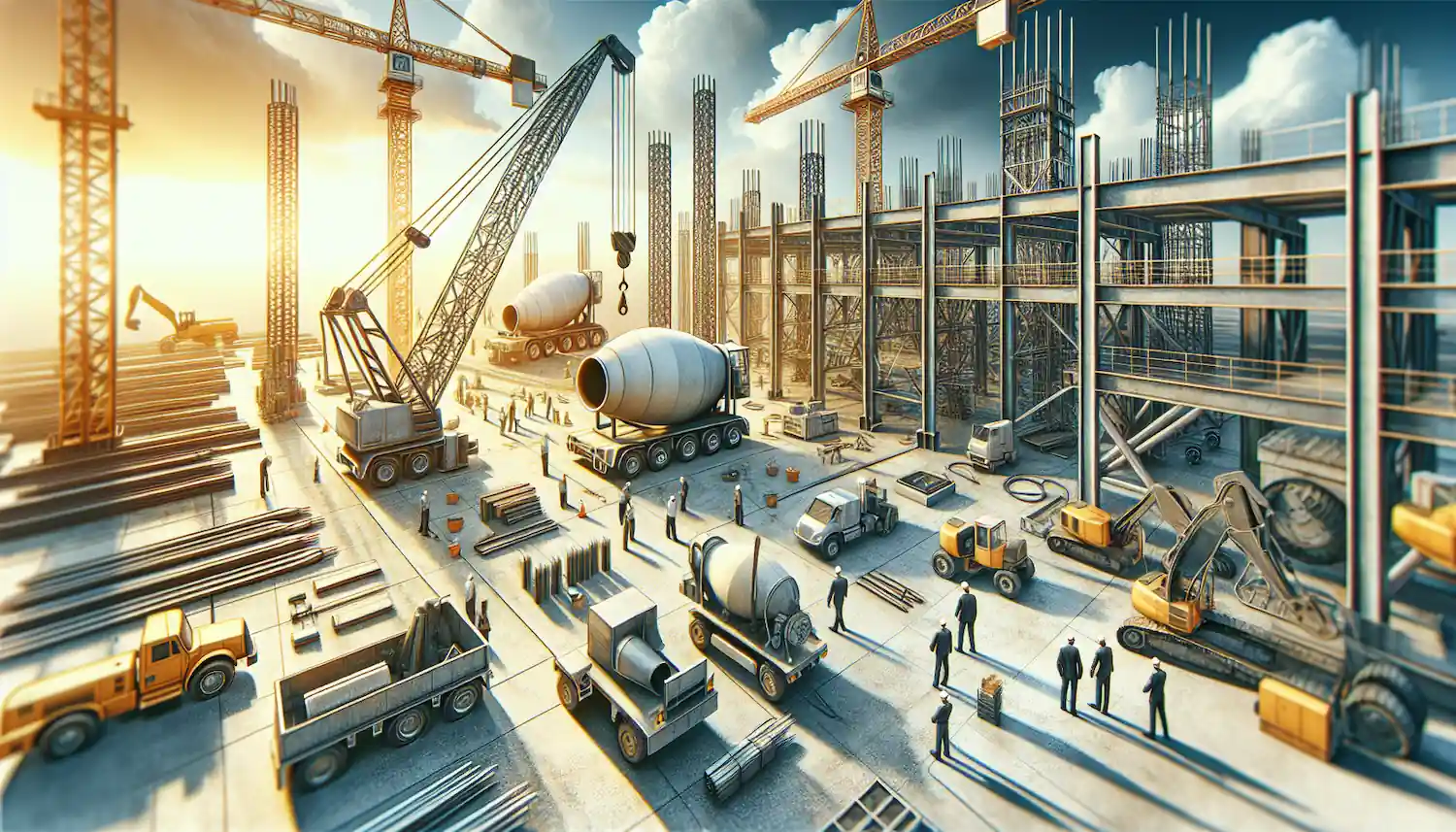