Advanced Heavy Equipment Diagnostic Tools: Ensuring Construction Machinery Quality
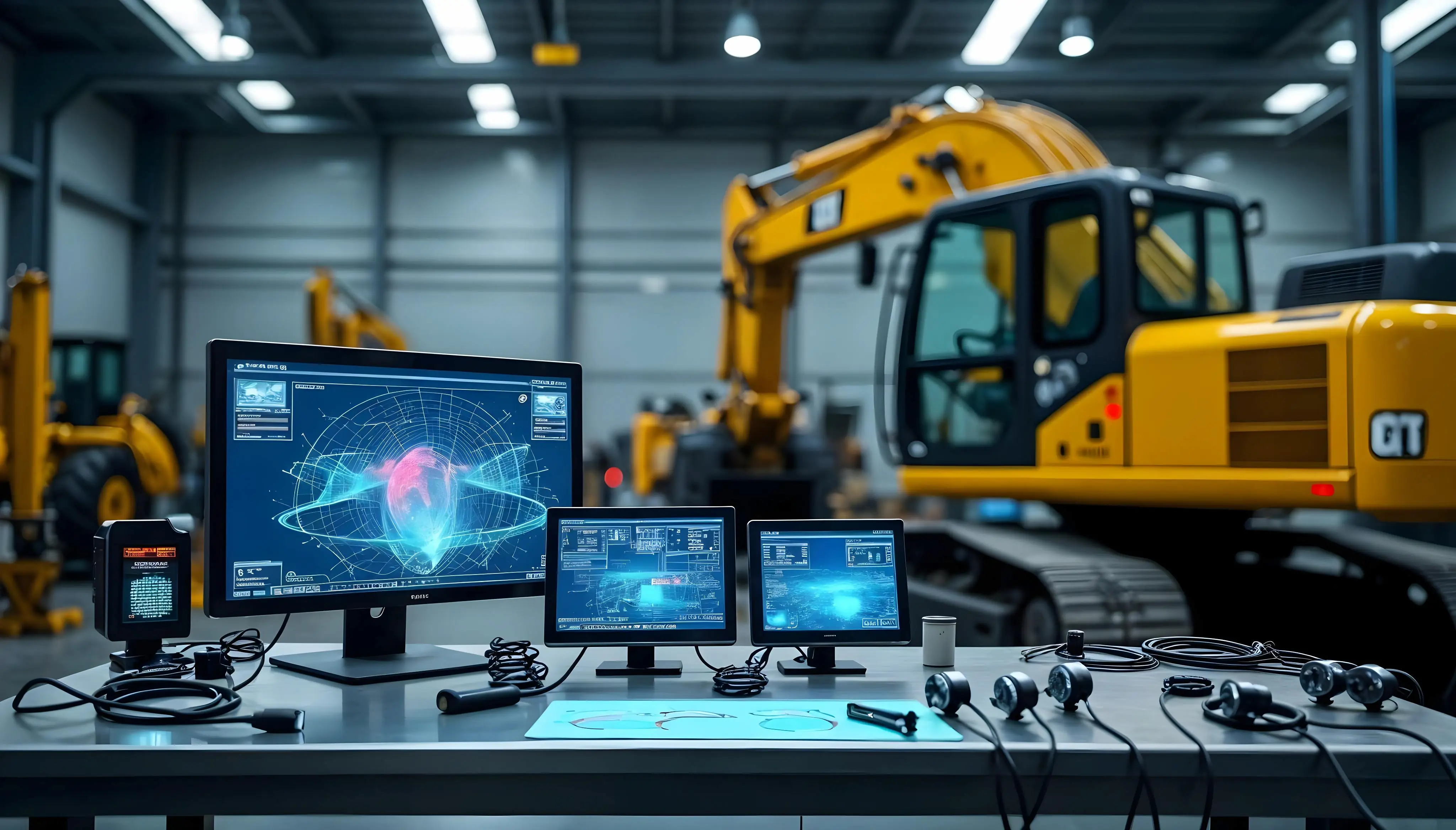
This comprehensive guide explores the latest advances in construction equipment diagnostic tools, their implementation, and how they ensure machinery quality through predictive maintenance. You'll discover how these systems work, what they can monitor, and why they're essential for modern construction operations, including their impact on total cost of ownership and overall productivity.
Modern Diagnostic Technologies
Modern diagnostic technologies have revolutionized how you monitor and maintain your construction equipment fleet. These advanced systems combine multiple technologies to provide comprehensive equipment health monitoring and predictive maintenance capabilities, utilizing equipment scan tools and sophisticated software.
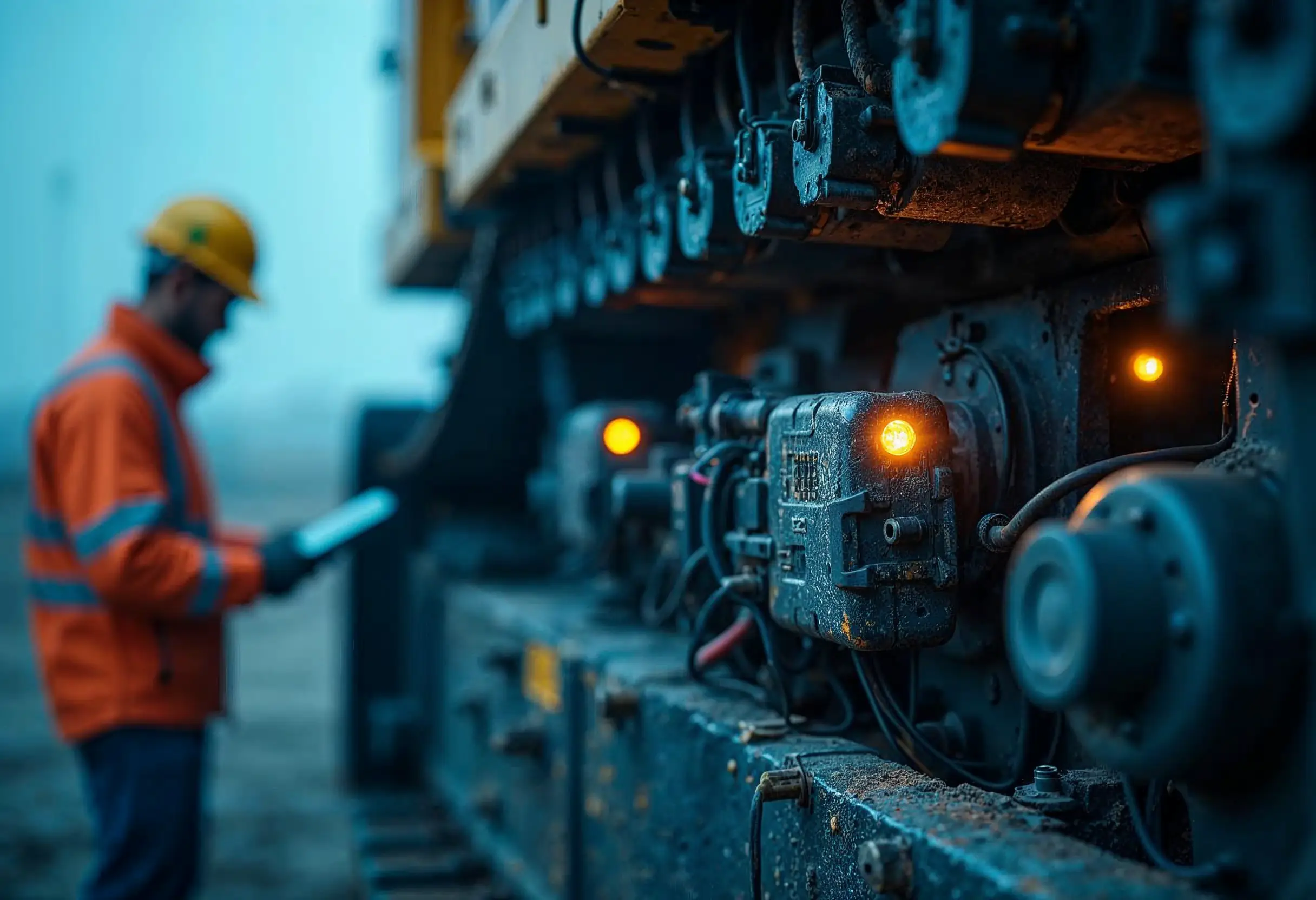
IoT Sensors and Real-time Monitoring
Your equipment's health is now continuously monitored through sophisticated IoT sensors that track critical parameters in real-time. These systems can monitor key components across different types, makes, and models. Modern sensors provide instant alerts for:
- Fault codes and engine diagnostics
- Fuel and DEF levels
- Battery status
- Equipment location and utilization
- Environmental conditions
Cloud-based Diagnostic Platforms
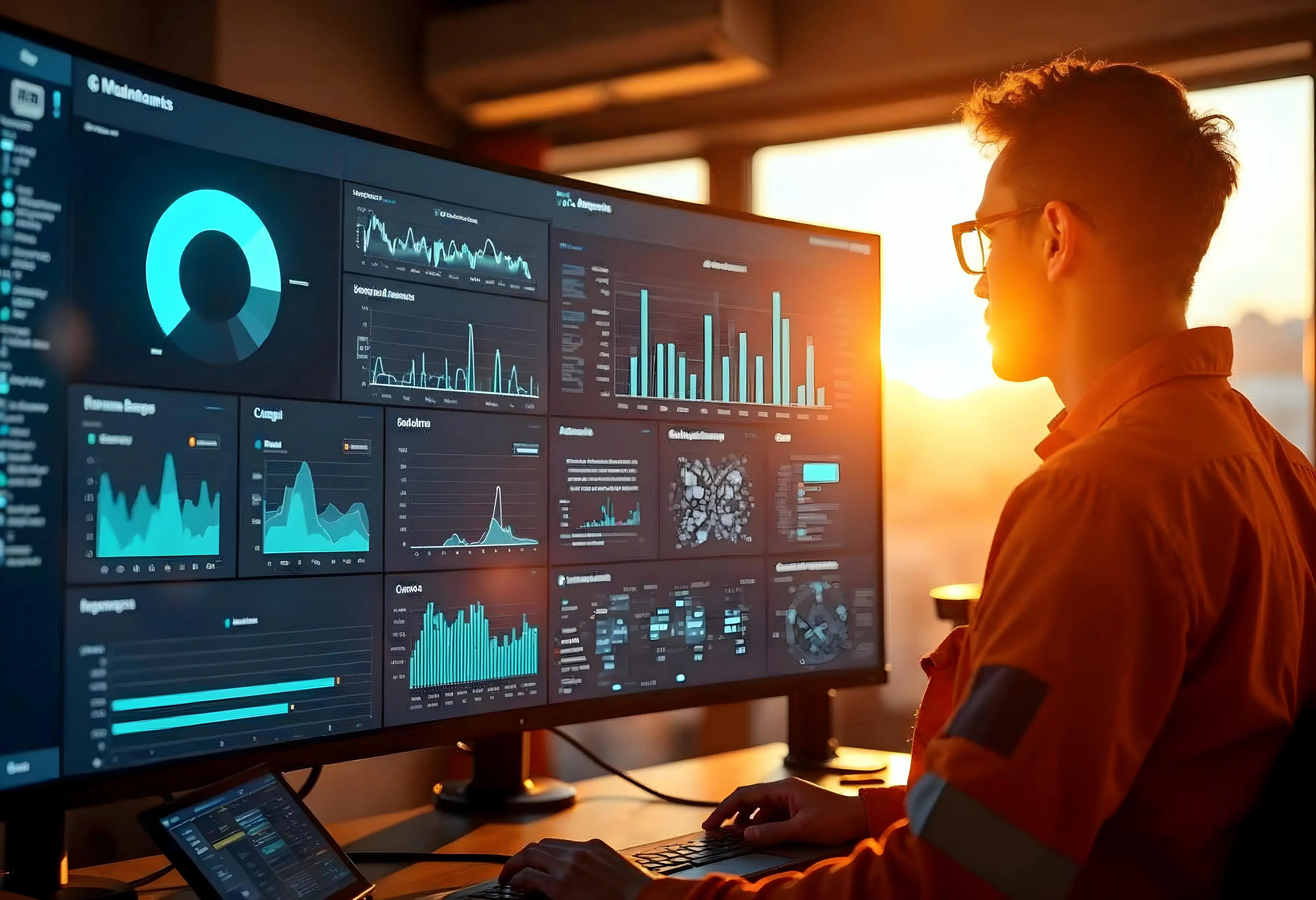
Cloud-based platforms transform raw sensor data into actionable insights through real-time dashboards. These platforms achieve an accuracy rate of over 90% in diagnosing equipment issues. Your maintenance team can access comprehensive diagnostic data pulled directly from vehicles through telematics control units (TCUs), enabling remote diagnostics and proactive maintenance scheduling.
Machine Learning Algorithms for Fault Detection
Advanced machine learning algorithms analyze equipment data to predict potential failures before they occur. These systems have demonstrated remarkable effectiveness, with hybrid unsupervised and supervised machine learning (HUS-ML) frameworks achieving an average F1 score of 86.6% in activity recognition and fault detection. The algorithms process data from multiple sources, including:
- Vibration analysis
- Temperature patterns
- Pressure readings
- Historical maintenance records
Through these integrated technologies, you can address potential issues before they impact your operations, significantly reducing downtime and maintenance costs. Heavy equipment diagnostics have become an integral part of modern construction and mining operations, ensuring optimal performance and durability of machinery.
Need expert guidance on selecting the right diagnostic tools for your equipment fleet? Contact MCH Parts for a free sourcing consultation and discover how to optimize your maintenance strategy using the best diagnostic tools for heavy equipment.
Implementation of Diagnostic Systems
Implementing diagnostic systems requires careful attention to hardware setup, software integration, and data collection protocols. Studies show that around 35-50% of annual operating budgets in the mining industry and 30% in construction are spent on equipment maintenance and repair alone. Proper implementation of diagnostic tools like the caterpillar diagnostic tool and bobcat scan tool can significantly reduce these costs.
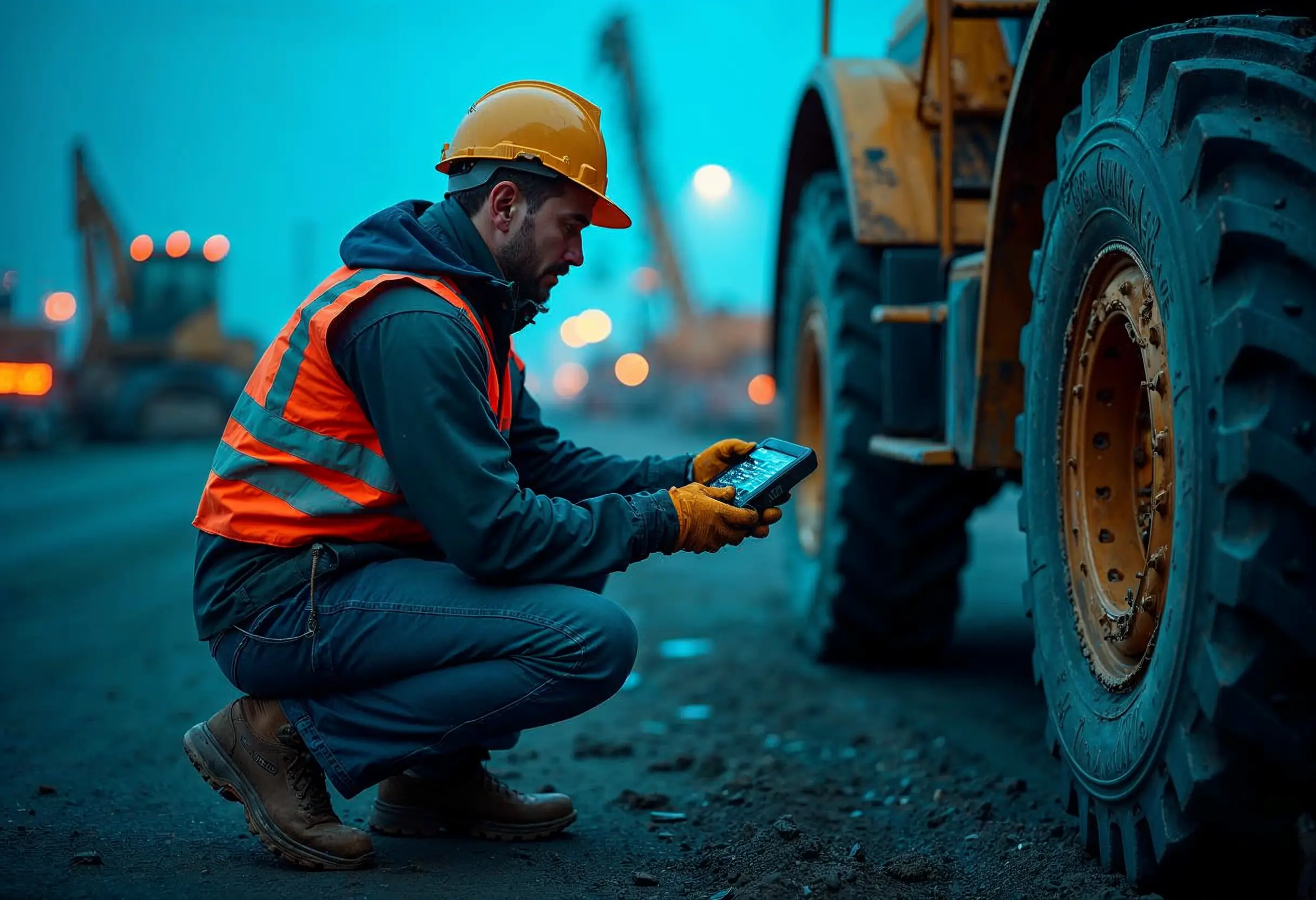
Hardware Installation Requirements
Your diagnostic system's effectiveness begins with proper hardware setup. Essential components include:
- Protective safety cages for main diagnostic units
- Vibration-resistant mounting systems
- Environmental protection against dust, sunlight, and moisture
- Properly positioned RPM sensors with adequate cable length
These components ensure that your heavy equipment scan tool can withstand harsh environments and provide accurate readings consistently.
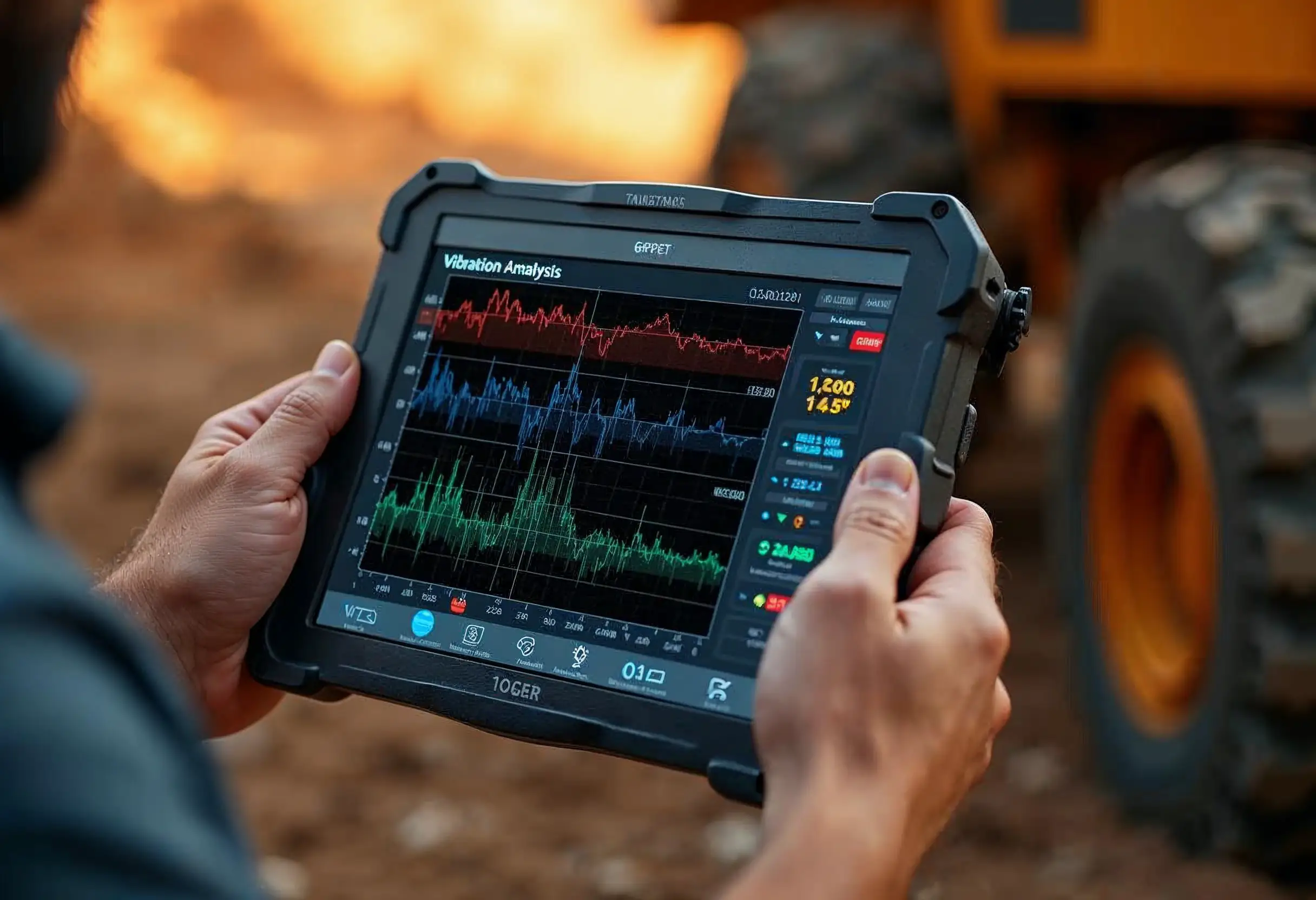
Software Integration Process
Successful software integration demands compatibility with your existing fleet management systems. The evolution of maintenance approaches has progressed significantly, aided by real-time data availability. Your integration process should focus on establishing reliable connections between diagnostic tools and cloud-based platforms while ensuring data security. This includes integrating heavy equipment diagnostic software with onboard vehicle computers for seamless data exchange.
Data Collection and Analysis Protocols
Your data collection strategy must include rigorous quality assurance measures. Field data requires periodic reviews to identify and correct potential errors or problems. Key considerations include:
- Regular system status checks for leakage detection
- Comparison of oxygen concentration readings with ambient air
- Implementation of data screening procedures
- Periodic sensor array verification
The implementation of proper diagnostic protocols has demonstrated significant improvements in equipment reliability. With condition-based monitoring (CBM), you can repair systems before failure by identifying signs of fatigue or other failure precursors. This approach, facilitated by advanced diagnostic tools, enhances the productivity and durability of your equipment fleet.
Need expert guidance on implementing diagnostic systems for your equipment fleet? Contact MCH Parts for a free sourcing consultation and discover how to optimize your maintenance strategy using state-of-the-art equipment scan tools and software.
Quality Assurance Through Diagnostics
Quality assurance in heavy equipment operations demands precise measurement and monitoring. Studies show that companies using comprehensive diagnostic tools can reduce maintenance costs by up to 20% while improving equipment availability by 15%. This improvement is largely due to the capabilities of advanced diagnostic tools like the cat scan tool and equipment scanner.
Performance Metrics and Benchmarking
Your equipment's performance should be measured across nine major categories to ensure optimal operation:
- Financial and Cost Management
- Equipment Utilization
- Safety Compliance
- Preventive Maintenance
- Planning and Scheduling
- Labor Efficiency
- Reliability Metrics
- Inventory Management
- Data Logging and Analysis
Automated Quality Control Systems
Implementing automated quality control systems transforms your inspection processes. These systems can reduce measurement times dramatically compared to traditional methods. Your automated inspection solution provides continuous data collection for better understanding of production quality, enabling fast or automated decisions based on comprehensive datasets. This approach is particularly effective when combined with digital diagnostics and remote diagnostics capabilities.
Compliance and Certification Standards
To ensure reliable service and protect workers, your heavy machinery must meet all applicable safety standards without exception. Modern certification processes involve:
Documentation Requirements: Compile technical documents and reports that facilitate successful equipment deployment.
Testing Protocols: Conduct state-of-the-art testing to ensure compliance with safety, acoustic, and electromagnetic requirements.
Regular Audits: Physical audits of documentation, procedures, and shop adherence are performed every three years to maintain certification standards.
These processes are greatly enhanced by the use of advanced diagnostic tools, which provide detailed insights into equipment performance and compliance.
Need expert guidance on implementing quality assurance systems for your equipment fleet? Contact MCH Parts for a free sourcing consultation and discover how to optimize your maintenance strategy using cutting-edge diagnostic technologies.
Future-Proofing Equipment Maintenance
The future of heavy equipment maintenance lies in smart, predictive technologies that transform how you manage your construction fleet. Studies show that implementing predictive maintenance can reduce equipment downtime by up to 30% while lowering maintenance costs by 20%. This future is being shaped by advancements in diagnostic tools and software.
Predictive Maintenance Strategies
Your maintenance strategy benefits from advanced analytics and IoT integration that revolutionize equipment monitoring. Modern predictive systems offer:
- Real-time performance tracking
- Automated geofencing alerts
- Strategic resource allocation
- Usage pattern analysis
These capabilities are enhanced by the use of sophisticated diagnostic tools like the caterpillar diagnostic tool for sale and mobile truck diagnostics solutions.
Digital Twin Technology
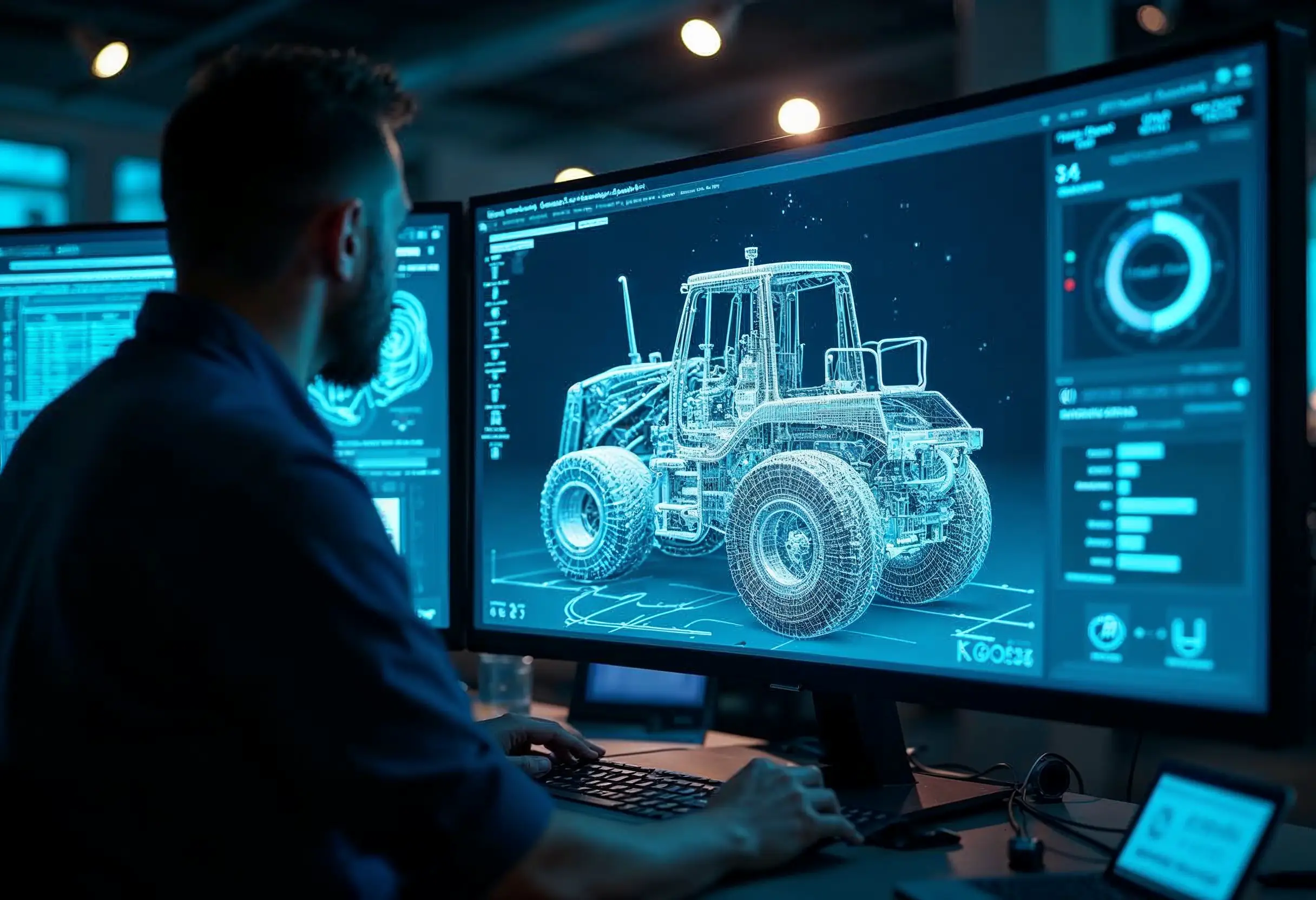
Digital twin solutions create virtual replicas of your physical assets, enabling comprehensive lifecycle management. These platforms integrate with AI to forecast maintenance needs and optimize performance. Your digital twin evolves throughout the asset's lifespan, providing actionable insights for operations and maintenance while transforming post-construction asset management. This technology works hand-in-hand with advanced diagnostic software to provide a complete picture of equipment health and performance.
Sustainability Considerations
Environmental responsibility shapes the future of equipment maintenance. Your sustainable maintenance strategy should focus on reducing carbon emissions and improving operational efficiency. Studies indicate that implementing comprehensive asset tracking solutions can reduce equipment theft by up to 40% while improving operational efficiency by 25%.
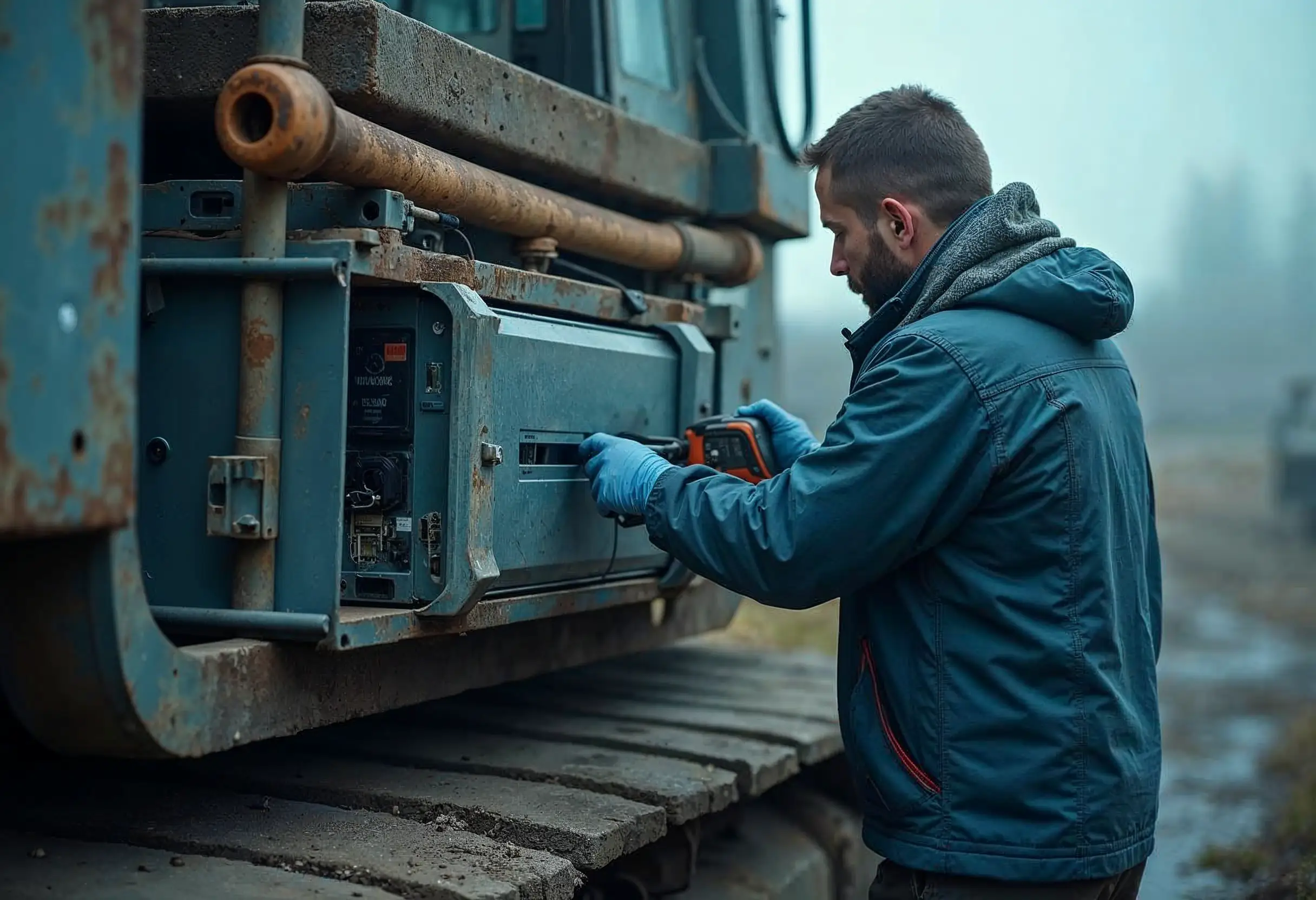
The integration of electric-powered machinery and fuel efficiency monitoring systems represents a significant shift toward sustainable operations. These technologies not only reduce environmental impact but also lower operating costs through improved resource management. Smart analytics transform equipment data into powerful business intelligence, helping you make informed decisions about maintenance scheduling and resource allocation.
Need expert guidance on implementing advanced diagnostic tools for your equipment fleet? Contact MCH Parts for a free sourcing consultation and discover how to optimize your maintenance strategy using state-of-the-art diagnostic software and hardware.
Conclusion
Advanced diagnostic tools have transformed construction equipment maintenance from reactive repairs to data-driven prevention. Your construction operations now benefit from sophisticated systems that combine IoT sensors, cloud platforms, and machine learning algorithms to detect issues before they cause costly downtime. Tools like the caterpillar scanner, john deere code reader, and bobcat scan tool have become indispensable for modern fleet management.
These diagnostic solutions deliver measurable results:
- 20% reduction in maintenance costs
- 30% decrease in equipment downtime
- 15% improvement in machinery availability
- 40% reduction in equipment theft risk
Smart maintenance strategies, paired with digital twin technology and sustainability measures, prepare your fleet operations for future challenges. Modern diagnostic tools make equipment health monitoring precise, predictable, and cost-effective. The use of heavy equipment diagnostic software and equipment scan tools has revolutionized how service technicians approach maintenance and repairs.
Consider reaching out to MCH Parts for a free sourcing machinery or parts consultation, ensuring your business benefits from top-tier equipment and service. Through proper implementation of these diagnostic solutions, you can maximize equipment lifespan, reduce operational costs, and maintain optimal performance across your entire fleet.
FAQs
Q1. What are the benefits of using advanced diagnostic tools for heavy equipment? Advanced diagnostic tools can reduce maintenance costs by up to 20%, decrease equipment downtime by 30%, and improve machinery availability by 15%. They also help in detecting potential issues before they cause costly breakdowns, enhancing overall productivity and durability.
Q2. What technologies are used in modern heavy equipment diagnostic systems? Modern diagnostic systems utilize IoT sensors for real-time monitoring, cloud-based platforms for data analysis, and machine learning algorithms for fault detection. These technologies work together to provide comprehensive equipment health monitoring and predictive maintenance capabilities. Examples include the caterpillar scanner, john deere code reader, and various equipment scan tools.
Q3. How do digital twin technologies contribute to equipment maintenance? Digital twin technologies create virtual replicas of physical assets, enabling comprehensive lifecycle management. They integrate with AI to forecast maintenance needs, optimize performance, and provide actionable insights for operations and maintenance throughout the asset's lifespan. This technology works in conjunction with heavy equipment diagnostic software for enhanced predictive maintenance.
Q4. What are some key performance metrics for heavy equipment quality assurance? Key performance metrics include financial and cost management, equipment utilization, safety compliance, preventive maintenance, planning and scheduling, labor efficiency, reliability metrics, and inventory management. These metrics help ensure optimal operation of heavy equipment and are often monitored using advanced diagnostic tools.
Q5. How can implementing diagnostic tools impact equipment theft and operational efficiency? Implementing comprehensive asset tracking solutions, which are part of advanced diagnostic systems, can reduce equipment theft by up to 40% while improving operational efficiency by 25%. These tools provide real-time tracking and monitoring of equipment location and usage, enhancing both security and productivity. Advanced features like wireless connectivity and remote diagnostics further contribute to improved operational efficiency.
Read More
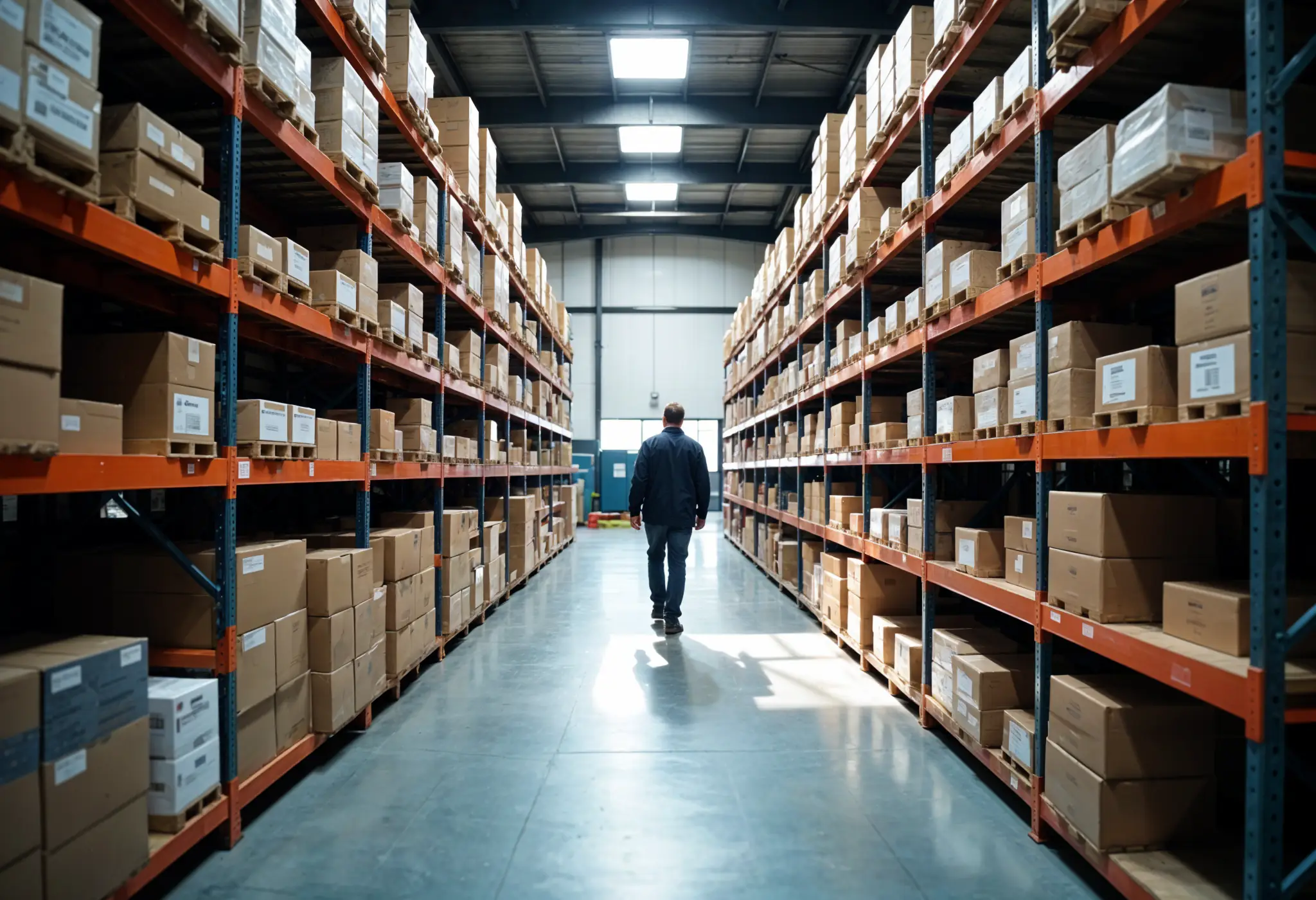
Cut Costs by 30%: Pre-Season Spare Parts Audit Checklist

Proven Success Factors for Agricultural Equipment Manufacturers in 2025
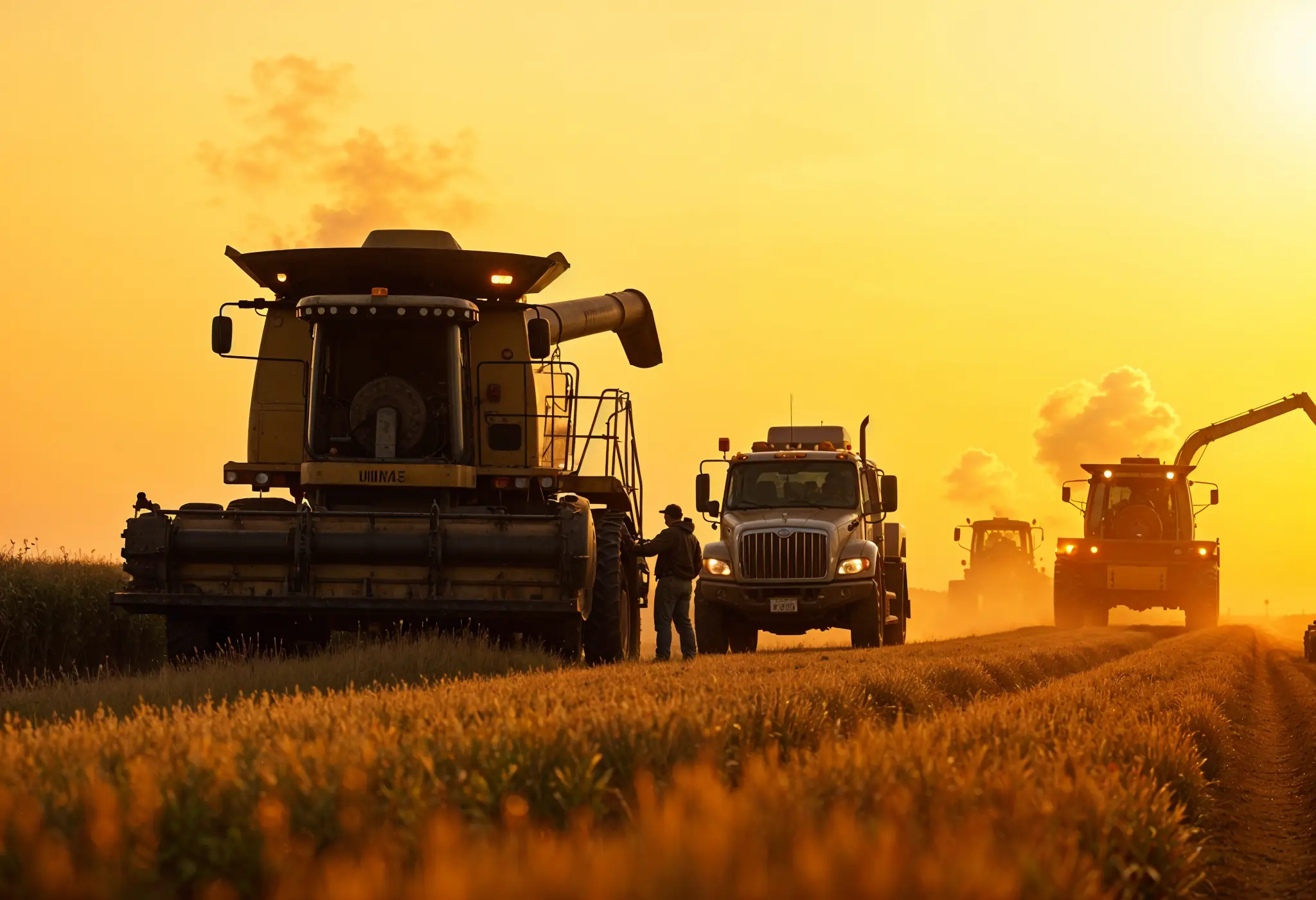
13 Overlooked Farm Spare Parts That Halt Operations — Pt. 2
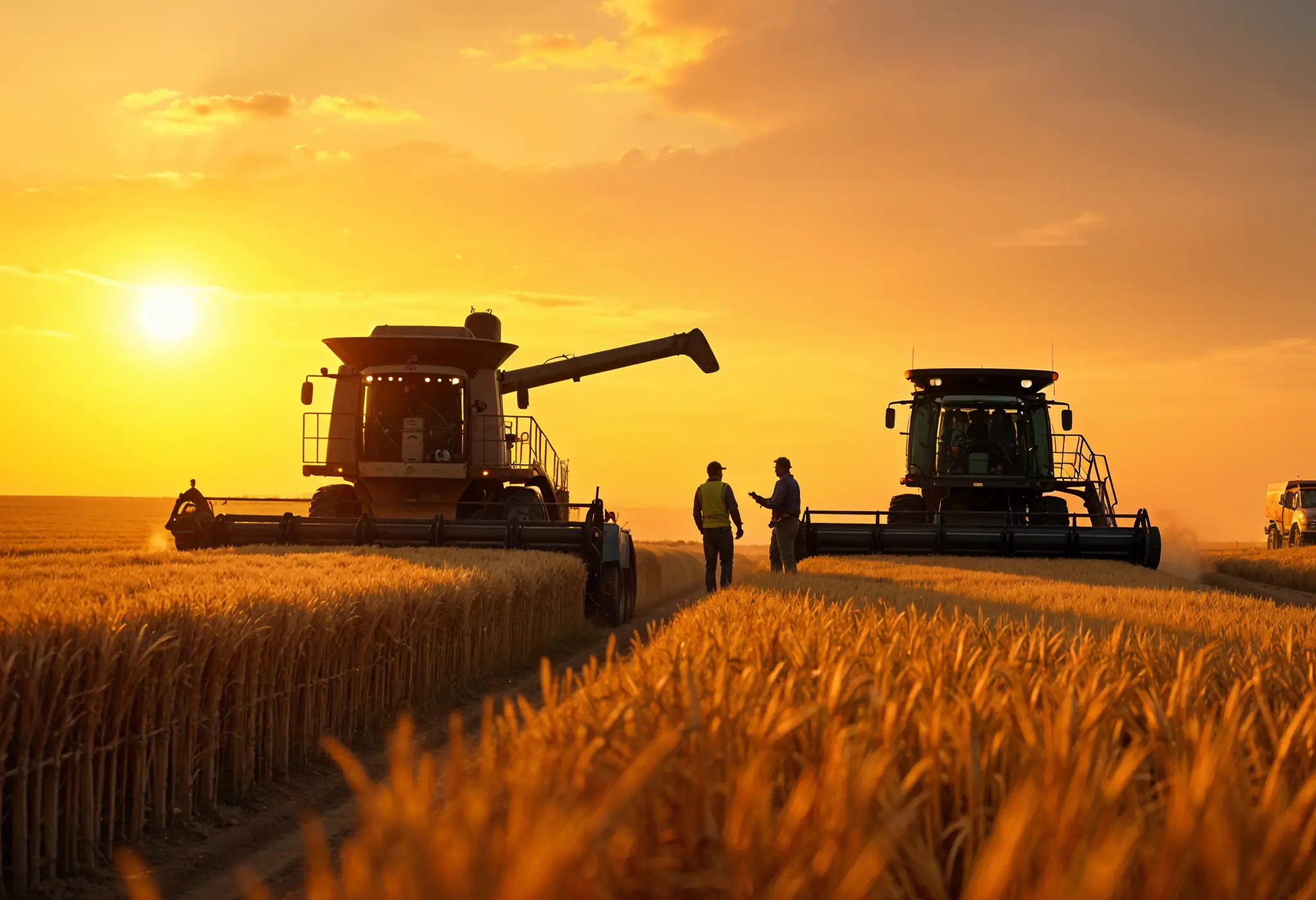
13 Overlooked Farm Spare Parts That Halt Operations — Pt. 1
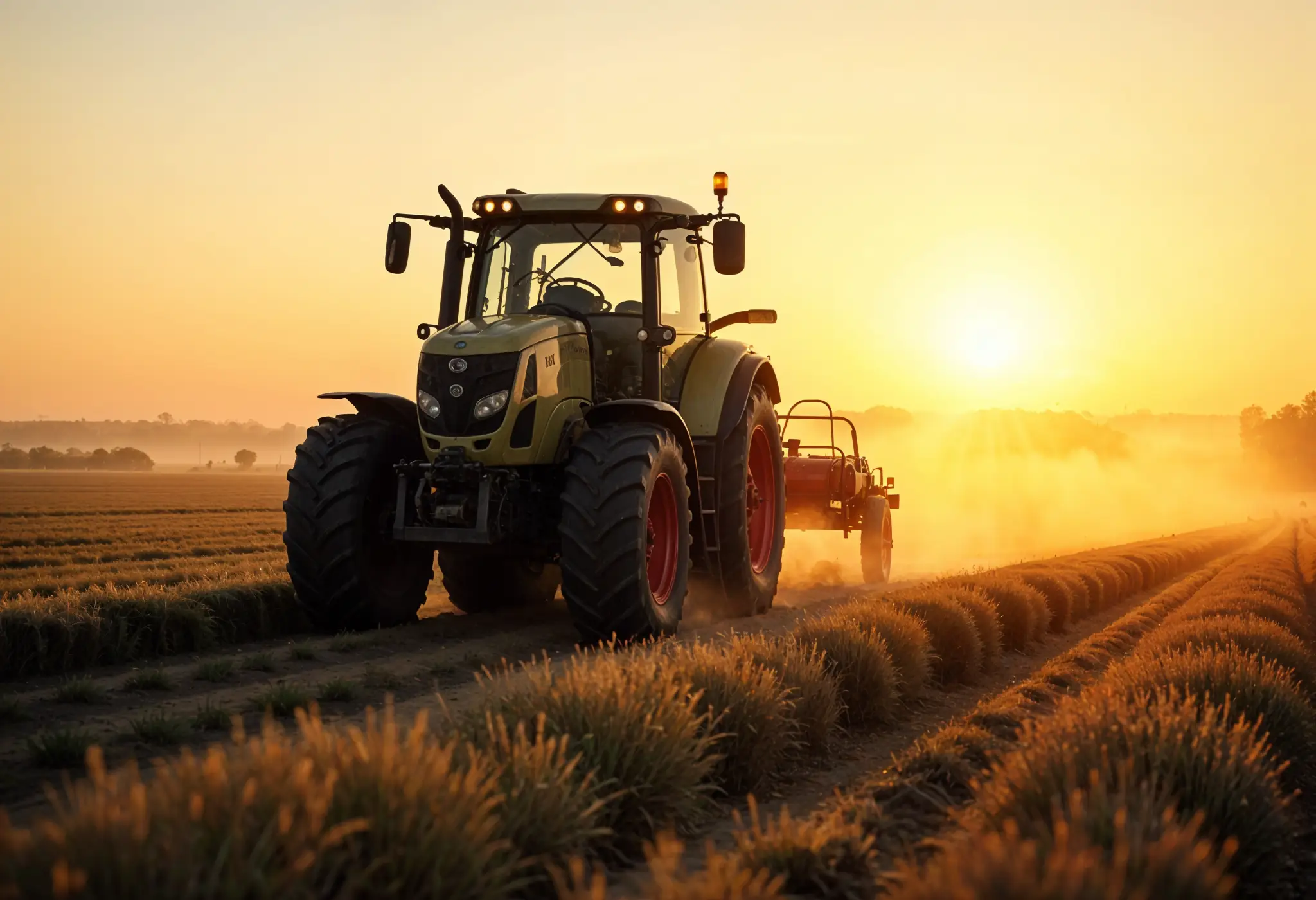
Top Hydraulic Components for Agricultural Equipment in 2025: Complete Guide
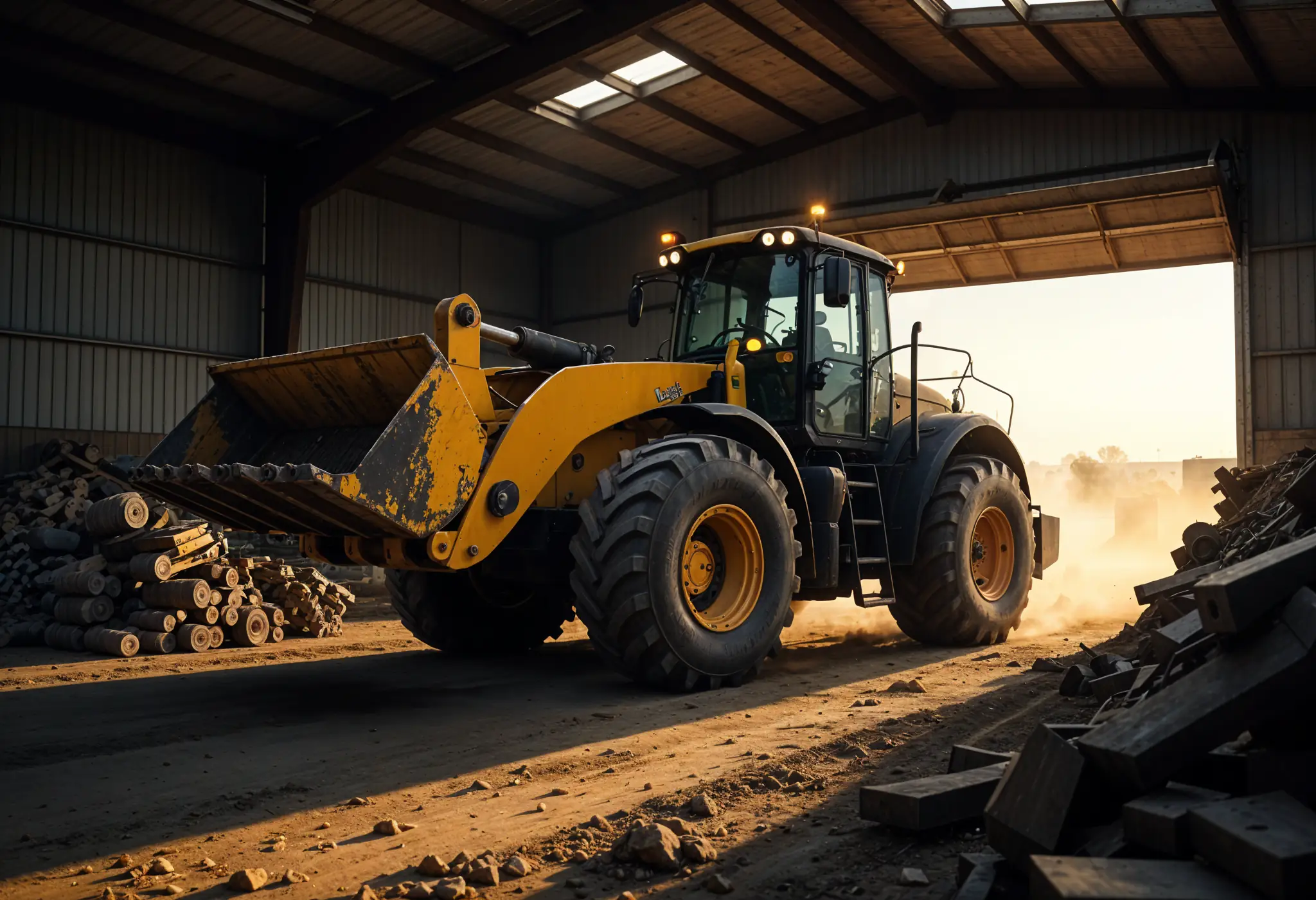
The Essential Farm Equipment Parts You Can't Afford to Run Out Of
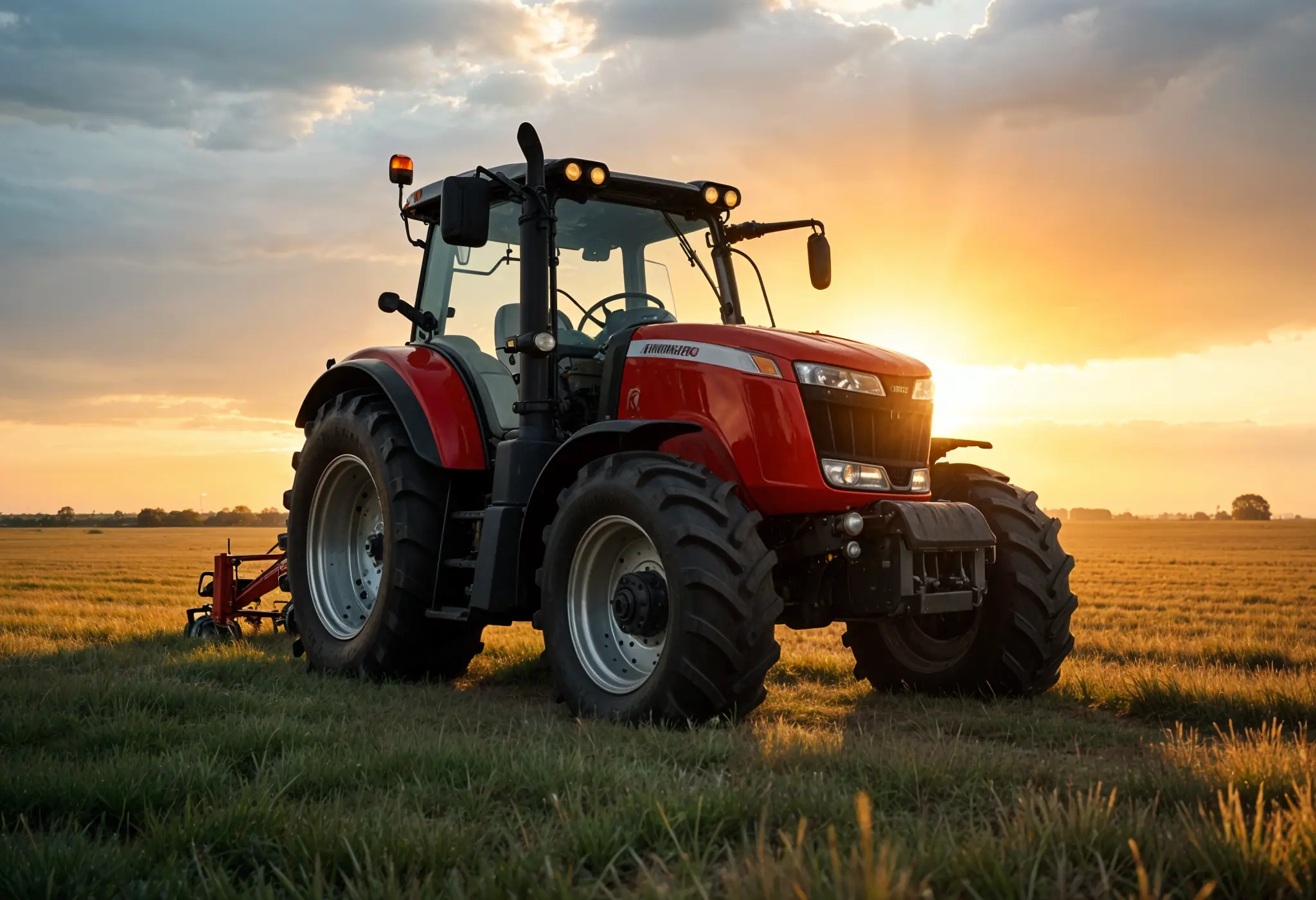
How to Service Farm Equipment: A Farmer's Guide to Zero Harvest Downtime
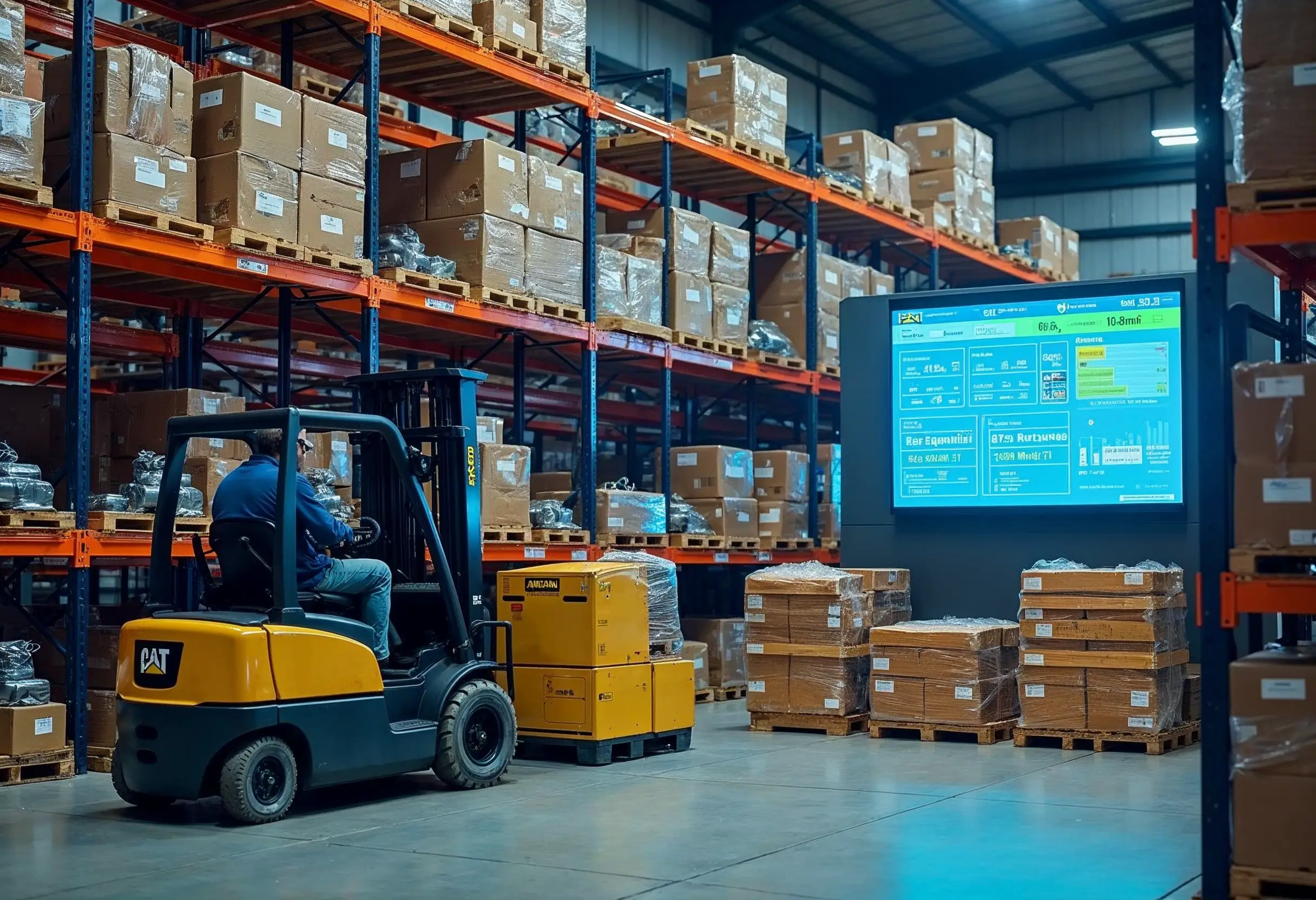
Construction Machinery Parts Suppliers: Expert Selection Guide
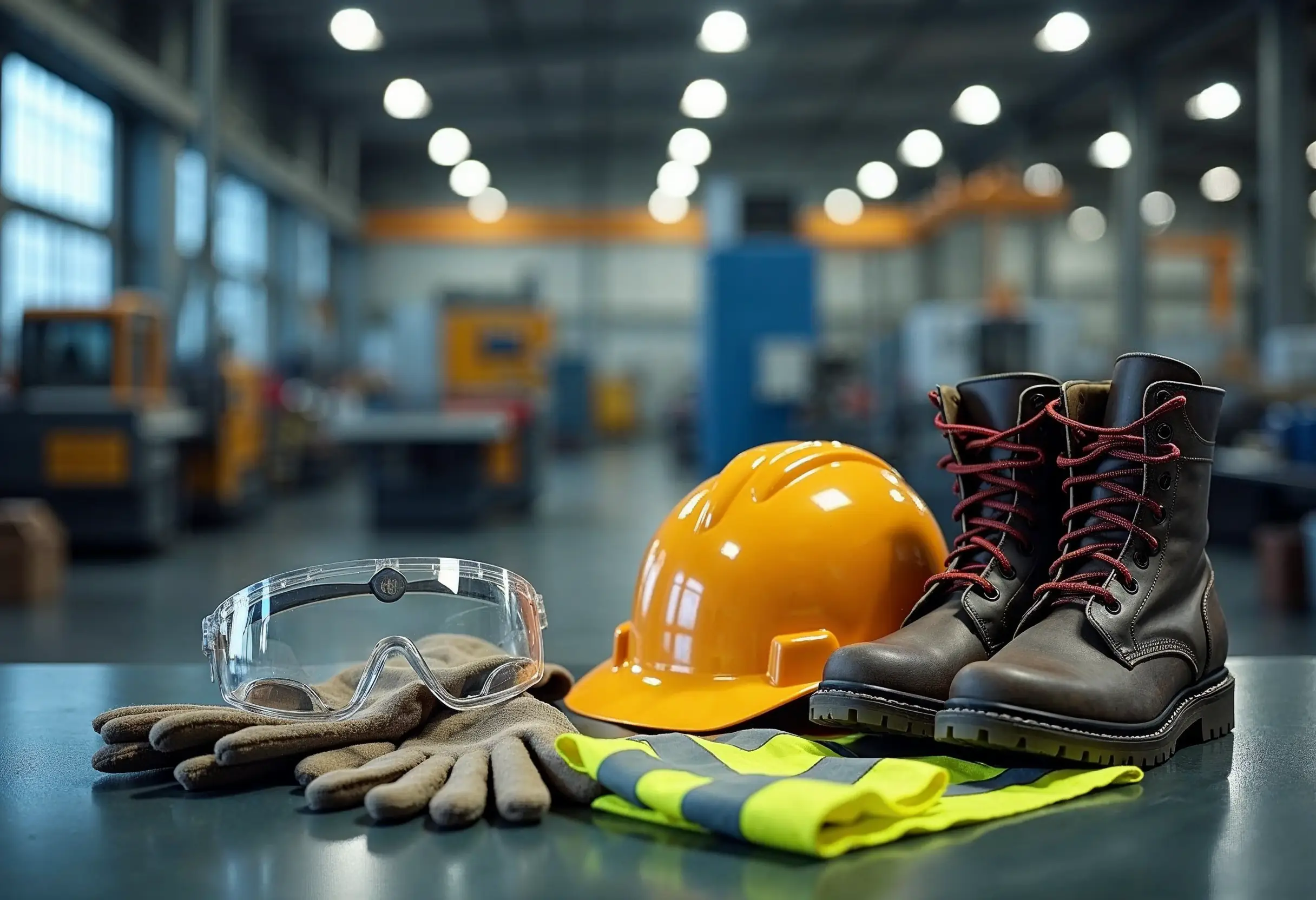
How to Apply Machine Safety Rules: From Selection to Installation
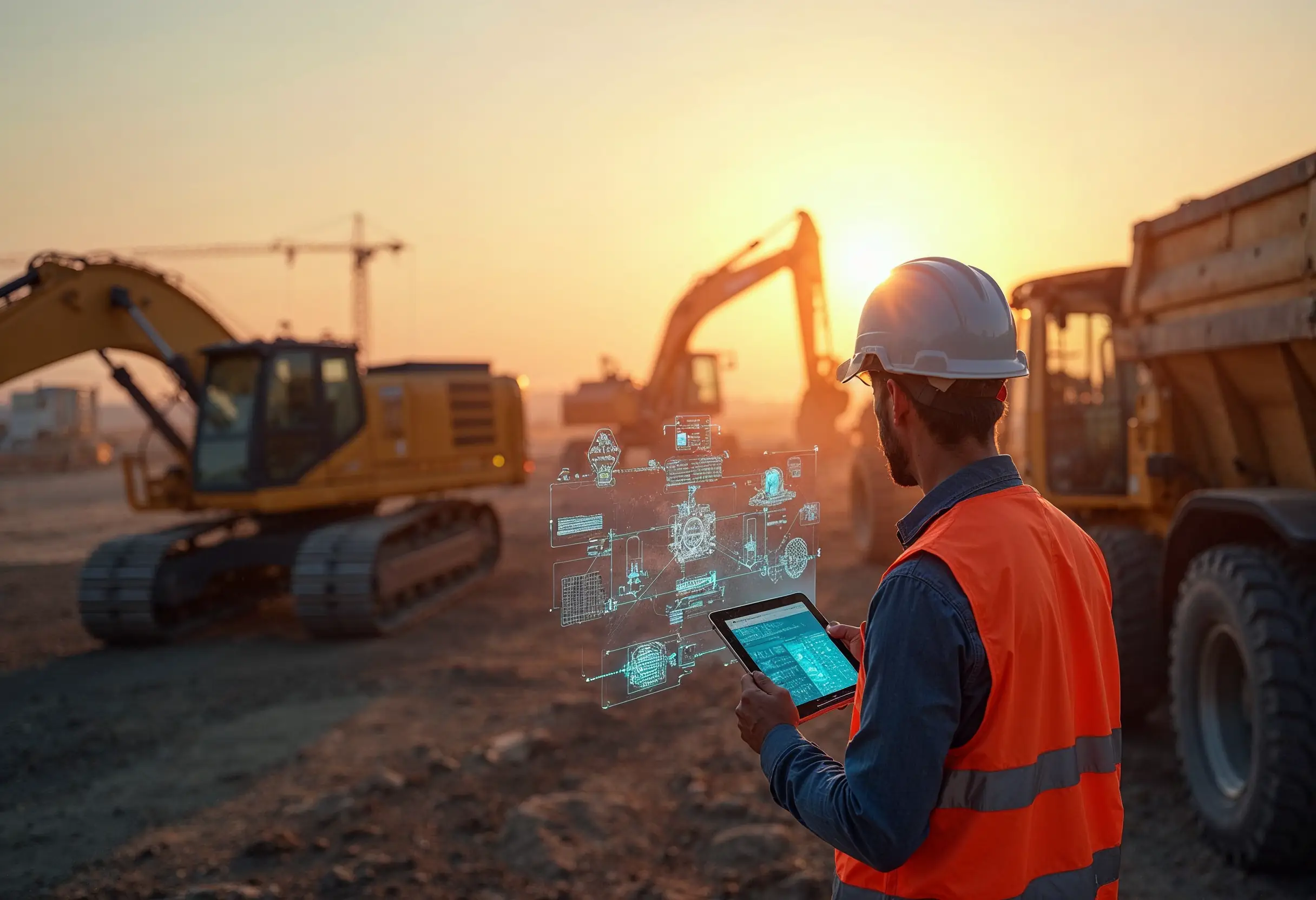
Smart Diagnostics Cut Heavy Equipment Failures by 73%
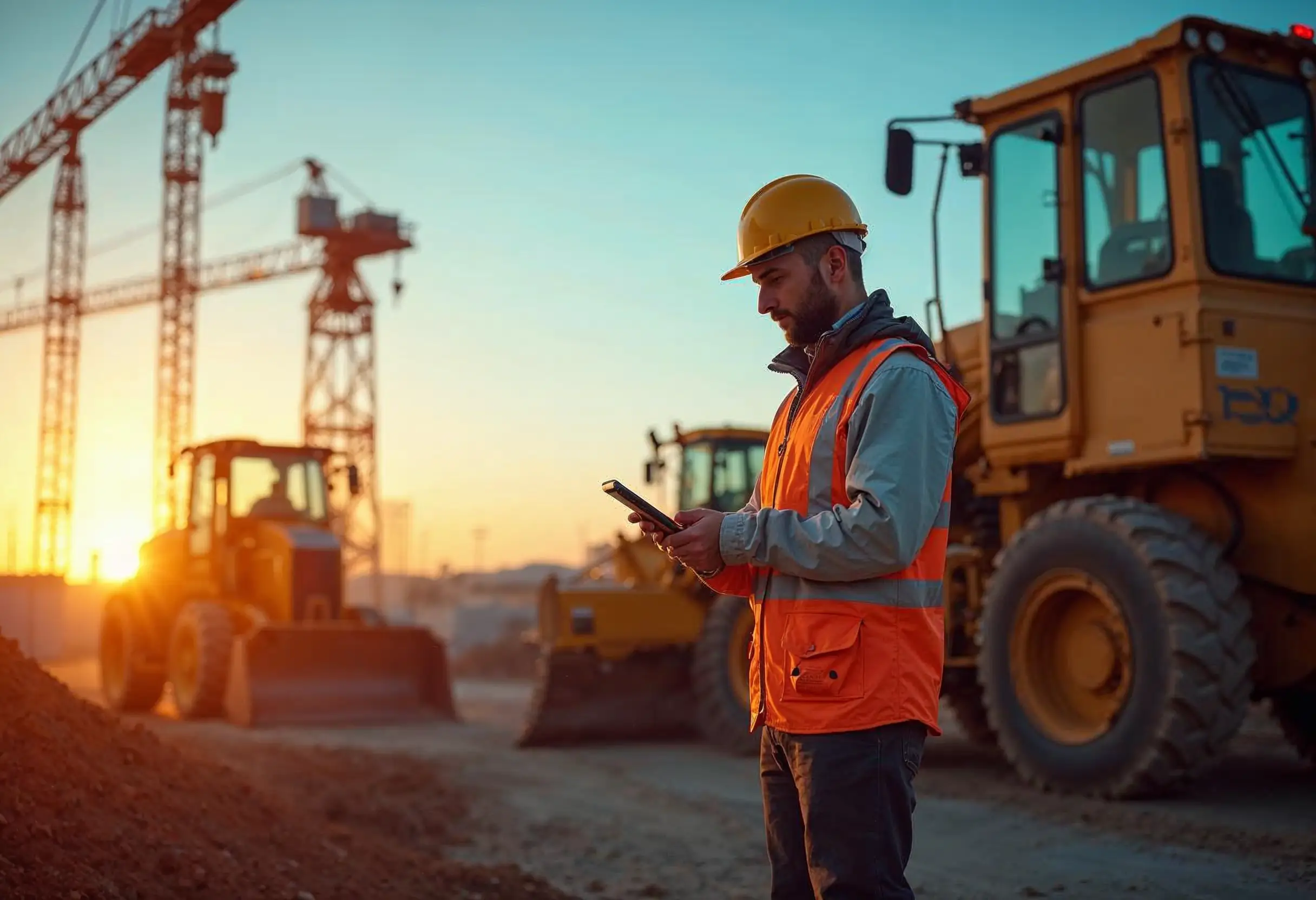
5 Ways to Assess the Environmental Impact of Heavy Construction Machinery
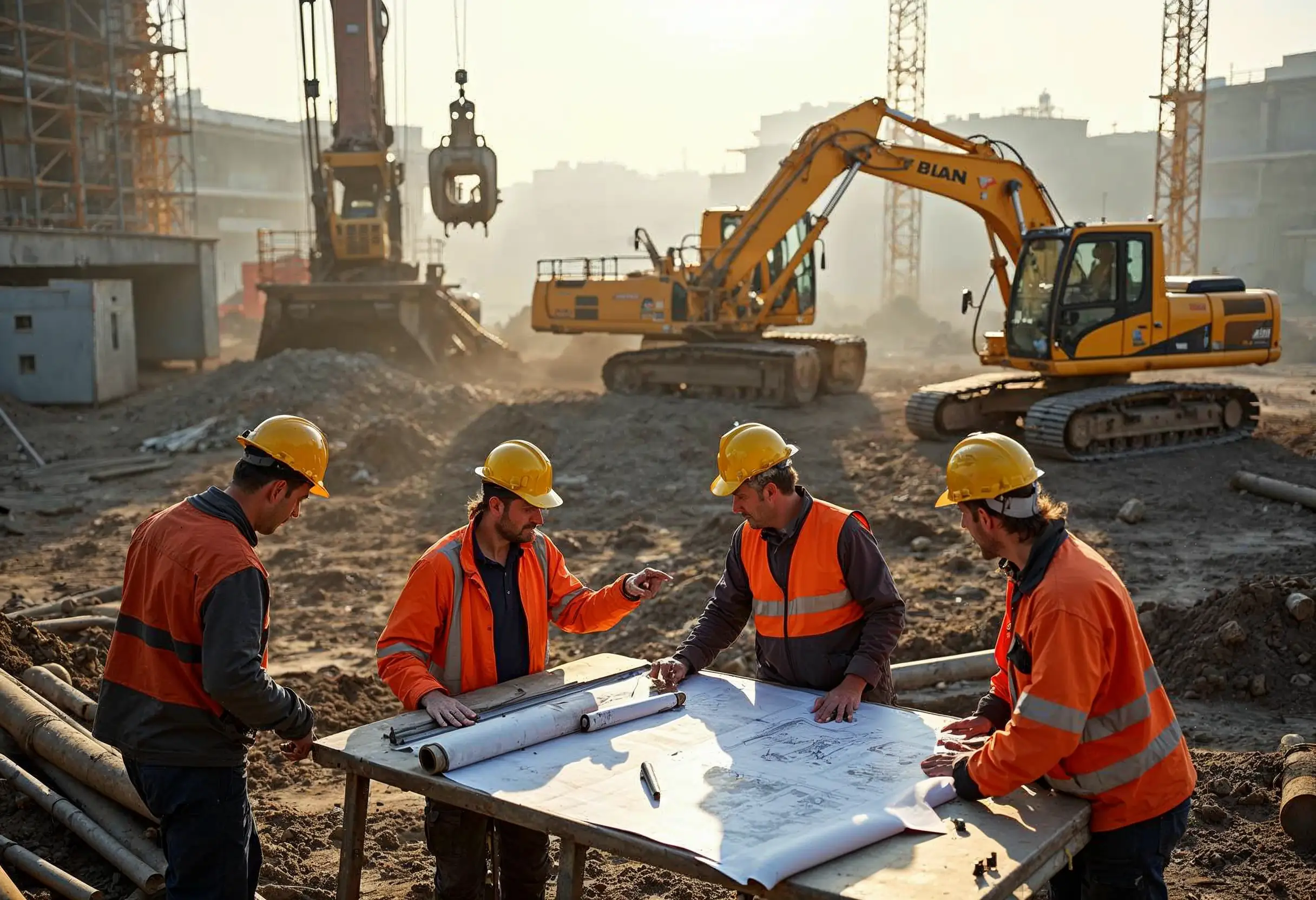
10 Smart Ways to Pick Construction Machinery for 2025 Projects
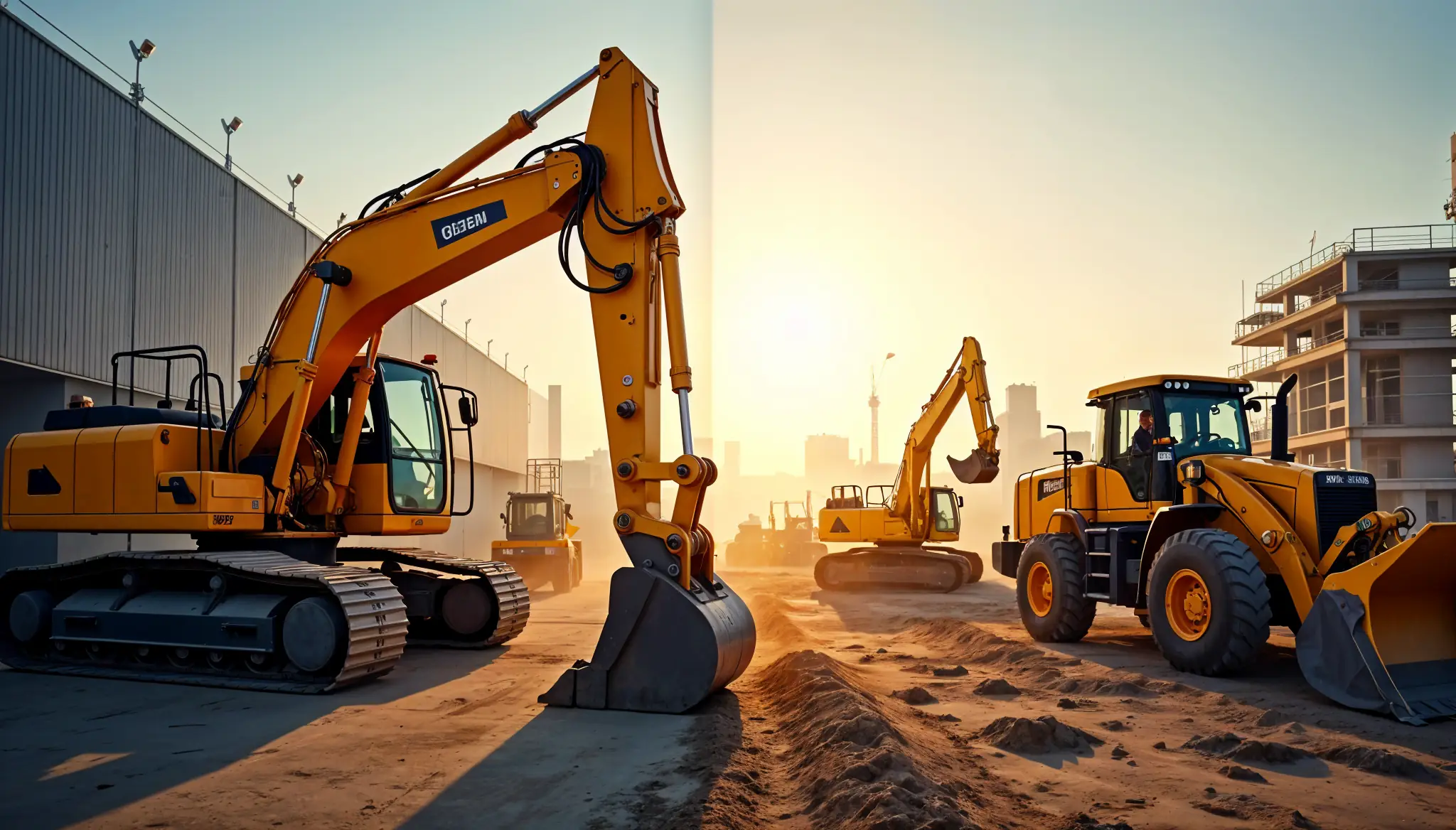
Rent vs Purchase Equipment: What Heavy Industry Experts Hide
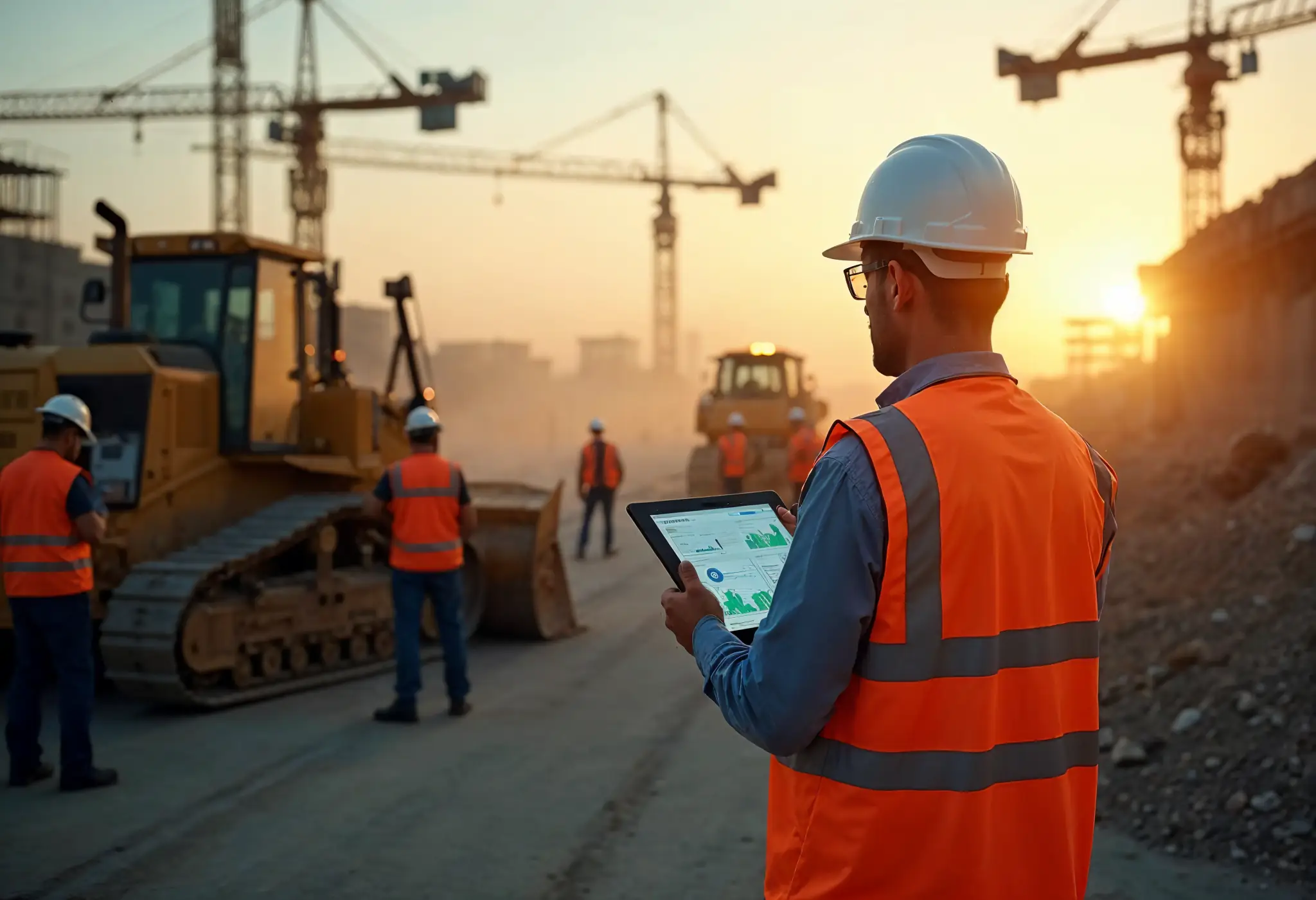
How to Implement a Construction Inventory Management System for Equipment Efficiency
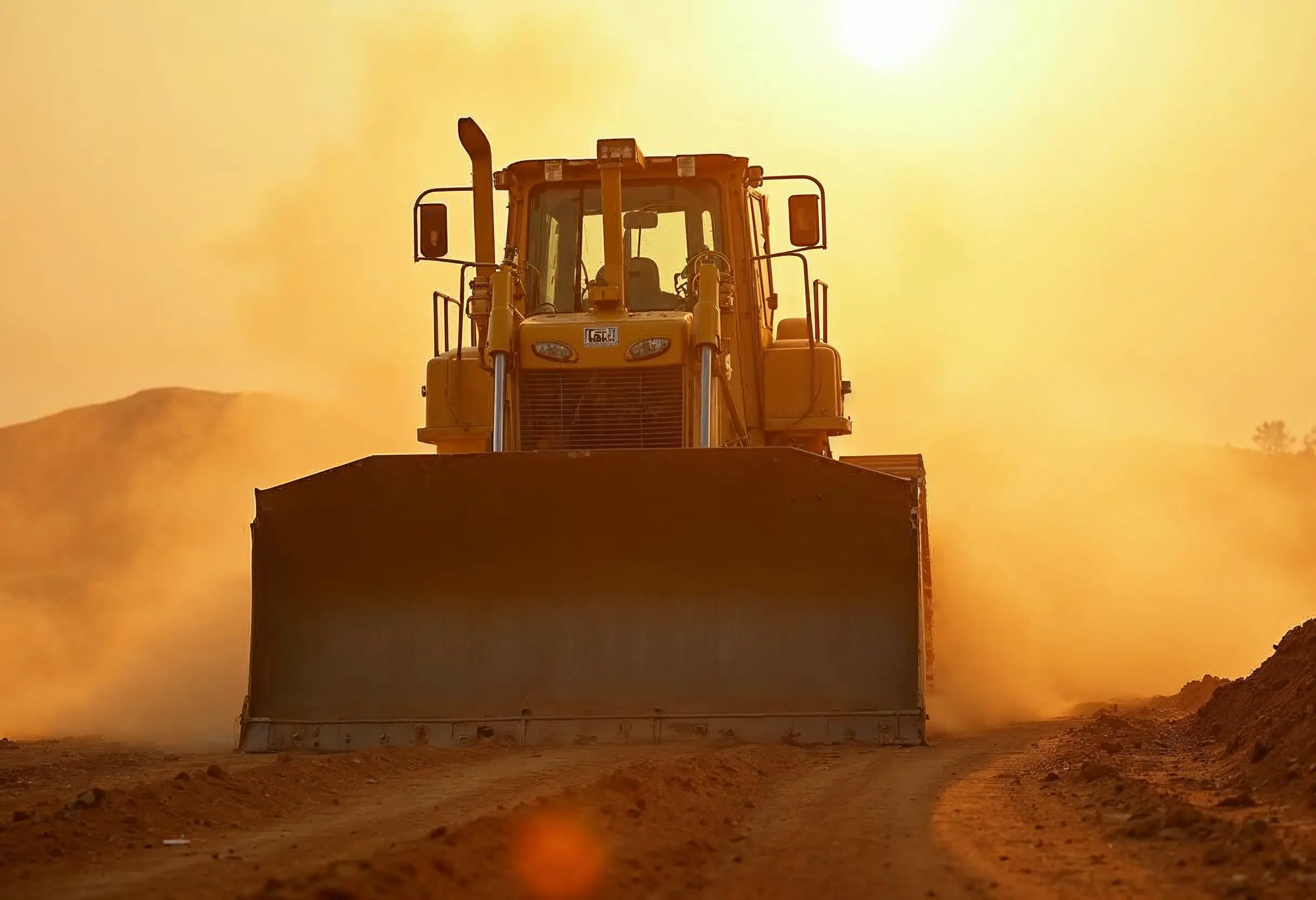
How to Extend Equipment Life Expectancy with Regular Maintenance
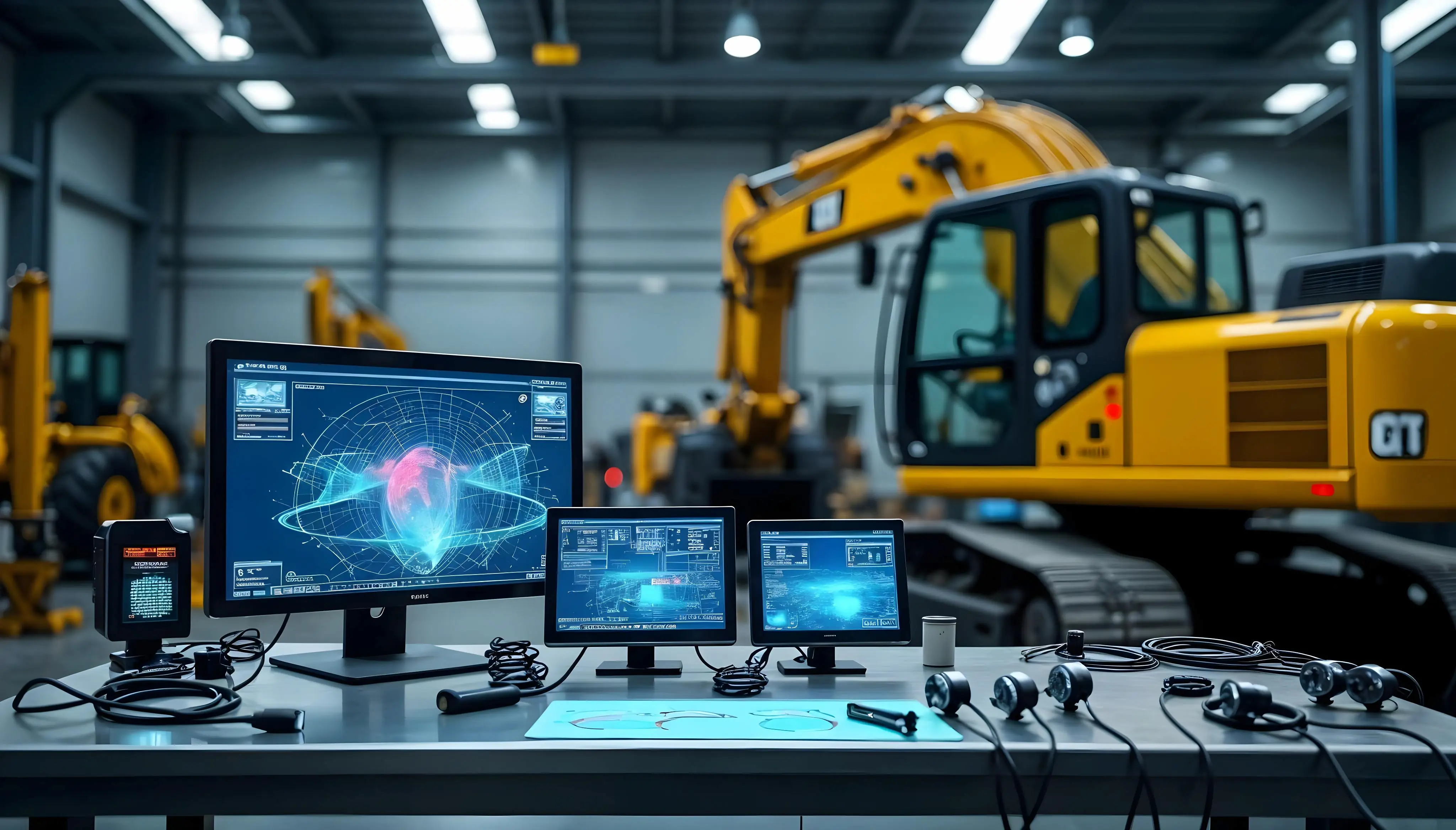
Advanced Heavy Equipment Diagnostic Tools: Ensuring Construction Machinery Quality
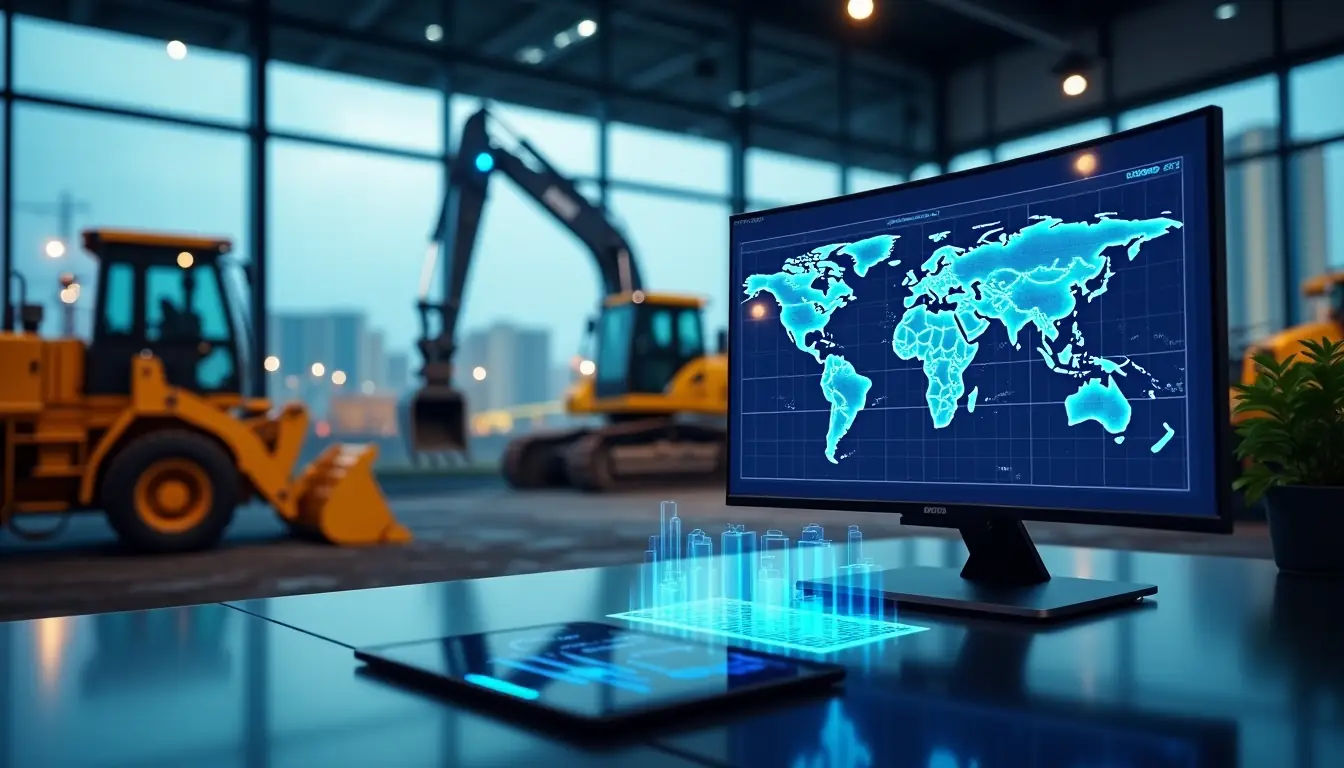
Essential Features Your Construction Equipment Inventory System Needs
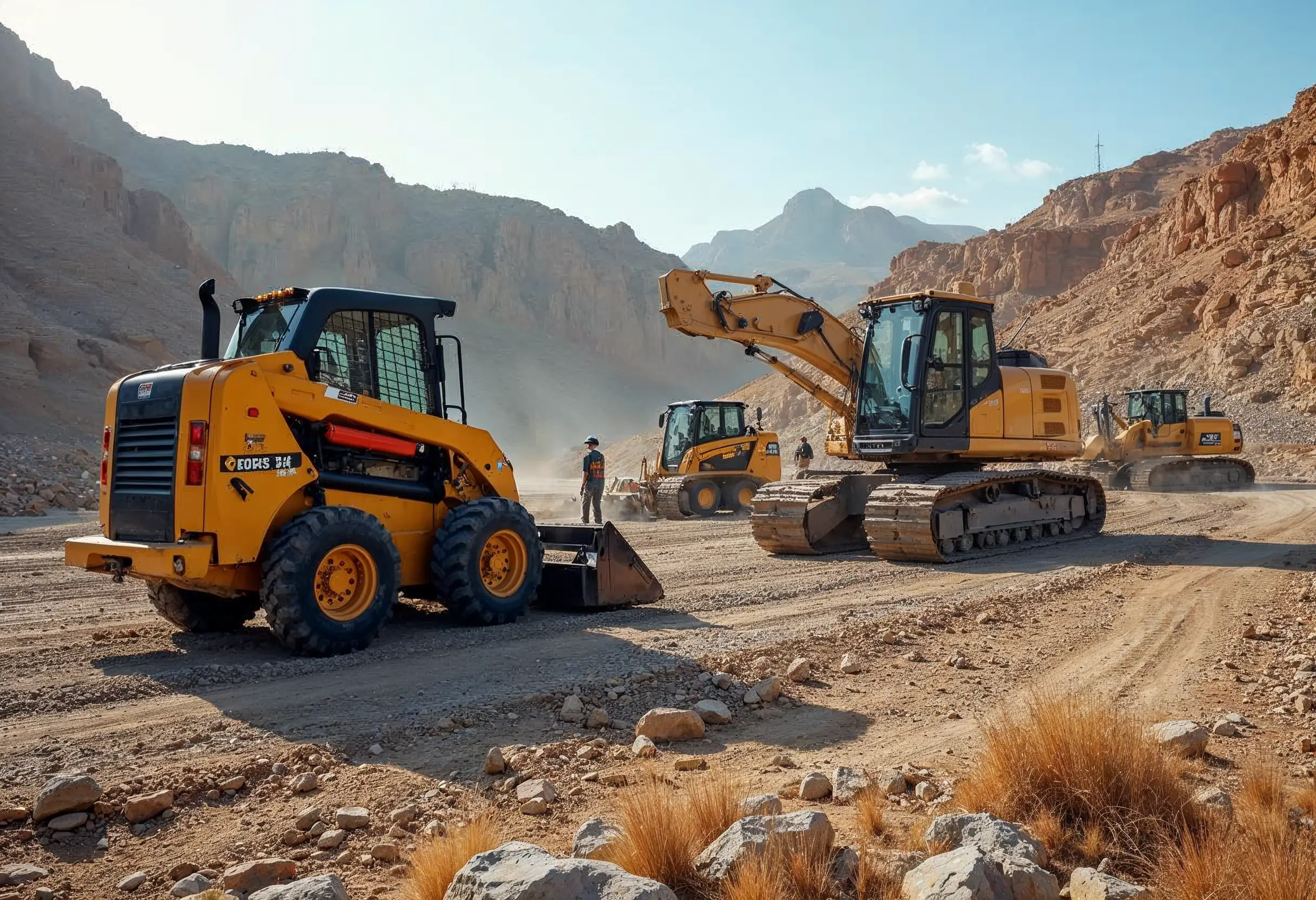
29 Quick Tips for Choosing Construction Equipment for Remote Locations
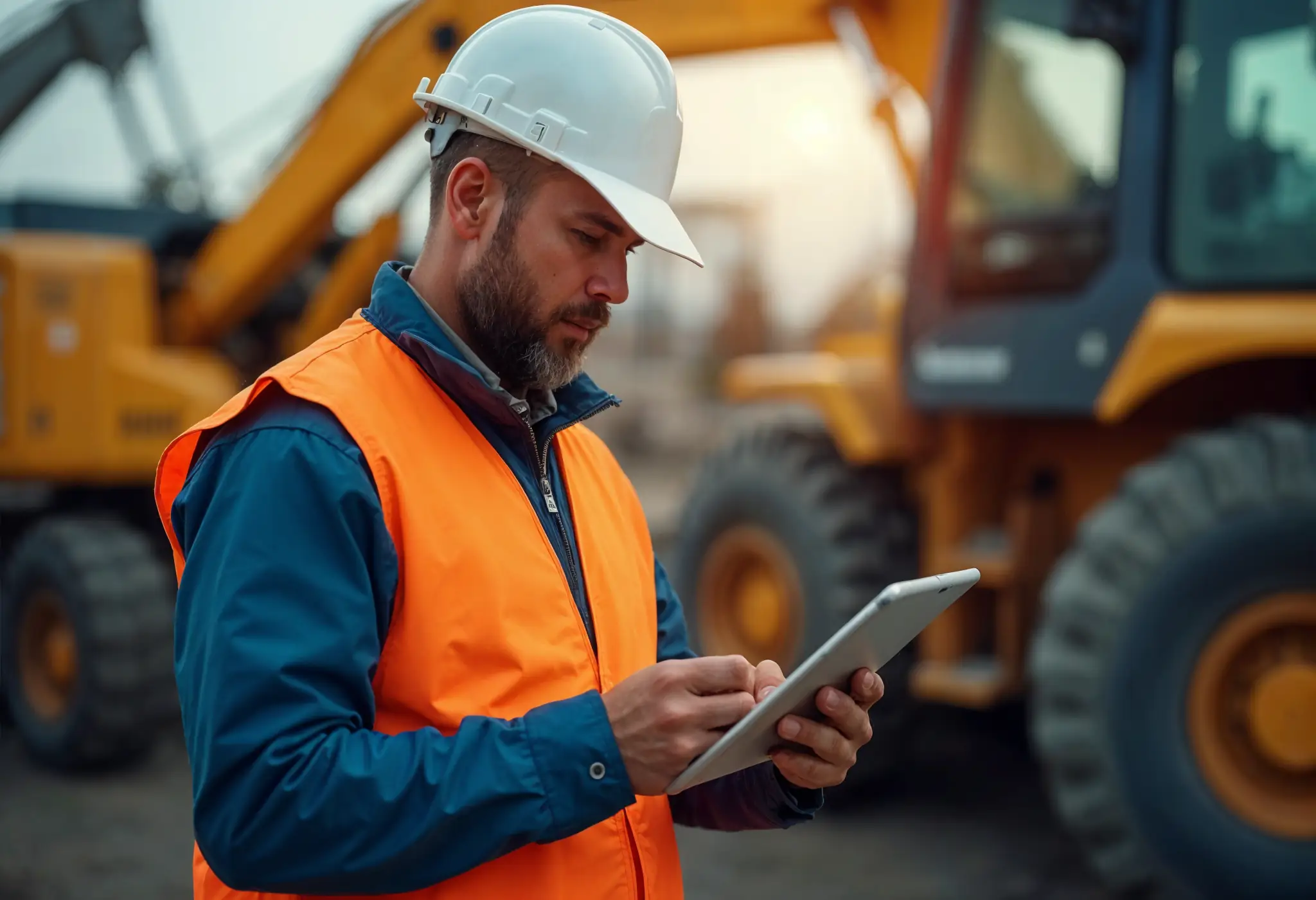
How to Select Construction Machinery with Optimal Equipment Maintenance in Mind
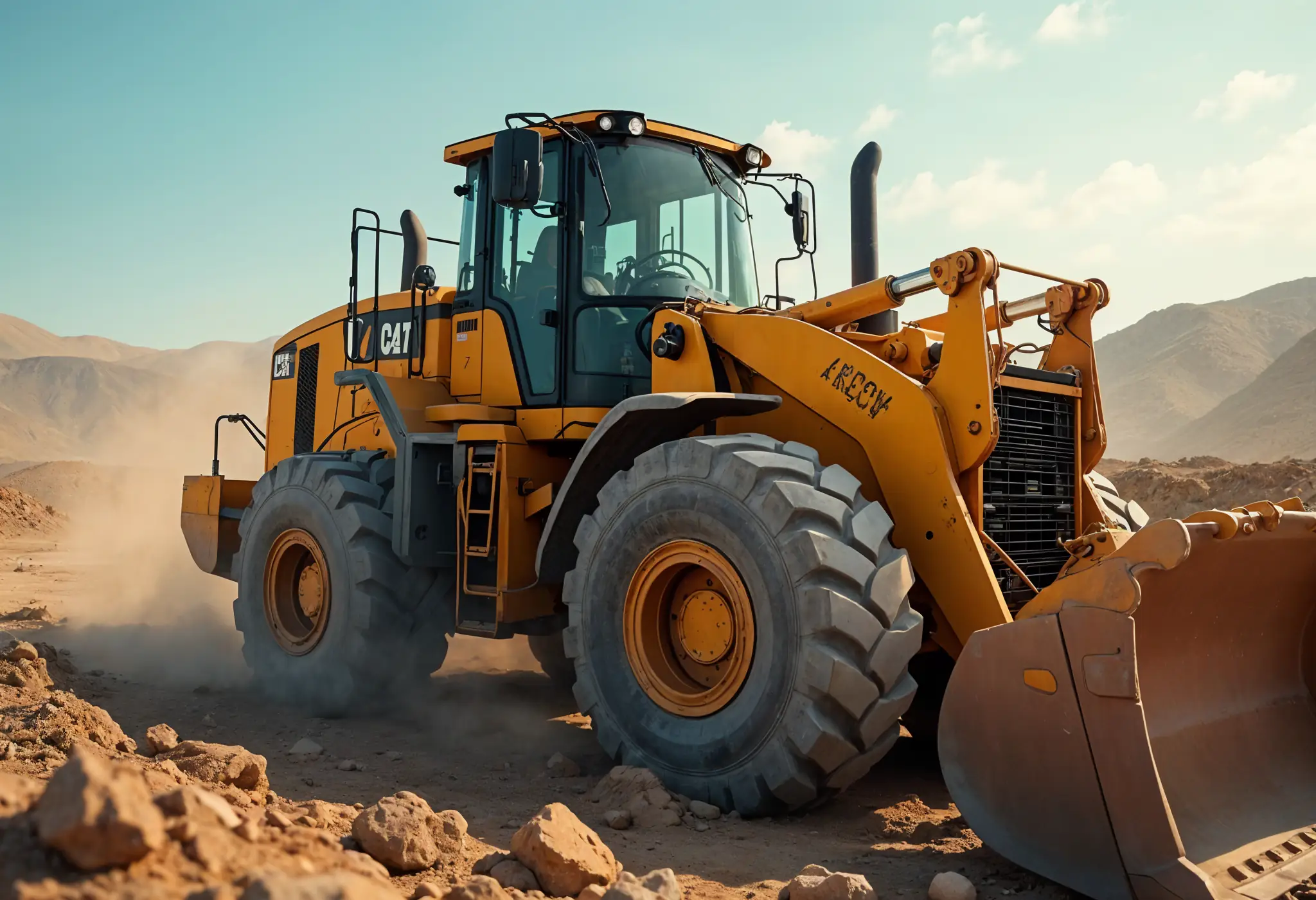
Top 25 Tips for Selecting Bulldozers for Construction Sites
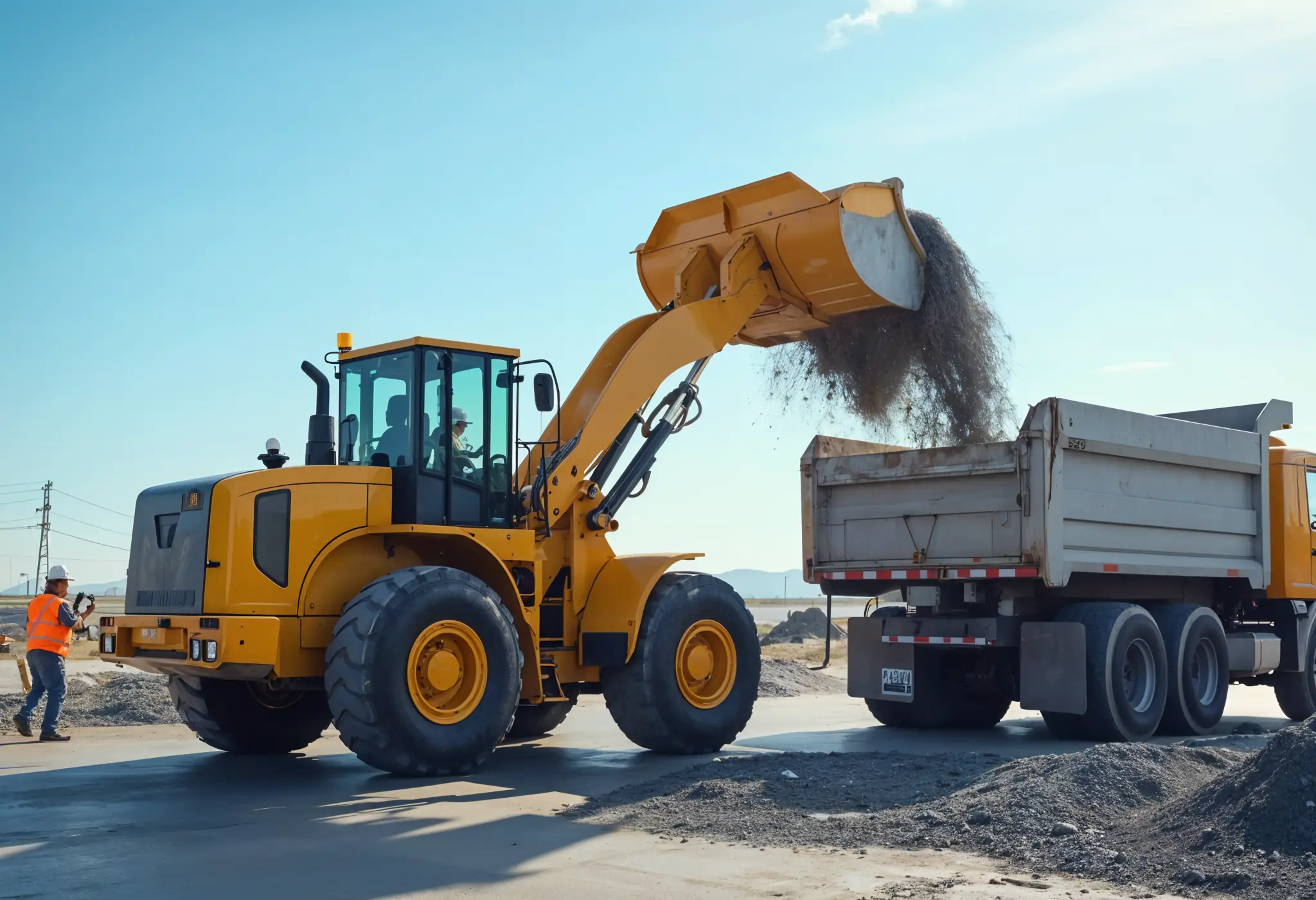
Which Construction Loader is Best for Your Project Needs?
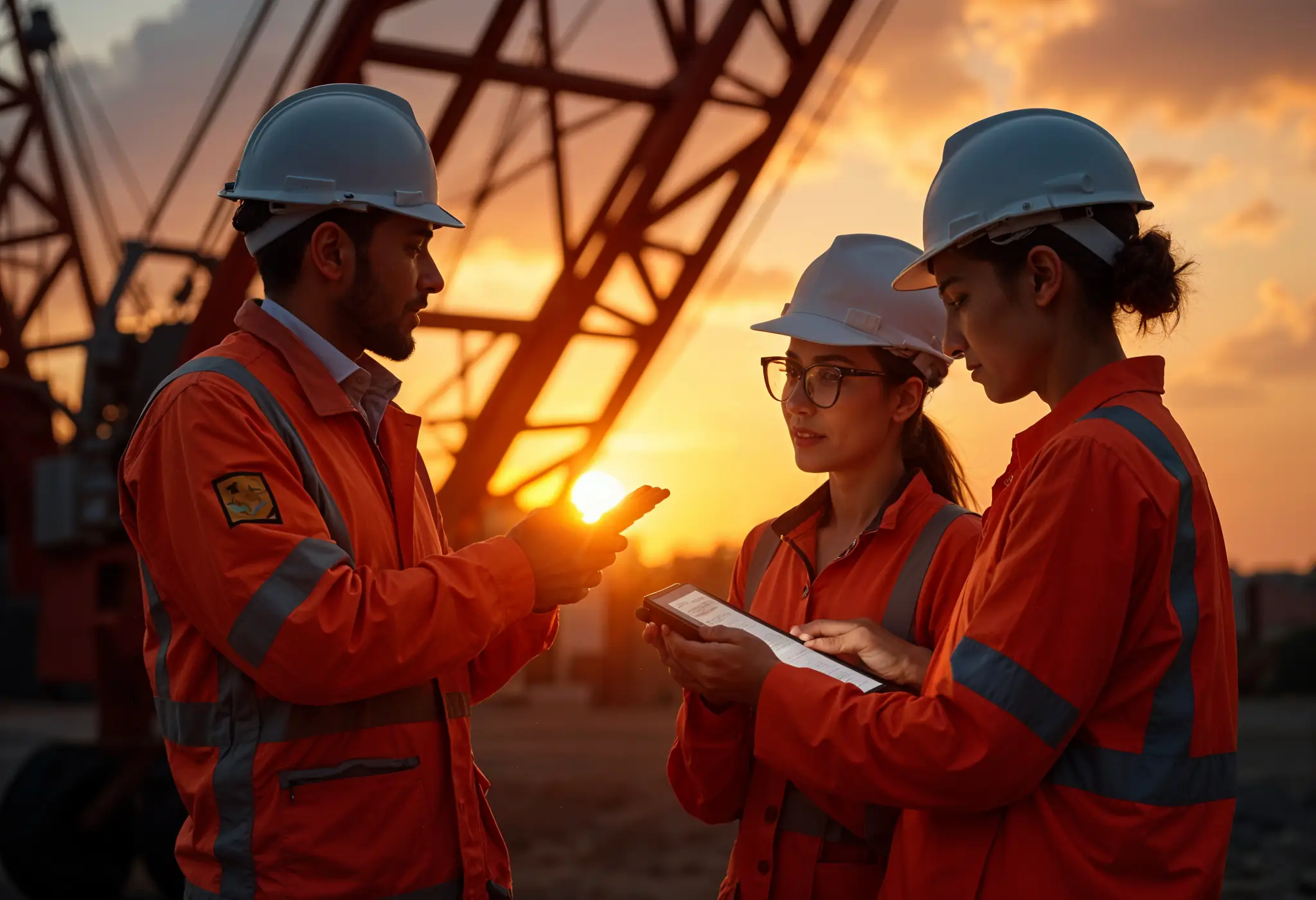
4 Key Steps to Form a Construction Machinery QC Team
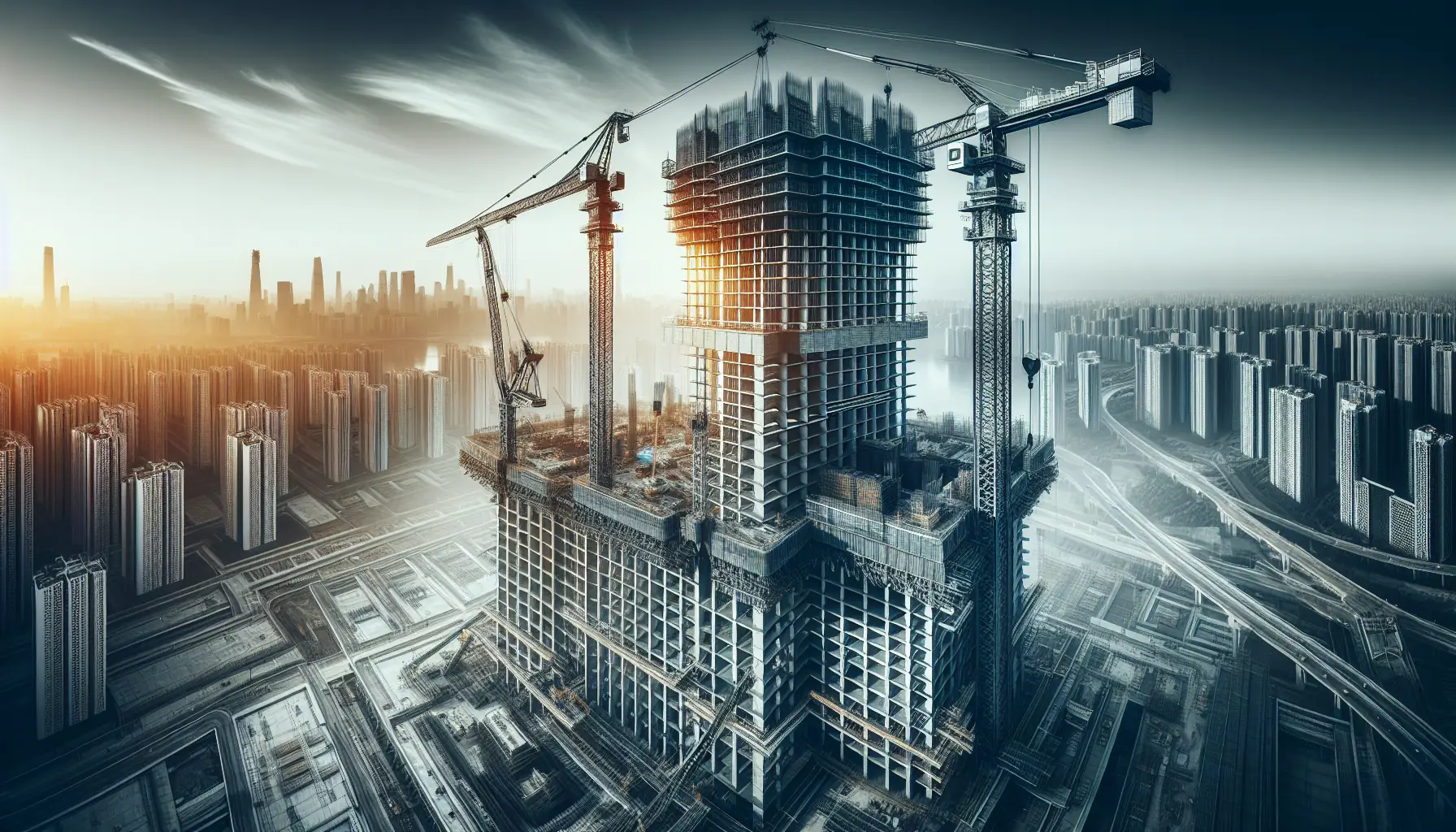
15 Essential Tips for Selecting the Perfect Crane for Construction
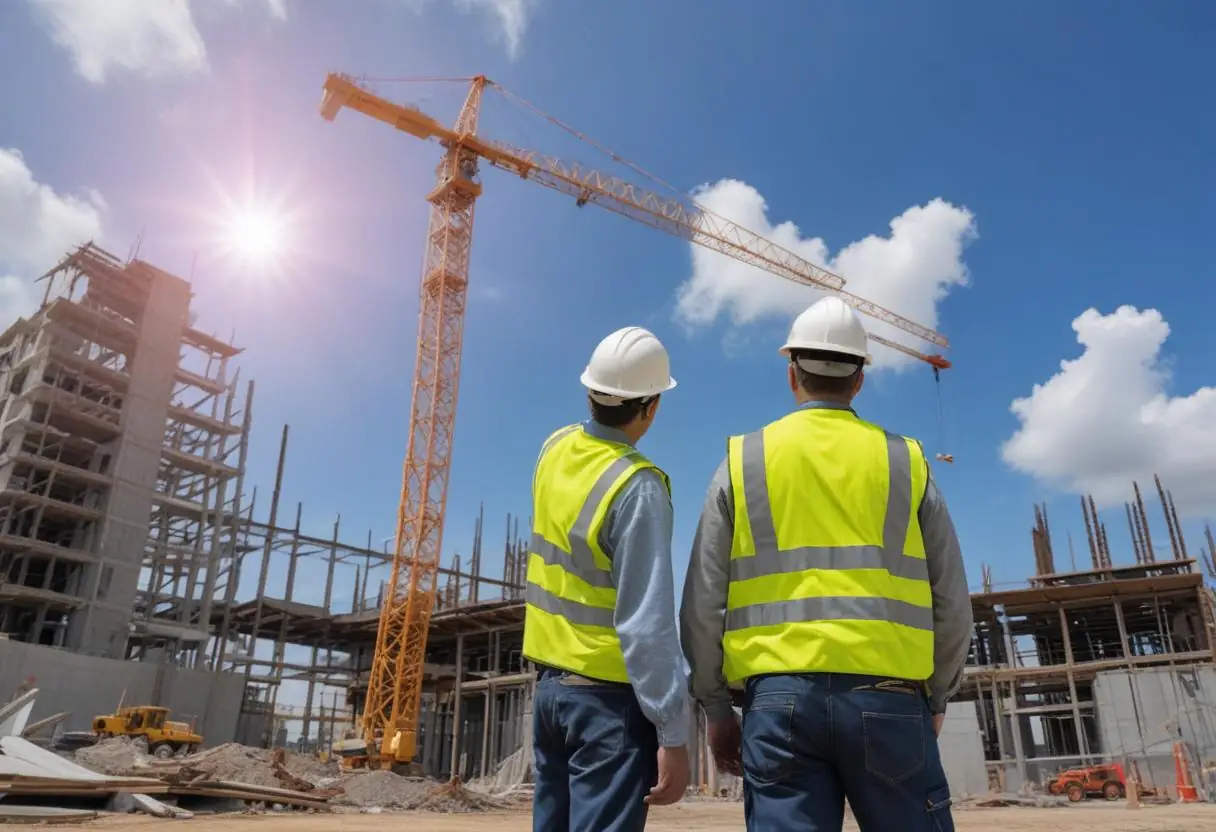
Maximize Savings: Multi-Purpose Construction Machinery for Lower Costs
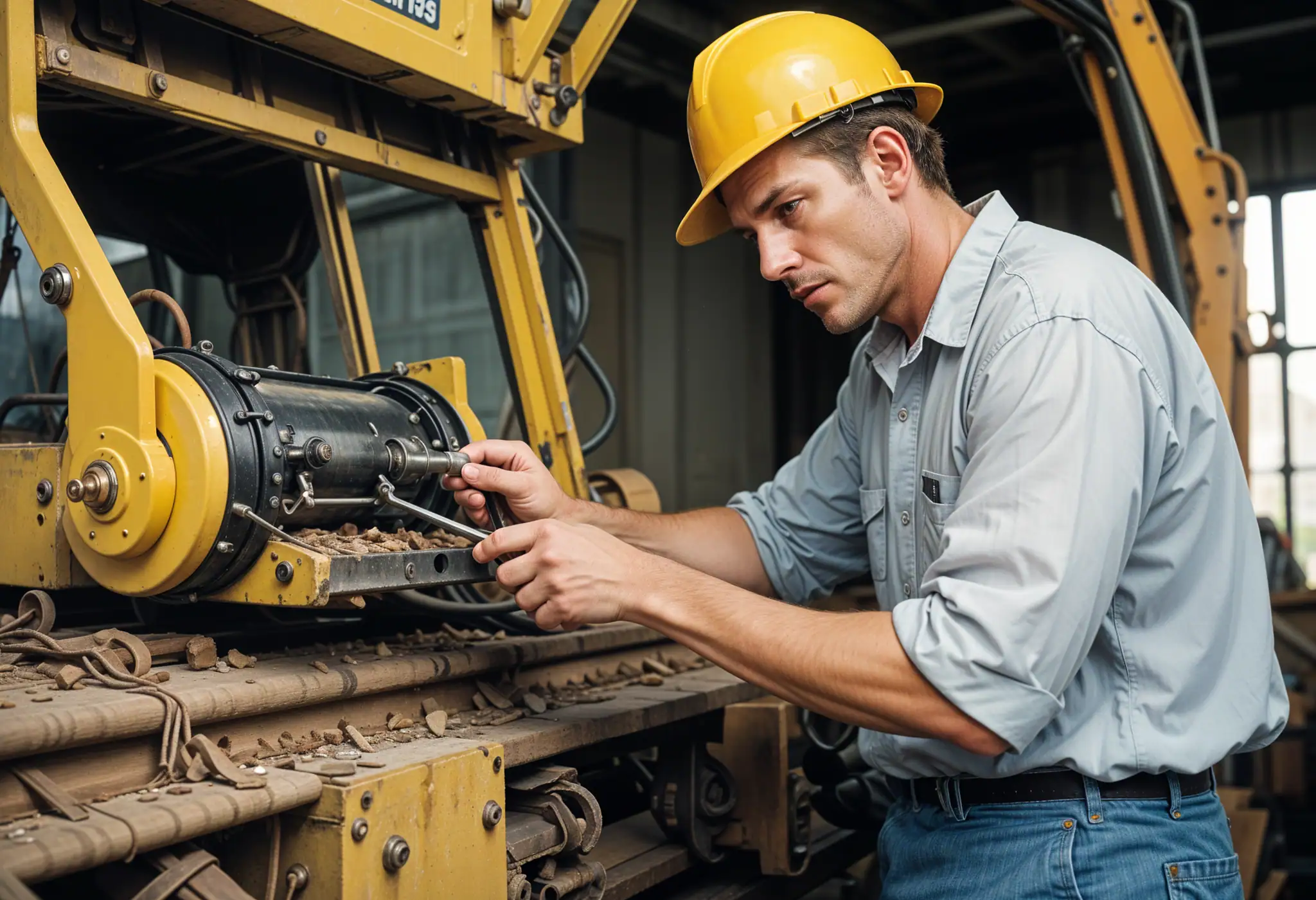
Affordable Heavy Equipment Parts: A Sourcing Guide
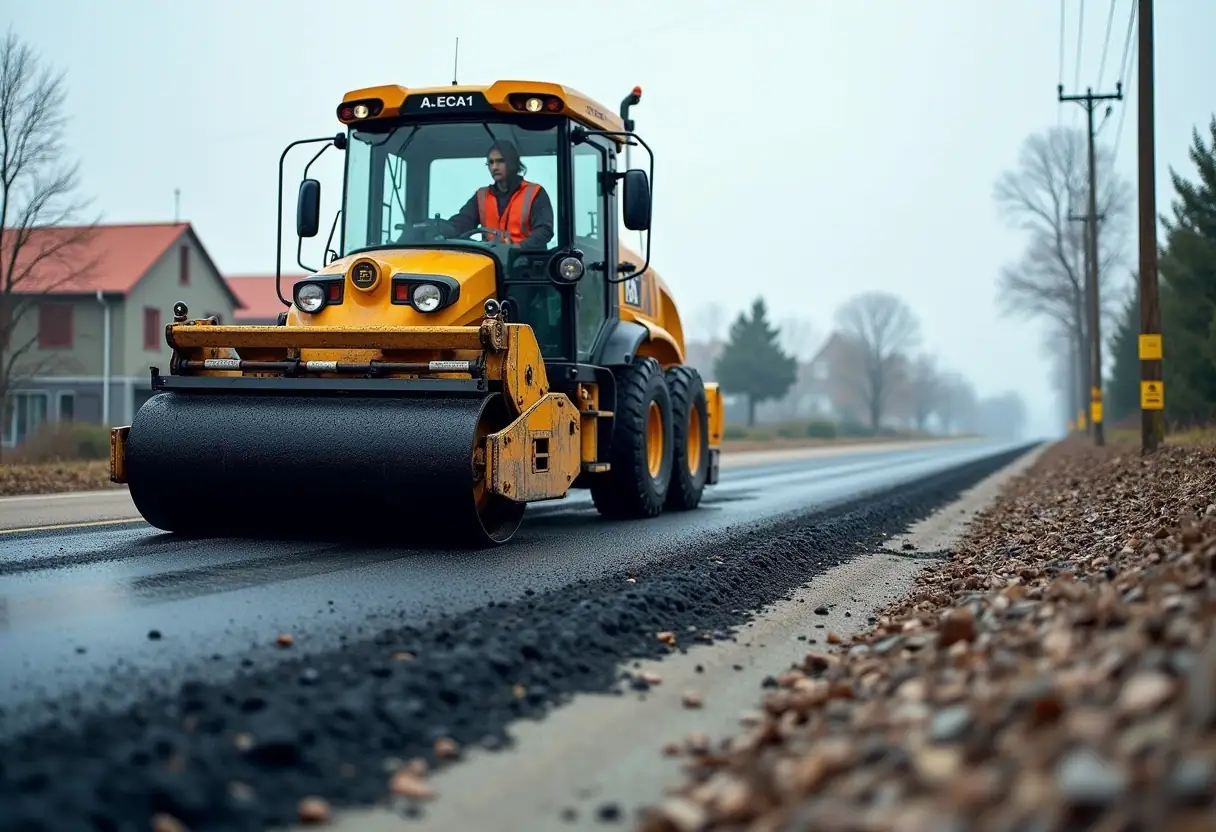
Choosing the Right Road Construction Equipment: A Complete Guide
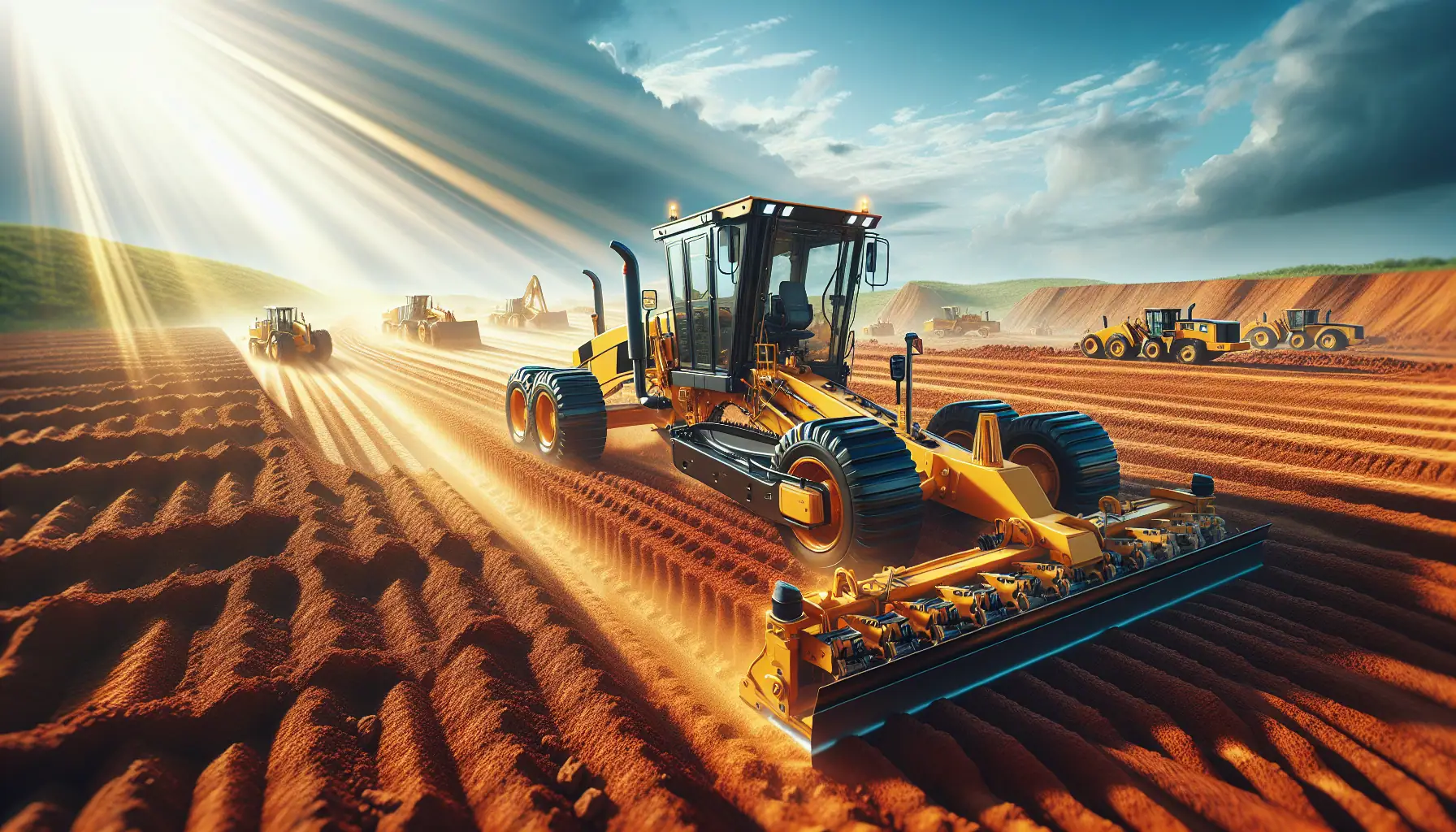
Motor Graders: Key Elements to Consider for Optimal Selection
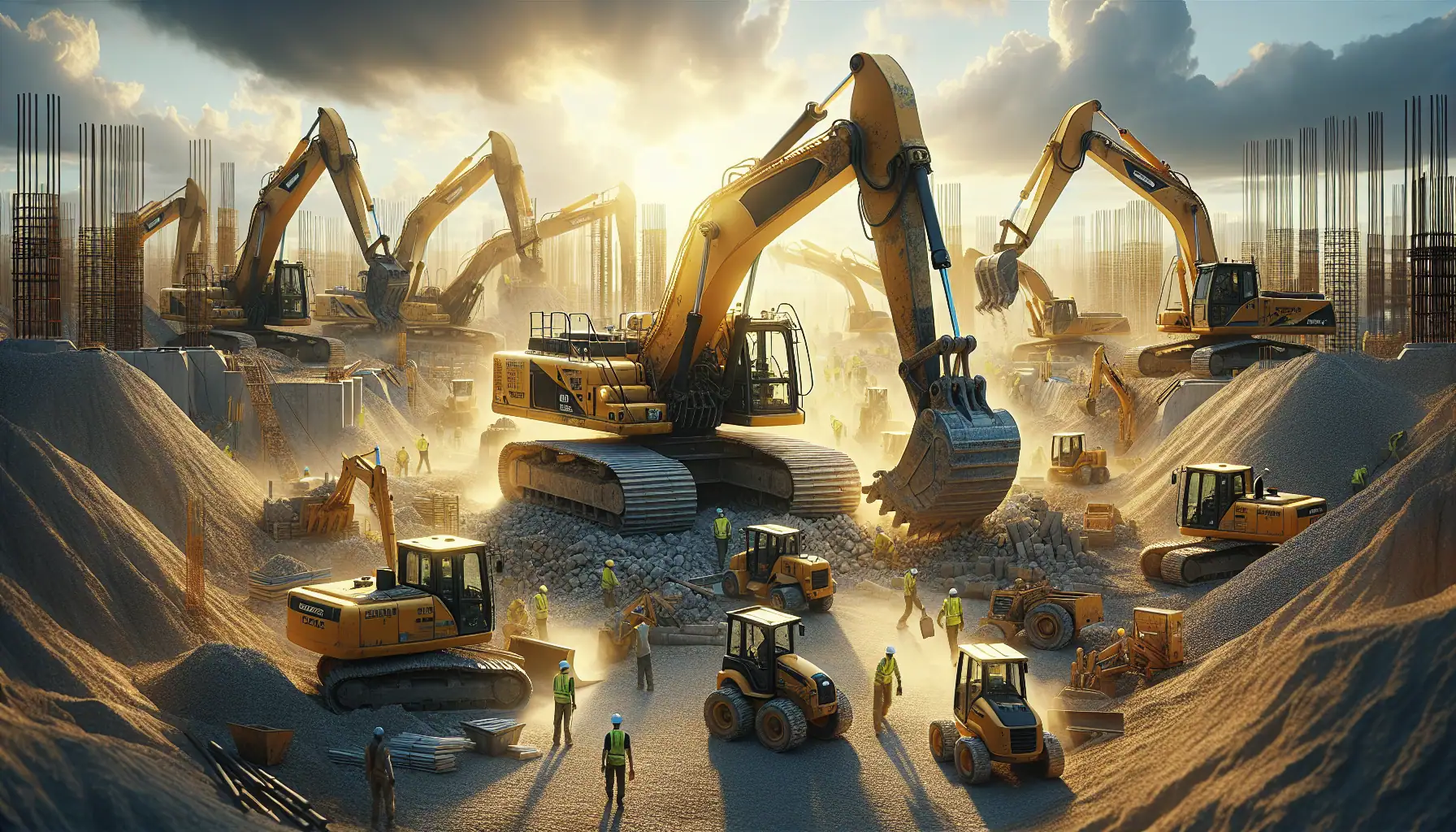
A Detailed Guide to Choosing Excavators for Construction Work
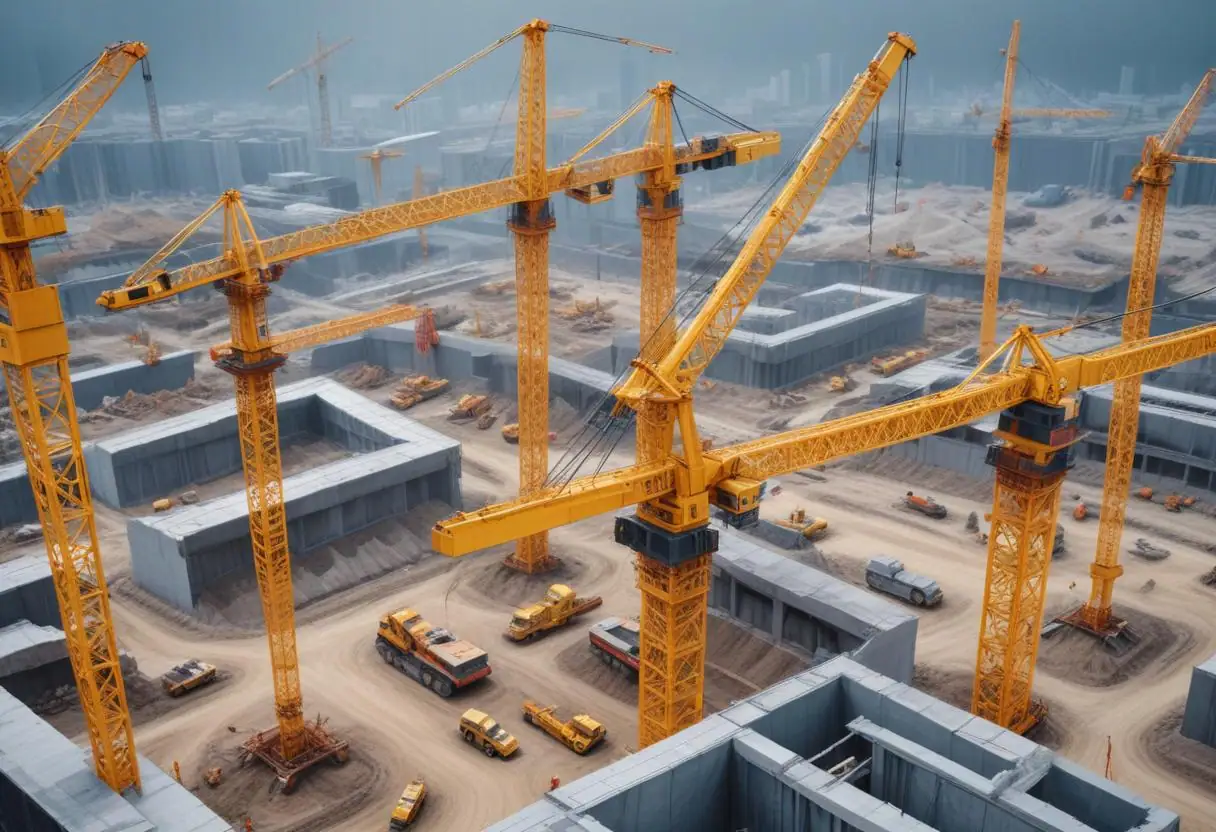
Top Tips for Choosing Cranes for Construction Projects
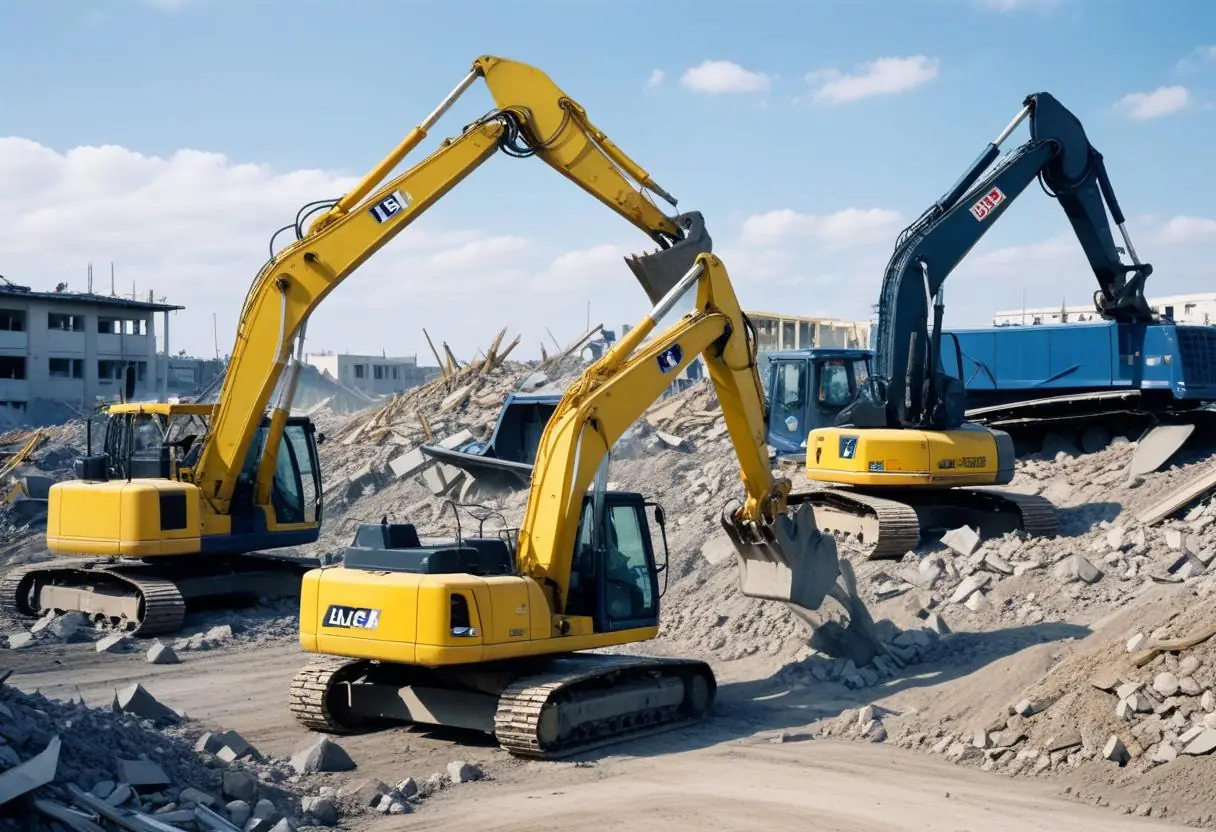
5 Top-Rated Demolition Machines for Construction Professionals
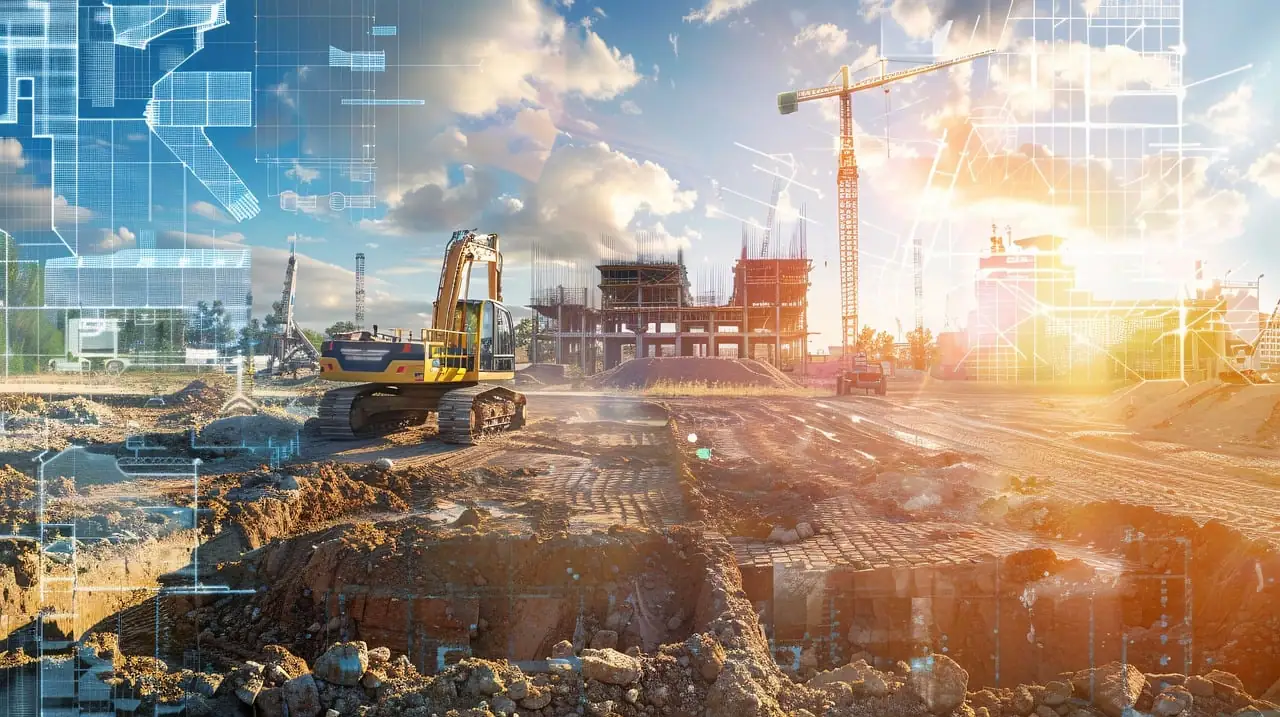
Expert Tips on Choosing Earthmoving Equipment for Large Projects
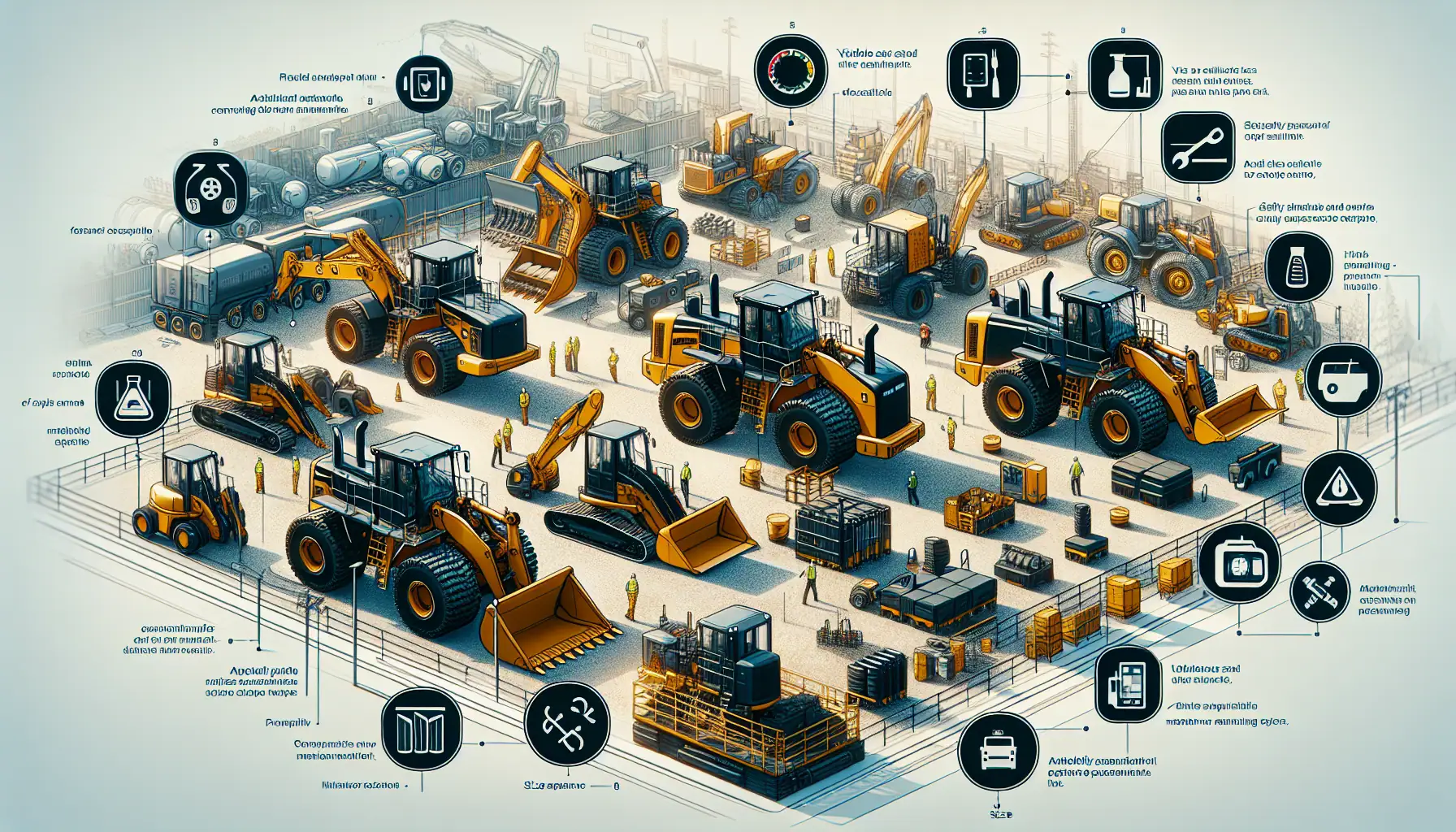
Top Functional Criteria for Selecting Heavy Construction Equipment
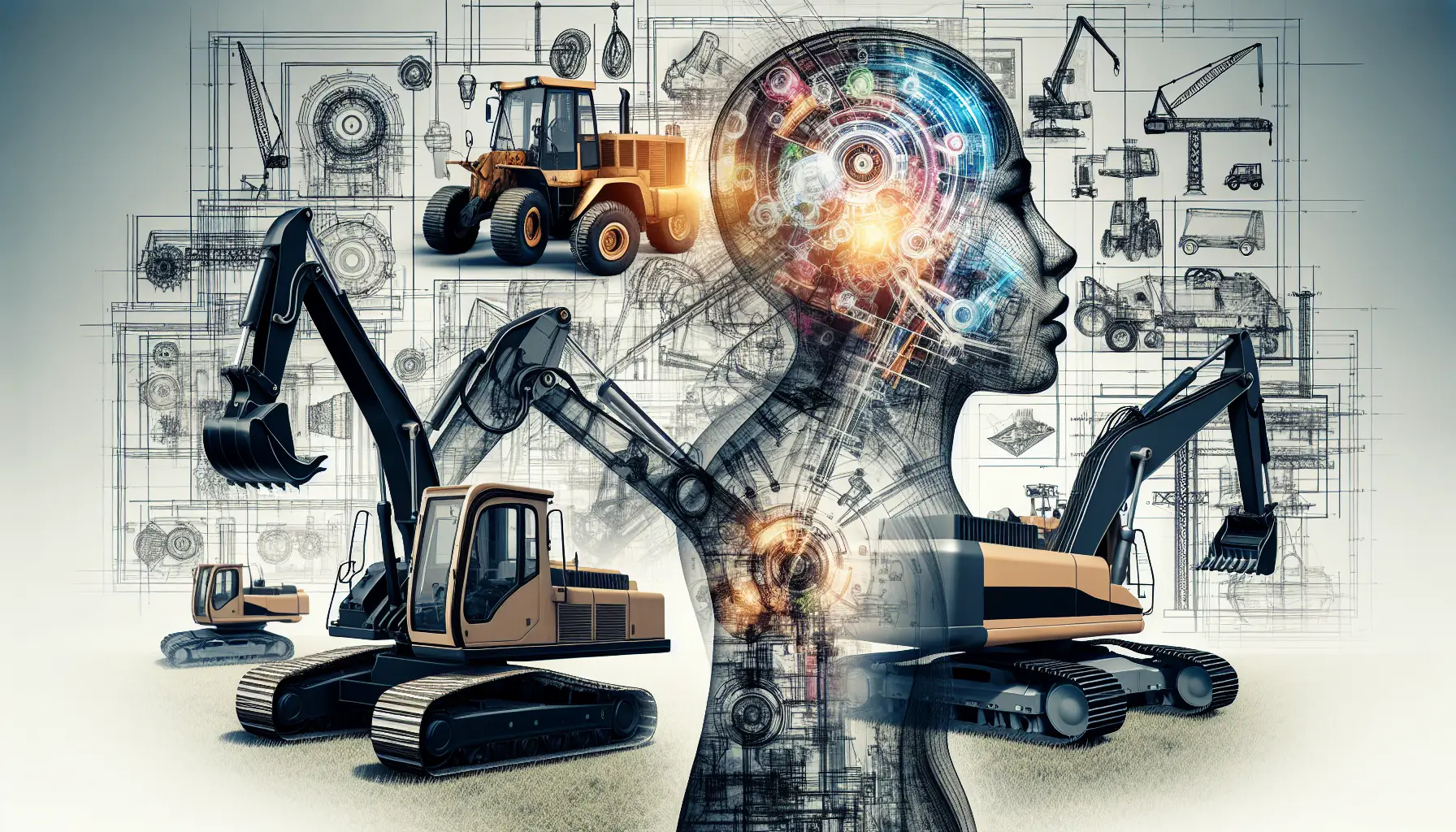
Construction Machinery: Detailed Guide to Equipment Specifications
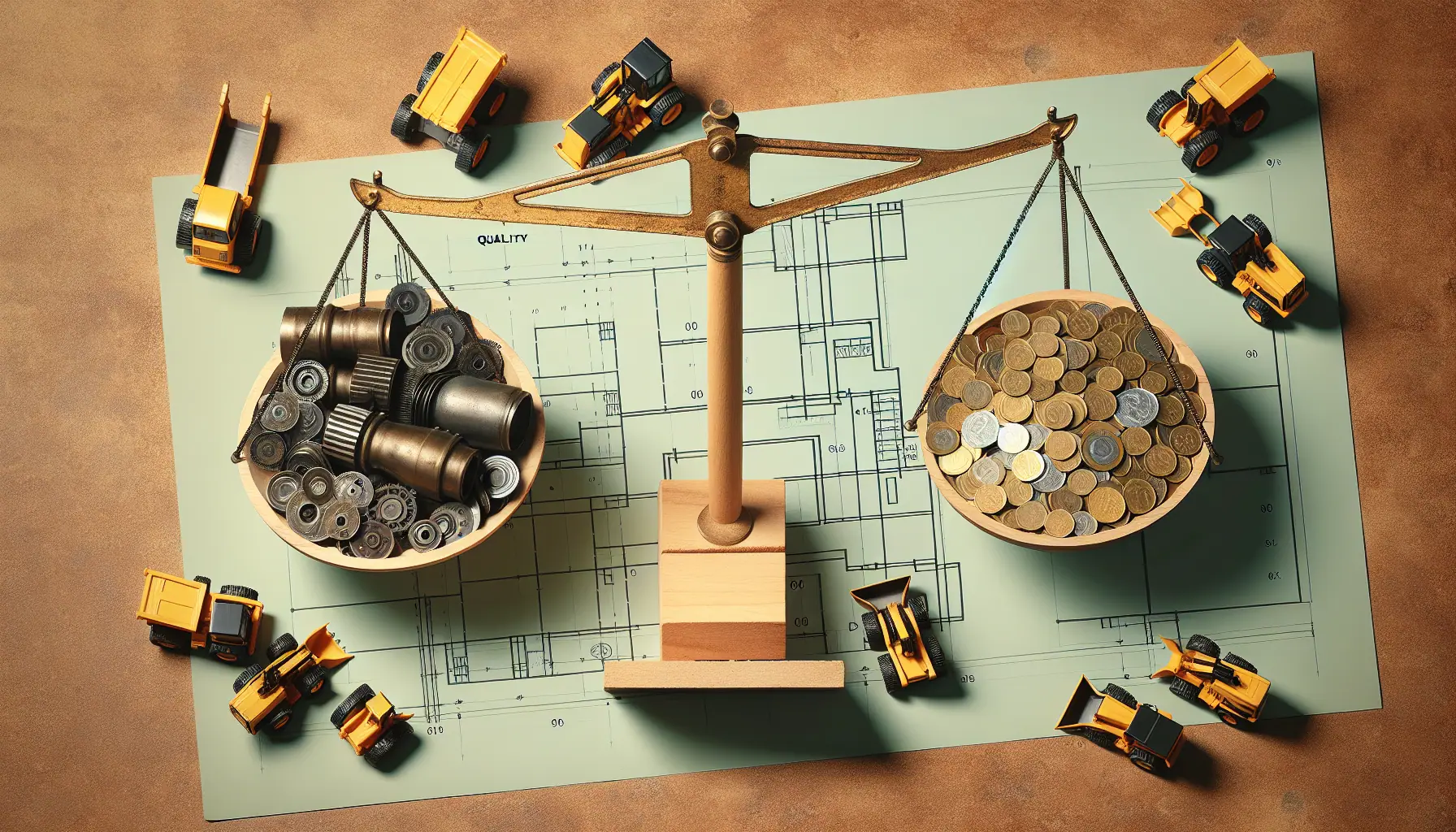
Heavy Machinery Prices: Key Factors in Cost and Quality Balance
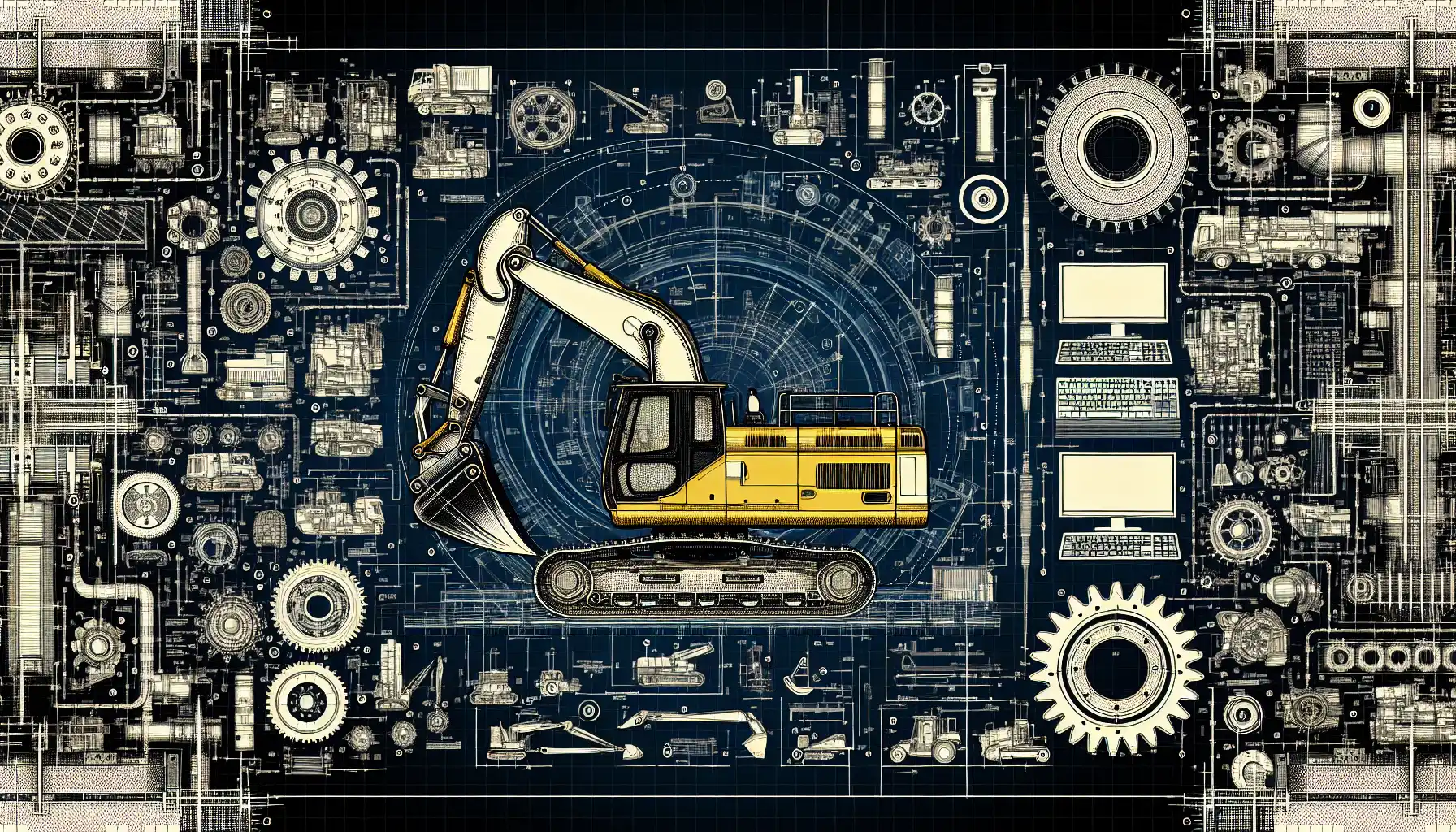
Best Construction Heavy Equipment Brands: Pros and Cons
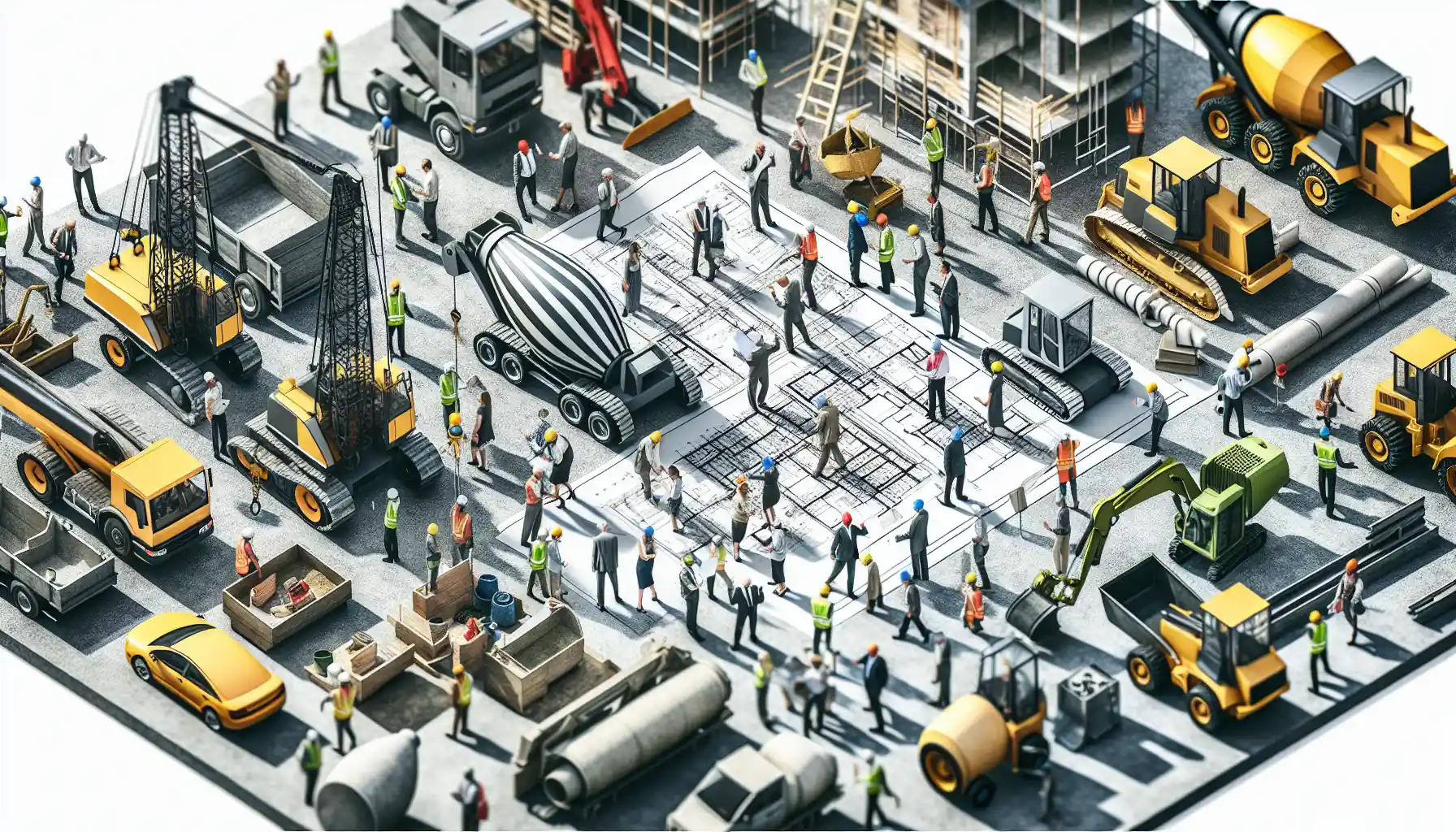
Construction Site Equipment: How to Determine Your Requirements
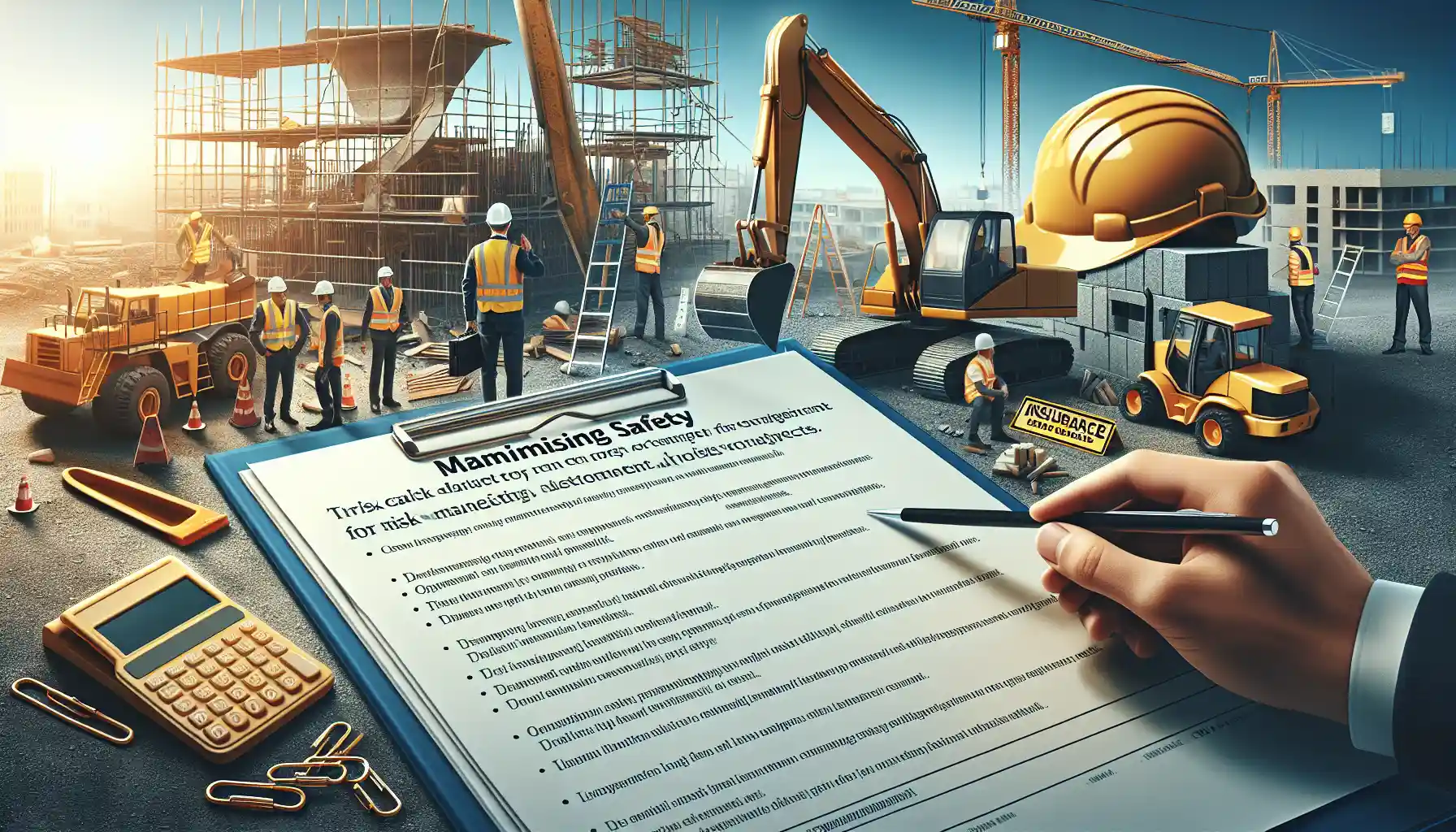
Maximizing Safety: Risk Management for Construction Projects
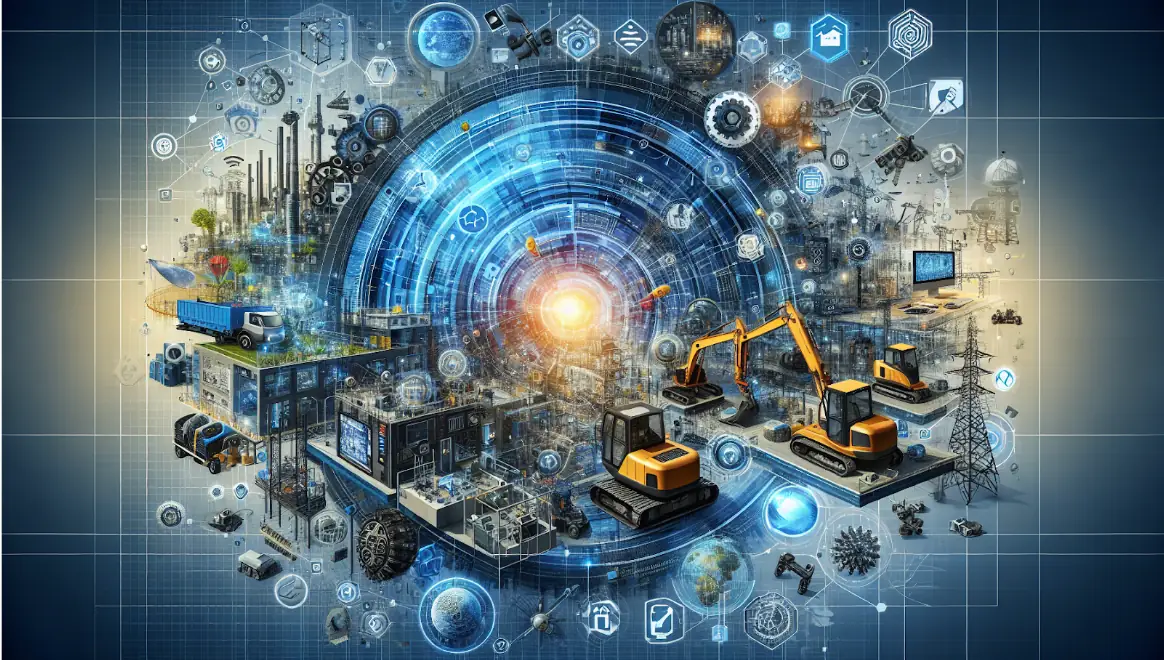
Innovations in Construction: Transforming Machinery and Equipment
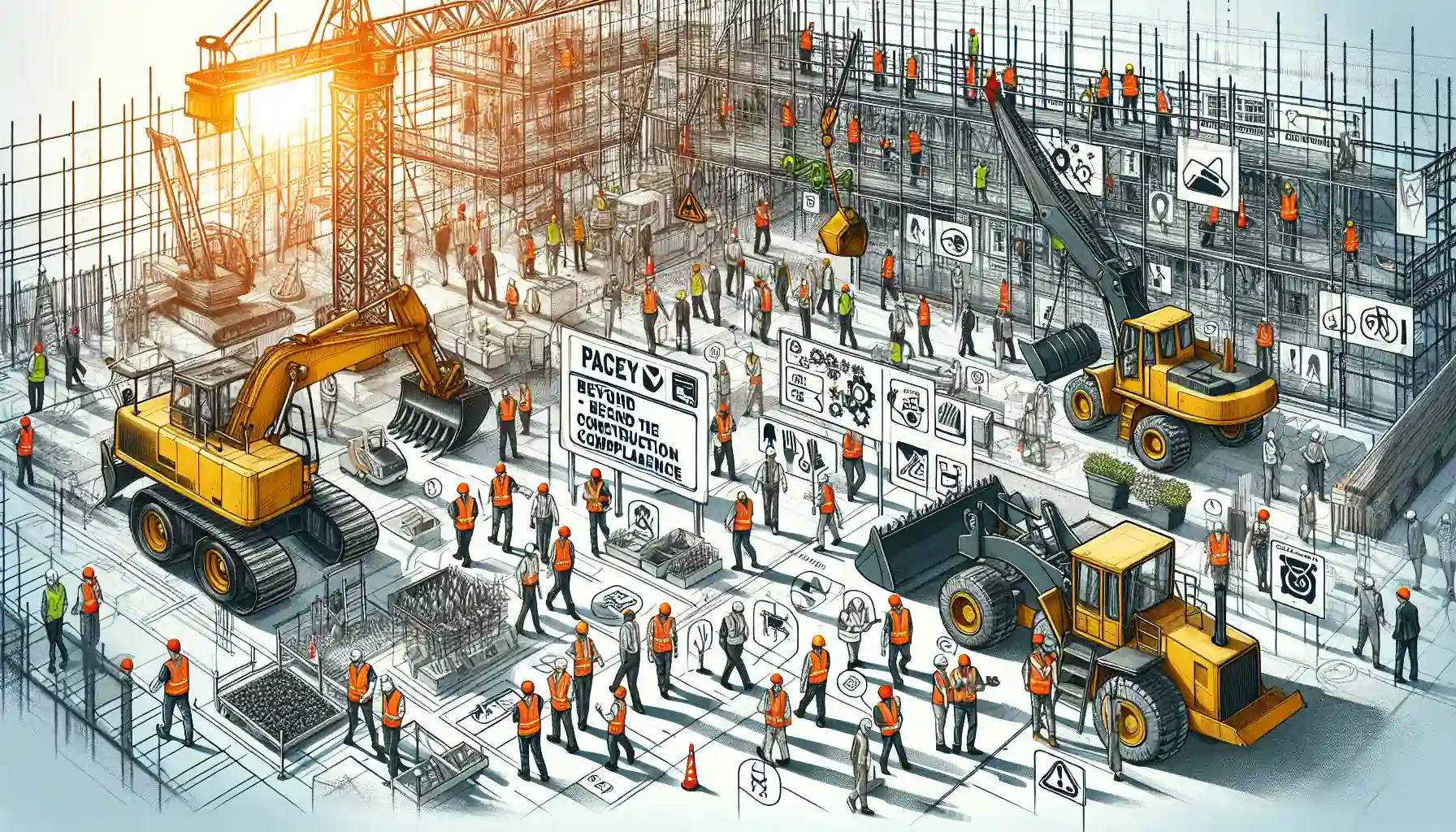
Heavy Equipment Safety: Beyond the Basics in Construction Compliance
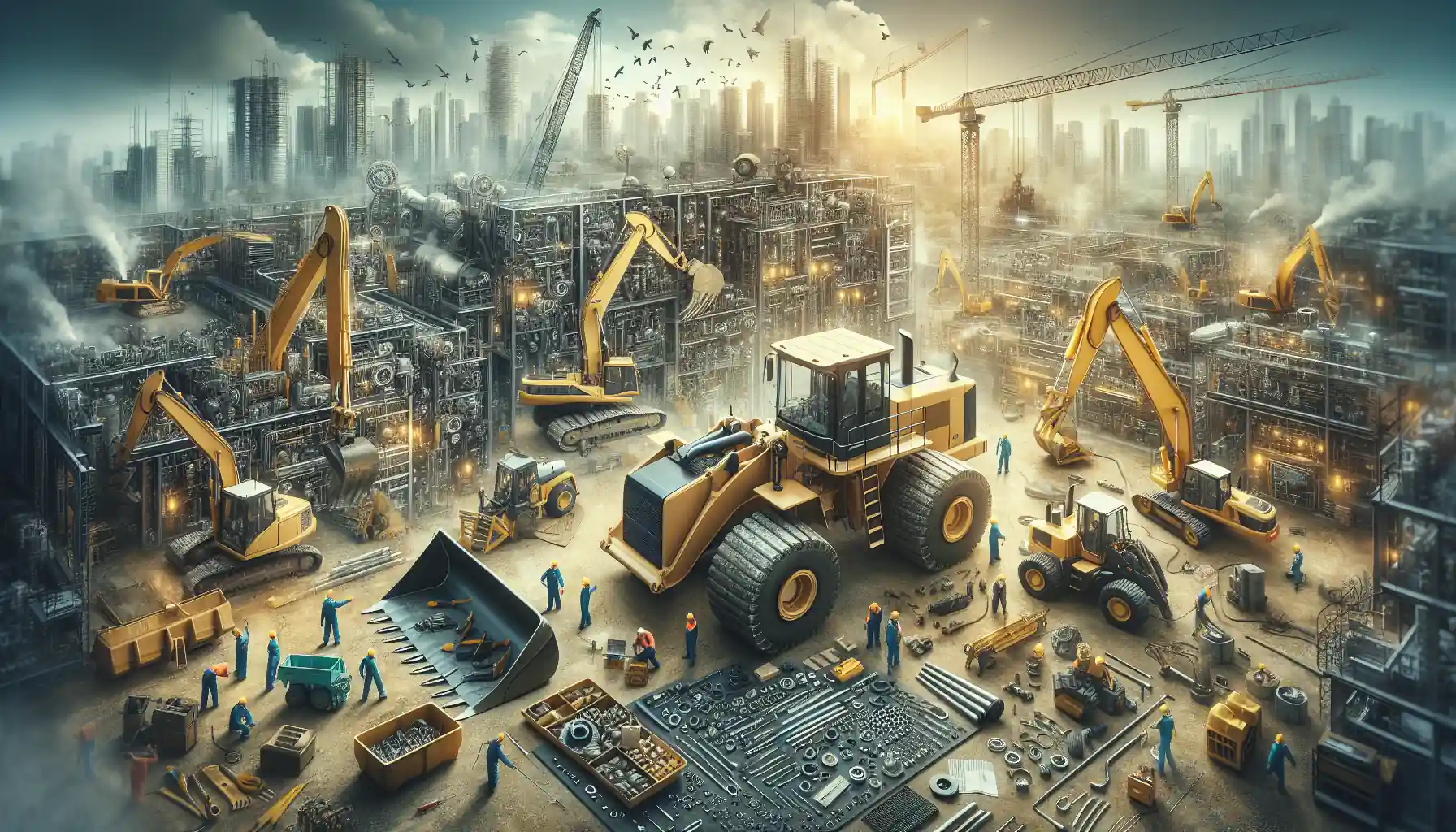
The Essential Handbook for Construction Equipment Repair and Maintenance
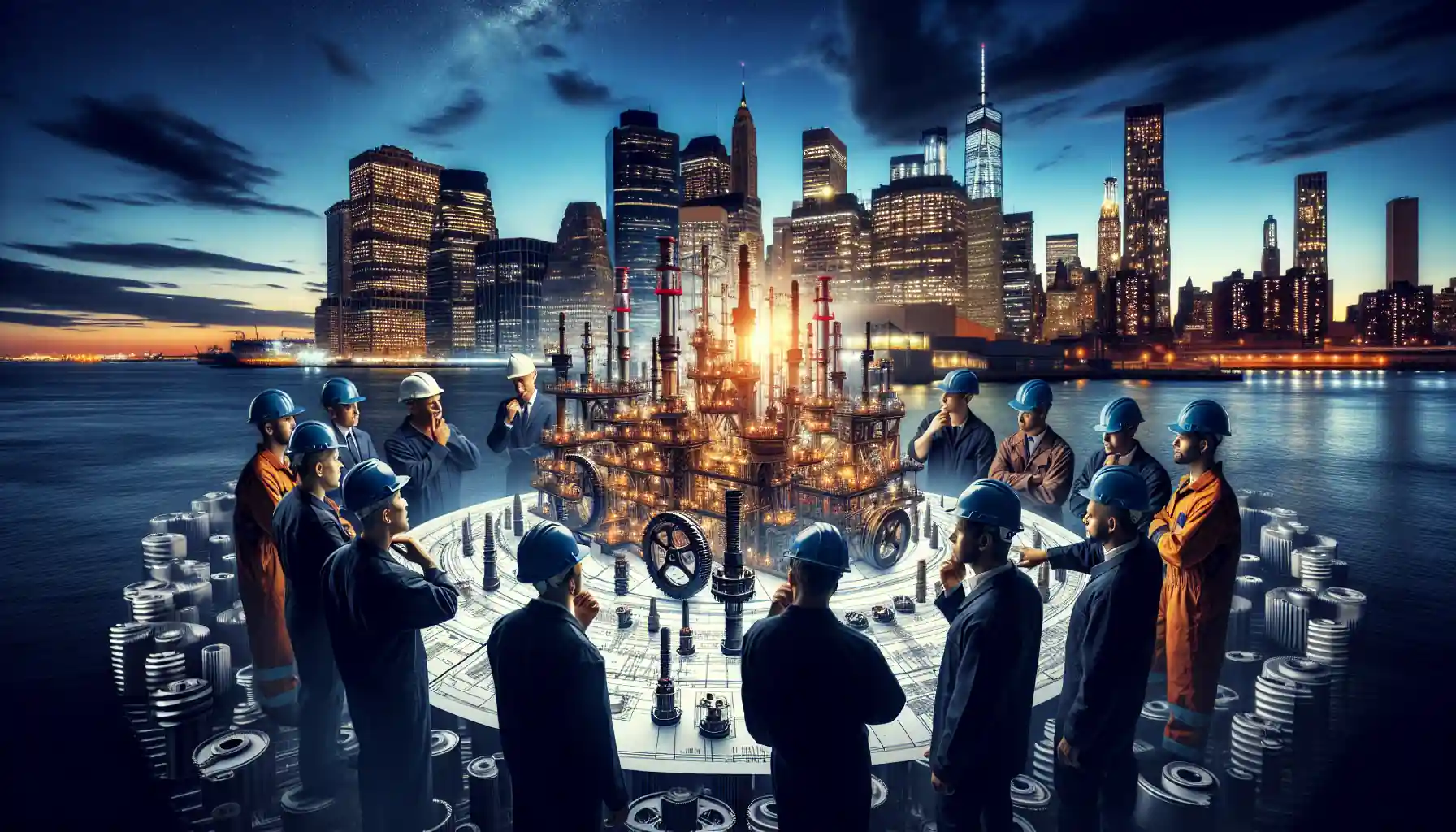
How to Efficiently Source Oil and Gas Machinery Parts in NYC
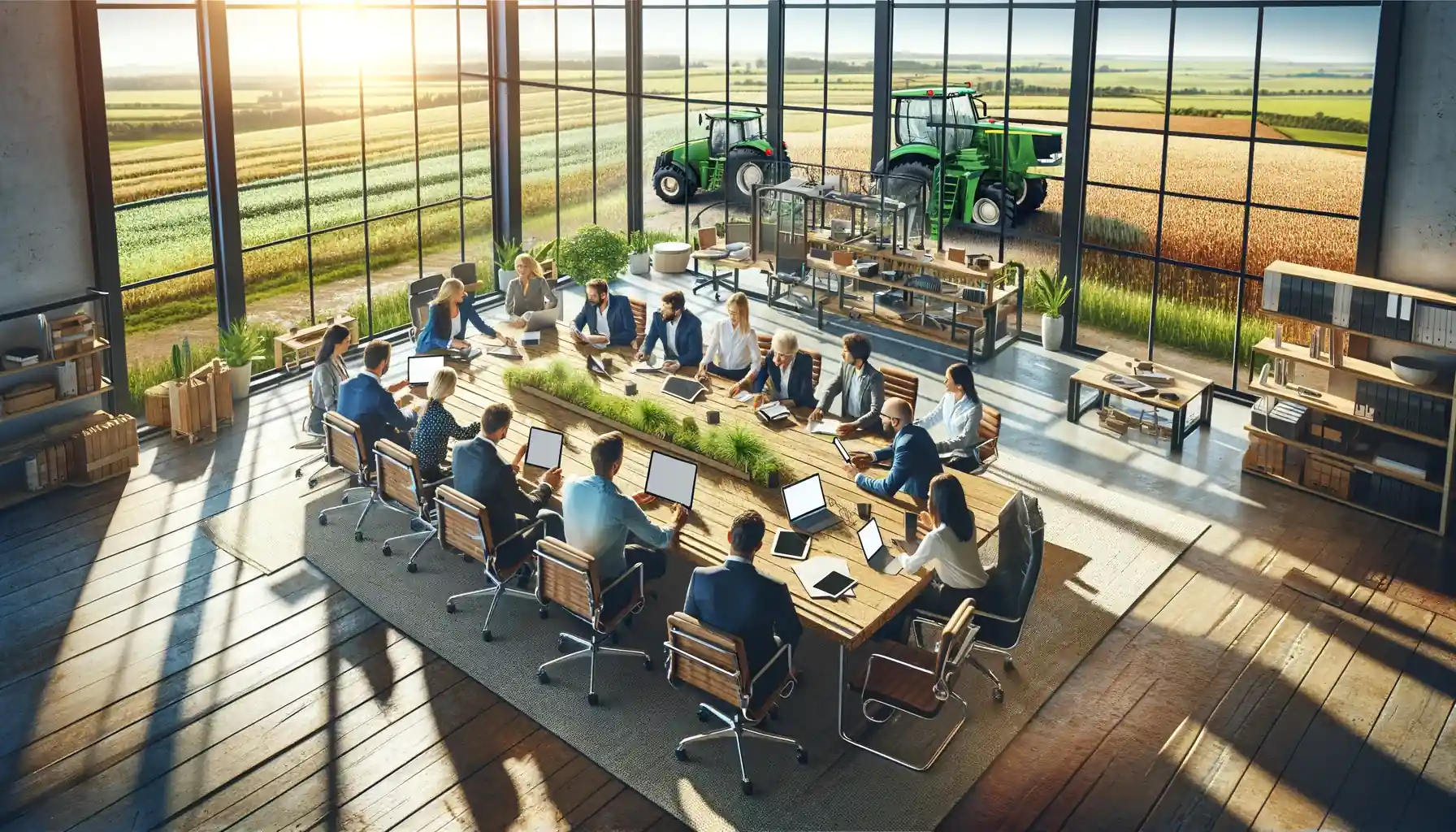
Essential Guide to Sourcing Agriculture Equipment Parts
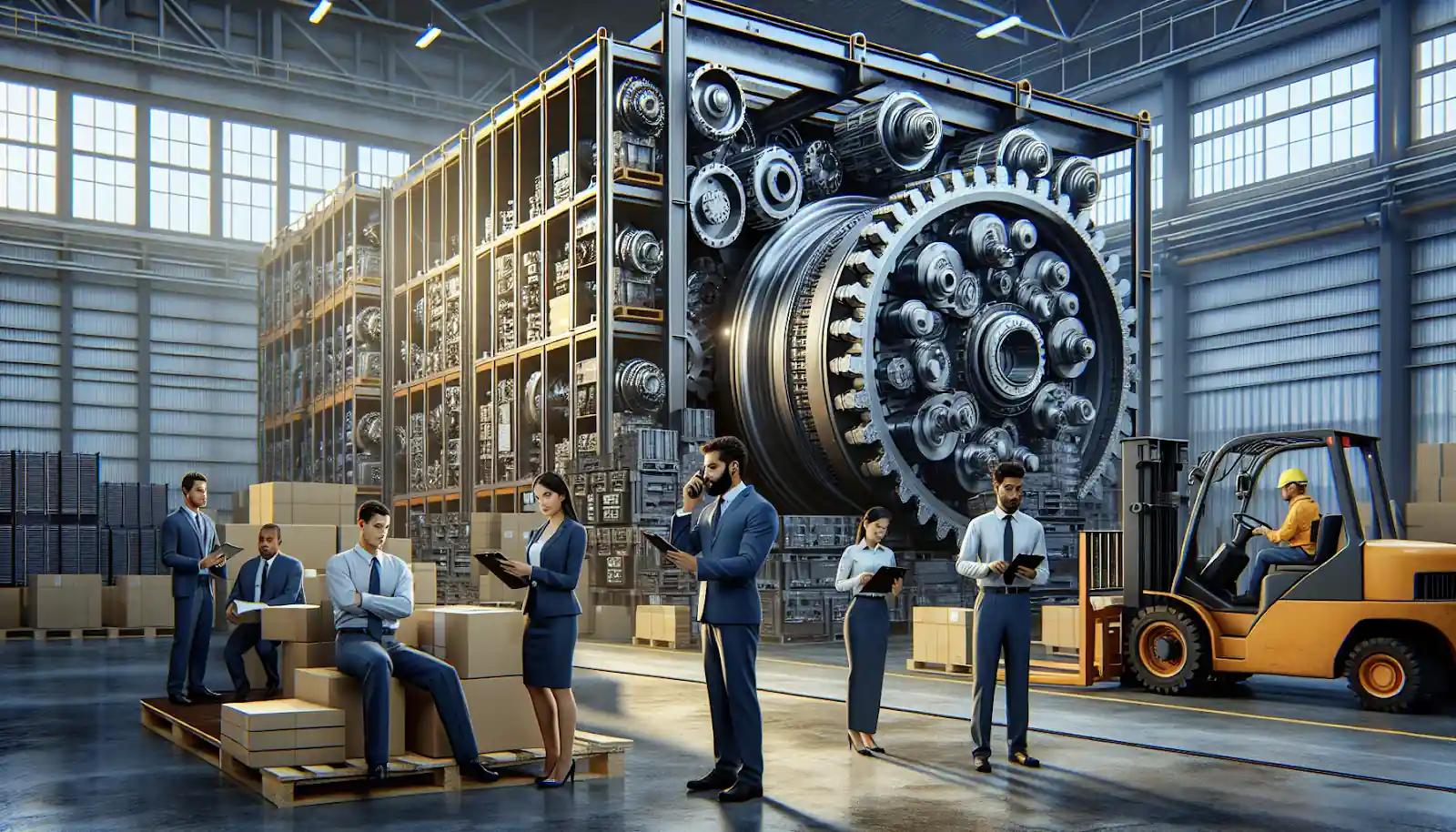
How to Source Mining Machinery Parts: Tips and Strategies
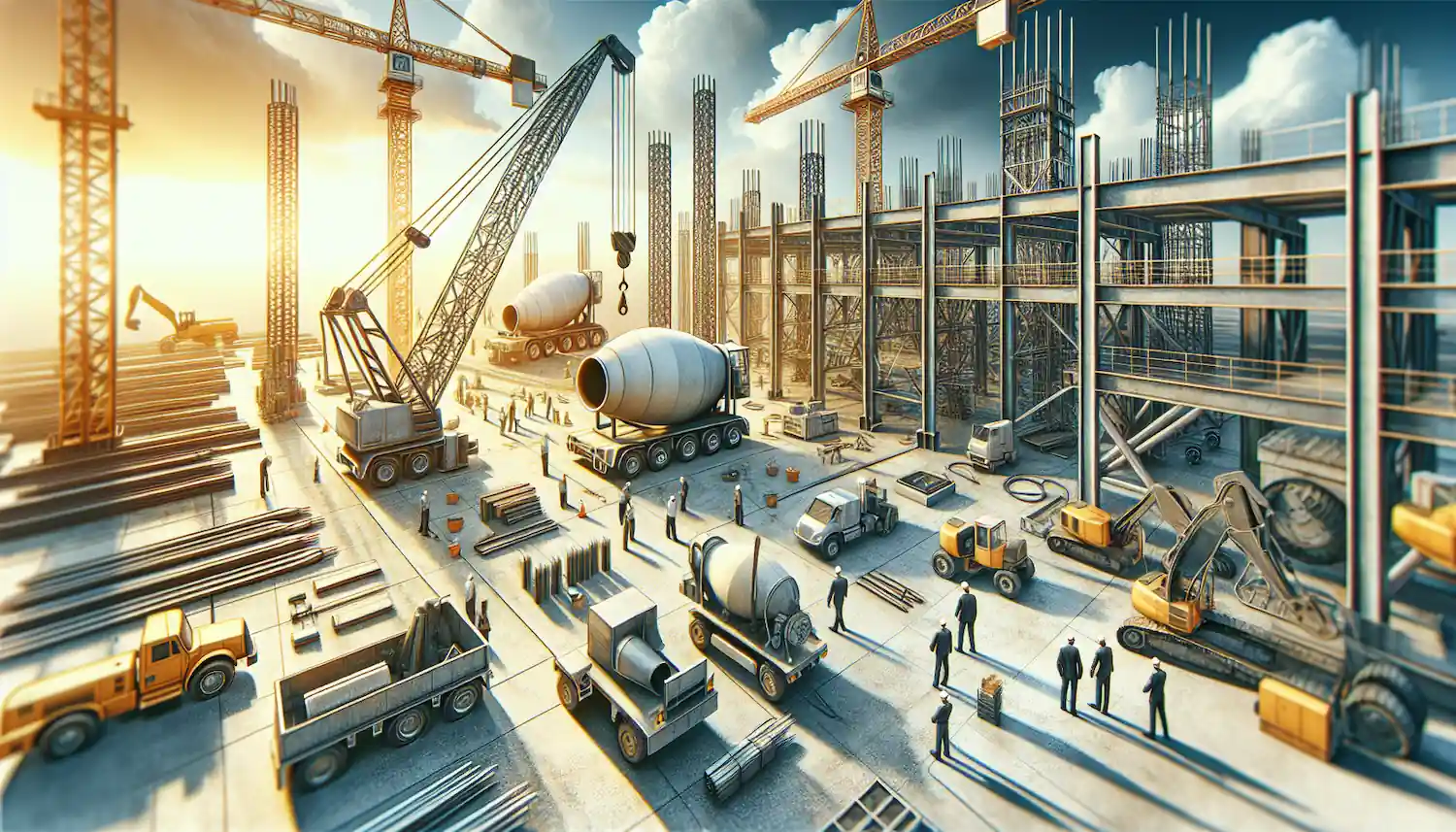