Motor Graders: Key Elements to Consider for Optimal Selection
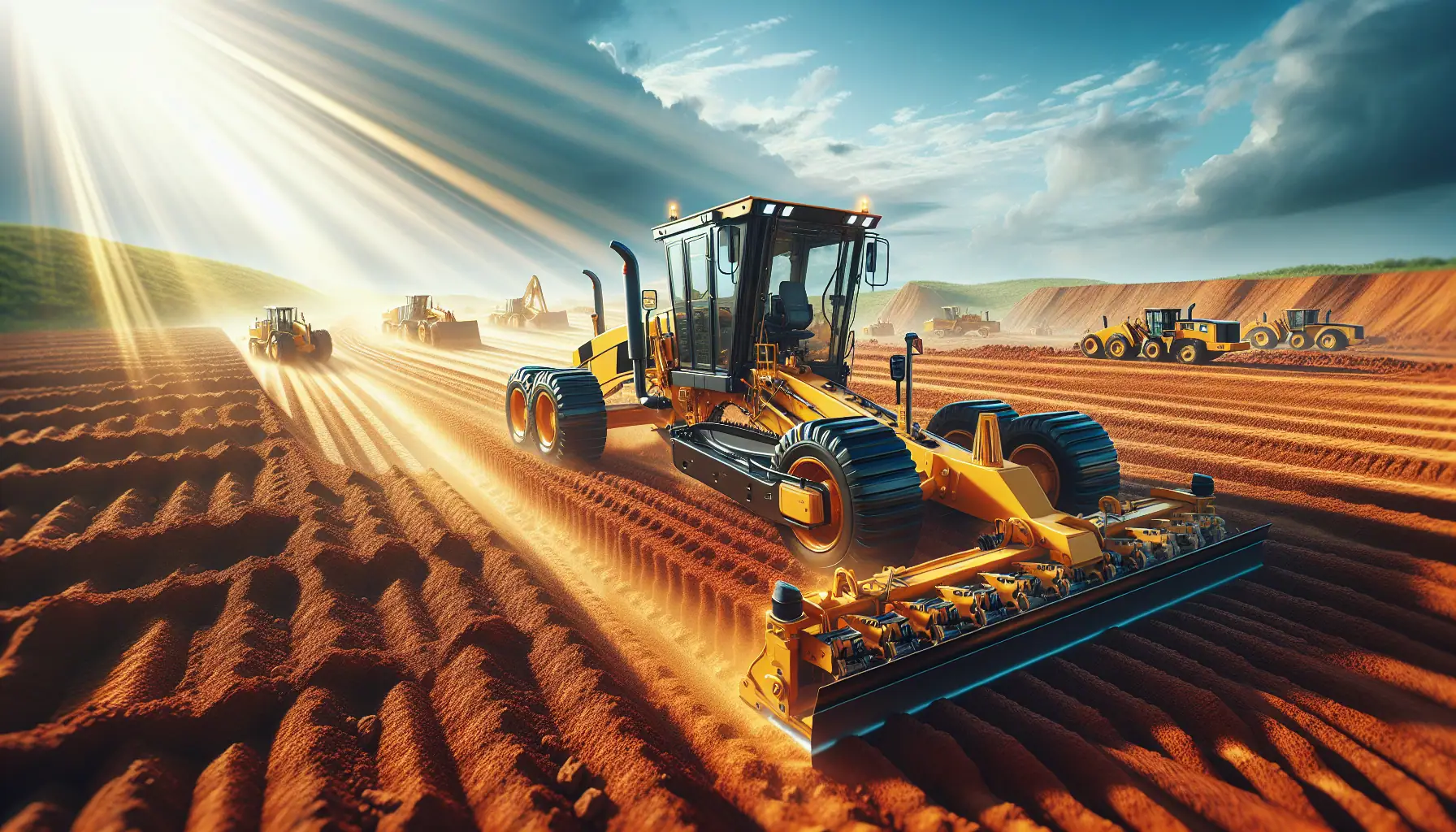
Motor graders, also known as grader machines, are essential pieces of grader equipment in construction and road building projects. When you're in the market for a motor grader, it's important to understand the key factors that influence your decision. From maintenance requirements to hydraulic systems, the right choice can lead to significant cost savings and improved job efficiency.
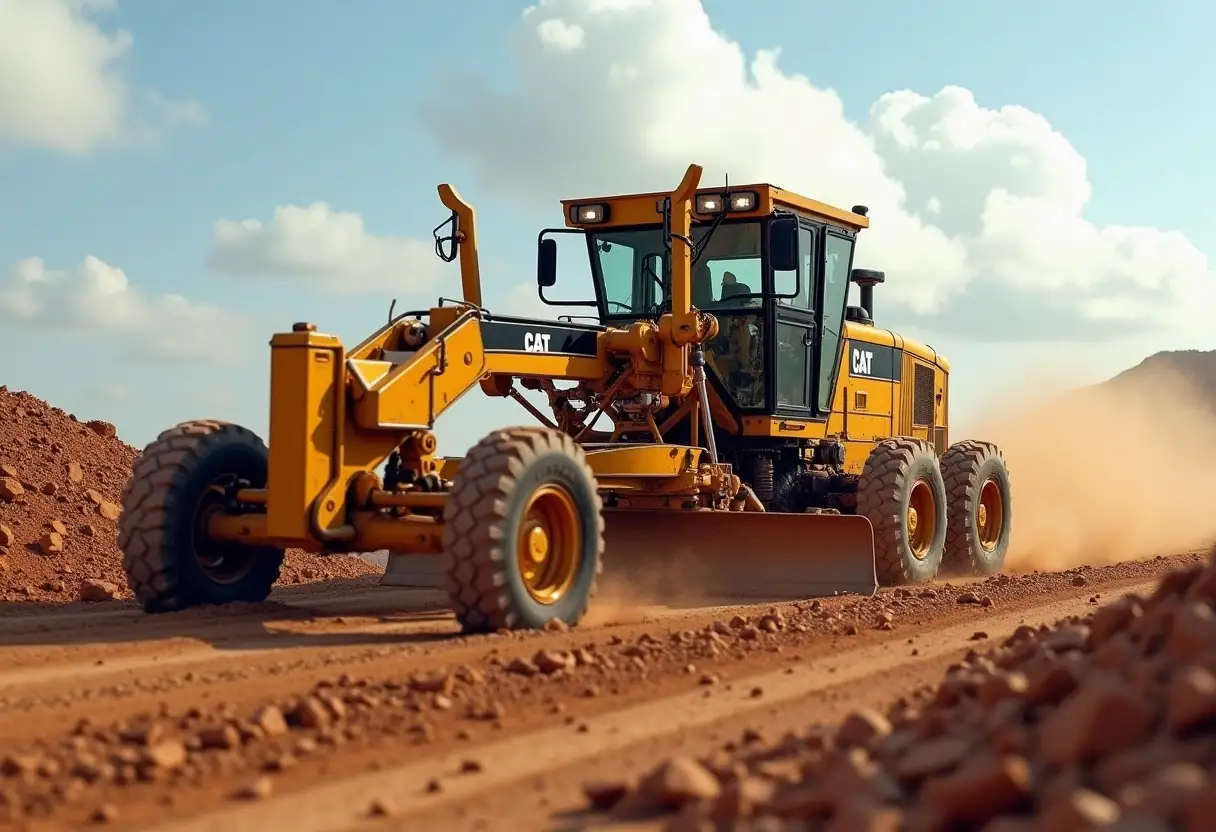
Selecting the optimal motor grader involves considering various aspects such as job requirements, motor grader technology features, and size specifications like cat motor grader sizes. You'll need to evaluate different grader types, including mini graders and construction graders from top manufacturers like Cat, Komatsu, and Volvo.
Understanding Motor Grader Specs
When you're looking to select the optimal motor grader for your projects, it's crucial to understand the key motor grader specs that influence performance and efficiency. Let's delve into the essential elements you need to consider.
Engine Power and Performance
The heart of any motor grader is its engine. You'll find a range of power outputs available, typically from 93 kW (125 hp) to 209 kW (280 hp) . For instance, the Cat C7.1 engine offers a power range of 131-147 kW (176-196 hp). It's important to note that many models feature a power range, allowing for optimal performance across various tasks.
Engine specifications to pay attention to include:
- Emissions compliance (e.g., U.S. EPA Tier 3/ EU Stage IIIA Equivalent)
- Torque rise (can be as high as 40-64%)
- Maximum torque (e.g., 889 N·m or 656 lbf-ft)
Blade Size and Configuration
The moldboard, or blade, is a critical component of your motor grader. The blade size configuration directly impacts performance. Standard blade widths typically range from 3.7 m (12 ft) to 4.3 m (14 ft). The blade's height and thickness also play crucial roles in performance and durability. Effective blade length is another key consideration.
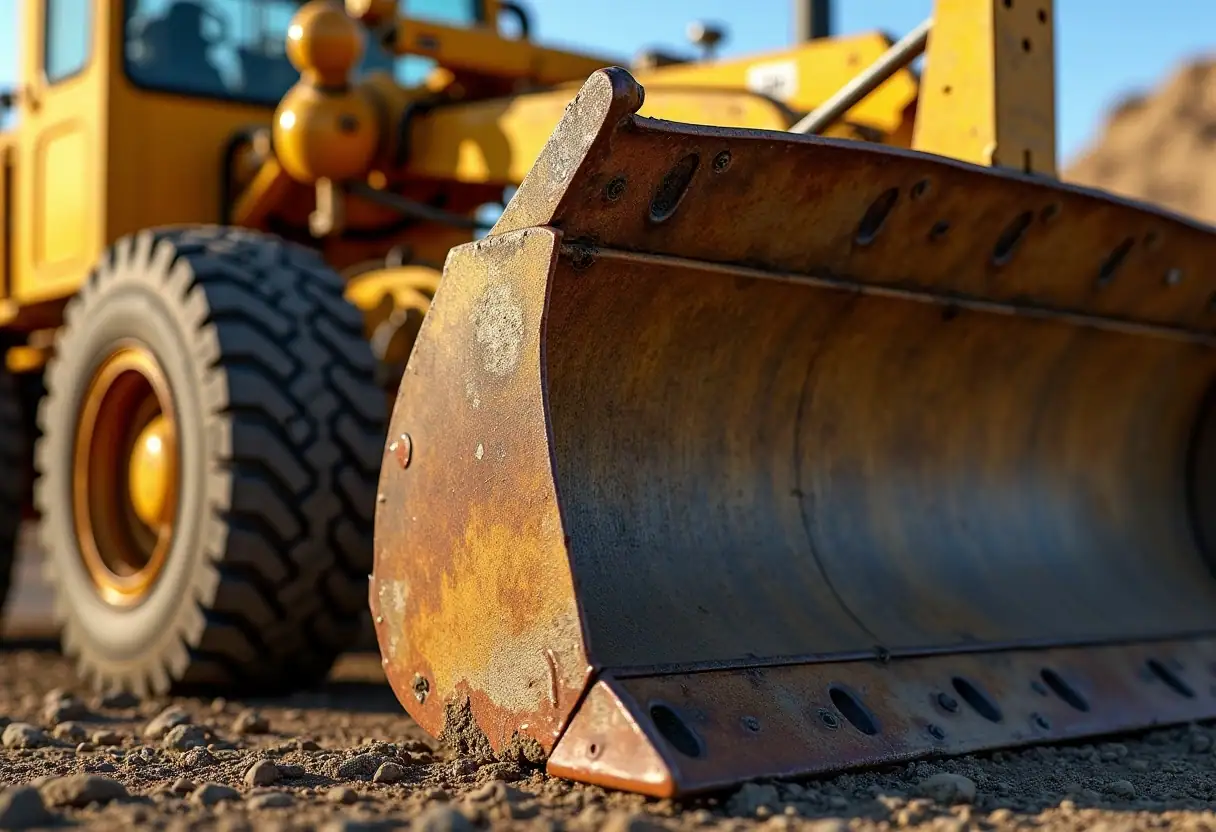
Key blade specifications include:
- Width: 3.7 m (12 ft) to 4.3 m (14 ft)
- Height: 509 mm (20 in) to 610 mm (24 in)
- Thickness: Standard 5/8-inch, with 3/4-inch and 1-inch options available
Motor grader blade pitch and grader blade angles also impact performance and should be considered when evaluating blade options.
Articulation and Maneuverability
Articulation has revolutionized motor grader design since its introduction in 1967. Modern graders typically offer an articulation range of 20° left and right. This feature, combined with front axle lean and oscillation, greatly enhances maneuverability. All-wheel-drive options can further improve traction and maneuverability in challenging conditions.
Key maneuverability specs:
- Turning radius: Can be as low as 7.21 m (23 ft 8 in)
- Steering range: Up to 50° left and right
- Front axle lean angle: 18° left and right
To get a free sourcing machinery or parts consultation and a free quote, don't hesitate to contact MCH Parts.
Assessing Job Requirements
When selecting a motor grader, it's crucial to evaluate your specific job requirements. This assessment will help you choose the right machine for optimal performance and efficiency across various project types and terrains.
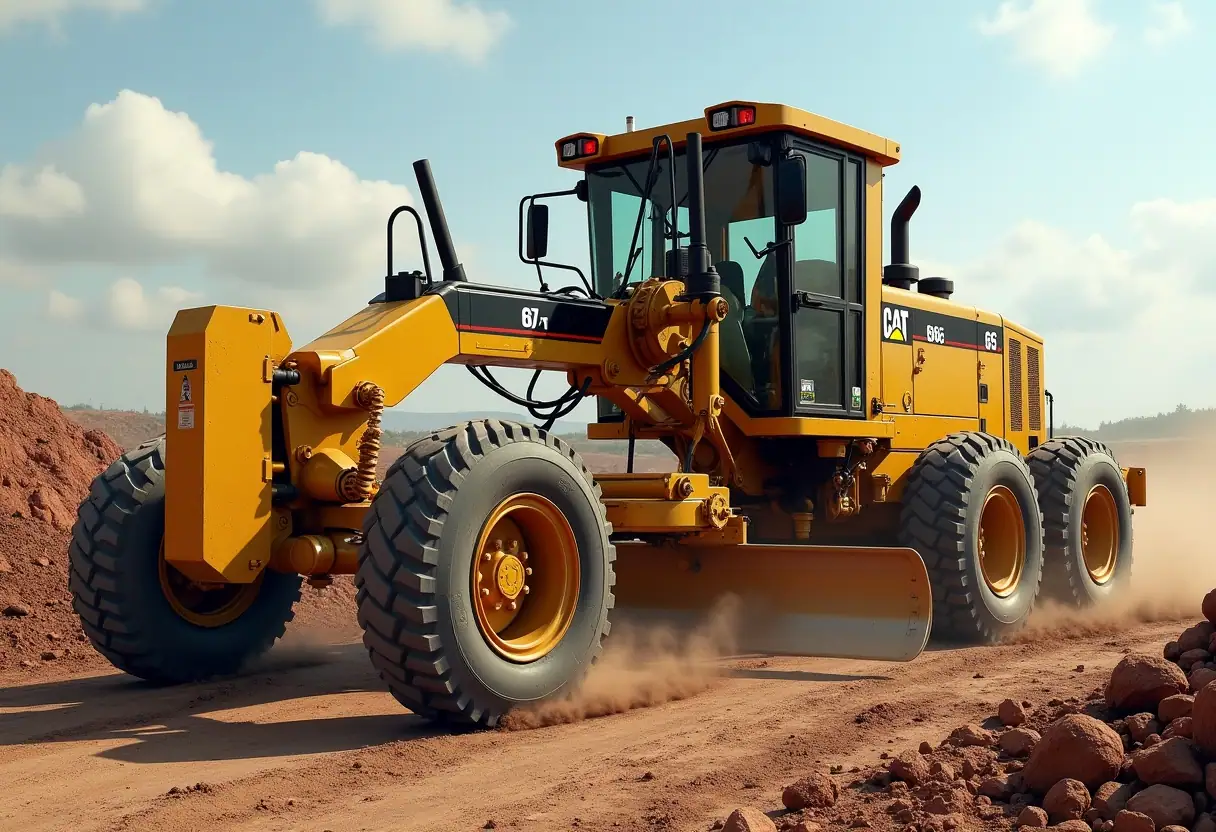
Project Types and Terrain
Motor graders are versatile machines used in a wide range of construction and road maintenance projects. They play a vital role in shaping and leveling surfaces for roads, highways, and other infrastructure. You'll find them essential in:
- Site preparation: Creating level bases for foundations, roadways, and parking lots.
- Landscaping: Sculpting land to meet precise design specifications from design files.
- Road construction: Preparing base courses and ensuring proper drainage.
- Building construction: Leveling grounds before laying foundations.
Consider the terrain you'll be working on, as motor graders excel in cutting and shaping surfaces to meet specific grades and slopes. Elevation control is a key factor in many projects.
Productivity Needs
To assess your productivity needs, calculate motor grader productivity - how much material your motor grader can move per day compared to the project requirements. Key factors to consider include:
- Blade size and configuration
- Engine power and performance
- Operator skill level
Use a productivity calculator or formulas to calculate motor grader performance based on the area covered by its moldboard. Efficiency typically ranges from 0.70 to 0.85, depending on job conditions. A productivity assessment can help optimize operating speed and job efficiency.
Versatility Considerations
Motor graders offer versatility through their ability to perform various tasks:
- Finish grading: Precise adjustment of ground surfaces for specific elevation control requirements and smoothness.
- Spreading materials: Even distribution of soil, gravel, or other aggregates.
- Creating drainage slopes: Shaping surfaces to ensure proper water runoff.
- Snow removal capabilities: Clearing roads and surfaces during winter months.
Consider specialized attachments like scarifiers for breaking up hard surfaces or wing blades for moving more material in one pass. These enhance the machine's versatility and make it valuable in various scenarios beyond its primary construction role.
To get a free sourcing machinery or parts consultation and a free quote, don't hesitate to contact MCH Parts.
Evaluating Technology and Control Systems
GPS and Machine Control
When selecting a motor grader, you should consider the advanced technology and control systems available. GPS machine control technology has revolutionized motor grader operations, enabling precise leveling and elevation control in all weather conditions. GPS-based grade control systems like Cat Grade Control can improve efficiency and speed by up to 50%, resulting in significant cost savings. These systems typically feature in-cab displays that provide operators with plan views, cross-section views, and cut/fill information.
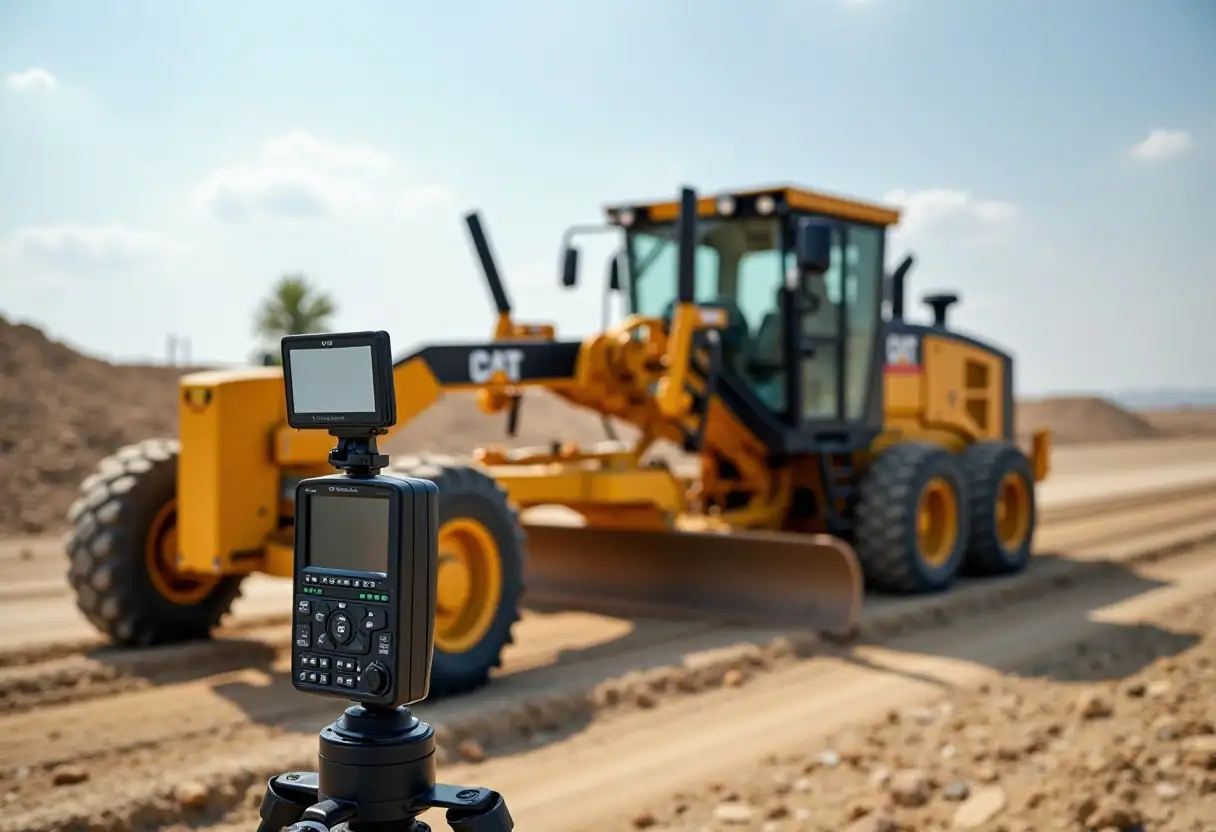
Machine control technology like AccuGrade GPS, AccuGrade Laser, and AccuGrade Sonic has evolved to offer numerous benefits:
- Reduced rework through fewer passes to reach final grade
- Enhanced productivity and accuracy
- Improved jobsite safety
- Simplified operator training
Advanced systems like Caterpillar's AccuGrade system combine digital design data with in-cab guidance features and automatic blade control, reducing the operator's workload and the need for survey stakes. AccuGrade Cross Slope allows for automatic cross slope control, while AccuGrade ATS provides 3D elevation control using an ATS instrument for target tracking. These systems often include features like automatic/manual modes and remote offset switches for enhanced control.
Operator Interface and Ergonomics
Modern motor graders prioritize operator comfort and efficiency. Joystick grader controls have replaced traditional steering wheels and levers, putting total control in the operator's hands. This change has led to a 78% reduction in hand motions and improved wrist angles, as demonstrated in a University of Wisconsin study.
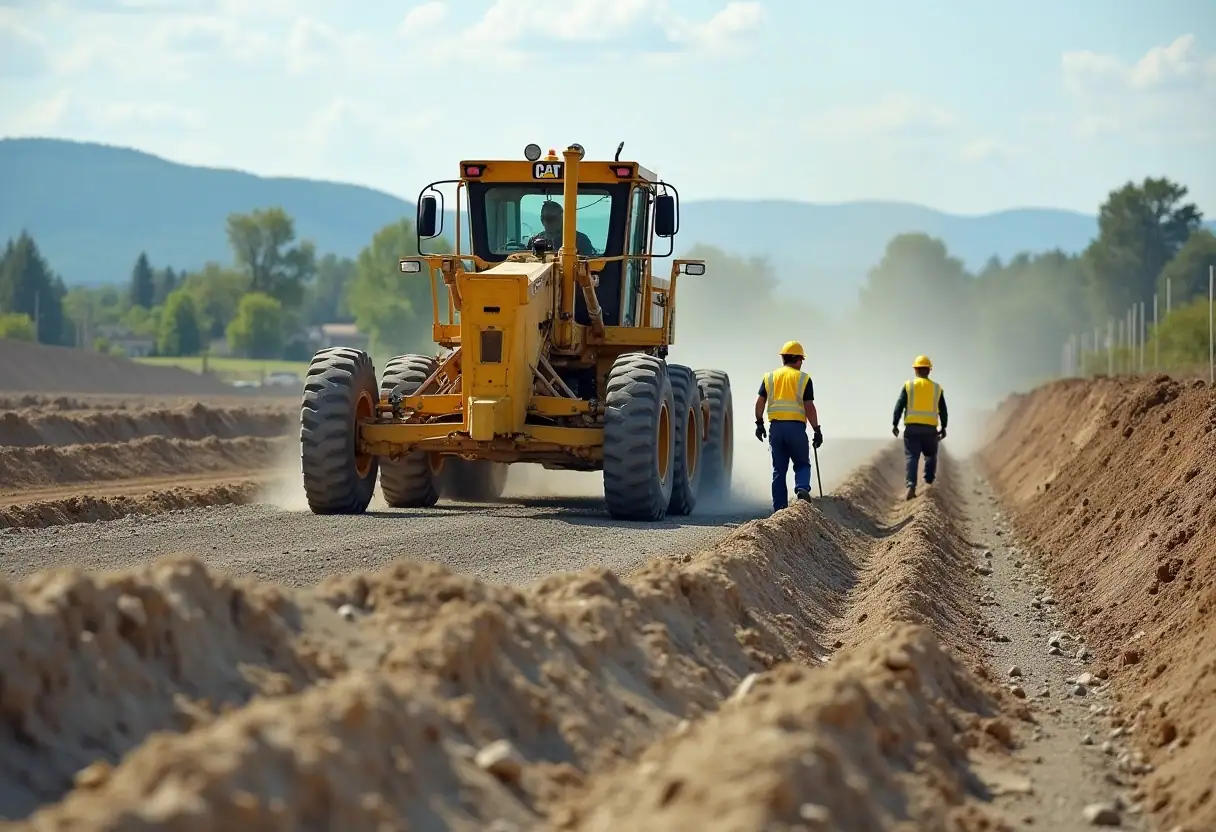
Key ergonomic features to look for include:
- Spacious, noise-reducing cabs
- Floor-to-ceiling windows for improved visibility
- Ergonomically positioned control levers
- Advanced HVAC systems
Telematics and Fleet Management
Telematics systems have become essential for efficient motor grader management. These systems provide real-time data on machine health, utilization, and maintenance needs. Key benefits include:
- Proactive problem identification
- Automated maintenance alerts
- Improved equipment security
- Accurate tracking of equipment hours
Telematics can help you optimize maintenance schedules, reduce idle times, and improve overall productivity. For example, CASE's ProCare program includes a telematics subscription as standard, offering comprehensive planned maintenance and machine support.
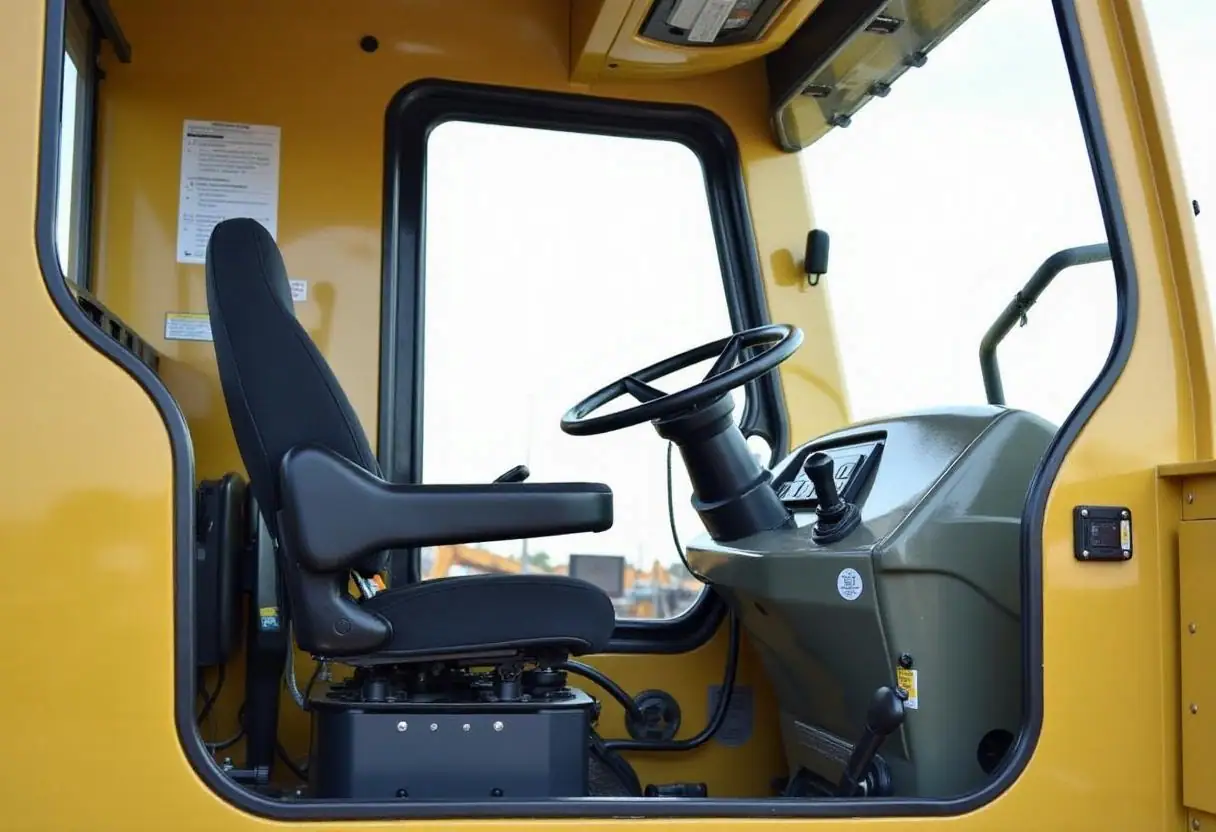
To get a free sourcing machinery or parts consultation and a free quote, don't hesitate to contact MCH Parts.
Size and Power Considerations
Weight Classes
When selecting a motor grader, you need to consider the weight class that suits your project requirements. Motor graders come in various sizes, with operating weights ranging from approximately 35,000 pounds to 162,000 pounds. The weight of the machine has a significant impact on its performance and capabilities. For instance, the CAT 120 series weighs around 35,000 pounds, while the larger CAT 24 can weigh up to 160,000 pounds.
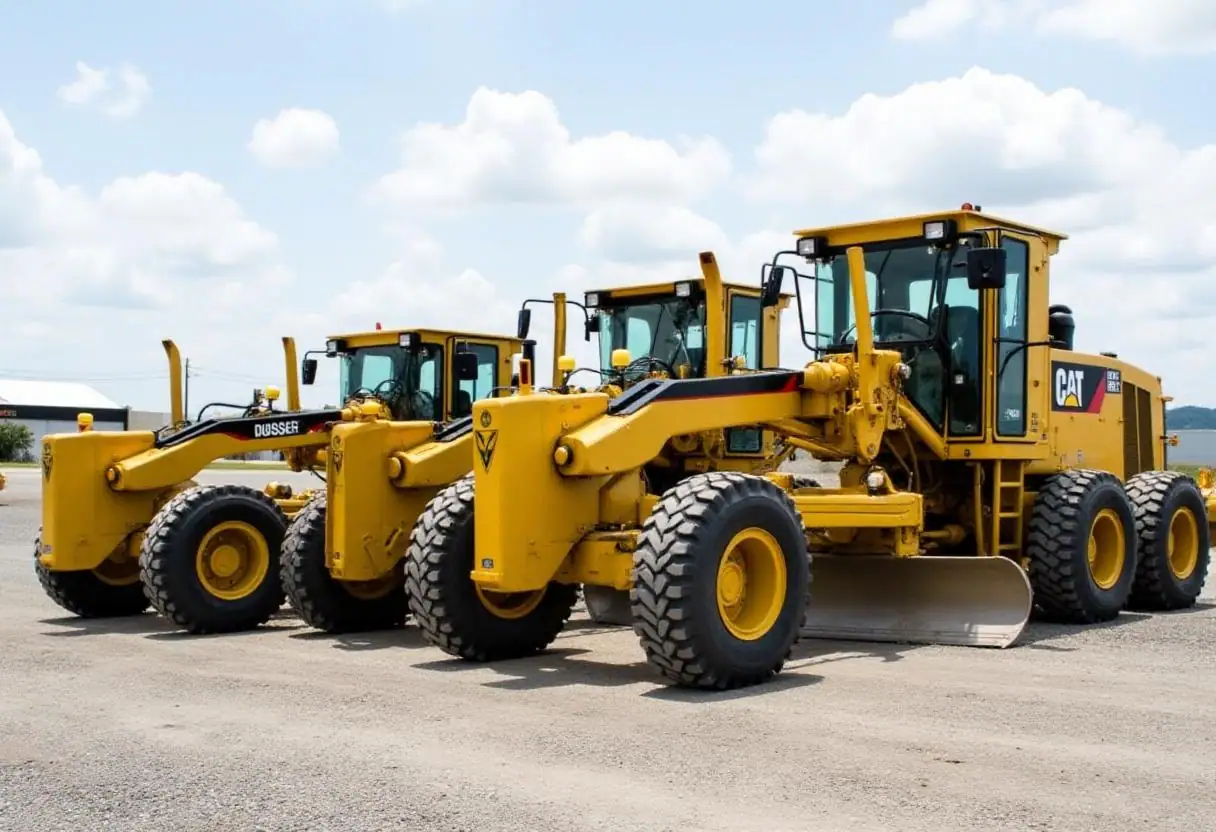
Horsepower Ranges
The horsepower of a motor grader directly affects its performance and ability to handle different tasks. Horsepower ranges typically correspond to the size of the machine. Small graders usually have 80 HP to 120 HP, medium-sized graders range from 125 HP to 180 HP, and large graders boast 250 HP or more. For example, the CAT 140 series offers 179 HP to 250 HP, depending on the specific model.
Fuel Efficiency
Fuel efficiency has become a crucial factor in motor grader selection, as fuel costs can account for up to 50% of operating expenses. Modern motor graders are designed with fuel efficiency in mind. For instance, the CAT C7.1 motor uses less fuel with ECO mode. Some manufacturers, like Mahindra Construction Equipment, offer highly fuel-efficient models such as the RoadMaster G75, which consumes only 4.5 liters per hour.
To get a free sourcing machinery or parts consultation and a free quote, don't hesitate to contact MCH Parts.
Conclusion
Choosing the right motor grader is a crucial decision that has a significant impact on project efficiency and cost-effectiveness. By carefully considering factors such as job requirements, technology features, and size specifications, you can select a machine that best suits your needs. The advancements in GPS technology, telematics, and ergonomic design have revolutionized the motor grader industry, offering improved accuracy, productivity, and operator comfort.
Ultimately, the optimal motor grader selection depends on a thorough understanding of your specific project demands and operational goals. Whether you're working on road construction, site preparation, or landscaping, the right motor grader can make all the difference in achieving superior results. Consider reaching out to MCH Parts for a free sourcing machinery or parts consultation, ensuring your business benefits from top-tier equipment and service. By making an informed decision, you'll be well-equipped to tackle your construction challenges with confidence and efficiency.
FAQs
What should I consider when selecting a cutting-edge for a motor grader?
When choosing a cutting edge for a motor grader, you should consider the shape, width, and thickness of the edge. Cat DH-2™ through-hardened steel edges are available in various shapes and thicknesses to suit different applications. For extended edge life, consider options with tungsten carbide edges.
What are the key operational considerations for a motor grader?
During the operation of a motor grader, three critical factors should be considered: Penetration - the ability of the grader to penetrate tough, compacted, rocky, or frozen material; Wear life: the durability of the grader against wear, scouring, and abrasive actions of the material being handled.
What are the primary components of a motor grader?
A typical motor grader consists of three axles (with the front and rear often having twin axles), an engine, a cab, and an adjustable blade. Modern motor graders may also include additional attachments such as a ripper, scarifier, loader bucket, and a compactor on the front and rear axles.
How do I choose the right motor grader for my needs?
When selecting a motor grader, consider the size and weight of the machine as these factors determine the amount of material it can handle and its efficiency. Larger projects usually require bigger graders, while smaller projects benefit from more maneuverable machines. Keep in mind that larger, heavier graders also use more fuel and require adequate transportation and storage capabilities.
Read More
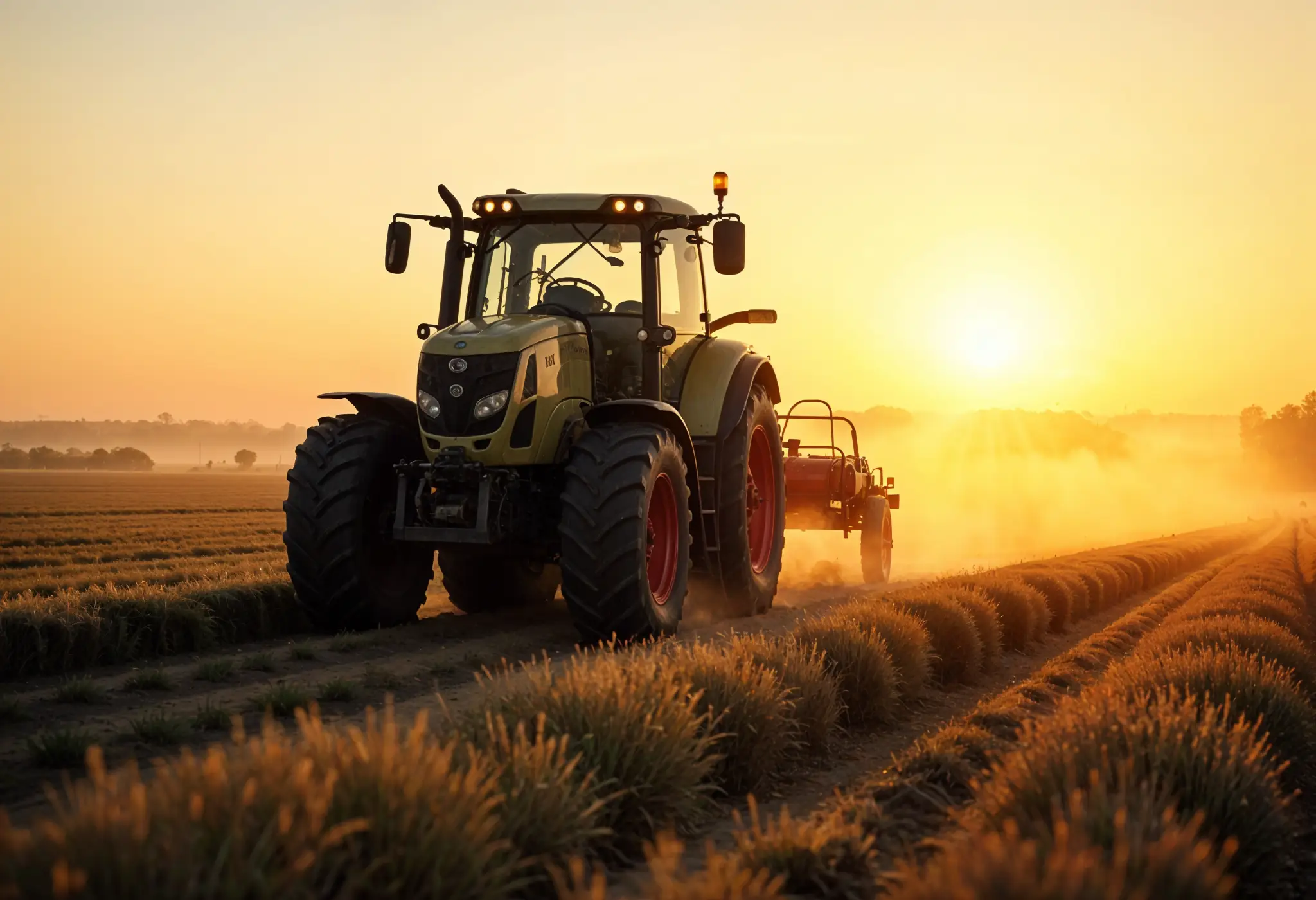
Top Hydraulic Components for Agricultural Equipment in 2025: Complete Guide
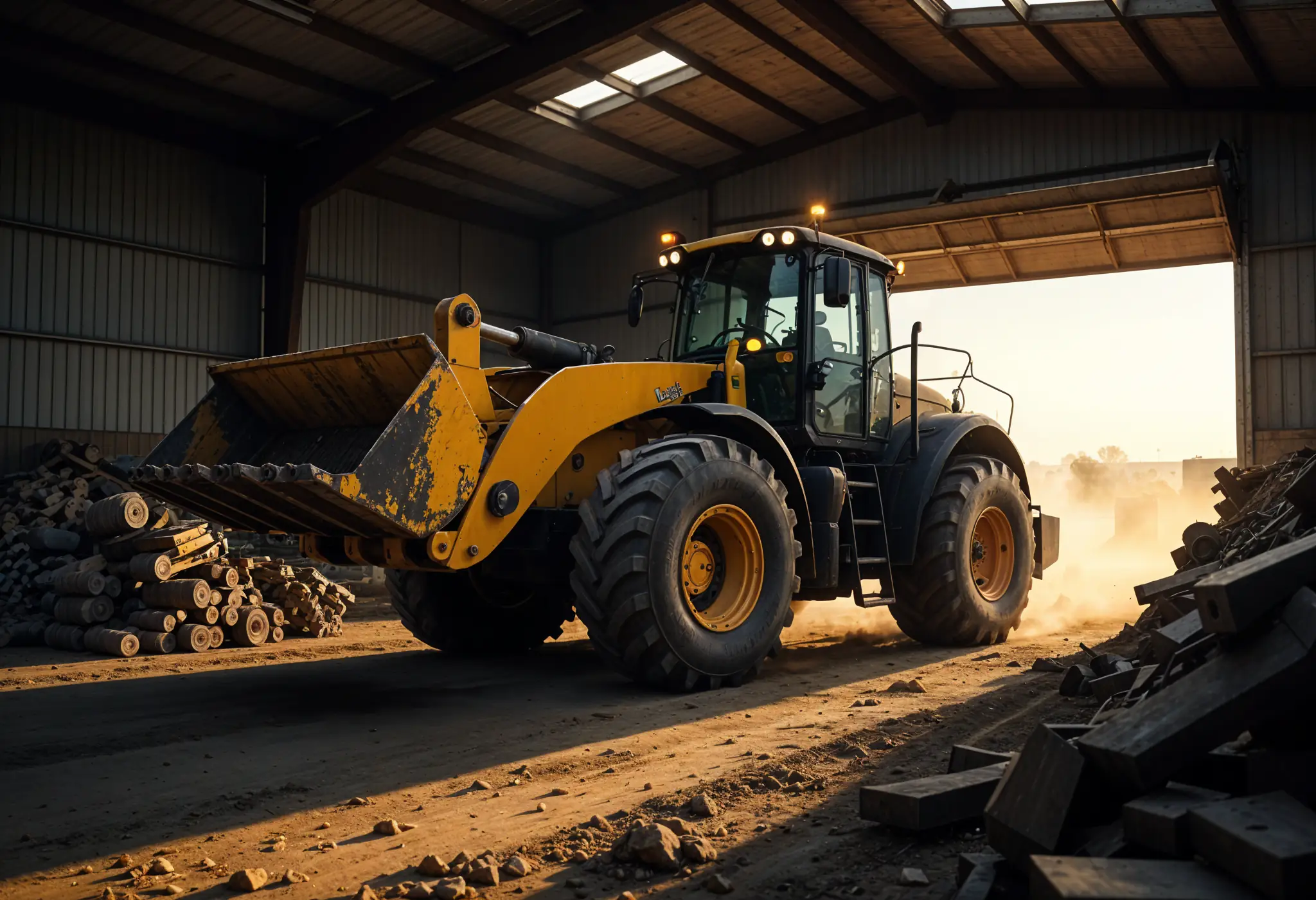
The Essential Farm Equipment Parts You Can't Afford to Run Out Of
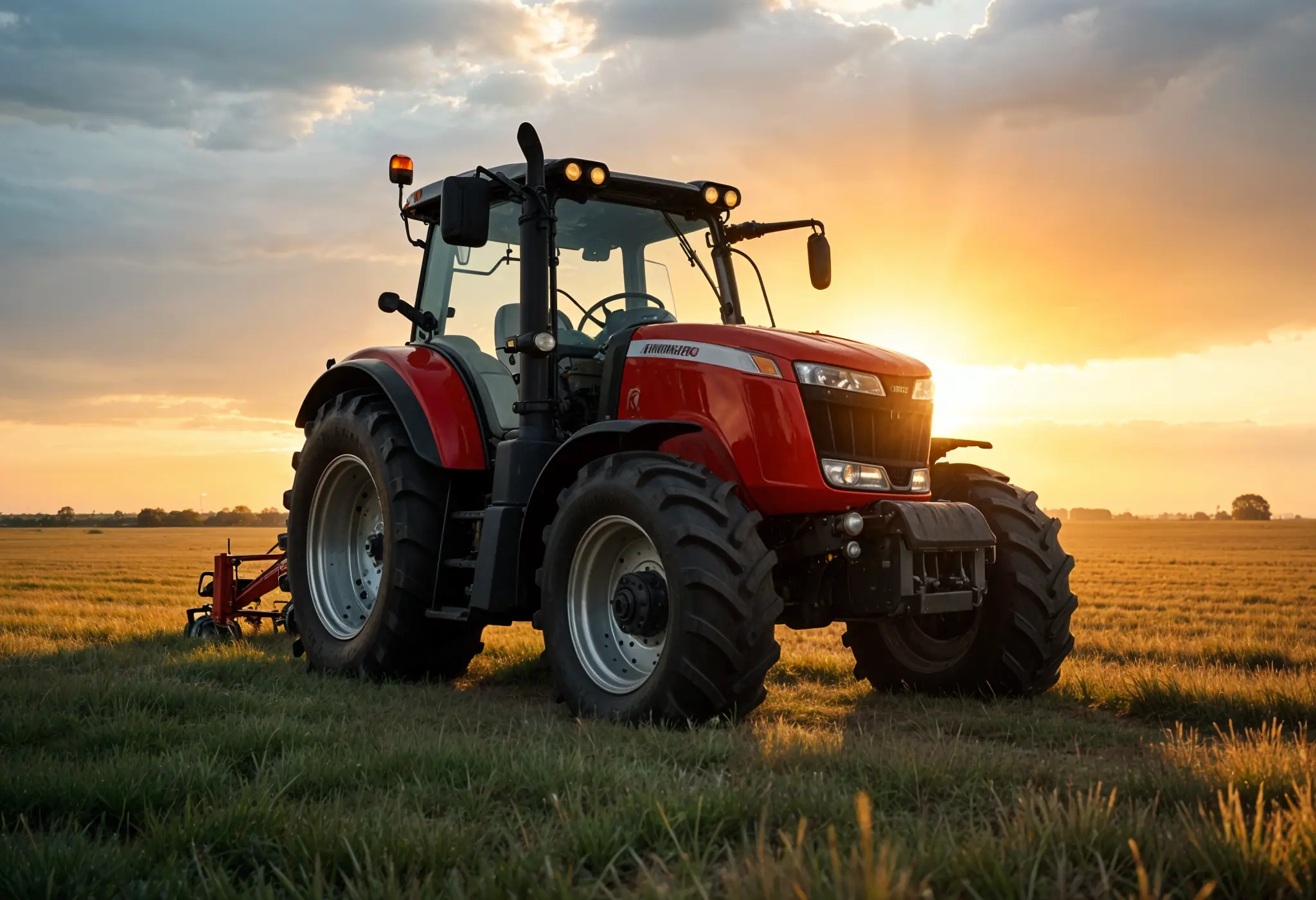
How to Service Farm Equipment: A Farmer's Guide to Zero Harvest Downtime
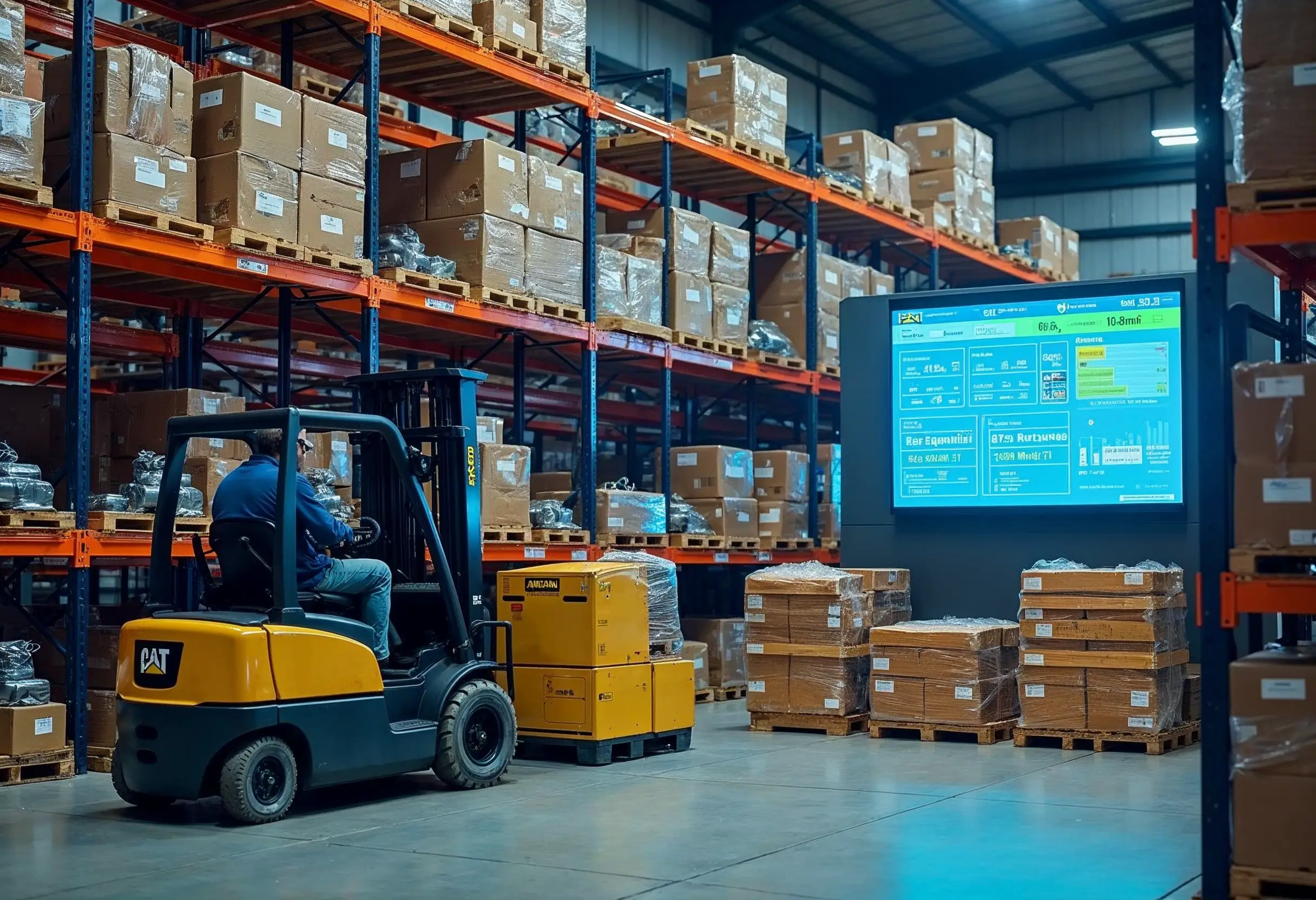
Construction Machinery Parts Suppliers: Expert Selection Guide
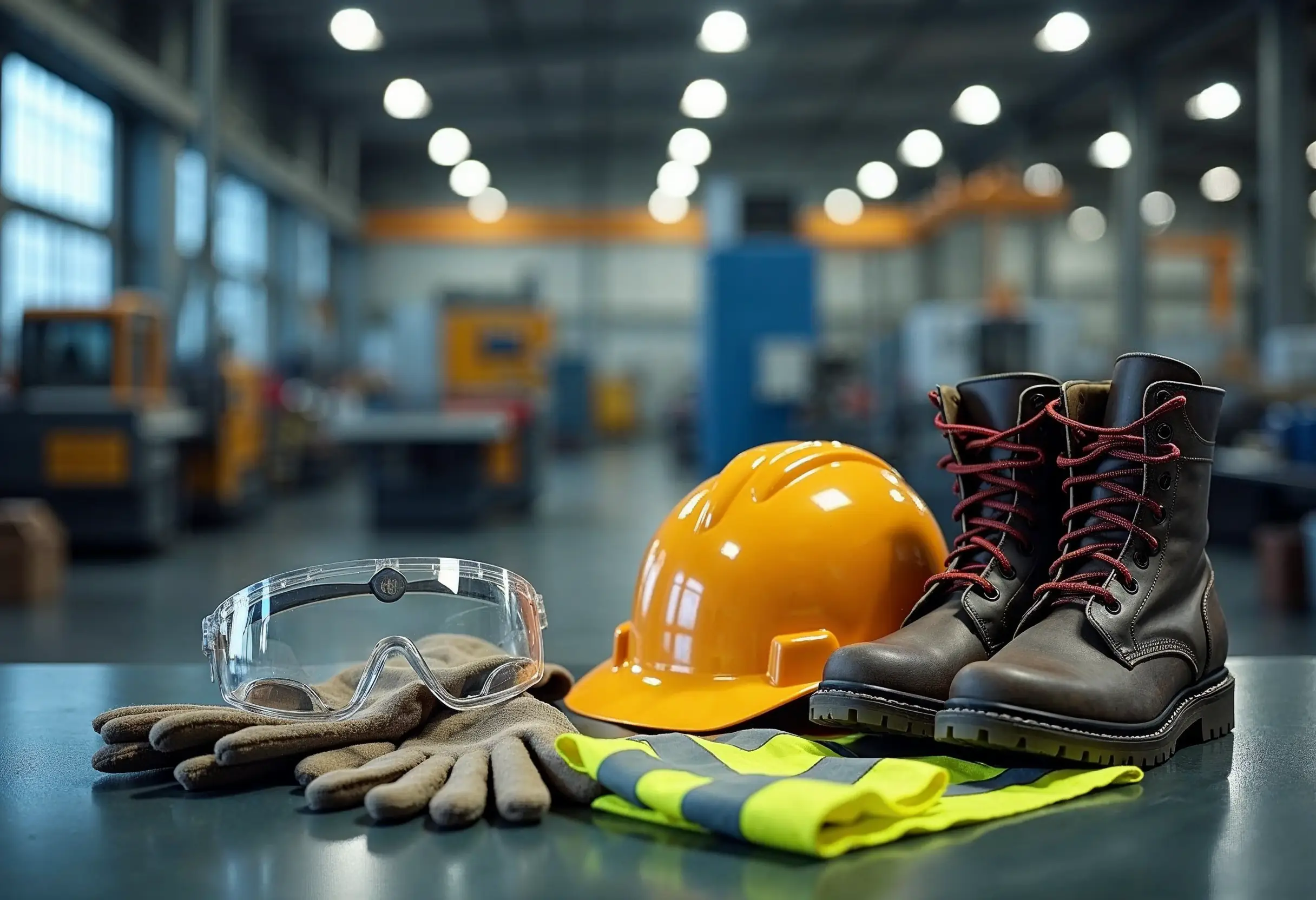
How to Apply Machine Safety Rules: From Selection to Installation
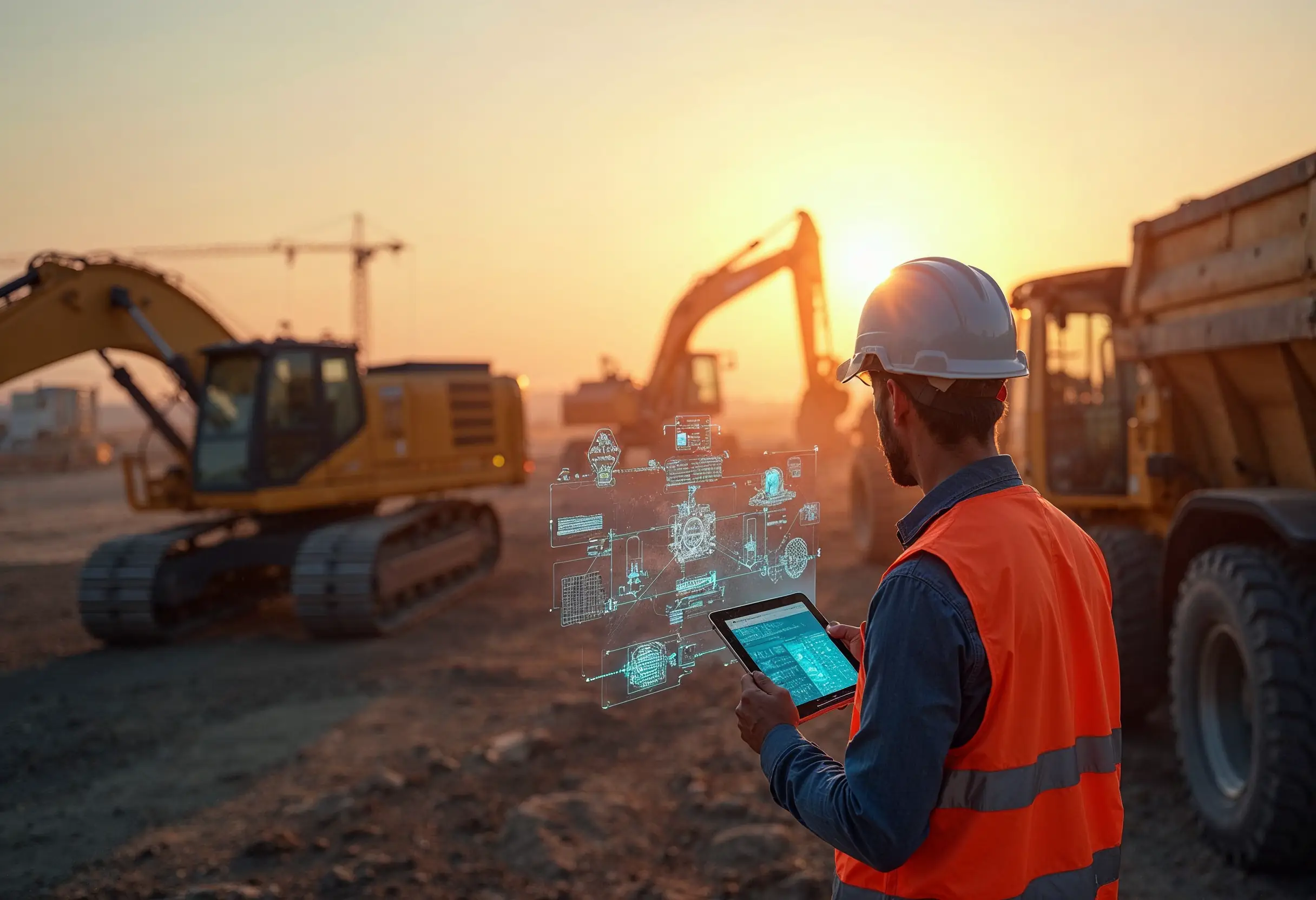
Smart Diagnostics Cut Heavy Equipment Failures by 73%
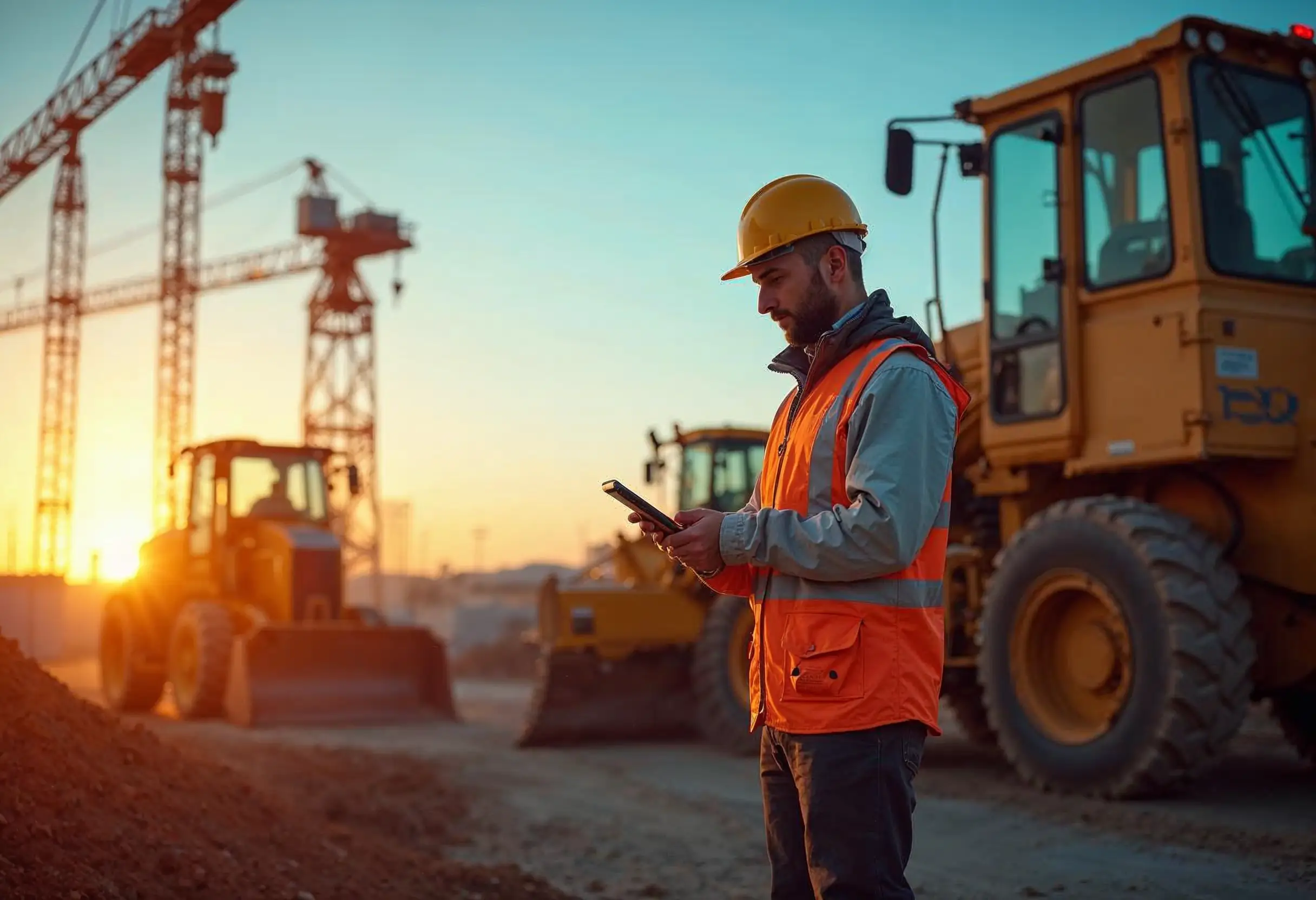
5 Ways to Assess the Environmental Impact of Heavy Construction Machinery
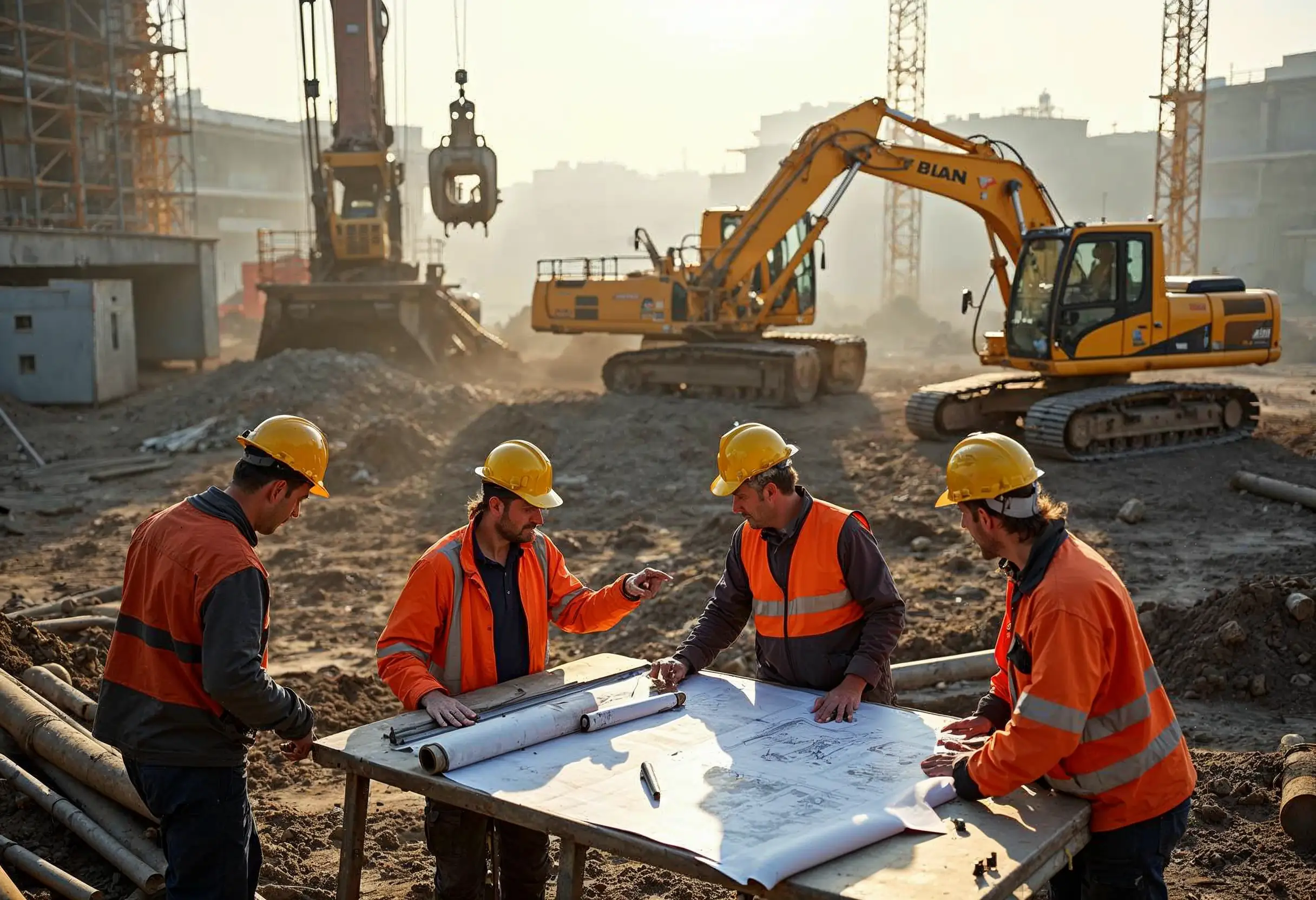
10 Smart Ways to Pick Construction Machinery for 2025 Projects
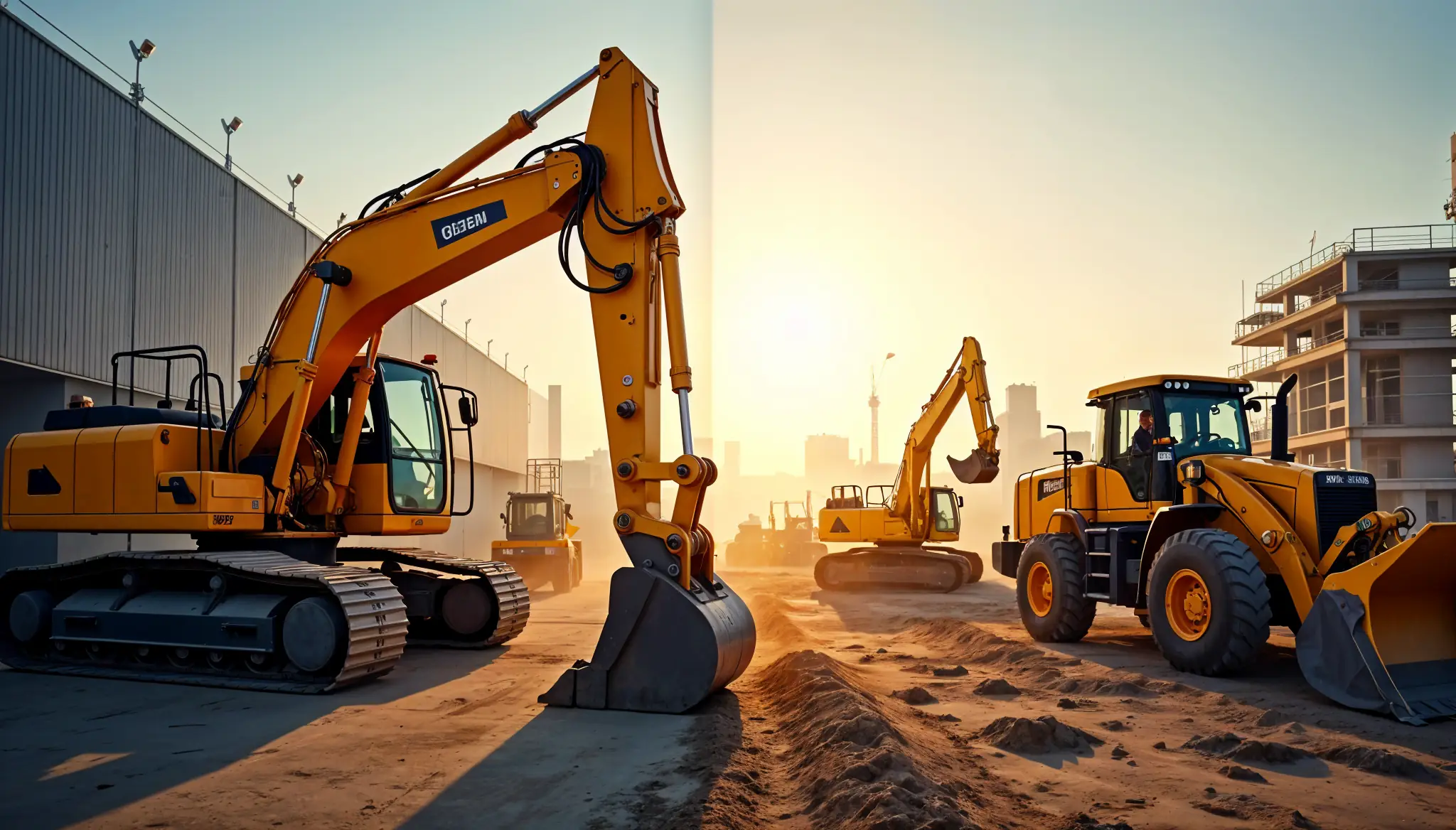
Rent vs Purchase Equipment: What Heavy Industry Experts Hide
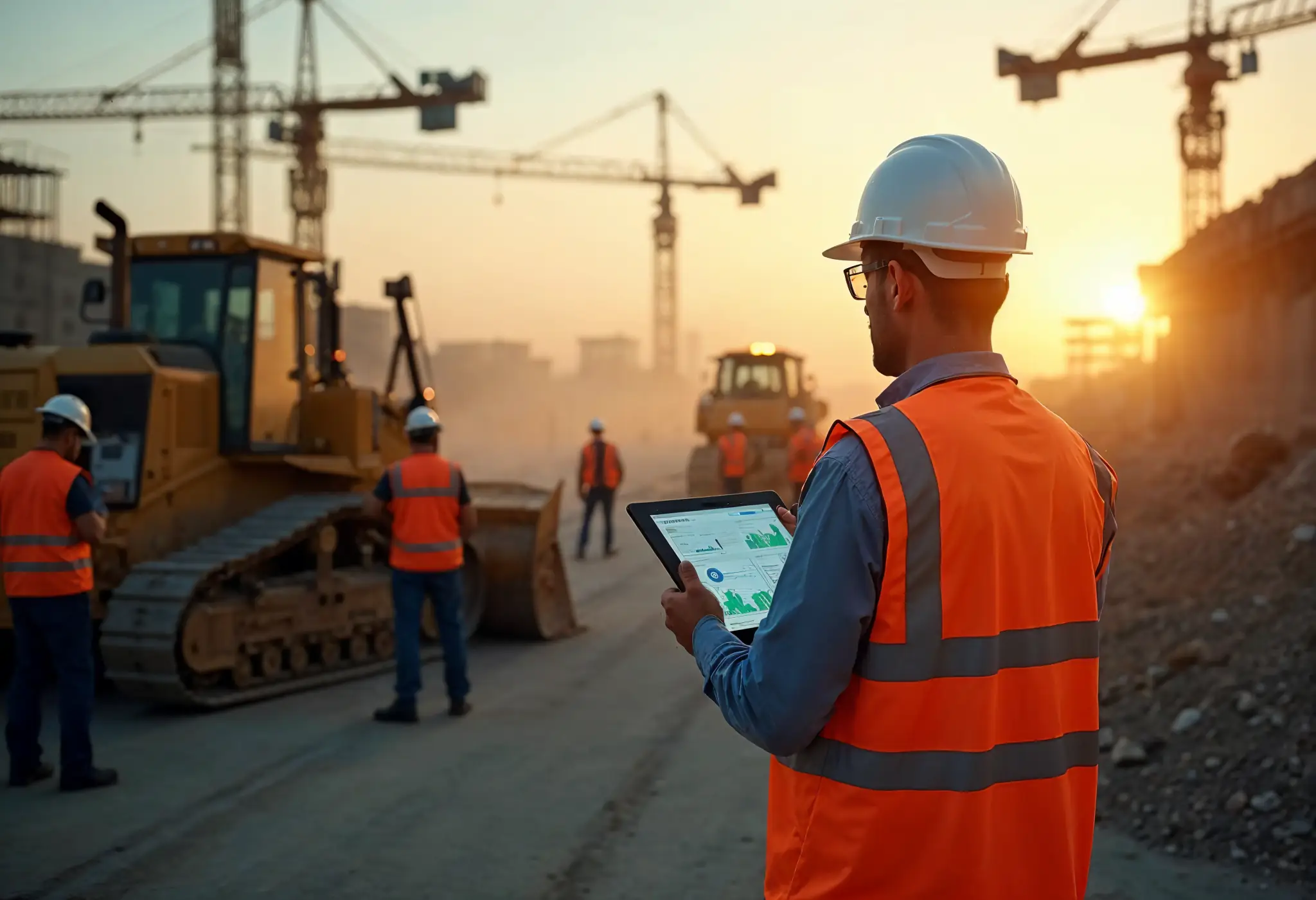
How to Implement a Construction Inventory Management System for Equipment Efficiency
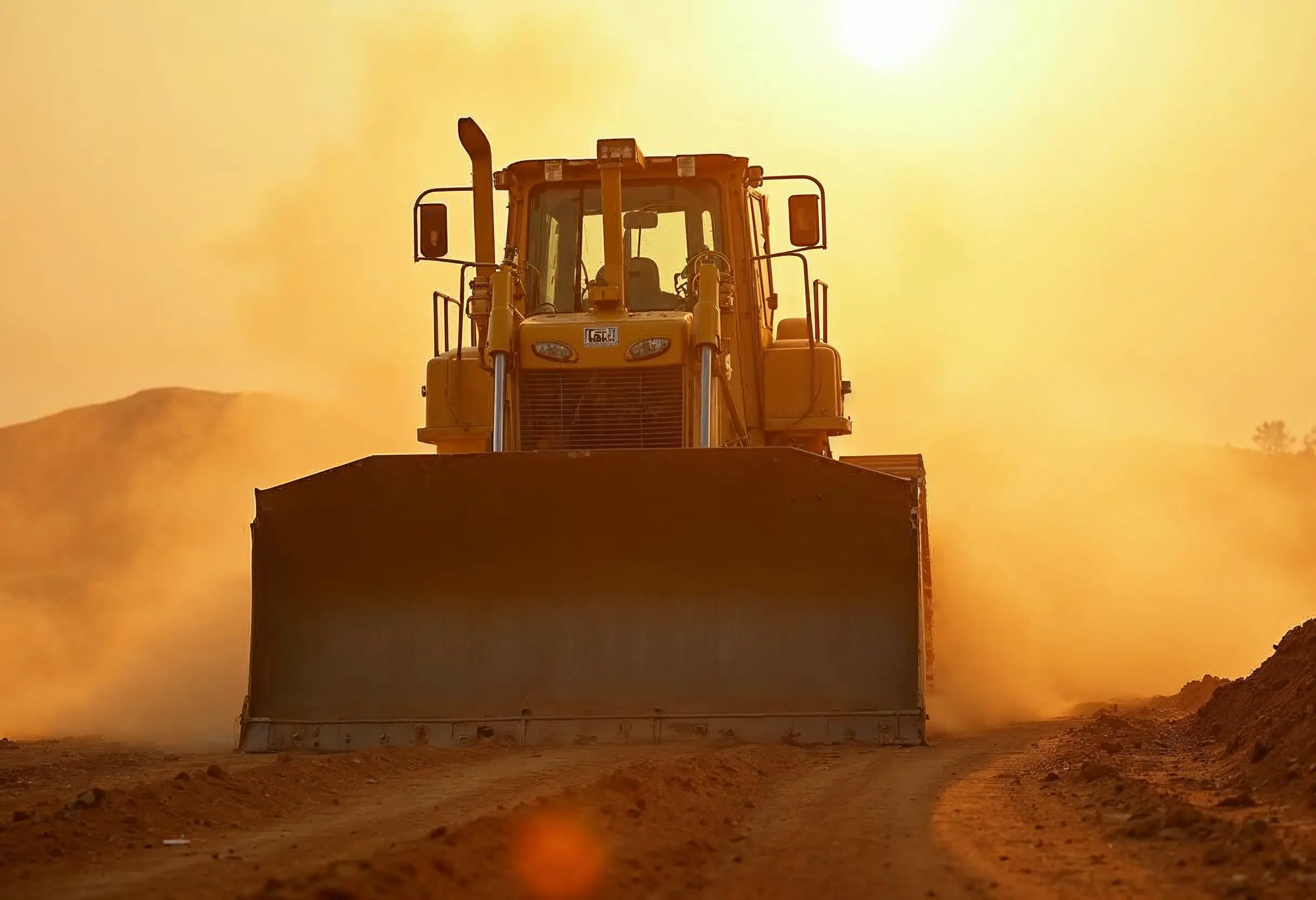
How to Extend Equipment Life Expectancy with Regular Maintenance
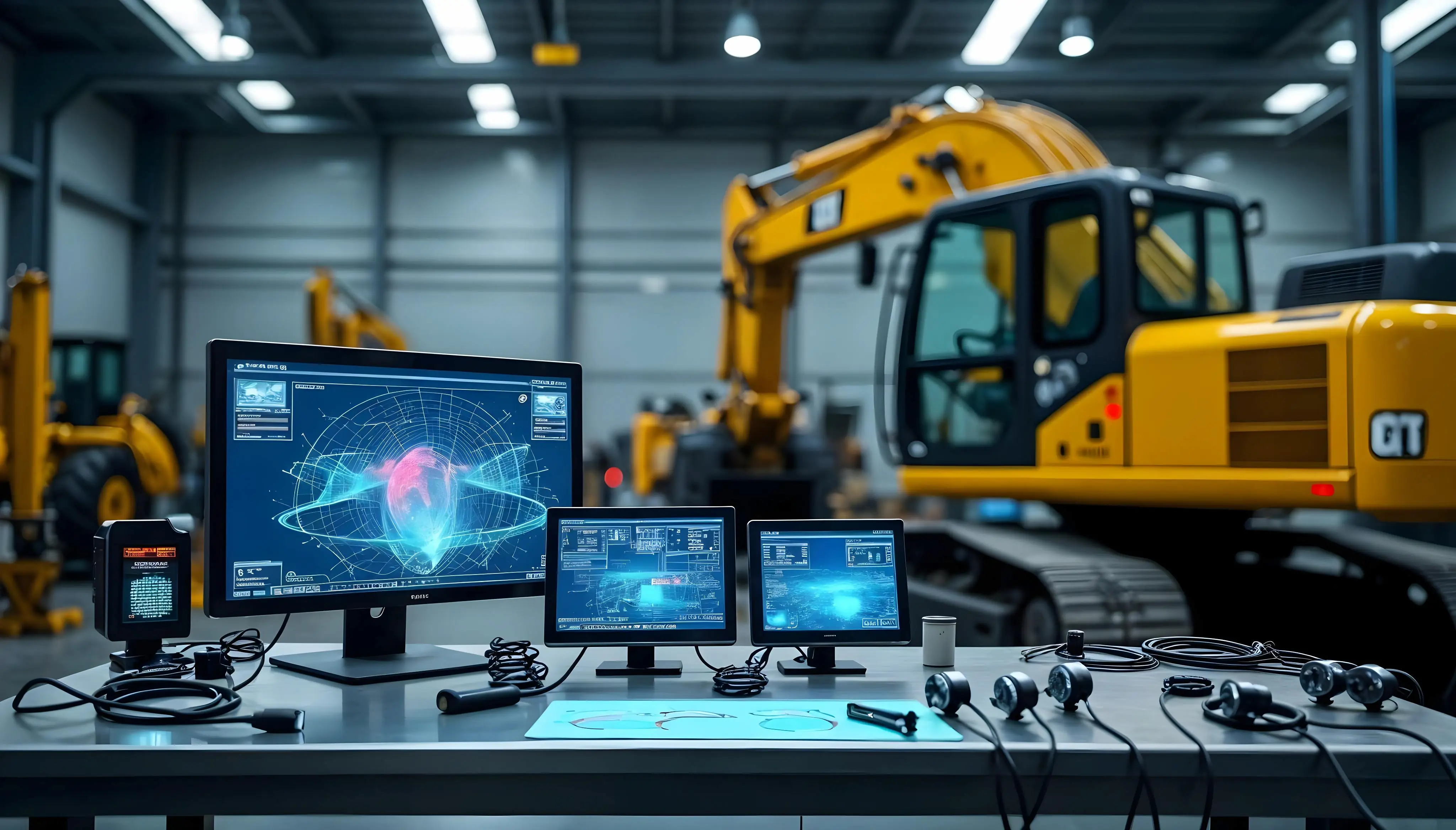
Advanced Heavy Equipment Diagnostic Tools: Ensuring Construction Machinery Quality
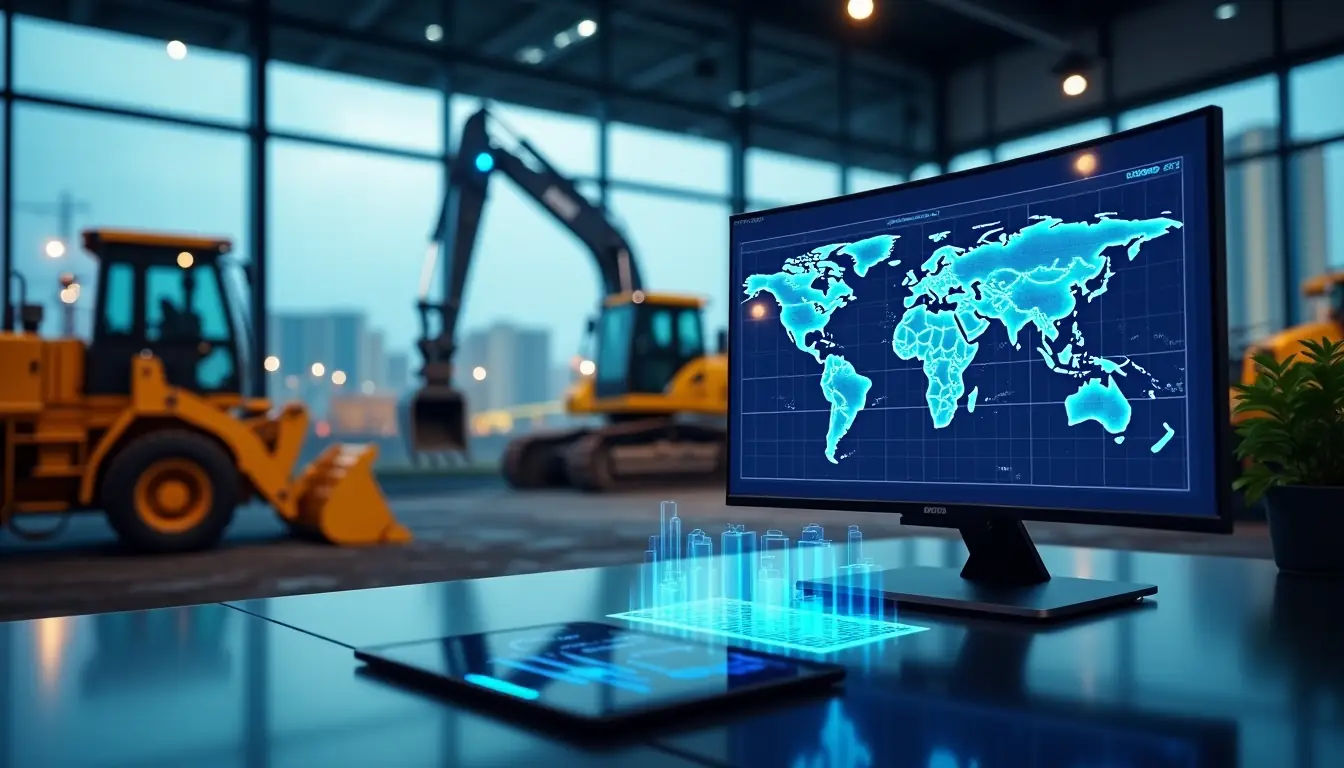
Essential Features Your Construction Equipment Inventory System Needs
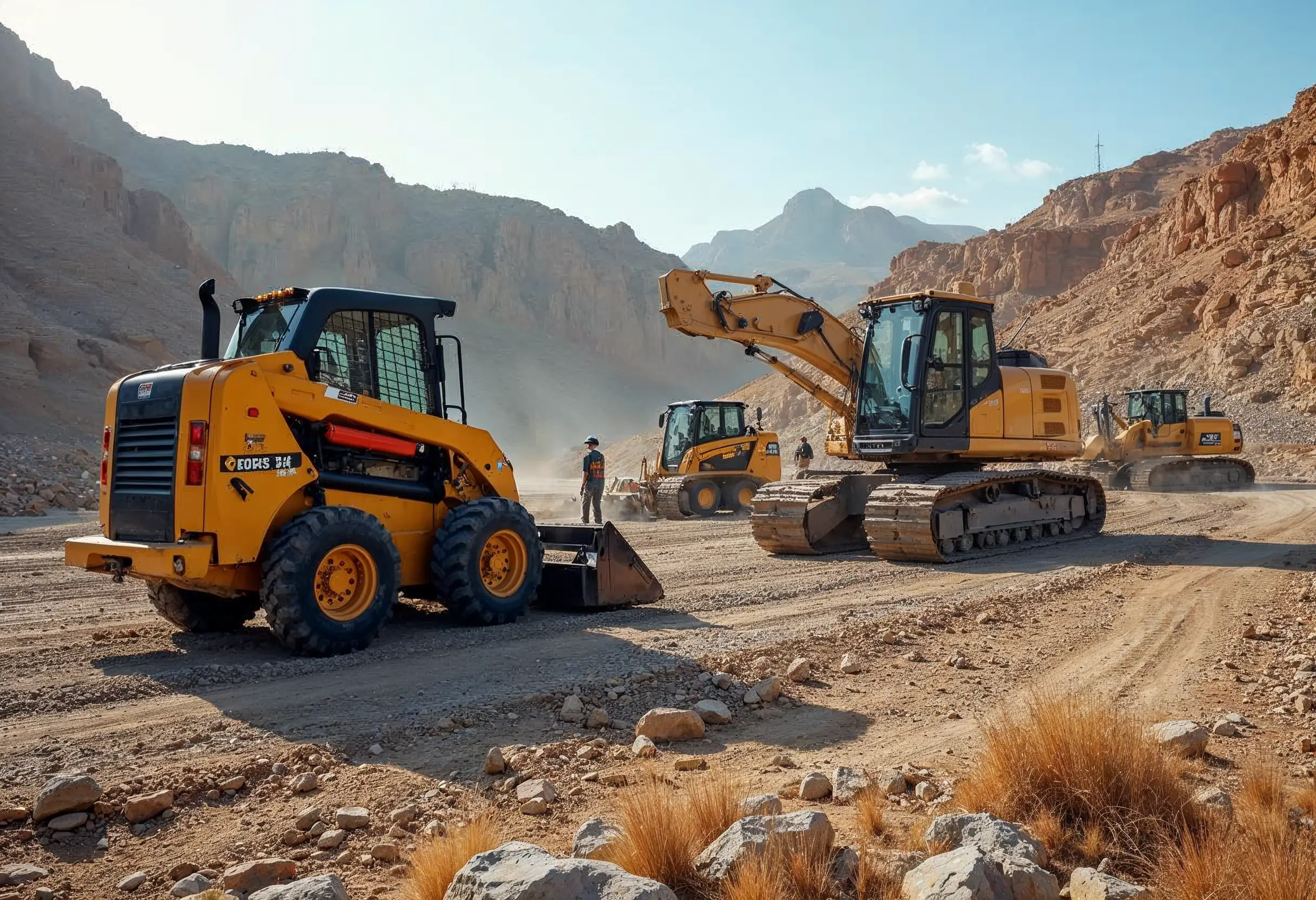
29 Quick Tips for Choosing Construction Equipment for Remote Locations
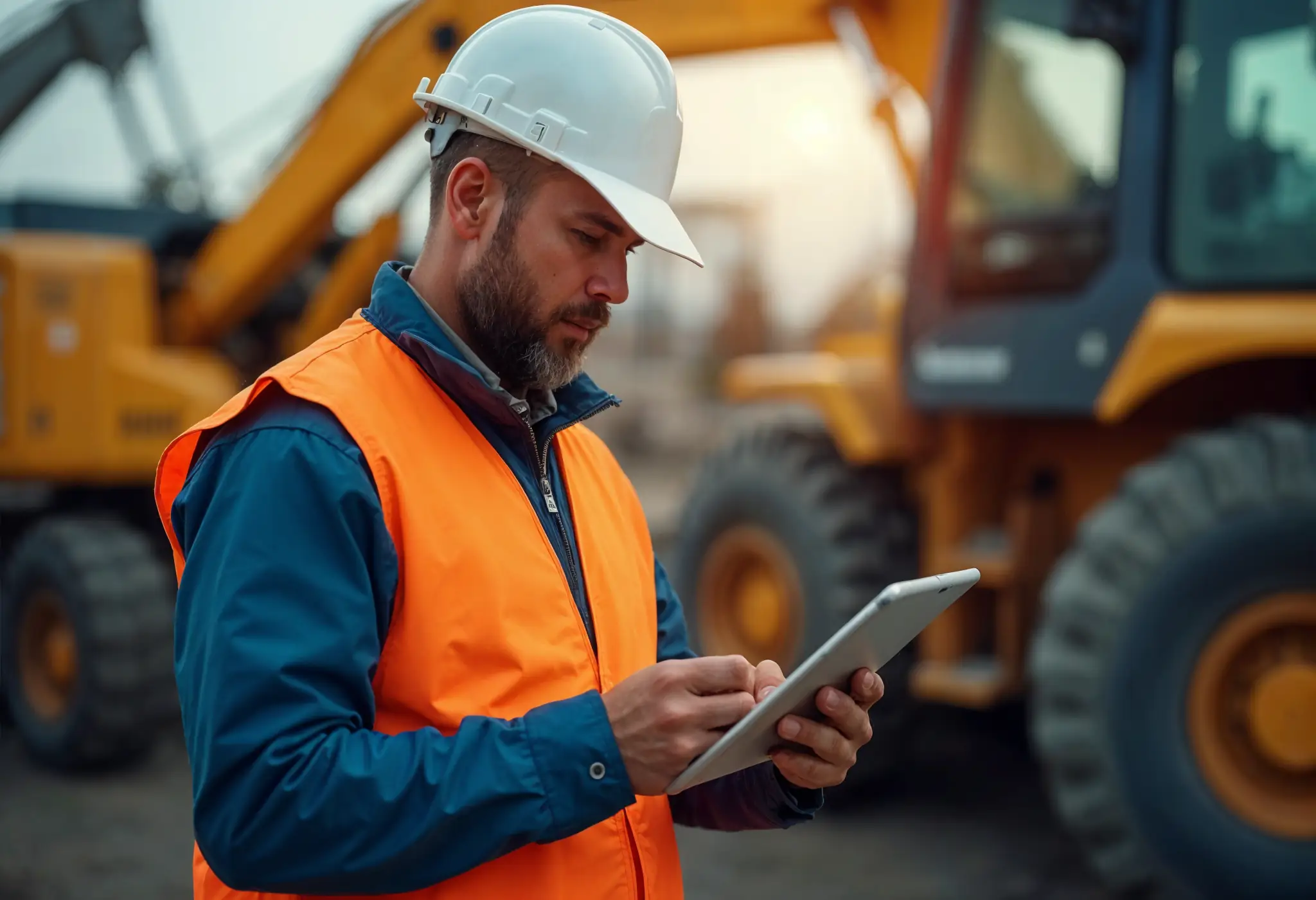
How to Select Construction Machinery with Optimal Equipment Maintenance in Mind
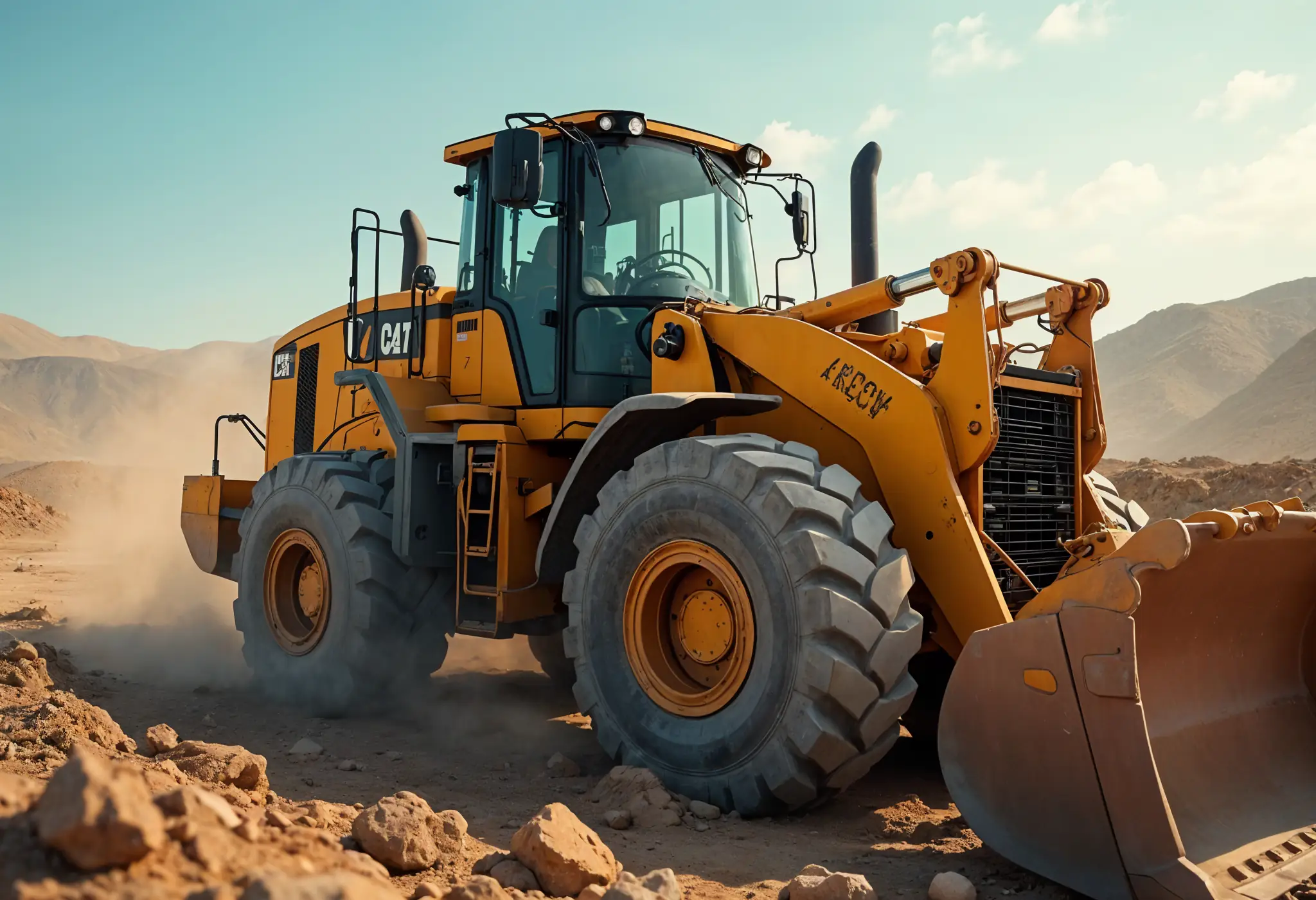
Top 25 Tips for Selecting Bulldozers for Construction Sites
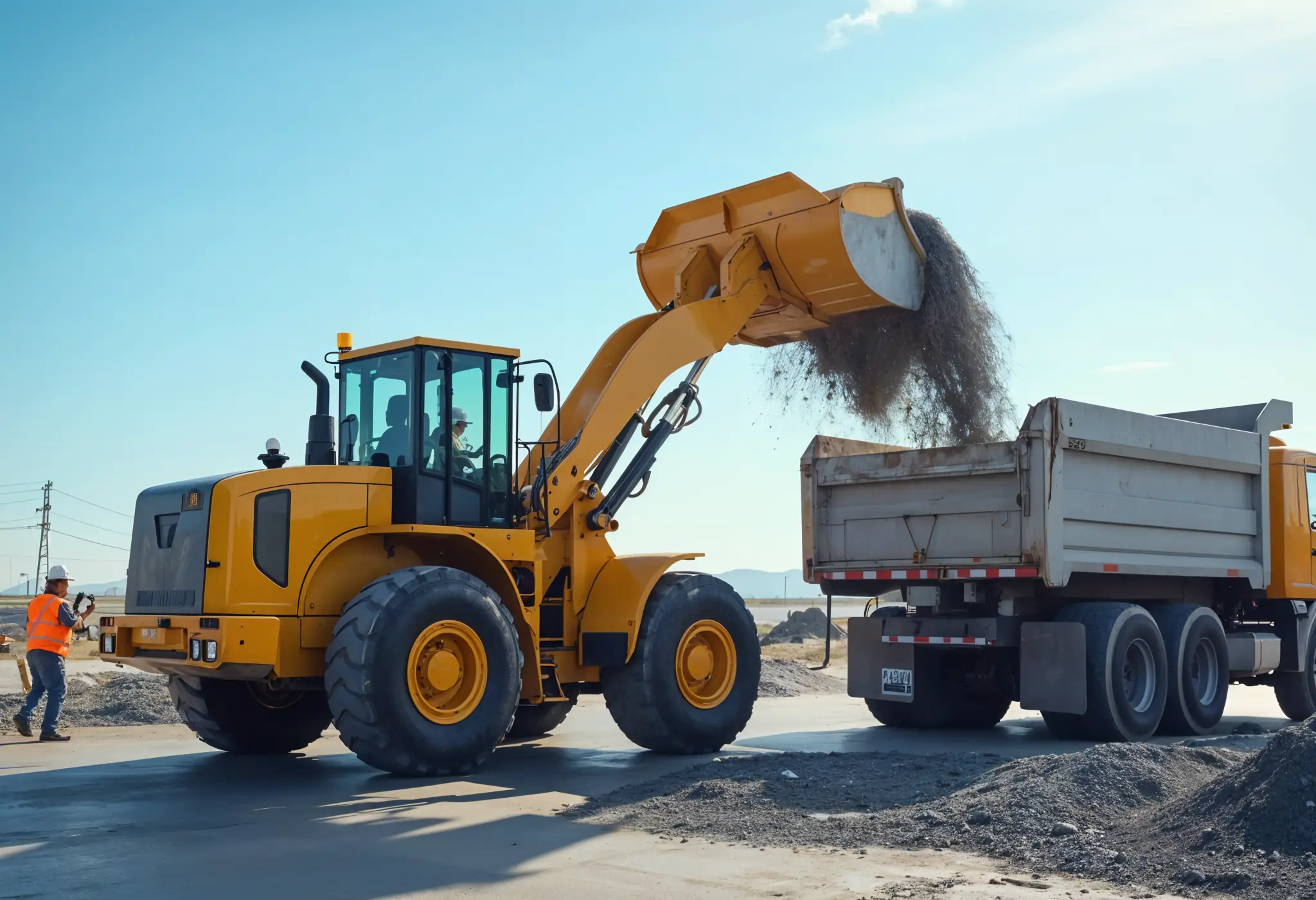
Which Construction Loader is Best for Your Project Needs?
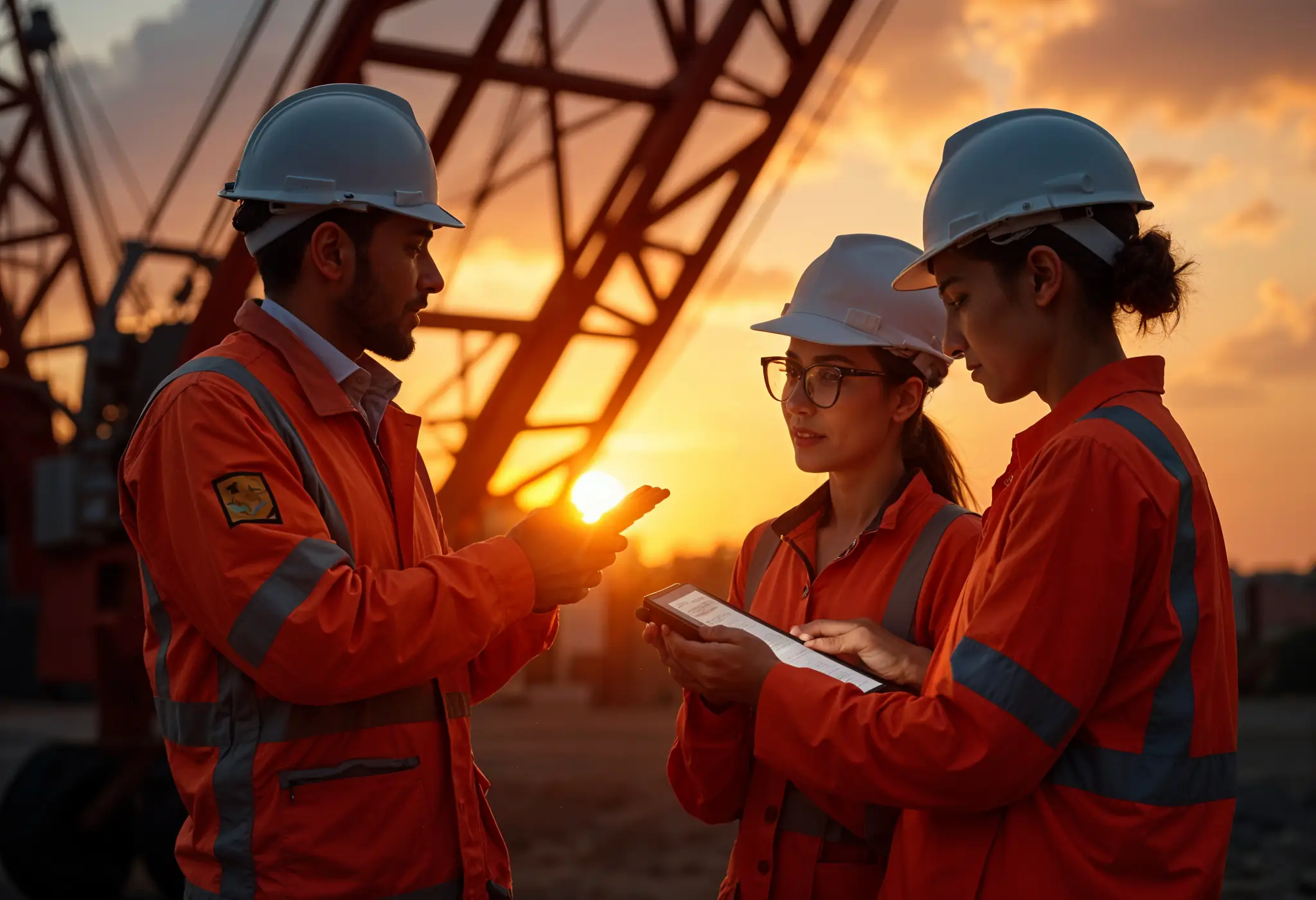
4 Key Steps to Form a Construction Machinery QC Team
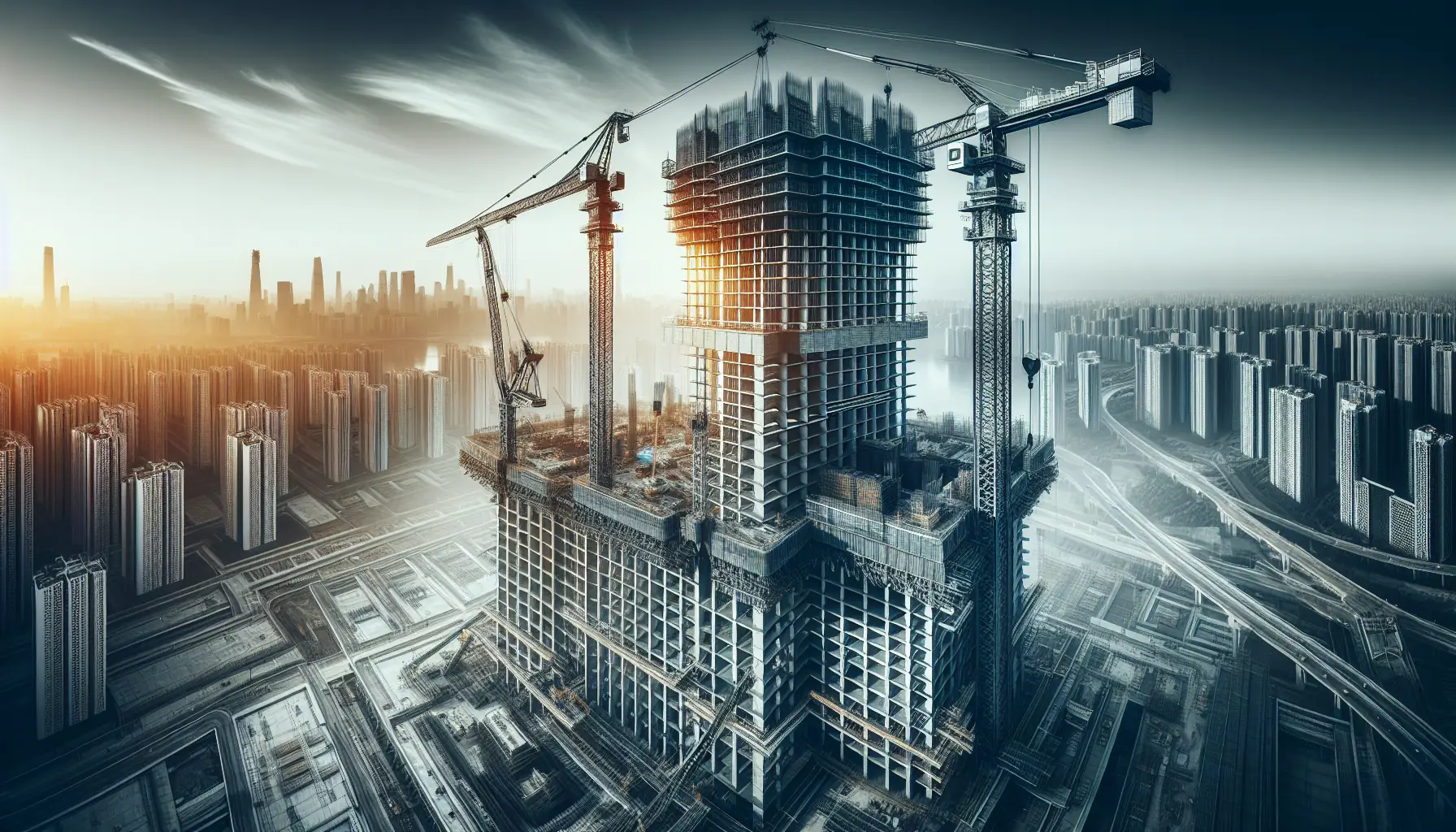
15 Essential Tips for Selecting the Perfect Crane for Construction
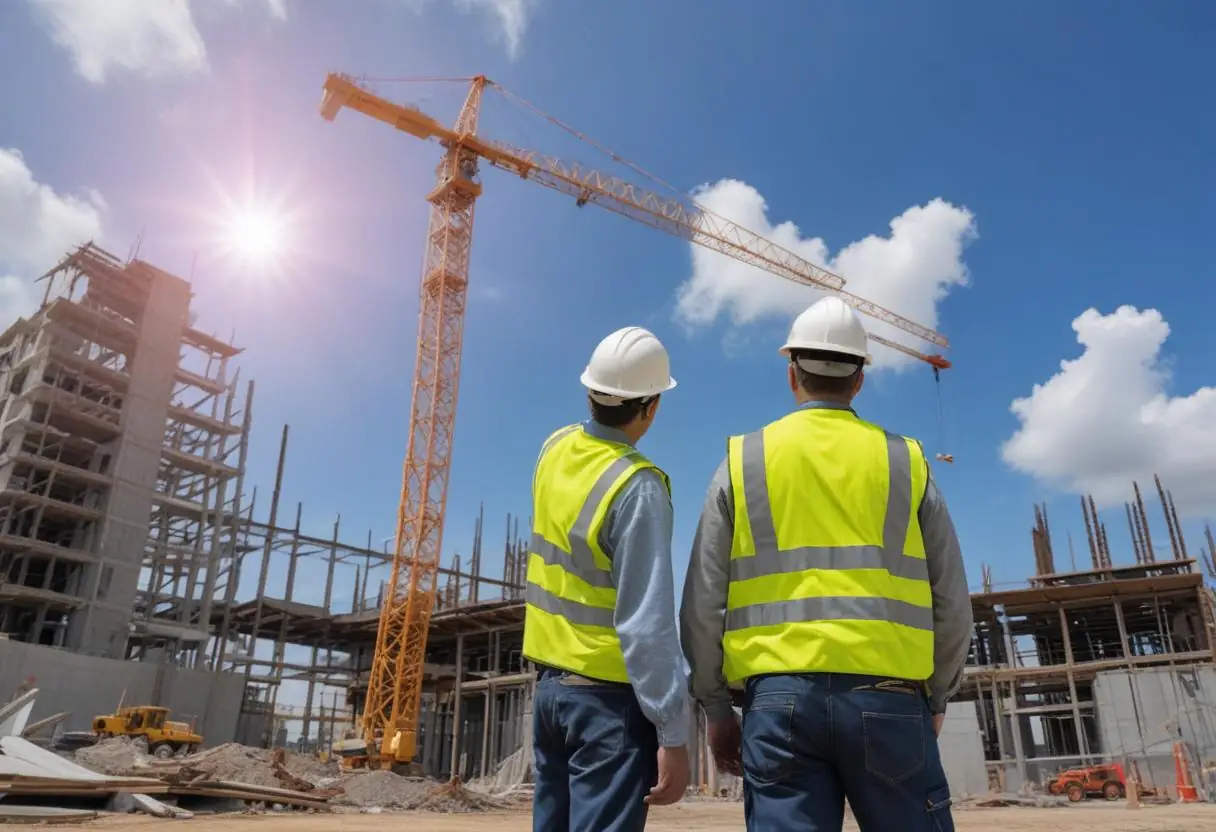
Maximize Savings: Multi-Purpose Construction Machinery for Lower Costs
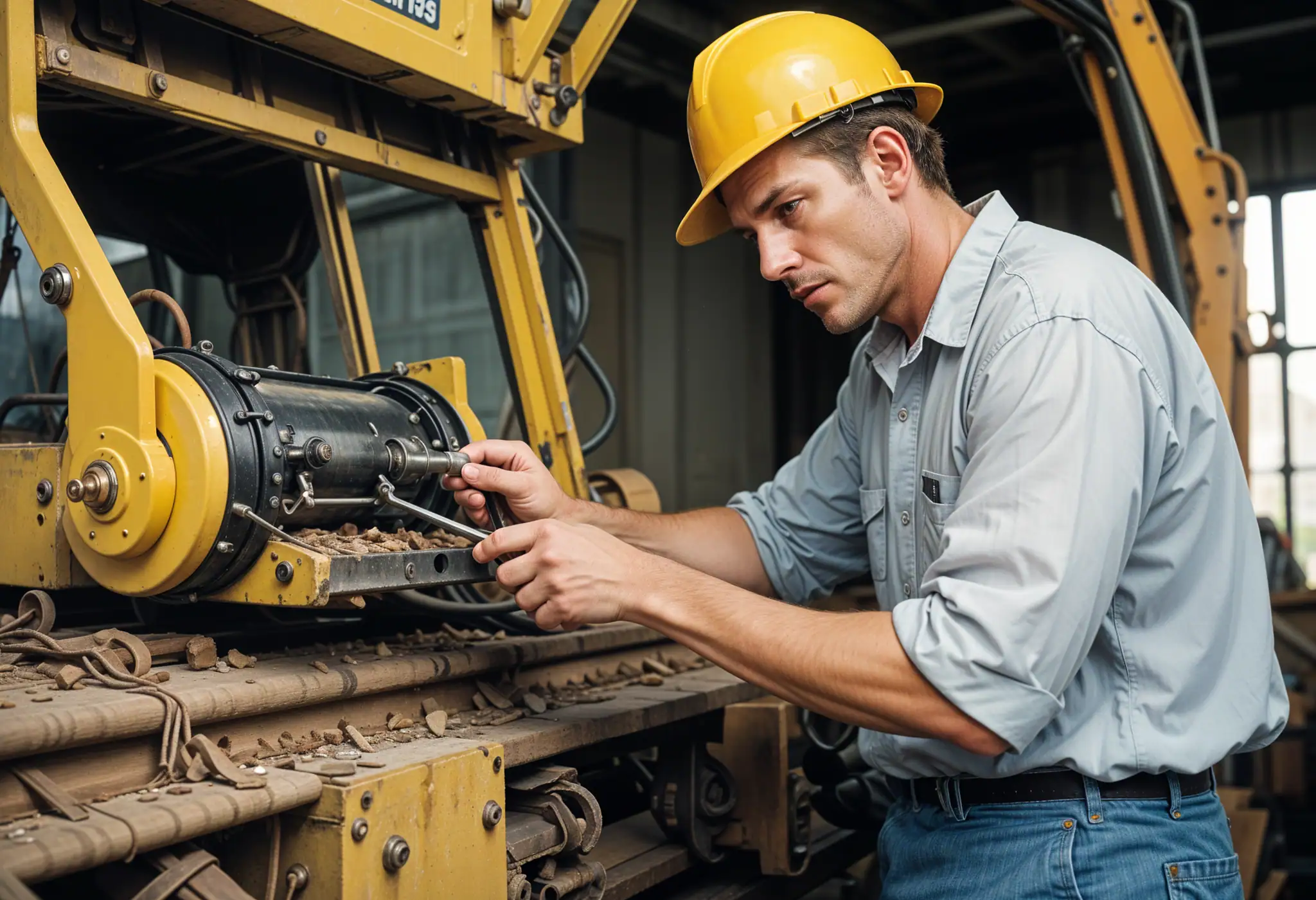
Affordable Heavy Equipment Parts: A Sourcing Guide
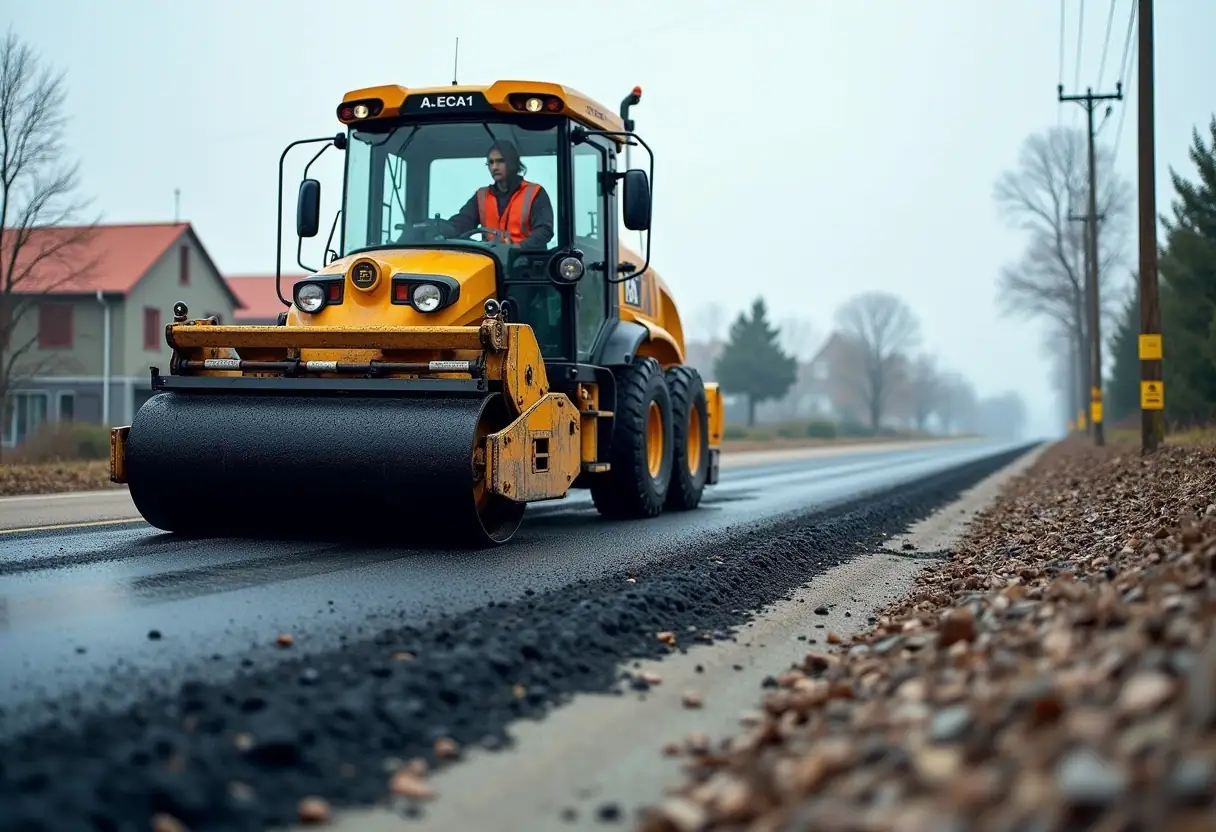
Choosing the Right Road Construction Equipment: A Complete Guide
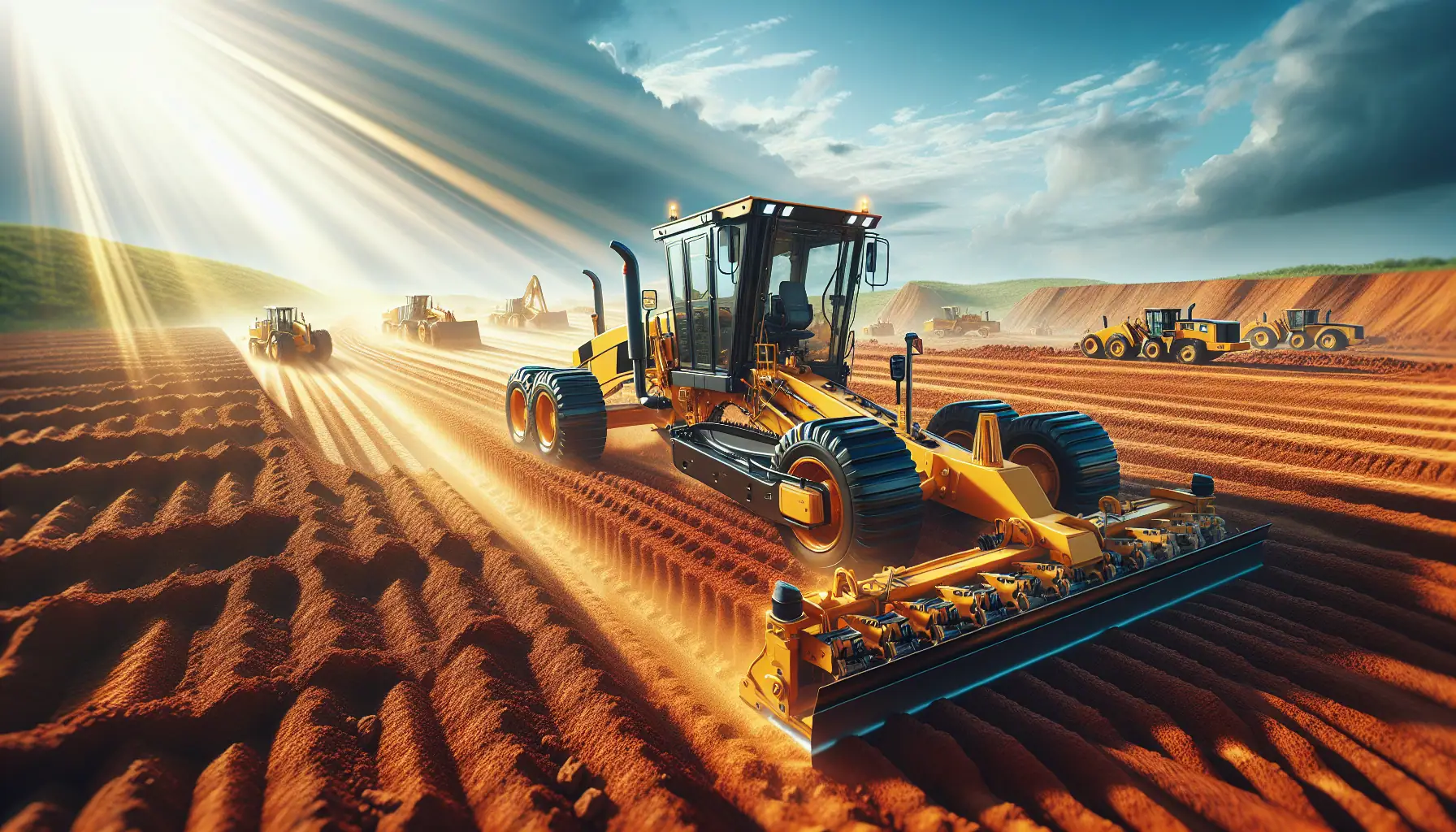
Motor Graders: Key Elements to Consider for Optimal Selection
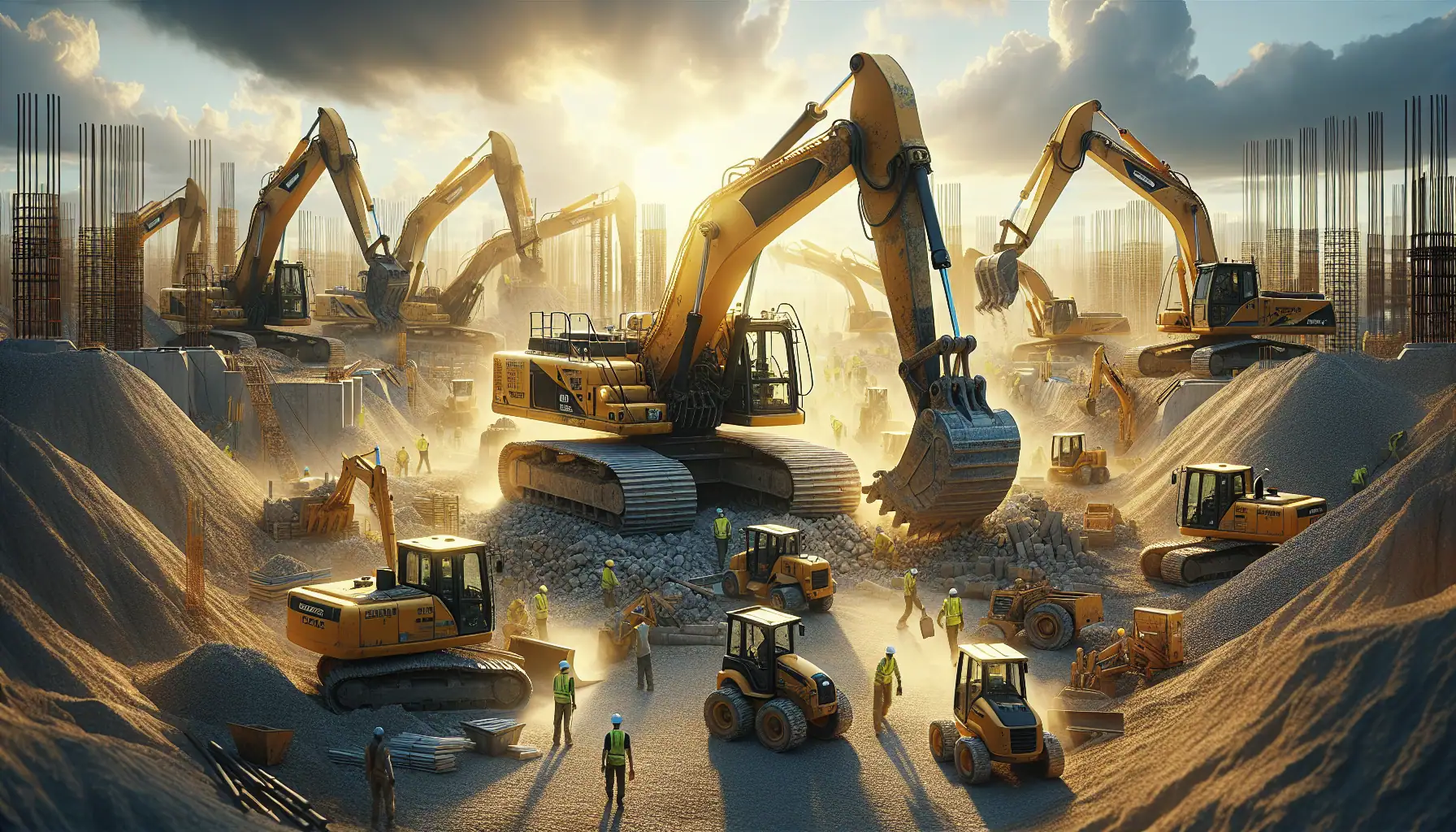
A Detailed Guide to Choosing Excavators for Construction Work
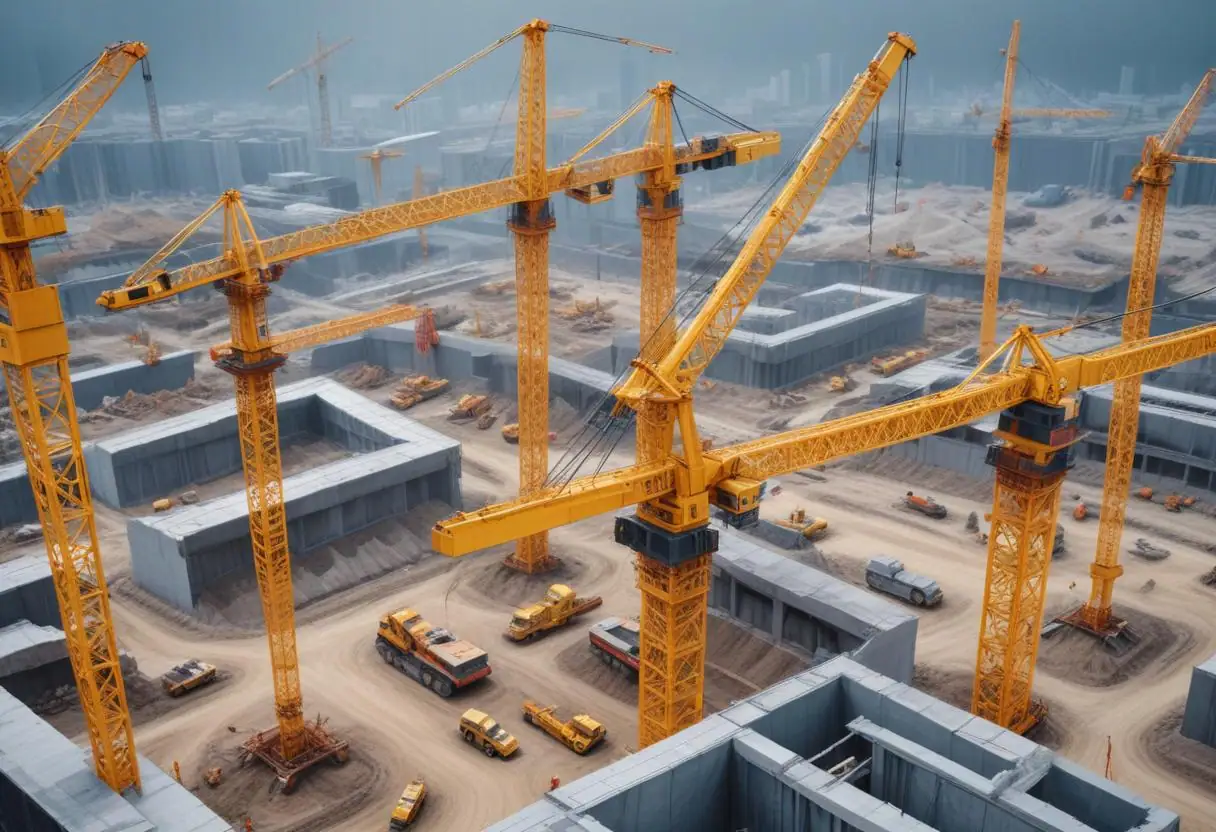
Top Tips for Choosing Cranes for Construction Projects
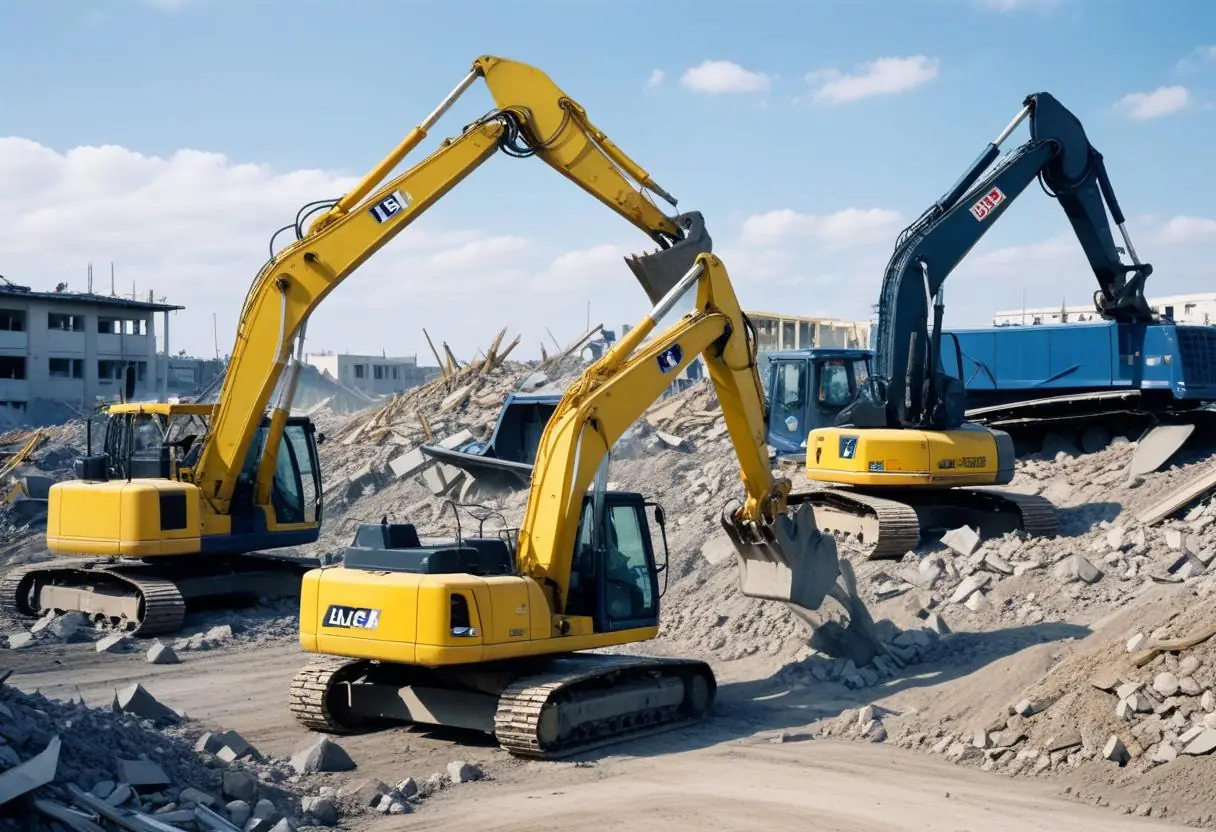
5 Top-Rated Demolition Machines for Construction Professionals
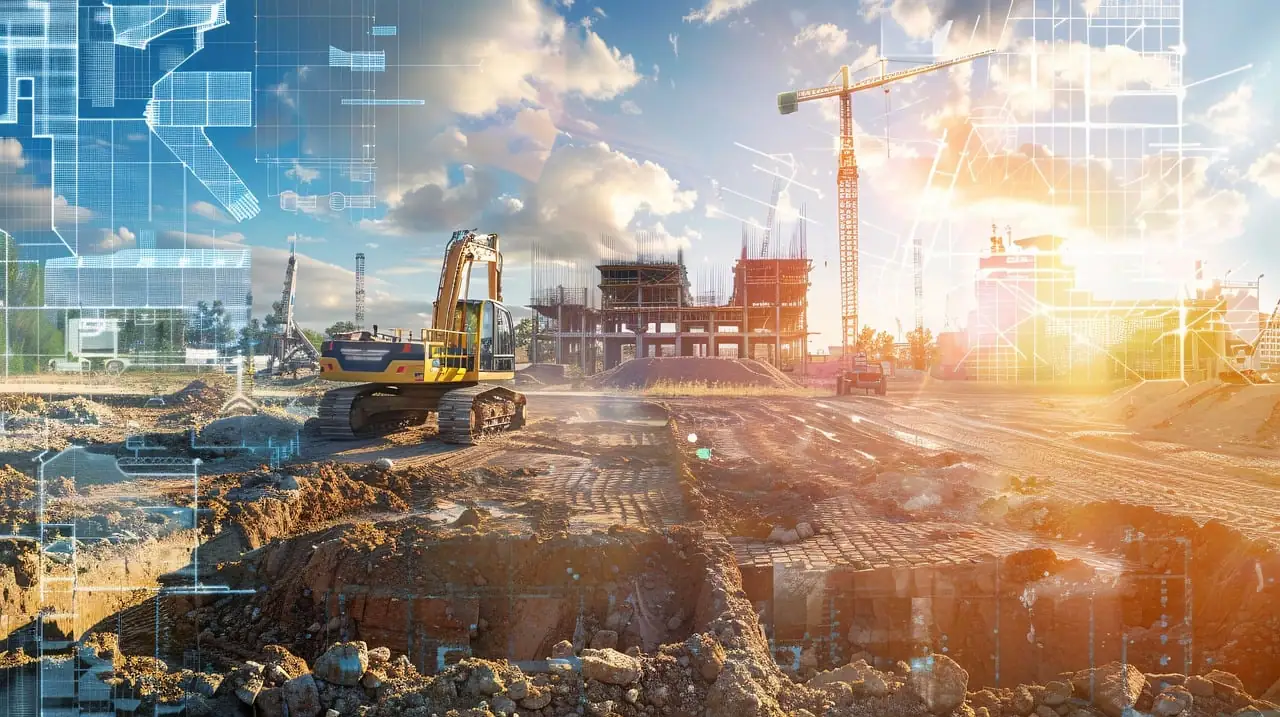
Expert Tips on Choosing Earthmoving Equipment for Large Projects
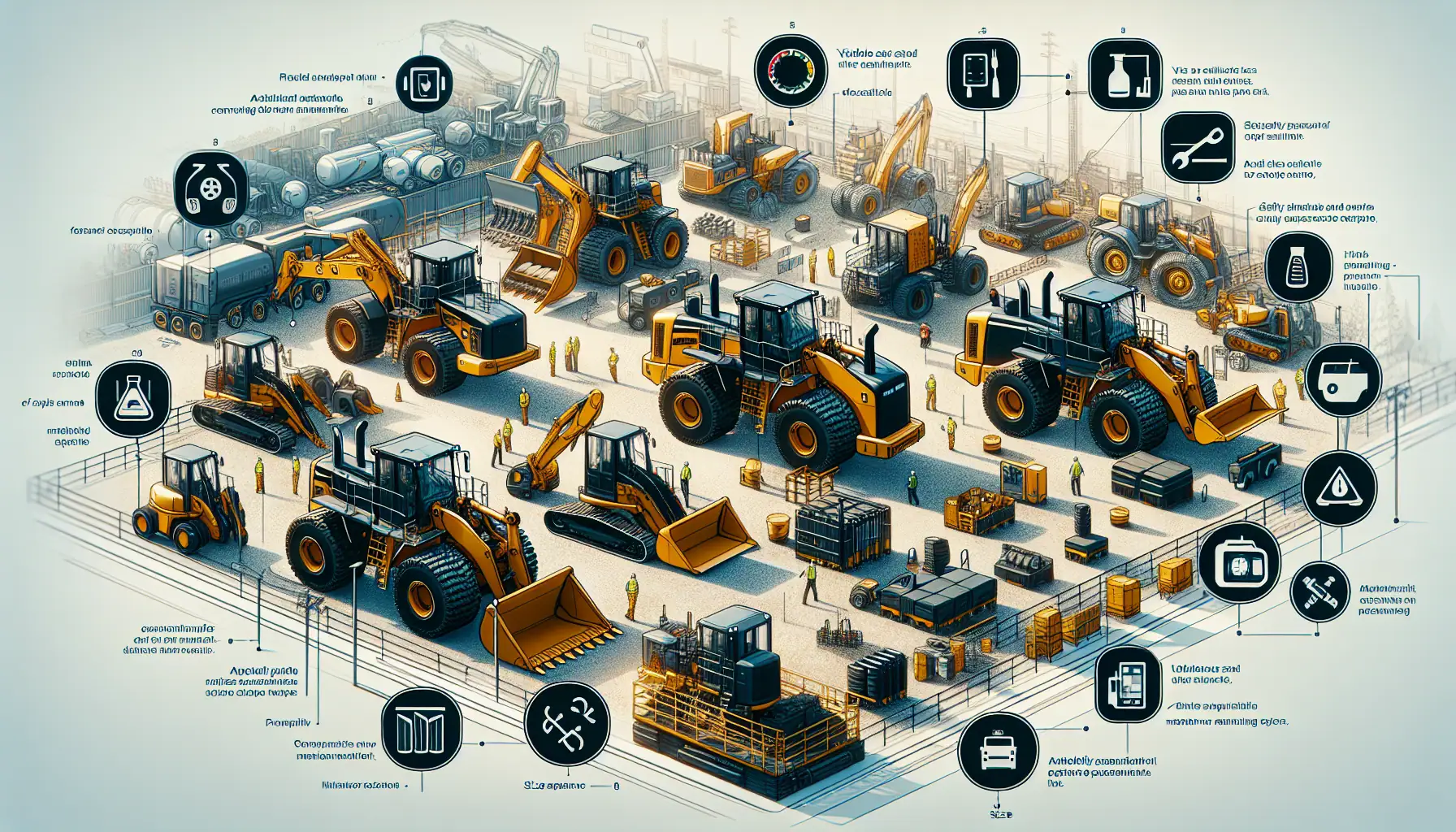
Top Functional Criteria for Selecting Heavy Construction Equipment
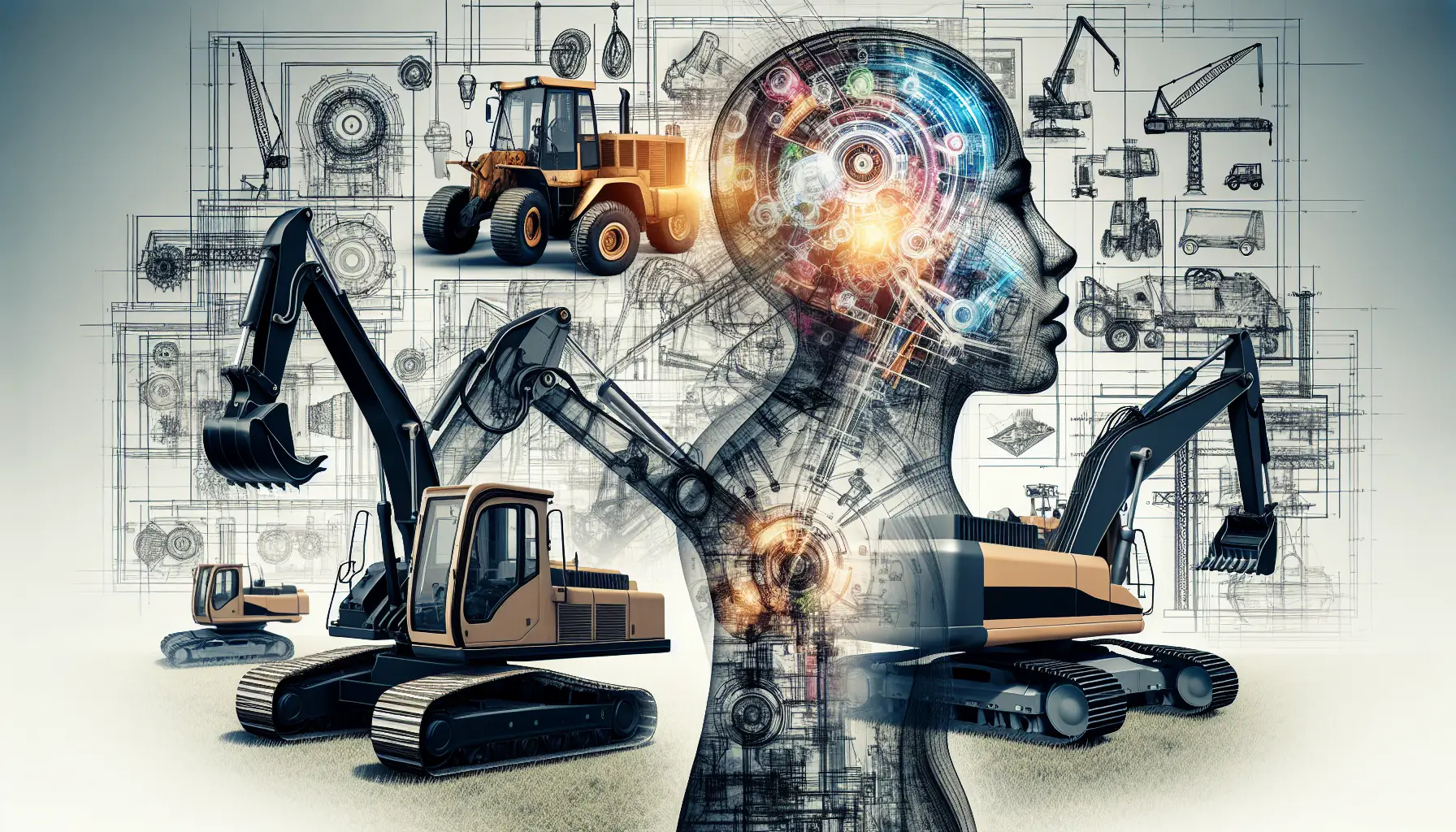
Construction Machinery: Detailed Guide to Equipment Specifications
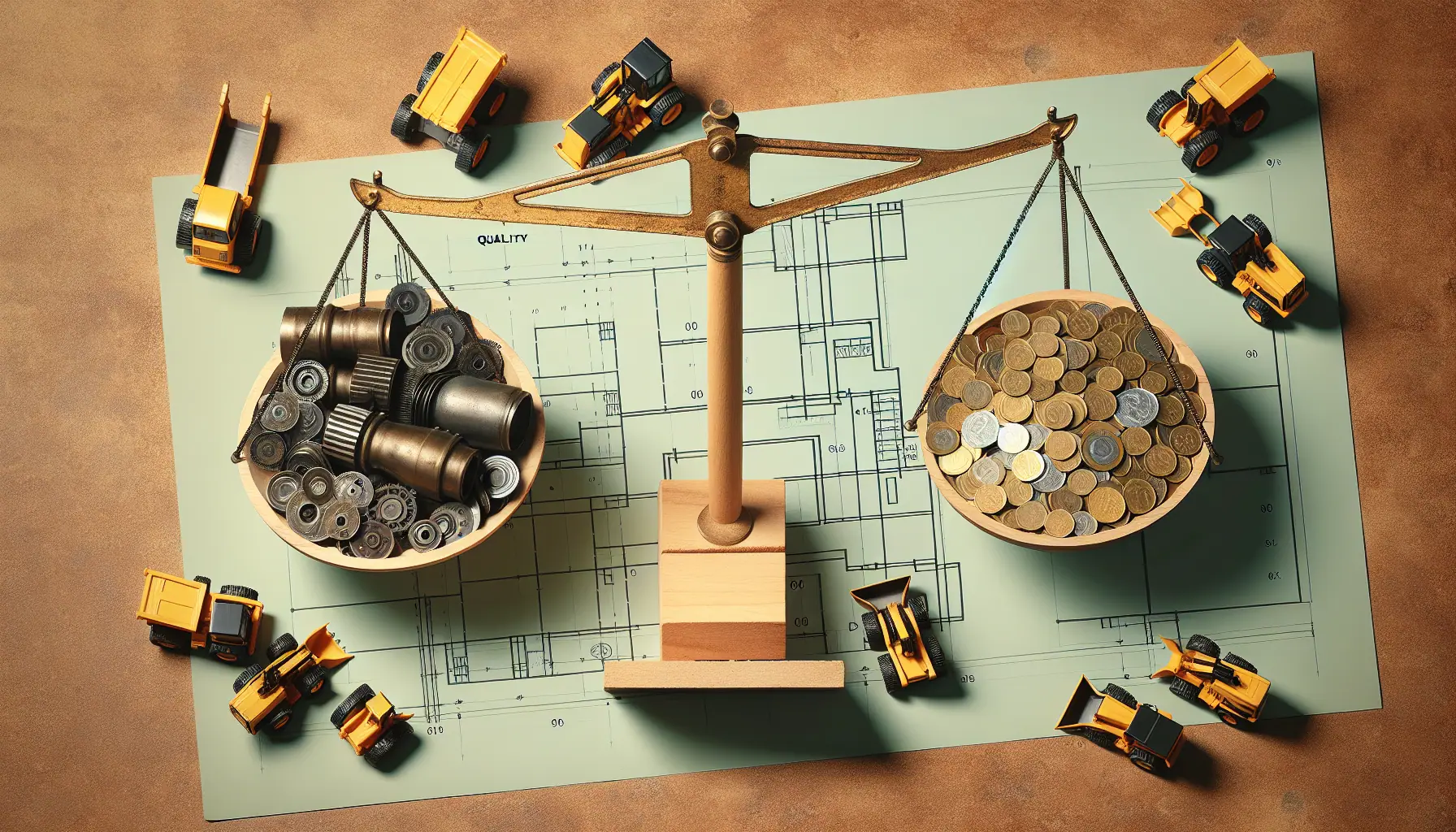
Heavy Machinery Prices: Key Factors in Cost and Quality Balance
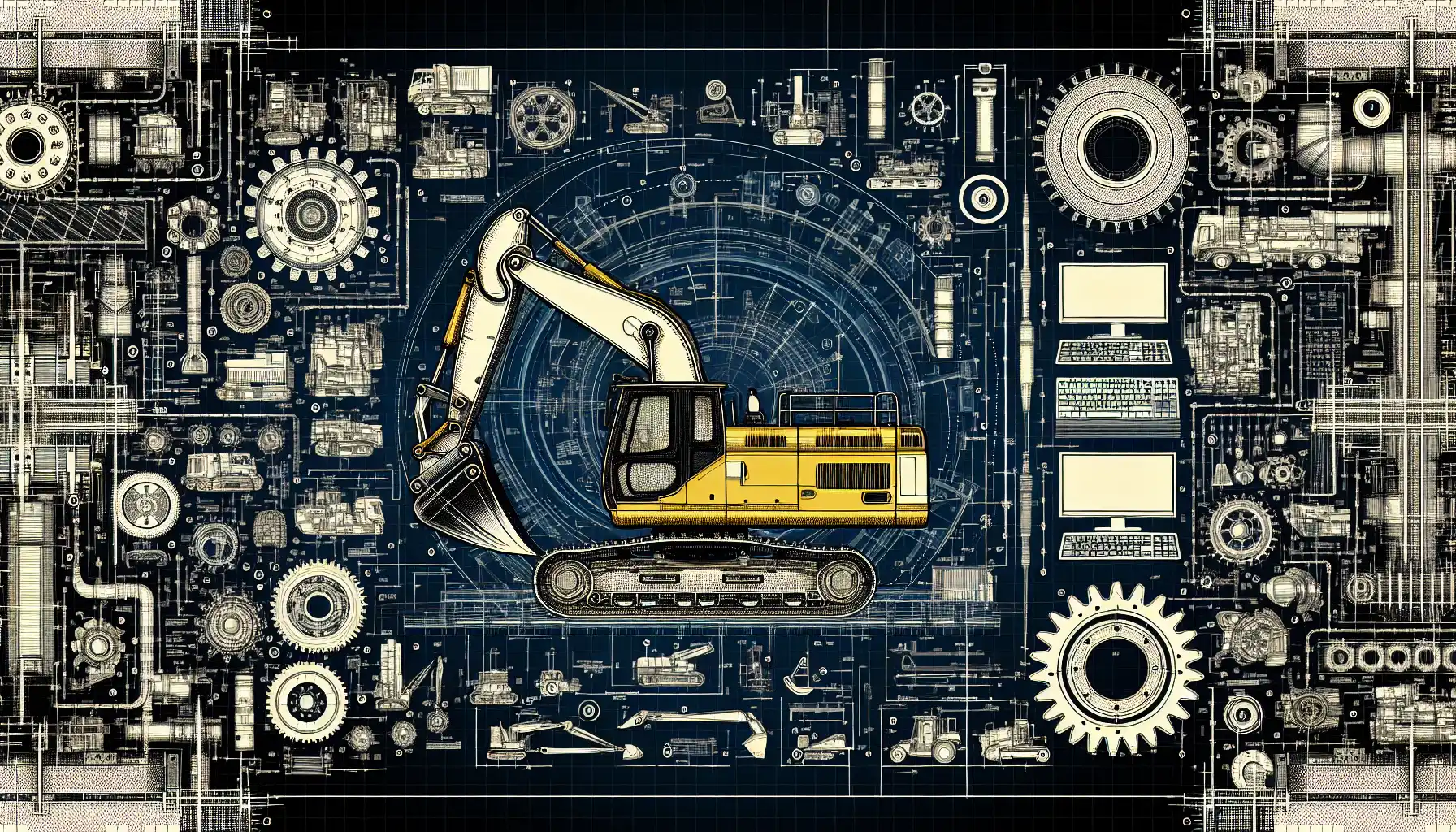
Best Construction Heavy Equipment Brands: Pros and Cons
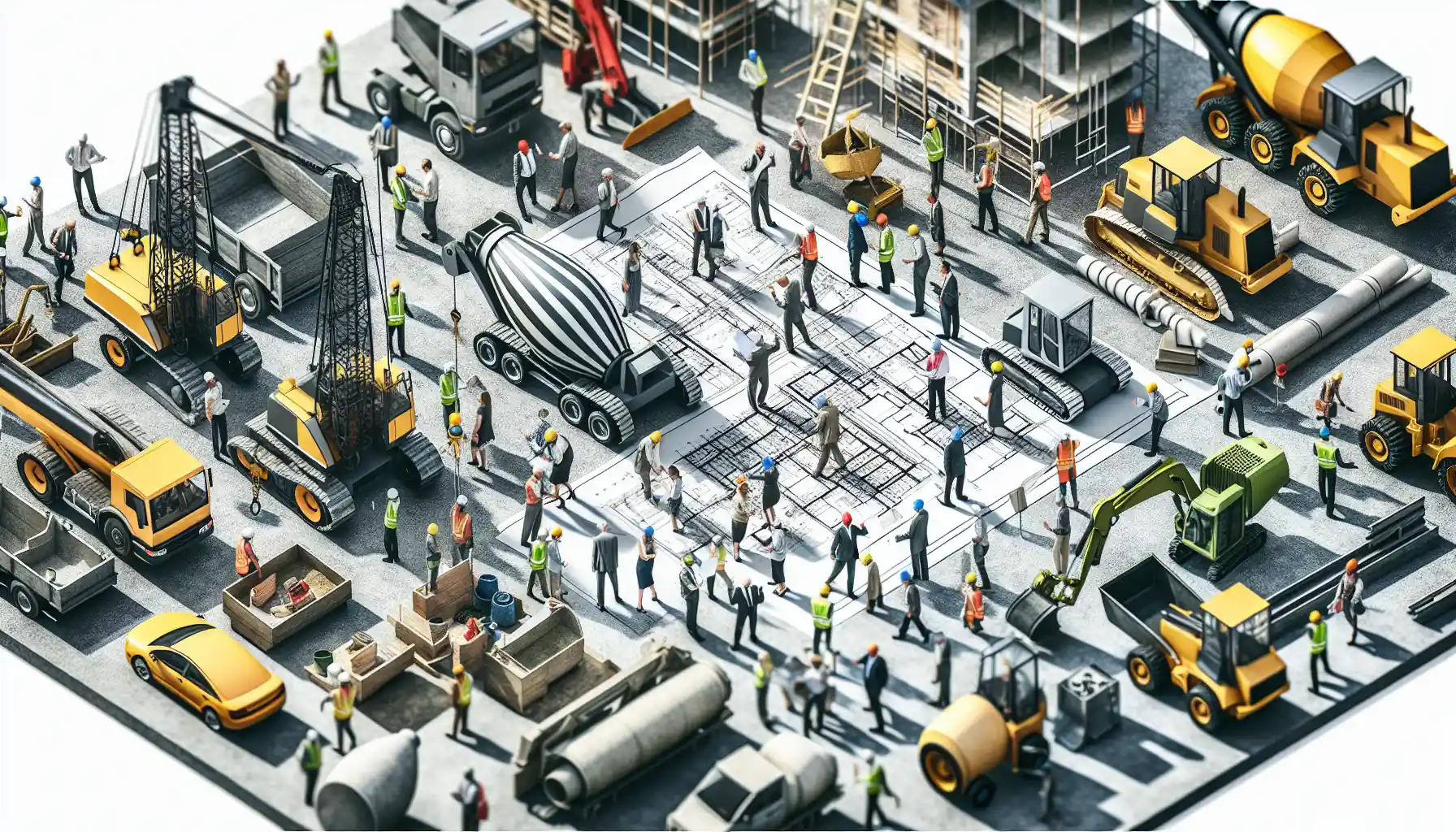
Construction Site Equipment: How to Determine Your Requirements
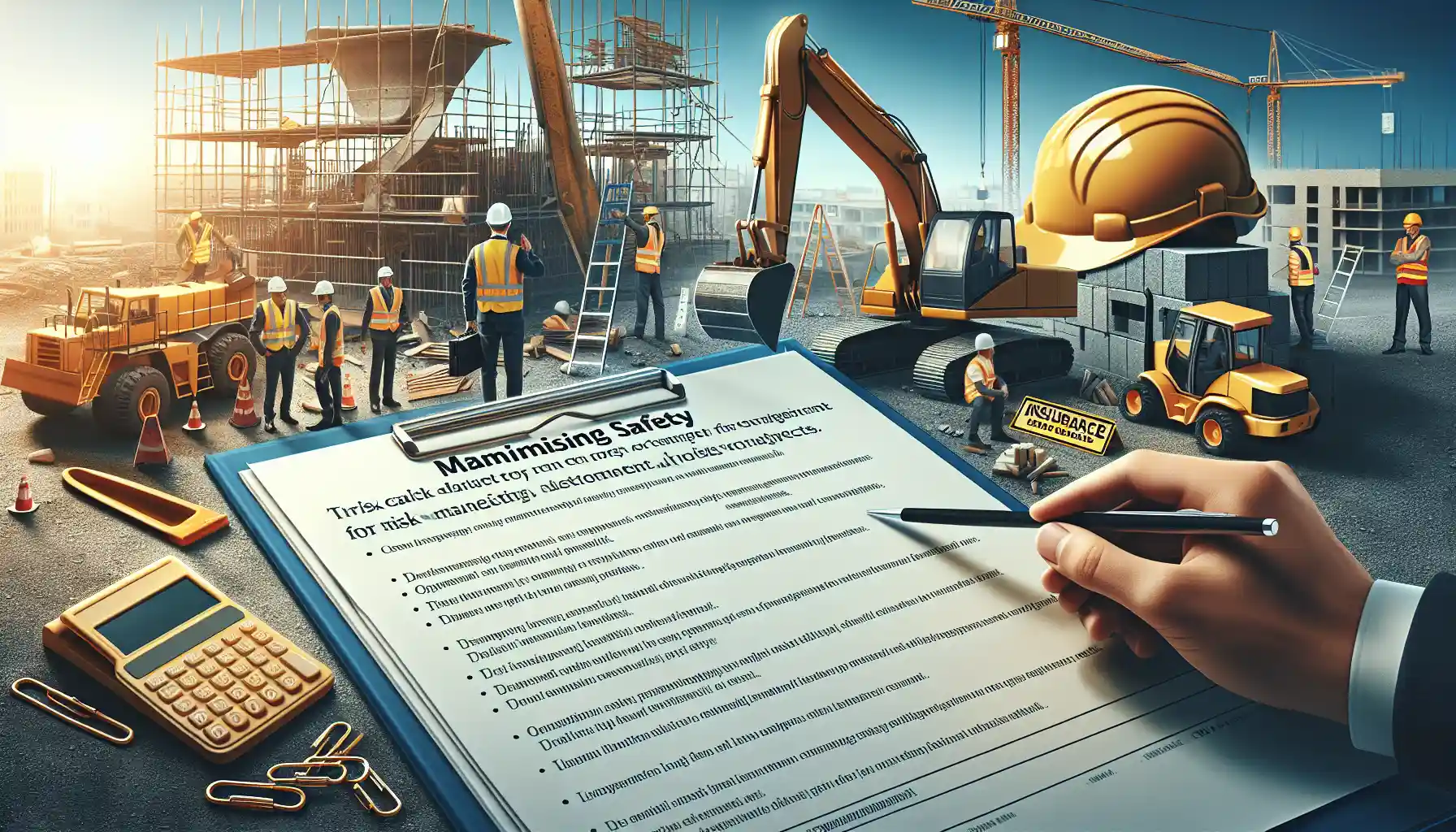
Maximizing Safety: Risk Management for Construction Projects
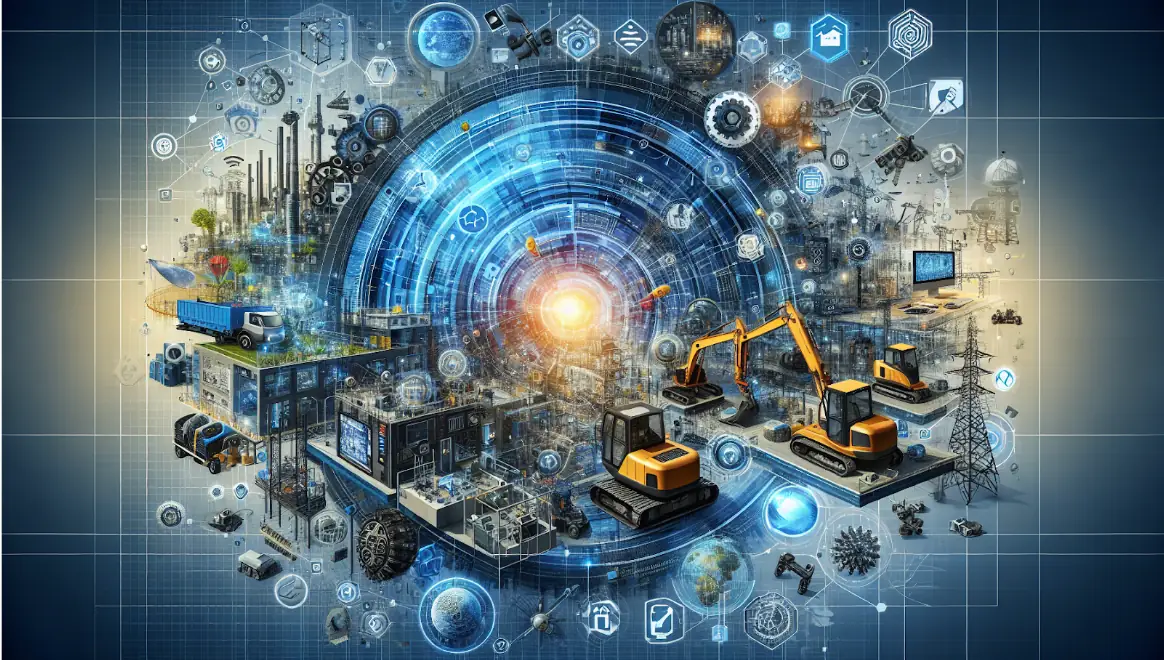
Innovations in Construction: Transforming Machinery and Equipment
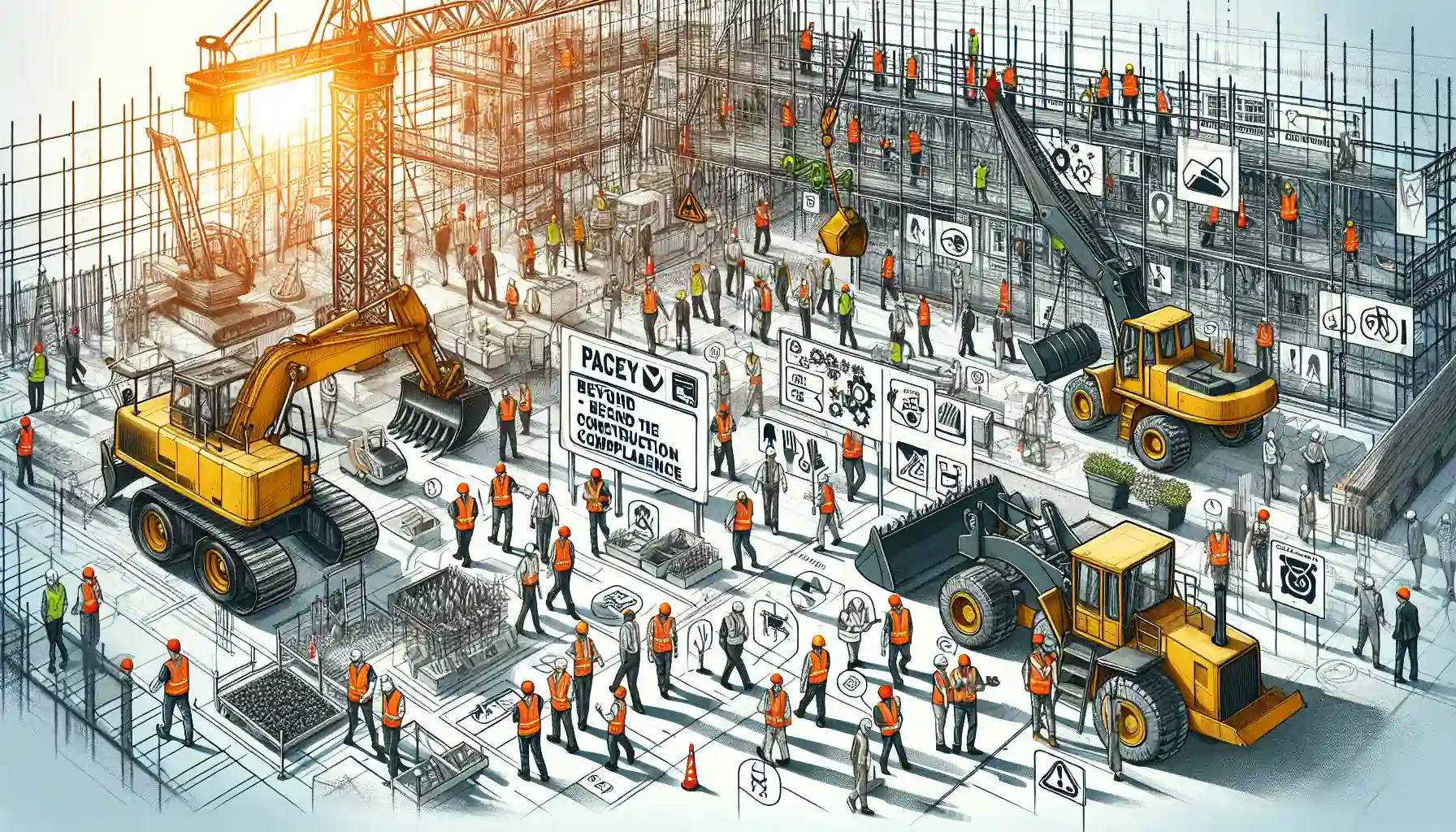
Heavy Equipment Safety: Beyond the Basics in Construction Compliance
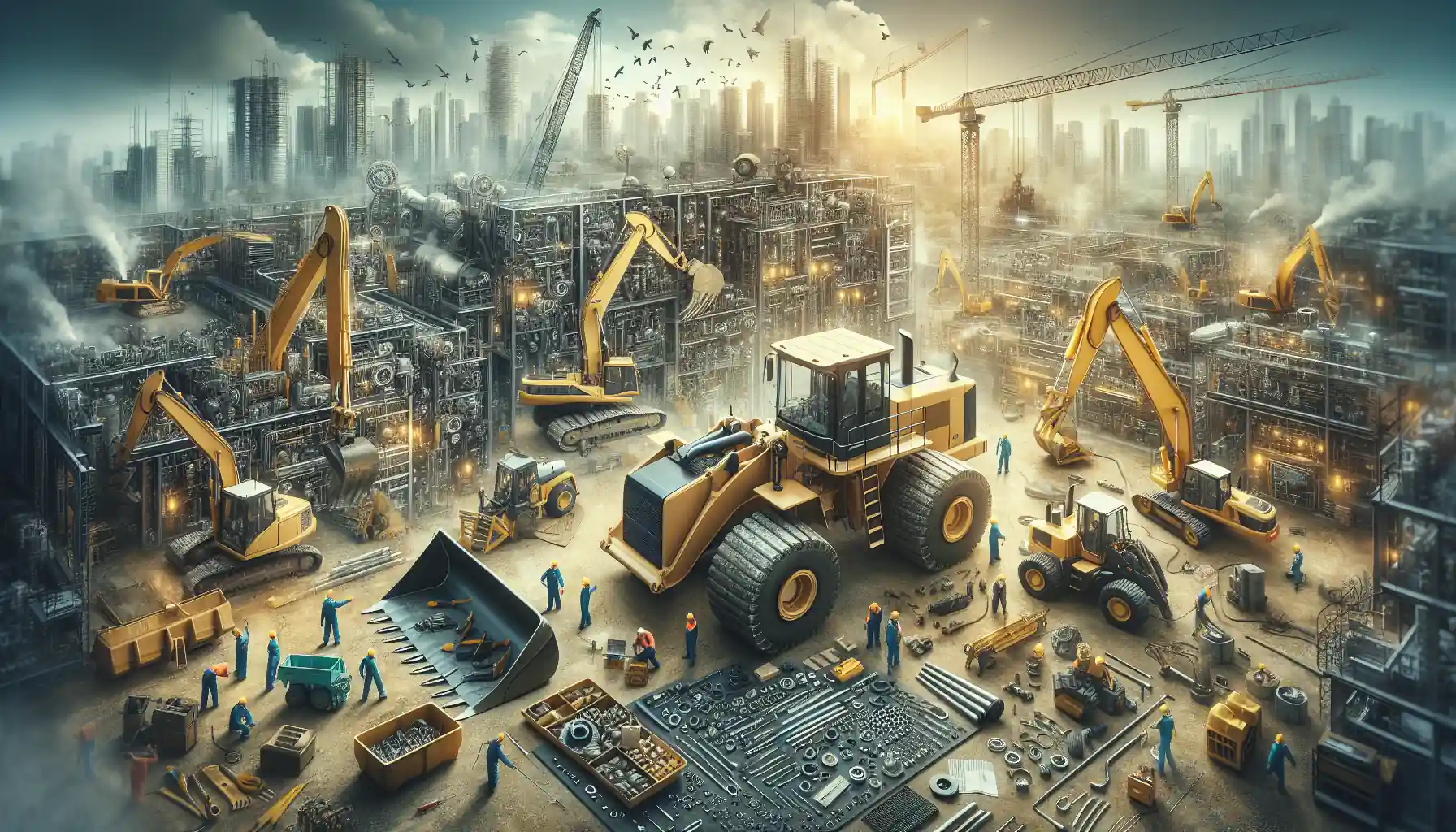
The Essential Handbook for Construction Equipment Repair and Maintenance
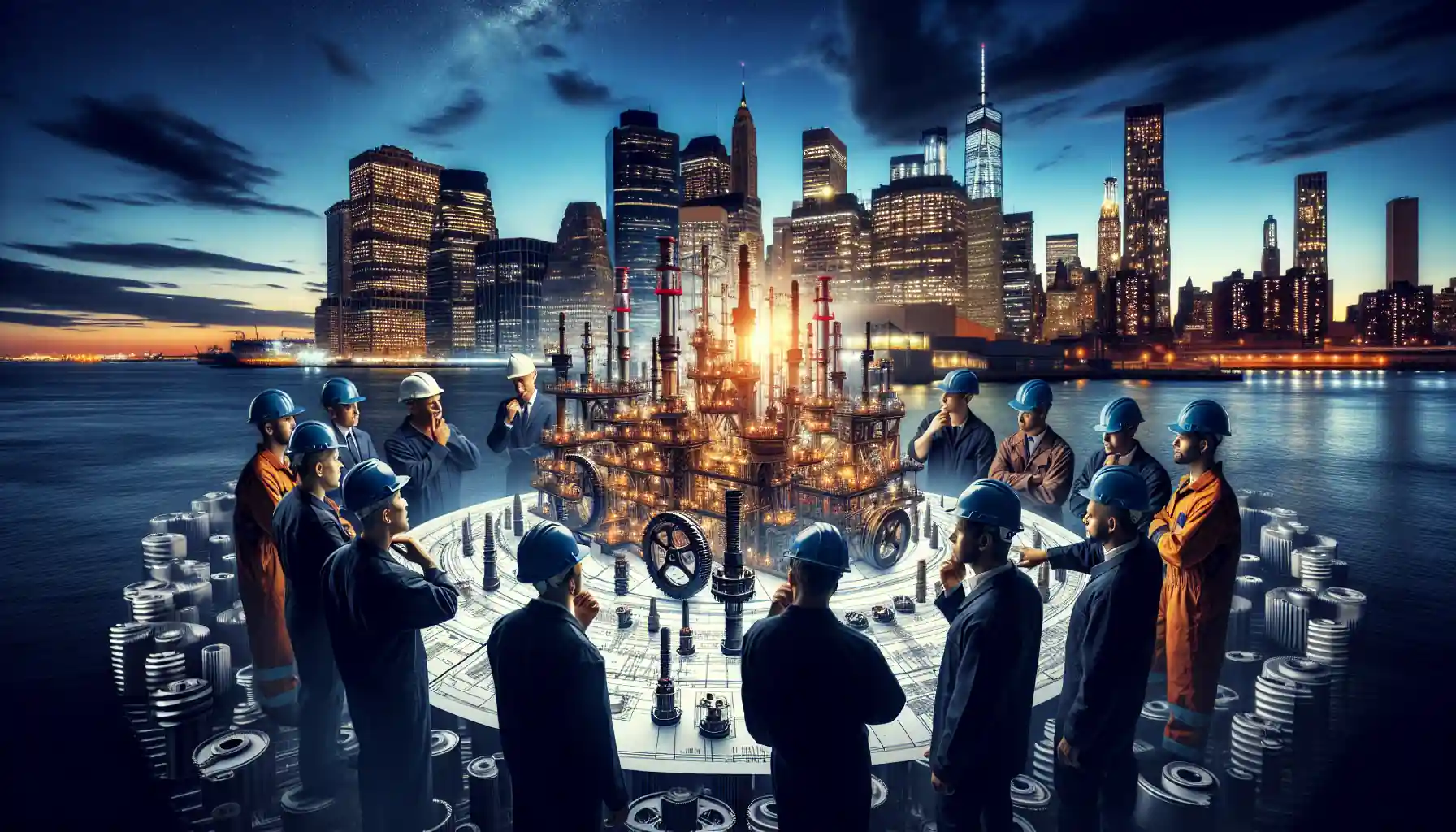
How to Efficiently Source Oil and Gas Machinery Parts in NYC
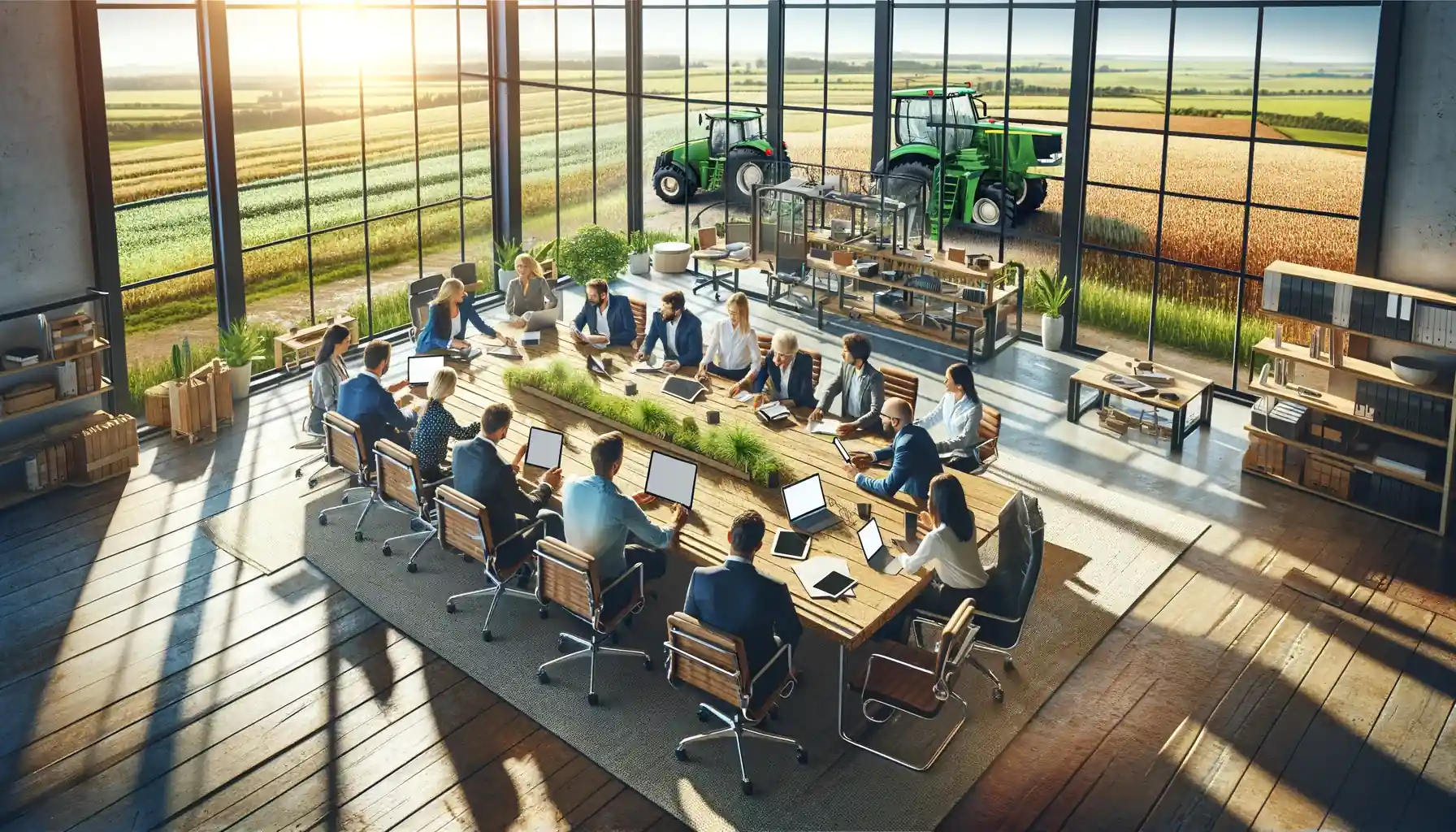
Essential Guide to Sourcing Agriculture Equipment Parts
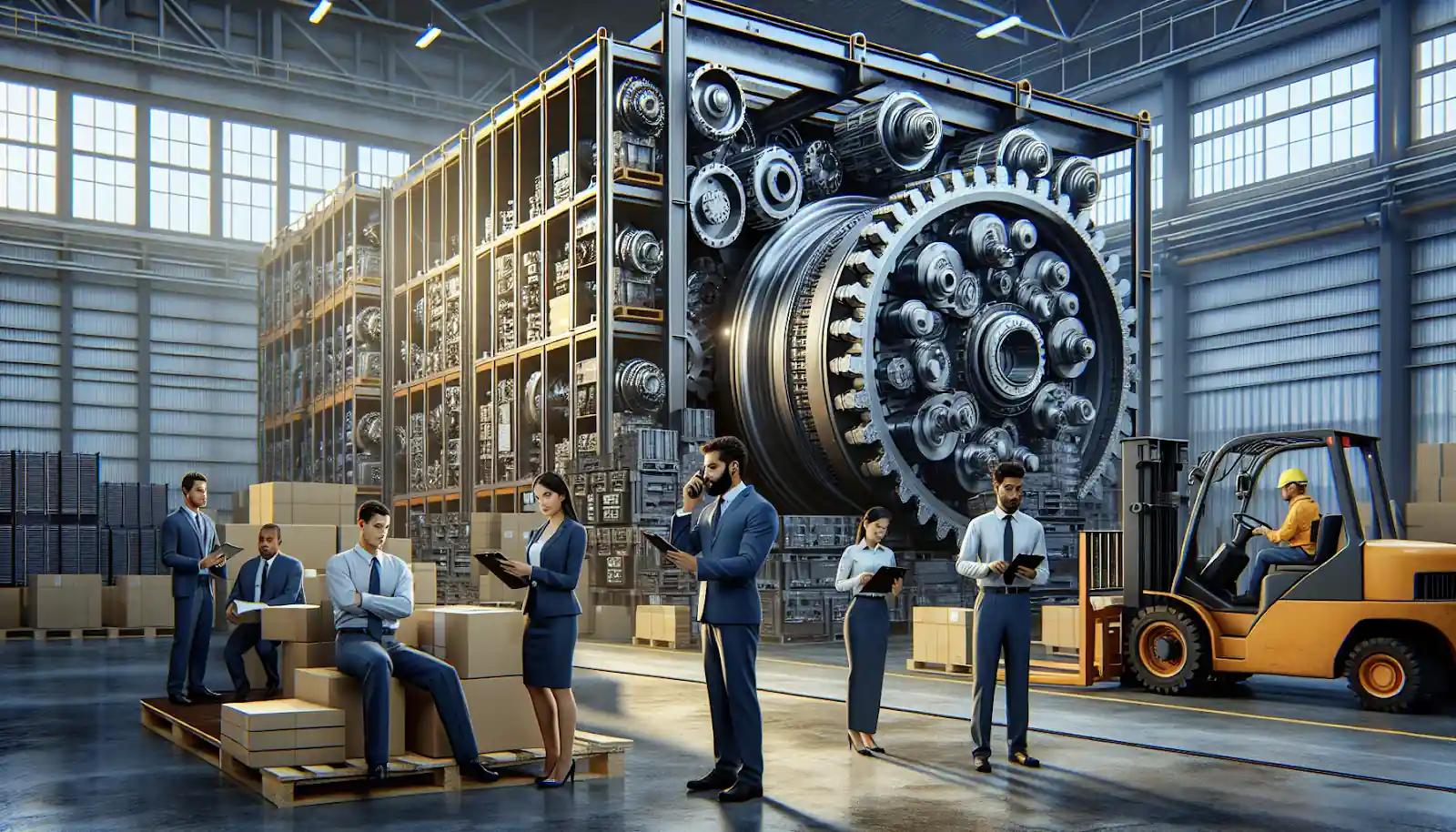
How to Source Mining Machinery Parts: Tips and Strategies
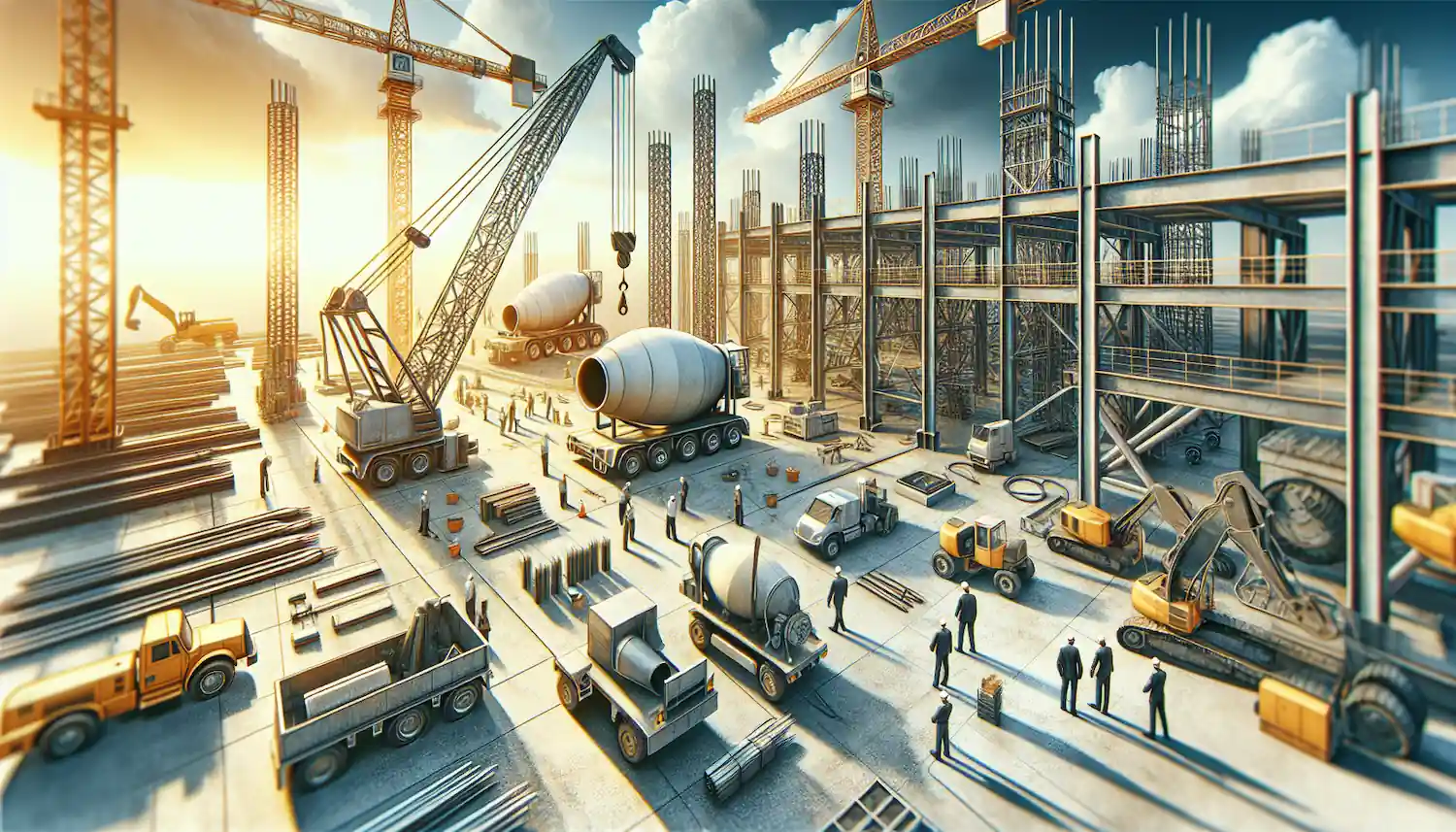