Smart Diagnostics Cut Heavy Equipment Failures by 73%
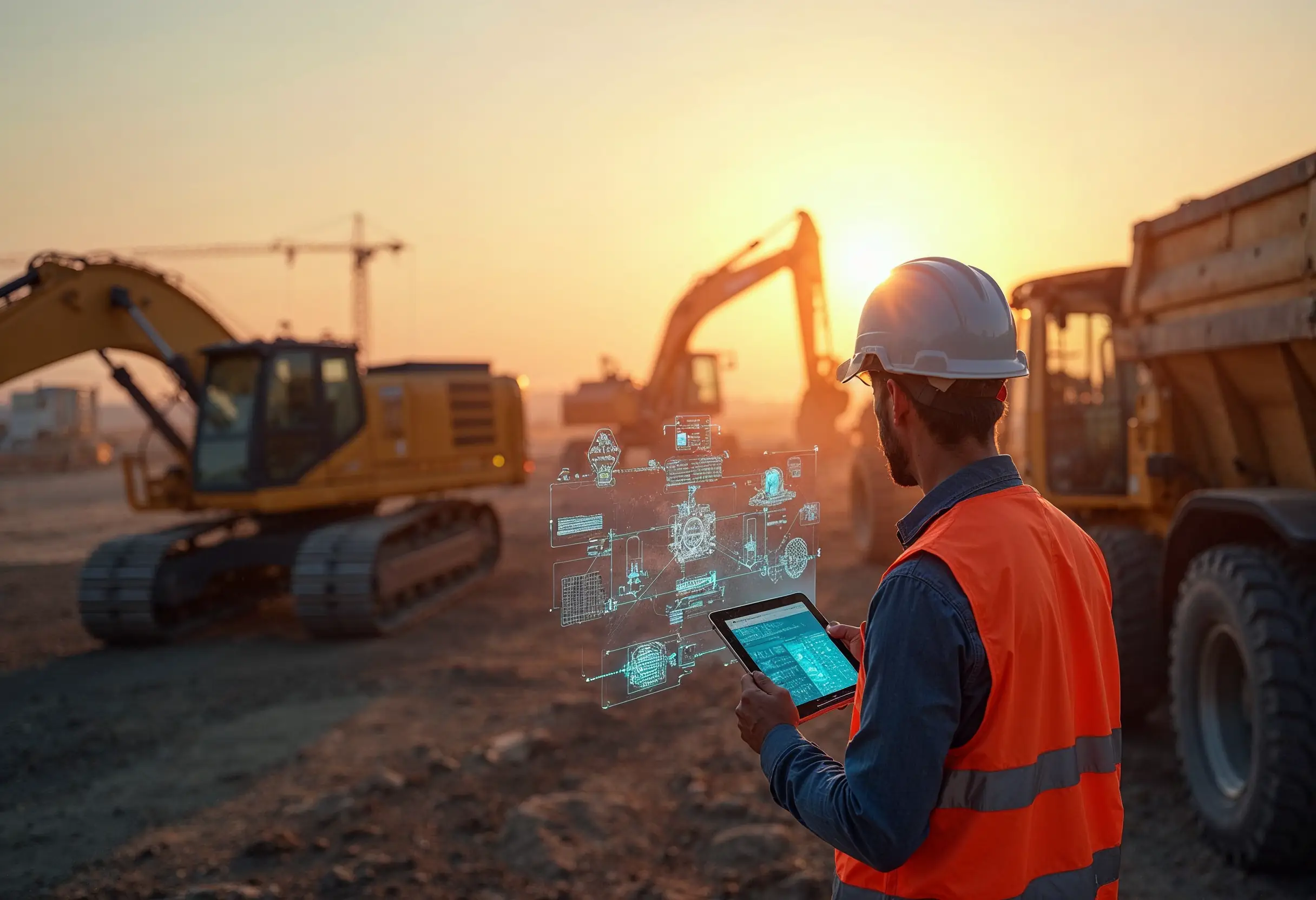
Equipment downtime costs manufacturers an average of $260,000 per hour. Smart diagnostics and predictive maintenance technologies protect your fleet from these costly disruptions while maximizing operational efficiency. Modern machine monitoring systems deliver measurable results across major industrial operations. Your maintenance strategy benefits from advanced condition monitoring systems that reduce unexpected failures by 30%, achieve 25% improvement in fuel efficiency, and boost fleet uptime by 20%.
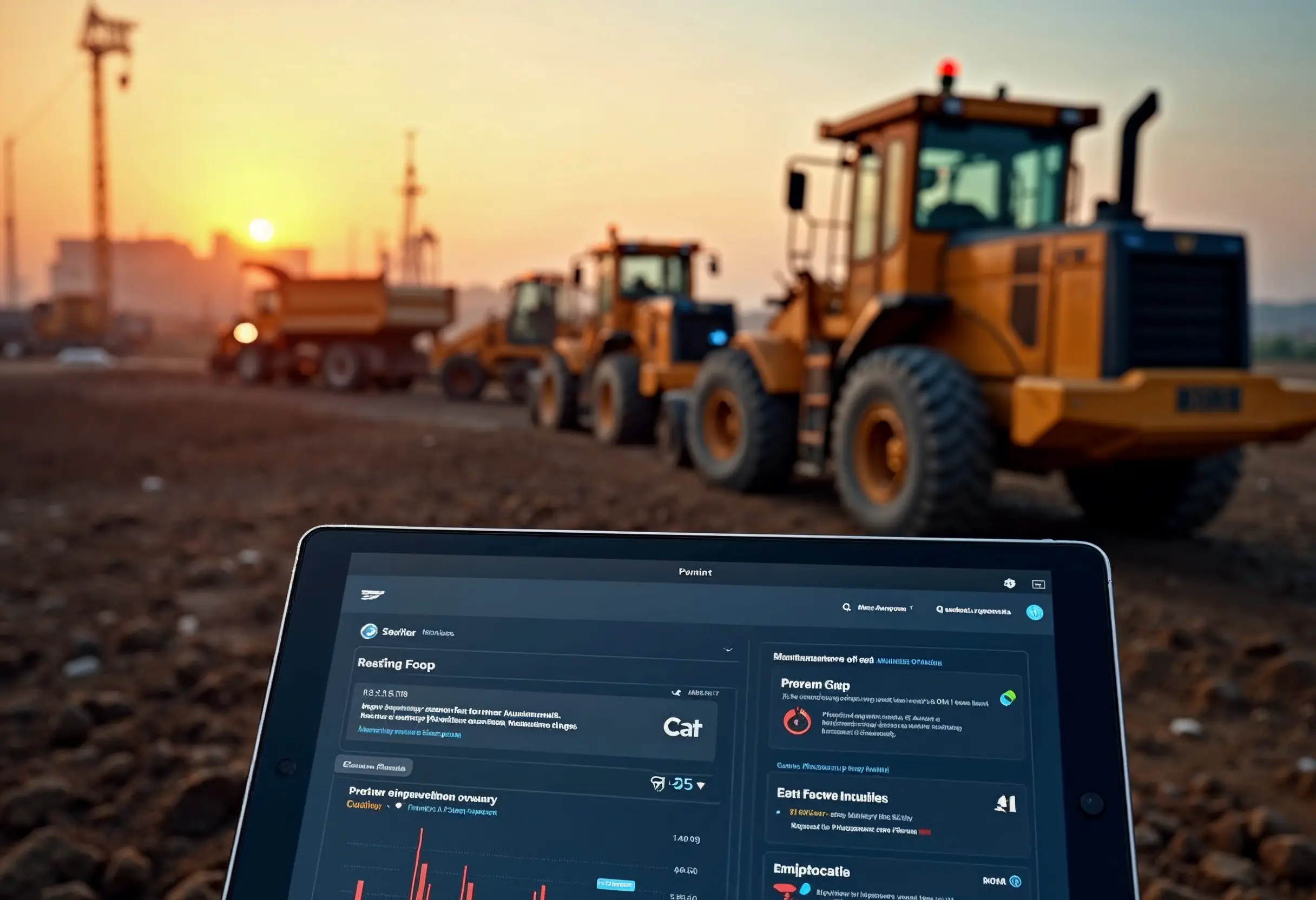
Predictive maintenance software detects potential issues before they impact your operations. Your asset health monitoring becomes precise and predictable through sensor-based analytics, cloud platforms, and anomaly detection algorithms.
This guide shows you the essential components of predictive maintenance systems, practical implementation steps for heavy equipment, and proven methods to measure success using machine data.
Modern Diagnostic Systems for Equipment Monitoring
Smart diagnostics mark a clear advancement over traditional equipment monitoring methods. Your machinery health monitoring becomes precise and predictable through sensor data analysis, enabling proactive repairs that prevent costly downtime.
Scheduled vs Smart Equipment Monitoring
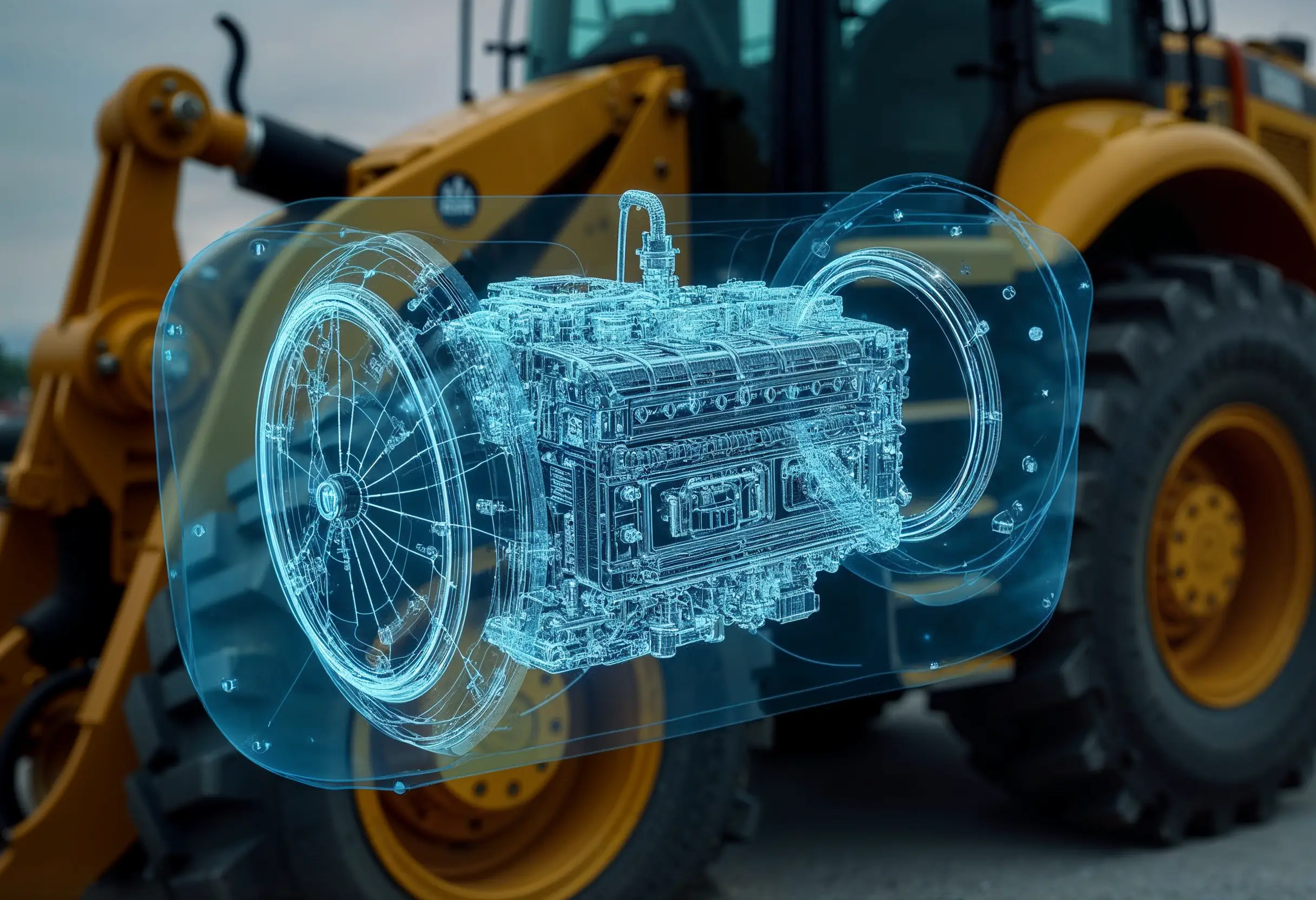
Traditional maintenance depends on fixed schedules or emergency repairs after breakdowns occur. This approach wastes resources through unnecessary servicing while missing critical warning signs. Manual inspections add human error risks and provide limited asset health insights.
Machine condition monitoring systems continuously track equipment performance in real-time. These advanced solutions help manufacturers reduce equipment stoppages by 30-50% while extending machinery lifetime by 20-40%. Your maintenance operations benefit from 40% improved efficiency through data-driven decision making.
Essential Components of Smart Diagnostic Systems
Your predictive maintenance platform combines several key elements for comprehensive equipment monitoring:
- Performance Sensors: Strategic sensor placement tracks critical metrics like temperature, pressure, vibration, and rotational speed
- Data Validation: Advanced filtering ensures accurate readings by removing noise and errors from sensor data
- Anomaly Detection: Sophisticated algorithms detect potential issues using historical and real-time performance data
- Action Dashboard: Clear maintenance recommendations help prioritize critical equipment needs
Predictive maintenance helps you spot potential failures early, but acting fast is what prevents costly downtime. MCH Parts provides high-quality replacement parts for heavy equipment, ensuring quick repairs and long-term reliability.
Real-time Equipment Health Tracking
Modern vibration monitoring systems use advanced sensor networks embedded throughout equipment components. These machine condition monitoring sensors provide continuous performance data streams, alerting your team to potential issues immediately.
Visual inspection systems add another monitoring layer, detecting subtle wear patterns, misaligned components, and damage that standard sensors might miss.
Your maintenance team gains comprehensive machine health insights through these integrated technologies. Advanced predictive analytics analyzes thousands of performance indicators to predict and prevent failures before they impact operations.
Equipment Diagnostic System Setup
Smart diagnostics demand careful attention to sensor placement, data collection, and anomaly detection training. Your equipment fleet benefits from systematic implementation focused on precise monitoring and performance tracking.
Strategic Sensor Installation

Modern condition monitoring systems start with proper sensor positioning. Your heavy equipment requires specific monitoring components:
- Engine diagnostic sensors for temperature and pressure tracking
- Advanced vibration monitoring units for mechanical analysis
- Fluid monitoring systems for oil and coolant levels
- Sound detection equipment for operational anomalies
These components create detailed machine data streams, enabling your maintenance team to spot potential issues early.
Equipment Performance Baselines
Proper sensor installation leads to crucial baseline data creation. Your setup process includes:
- Performance History: Compile equipment records including maintenance logs, failure incidents, and sensor readings for comprehensive analysis
- Data Quality Control: Filter and standardize collected information to remove errors, ensuring accurate diagnostic readings
- Critical Indicators: Identify key performance patterns that signal potential equipment issues like temperature fluctuations or pressure anomalies
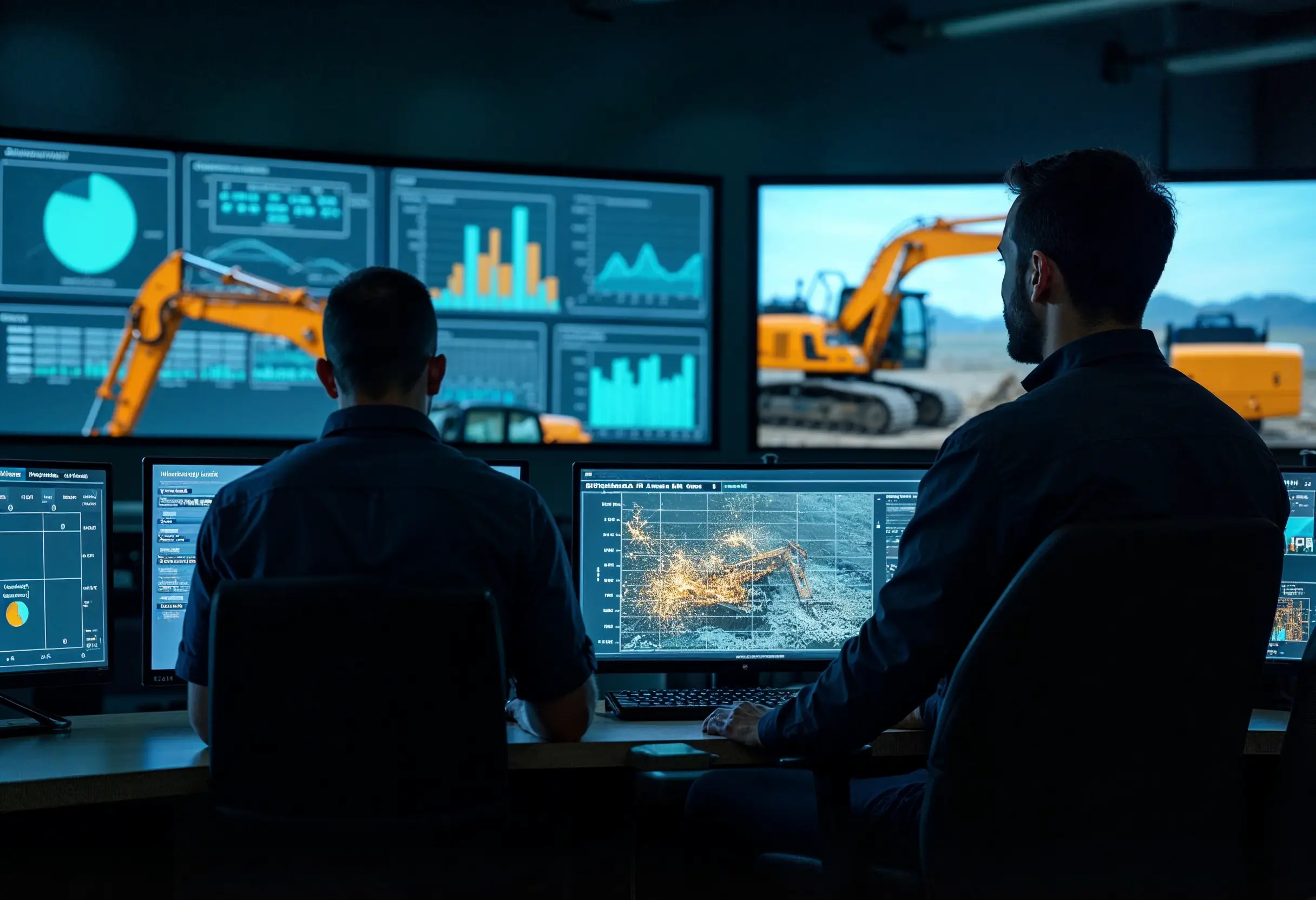
Advanced Anomaly Detection Setup
The final phase adapts monitoring systems to your specific machinery. Two key approaches enhance equipment diagnostics:
- Historical Pattern Matching: Uses past maintenance records to identify similar issues during operation
- Deviation Detection: Spots unusual equipment behavior when previous failure data isn't available
These sophisticated systems analyze machine data to create detailed asset health profiles, enabling precise maintenance scheduling. Studies show manufacturers achieve significant results, reducing herbicide usage by more than two-thirds through proper implementation of predictive maintenance technologies.
Diagnostic System Performance Metrics
Smart diagnostics deliver measurable improvements in equipment reliability and operational efficiency. Your maintenance strategy benefits from clear performance indicators that demonstrate real value.
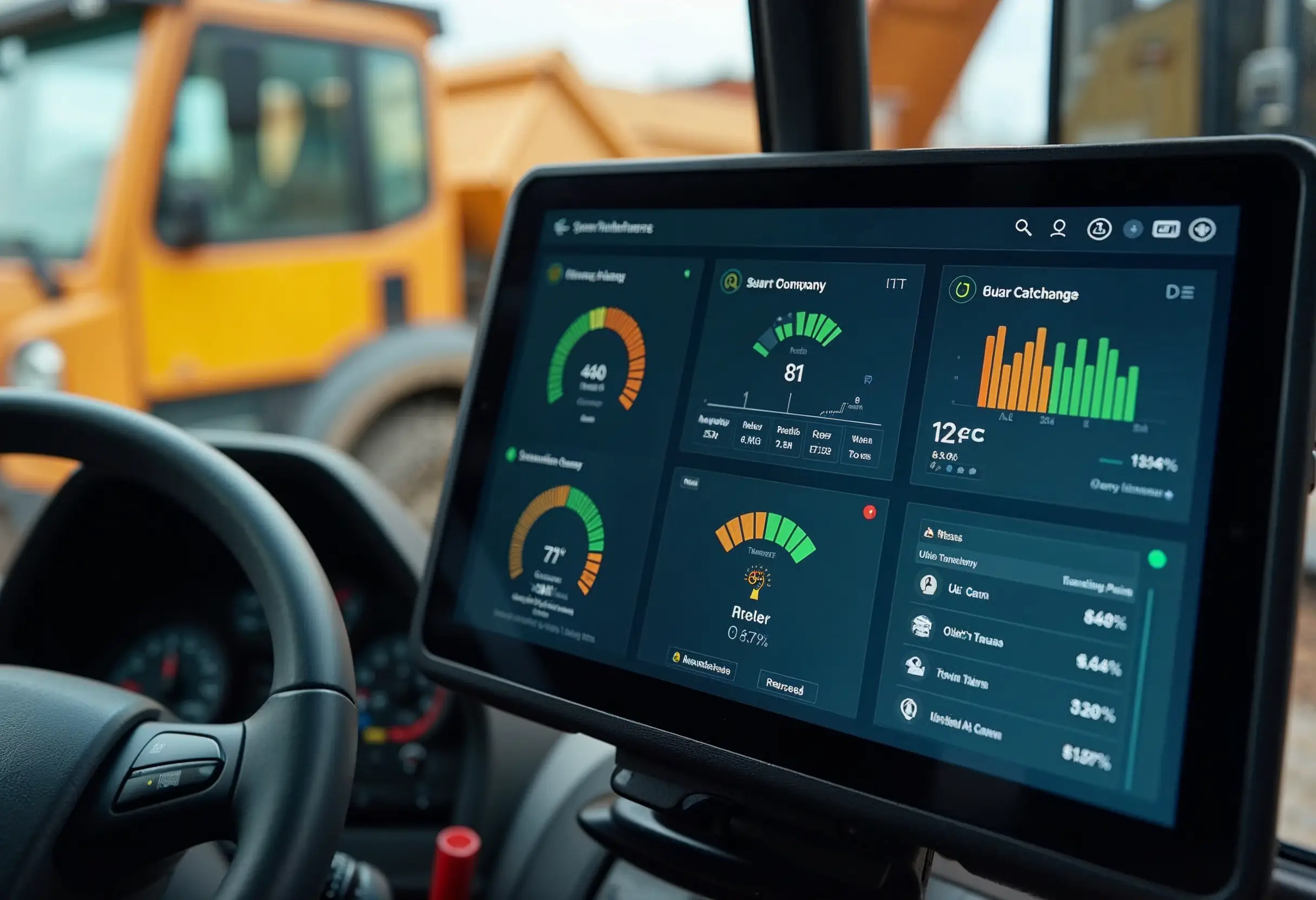
Equipment Reliability Gains
Modern predictive maintenance software enhances machinery uptime through early problem detection. Your manufacturing operations achieve 15% reduction in equipment downtime, while equipment lifespan increases by 20-25%. Maintenance teams report 5-20% better labor efficiency through optimized scheduling.
Cost Savings Analysis
Your predictive maintenance solutions generate savings across multiple areas:
- 8-12% lower maintenance costs versus preventive methods, up to 40% compared to reactive maintenance
- 18-25% reduction in total maintenance spending through better uptime
- 10% decrease in MRO (Maintenance, Repair, and Operations) inventory costs
These improvements stem from preventing equipment damage and smart asset management. Your proactive maintenance approach minimizes emergency repairs while extending machinery life.
Performance Measurement Framework
Your diagnostic system success relies on key metrics:
- Equipment Reliability (MTBF): Monitor time between failures to track system improvements
- Operational Availability: Track percentage of equipment ready for use
- Value-Based Maintenance: Compare maintenance costs against replacement value (MC/ERV)
Studies show predictive maintenance technologies deliver ten times return on initial investment. Industry projections indicate manufacturer savings between $240 and $630 billion by 2025 through predictive analytics and condition-based maintenance.
Smart Diagnostic System Implementation Challenges
Predictive maintenance technologies offer proven benefits, yet your implementation journey may face several hurdles. Understanding these challenges helps ensure successful adoption of advanced maintenance strategies.
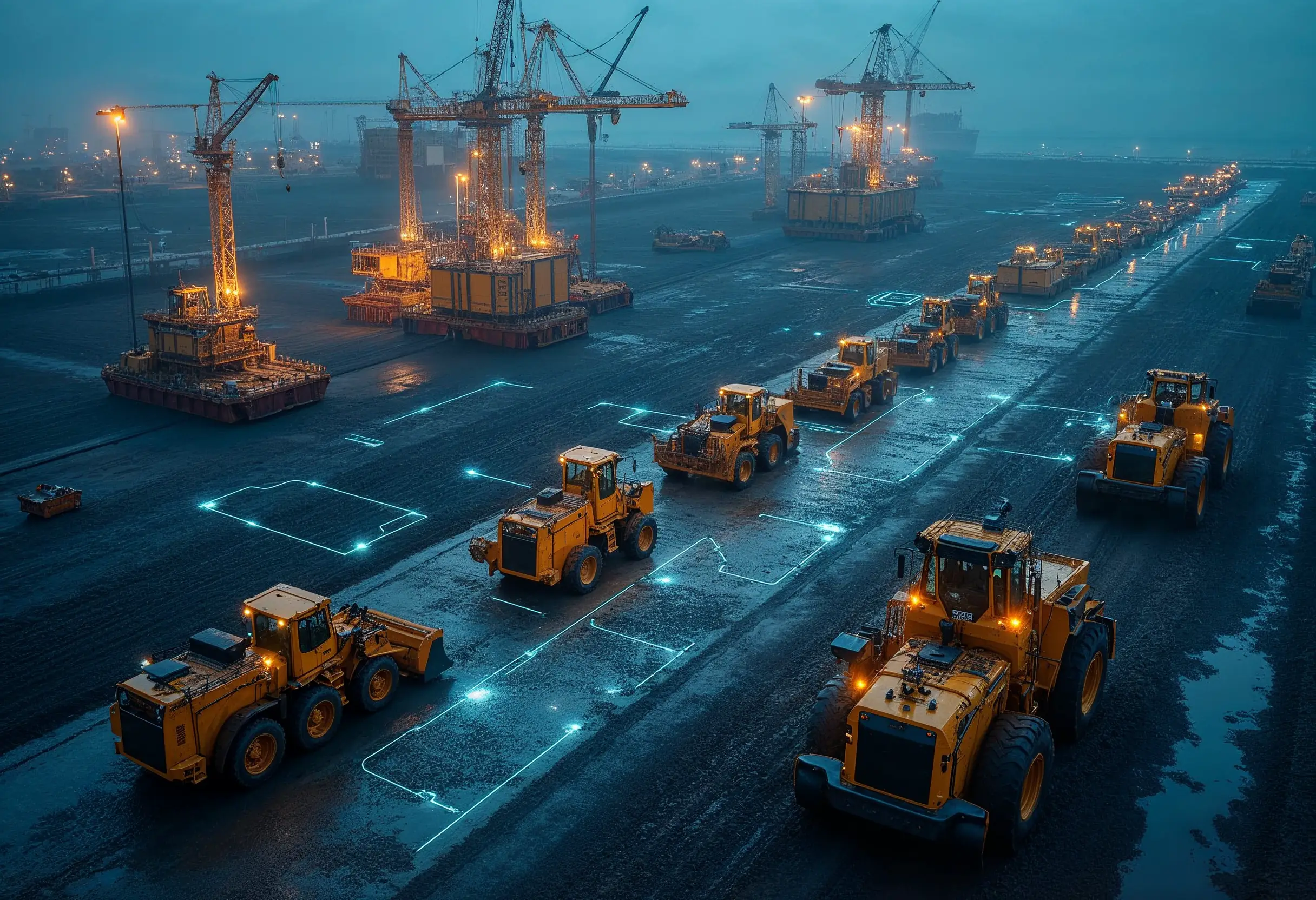
Data Accuracy Requirements
Your predictive maintenance platform effectiveness depends heavily on data quality. Manufacturing companies report unreliable predictions from poor quality data. Your maintenance team might encounter:
- Equipment sensors missing critical readings
- Data format differences between facilities
- Redundant information in system databases
- Mixed data standards from multiple sources
Your data analytics strategy needs robust quality controls. Studies show standardized data collection and regular audits improve maintenance effectiveness by 30%. Data validation tools help reduce maintenance costs by 8-12%.
Existing Equipment Integration
Your older machinery and systems create unique monitoring challenges. Traditional equipment often uses outdated data formats, complicating integration with modern predictive maintenance software. Key obstacles include:
- Processing power limitations
- System compatibility issues
- Data access restrictions
- Security requirements for new technology
Smart integration approaches solve these challenges. Your existing systems benefit from specialized interface solutions that maintain core functionality. Hybrid monitoring systems improve operational efficiency while preserving critical operations.
Proper planning helps manufacturers reduce maintenance costs by 30% and achieve 10x return on investment. These results show how addressing implementation challenges leads to significant operational gains.
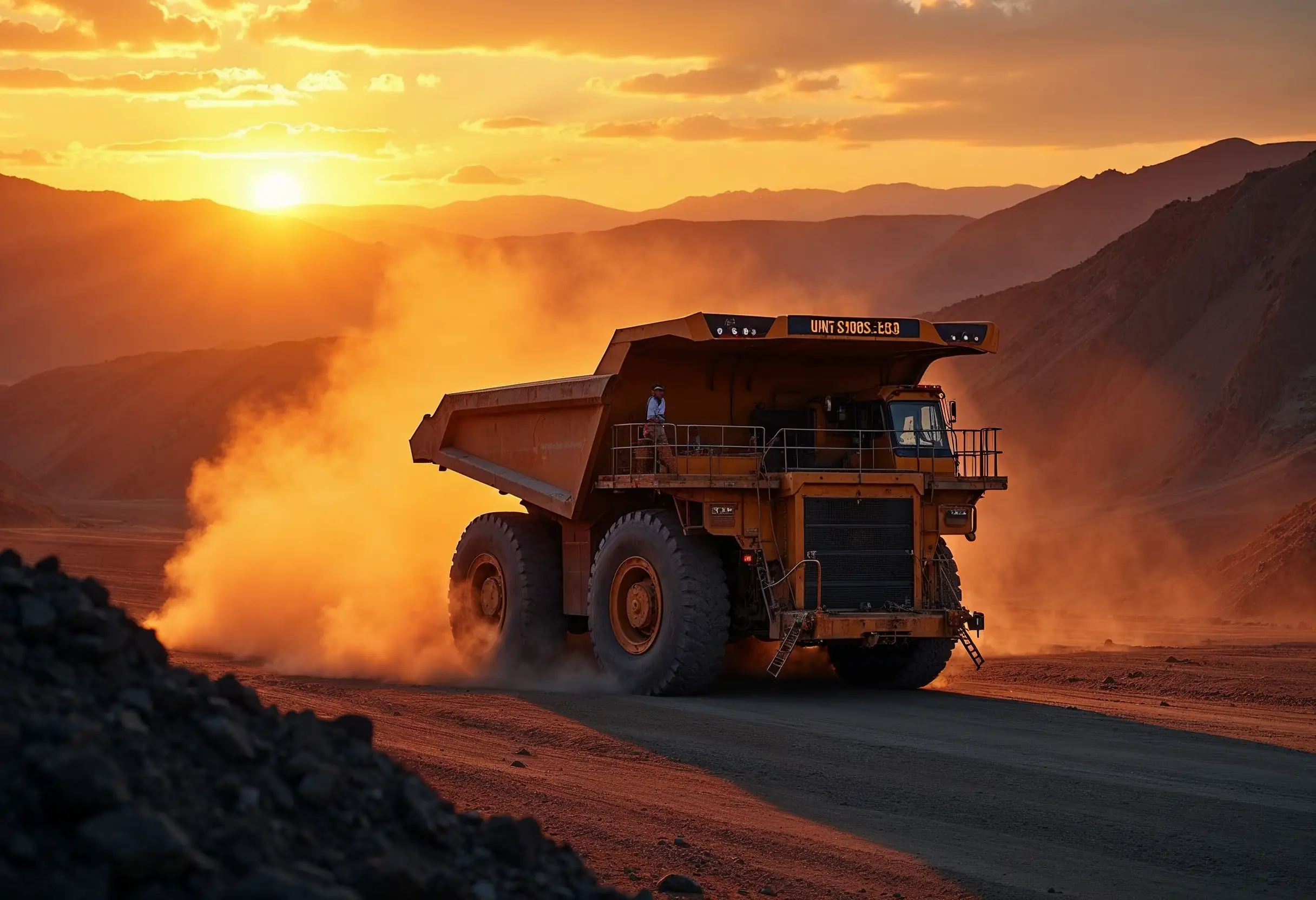
Smart Diagnostics: Proven Results
Predictive maintenance technologies demonstrate clear value across industrial operations. Your maintenance strategy benefits from proven results: 73% fewer equipment failures, 25% better fuel efficiency, and substantial maintenance cost reductions.
Studies show predictive maintenance solutions deliver 10 times return on initial investment. Your manufacturing operations achieve these gains through strategic sensor placement, quality data management, and advanced anomaly detection that spots issues before costly breakdowns occur.
Equipment reliability improves 15-20% while maintenance costs drop 18-25%. These benefits compound as your team masters implementation challenges through systematic planning and execution.
Smart maintenance strategies prepare your fleet operations for future challenges. Modern predictive maintenance technologies make machinery health monitoring precise, predictable, and cost-effective. Your construction operations benefit from extended machinery lifespans and optimized maintenance scheduling.
Predictive maintenance tells you which components need attention—now it’s time to act. MCH Parts supplies critical replacement parts with fast shipping, helping you avoid unexpected breakdowns and expensive delays. Minimize risk—get the right parts before failure happens, contact us today.
FAQs
Q1. How does artificial intelligence enhance predictive maintenance for heavy equipment? AI analyzes real-time data from sensors to detect potential failures before they occur. It continuously monitors parameters like temperature, vibration, and pressure, allowing for proactive repairs and reducing costly downtime.
Q2. What are the key benefits of implementing AI-powered predictive maintenance? Implementation of AI-powered predictive maintenance can lead to a 73% reduction in equipment failures, 25% improvement in fuel efficiency, and 18-25% decrease in overall maintenance costs. It also extends machinery lifespan by 20-40%.
Q3. How do companies measure the success of AI predictive maintenance systems? Success is measured through key performance indicators such as Mean Time Between Failures (MTBF), asset availability, and maintenance cost to estimated replacement value ratio. Companies typically see a return on investment of about ten times the initial cost.
Q4. What are the main challenges in implementing AI-powered predictive maintenance? The primary challenges include data quality issues, such as incomplete or inaccurate data, and integration with legacy systems. Overcoming these obstacles requires robust data management practices and strategic approaches to system integration.
Q5. Can AI predict maintenance needs for different types of heavy equipment? Yes, AI can be trained to predict maintenance needs for various types of heavy equipment, including cranes, bulldozers, and excavators. By analyzing data from machine condition monitoring sensors, AI models can accurately forecast potential breakdowns and schedule maintenance activities during downtime to minimize project delays.
Read More
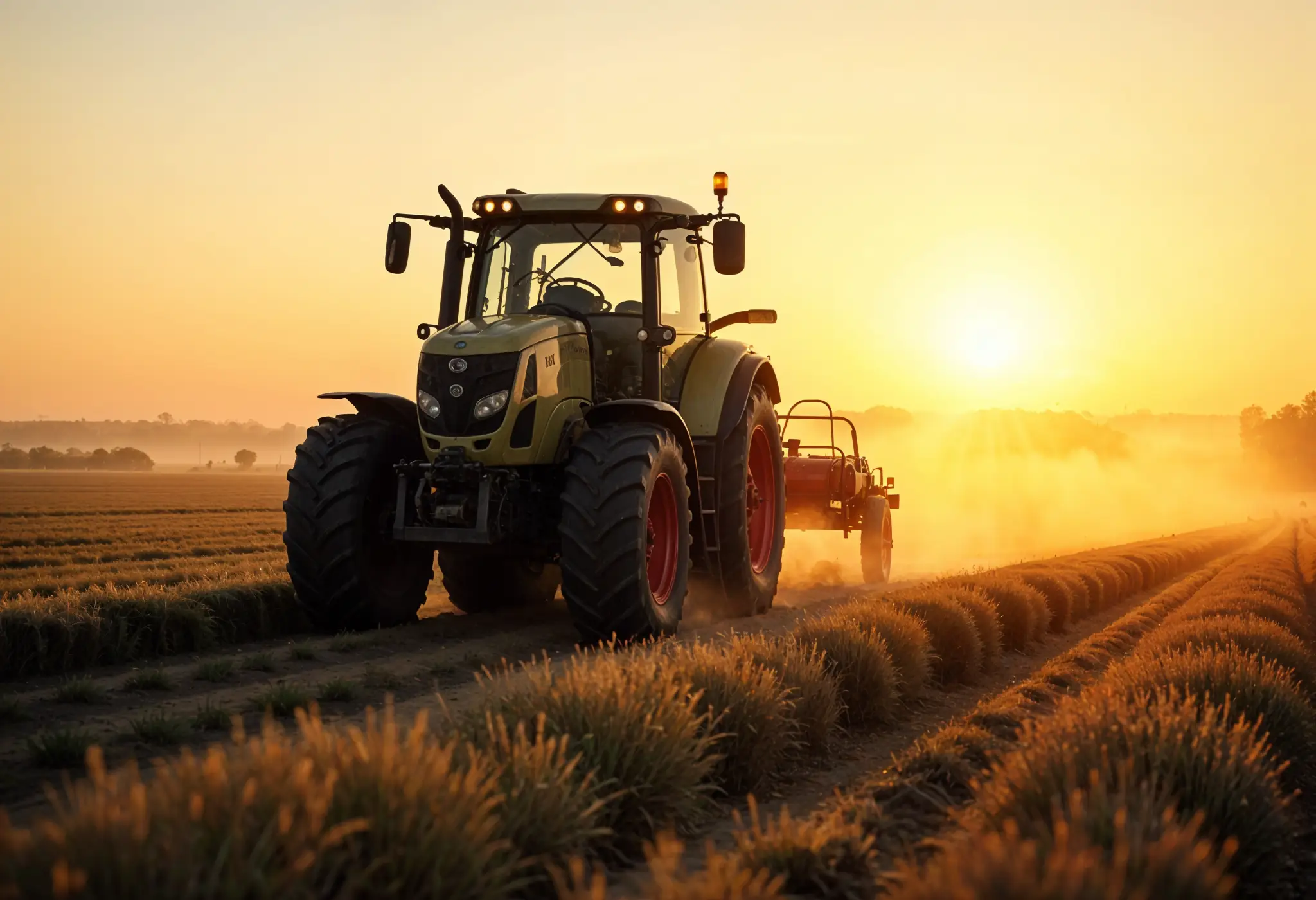
Top Hydraulic Components for Agricultural Equipment in 2025: Complete Guide
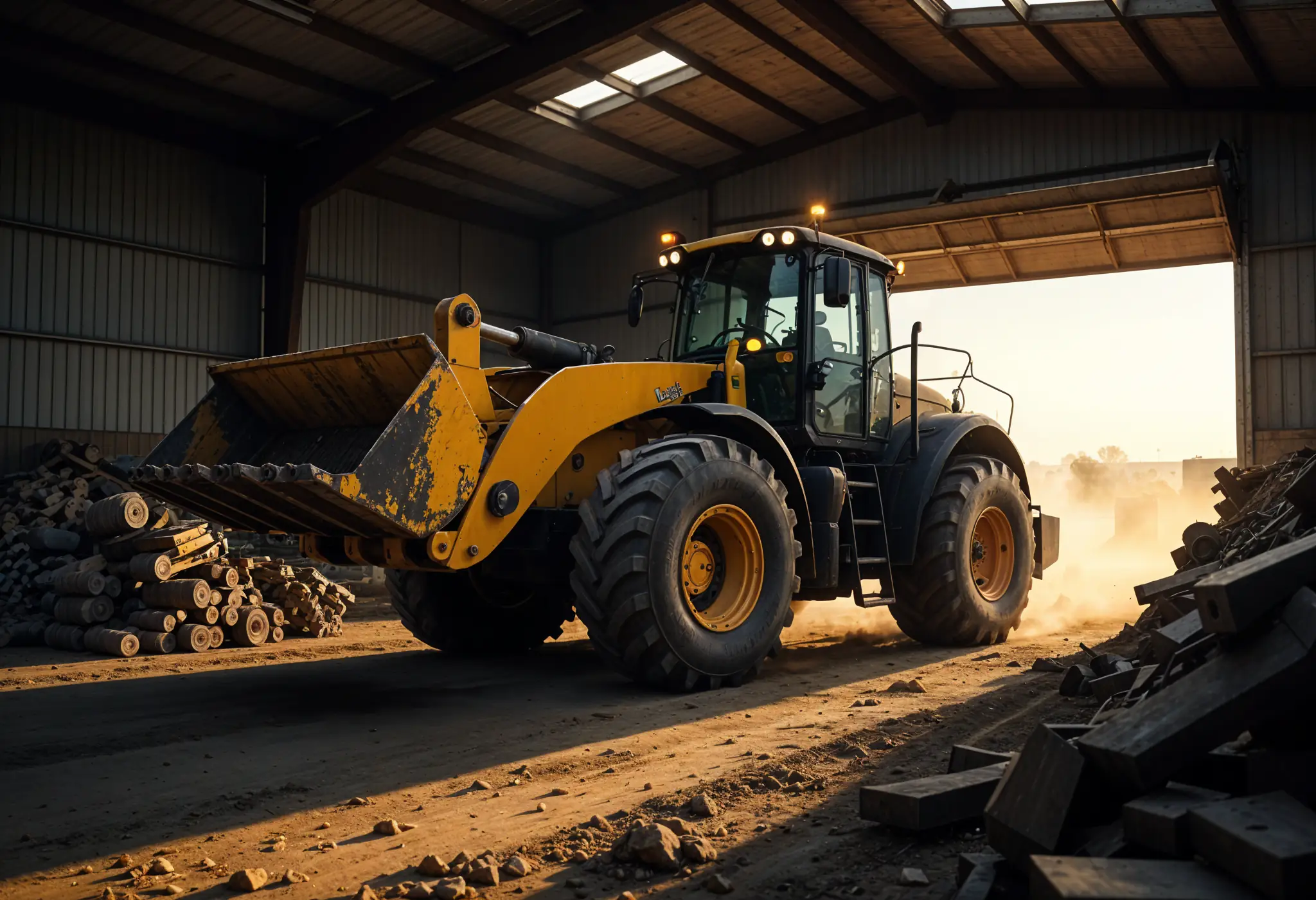
The Essential Farm Equipment Parts You Can't Afford to Run Out Of
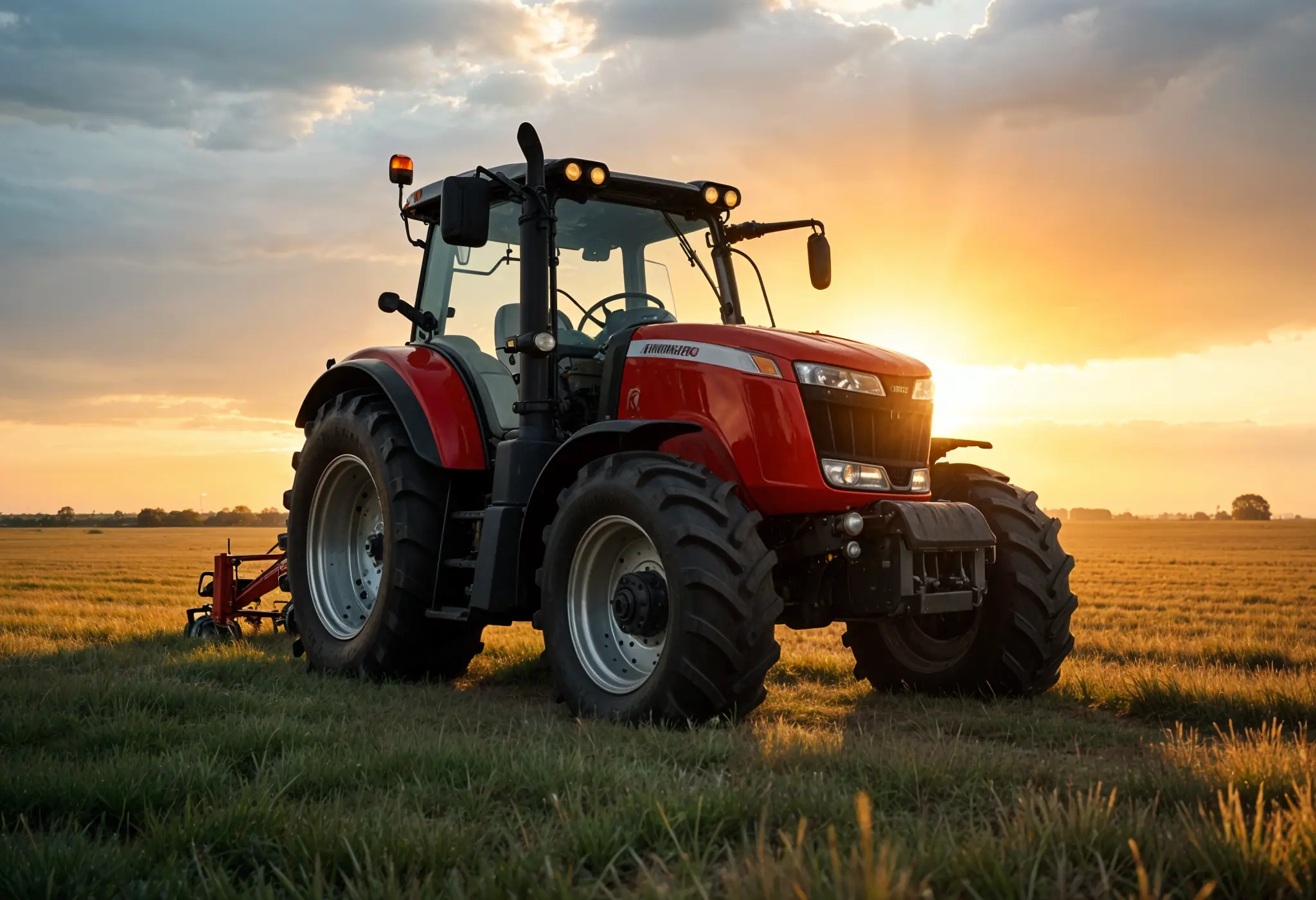
How to Service Farm Equipment: A Farmer's Guide to Zero Harvest Downtime
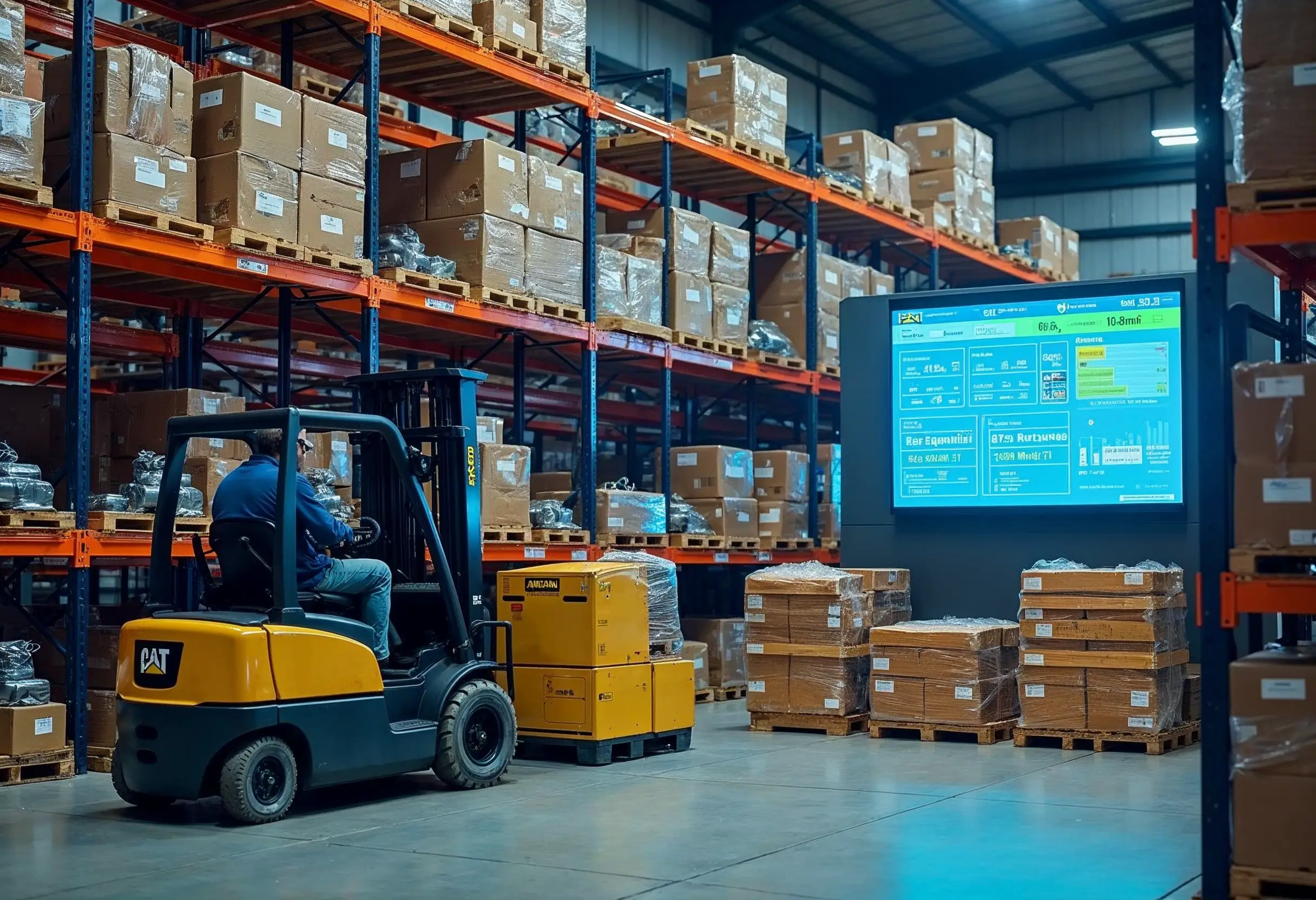
Construction Machinery Parts Suppliers: Expert Selection Guide
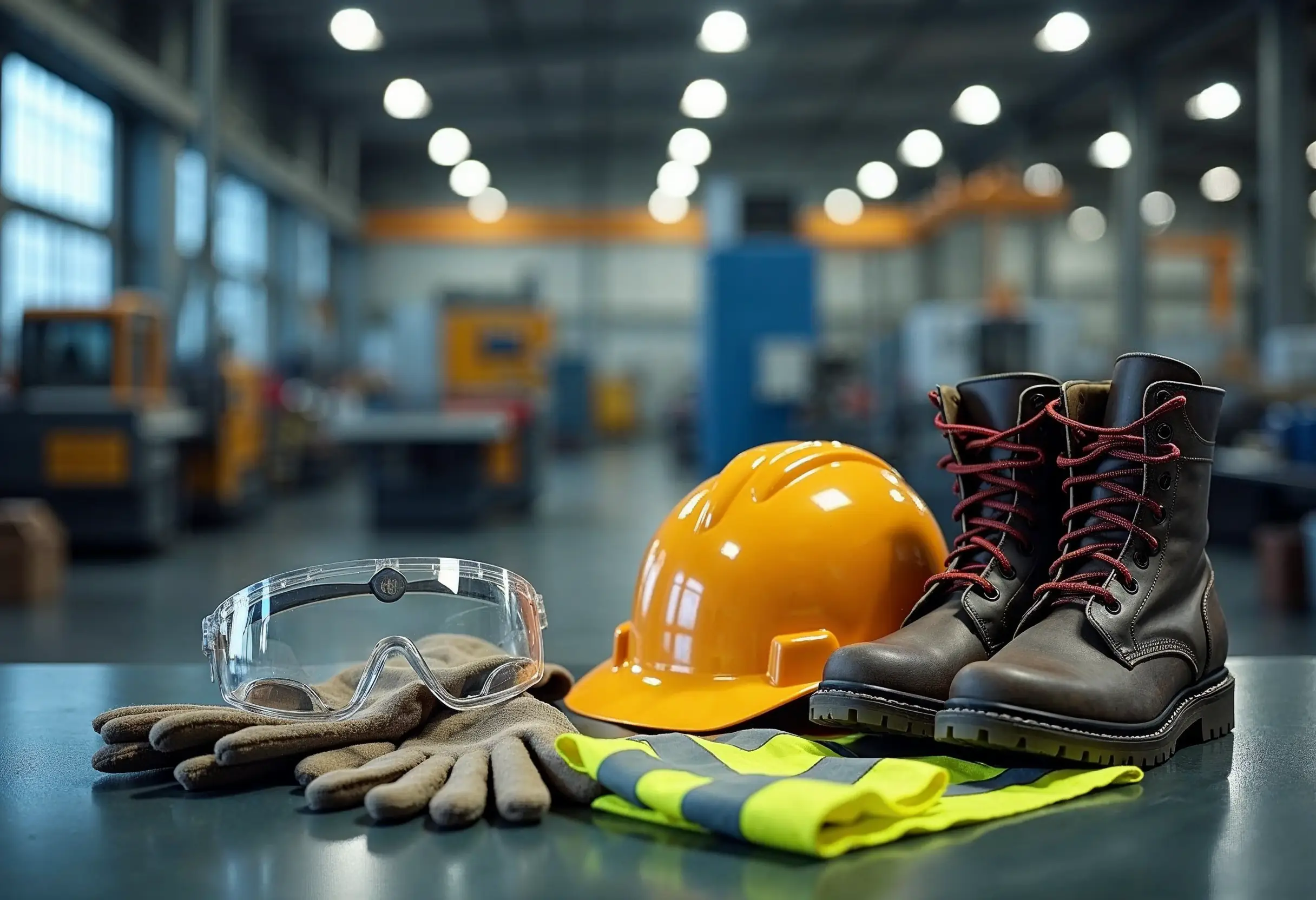
How to Apply Machine Safety Rules: From Selection to Installation
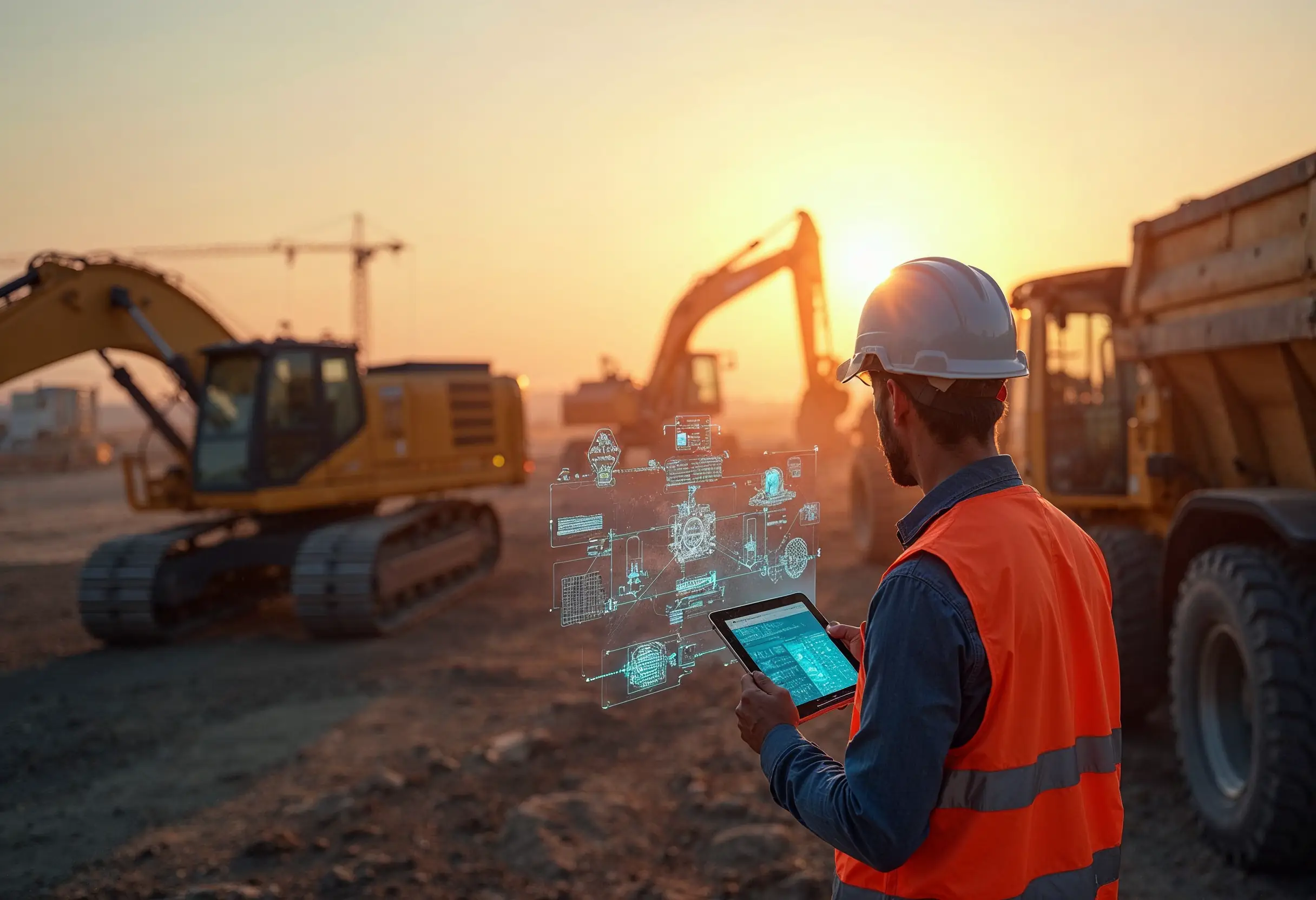
Smart Diagnostics Cut Heavy Equipment Failures by 73%
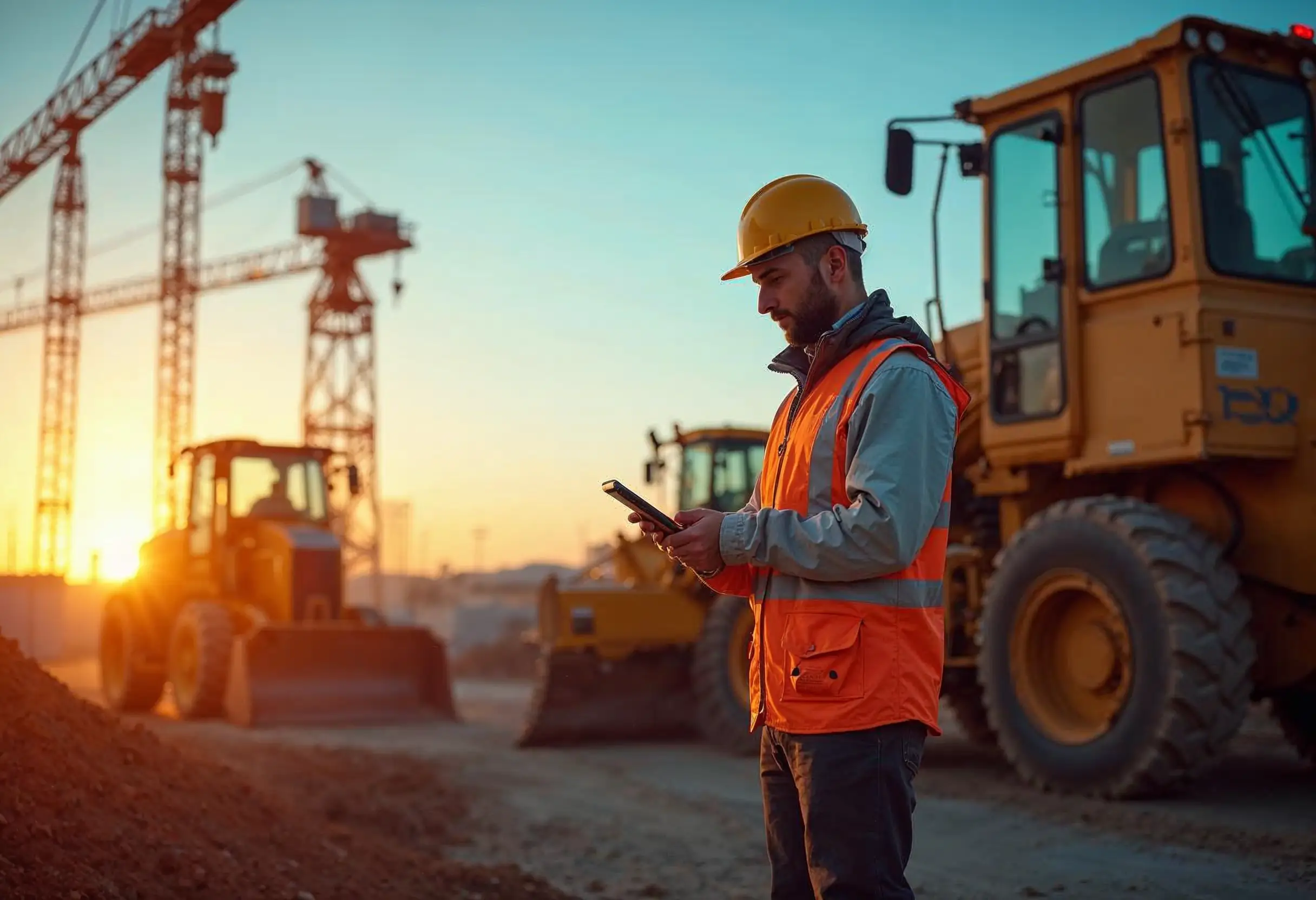
5 Ways to Assess the Environmental Impact of Heavy Construction Machinery
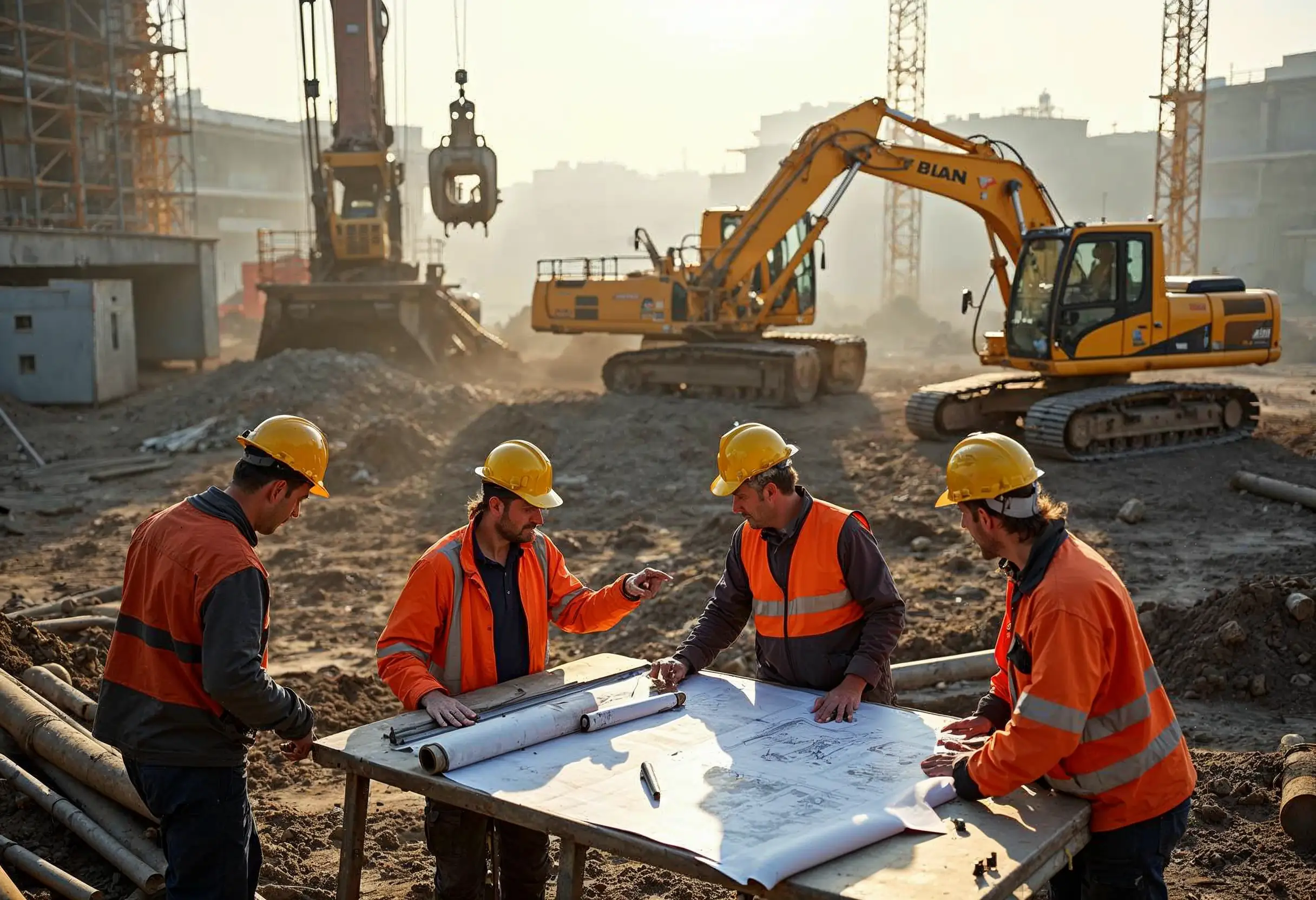
10 Smart Ways to Pick Construction Machinery for 2025 Projects
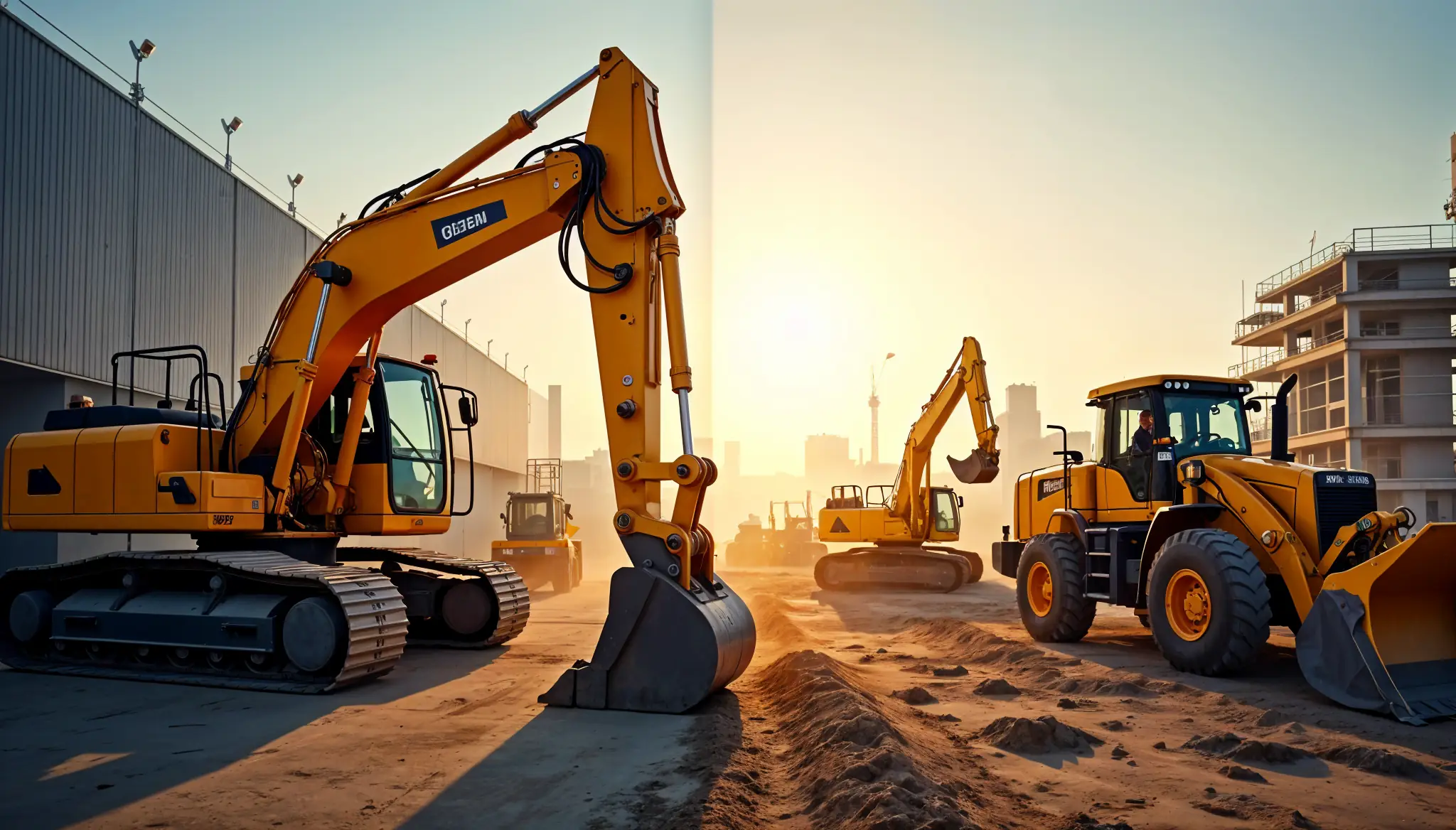
Rent vs Purchase Equipment: What Heavy Industry Experts Hide
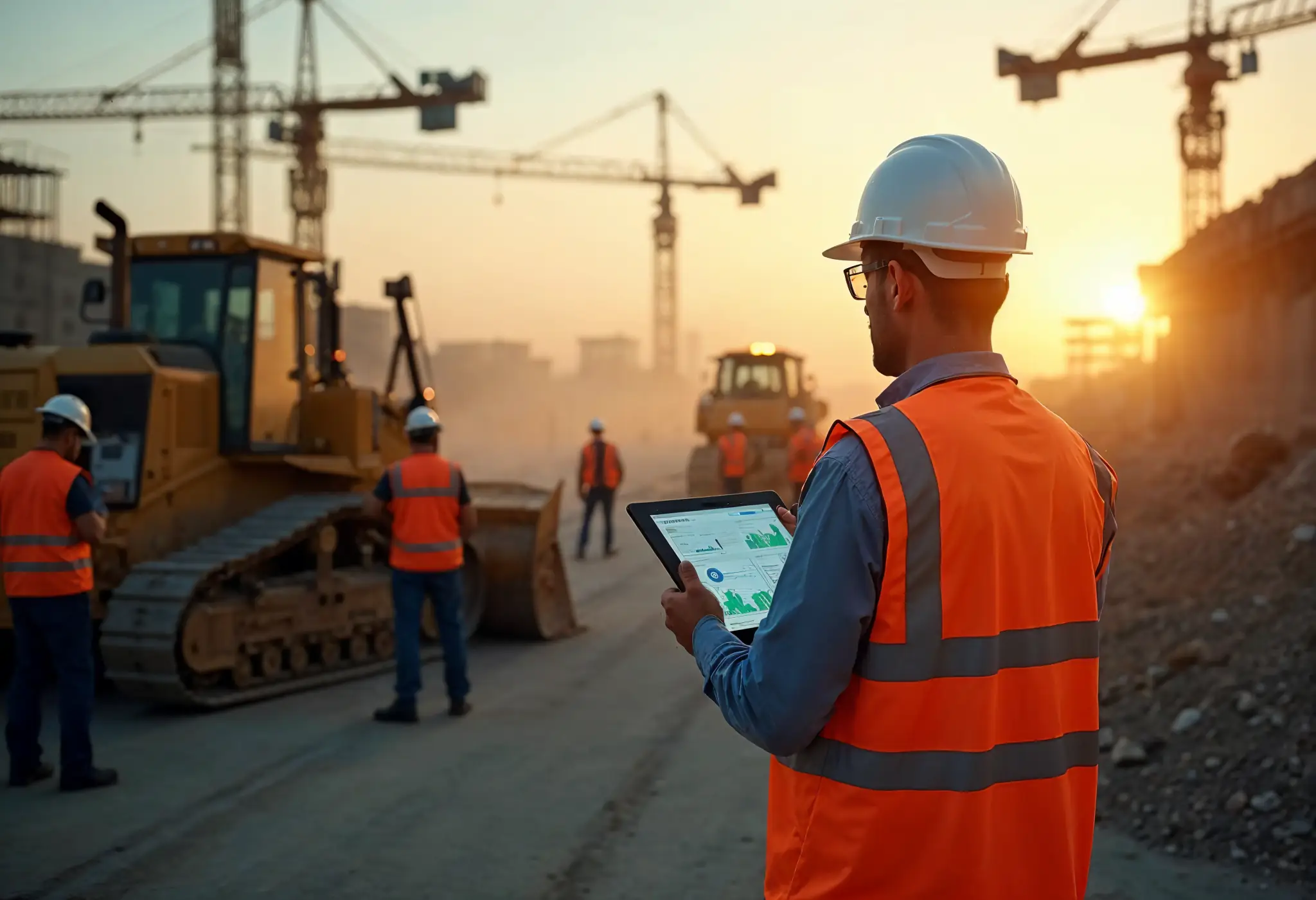
How to Implement a Construction Inventory Management System for Equipment Efficiency
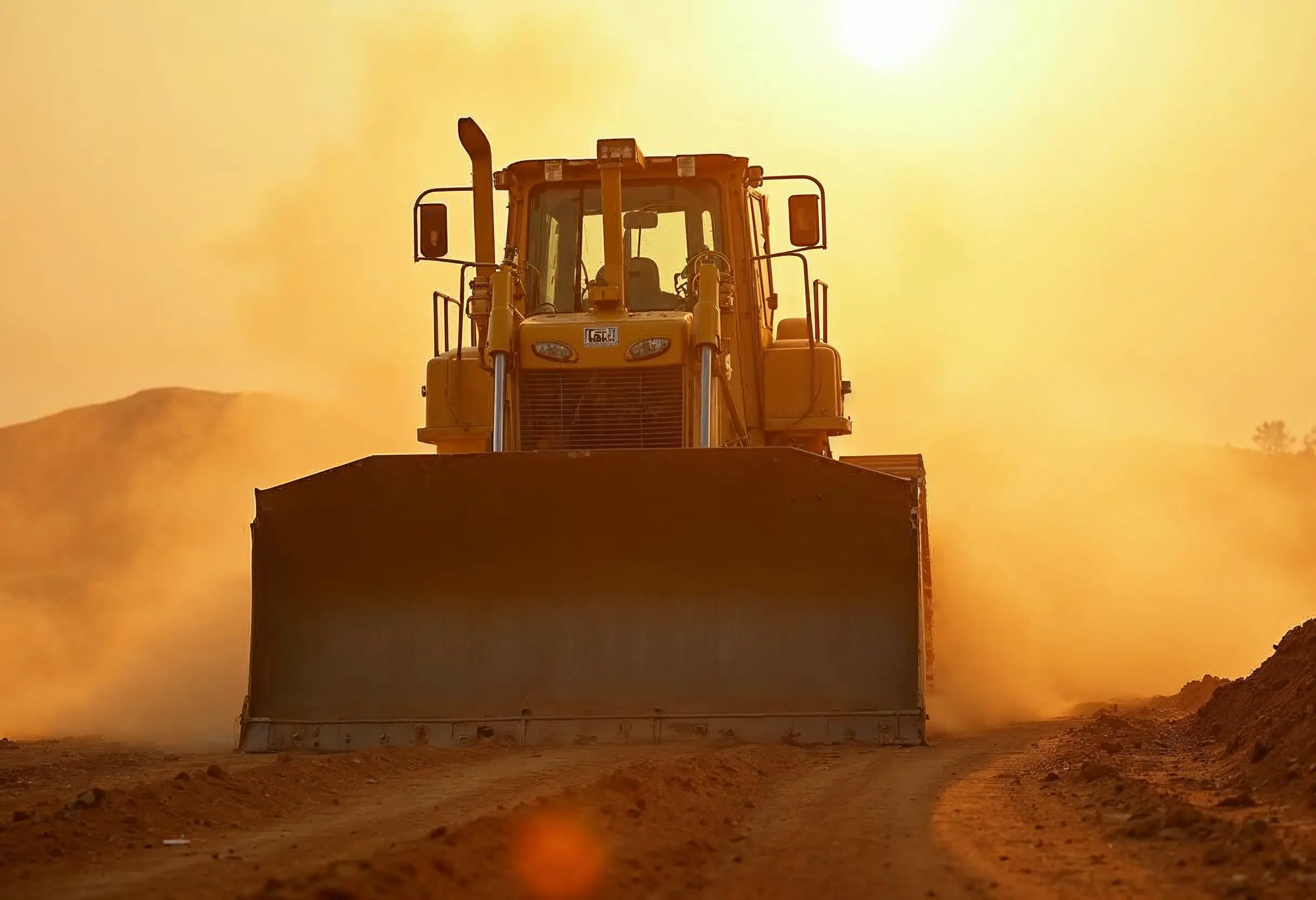
How to Extend Equipment Life Expectancy with Regular Maintenance
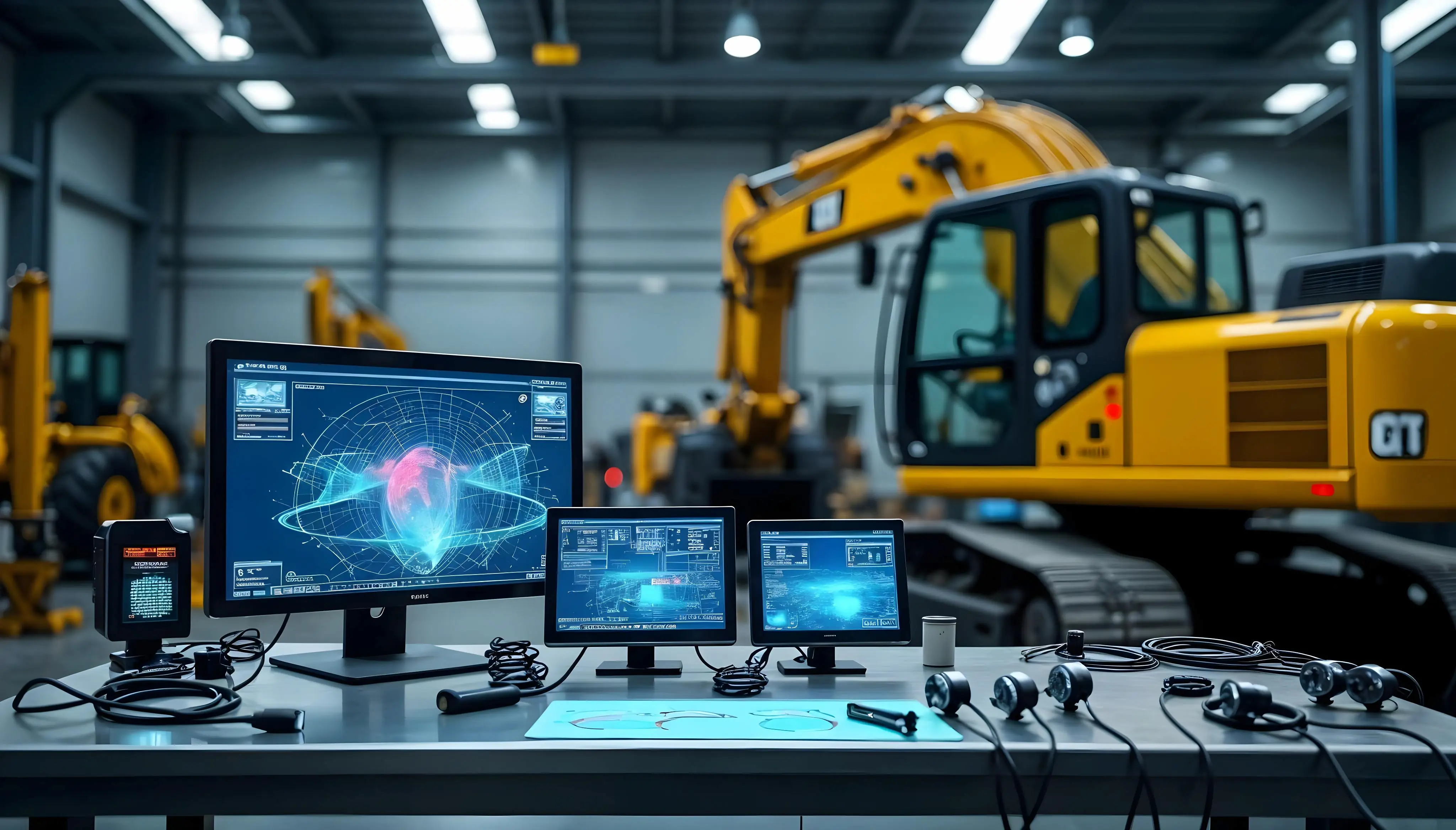
Advanced Heavy Equipment Diagnostic Tools: Ensuring Construction Machinery Quality
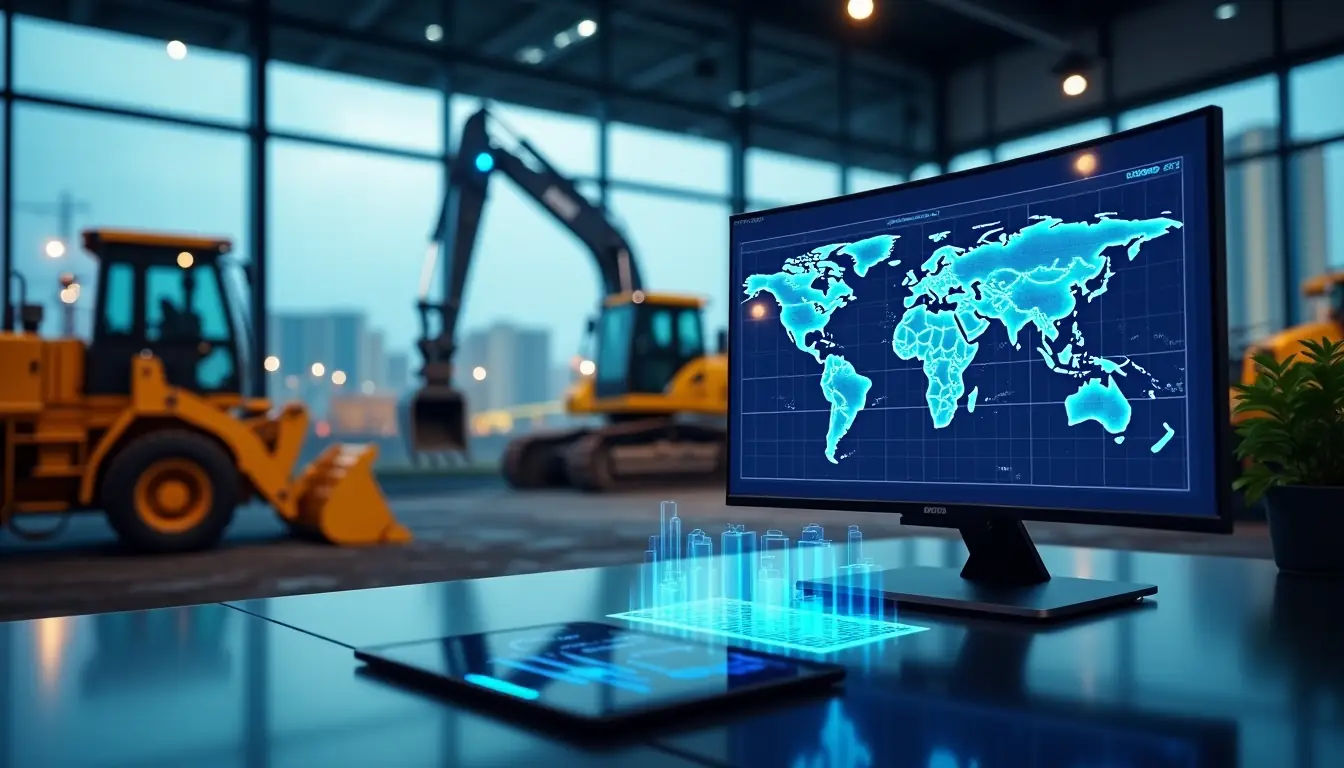
Essential Features Your Construction Equipment Inventory System Needs
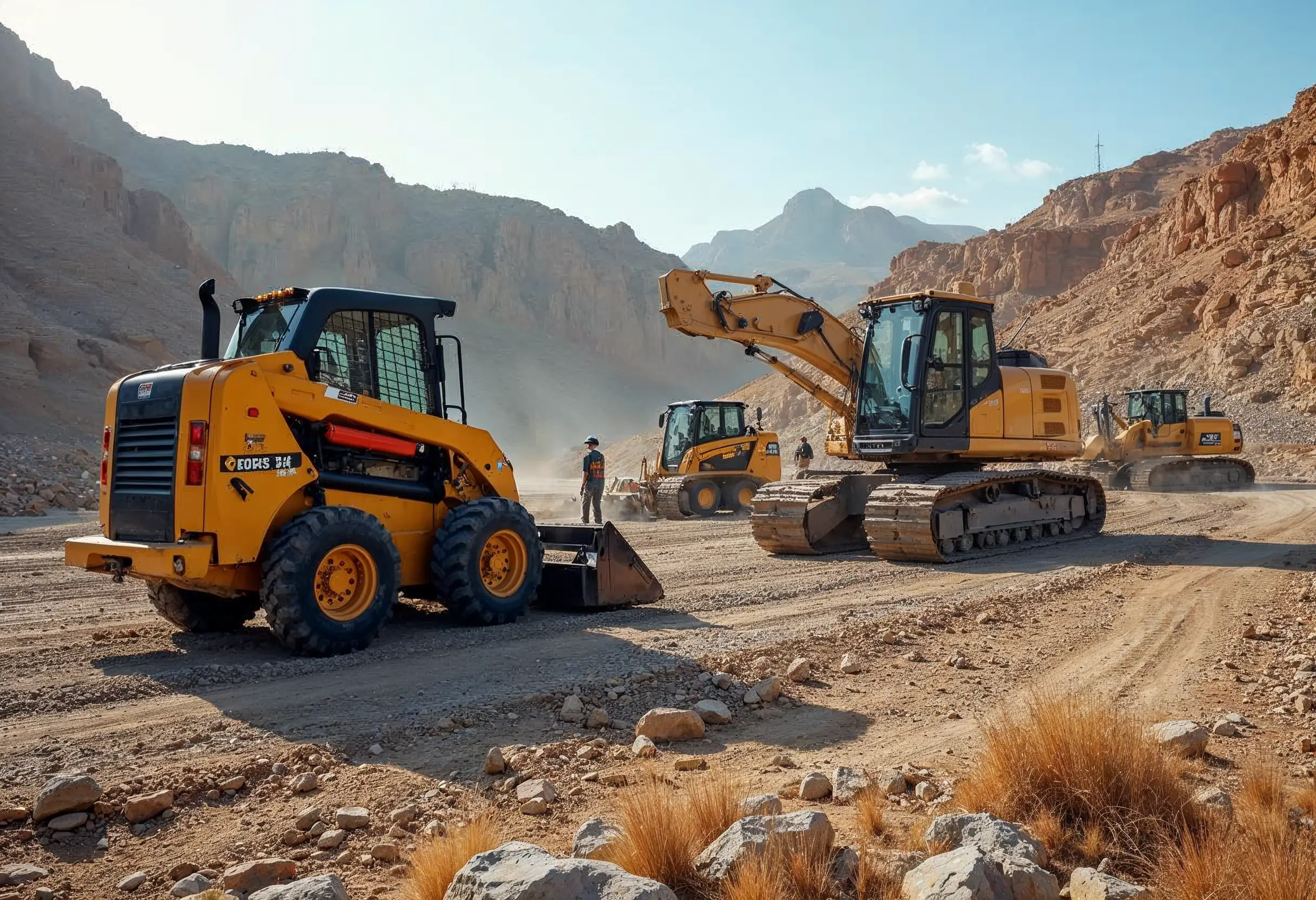
29 Quick Tips for Choosing Construction Equipment for Remote Locations
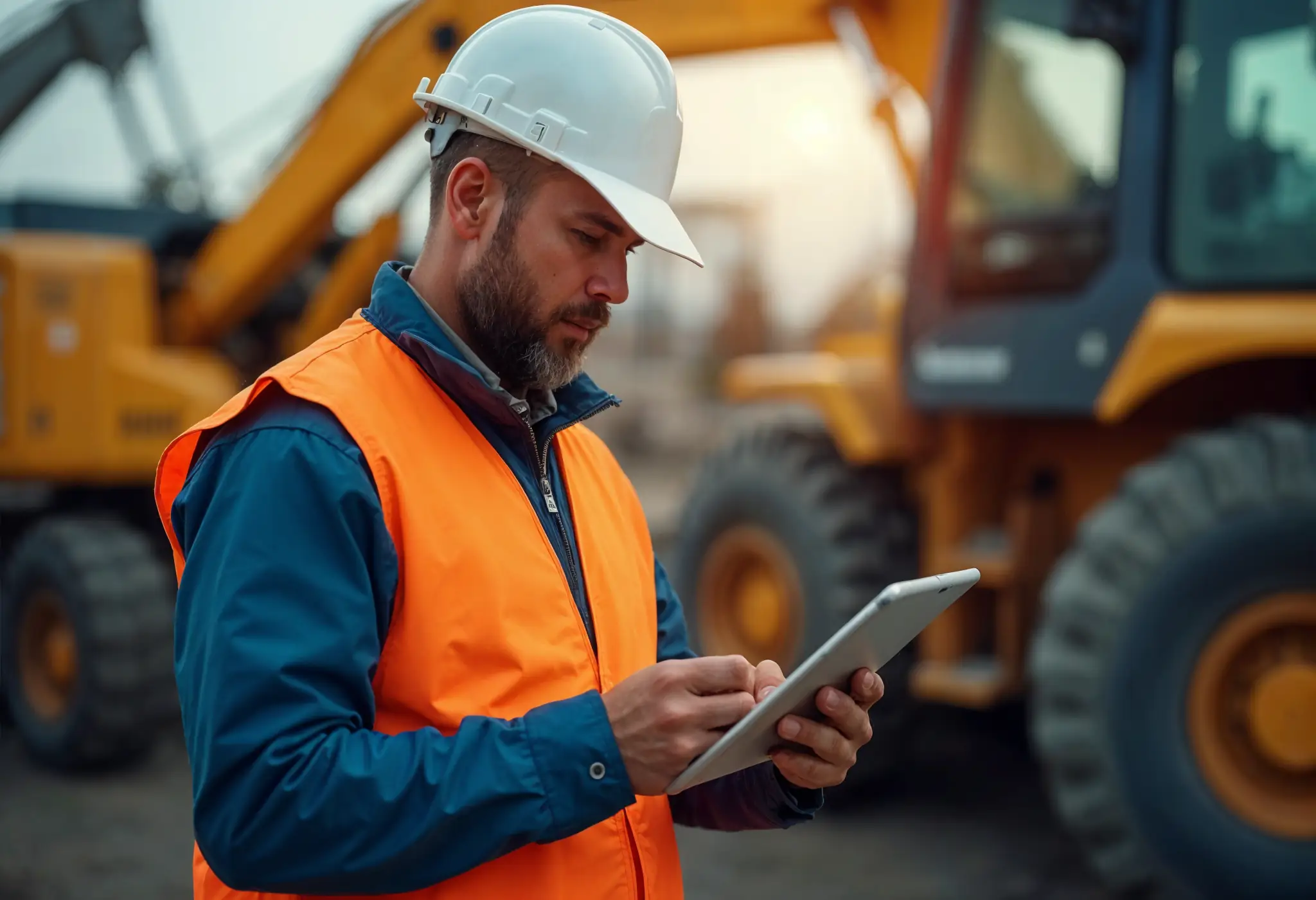
How to Select Construction Machinery with Optimal Equipment Maintenance in Mind
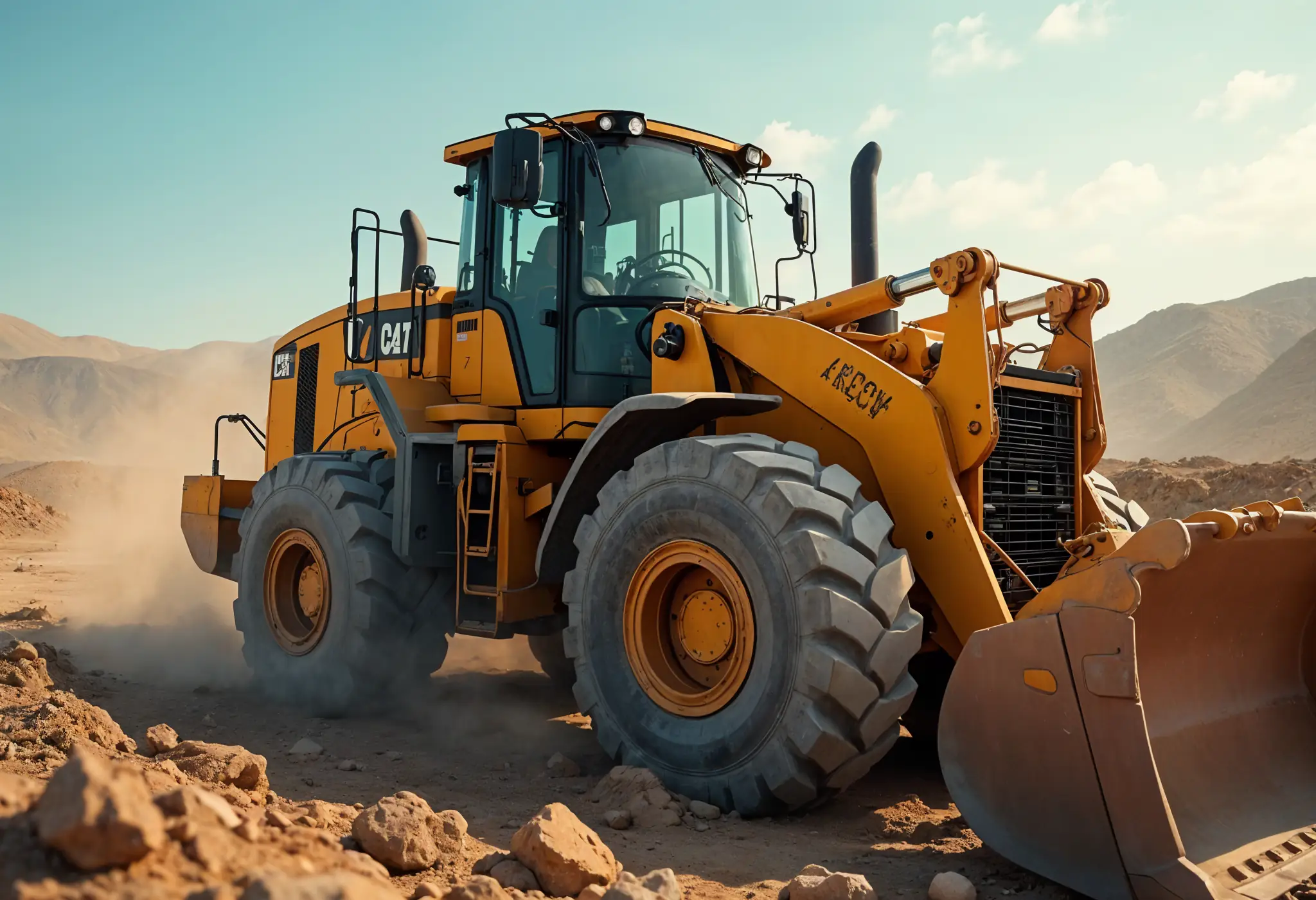
Top 25 Tips for Selecting Bulldozers for Construction Sites
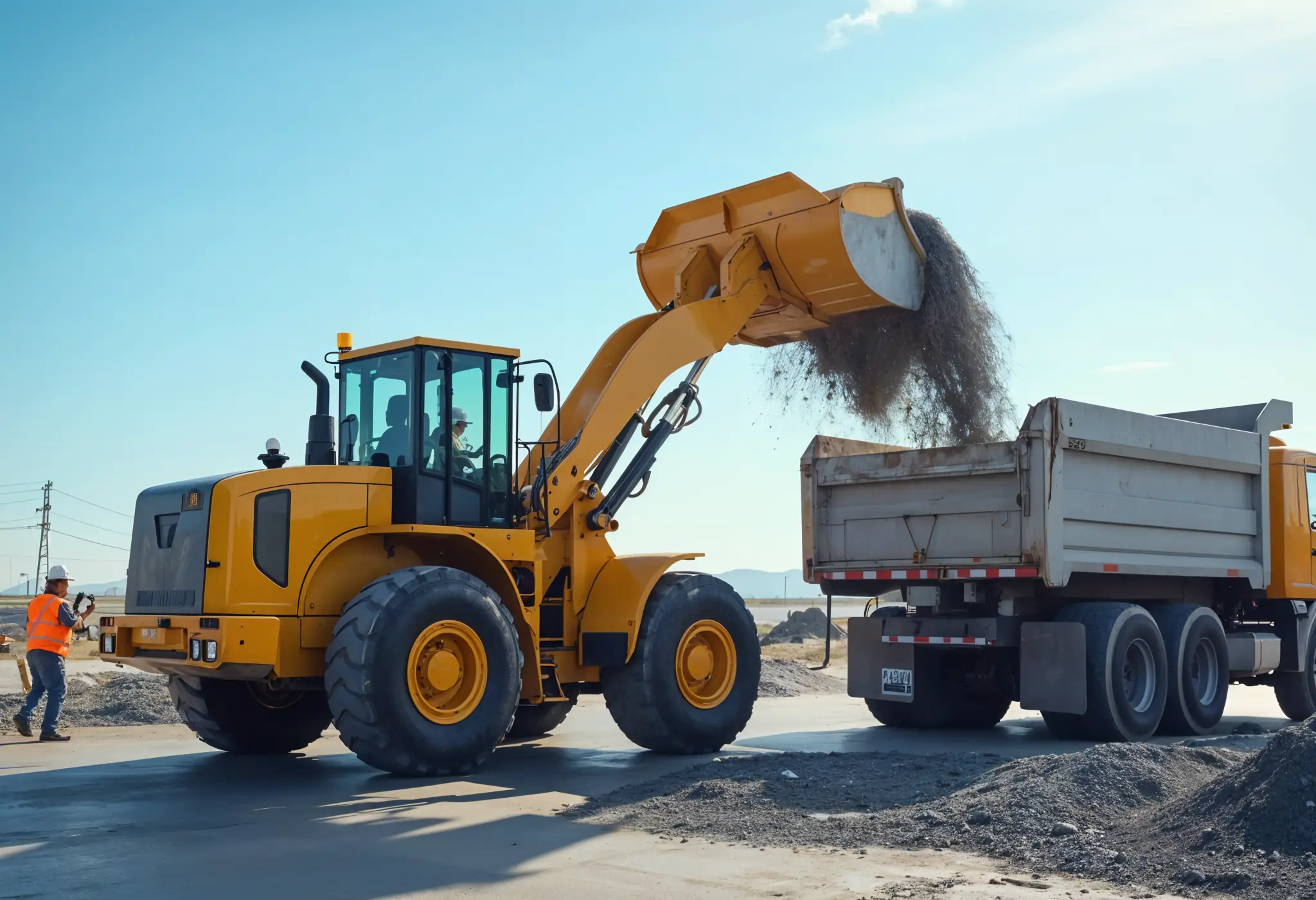
Which Construction Loader is Best for Your Project Needs?
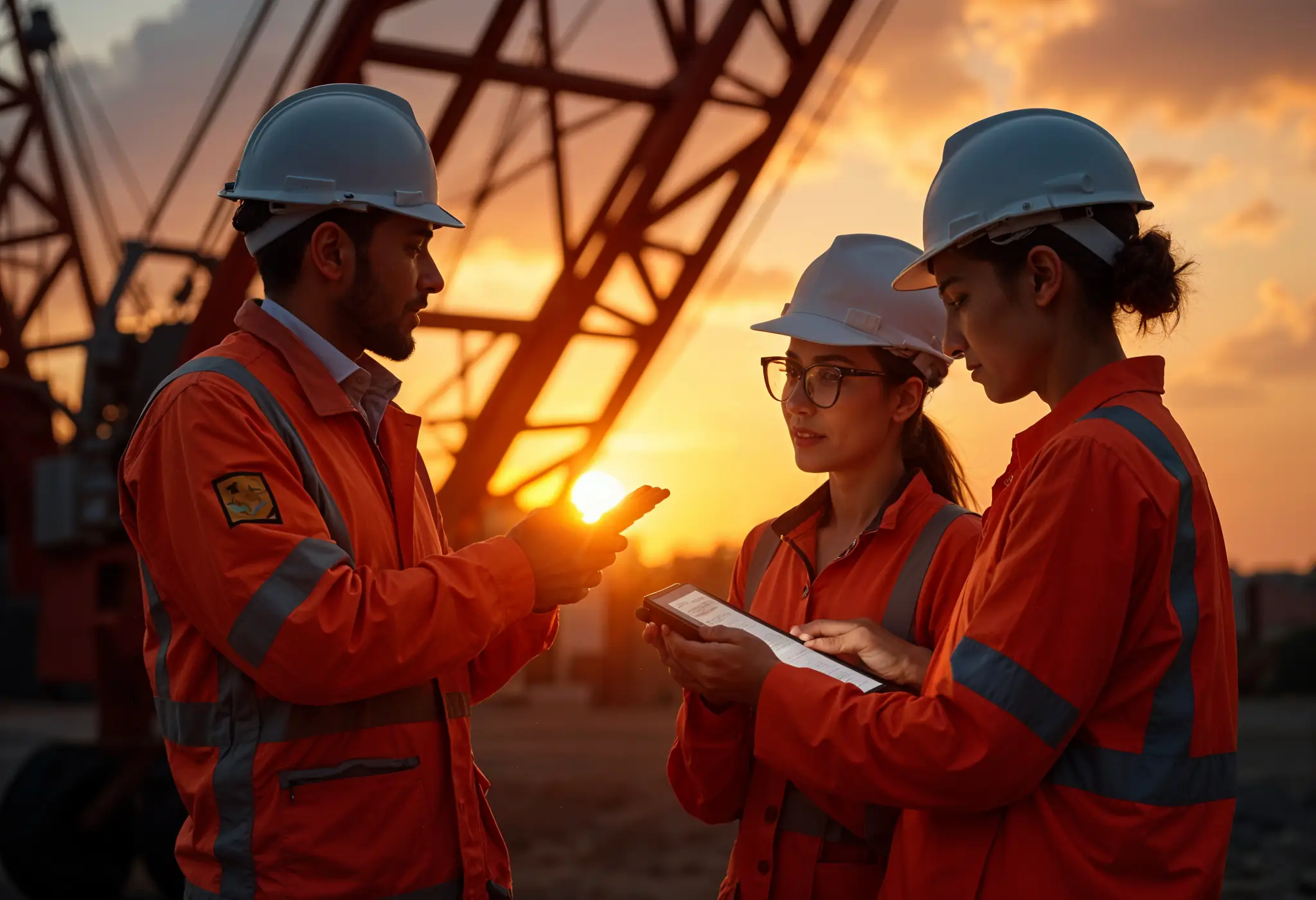
4 Key Steps to Form a Construction Machinery QC Team
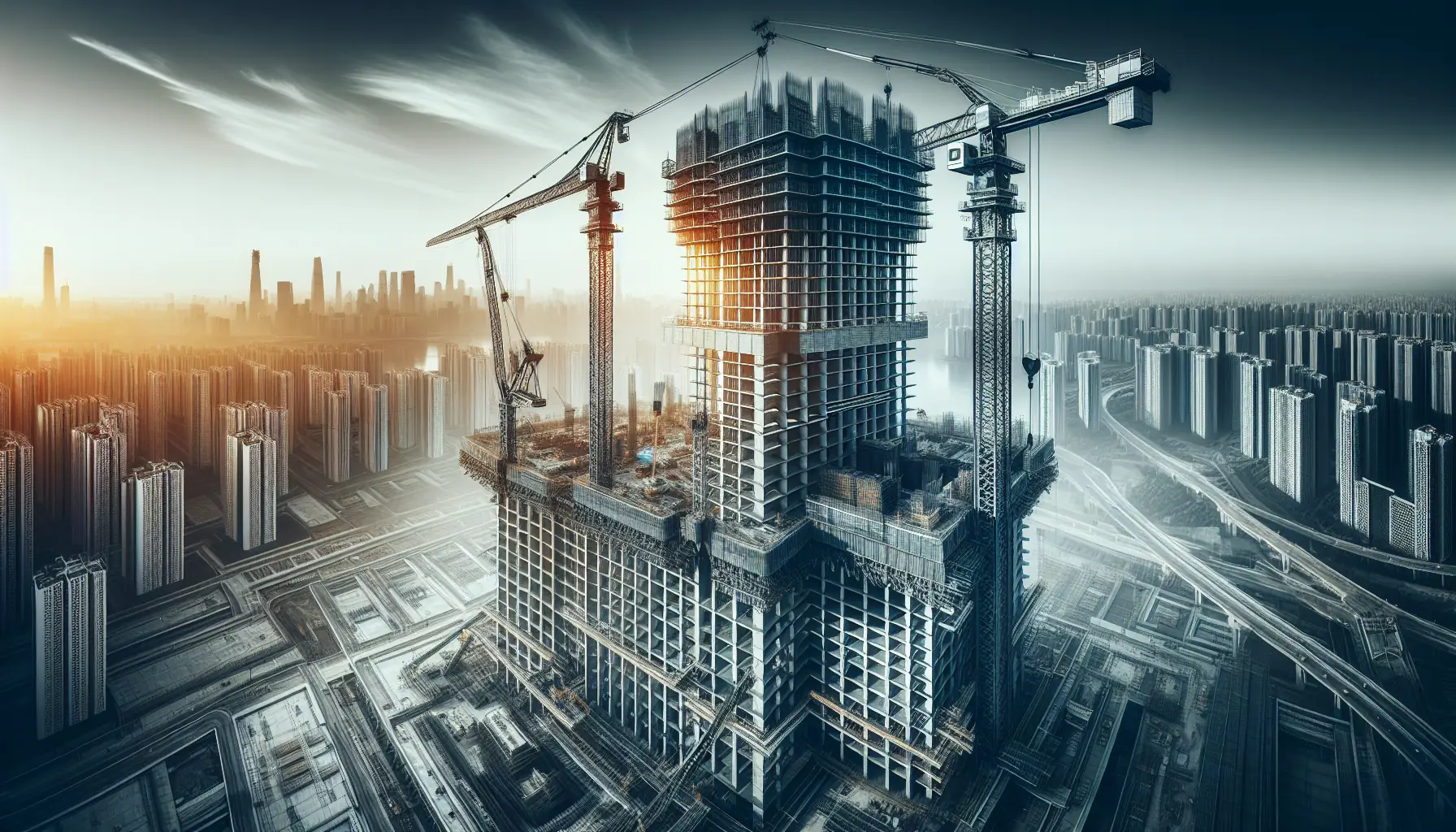
15 Essential Tips for Selecting the Perfect Crane for Construction
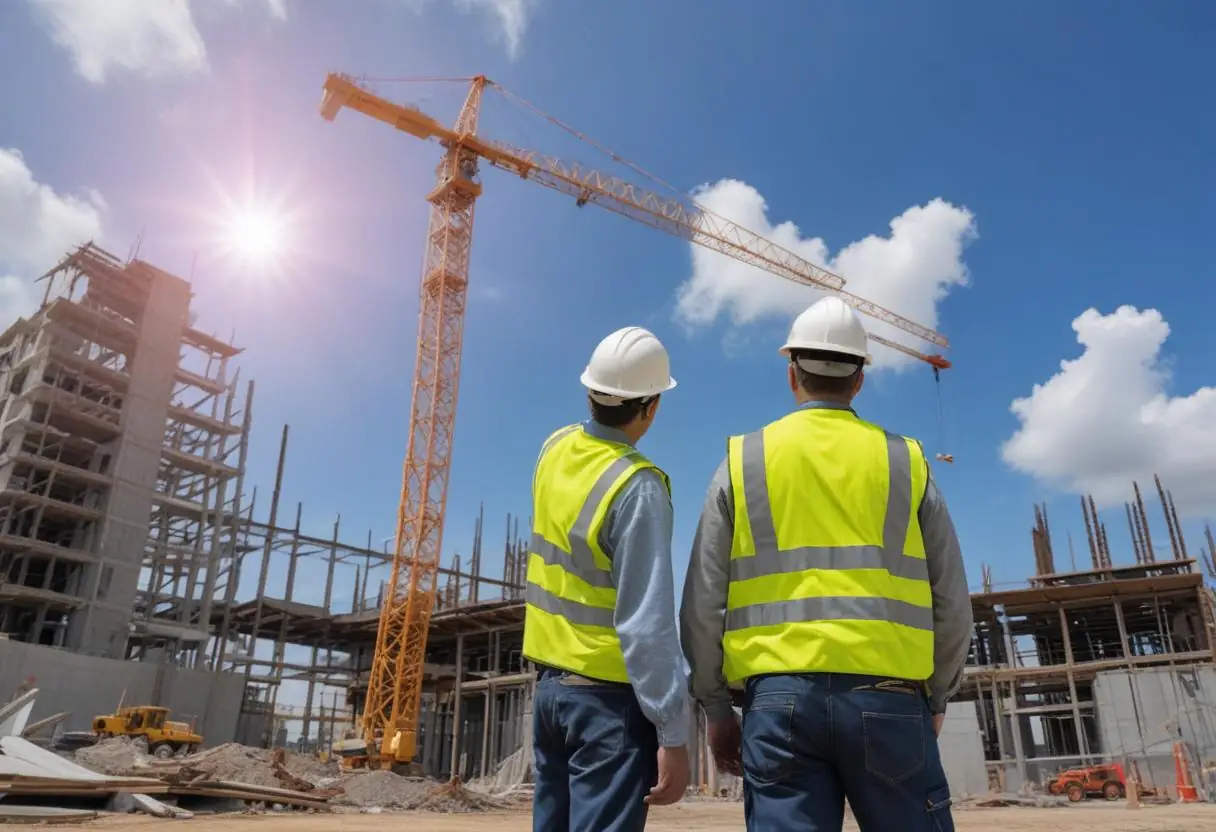
Maximize Savings: Multi-Purpose Construction Machinery for Lower Costs
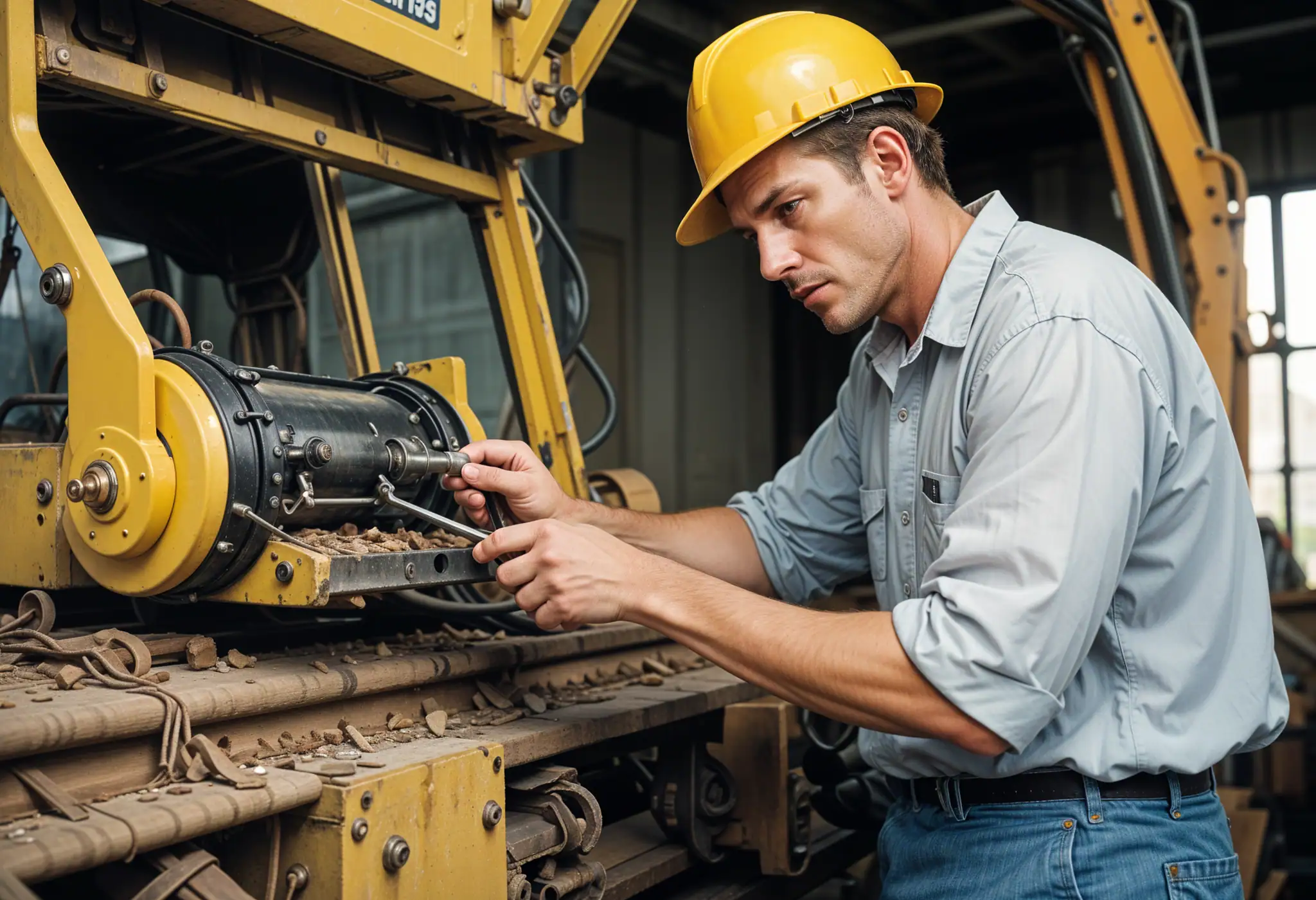
Affordable Heavy Equipment Parts: A Sourcing Guide
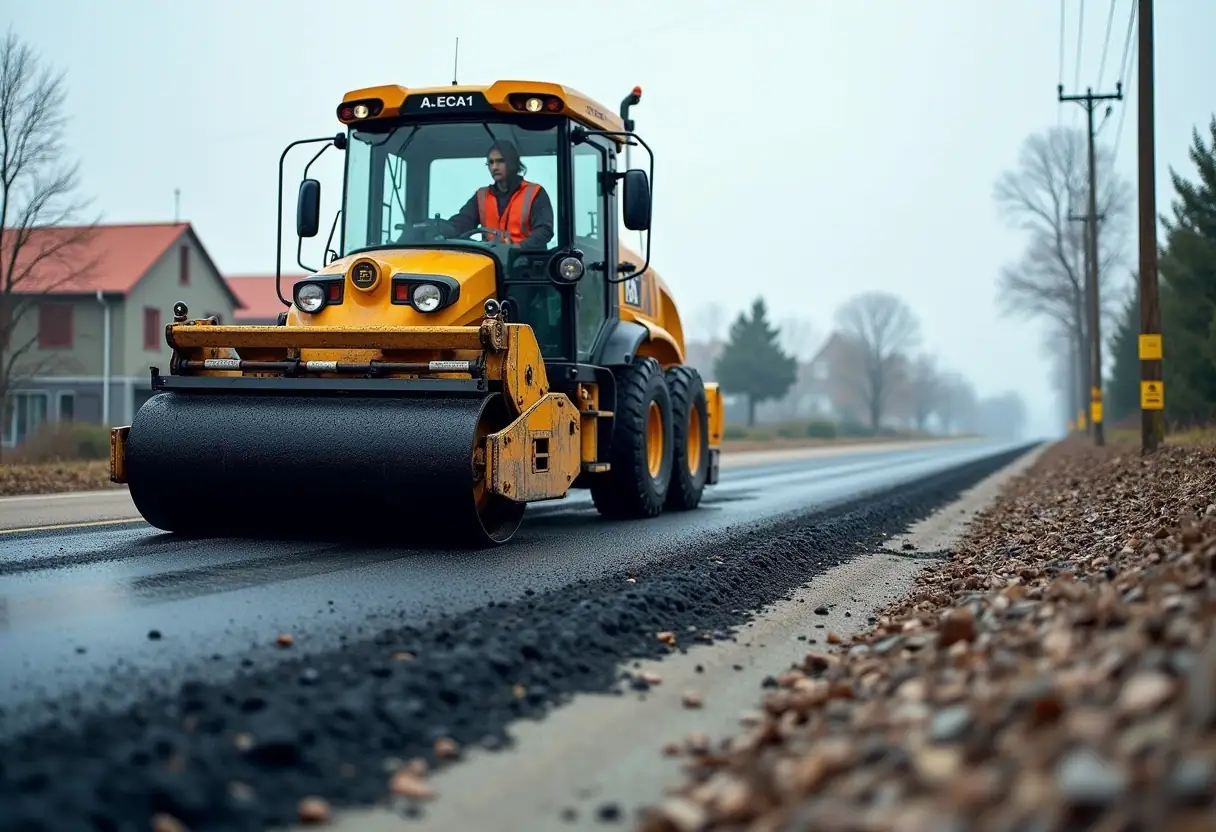
Choosing the Right Road Construction Equipment: A Complete Guide
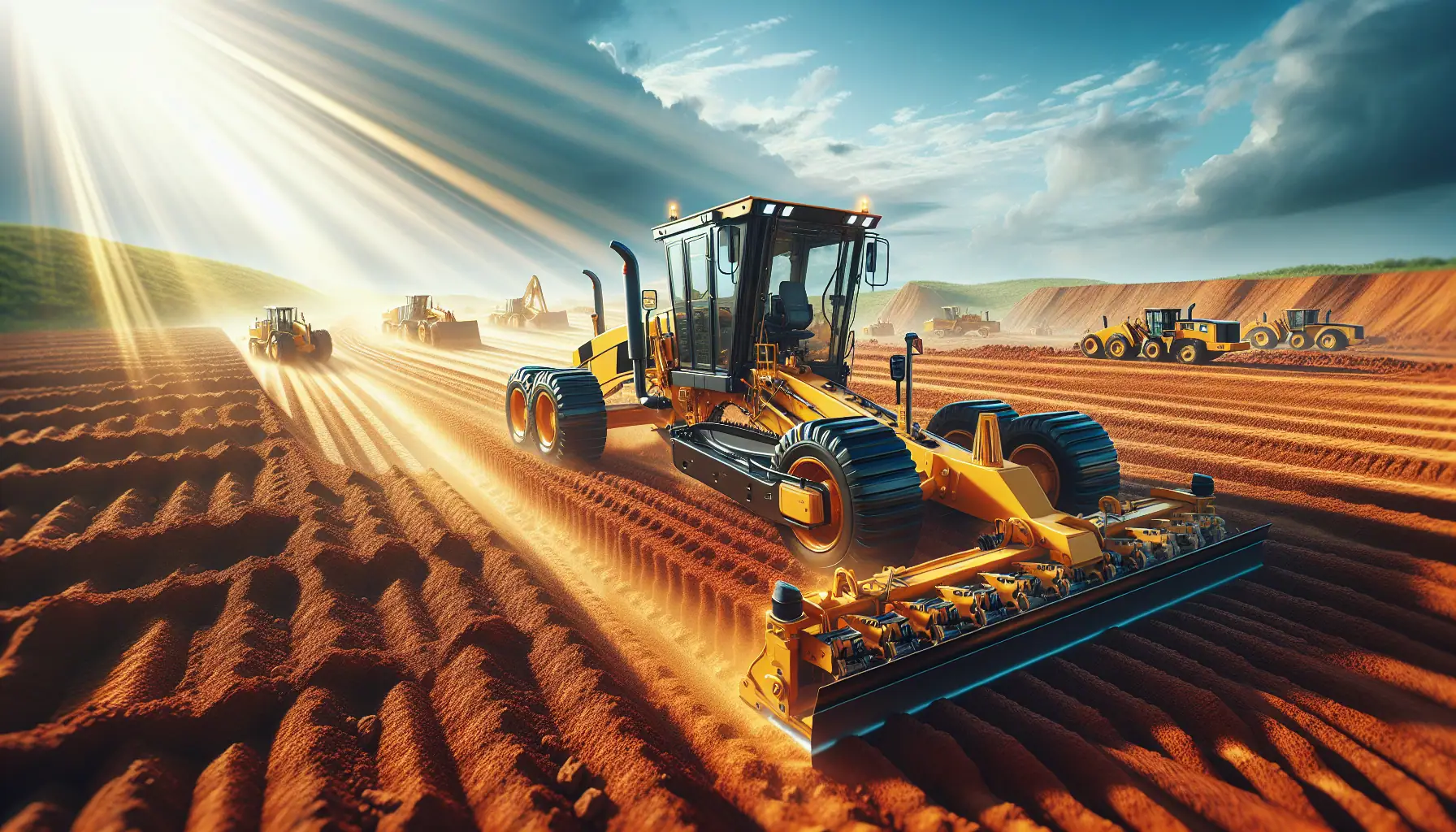
Motor Graders: Key Elements to Consider for Optimal Selection
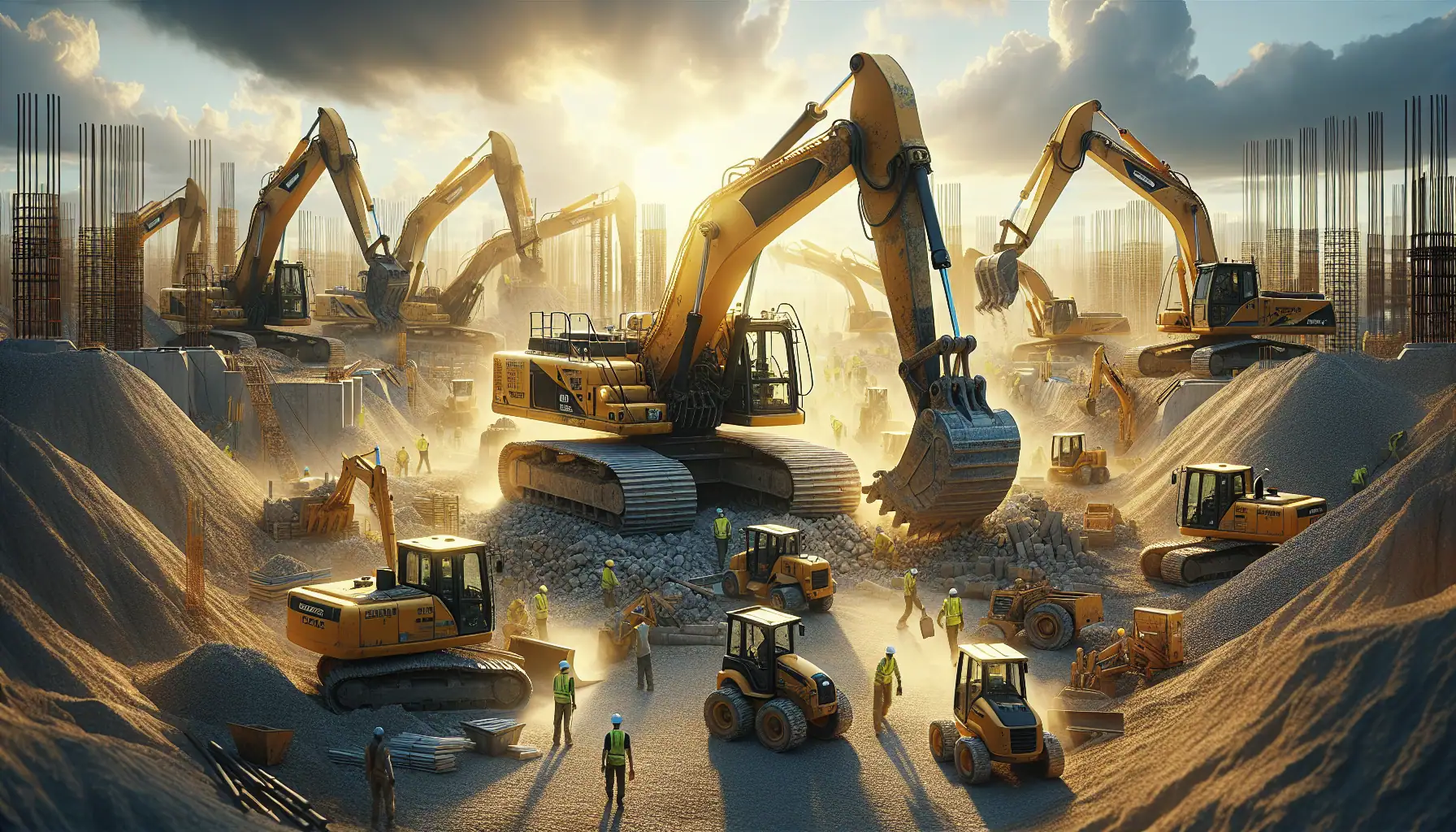
A Detailed Guide to Choosing Excavators for Construction Work
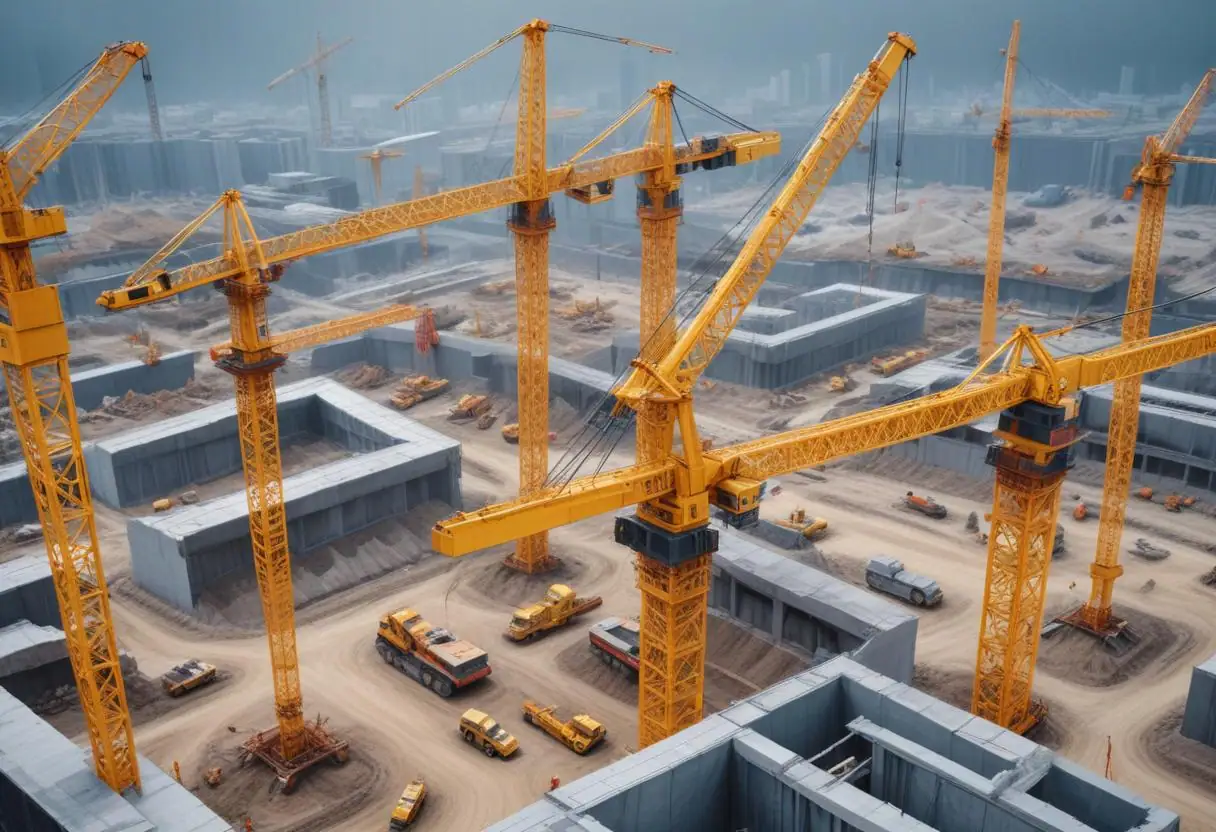
Top Tips for Choosing Cranes for Construction Projects
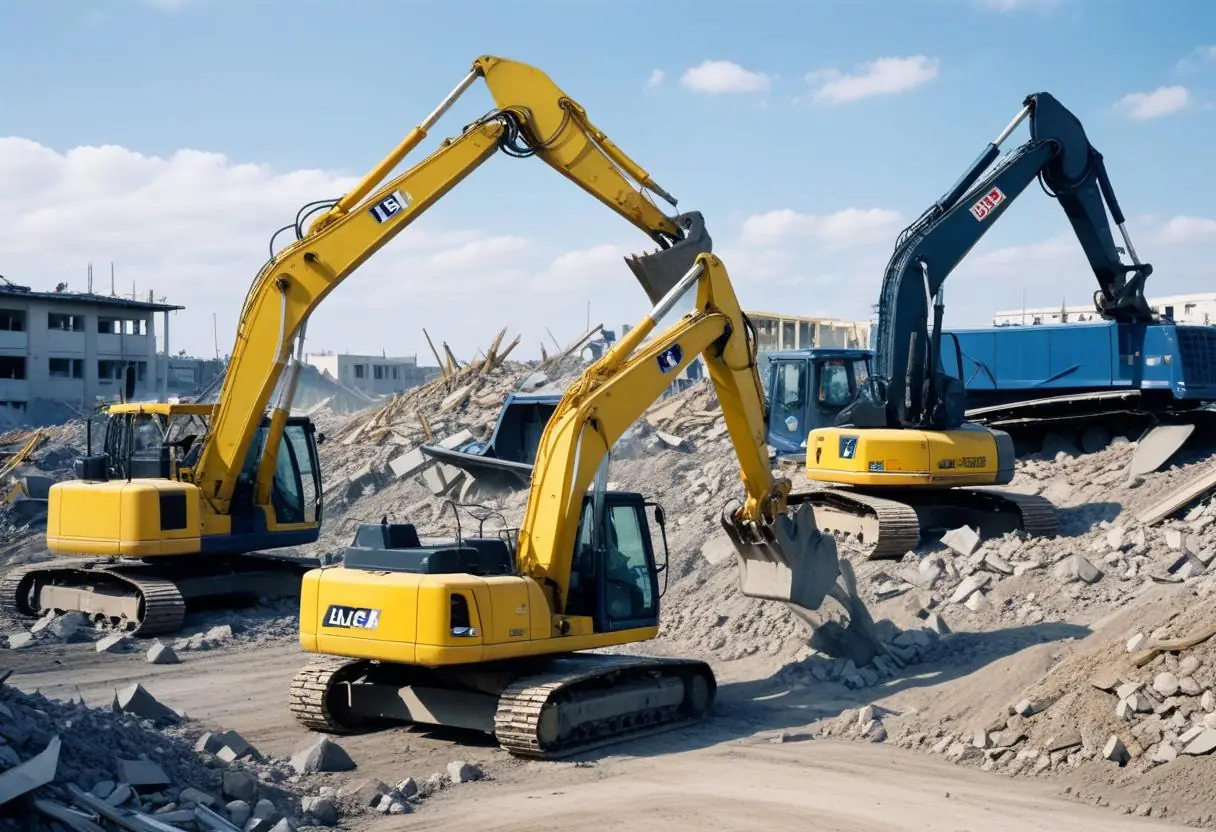
5 Top-Rated Demolition Machines for Construction Professionals
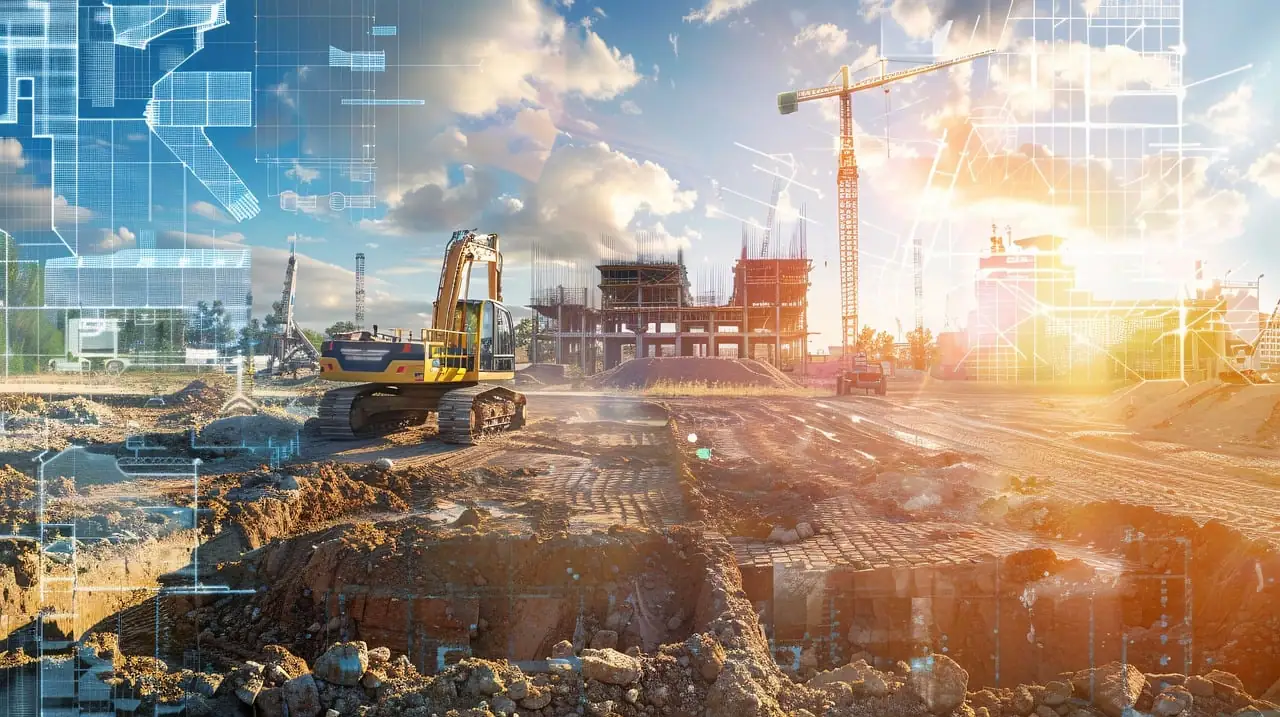
Expert Tips on Choosing Earthmoving Equipment for Large Projects
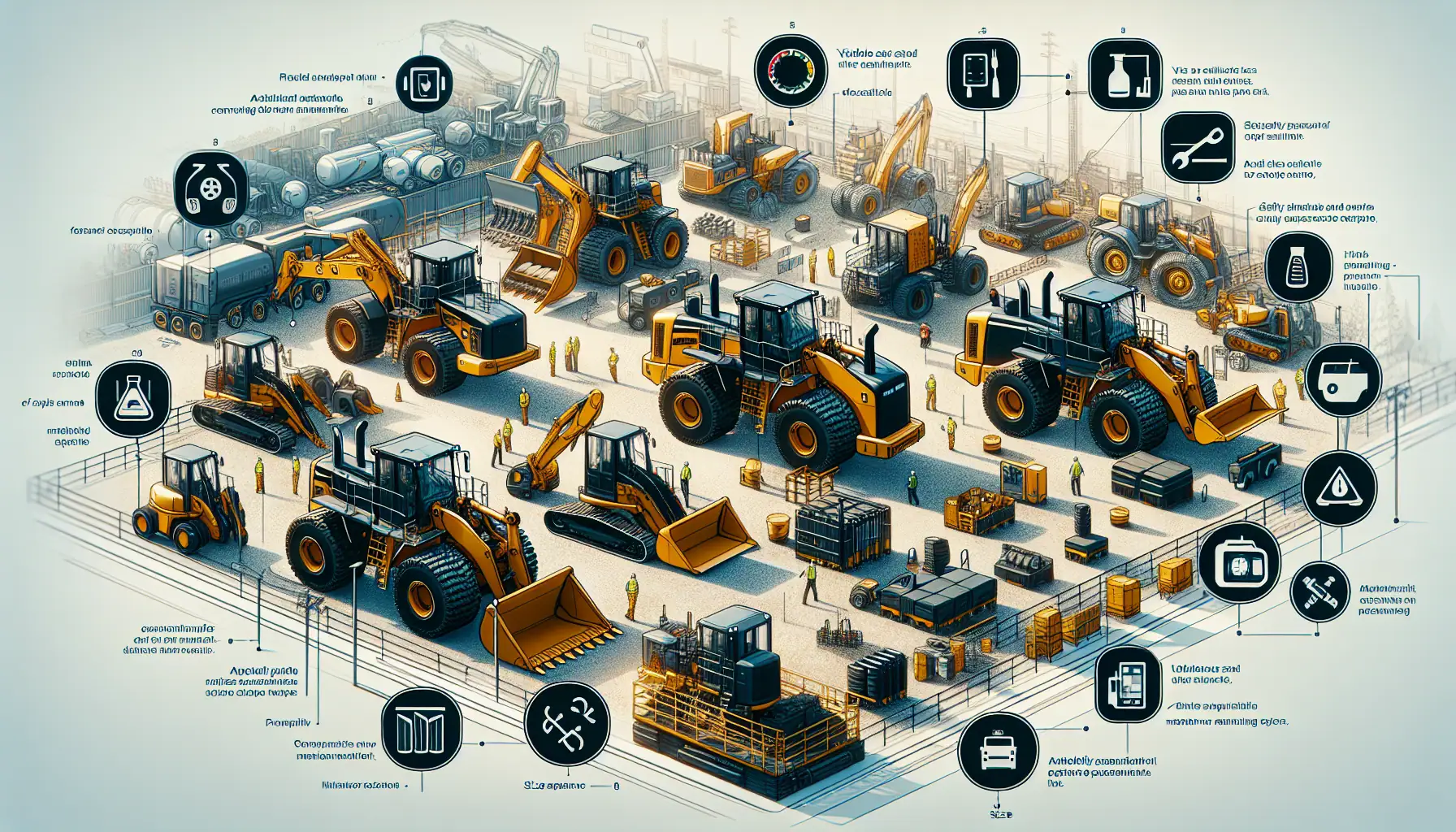
Top Functional Criteria for Selecting Heavy Construction Equipment
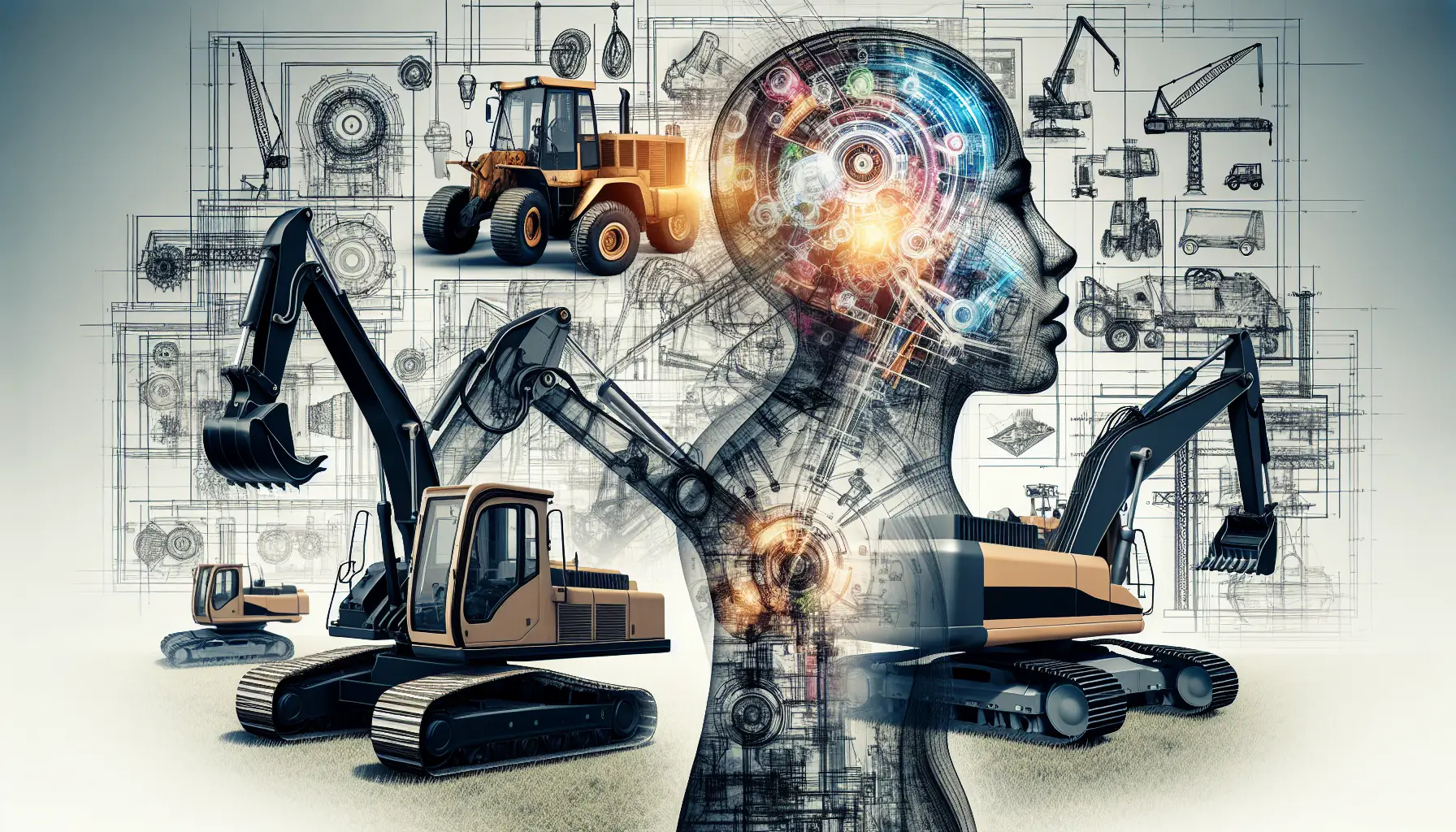
Construction Machinery: Detailed Guide to Equipment Specifications
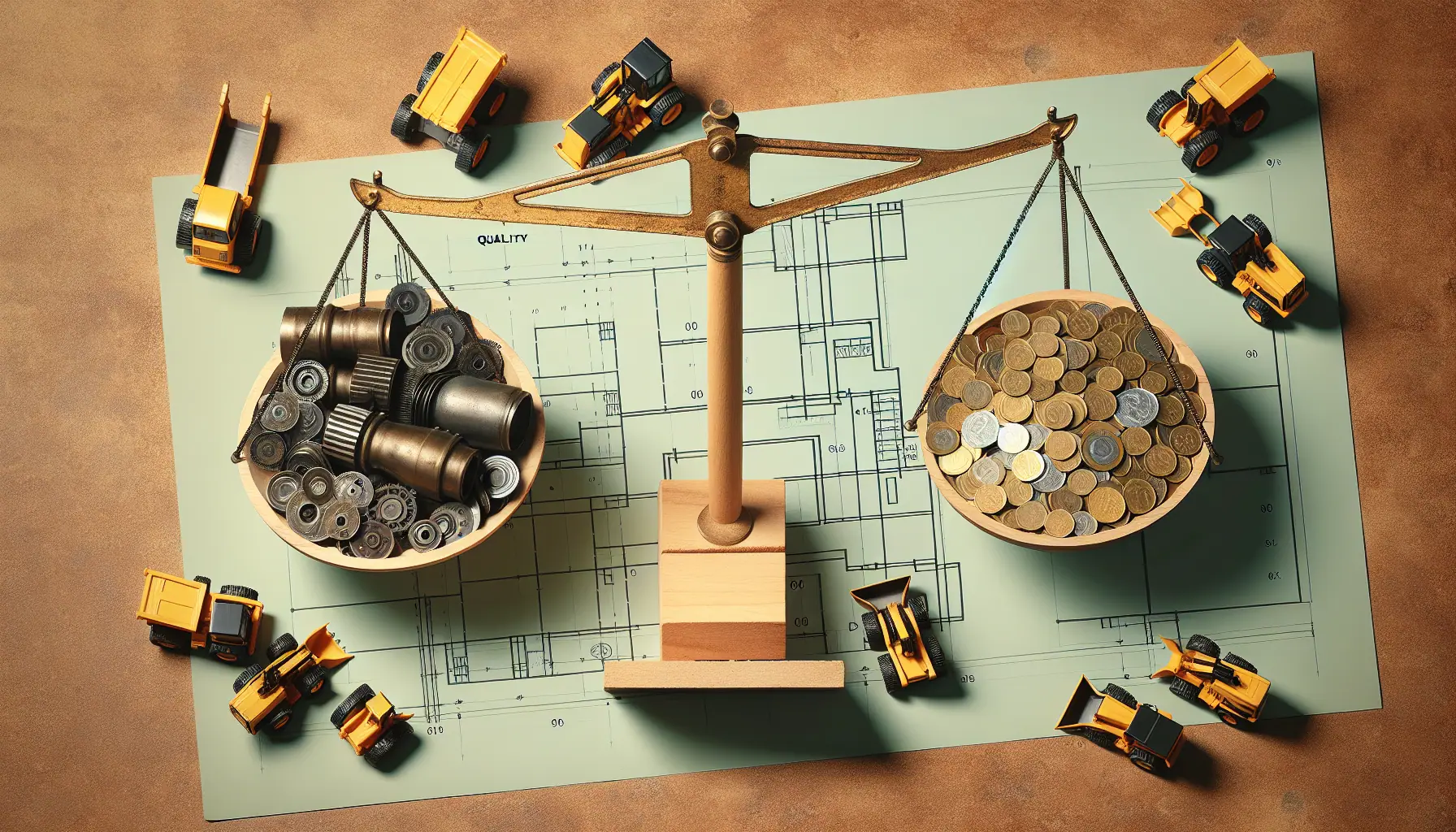
Heavy Machinery Prices: Key Factors in Cost and Quality Balance
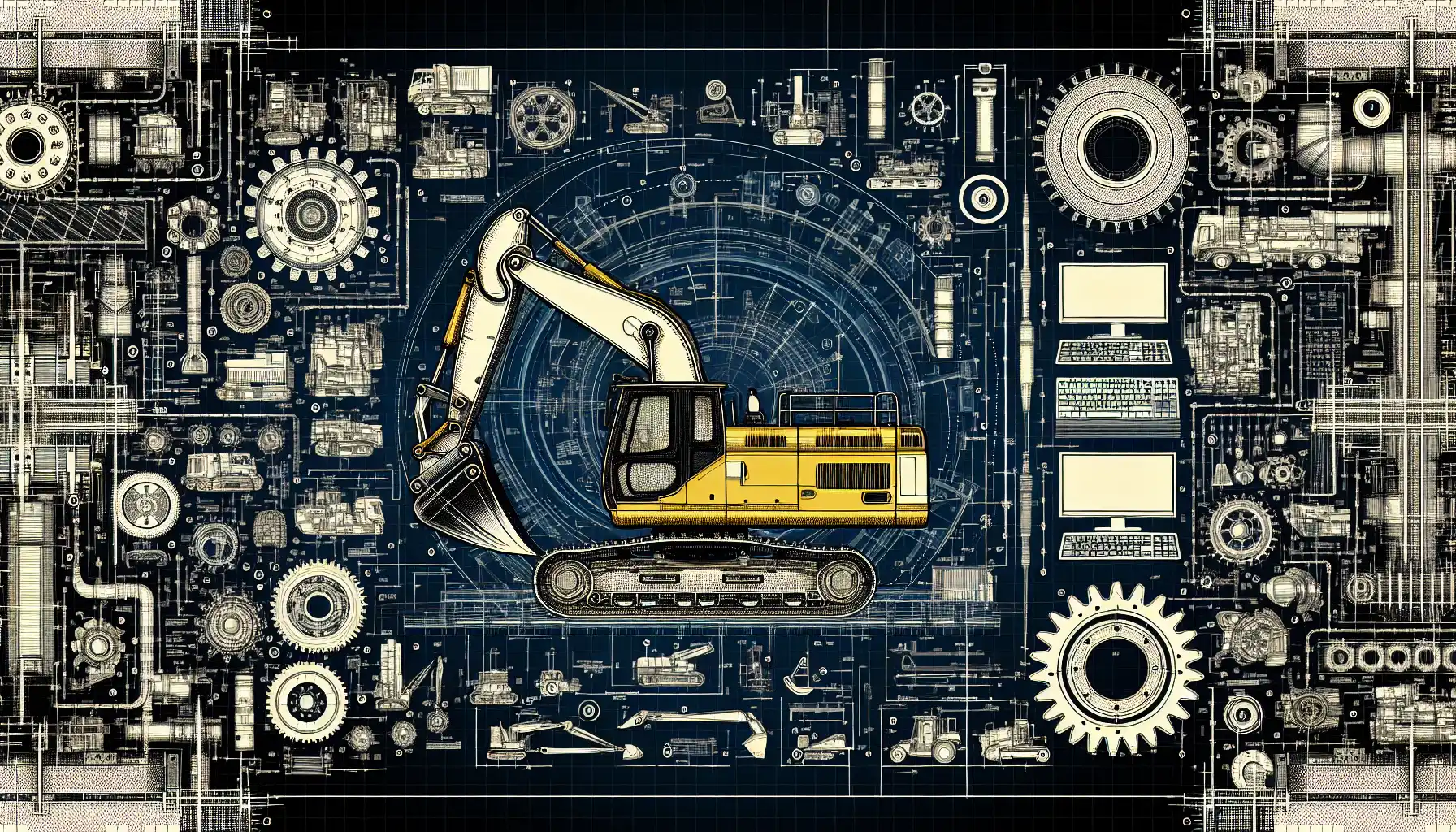
Best Construction Heavy Equipment Brands: Pros and Cons
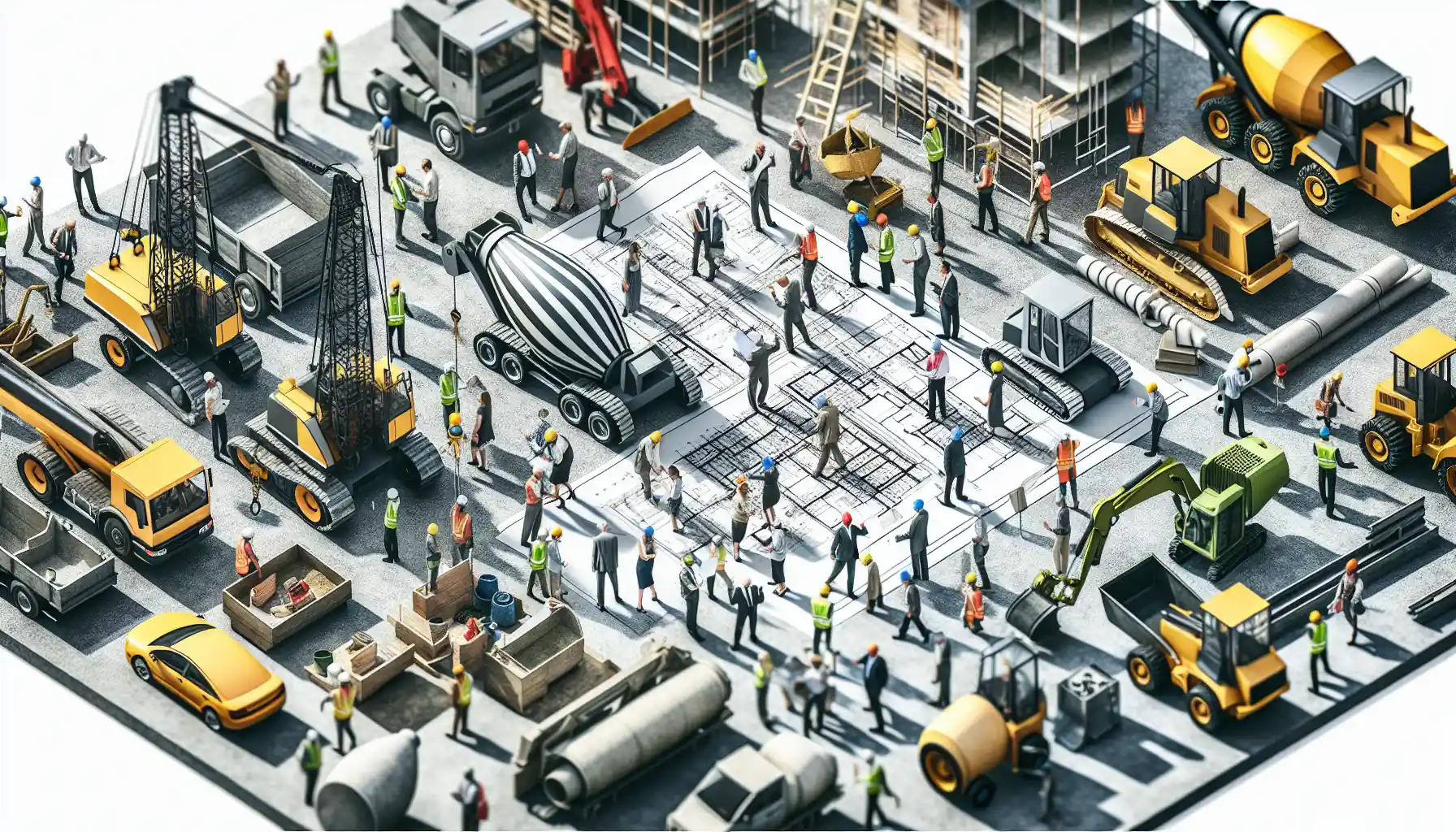
Construction Site Equipment: How to Determine Your Requirements
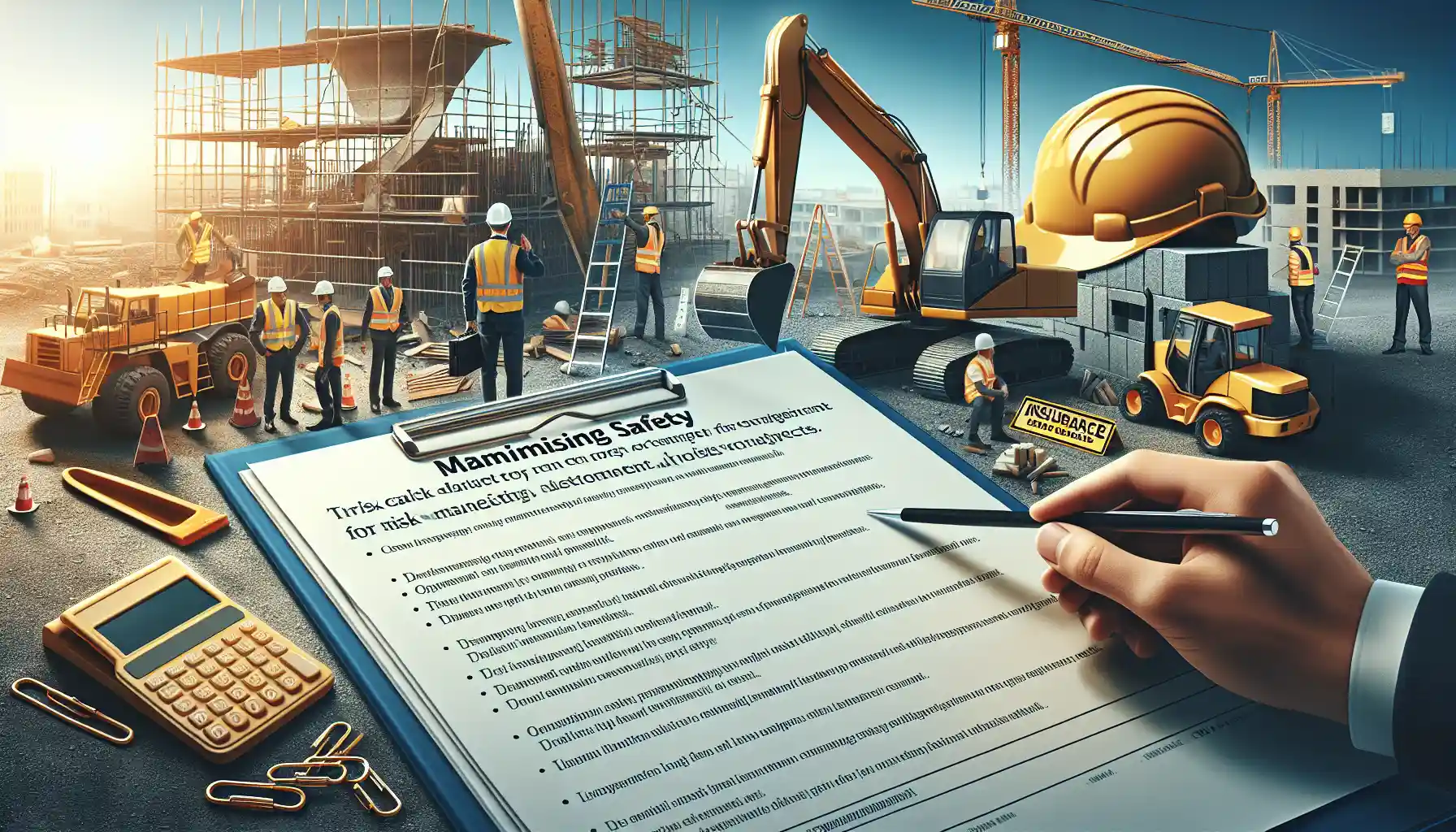
Maximizing Safety: Risk Management for Construction Projects
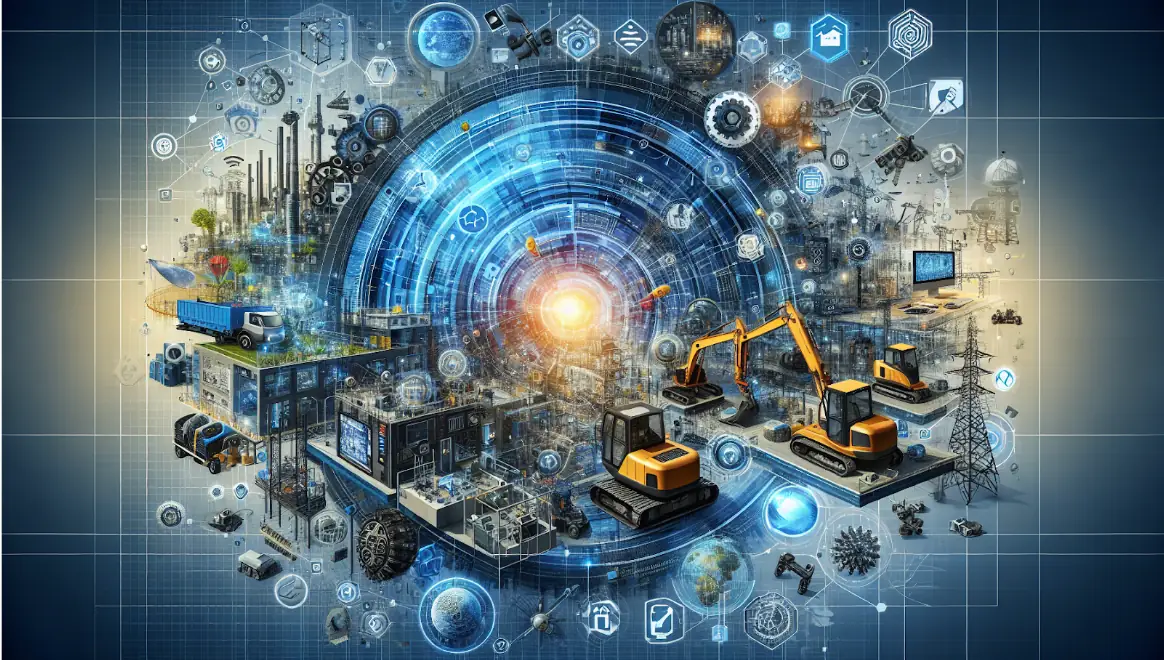
Innovations in Construction: Transforming Machinery and Equipment
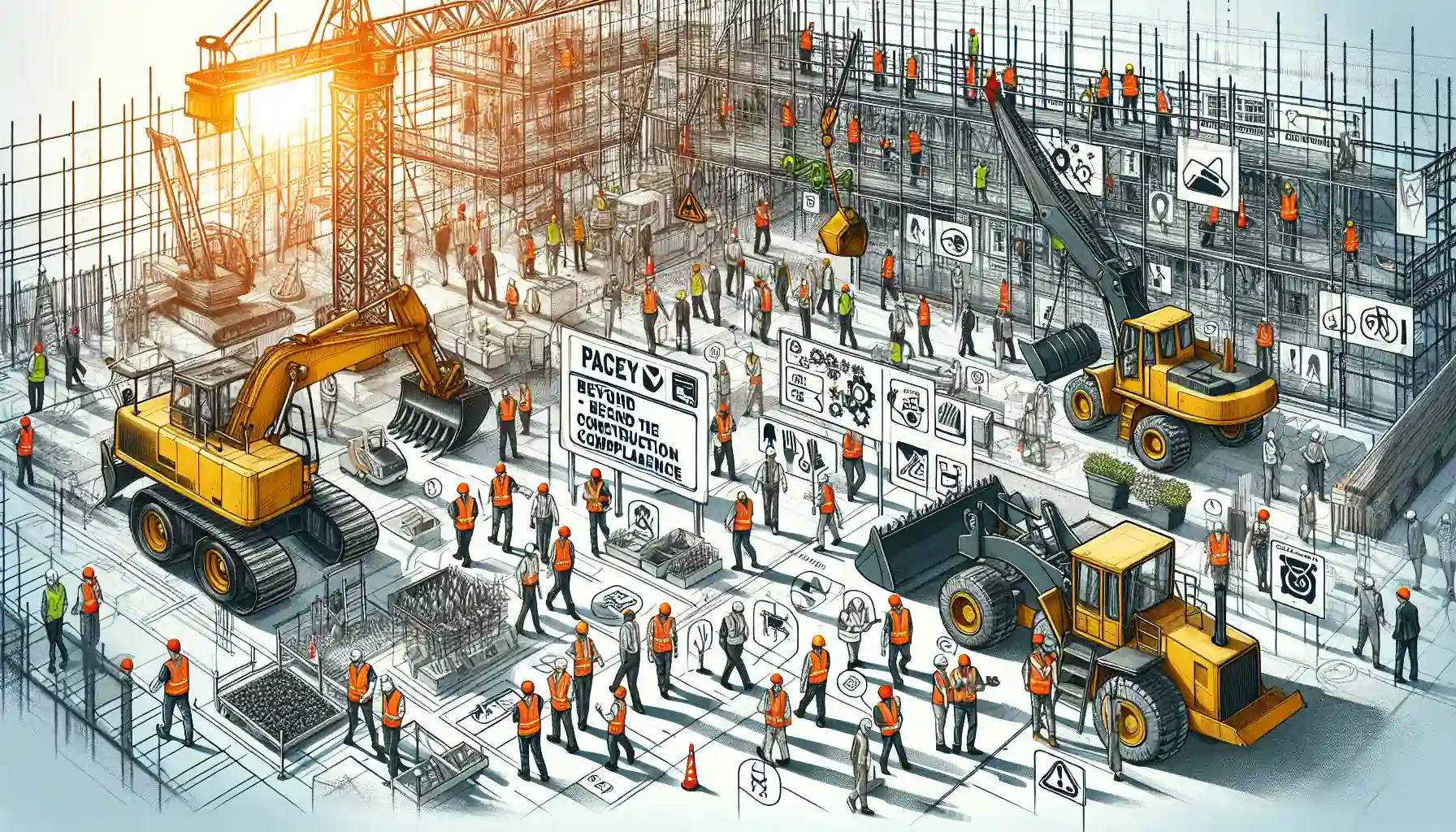
Heavy Equipment Safety: Beyond the Basics in Construction Compliance
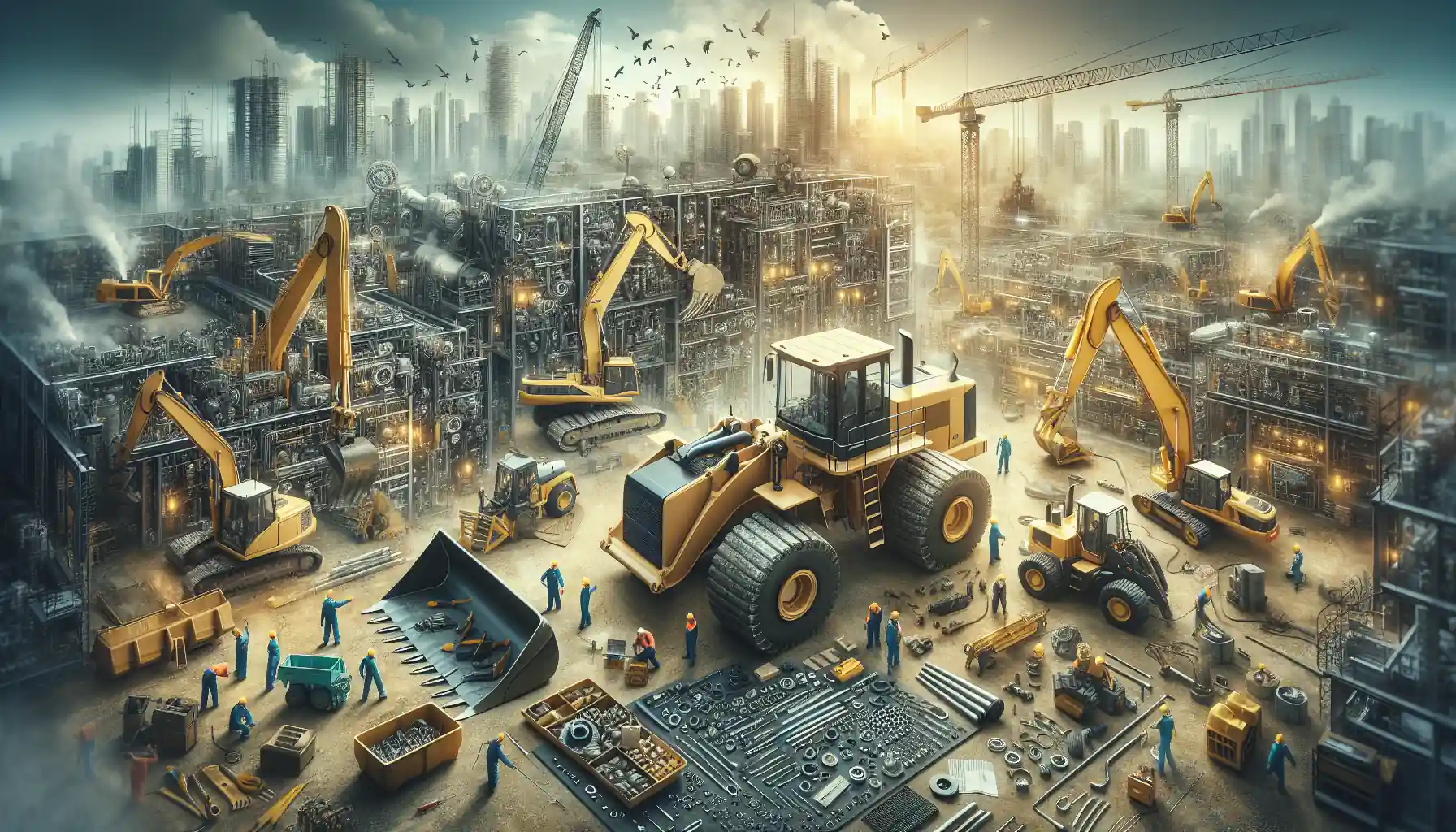
The Essential Handbook for Construction Equipment Repair and Maintenance
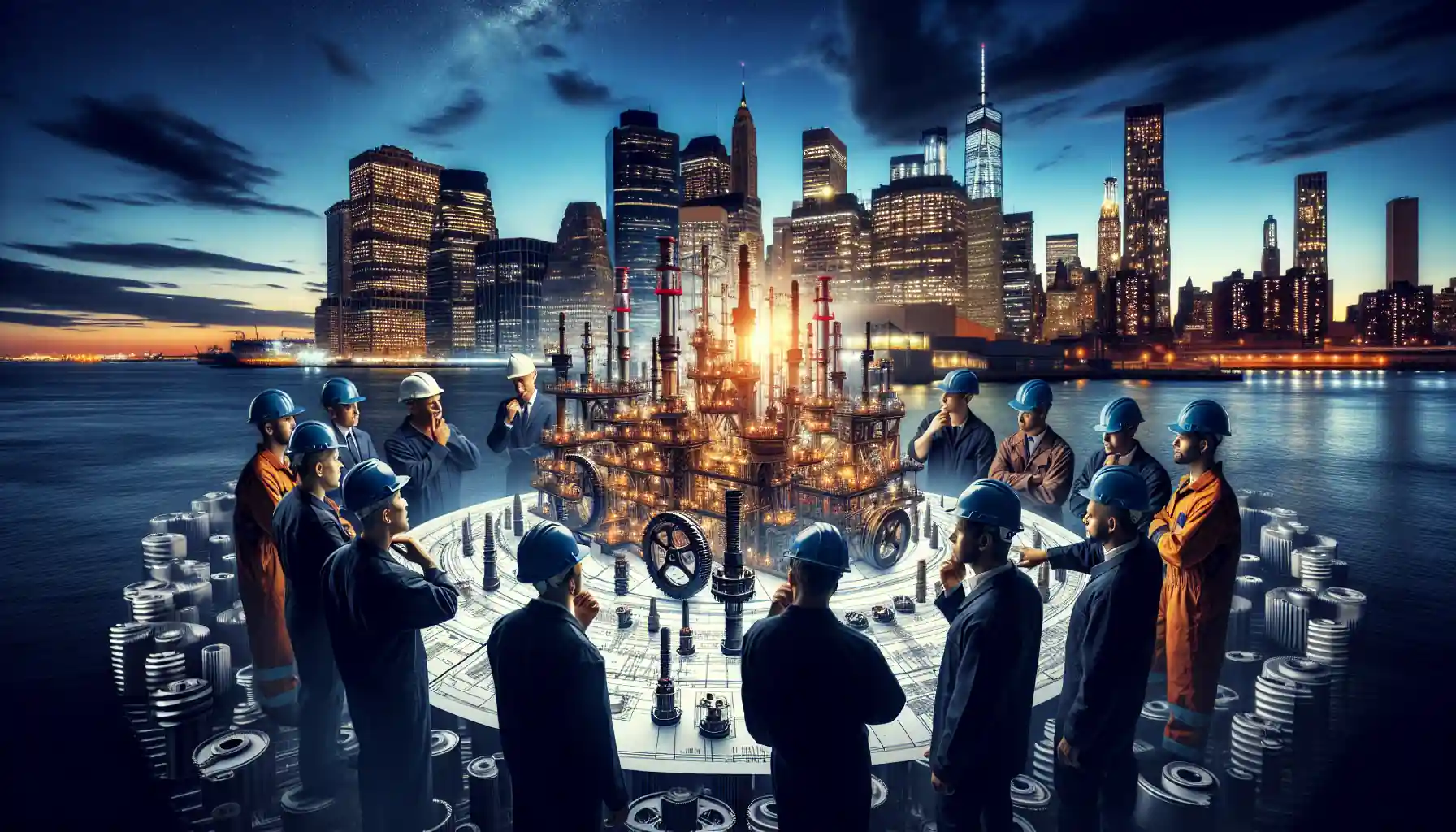
How to Efficiently Source Oil and Gas Machinery Parts in NYC
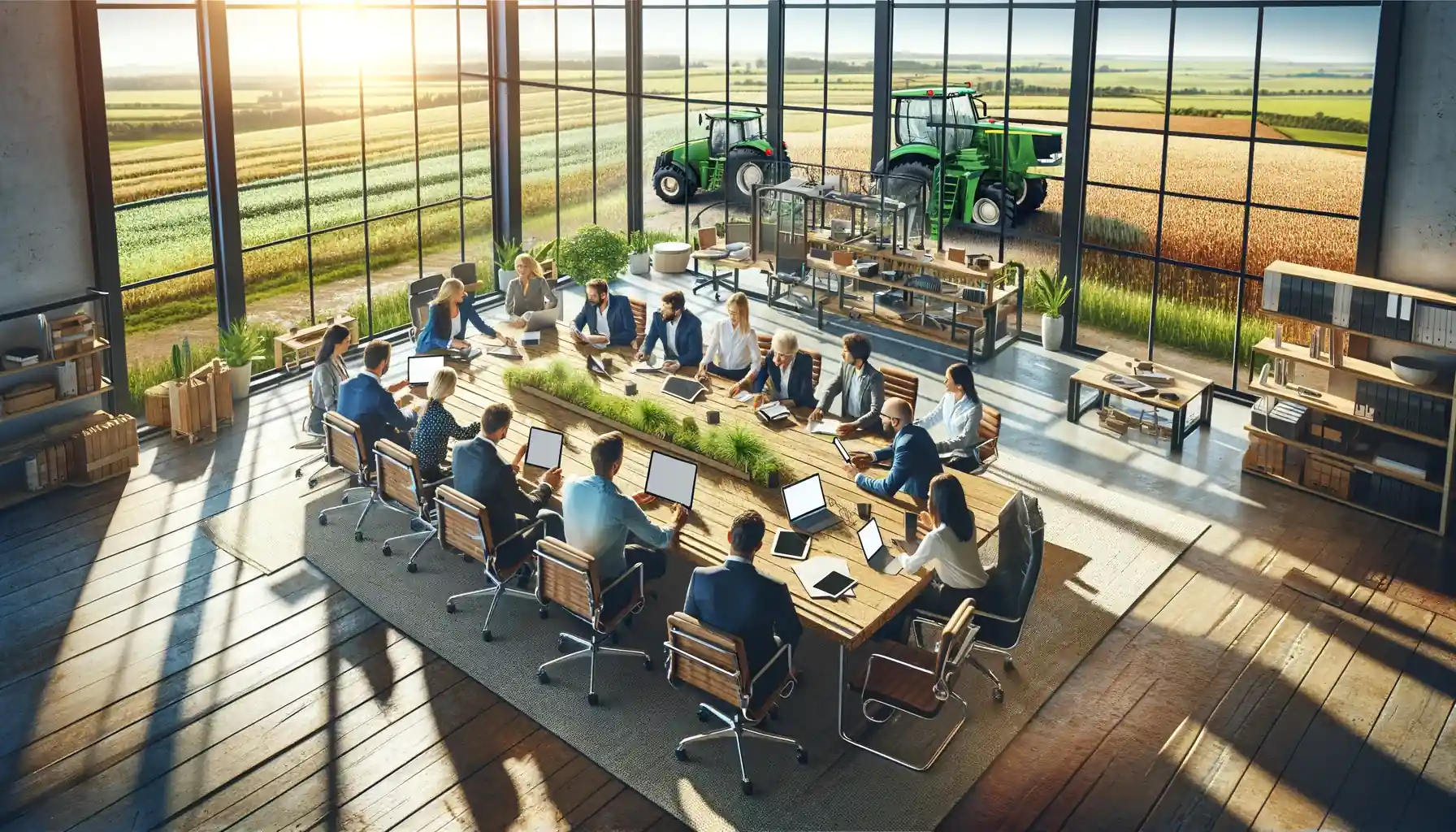
Essential Guide to Sourcing Agriculture Equipment Parts
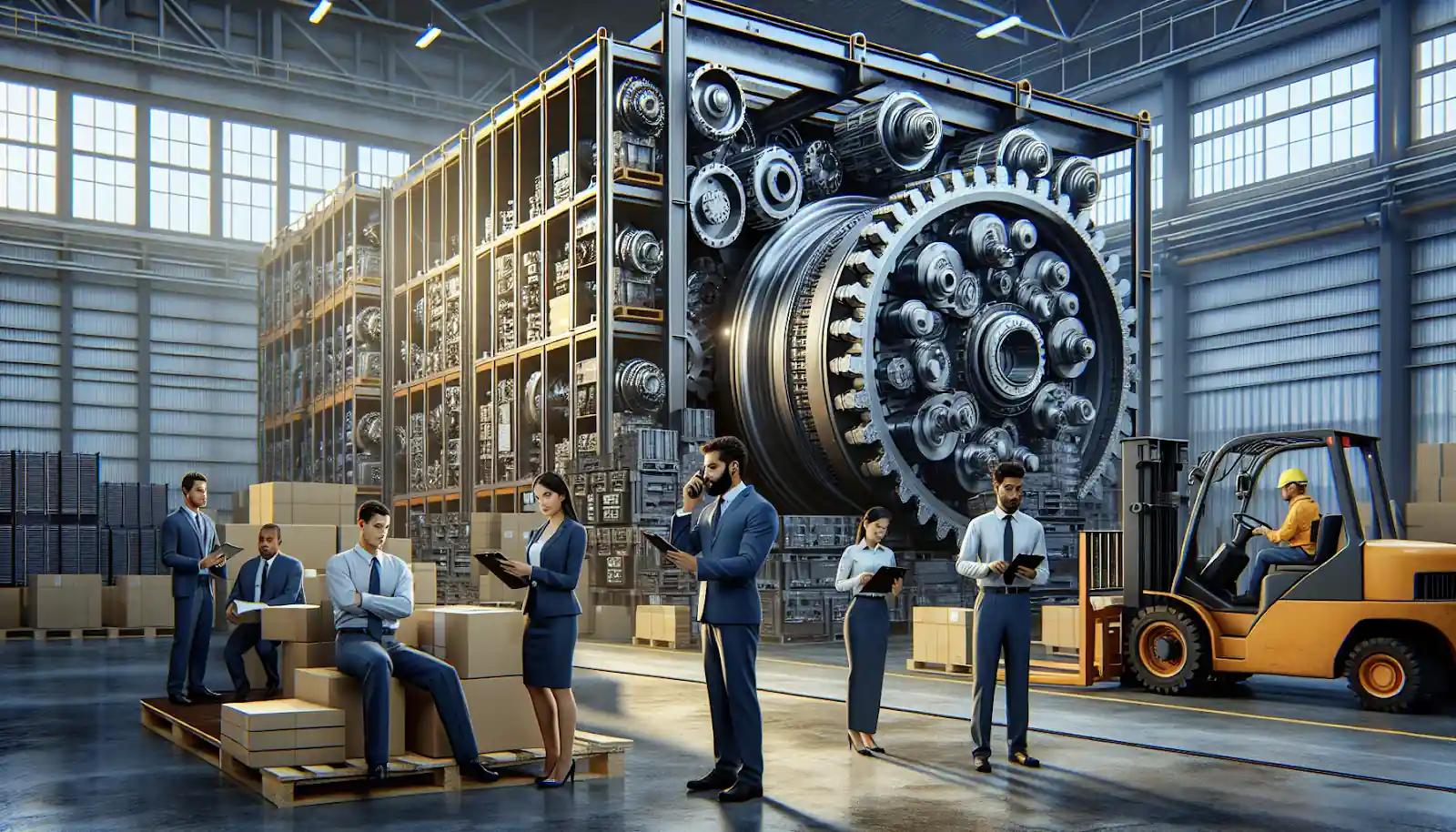
How to Source Mining Machinery Parts: Tips and Strategies
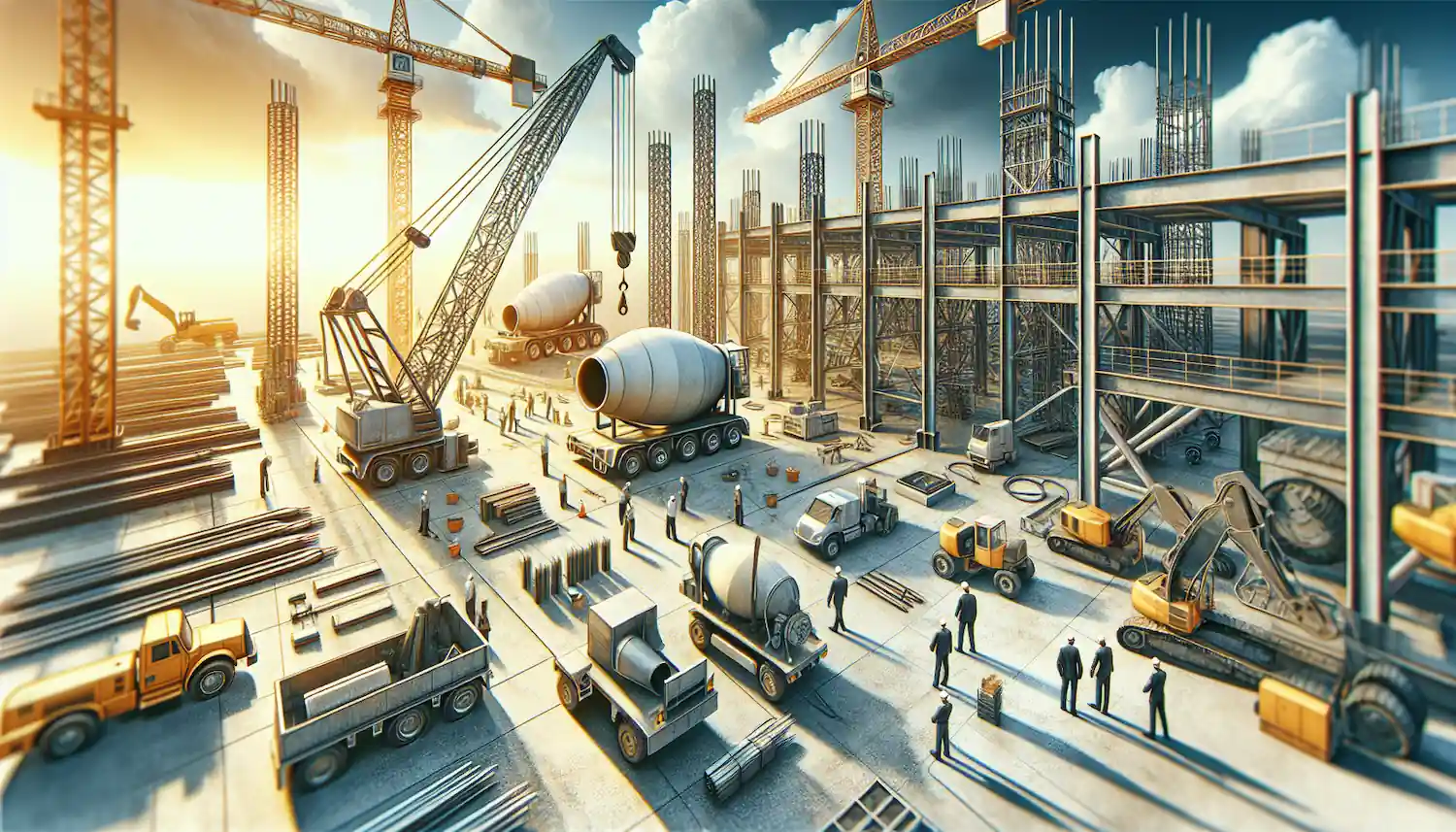