How to Implement a Construction Inventory Management System for Equipment Efficiency
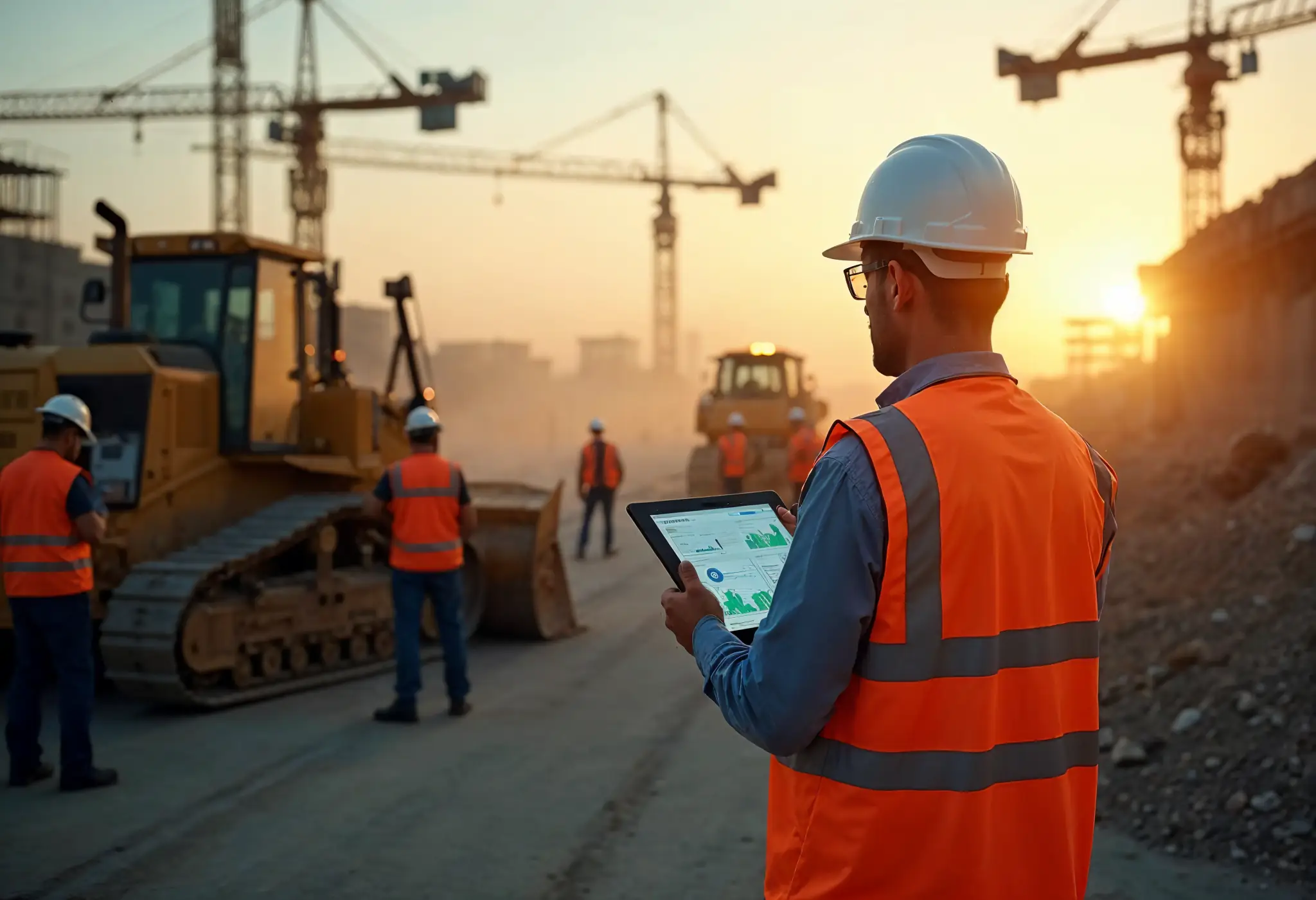
Your construction equipment represents a significant investment, and managing it effectively can mean the difference between project success and costly delays. A construction inventory management system helps you track, maintain, and optimize your equipment fleet while reducing unnecessary expenses and improving operational efficiency. Implementing a robust preventive maintenance program is crucial for ensuring equipment longevity and reliability.
Modern inventory management software for the construction industry combines real-time tracking, automated alerts, and detailed reporting capabilities. These systems help you maintain accurate equipment records, schedule preventive maintenance efficiently, and make data-driven decisions about your fleet management strategy. By focusing on safety and compliance, you can significantly reduce risks associated with equipment failures.
In this comprehensive guide, you'll discover:
- How to assess your current equipment management needs
- Steps to build the right technology infrastructure
- Methods for creating effective tracking workflows
- Strategies for successful staff training and adoption
- Ways to optimize your system's performance and implement effective maintenance strategies
Let's explore how you can transform your equipment operations and boost your operational efficiency through improved resource management and preventive maintenance.
Assessing Current Equipment Management Needs
Starting a successful construction inventory management system requires a thorough assessment of your current operations. Studies show that companies using comprehensive diagnostic tools can reduce maintenance costs by up to 20% while improving equipment availability by 15%.
Equipment Inventory Audit Process
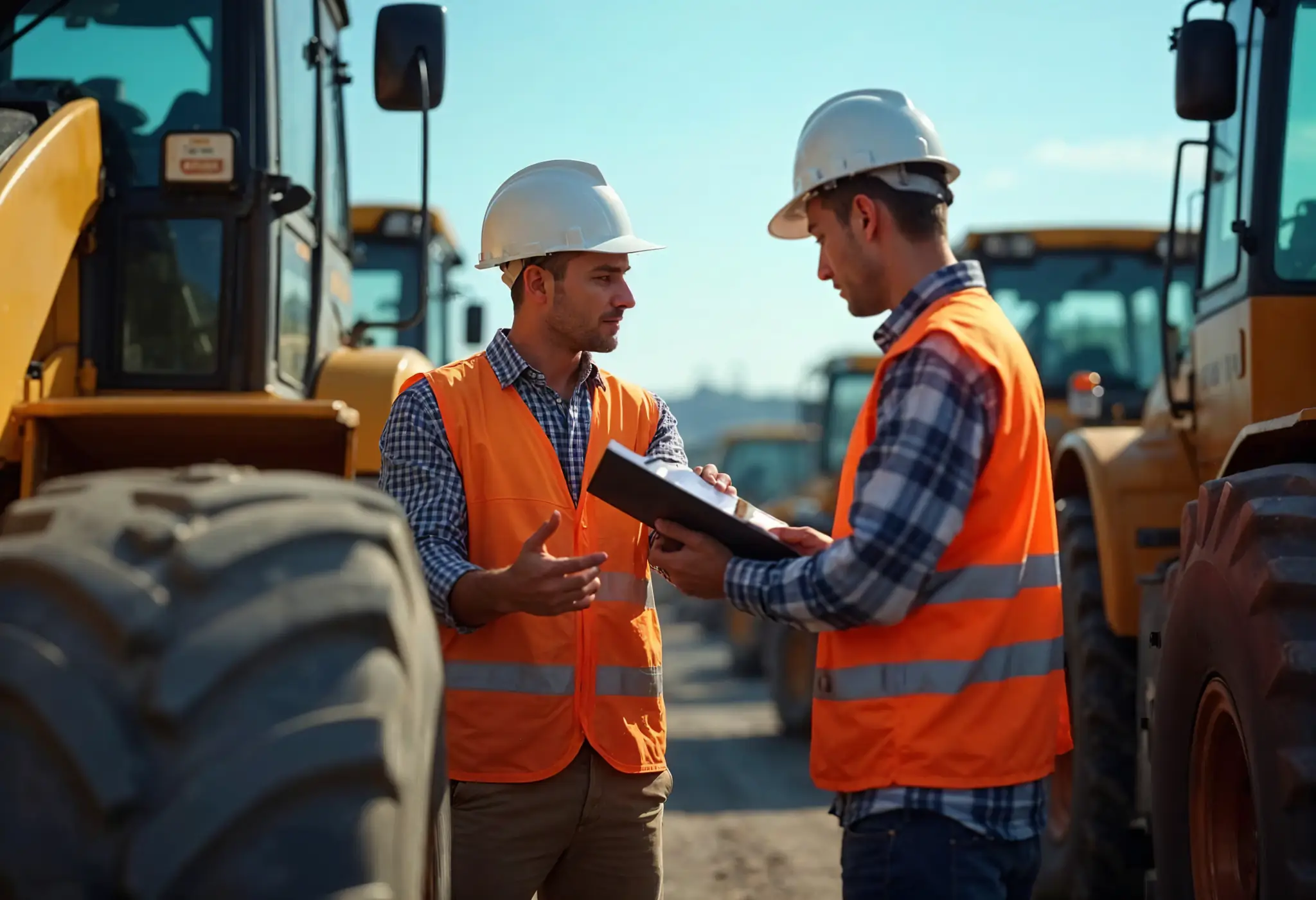
Your first step is conducting a detailed equipment audit. A proper audit helps you identify gaps in your current system and create a foundation for improvement. Key audit components include:
- Physical verification of all equipment and their conditions
- Documentation review of maintenance records and preventive maintenance schedules
- Analysis of equipment usage patterns and life expectancy
- Assessment of current tracking methods and safety protocols
- Evaluation of maintenance schedules and compliance with manufacturer guidelines
Identifying Operational Bottlenecks
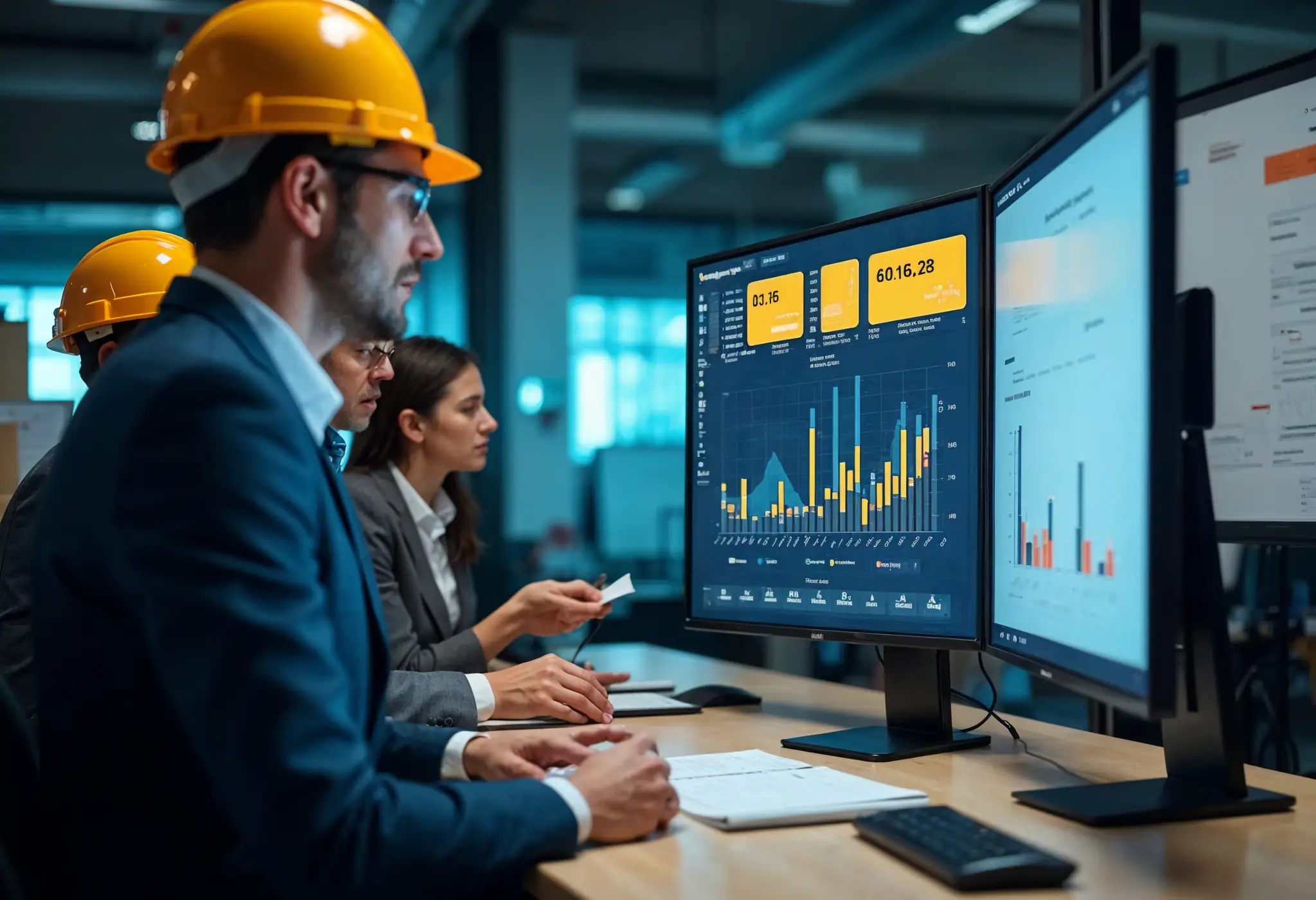
Understanding your operational challenges helps prevent costly delays and inefficiencies. Construction companies spend between 30-50% of their annual operating budgets on equipment maintenance and repair. To identify bottlenecks effectively, follow these steps:
- Review equipment movement patterns and safety procedures
- Analyze maintenance schedules and unplanned downtime
- Assess current utilization rates and equipment uptime
- Examine equipment check-in/check-out processes
- Evaluate communication workflows between maintenance technicians and other teams
Setting System Requirements
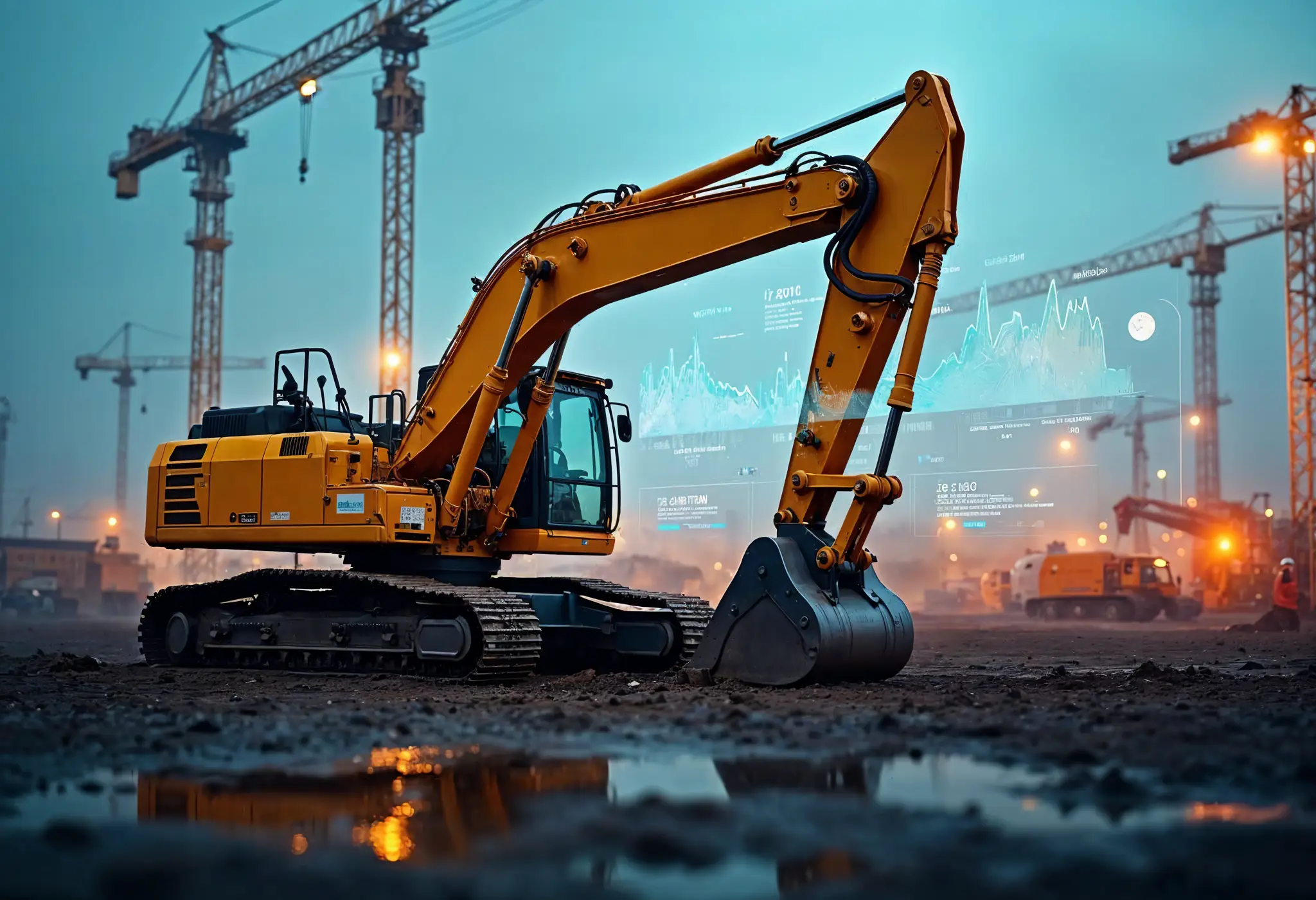
Your construction inventory management system should address specific operational needs. Research indicates that implementing predictive maintenance can reduce equipment downtime by up to 30%. Focus on these essential features:
Real-Time Tracking: Your system should provide instant updates on equipment location and status. IoT sensors can help track equipment status, utilization, and fluid levels in real-time.
Maintenance Scheduling: Set up automated alerts for routine inspections and preventive maintenance. This helps extend equipment life span and reduces unexpected breakdowns.
Data Integration: Your system should connect with existing software platforms to provide comprehensive oversight of all operations, including maintenance planning and resource management.
Security Controls: Implement role-based access and robust security measures to protect sensitive equipment data and ensure compliance with safety regulations.
Need expert guidance on selecting the right construction inventory management system for your equipment fleet? Contact MCH Parts for a free sourcing consultation and discover how to optimize your equipment management strategy and implement effective preventive maintenance.
Building a Technology Infrastructure
Building the right technology infrastructure is crucial for your construction inventory management system's success. Studies show that cloud-based construction management solutions are leading the market and expected to grow significantly in upcoming years.
Hardware Requirements and Setup
Your hardware foundation needs to support real-time tracking and data collection. Essential components include:
- Computers with Windows 7 or later operating systems
- Barcode scanners or RFID readers for quick asset identification
- IoT sensors for equipment monitoring and condition-based maintenance
- GPS tracking devices for location management and safety monitoring
- Stable internet connection for cloud access and real-time data transmission
Studies indicate that organizations using comprehensive diagnostic tools can reduce maintenance costs by up to 20% while improving equipment availability.
Software Integration Points
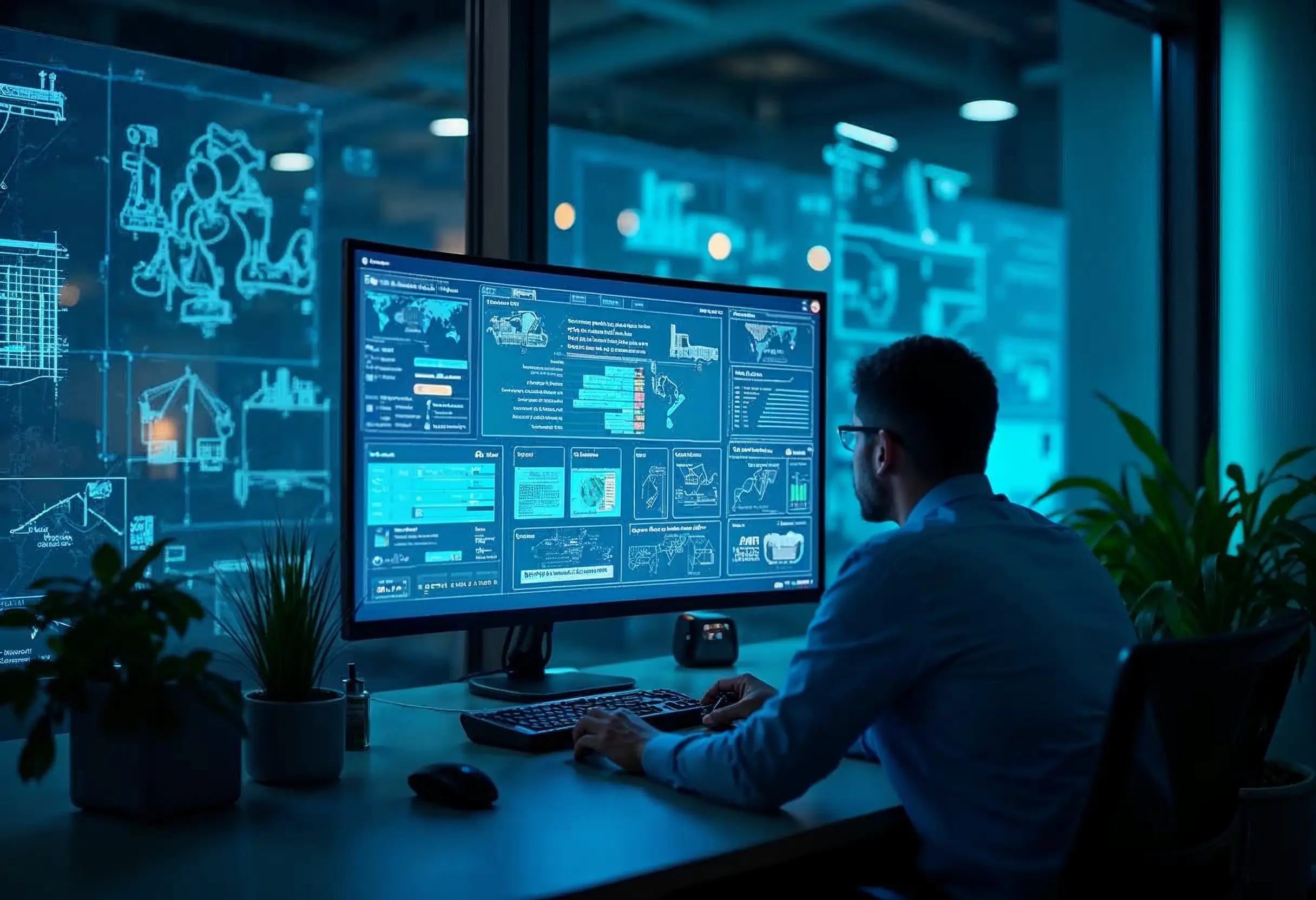
Your software infrastructure must connect seamlessly with existing systems. Cloud-based platforms enable you to access, share, and process project data from any device with an internet connection. Integration priorities should focus on:
ERP Connection: Link your inventory system with accounting and enterprise resource planning software for comprehensive financial tracking and maintenance planning.
Real-Time Analytics: Implement software that provides instant updates on equipment status, location, and performance metrics. Companies using these systems have reported savings of approximately $700,000 annually through predictive maintenance and condition monitoring.
Mobile Accessibility: Ensure your system works across multiple devices, allowing field teams and maintenance technicians to access and update information instantly.
Security and Access Controls
Protecting your equipment data is crucial. Research shows that implementing proper access controls and security measures significantly reduces unauthorized use and theft. Key security features should include:
Role-Based Access: Restrict system access based on job functions and responsibilities. This helps maintain accountability and prevents unauthorized equipment use while ensuring compliance with safety protocols.
Monitoring Systems: Install surveillance systems and IoT sensors to track equipment movement, usage patterns, and perform machine monitoring for preventive maintenance purposes.
Data Protection: Implement encryption and secure authentication methods to protect sensitive equipment information and maintenance records.
Need help selecting and implementing the right technology infrastructure for your construction equipment management? Contact MCH Parts for a free sourcing consultation and discover how to build a robust system tailored to your needs, including preventative maintenance software.
Creating Equipment Tracking Workflows
Effective equipment tracking workflows are essential for your construction inventory management system. Studies show that construction companies report nearly 1,000 pieces of equipment stolen monthly, making robust tracking procedures crucial for your operations and overall safety.
Check-in/Check-out Procedures
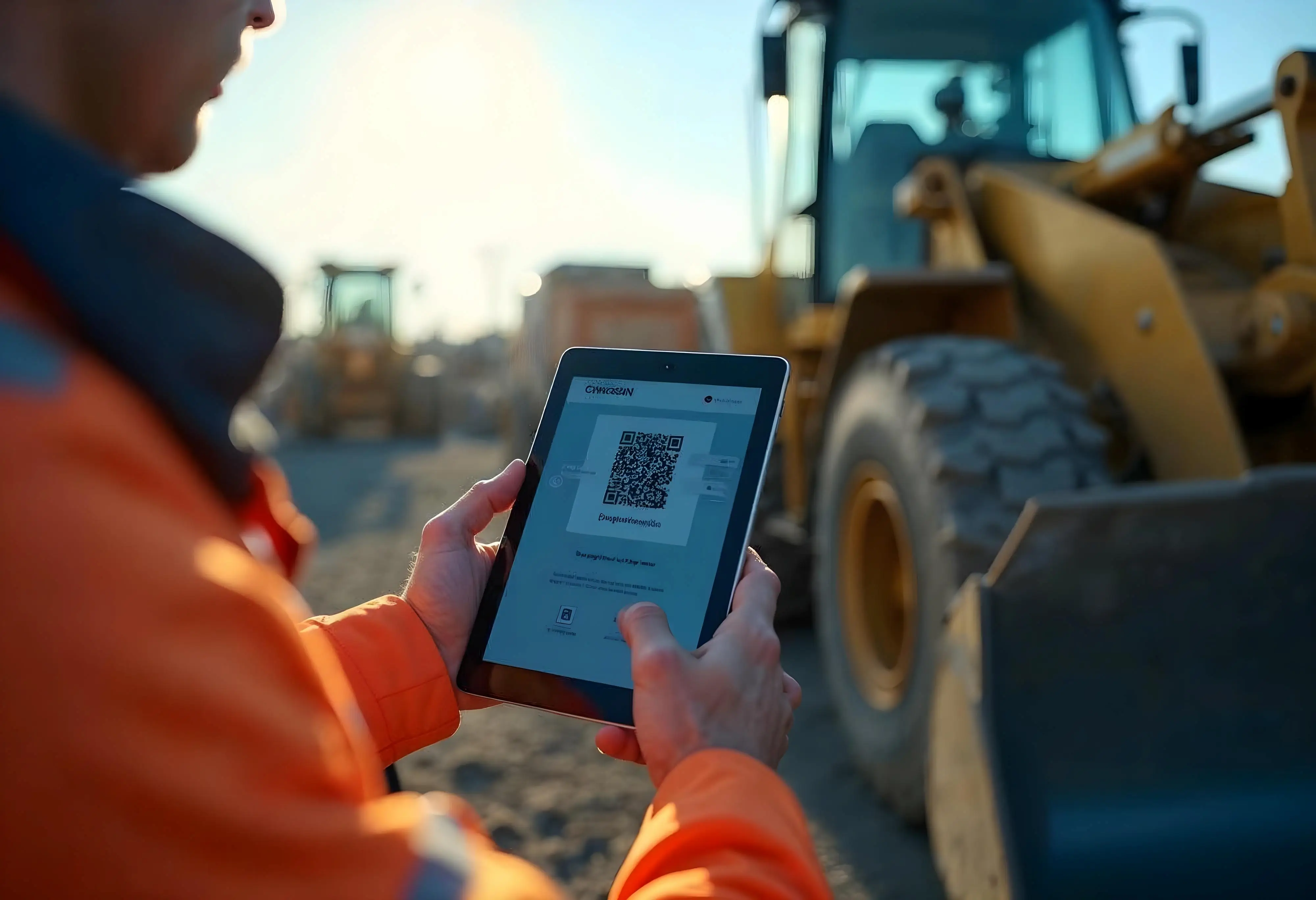
Your equipment tracking starts with a reliable check-in/check-out system. Using QR codes or RFID tags, you can create a clear trail of equipment movement and responsibility. This system provides:
- Accurate records of equipment location and user assignments
- Fast and easy tracking of items for preventive maintenance
- Enhanced accountability for equipment users and maintenance technicians
- Detailed maintenance and repair documentation
- Usage history for each piece of equipment, aiding in usage-based maintenance
Research indicates that implementing these procedures can reduce equipment downtime by up to 30% while lowering maintenance costs by 20%.
Location Tracking Systems
Modern location tracking combines GPS technology and IoT sensors to provide real-time visibility of your equipment fleet. Your tracking system should enable:
- Instant notifications when equipment moves off-site
- Geographic boundary setting with geofences for improved safety
- Real-time equipment status monitoring and condition-based maintenance alerts
- Automated location updates for efficient resource management
- Theft prevention alerts and compliance monitoring
Studies show that companies using equipment tracking software experience a 14% increase in equipment utilization and improved safety performance.
Usage Monitoring Protocols
Your usage monitoring system helps optimize equipment performance and maintenance scheduling. Implementation of condition-based monitoring (CBM) allows you to identify potential issues before they cause failures. Key monitoring elements include:
Engine Hours Tracking: Automatically log runtime hours for preventive maintenance scheduling and equipment life expectancy estimation.
Utilization Analysis: Compare idle time versus work time to optimize equipment deployment and resource management.
Maintenance Alerts: Set up automated notifications for required service based on usage patterns, enhancing your preventive maintenance program.
Performance Metrics: Track fuel levels, engine status, and other critical parameters in real-time for performance optimization and condition-based maintenance.
By implementing these protocols, you can reduce your annual operating budget spent on equipment maintenance, which typically ranges from 35-50% in the construction industry.
Need expert guidance on implementing effective tracking workflows for your equipment fleet? Contact MCH Parts for a free sourcing consultation and discover how to optimize your equipment management strategy and enhance your preventive maintenance program.
Training and Change Management
Successful implementation of your construction inventory management system depends heavily on proper staff training and change management. Studies show that companies implementing customized training programs see a 20% improvement in operational efficiency and enhanced safety performance.
Staff Training Programs
Your training program should combine different learning approaches for maximum effectiveness. Key components include:
- Group training sessions (60-minute maximum) on preventive maintenance strategies
- One-on-one coaching for specific roles, including maintenance technicians
- Hands-on practice with real equipment and maintenance planning software
- Regular refresher courses on safety protocols and compliance requirements
- Interactive demonstrations of condition monitoring techniques
- Documentation and reference materials for ongoing support
Research indicates that companies using comprehensive training software see up to 30% reduction in equipment-related errors and improved equipment uptime.
Role-based Responsibilities
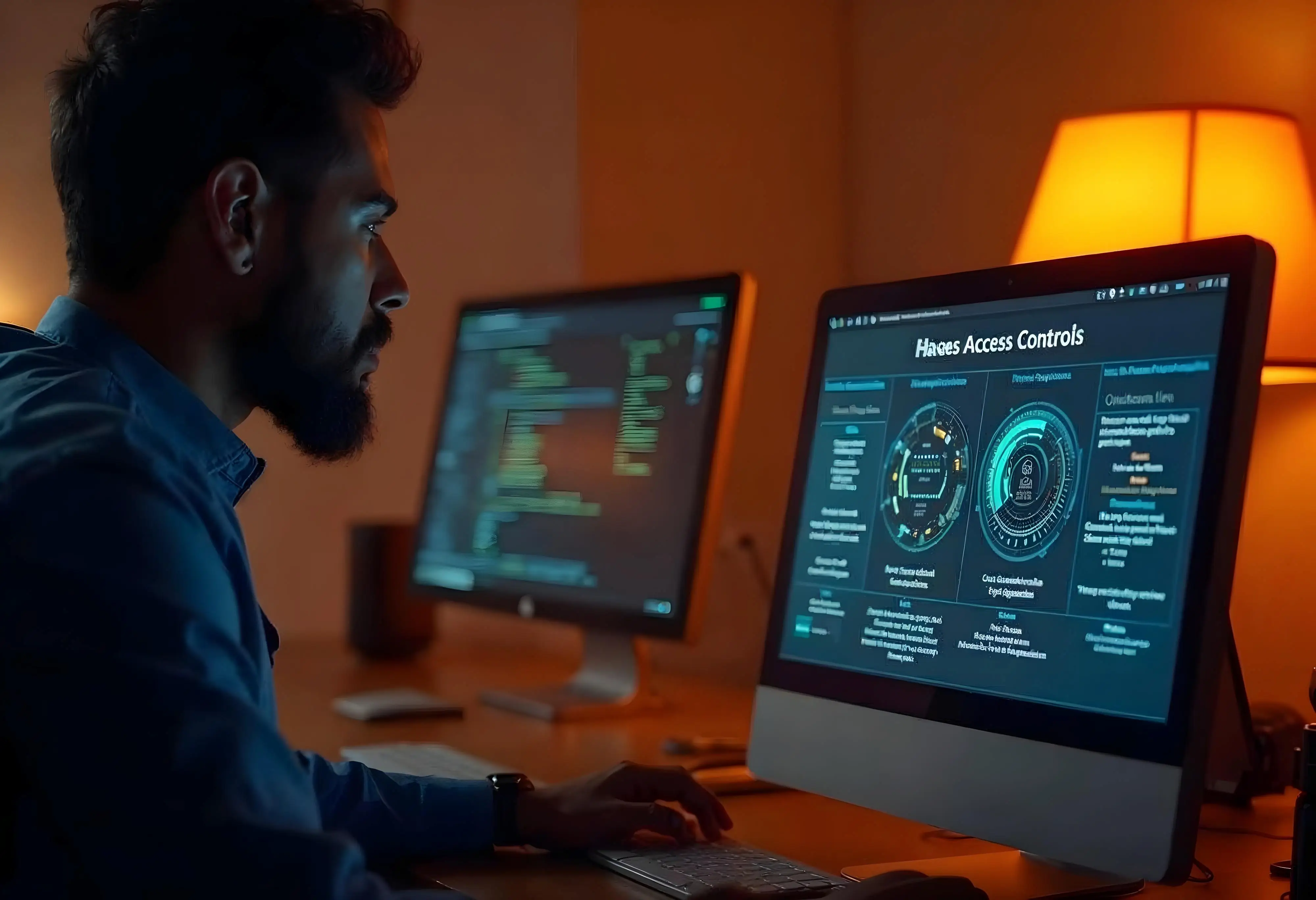
Your inventory management system requires clear role definition and accountability. Assign specific responsibilities based on job functions and expertise. For example, warehouse managers should focus on inventory oversight, while maintenance technicians need training in preventive maintenance procedures and equipment life span optimization.
Equipment Handlers: Train on proper verification, damage identification, and documentation procedures.
Supervisors: Focus on data analysis, reporting, and system optimization for improved resource management.
Field Teams: Emphasize mobile application usage, real-time updates, and safety compliance.
Maintenance Technicians: Provide specialized training on preventive maintenance, condition monitoring, and usage-based maintenance techniques.
Adoption Monitoring
Track your team's progress through specific metrics and regular assessments. Companies that implement structured adoption monitoring report 86.6% higher success rates in system implementation. Follow these implementation steps:
- Set clear performance benchmarks for equipment uptime and maintenance efficiency
- Monitor daily system usage patterns and adherence to preventive maintenance schedules
- Collect regular feedback from users, including maintenance technicians
- Identify areas needing additional support, such as advanced condition monitoring techniques
- Adjust training programs based on results and evolving maintenance strategies
Your adoption strategy should include regular check-ins and support sessions. Studies show that ongoing training support increases system adoption rates by 15%. Focus on addressing specific challenges your team encounters while using the new system and implementing preventive maintenance protocols.
Progress Tracking: Monitor individual and team performance metrics to identify areas needing additional support. Companies using detailed progress tracking report 20% faster system adoption rates and improved equipment reliability.
Continuous Improvement: Regular assessment of your training program helps identify gaps and opportunities for enhancement. Update your training materials based on user feedback, changing operational needs, and advancements in preventive maintenance techniques.
Need expert guidance on implementing an effective training program for your construction inventory management system? Contact MCH Parts for a free sourcing consultation and discover how to optimize your equipment management strategy and enhance your preventive maintenance program.
Optimizing System Performance
Your construction inventory management system's success depends on continuous optimization and refinement. Studies show that companies using data-driven equipment management can reduce maintenance costs by up to 20% while improving equipment availability by 15%.
Data Analysis and Reporting
Your system's reporting capabilities provide valuable insights for decision-making. Equipment data platforms help maximize productivity by tracking key metrics:
- Equipment utilization rates and uptime
- Preventive maintenance schedule adherence
- Cost per operating hour and overall equipment efficiency
- Downtime frequency and causes
- Resource allocation efficiency and equipment longevity
Studies indicate that implementing predictive maintenance through data analysis can reduce equipment downtime by up to 30%. Your reporting dashboard should provide real-time updates on equipment status, enabling quick responses to potential issues and optimizing your preventive maintenance program.
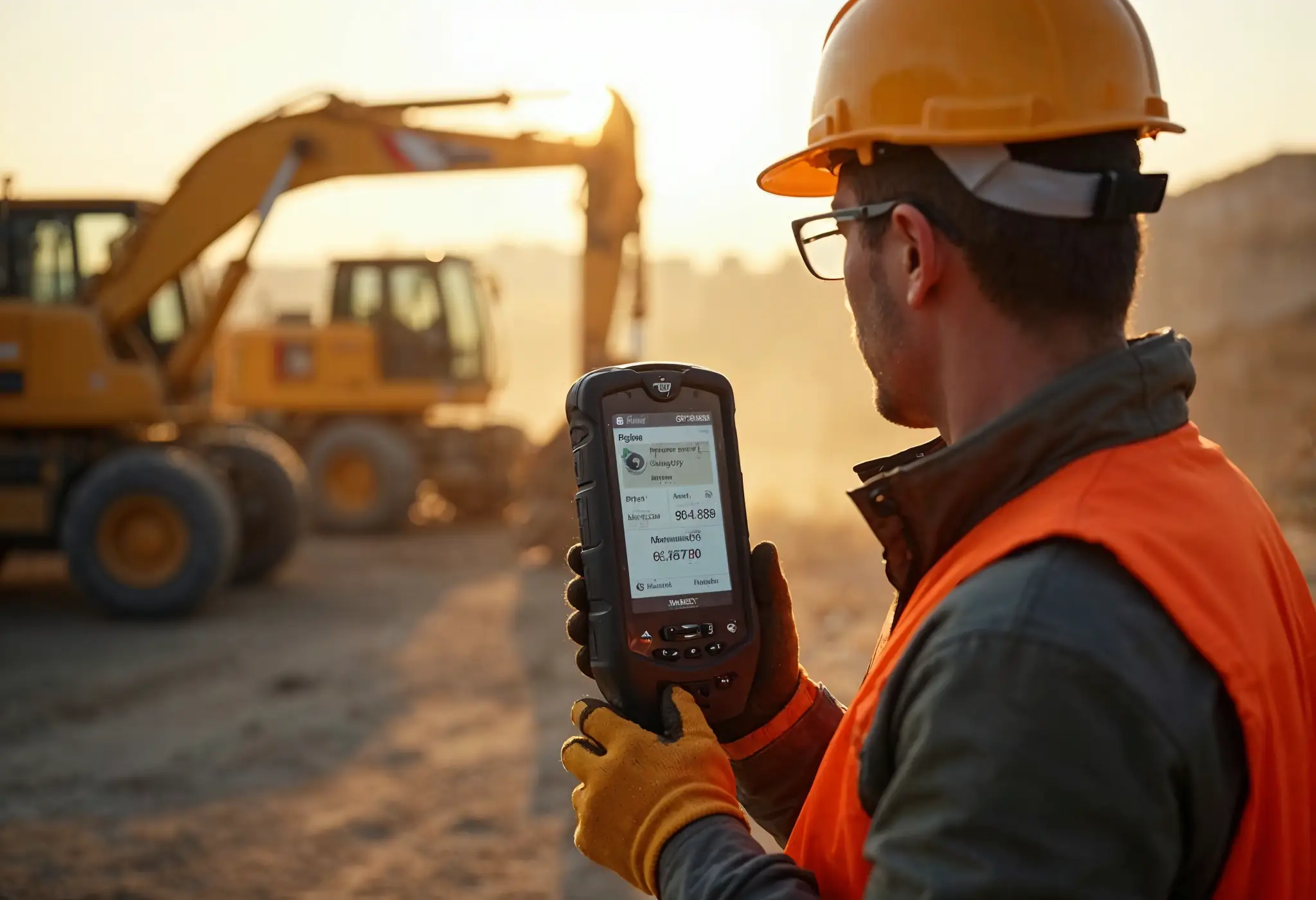
Process Refinement Strategies
Value-stream mapping helps identify areas for improvement in your equipment management workflow. This methodical approach tracks efficiency across your construction processes, including maintenance strategies. To optimize your system's performance, follow these key steps:
- Map current workflows and identify bottlenecks in maintenance procedures
- Analyze value-adding versus non-value-adding activities in your preventive maintenance program
- Implement targeted improvements, such as condition-based maintenance techniques
- Monitor results through data analytics and performance optimization metrics
- Adjust strategies based on performance metrics and equipment life expectancy data
Companies implementing systematic process refinement report up to 42% improvement in on-time equipment delivery and enhanced equipment reliability.
Continuous Improvement Methods
Your system benefits from ongoing refinement using proven methods like Plan-Do-Check-Act (PDCA) and the 5 Whys technique. The PDCA cycle helps improve construction methods and maintenance strategies by testing changes on a small scale before full implementation.
Performance Monitoring: Track your equipment's health through IoT sensors and real-time monitoring. Companies using comprehensive diagnostic tools achieve an average F1 score of 86.6% in activity recognition and fault detection, leading to more effective preventive maintenance.
Data-Driven Decisions: Use analytics to forecast equipment needs and arrange repairs before breakdowns occur. This proactive approach, including condition-based maintenance, has helped construction companies reduce purchasing time by 25% and extend equipment life span.
Resource Optimization: Regular analysis of equipment usage patterns helps identify underutilized assets and opportunities for better resource allocation. Studies show that hybrid unsupervised and supervised machine learning frameworks achieve significant improvements in equipment management efficiency and maintenance planning.
Your construction inventory management system should include automated scheduling and monitoring capabilities for preventive maintenance. By implementing these optimization strategies, you can reduce your annual operating budget spent on equipment maintenance, which typically ranges from 35-50% in the construction industry.
Need expert guidance on optimizing your construction inventory management system and enhancing your preventive maintenance program? Contact MCH Parts for a free sourcing consultation and discover how to improve your equipment management efficiency and extend equipment longevity.
Conclusion
Construction equipment management directly impacts your project success and bottom line. Through this comprehensive guide, you learned essential strategies to transform your equipment operations and reduce costs significantly through effective preventive maintenance and resource management.
Modern inventory management systems offer powerful solutions for your construction business:
- Real-time tracking cuts equipment losses by up to 30% and enhances safety
- Predictive maintenance reduces downtime by up to 30% and extends equipment life span
- Data-driven decisions lower maintenance costs by 20% and improve equipment reliability
- Structured training programs boost operational efficiency by 20% and enhance safety compliance
- Process refinement improves equipment delivery times by 42% and optimizes resource allocation
Your journey toward efficient equipment management starts with proper assessment, continues through strategic implementation of preventive maintenance, and succeeds through consistent optimization. Consider reaching out to MCH Parts for a free sourcing machinery or parts consultation, ensuring your business benefits from top-tier equipment and service.
Smart equipment management, including robust preventive maintenance strategies, creates a strong foundation for construction success. Armed with these insights and tools, you can build an efficient, cost-effective system that drives your projects forward while protecting your valuable equipment investments and ensuring optimal equipment longevity.
FAQs
Q1. What are the key benefits of implementing a construction inventory management system? A construction inventory management system can reduce equipment losses by up to 30%, lower maintenance costs by 20%, and improve equipment availability by 15%. It also enables real-time tracking, efficient preventive maintenance scheduling, and data-driven decision-making for enhanced equipment reliability and safety.
Q2. How can I assess my current equipment management needs? Start by conducting a detailed equipment audit, which includes physical verification of all equipment, reviewing maintenance records, analyzing usage patterns, and evaluating current tracking methods. This process helps identify gaps in your current system and creates a foundation for improvement, including opportunities to enhance your preventive maintenance program.
Q3. What technology infrastructure is needed for an effective inventory management system? Essential components include computers with up-to-date operating systems, barcode scanners or RFID readers, IoT sensors for condition monitoring, GPS tracking devices, and a stable internet connection. The software should integrate with existing systems, provide real-time analytics, and support mobile accessibility for maintenance technicians and field teams.
Q4. How can I ensure successful adoption of the new inventory management system? Implement a comprehensive training program that includes group sessions, one-on-one coaching, and hands-on practice with preventive maintenance software. Assign clear role-based responsibilities, including specific tasks for maintenance technicians. Monitor adoption through specific metrics and provide ongoing support to increase system adoption rates by 15%.
Q5. What strategies can I use to optimize the performance of my inventory management system? Continuously analyze data and generate reports to gain valuable insights for performance optimization. Implement process refinement strategies like value-stream mapping and use continuous improvement methods such as the Plan-Do-Check-Act cycle. Regularly monitor performance metrics, implement condition-based maintenance techniques, and make data-driven decisions to optimize resource allocation and equipment usage. Focus on preventive maintenance strategies to extend equipment life expectancy and reduce unplanned downtime.
Read More
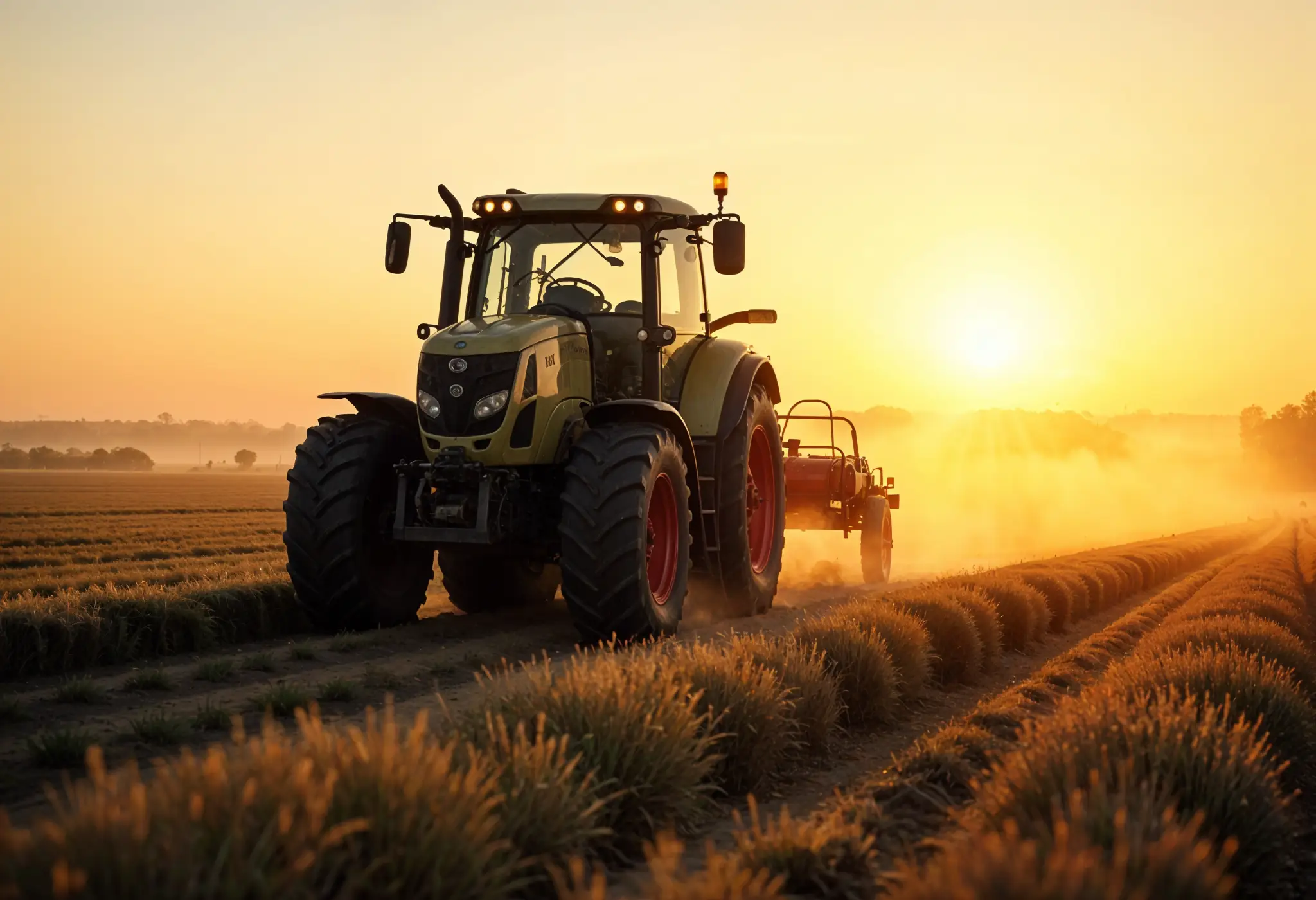
Top Hydraulic Components for Agricultural Equipment in 2025: Complete Guide
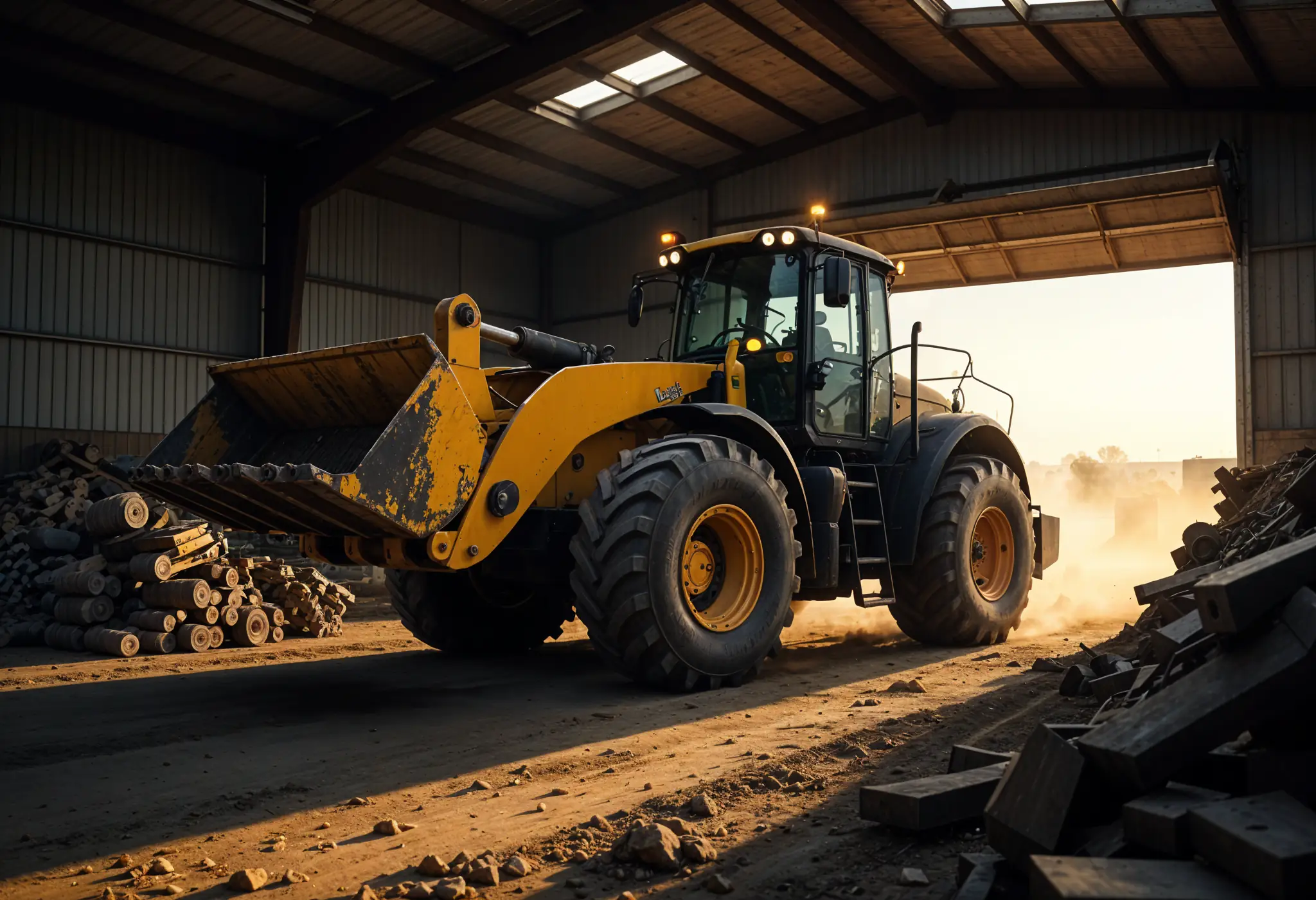
The Essential Farm Equipment Parts You Can't Afford to Run Out Of
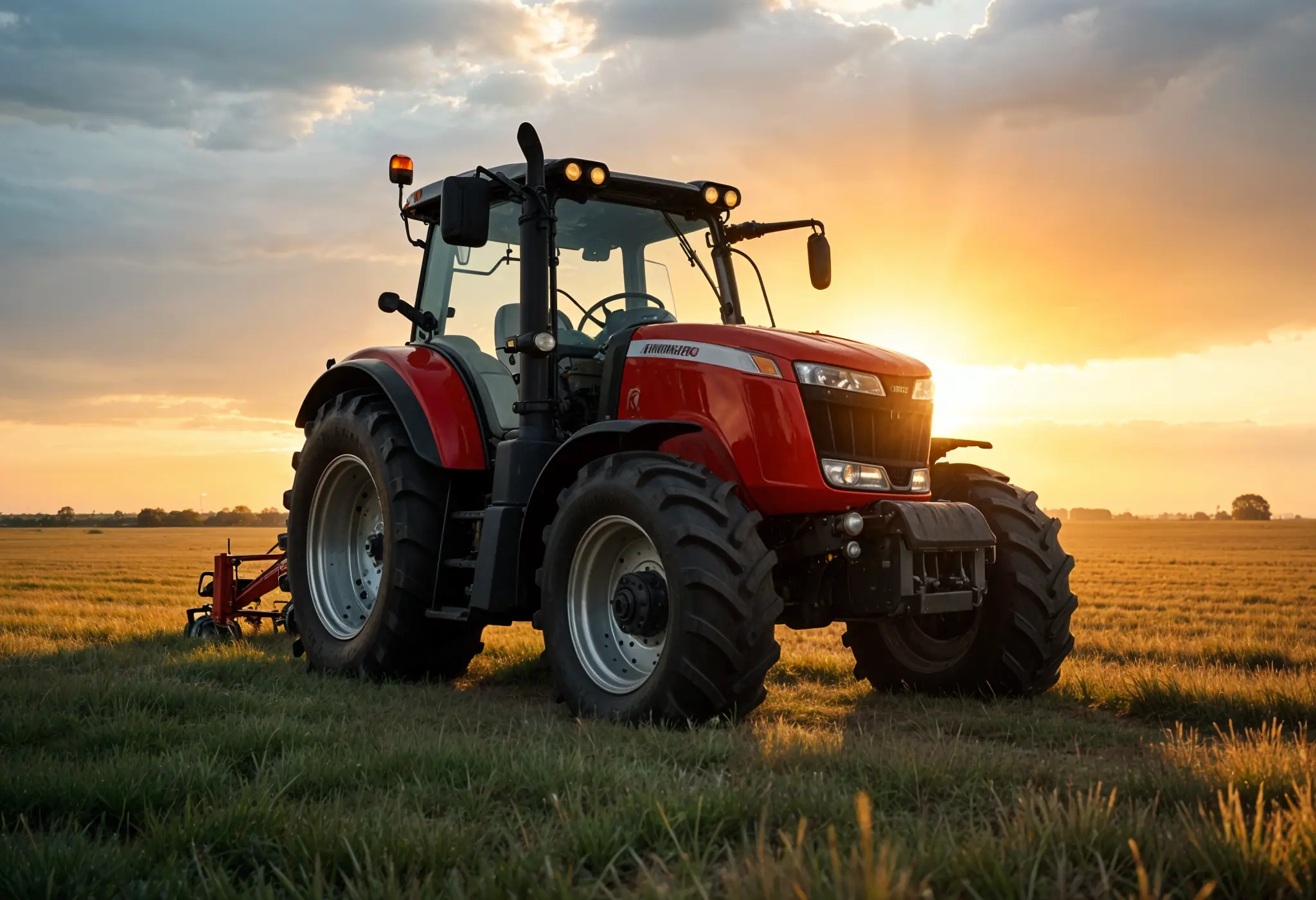
How to Service Farm Equipment: A Farmer's Guide to Zero Harvest Downtime
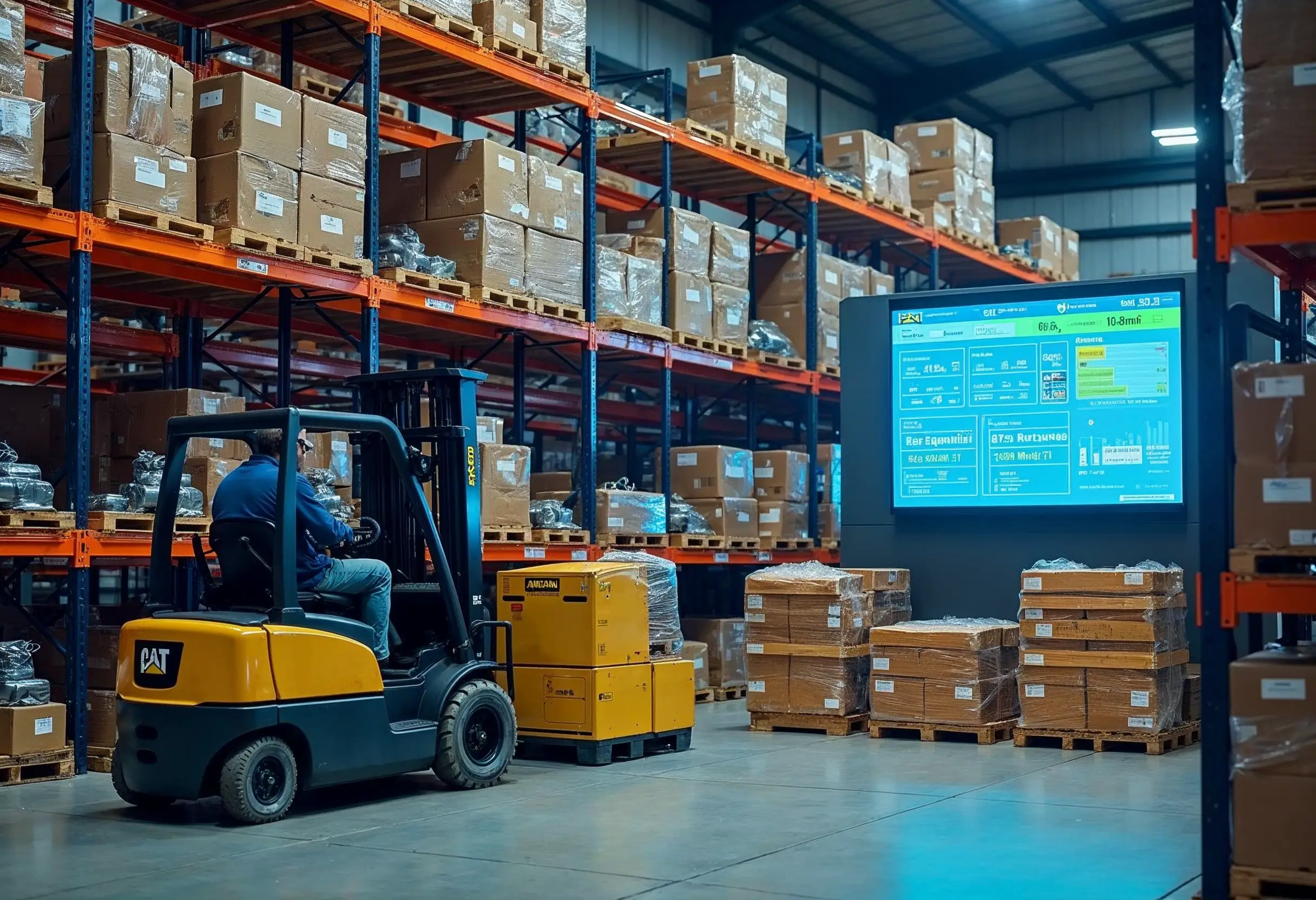
Construction Machinery Parts Suppliers: Expert Selection Guide
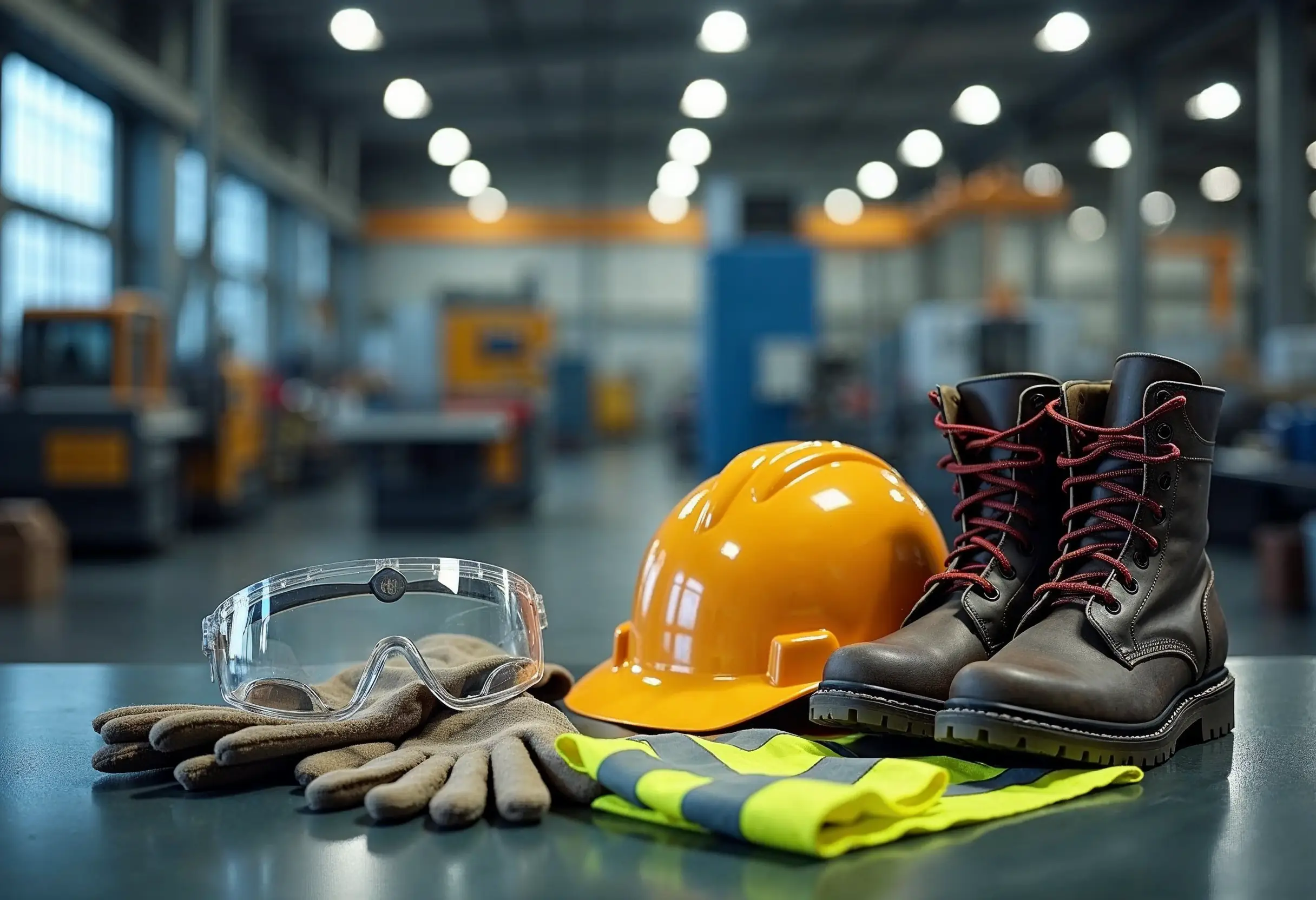
How to Apply Machine Safety Rules: From Selection to Installation
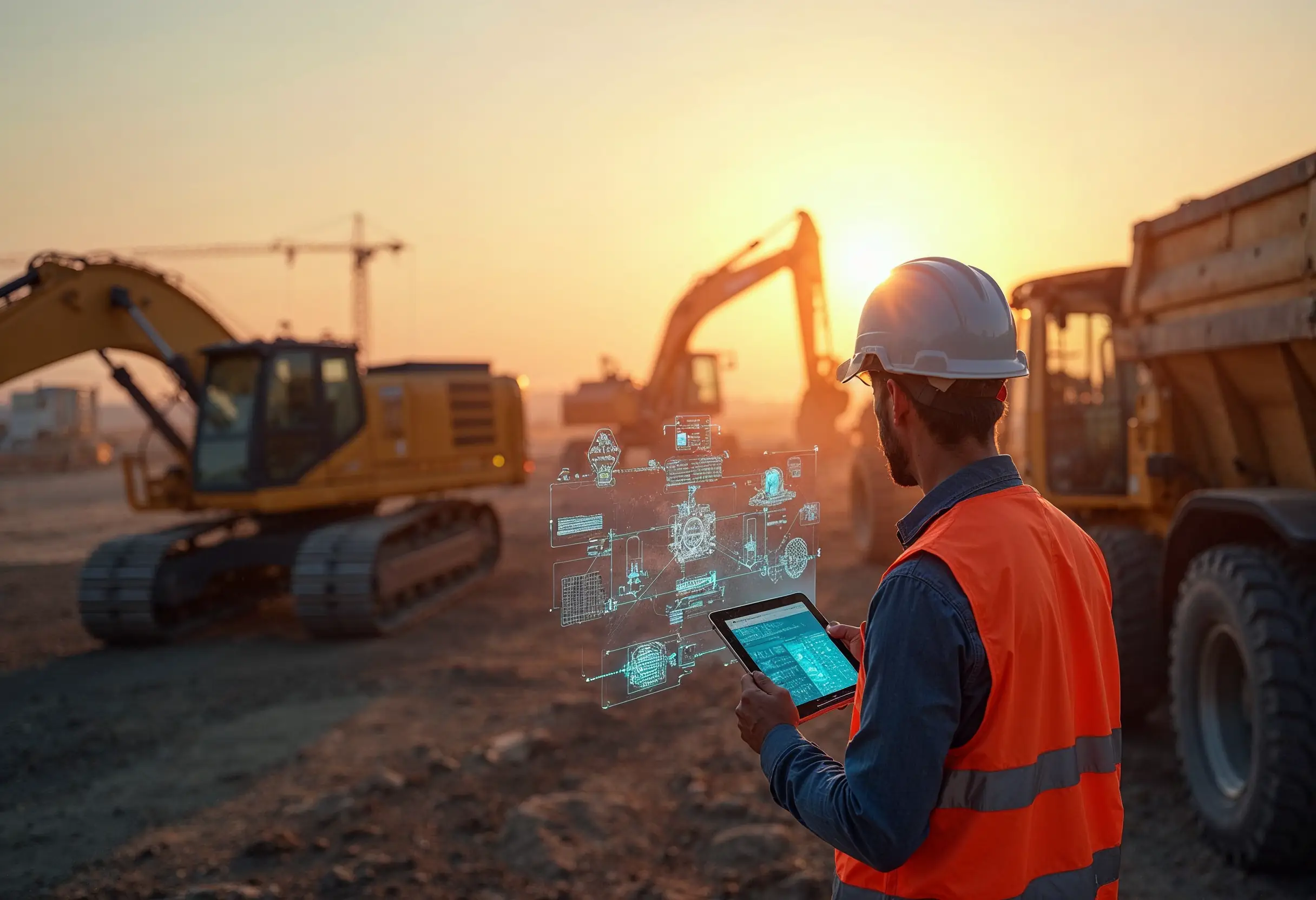
Smart Diagnostics Cut Heavy Equipment Failures by 73%
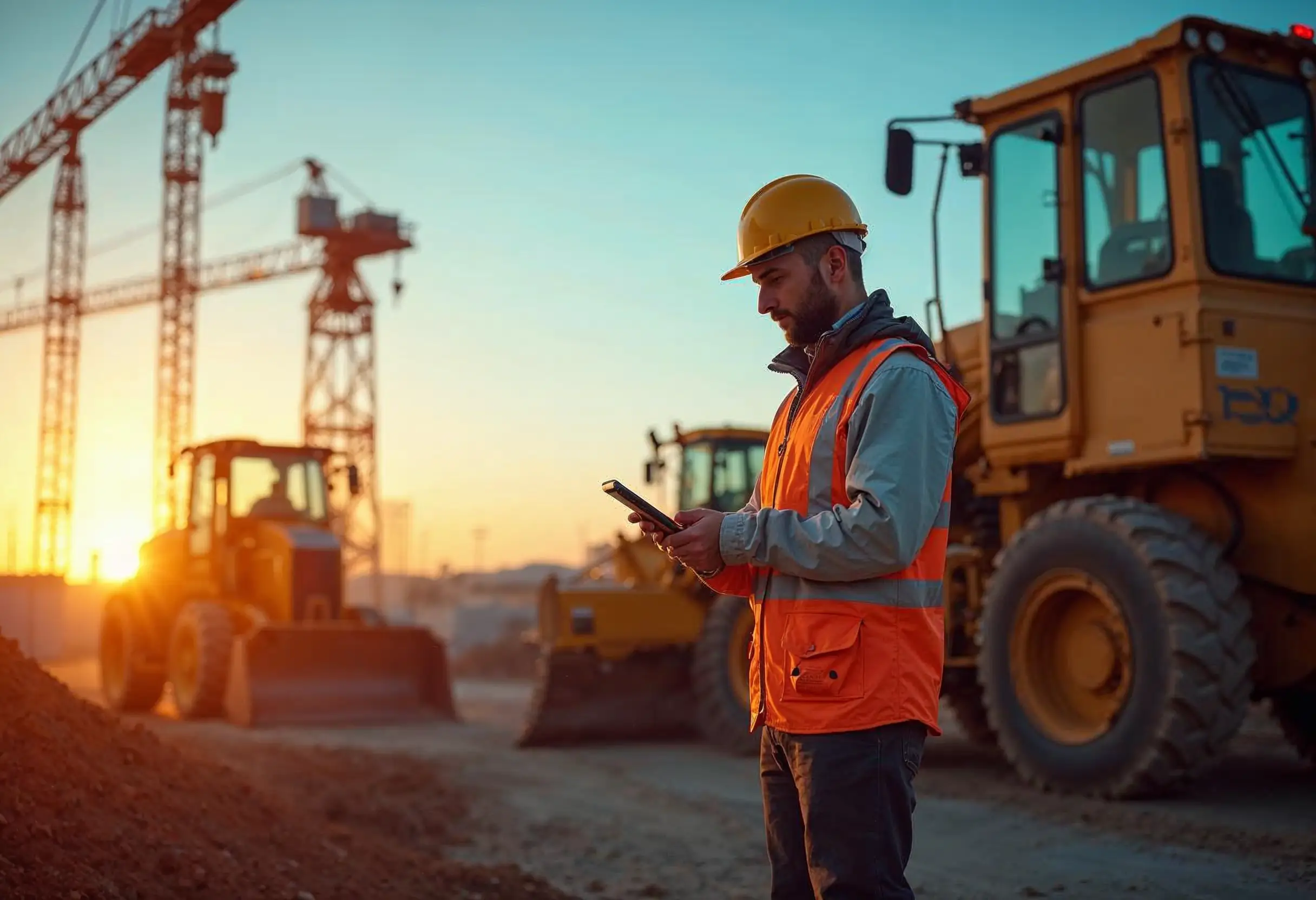
5 Ways to Assess the Environmental Impact of Heavy Construction Machinery
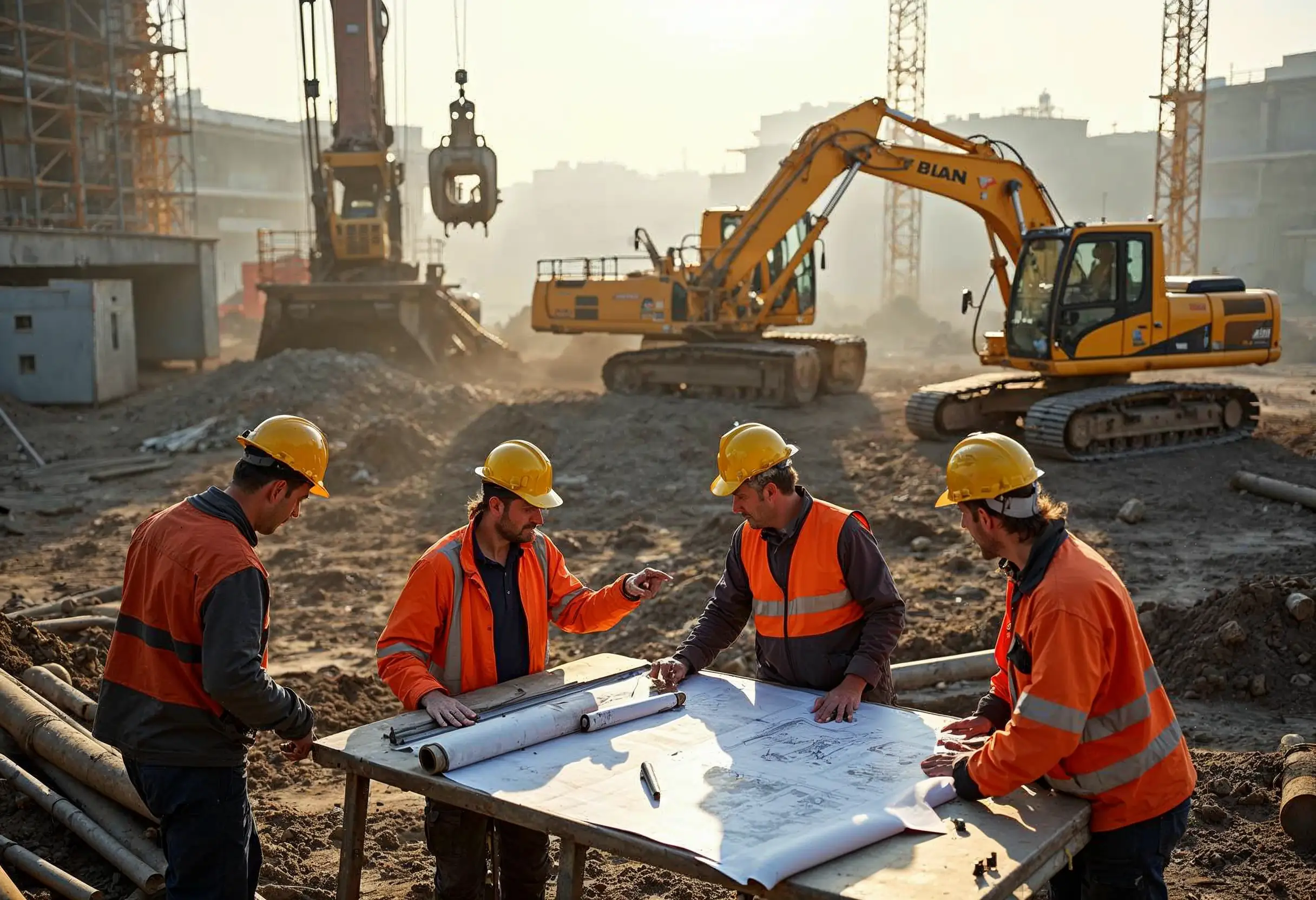
10 Smart Ways to Pick Construction Machinery for 2025 Projects
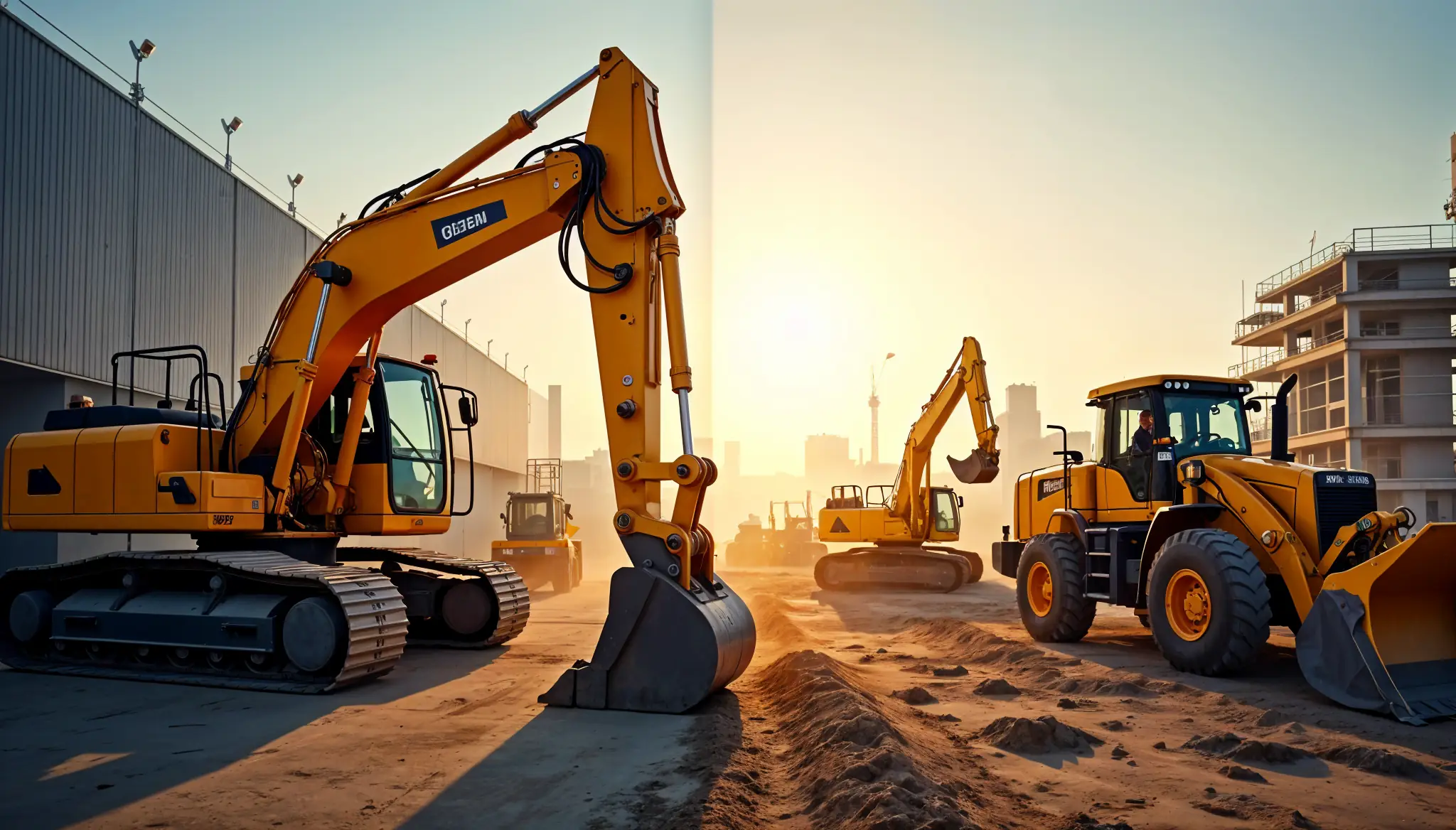
Rent vs Purchase Equipment: What Heavy Industry Experts Hide
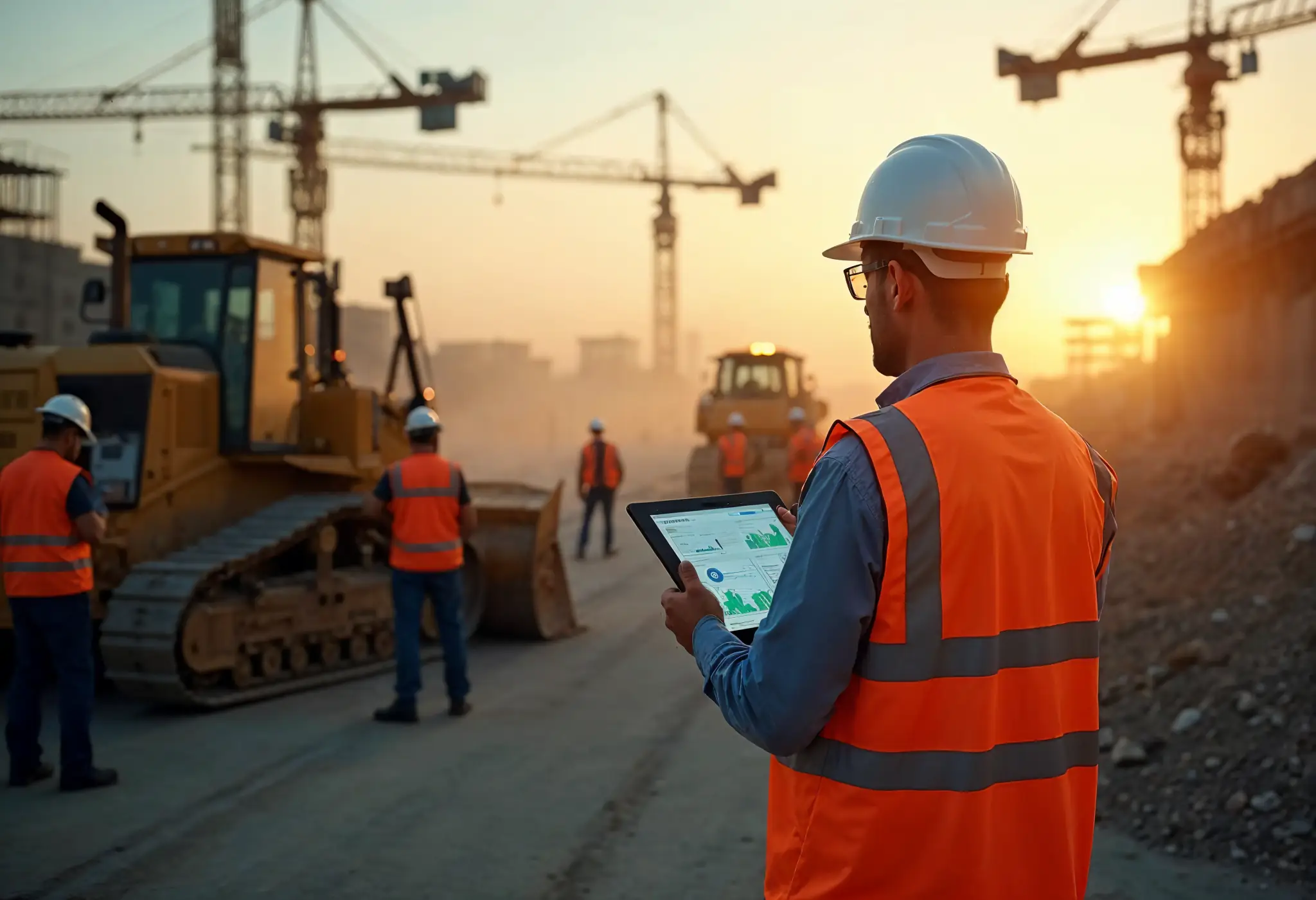
How to Implement a Construction Inventory Management System for Equipment Efficiency
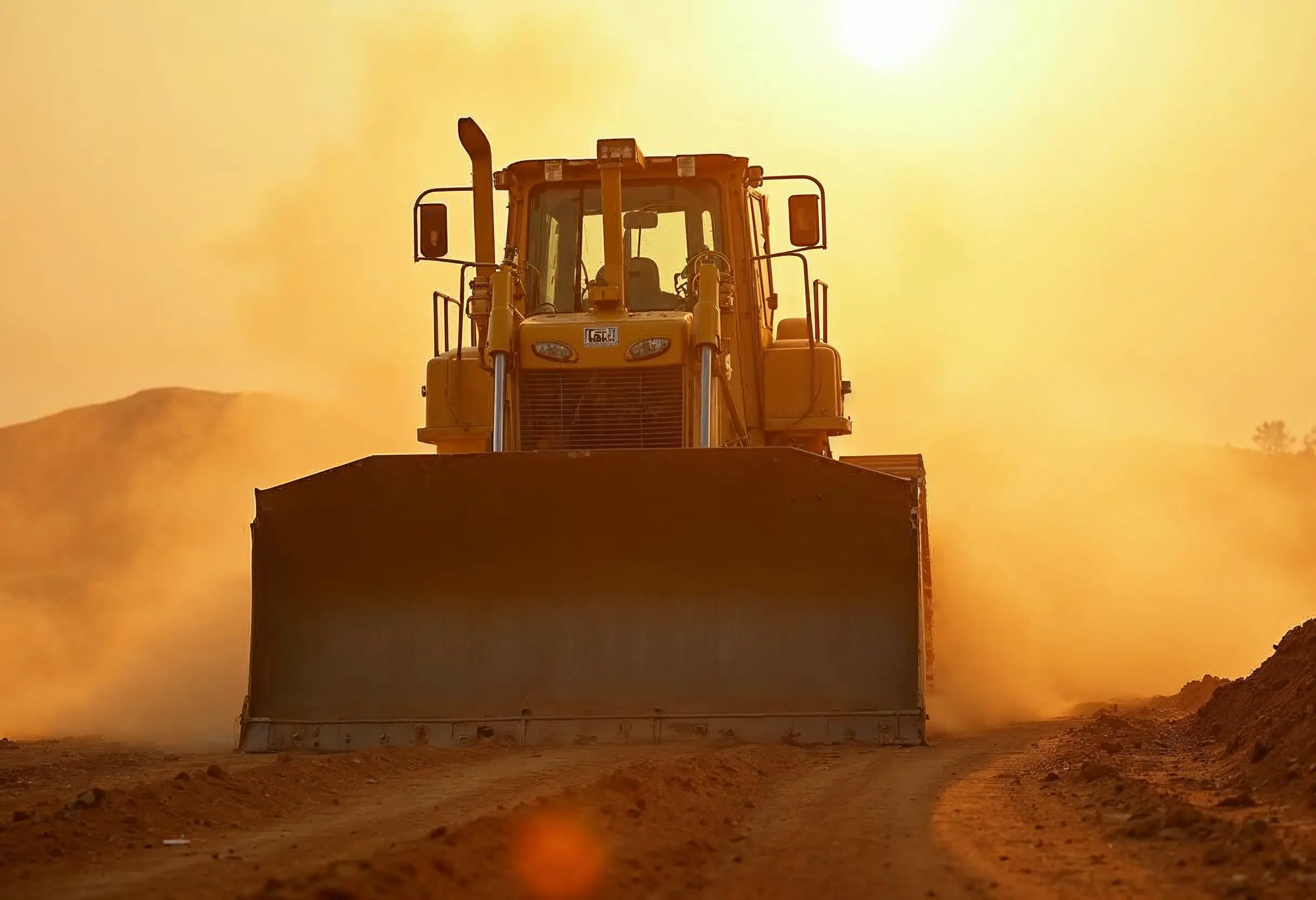
How to Extend Equipment Life Expectancy with Regular Maintenance
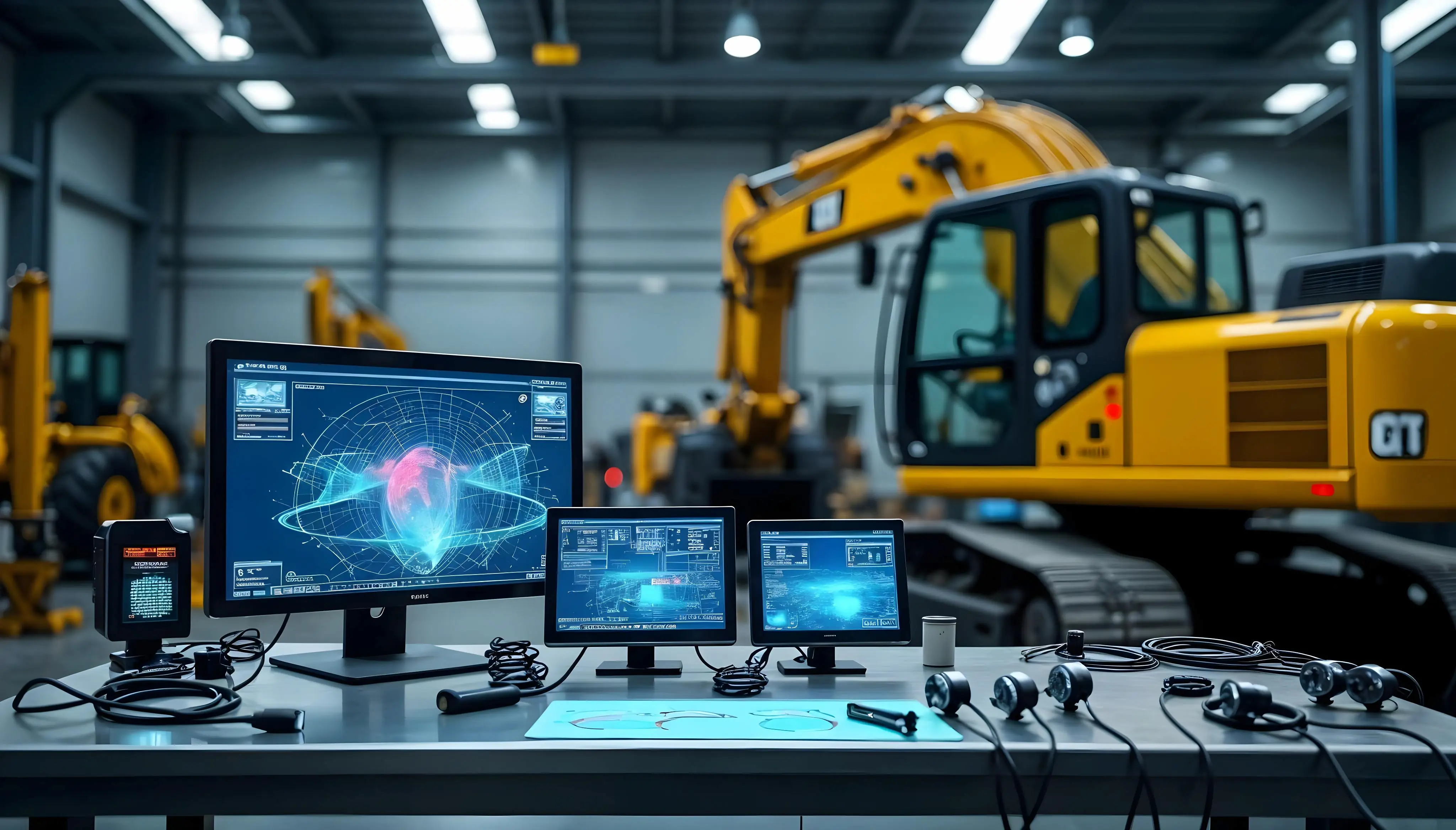
Advanced Heavy Equipment Diagnostic Tools: Ensuring Construction Machinery Quality
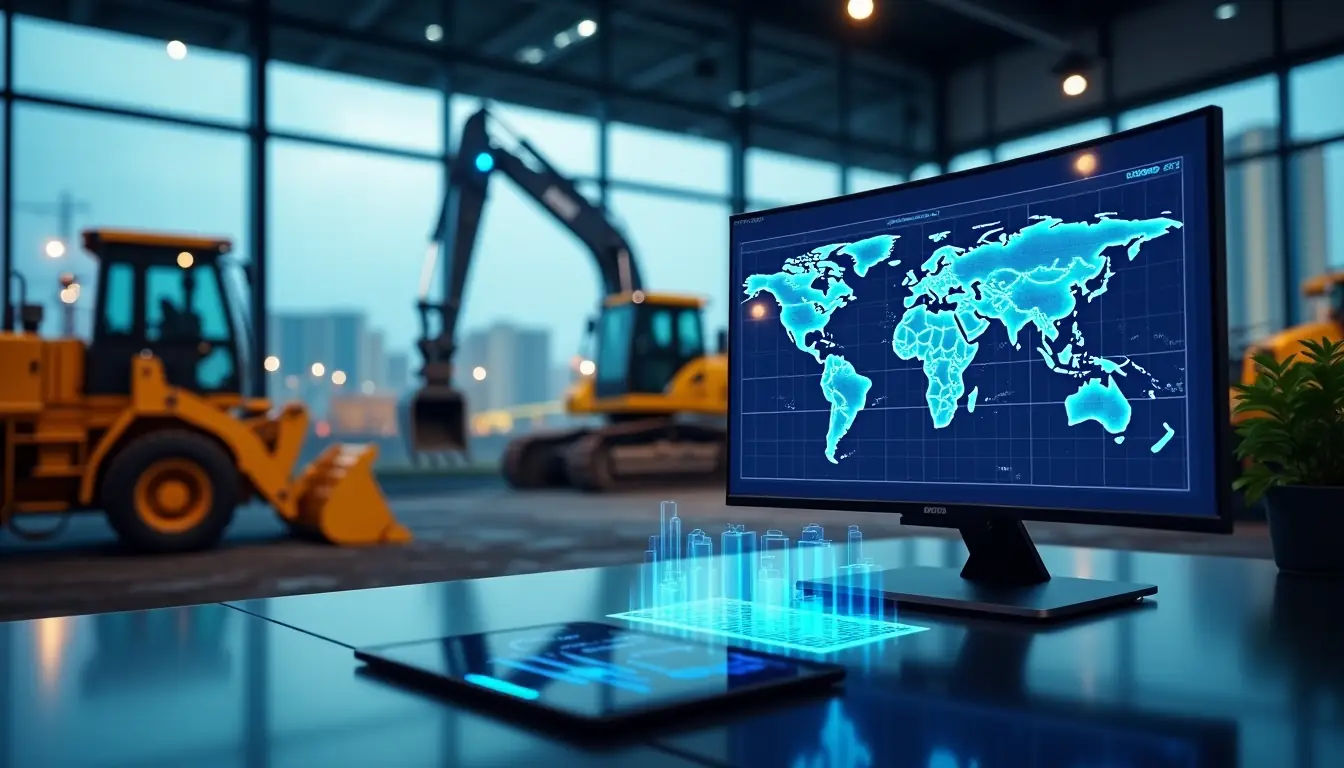
Essential Features Your Construction Equipment Inventory System Needs
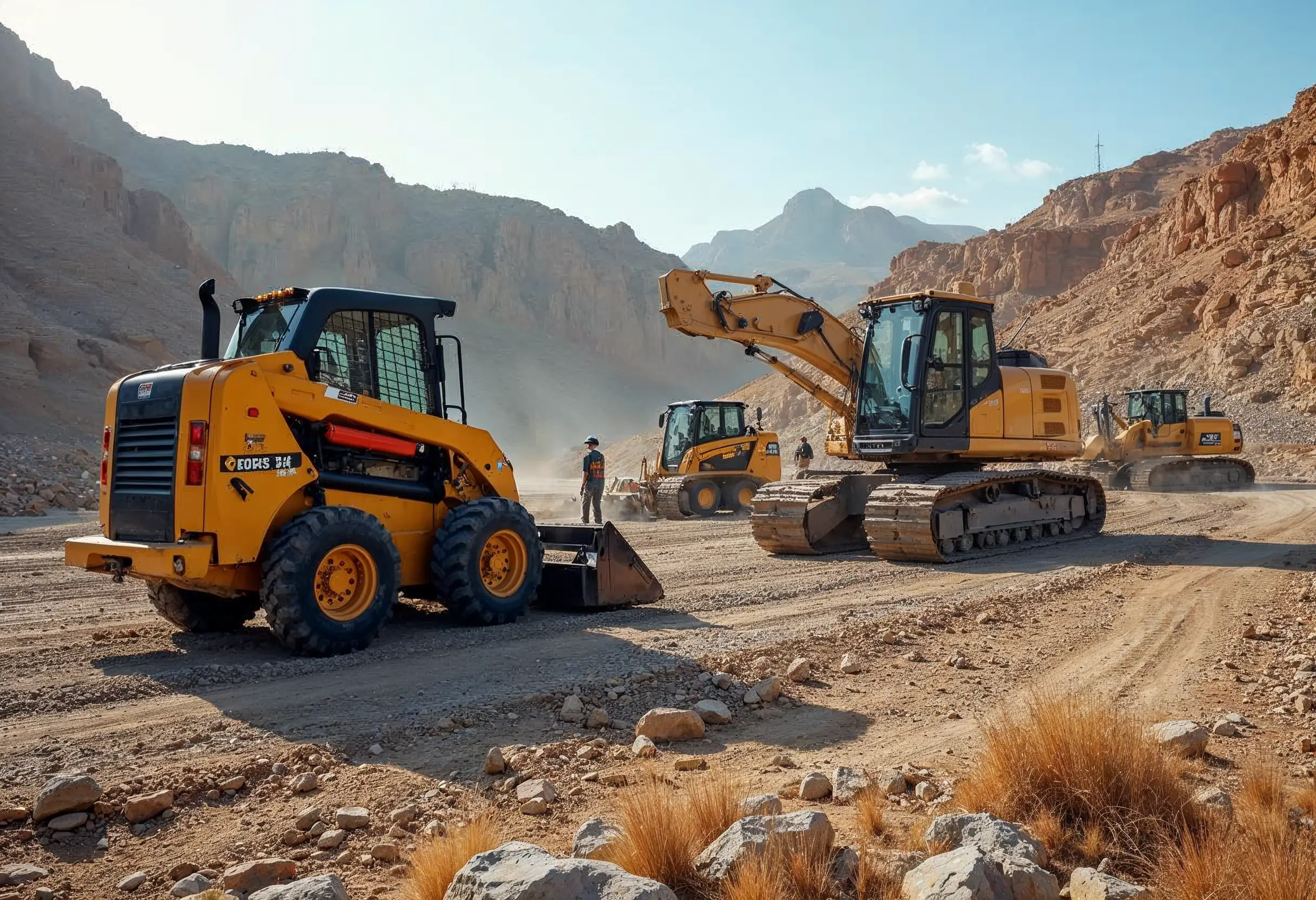
29 Quick Tips for Choosing Construction Equipment for Remote Locations
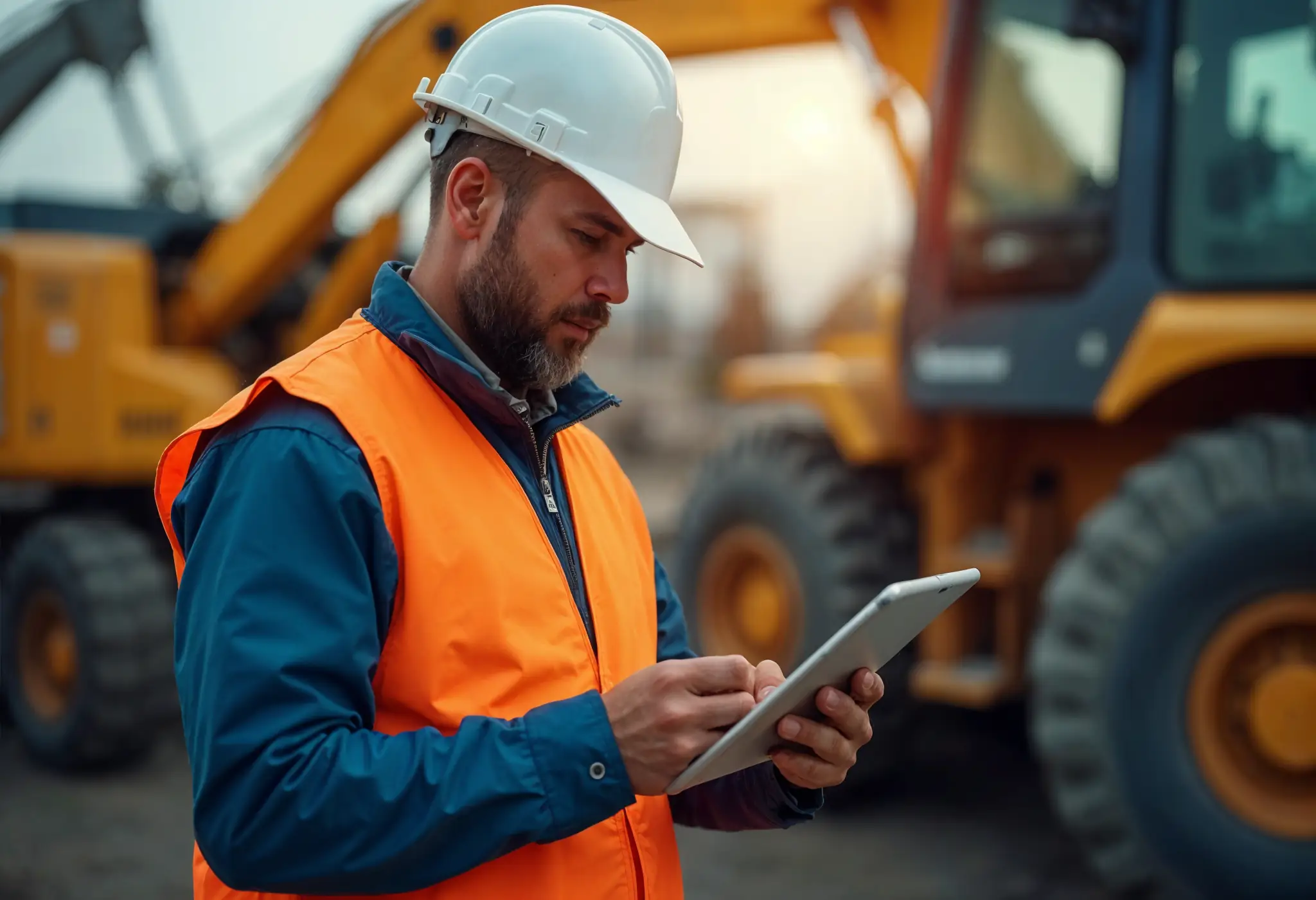
How to Select Construction Machinery with Optimal Equipment Maintenance in Mind
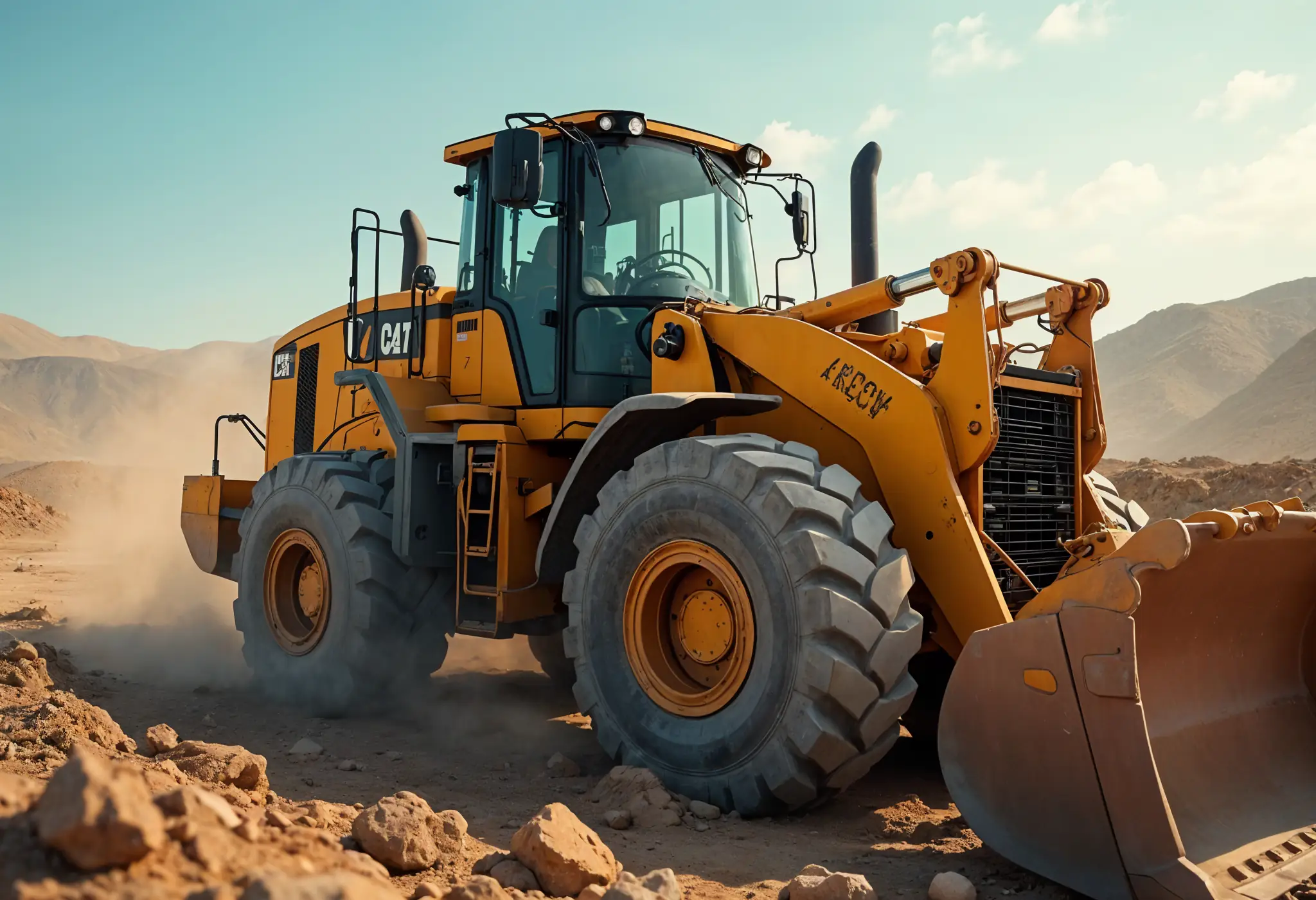
Top 25 Tips for Selecting Bulldozers for Construction Sites
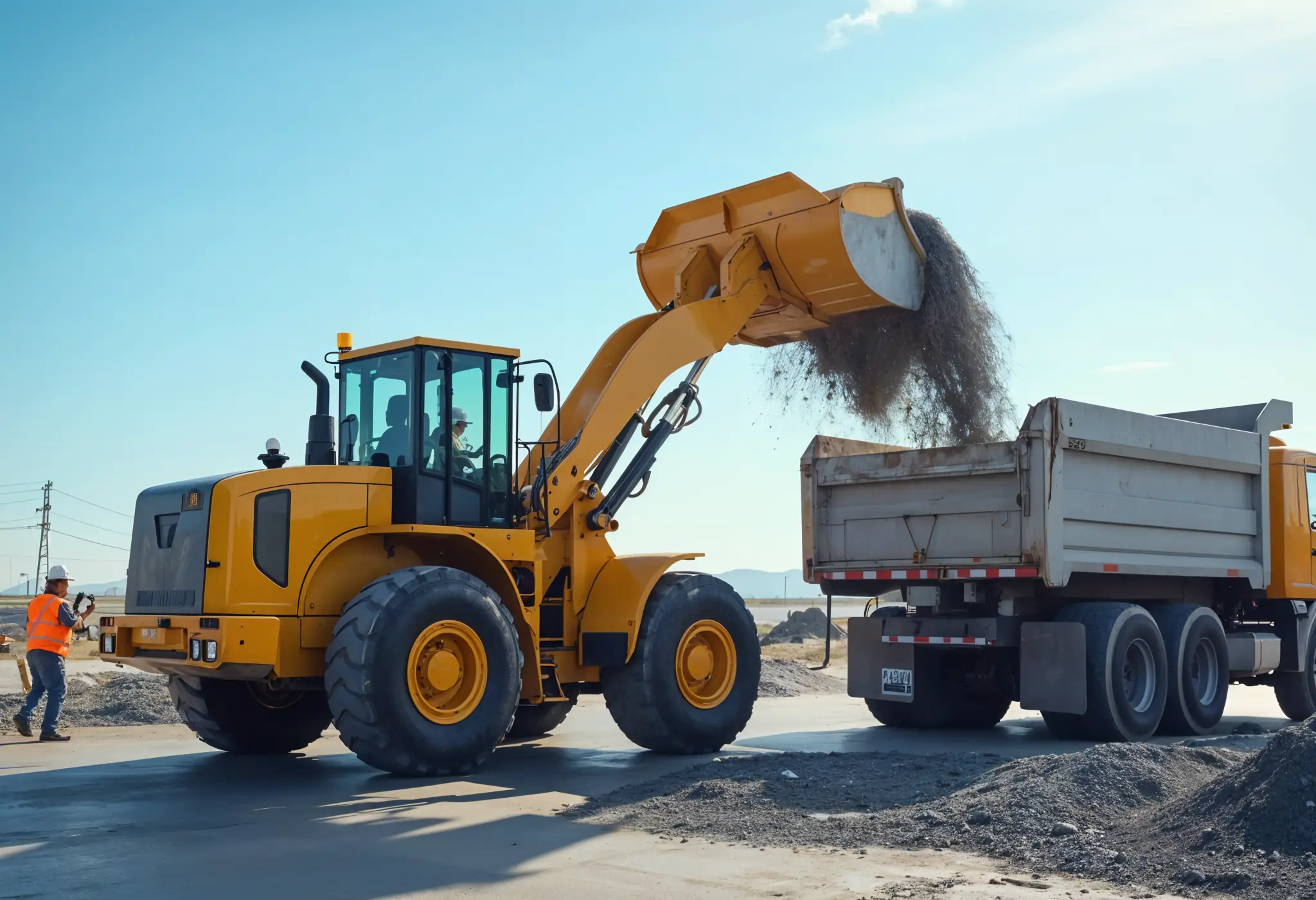
Which Construction Loader is Best for Your Project Needs?
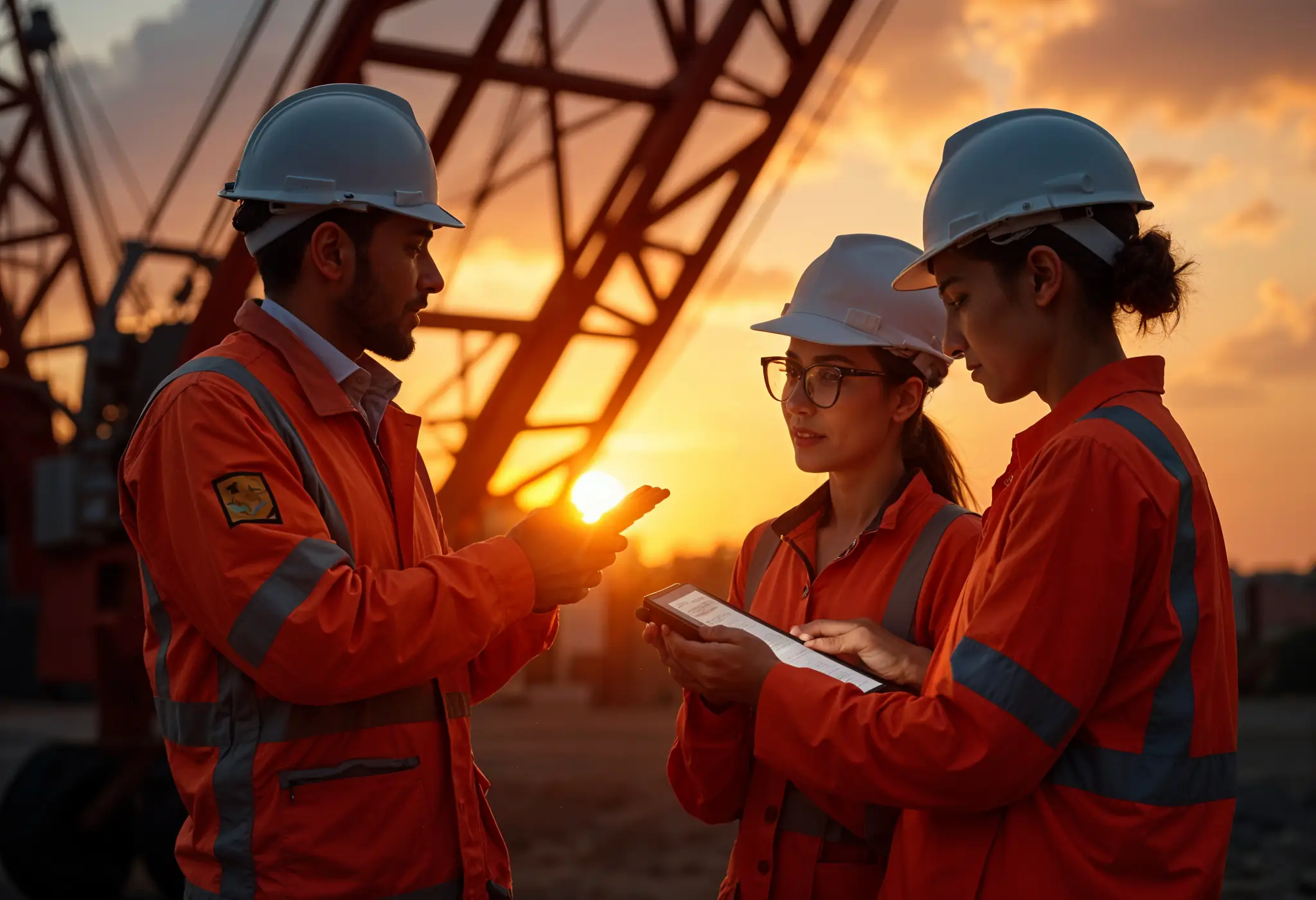
4 Key Steps to Form a Construction Machinery QC Team
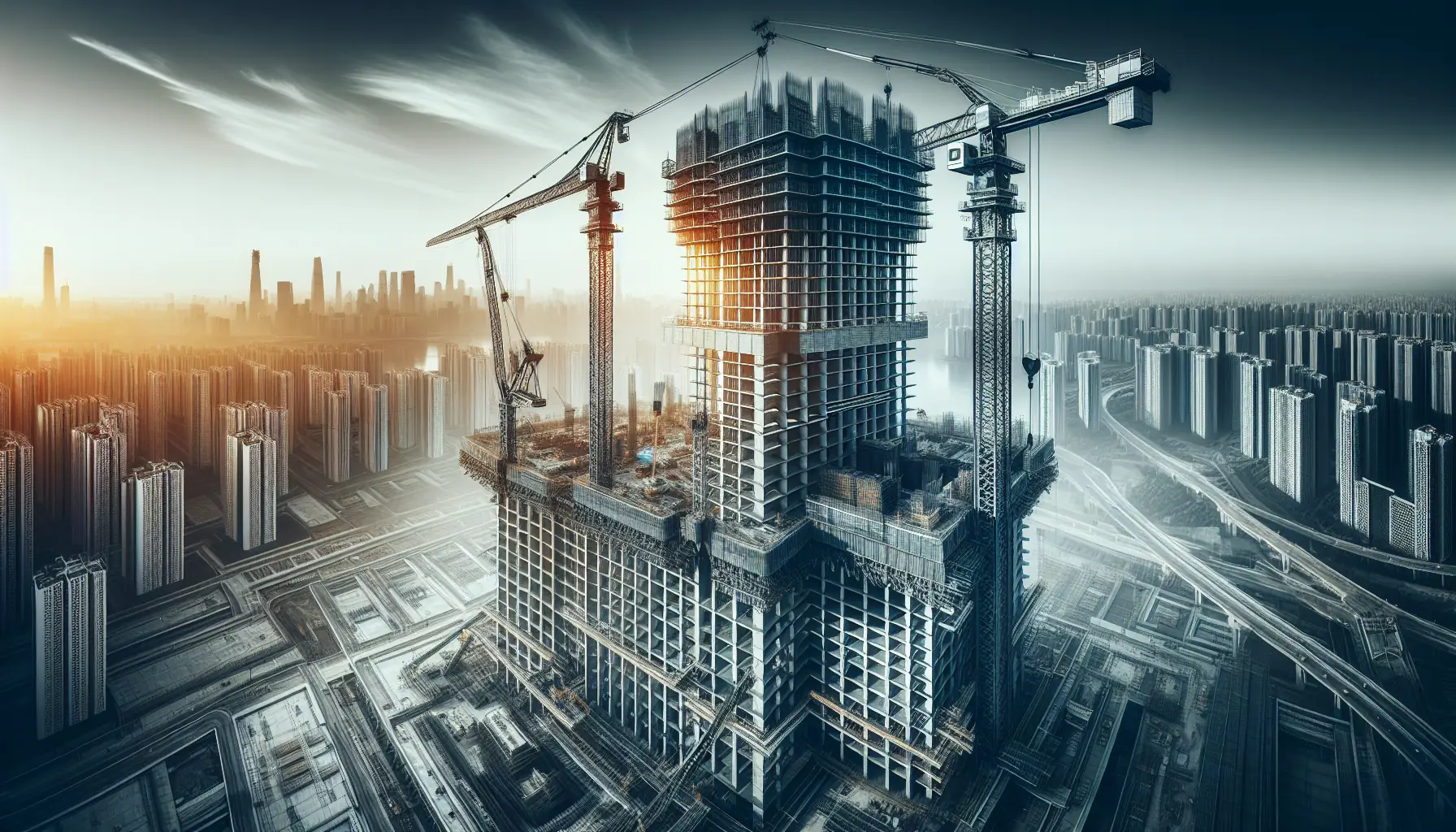
15 Essential Tips for Selecting the Perfect Crane for Construction
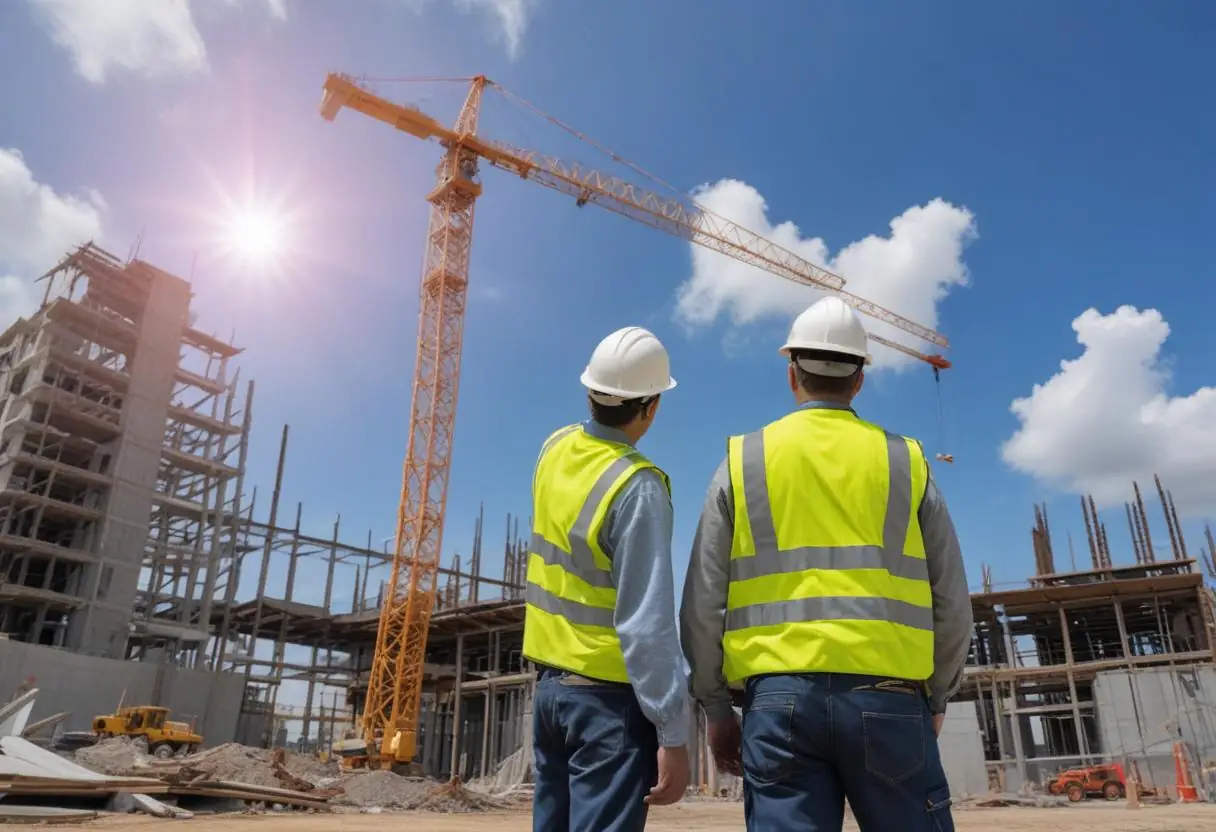
Maximize Savings: Multi-Purpose Construction Machinery for Lower Costs
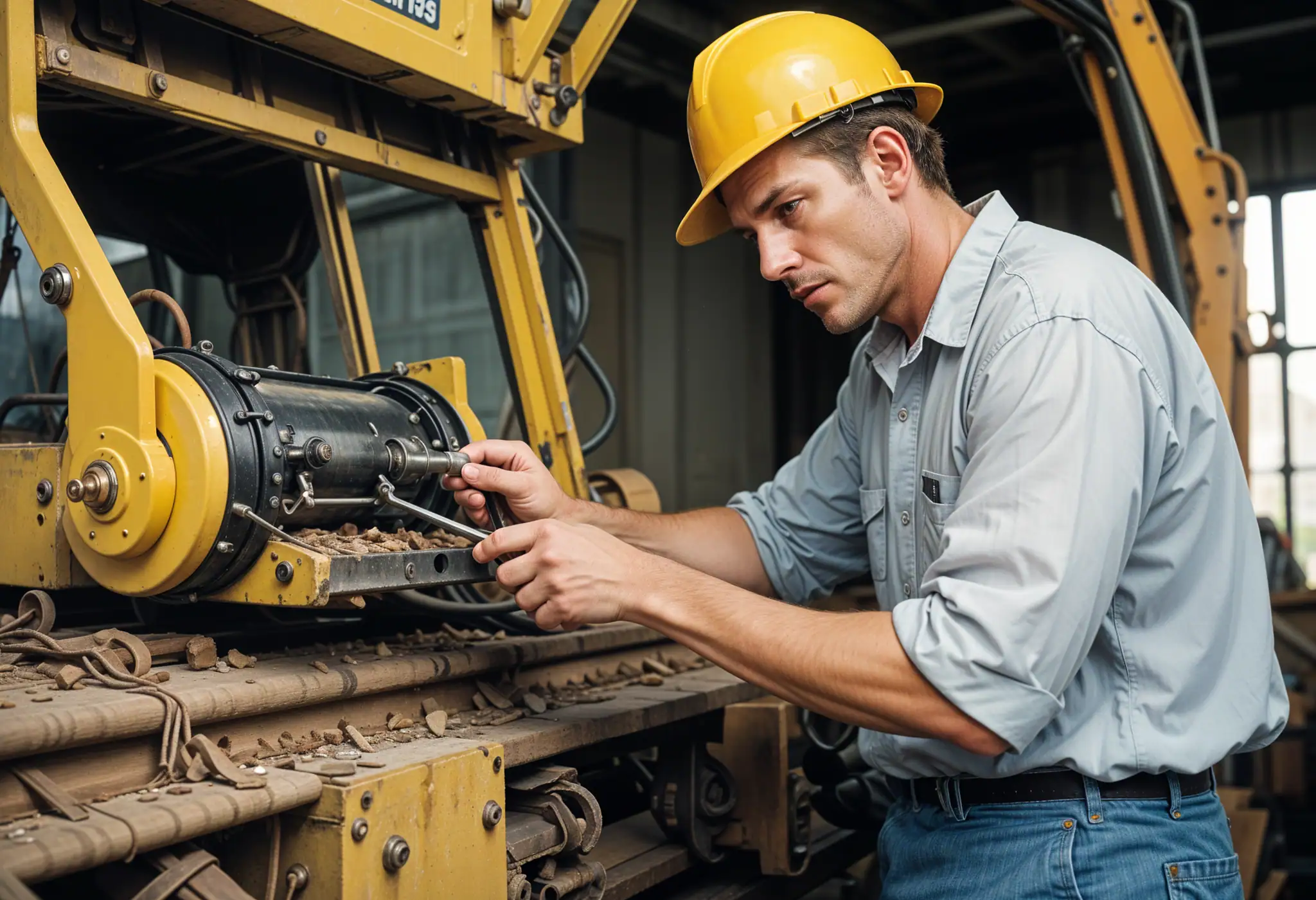
Affordable Heavy Equipment Parts: A Sourcing Guide
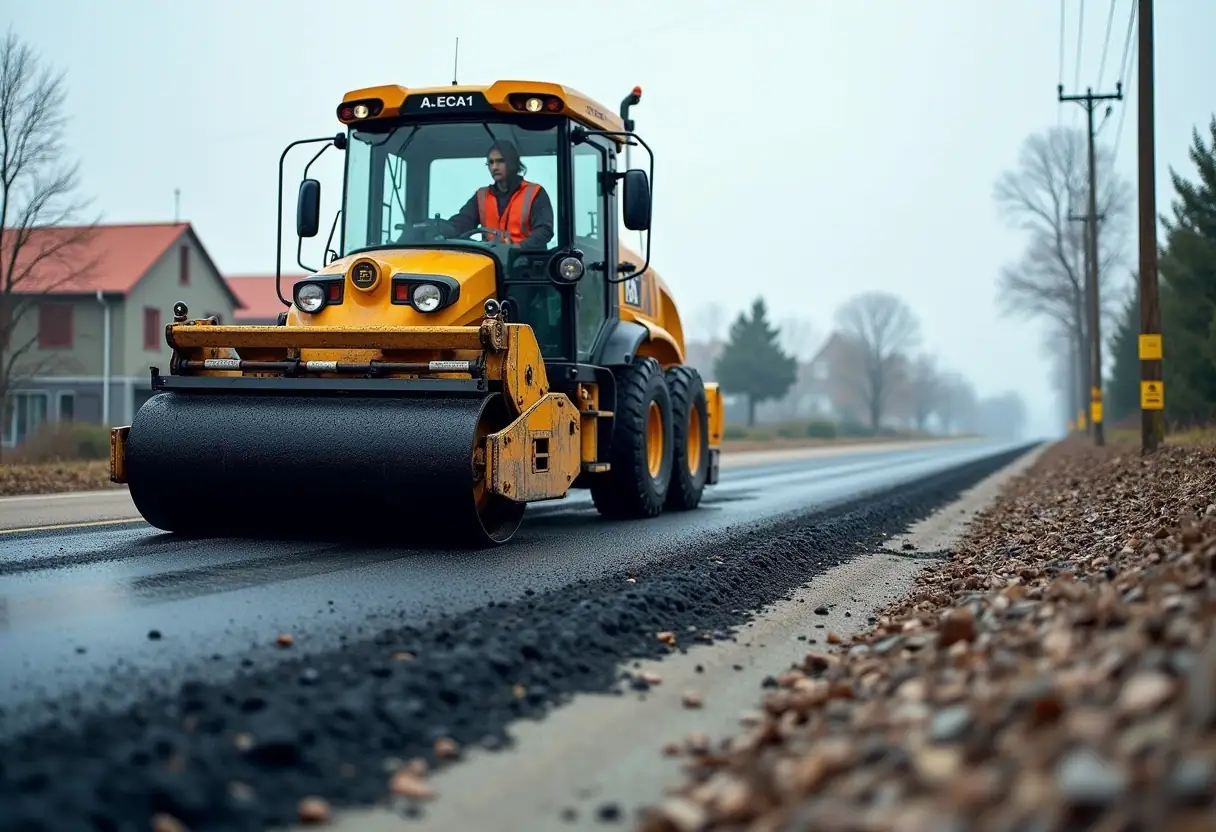
Choosing the Right Road Construction Equipment: A Complete Guide
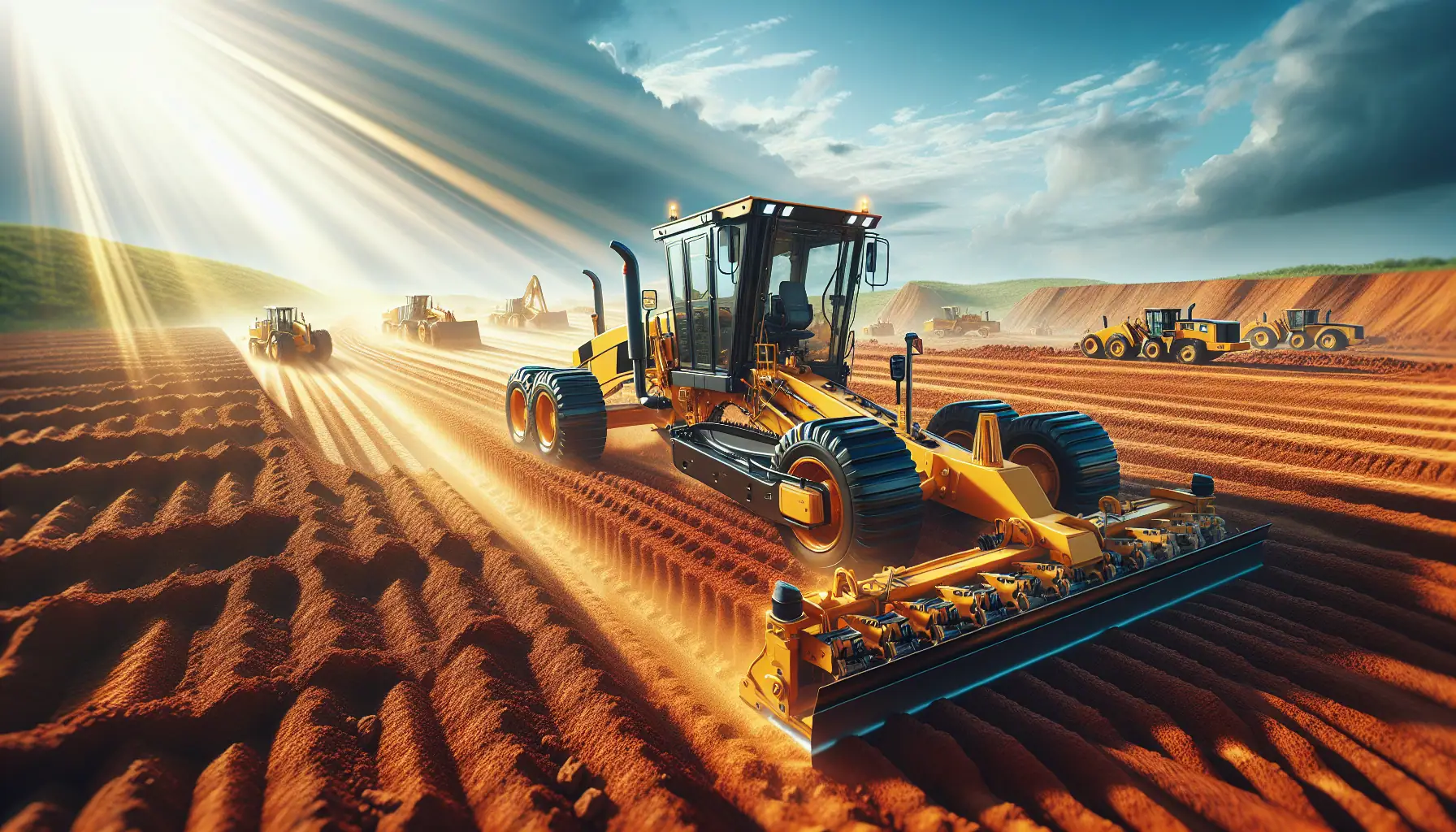
Motor Graders: Key Elements to Consider for Optimal Selection
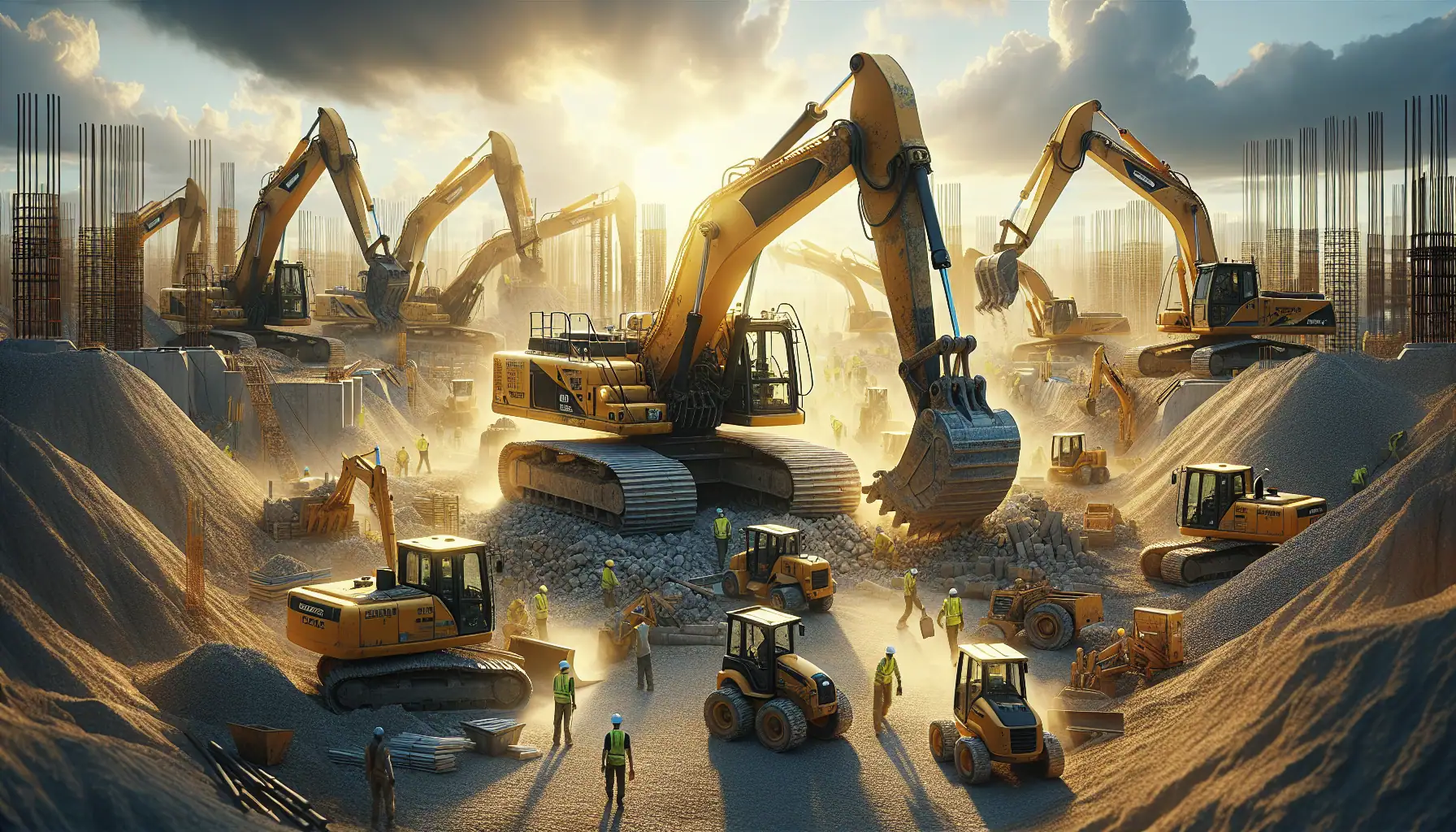
A Detailed Guide to Choosing Excavators for Construction Work
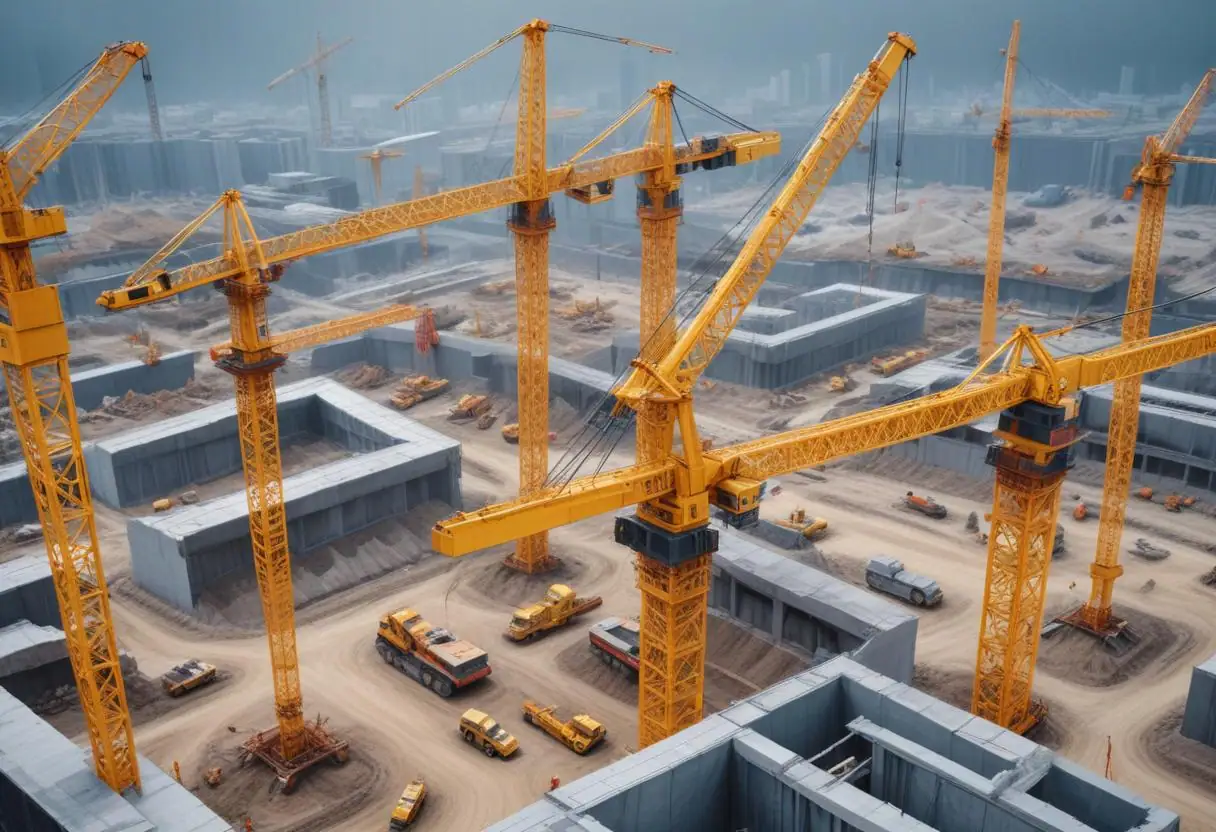
Top Tips for Choosing Cranes for Construction Projects
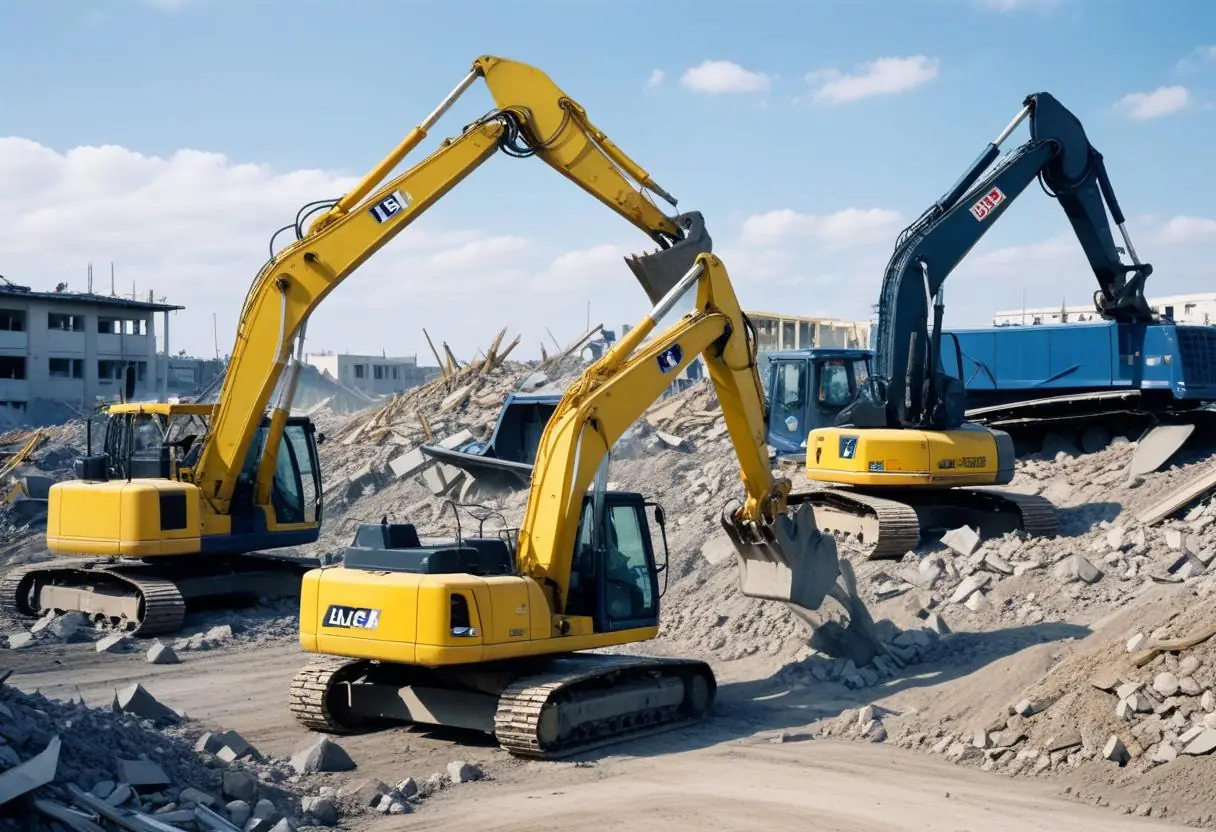
5 Top-Rated Demolition Machines for Construction Professionals
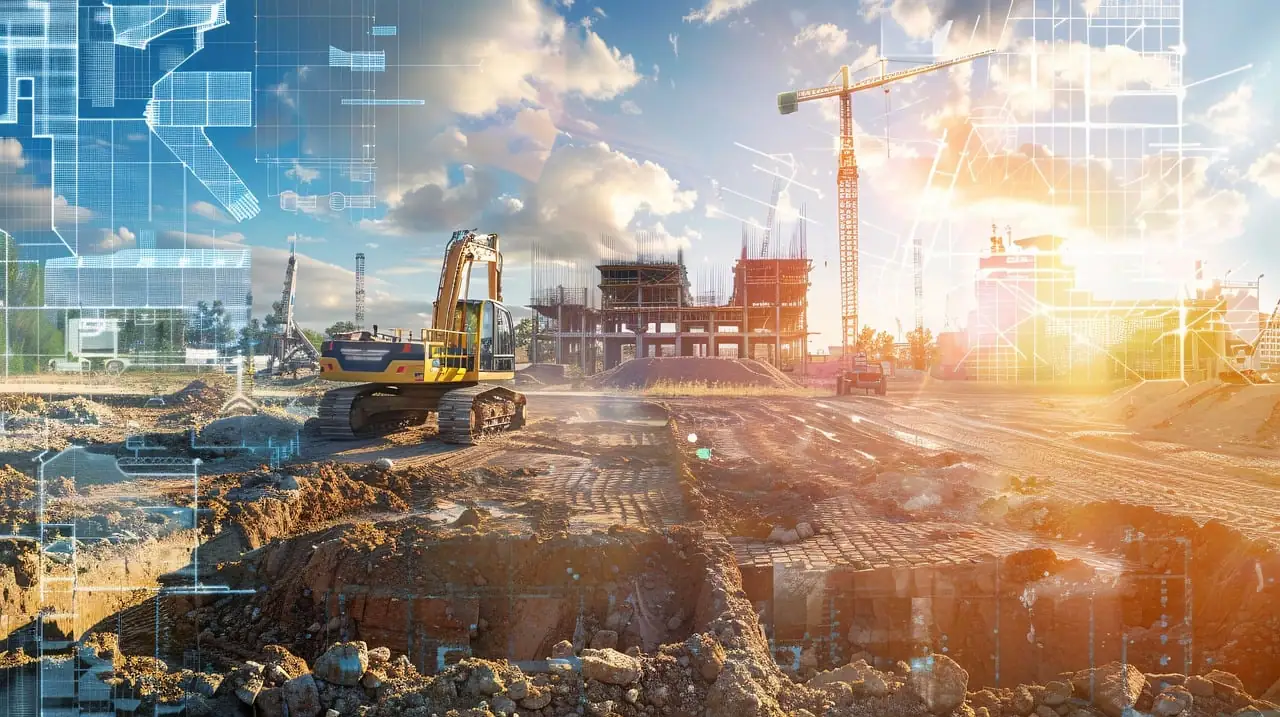
Expert Tips on Choosing Earthmoving Equipment for Large Projects
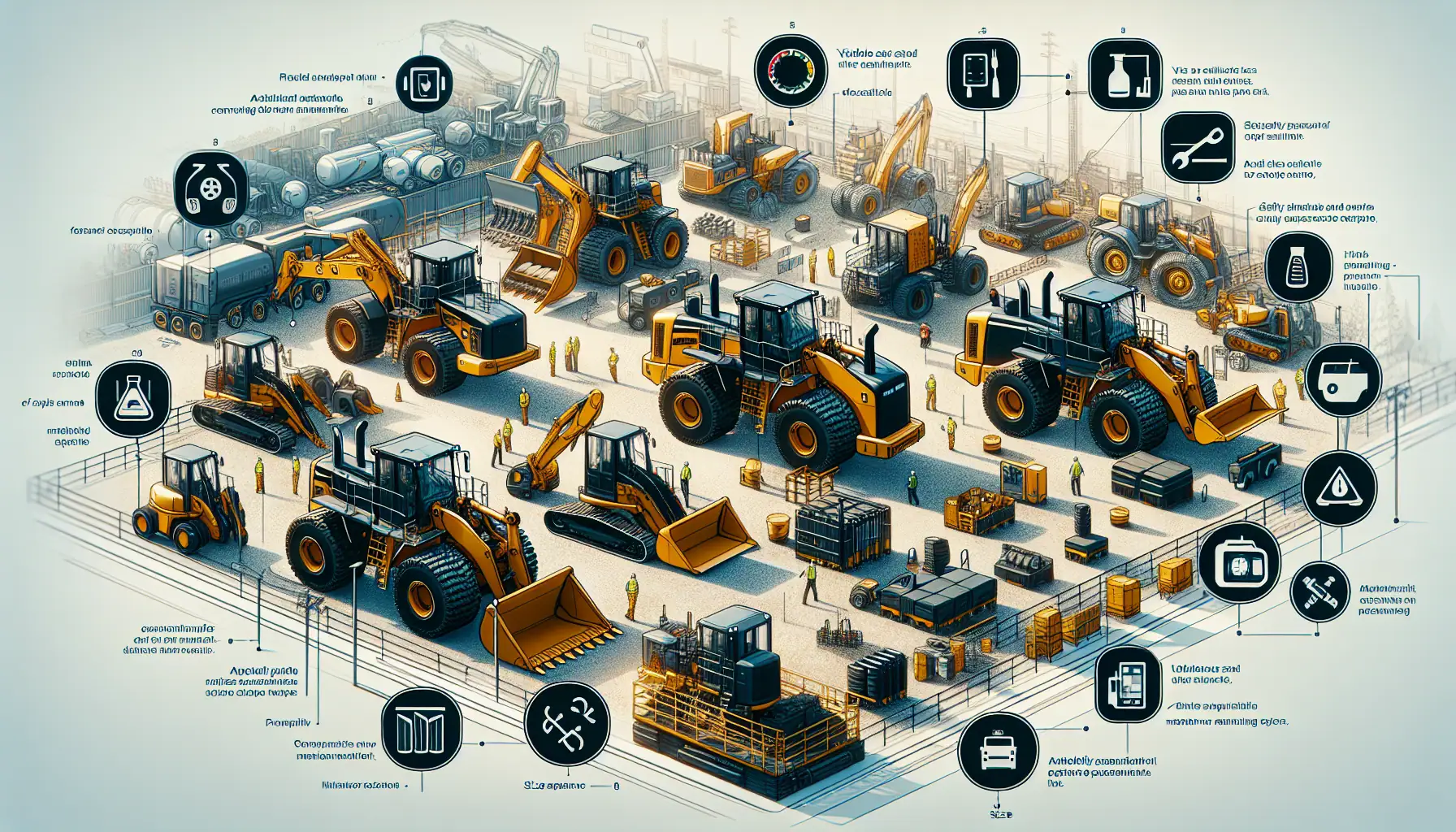
Top Functional Criteria for Selecting Heavy Construction Equipment
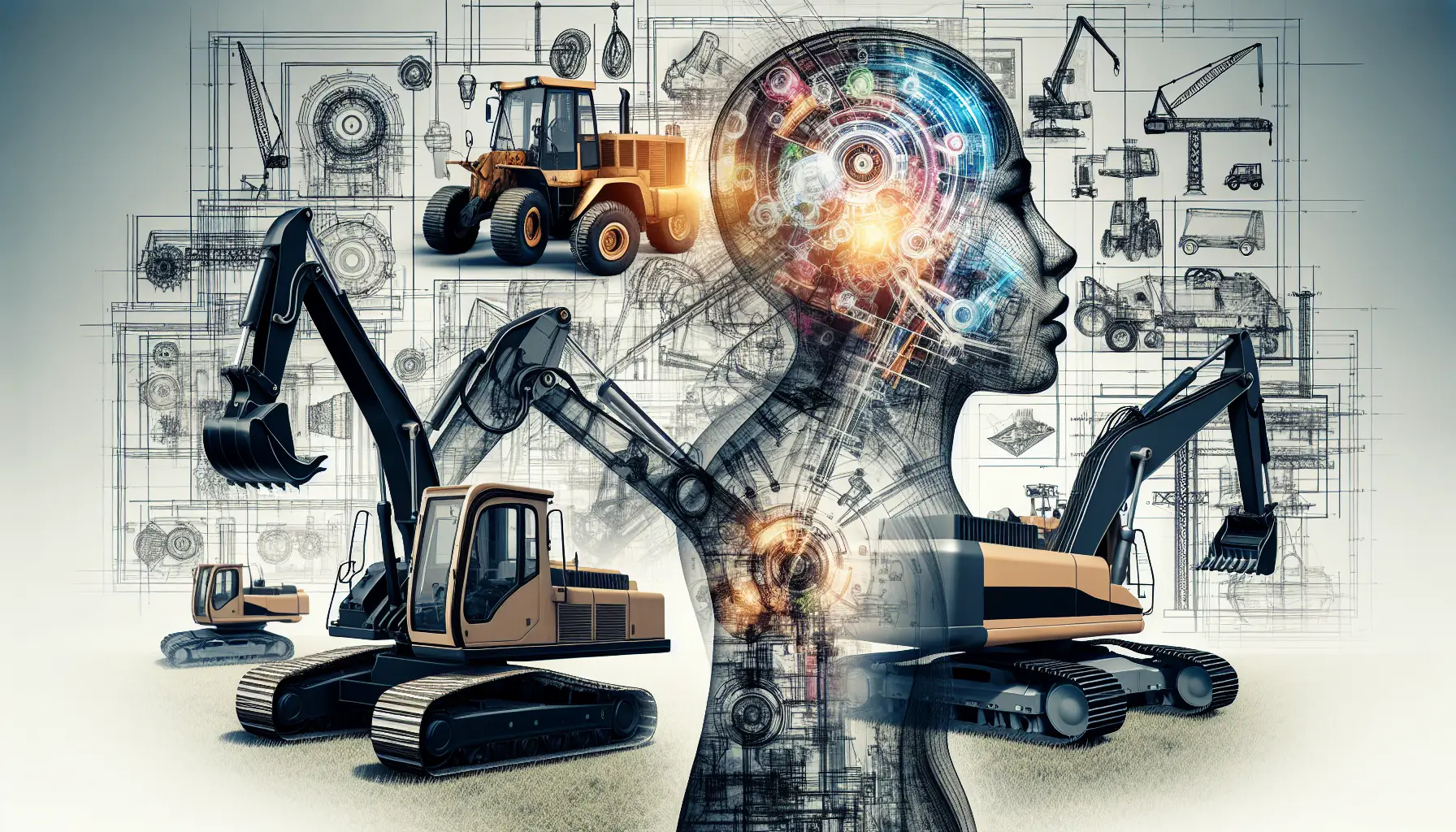
Construction Machinery: Detailed Guide to Equipment Specifications
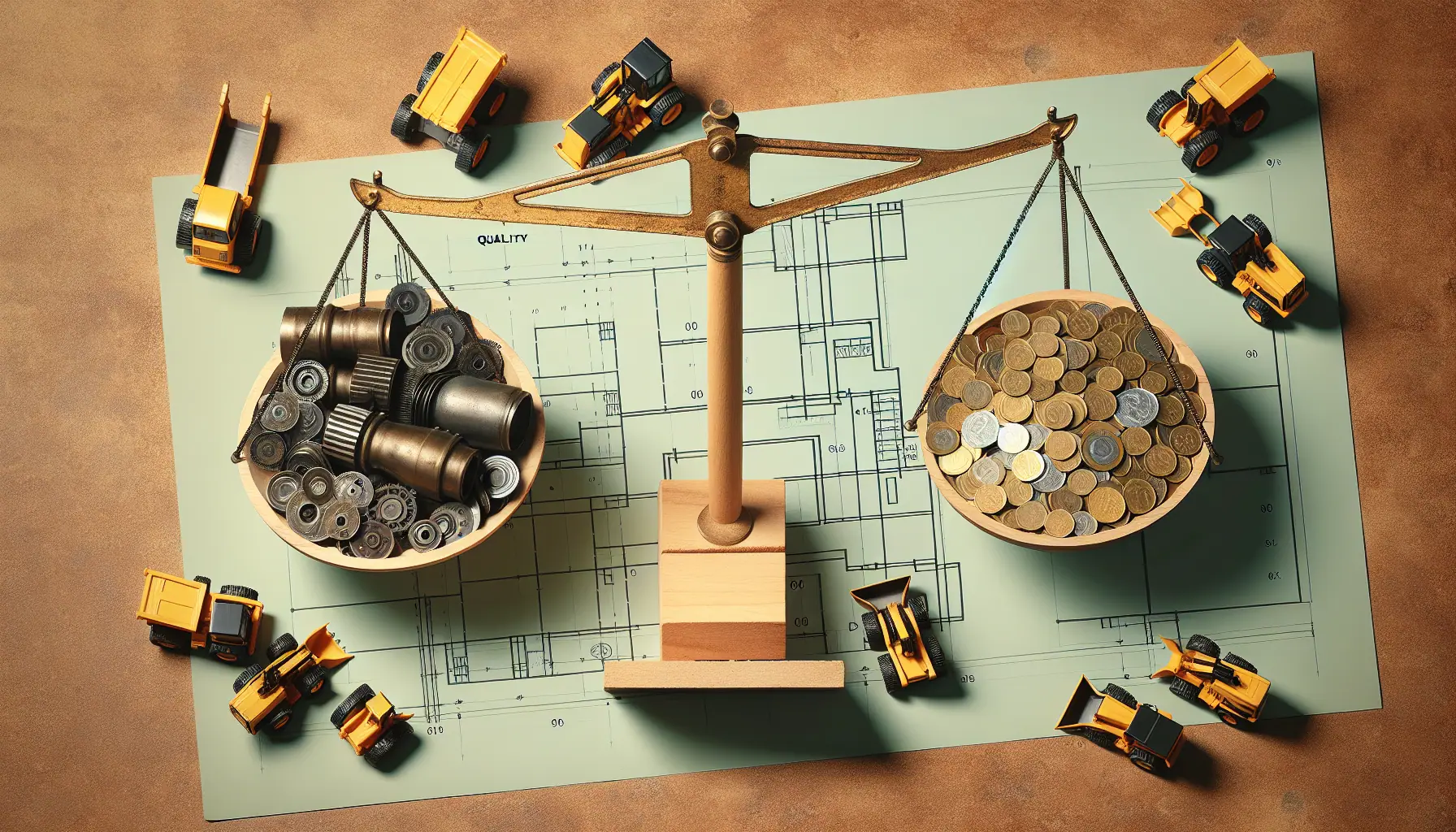
Heavy Machinery Prices: Key Factors in Cost and Quality Balance
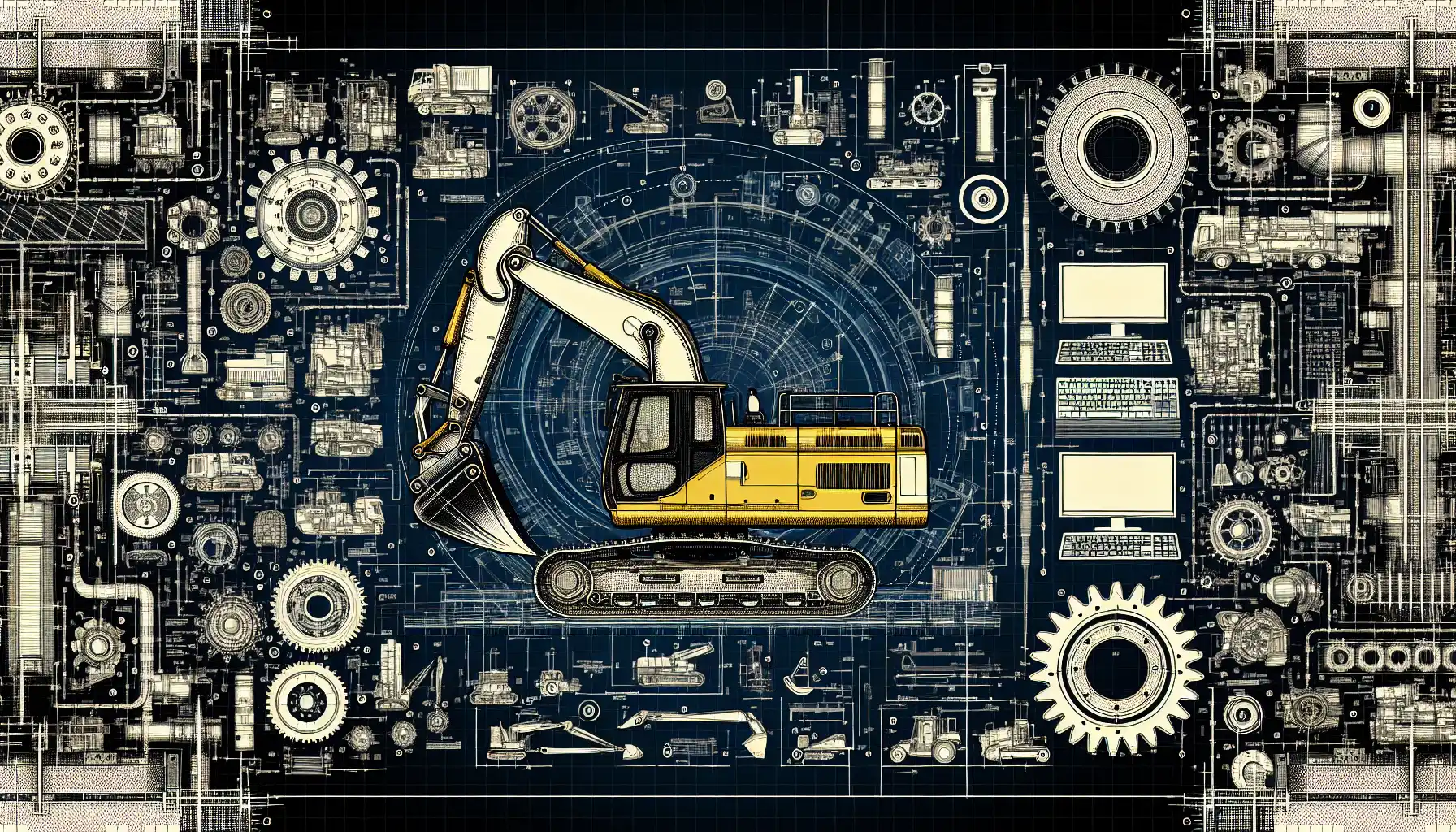
Best Construction Heavy Equipment Brands: Pros and Cons
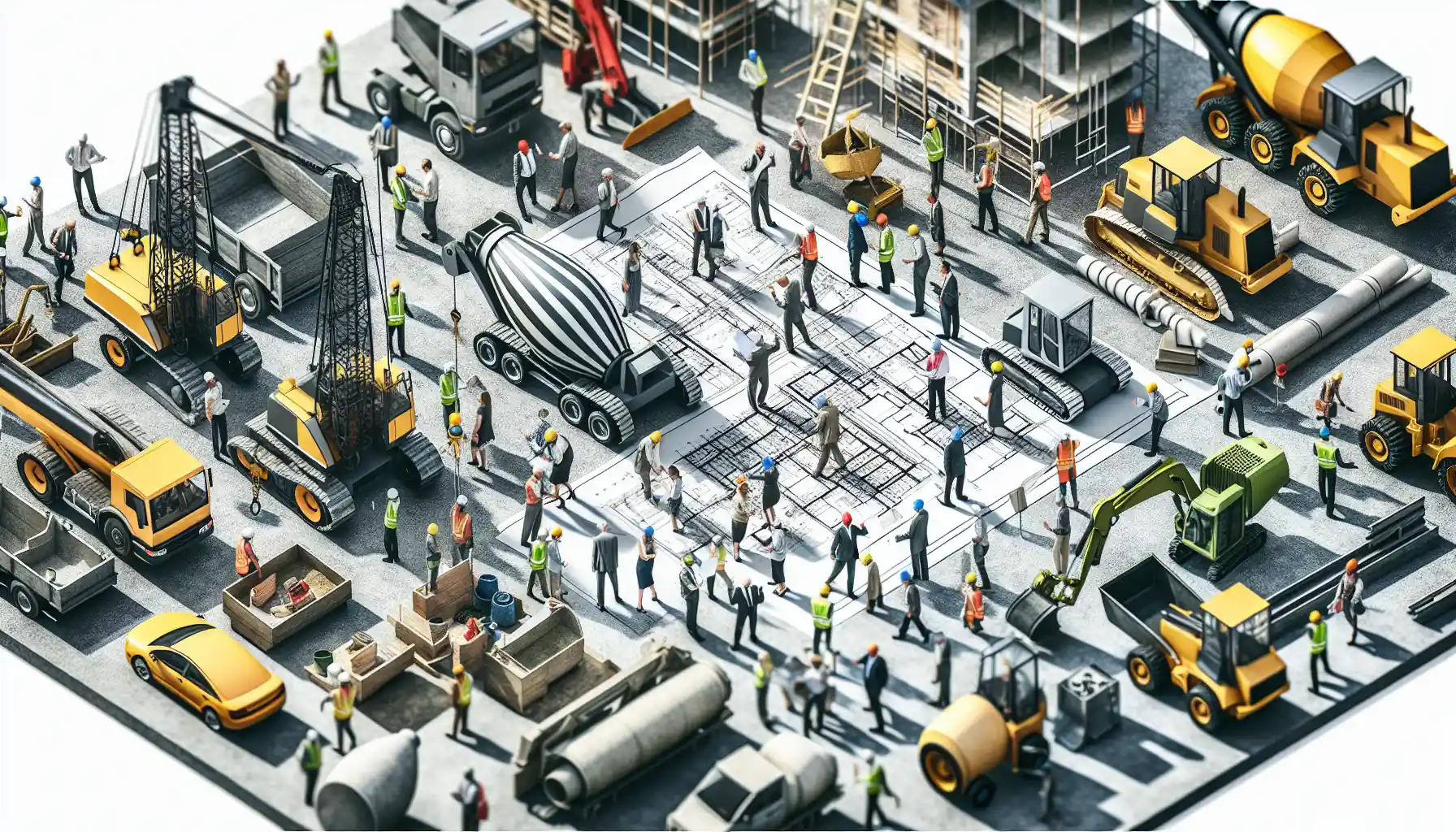
Construction Site Equipment: How to Determine Your Requirements
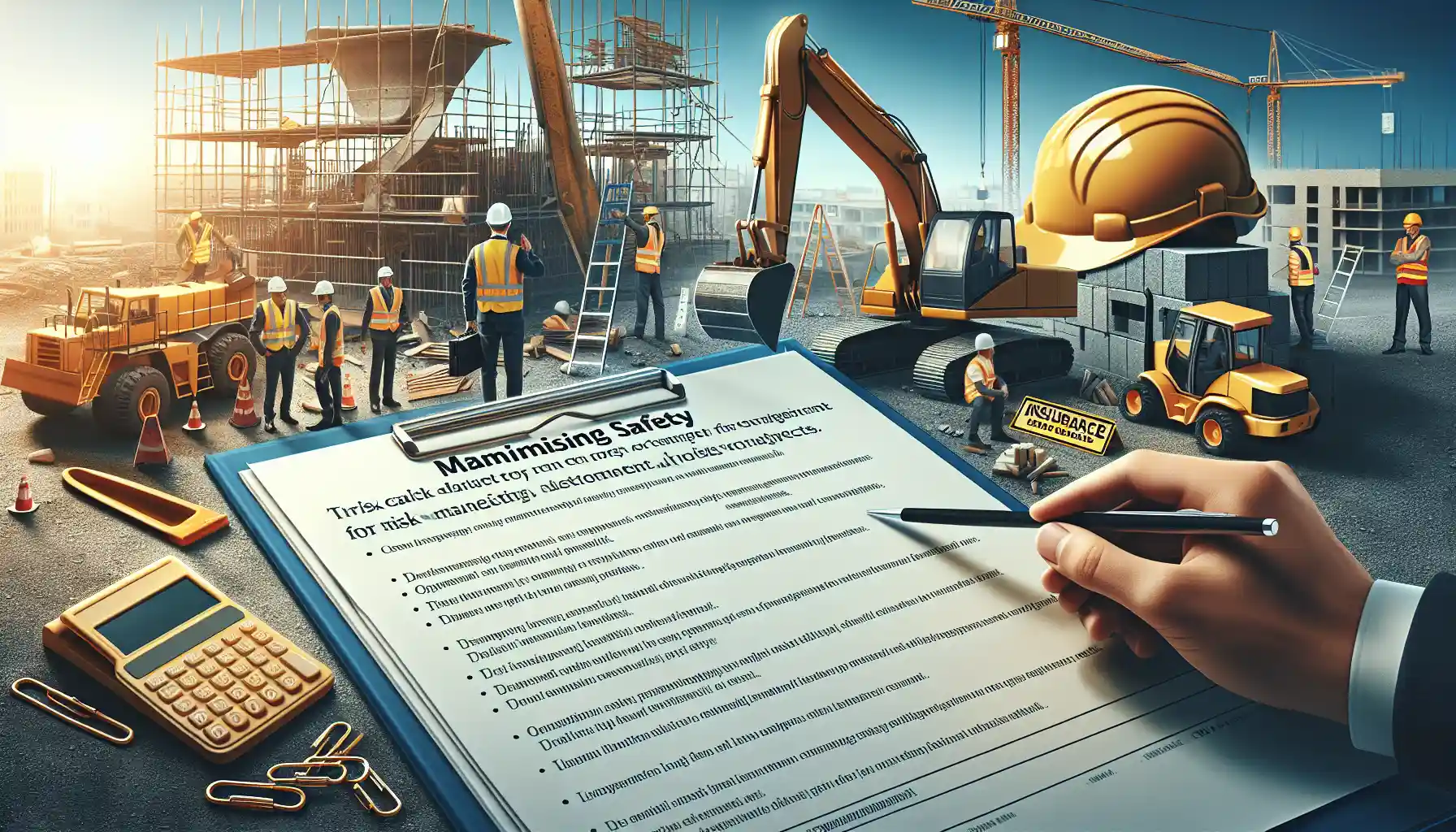
Maximizing Safety: Risk Management for Construction Projects
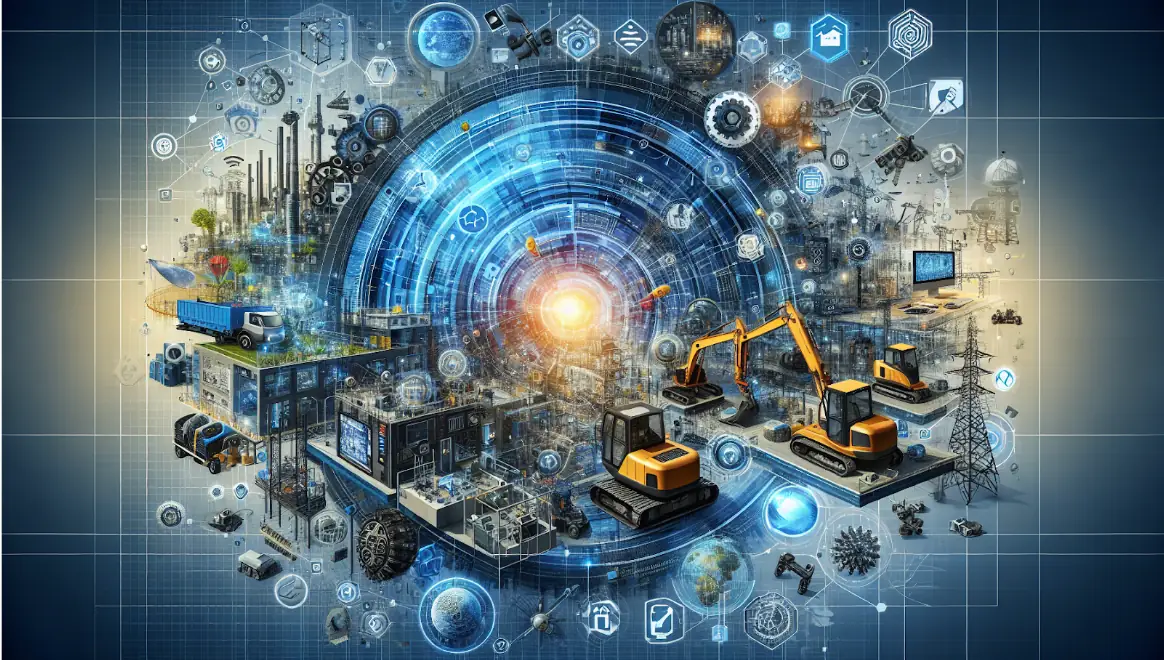
Innovations in Construction: Transforming Machinery and Equipment
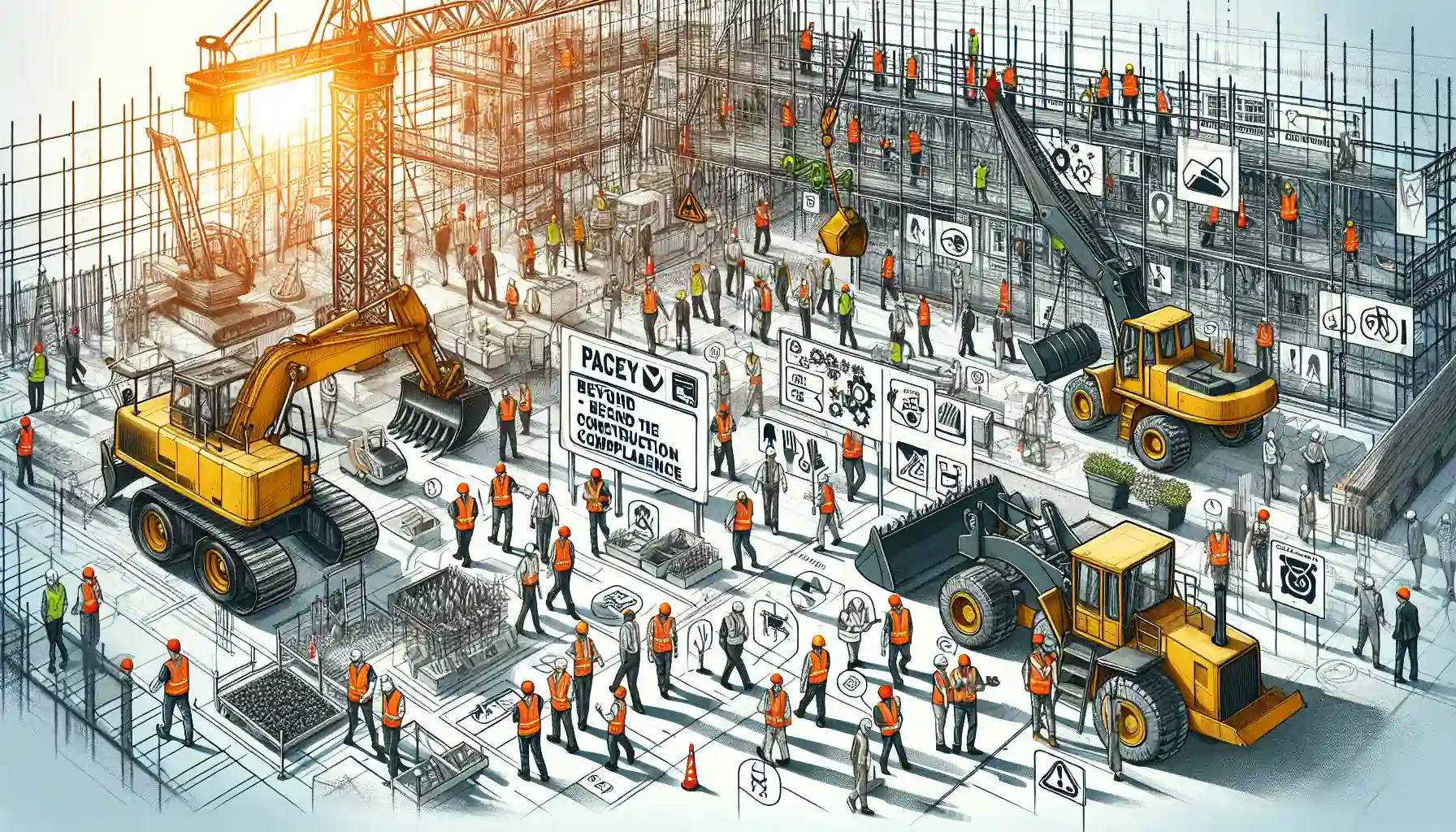
Heavy Equipment Safety: Beyond the Basics in Construction Compliance
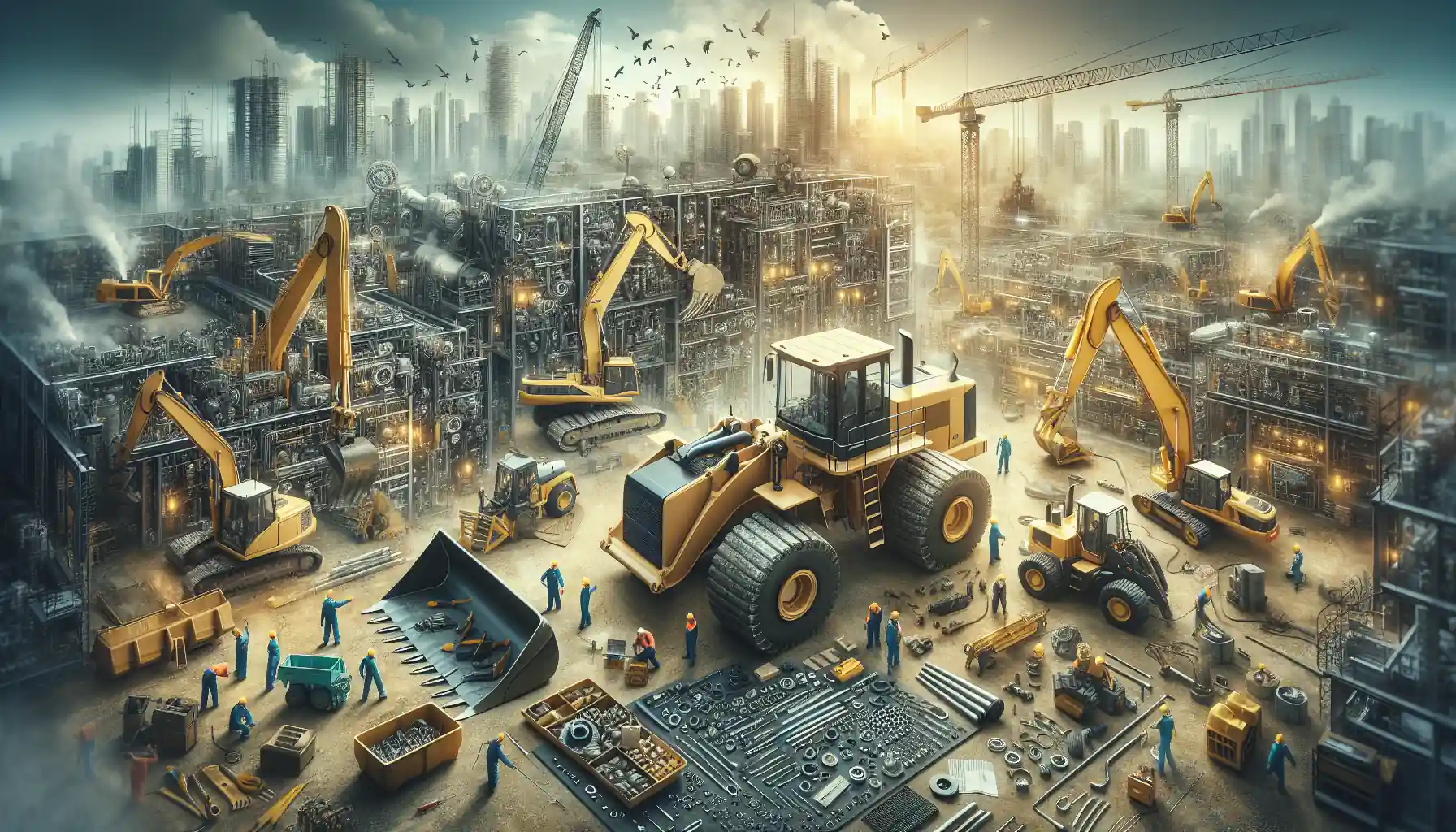
The Essential Handbook for Construction Equipment Repair and Maintenance
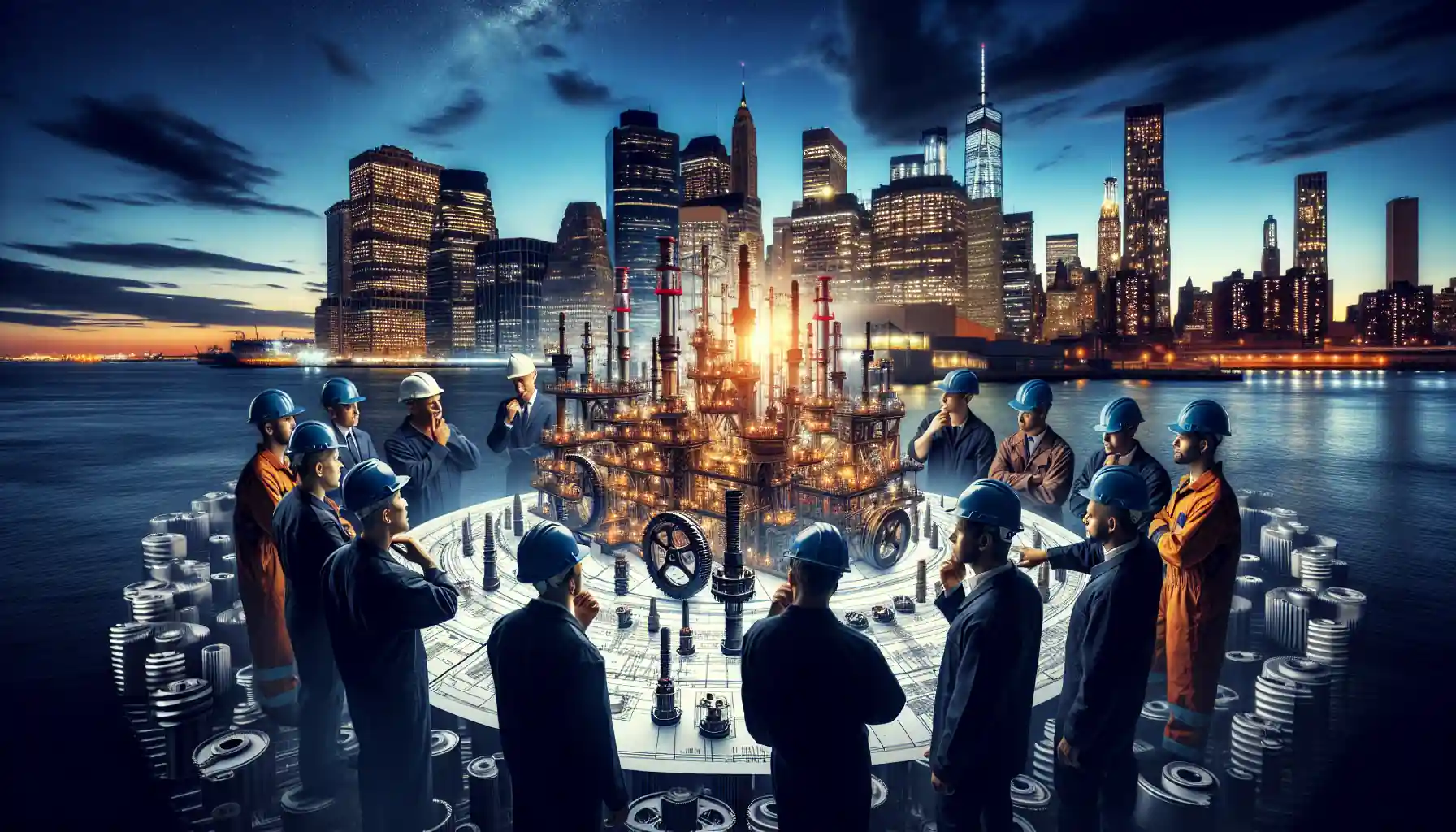
How to Efficiently Source Oil and Gas Machinery Parts in NYC
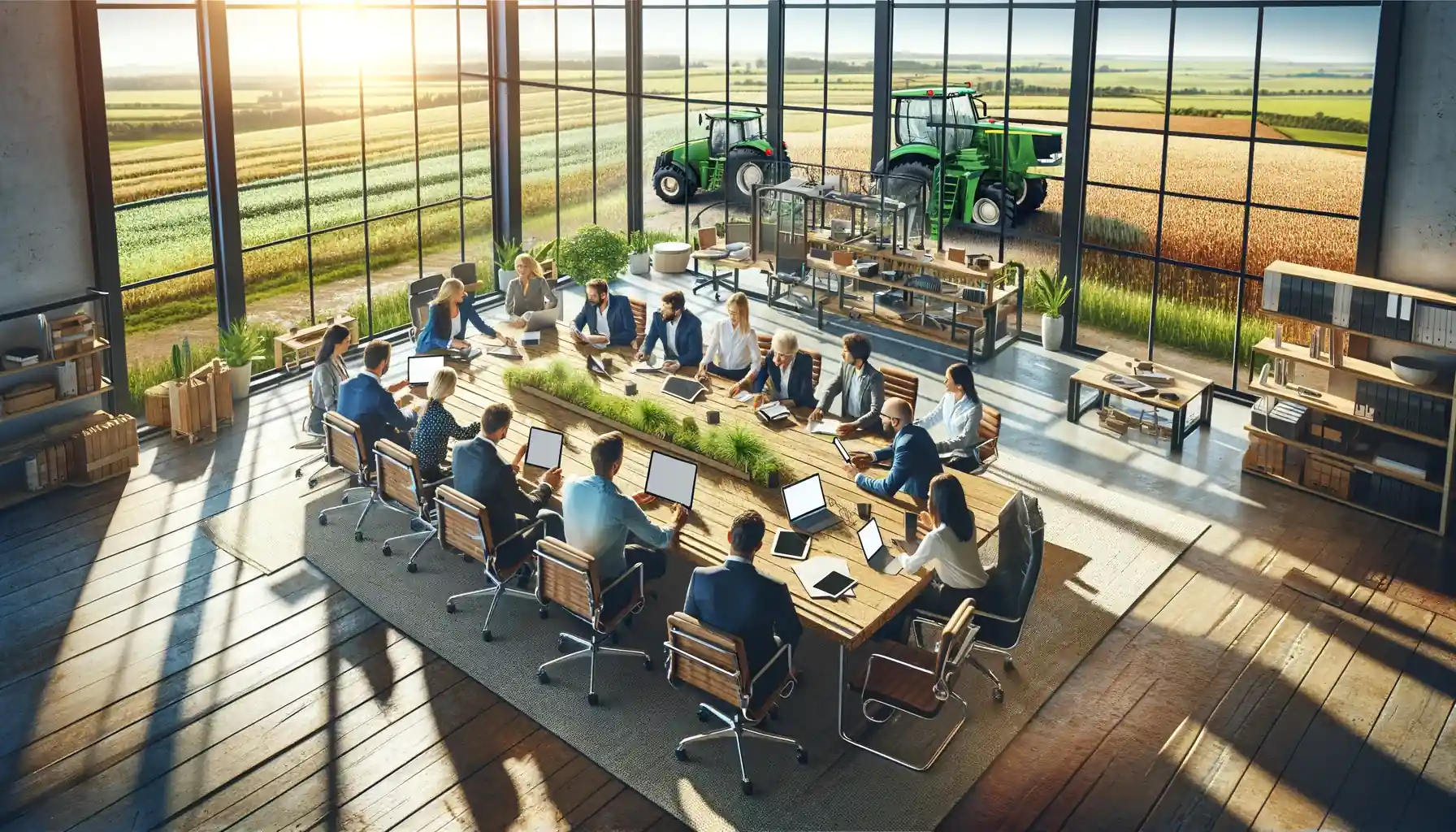
Essential Guide to Sourcing Agriculture Equipment Parts
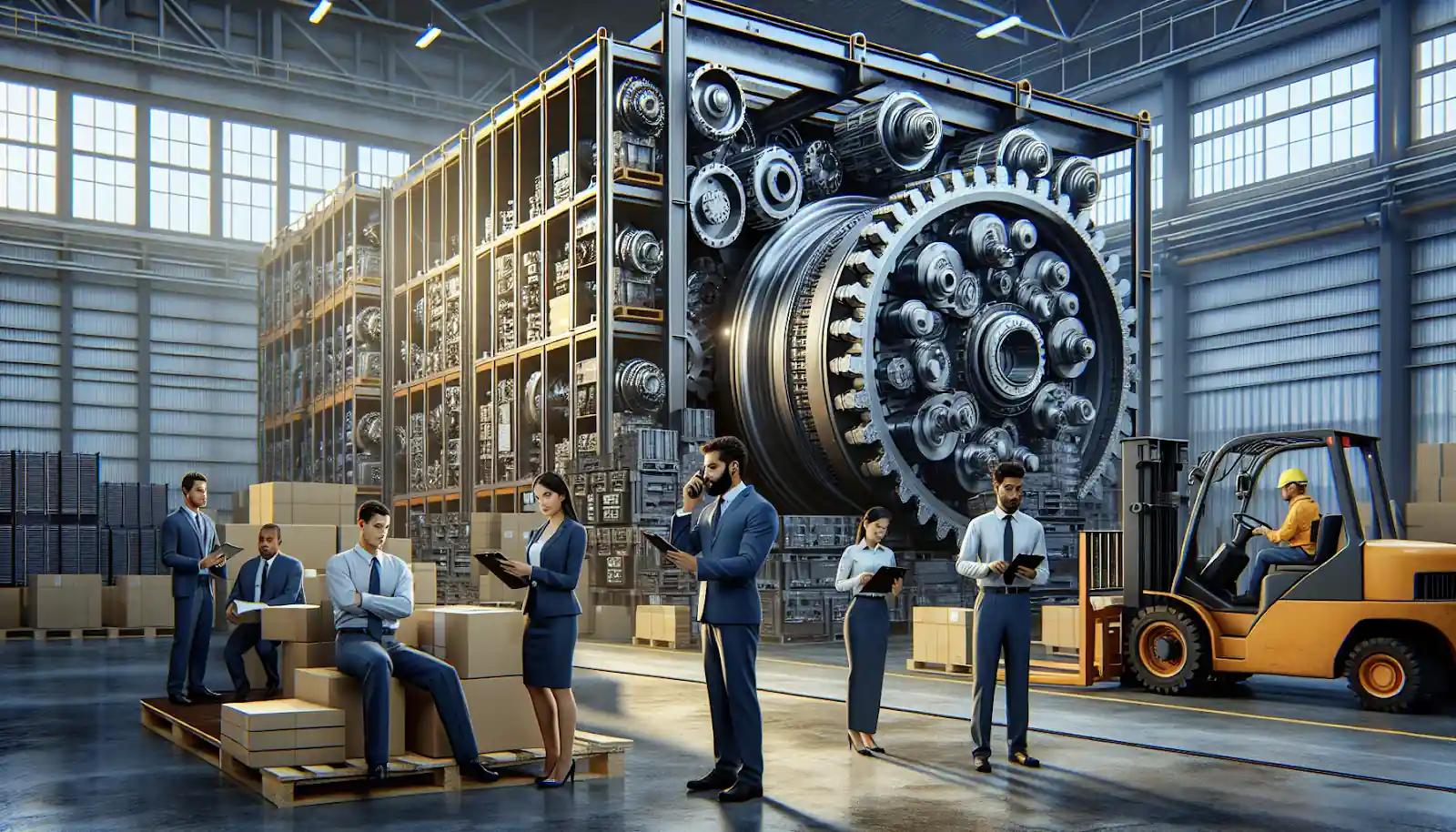
How to Source Mining Machinery Parts: Tips and Strategies
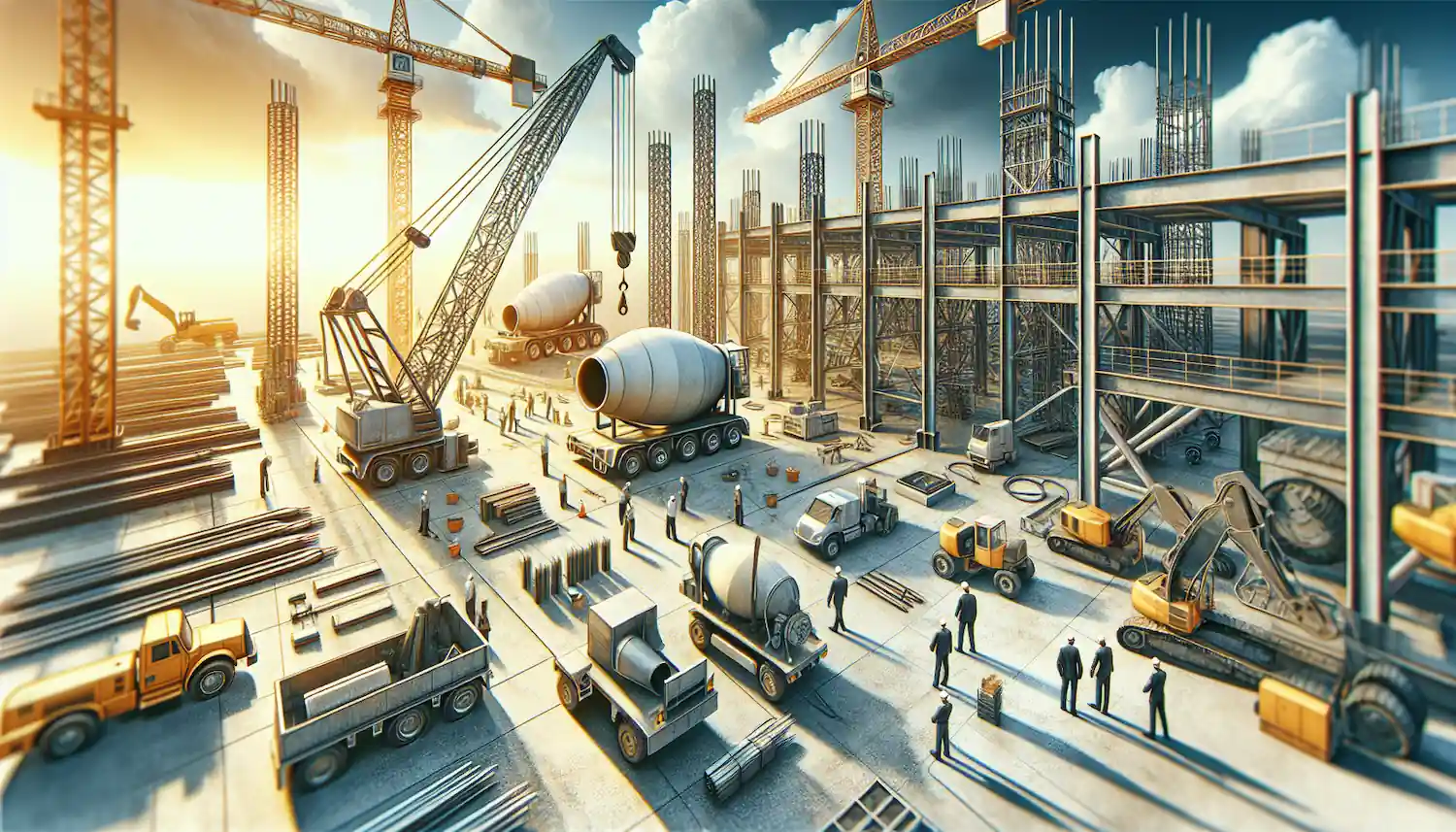